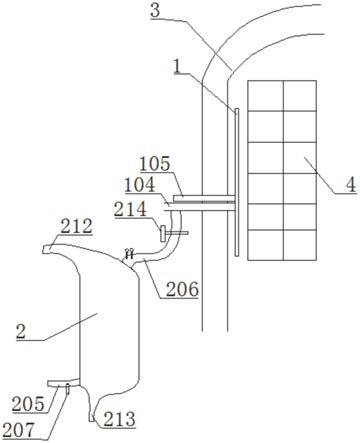
一种梭式窑用燃烧设备
【技术领域】
1.本实用新型涉及氧化铝生产技术领域,具体涉及一种梭式窑用燃烧设备。
背景技术:2.电工填料氧化铝生产过程中需要将原料研磨后压制砖坯,送入梭式窑进行高温烧结,以完成从γ相到α相的转变。目前梭式窑燃烧器为简单的直喷火嘴,火焰温度高,产生的气流压力大,直接喷在附近的砖坯上,造成砖坯骤然受热,局部加热不均衡,因而火嘴周围的砖坯变形、断裂、破碎以至于砖堆倒塌;另外,由于电工填料氧化铝烧结温度>1500℃,当窑内温度上升至1000℃以上时,新风与烟气经换热器进行换热后,热新风(即助燃风)温度升高(>600℃),风压升高,助燃风氧含量降低,燃气燃烧不充分,造成升温困难,常规采用提高新风压力补充氧含量的操作会导致窑压持续升高,操作危险性大;有研究采用直接通氧气方式提高燃气燃烧效率,但此方式会导致火焰温度过高,烧坏炉体和燃烧嘴,应用效果较差。若直接将高于600摄氏度的助燃风提高氧含量至所需,在管路内与天然气混合后有爆炸的风险。
技术实现要素:3.针对现有技术的缺陷,本实用新型提供一种梭式窑用燃烧设备,所述燃烧设备能够降低助燃风压力、提高氧含量,并将热量均匀传递至砖坯,提高了热能利用率,降低了生产成本。
4.本实用新型提供一种梭式窑用燃烧设备,包括燃烧器以及连接在燃烧器主进气管前的预混调温装置,所述燃烧器设置为h型,包括两根相对设置的竖直燃烧管以及连接在两竖直燃烧管之间的水平燃烧管,所述竖直燃烧管的两端封堵,中部与水平燃烧管连通,所述竖直燃烧管及水平燃烧管的一侧面均均匀设置有多个燃烧孔,所述水平燃烧管长度方向的中间位置远离燃烧孔的一侧设置一混合气体进气口。
5.优选地,所述燃烧器的竖直燃烧管和水平燃烧管上均设置有两排燃烧孔,其中,竖直燃烧管上的两排燃烧孔分别以其所在面的中间位置左右对称分布;水平燃烧管上的两排燃烧孔以其所在面的中间位置上下对称分布。
6.优选地,所述竖直燃烧管上的两排燃烧孔分别向远离其对称轴的一侧喷射,且其喷射方向与竖直方向的夹角为30~45
°
,使得火焰不直喷砖坯。
7.优选地,所述水平燃烧管上的两排燃烧孔分别向远离其对称轴的一侧喷射,且其与水平方向的夹角为30~45
°
,使得火焰不直喷砖坯。
8.优选地,所述预混调温装置包括预混装置及包覆在预混装置外的调温壳体,所述预混装置包括上封头、下封头以及连接在上封头与下封头之间的换热结构,所述换热结构包括换热壳体、分别固定在换热壳体内上下两端的管板以及连接在两管板之间的换热管。
9.优选地,所述下封头的侧面设置一进气管,所述进气管穿出调温壳体,并与调温壳体固定连接,位于调温壳体外的进气管上连接一氧气喷头,所述下封头与换热管下端管板
之间的空间作为助燃气与氧气的混合空间;所述上封头上远离进气管的一侧设置一出气管,所述出气管穿出调温壳体,并与调温壳体固定连接,所述出气管的另一端通过主进气管与燃烧器上的混合气体进气口连接,主进气管的另一端与天然气管道连接,使得预混气体与天然气混合后通入燃烧器。
10.优选地,位于调温壳体外的出气管上设置一氧含量检测仪和一测温仪,用于检测换热后气体的氧含量和温度。
11.优选地,位于调温壳体外的出气管上还设置一阀门,当预混气体的氧含量与温度达到要求后,打开阀门,将预混气体通入主进气管。
