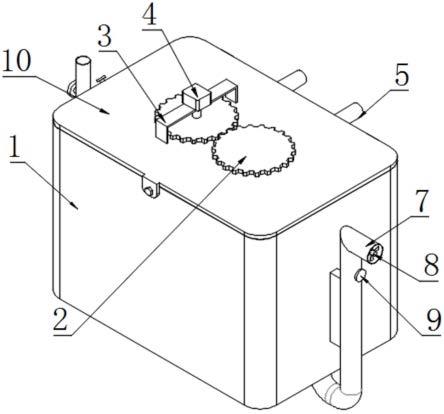
1.本实用新型涉及瓦斯气体技术领域,尤其涉及一种超低浓度瓦斯气体蓄热式直燃焚烧装置。
背景技术:2.现有的瓦斯气体在制造过程中,由于生产过程中的变量,导致生产出来的瓦斯浓度会有所偏差,而低浓度的瓦斯无法进行收集使用,但是直接排放的话会造成空气污染,或者被人员误吸,造成人员受伤。
技术实现要素:3.本实用新型的目的是为了解决现有技术中现有的瓦斯气体在制造过程中,由于生产过程中的变量,导致生产出来的瓦斯浓度会有所偏差,而低浓度的瓦斯无法进行收集使用,但是直接排放的话会造成空气污染,或者被人员误吸,造成人员受伤的问题,而提出的一种超低浓度瓦斯气体蓄热式直燃焚烧装置。
4.为了实现上述目的,本实用新型采用了如下技术方案:一种超低浓度瓦斯气体蓄热式直燃焚烧装置,包括燃烧炉,所述燃烧炉的顶部后侧位置铰链连接有盖板,所述盖板的顶部中心处对称转动连接有两个齿轮,且盖板的顶部一侧固定连接有支撑架,所述支撑架的顶部中心处固定连接有电机,所述盖板的底部位于每一个齿轮的位置转动连接有搅拌件,所述燃烧炉的一侧外表面设置有连接管,所述连接管外表面靠近顶部位置设置有第一电磁阀,且连接管的内表面顶部位置设置有风扇,所述燃烧炉的另一侧顶部位置连通有空心管,所述空心管的外表面一侧设置有两个第二电磁阀,且空心管的外表面靠近燃烧炉的位置设置有第三电磁阀。
5.优选的,所述电机的驱动端贯穿支撑架的表面向外延伸与齿轮的顶部中心处固定连接。
6.优选的,两个所述齿轮的表面啮合连接,所述搅拌件的顶部端面贯穿盖板的表面与齿轮的底部中心处固定连接。
7.优选的,所述连接管的底部端面与燃烧炉的内底部一侧连通。
8.优选的,所述连接管和空心管的内表面底部位置分别设置有检测仪。
9.优选的,所述空心管的内表面顶部位置设置有电子打火器。
10.优选的,所述燃烧炉的后表面顶部位置对称连通有两个进气管。
11.与现有技术相比,本实用新型的优点和积极效果在于,
12.1、本实用新型中,通过设置盖板,便于通过盖板实现齿轮和搅拌件的位置固定,并且通过设置的电机驱动实现其中一个齿轮旋转,并且通过两个齿轮的啮合连接实现另一个齿轮旋转,设置的两个进气管便于实现低浓度瓦斯气体和氢气的进入,进而实现两个搅拌件旋转实现燃烧炉中气体充分混合,便于实现低浓度的瓦斯气体可以顺利燃烧。
13.2、本实用新型中,通过设置连接管和空心管,便于通过连接管实现加入瓦斯和氢
气时,燃烧炉中的空气可以顺利排出,并且通过设置的风扇便于向燃烧炉中加入空气,进而实现燃烧炉中的气体进入空心管中,并且通过空心管内顶部的电子打火器实现混合完成的气体的点燃。
附图说明
14.图1为本实用新型提出一种超低浓度瓦斯气体蓄热式直燃焚烧装置的立体结构示意图;
15.图2为本实用新型提出一种超低浓度瓦斯气体蓄热式直燃焚烧装置图1的左视结构示意图;
16.图3为本实用新型提出一种超低浓度瓦斯气体蓄热式直燃焚烧装置图1的后视结构示意图;
17.图4为图1的剖视结构示意图。
18.图例说明:1、燃烧炉;2、齿轮;3、支撑架;4、电机;5、进气管;6、空心管;7、连接管;8、风扇;9、第一电磁阀;10、盖板;11、搅拌件; 12、检测仪;13、第二电磁阀;14、第三电磁阀;15、电子打火器。
具体实施方式
19.为了能够更清楚地理解本实用新型的上述目的、特征和优点,下面结合附图和实施例对本实用新型做进一步说明。需要说明的是,在不冲突的情况下,本技术的实施例及实施例中的特征可以相互组合。
