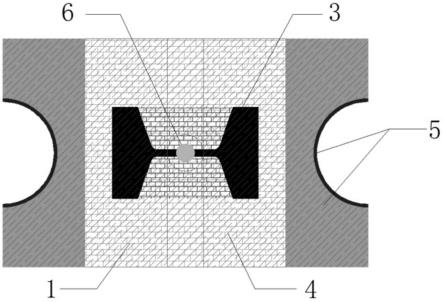
1.本实用新型属于火工品技术领域以及电子封装技术领域,特别是涉及一种一体化封装半导体桥点火器。
背景技术:2.点火器的安全性和可靠性是整个火工品系统安全与可靠作用的关键。传统桥丝式或薄膜桥点火器虽然也能满足 1a/1w、5min 条件下不点火的安全要求,但由于需将分离元件进行整合封装,可靠性不能适应当前火工品的使用要求。
3.点火器现有技术的主要缺点在于:1、封装困难;2、可靠性差。现有技术无法解决以上缺点的原因为:薄膜桥点火器传统封装是先将薄膜桥用环氧树脂粘结在陶瓷塞或to电极塞上脚线间的凹槽内,然后用超声波或金丝球焊将金属连接脚线焊接在薄膜桥上的焊接区上,而在实际应用中存在陶瓷破裂和焊线断开或接点松动问题,不适合压装起爆药剂;并且该种封装形式的点火器抗环境振动、冲击干扰能力较差,一般情况下点火器在使用和运输途中不可避免受到振动影响,可能造成焊接点破裂脱焊,影响火工品点火的可靠性。因此,传统引线焊接封装形式不满足火工品系统高安全性和可靠性要求。
技术实现要素:4.本实用新型的目的是克服上述现有技术存在的缺陷,提供一种一体化封装的半导体桥点火器,采用更可靠的回流焊工艺和预埋式结构替代传统的金属引线键合、包封等方式。
5.本实用新型解决其技术问题所采用的技术方案是:一种一体化封装半导体桥点火器,包括:封装基体,对称设于所述封装基体的上表面两端的第一电极层;所述封装基体的上表面自上而下凹陷形成芯腔;还包括:
6.半导体电阻桥芯片,粘合于所述芯腔内;所述半导体电阻桥芯片的上表面的对应位置向下凹陷形成芯孔;
7.含能层,铺设于所述芯孔内;
8.连接电极层,一端粘结于所述第一电极层,另一端连接于半导体电阻桥芯片的电极。
9.在进一步的实施例中,还包括:对称设于所述封装基体的下表面两端的第二电极层。
10.在进一步的实施例中,所述封装基体两侧面为向内凹陷的曲面,形成连通于第一电极层和第二电极层的半孔结构;
11.所述曲面上设置有第三电极层。
12.在进一步的实施例中,半导体电阻桥芯片的底面与芯腔之间设置有粘合层,所述粘合层为环氧树脂粘结胶或daf膜,其厚度为10~50μm。
13.在进一步的实施例中,所述封装基体为双面覆铜fr4基板或聚酰亚胺基板,所述芯
腔的深度比半导体电阻桥芯片的厚度大10~50μm。
14.在进一步的实施例中,所述含能层为al/cuo、al/fe2o3或al/nio至少一层复合含能薄膜。
15.在进一步的实施例中,所述连接电极层为单面或双面覆铜柔性聚酰亚胺材料,厚度25~100μm。
16.在进一步的实施例中,所述第一电极层、第二电极层和第三电极层的结构相同,厚度为8~38μm,至少包括:4~15μm的铜层、1~8μm的镍层、3~15μm的锡层和0.05~0.5μm的金层。
17.本实用新型的有益效果:本实用新型的一体化封装半导体桥点火器的半导体桥电阻芯片与基体整体元件合成一体,使用时无需引线封装,半导体桥电阻可覆盖复合含能薄膜,工作过程中,复合含能薄膜发生铝热反应,放出热量,引爆火药,大大地降低点火所需能量及点火时间,能够用于解决现有的金属引线键合封装点火器存在的安全性、可靠性难题。与现有传统的金属引线键合封装的半导体桥点火器相比,本实用新型的一体化薄膜桥点火器减少了金丝引线这道工序,避免了在运输和使用过程中可能出现的金丝断裂或焊点不牢等情况,大大提高了薄膜桥点火器的可靠性、安全性,加强了加工工艺一致性。
18.本实用新型的一体化封装半导体桥点火器采用半导体加工工艺和激光钻孔工艺,有利于提高加工工艺的一致性和点火器使用的可靠性水平,并可实现批量化生产,有效降低制造成本。
附图说明
19.图1为一体化封装半导体桥点火器的俯视图。
20.图2为一体化封装半导体桥点火器的主视图。
21.图1至图2中的各标注为:封装基体1、粘合层2、半导体电阻桥芯片3、连接电极层4、表面电极层5、含能层6、第一电极层501、第二电极层502、第三电极层503。
具体实施方式
22.下面结合说明书附图和实施例对本实用新型做进一步的描述。
23.提供一种一体化封装的半导体桥点火器,采用更可靠的回流焊工艺和预埋式结构替代传统的金属引线键合、包封等方式。具体表现为,如图1和图2所示,一体化封装半导体桥点火器,包括:封装基体1、粘合层2、半导体电阻桥芯片3、连接电极层4和含能层6。其中,封装基体1的上表面自上而下凹陷形成芯腔,所述芯腔采用激光加工而成。所述芯腔内的上表面铺设用粘合层2,所述粘合层2用于固定半导体电阻桥芯片3。在进一步的实施例中,封装基体1为双面覆铜fr4基板或聚酰亚胺基板,所述芯腔的深度比半导体电阻桥芯片3的厚度大10~50μm。同时,粘合层2为环氧树脂粘结胶或daf膜,其厚度为10~50μm。即芯腔内填充粘合层2后应于半导体电阻桥芯片3高度基本一致。需要说明的是,芯腔应比半导体电阻桥芯片3尺寸稍大以方便贴装,防止半导体电阻桥芯片3在贴装时因偏位或旋转造成芯片的损伤失效。