12.优选地,所述调温壳体内侧顶部设置一向预混装置喷水的冷水喷头,所述冷水喷头外接水泵,用于对换热结构内的预混气体换热。
13.优选地,所述调温壳体的顶部设置一蒸汽出口,用于收集产生的蒸汽,底部设置一热水出口,用于收集换热后的热水。
14.与现有技术相比,本实用新型具有以下有益效果:
15.本实用新型所述燃烧设备使用的燃烧器设置为h型结构,火焰分布均匀,能够将热量均匀温和地传递至砖坯,且其燃烧孔呈一定角度,不直喷砖坯,减少了砖坯烧碎、倒塌现象的发生,提高了热能利用率,降低了生产成本,提高了α转化率;
16.本实用新型所述燃烧设备使用的预混调温装置,能够降低助燃风压力从而降低高温区窑压,通过适量补充氧气提高助燃风氧含量,有利于高温短温度的攀升,提高了操作的安全性,延长了窑炉使用寿命,操作简便。
【附图说明】
17.为了更清楚地说明本实用新型实施例或现有技术中的技术方案,下面将对实施例或现有技术描述中所需要使用的附图作简单地介绍,显而易见地,下面描述中的附图仅仅是本实用新型的一些实施例,对于本领域普通技术人员来讲,在不付出创造性劳动的前提下,还可以根据这些附图获得其他的附图。
18.图1是本实用新型所述燃烧设备的结构示意图;
19.图2是本实用新型所述燃烧器的结构示意图;
20.图3是竖直燃烧管的截面示意图;
21.图4是本实用新型所述预混调温装置的剖视图;
22.其中,1-燃烧器;101-竖直燃烧管;102-水平燃烧管;103-燃烧孔;104-主进气管;105-点火器;2-预混调温装置;201-上封头;202-下封头;203-换热管;204-管板;205-进气管;206-出气管;207-氧气喷头;208-氧含量检测仪;209-测温仪;210-调温壳体;211-冷水喷头;212-蒸汽出口;213-换热水出口;214-阀门;3-梭式窑;4-砖坯。
【具体实施方式】
23.为使本实用新型的目的、技术方案和优点更加清楚,下面结合附图和具体实施例,对本实用新型做进一步描述,显然,所描述的实施例仅仅是本实用新型一部分实施例,而不是全部的实施例。基于本实用新型的实施例,本领域普通技术人员在没有做出创造性劳动前提下所获得的所有其他实施例,都属于本实用新型保护的范围。
24.如图1所示,本实用新型提供了一种梭式窑用燃烧设备,包括燃烧器1以及连接在燃烧器主进气管前的预混调温装置2,所述燃烧器1设置为h型,包括两根相对设置的竖直燃烧管101以及连接在两竖直燃烧管101之间的水平燃烧管102,所述竖直燃烧管101的两端封堵,中部与水平燃烧管102连通,所述竖直燃烧管101及水平燃烧管102靠近砖坯的一侧面均均匀设置有多个燃烧孔103,所述水平燃烧管102长度方向的中间位置远离燃烧孔的一侧设置一混合气体进气口。
25.作为优选,如图2和3所示,所述燃烧器1的竖直燃烧管101和水平燃烧管102上均设置有两排燃烧孔103,其中,竖直燃烧管101上的两排燃烧孔103分别以其所在面的中间位置左右对称分布;水平燃烧管102上的两排燃烧孔103以其所在面的中间位置上下对称分布。
26.作为优选,如图3所示,所述竖直燃烧管101上的两排燃烧孔103分别向远离其对称轴的一侧喷射,且其喷射方向与竖直方向的夹角为30~45