20.在下面的描述中阐述了很多具体细节以便于充分理解本实用新型,但是,本实用新型还可以采用不同于在此描述的其他方式来实施,因此,本实用新型并不限于下面公开说明书的具体实施例的限制。
21.实施例1,如图1-4所示,一种超低浓度瓦斯气体蓄热式直燃焚烧装置,包括燃烧炉1,燃烧炉1的后表面顶部位置对称连通有两个进气管5,燃烧炉1的顶部后侧位置铰链连接有盖板10,盖板10的顶部中心处对称转动连接有两个齿轮 2,且盖板10的顶部一侧固定连接有支撑架3,支撑架3的顶部中心处固定连接有电机4,电机4的驱动端贯穿支撑架3的表面向外延伸与齿轮2的顶部中心处固定连接,盖板10的底部位于每一个齿轮2的位置转动连接有搅拌件11,两个齿轮2 的表面啮合连接,搅拌件11的顶部端面贯穿盖板10的表面与齿轮2的底部中心处固定连接。
22.其整个实施例1达到的效果为,设置的盖板10便于实现齿轮2和搅拌件11的位置固定,并且如图4所示,设置两个搅拌件11交错设置,而设置的两个齿轮2 互相啮合连接,并且设置的齿轮2与相邻的搅拌件11的顶部端面固定连接,因此在电机4的驱动作用下,便于试下其中一个齿轮2带动另一个齿轮2旋转,并且两个齿轮2做反向旋转,进而实现两个搅拌件11反向旋转,而设置的两个进气管5 分别用于低浓度瓦斯气体和氢气的进入,通过在瓦斯气体中掺杂氢气,便于保证瓦斯气体可以顺利的被点燃,而通过两个搅拌件11旋转产生的风力实现加入的瓦斯气体和氢气的快速混合均匀。
23.实施例2,如图1-4所示,燃烧炉1的一侧外表面设置有连接管7,连接管7的底部端面与燃烧炉1的内底部一侧连通,连接管7外表面靠近顶部位置设置有第一电磁阀9,且连接
管7的内表面顶部位置设置有风扇8,燃烧炉1的另一侧顶部位置连通有空心管6,空心管6的内表面顶部位置设置有电子打火器15,连接管7 和空心管6的内表面底部位置分别设置有检测仪12,空心管6的外表面一侧设置有两个第二电磁阀13,且空心管6的外表面靠近燃烧炉1的位置设置有第三电磁阀14。
24.其整个实施例2达到的效果为,设置的连接管7便于在向燃烧炉1中加入比空气轻的瓦斯气体和氢气时,实现燃烧炉1中的空气通过连接管7排出,设置的检测仪12为现有的气体检测仪,便于判断连接管7和空心管6中的气体为空气还是氢气,并且通过设置的第一电磁阀9实现连接管7的及时关闭,防止瓦斯或者氢气通过连接管7外泄,而设置在空心管6表面的第三电磁阀14便于实现空心管6的开合,防止在加入瓦斯和氢气时,气体进入空心管6中,而设置两个第二电磁阀 13便于实现空心管6某一段部分的开合,便于试下空心管6的逐次关闭。
25.工作原理,第三电磁阀14控制实现空心管6关闭,然后通过两个进气管5实现瓦斯和氢气的注入,并且在注入的过程中,电机4驱动实现其中一个齿轮2旋转,进而实现两个齿轮2带动两个搅拌件11反向旋转,实现加入的瓦斯和氢气混合均匀,并且加入的瓦斯和氢气在燃烧炉1的内顶部堆积实现燃烧炉1中的空气通过连接管7排出,并且当连接管7中的检测仪12检测到瓦斯时,第一电磁阀9控制实现连接管7关闭,然后风扇8启动,第一电磁阀9、第二电磁阀13和第三电磁阀14控制实现连接管7和空心管6打开,通过风扇8启动实现燃烧炉1中的混合气体进入空心管6中,并且通过空心管6内顶部设置的电子打火器15实现混合气体的点燃。
26.以上所述,仅是本实用新型的较佳实施例而已,并非是对本实用新型作其它形式的限制,任何熟悉本专业的技术人员可能利用上述揭示的技术内容加以变更或改型为等同变化的等效实施例应用于其它领域,但是凡是未脱离本实用新型技术方案内容,依据本实用新型的技术实质对以上实施例所作的任何简单修改、等同变化与改型,仍属于本实用新型技术方案的保护范围。