24.在进一步的实施例中,半导体电阻桥芯片3的上表面的对应位置向下凹陷形成芯孔;所述含能层6则铺设在所述芯孔内,其中,含能层6为al/cuo、al/fe2o3或al/nio至少一层复合含能薄膜。
25.在另一个实施例中,所述封装基体1的上表面两端对称设置有第一电极层501,即所述第一电极层501对应铺设于封装基体1的上表面,则连接电极层4的一端通过焊接的方式连接于所述第一电极层501,另一端焊接于半导体电阻桥芯片3的电极。在进一步的实施例中,连接电极层4为单面或双面覆铜柔性聚酰亚胺材料,厚度25~100μm。
26.还包括:对称设于所述封装基体1的下表面两端的第二电极层502。
27.在进一步的实施例中,封装基体1两侧面为向内凹陷的曲面,形成连通于第一电极层501和第二电极层502的半孔结构;所述曲面上设置有第三电极层503。在本实施例中,第一电极层501、第二电极层502和第三电极层503构成一完整的表面电极层5。表面电极层5的厚度为8~38μm,至少包括:4~15μm的铜层、1~8μm的镍层、3~15μm的锡层和0.05~0.5μm的金层。换言之,第一电极层501、第二电极层502和第三电极层503的结构相同。
28.本实施例的一体化封装半导体桥点火器的制备工艺如下:
29.a、封装基体1采用双面覆铜fr4基板或聚酰亚胺基板,采用激光加工工艺在半导体电阻桥芯片3对应位置加工出芯腔,所述芯腔比半导体电阻桥芯片3深10~50μm,芯腔内填充粘合层2后应于半导体电阻桥芯片3高度基本一致;
30.可选的,所述封装基体1可用两层fr4基板或聚酰亚胺基板,所述上层封装基板比半导体电阻桥芯片3厚10~50μm,采用激光加工工艺在半导体电阻桥芯片3对应位置钻出芯腔孔,所述上层封装基板与下层封装基板粘合后形成带芯腔的封装基板;
31.进一步的,所述芯腔应比半导体电阻桥芯片3尺寸稍大以方便贴装,防止芯片在贴装时因偏位或旋转造成芯片的损伤失效;
32.b、将完成芯腔加工的封装基体1采用激光钻孔工艺进行通孔处理,实际生产中可多颗产品串联成阵列排布,分割后形成半孔结构由两颗产品分享,形成连通于所述联通封装基体1上、下表面电极5的半孔结构,所述半孔结构进过金属化处理以便形成完整的电极层,进一步的通孔处理采用激光钻孔,激光钻孔在保证高加工精度同时可以防止薄膜基体变形或卷曲;
33.c、将完成通孔处理带芯腔的封装基体1利用半导体光刻工艺制备出表面电极5图形,进一步的所述表面图形线路缺陷控制《
±
20μm;
34.d、在完成通孔处理带芯腔的封装基体1裸露出的上表面、下表面及半孔结构电极电镀铜、电镀镍和电镀锡或金后形成完整的表面电极层5;
35.e、将上述得到的电镀封装基板经过预清洗,烘干备用,将背面有daf膜(粘合层2)的半导体电阻桥芯片3,通过自动粘片机粘接固定于封装基板的芯腔内;
36.可选的,半导体电阻桥芯片3可以在封装基体1的芯腔内点上环氧等粘接剂(粘合层2)将半导体电阻桥芯片3与封装基板固定在一起;
37.f、连接电极层4采用单面或双面覆铜柔性聚酰亚胺薄膜,采用激光钻孔工艺进行通孔处理,在贴合后半导体电阻桥芯片3的核心发火电阻对应位置钻孔,钻通孔后对孔壁进行修整及非金属化处理,形成芯孔;
38.进一步的,所述芯孔应比半导体电阻桥芯片3的核心发火电阻尺寸稍大,以保证贴装完成后核心发火电阻尺寸刚好位于芯孔中部而不被聚酰亚胺薄膜基体覆盖;
39.g将上述完成非金属化孔处理的柔性聚酰亚胺薄膜采用半导体光刻工艺制备出连接电极图形,进一步的所述连接电极图形线路缺陷控制《
±
20μm;
40.h、在完成连接电极图形蚀刻的柔性聚酰亚胺基板经电镀锡或电镀镍和金后形成完整的连接电极层4;
41.i、通过印刷网版或焊膏点胶机在封装基体1和半导体电阻桥芯片3的对应电极位置印刷一层焊锡膏,将所述连接电极层4利用定位装置覆盖在封装基体1和半导体电阻桥芯片3之上,经过回流焊形成焊接互联,完成后连接电极层4分别与封装基体1的表面电极层5和半导体电阻桥芯片3的电极互联,并且半导体电阻桥芯片3的核心发火电阻位于连接电极层4的芯孔位置中部;
42.j、将所述半成品基板按设计的尺寸要求切割成若干个粒状产品,然后经过清洗、烘干后即得到所述的点火器成品。
43.本实施例不需要引线键合互联结构,也不需要包封结构,封装工艺简单可靠效率高,适合汽车气囊、汽车安全锤、数码电子雷管等中半导体电阻桥对封装的薄型化、标准化表面安装以及低成本、高可靠的要求。