°
,使得火焰不直喷砖坯4。
27.作为优选,所述水平燃烧管102上的两排燃烧孔103分别向远离其对称轴的一侧喷射,且其与水平方向的夹角为30~45
°
,使得火焰不直喷砖坯4。
28.作为优选,如图4所示,所述预混调温装置2包括预混装置及包覆在预混装置外的调温壳体210,所述预混装置包括上封头201、下封头202以及连接在上封头201与下封头202之间的换热结构,所述换热结构包括换热壳体、分别固定在换热壳体内上下两端的管板204以及连接在两管板之间的换热管203。
29.作为优选,所述上封头、下封头与换热壳体可以是一体成型,也可以通过法兰连接。
30.作为优选,所述下封头202的侧面设置一进气管205,所述进气管205穿出调温壳体210,并与调温壳体210固定连接(采用本领域技术人员常用的固定方式即可,如焊接、法兰),位于调温壳体外的进气管205上连接一氧气喷头207,所述下封头202与换热管下端管板之间的空间作为助燃气与氧气的混合空间;所述上封头201远离进气管205的一侧设置一出气管206,所述出气管206穿出调温壳体210,并与调温壳体210固定连接,所述出气管的另一端通过主进气管104与燃烧器上的混合气体进气口连接,所述主进气管104的另一端与天然气管道连接。
31.作为优选,位于调温壳体外的出气管206上设置有氧含量检测仪208和测温仪209,用于检测换热后气体的氧含量和温度(所述氧含量检测仪和测温仪位于靠近调温壳体的一侧)。
32.作为优选,位于调温壳体外的出气管206上设置一阀门214,所述阀门214设置在远离调温壳体的一侧,当预混气体的氧含量与温度达到要求后,打开阀门214,将预混气体通入主进气管104。
33.作为优选,所述调温壳体210的内侧顶部设置一向预混装置喷水的冷水喷头211,所述冷水喷头211外接水泵,用于对换热结构内的预混气体换热。
34.作为优选,所述调温壳体210的顶部设置一蒸汽出口212,用于收集产生的蒸汽,底部设置一热水出口213,用于收集换热后的热水。
35.本实用新型所述均化装置的工作原理:如图1所示,在使用时,所述燃烧器1置于梭式窑内,将带有燃烧孔的一面面向砖坯4,点火器105穿过梭式窑3,点火端位于水平燃烧管中间位置燃烧孔的上端,预混调温装置2置于梭式窑3外,预混调温装置的出气管206与主进
气管104连通后穿过梭式窑3与燃烧器水平燃烧管上的混合气体进气口连接,气体在窑外混合后通入燃烧器1内。
36.如图2所示,助燃气和氧气分别通过进气管205及氧气喷头207进入预混装置内,在下封头202与下端管板之间的空间内混合均匀后通过换热管203汇聚到上封头201与上端管板之间的空间内,通过氧含量检测仪208及测温仪209检测换热后气体中的氧含量及温度,根据氧含量数据调整氧气喷头207的喷氧压力,使得氧含量在19%~25%之间;根据测得的温度数据,调整与冷水喷头连接的水泵的流量,使得出气温度在300~500℃之间,当氧含量及温度符合要求后,打开阀门214,使得预混后的气体通入主进气管104与天然气混合后进入燃烧器1内,点火后,火苗迅速向各燃烧管蔓延,将燃烧热量均匀温和地传递至砖坯。换热后的热水及过程中产生的蒸汽分别通过调温壳体下部的换热水出口213及上部的蒸汽出口212排至循环水池回收余热。