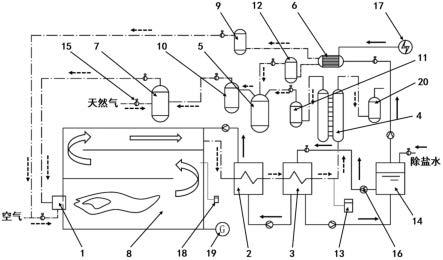
1.本实用新型属于气体燃料低碳低氮清洁发电技术领域,具体涉及一种耦合绿氢制氨的天然气掺氨燃烧系统。
背景技术:[0002]“碳达峰碳中和”背景下,以燃天然气为主的燃气锅炉也面临着极大的节能降碳挑战,当前主流碳中和技术路线除二氧化碳捕集、利用与封存(ccus)外,还可采用“零碳”燃料部分代替含碳燃料来降低整体碳排放水平。另一方面,随着可再生能源装机容量的逐年猛增及大规模储能尚未发展,绿电弃电率也居高不下,如何有效利用弃电亦是亟待解决的问题。
[0003]
氢气分“灰氢”、“蓝氢”和“绿氢”,目前全球化石能源制灰氢占95%以上,但利用可再生能源进行电解水制绿氢正蓬勃发展。相较于氢气,氨气作为氢能的有效载体,其制取工艺非常成熟,加之储运成本低安全性高,可在全生命周期内实现零碳排放,作为“零碳”燃料备受关注。psa碳氮分离装置现可实现烟气变压吸附工艺制取氮气及同步进行二氧化碳捕集。综合现有研究情况看,现有燃气锅炉掺氨燃烧面临掺氨比例小、氮氧化物排放高、整体热效率不够高等问题。因此,如何在实现燃气锅炉最大程度降碳低氮排放的同时进行热质综合循环回收利用,对石油化工园区、煤化工园区以及钢铁、冶金等行业发展绿色循环经济具有深远的意义。
技术实现要素:[0004]
为了克服上述现有技术的不足,本实用新型的目的在于提供了一种耦合绿氢制氨的天然气掺氨燃烧系统,本实用新型能够在实现天然气掺氨富氧降碳低氮燃烧的同时,对烟气的热质进行最大程度的综合回收利用及节水零碳排放,实现能量的梯级利用及物质的有机循环。
[0005]
为达到上述目的,本实用新型采用如下技术方案:
[0006]
一种耦合绿氢制氨的天然气掺氨燃烧系统,包括锅炉、由若干节能器串联而成的节能器组、psa碳氮分离装置、氨合成装置、水电解制氢槽、气体混合罐和氧气缓冲罐,锅炉的燃烧器设置为天然气氨气燃烧器,节能器组设置于锅炉的尾部烟道末端,节能器组中末级的节能器的烟气出口与psa碳氮分离装置的入口连接,psa碳氮分离装置的氮气出口与氨合成装置的氮气入口连接,水电解制氢槽的氢气出口与氨合成装置的氢气入口连接,水电解制氢槽的氧气出口与氧气缓冲罐的入口连接,氧气缓冲罐的出口与空气源连接后共同与天然气氨气燃烧器的助燃风通道连接,氨合成装置的氨气出口与气体混合罐的氨气入口连接,气体混合罐上还设有天然气入口,气体混合罐的混合气出口与天然气氨气燃烧器的燃气通道连接;
[0007]
氨合成装置的氢气入口、氨合成装置的氮气入口、气体混合罐的氨气入口、气体混合罐的天然气入口、气体混合罐的混合气出口、氧气缓冲罐的出口和天然气氨气燃烧器助
燃风通道的入口均设有流量调节阀;
[0008]
水电解制氢槽与绿电连接。
[0009]
优选的,节能器组包括依次串联的一级节能器与二级节能器,二级节能器的烟气出口与psa碳氮分离装置的入口连接。
[0010]
优选的,本实用新型耦合绿氢制氨的天然气掺氨燃烧系统还包括除盐水箱;烟气经二级节能器后温度能够降至水露点以下,所述二级节能器上设有排水口,二级节能器的排水口与除盐水箱连接,除盐水箱还与二级节能器的冷端入口连接,二级节能器的冷端出口与一级节能器的冷端入口连接,一级节能器的冷端出口与锅炉的汽水系统入口连接;二级节能器的排水口与除盐水箱连接的管路上、除盐水箱与二级节能器冷端入口连接的管路上、二级节能器的冷端出口与一级节能器冷端入口连接的管路上以及一级节能器的冷端出口与锅炉汽水系统入口连接的管路上均设有水泵,除盐水箱与二级节能器冷端入口连接的管路上的水泵出口设有流量调节阀。
[0011]
优选的,所述除盐水箱与水电解制氢槽连接,除盐水箱与水电解制氢槽连接的管路上设有水泵,水泵的出口设有流量调节阀。
[0012]
优选的,本实用新型耦合绿氢制氨的天然气掺氨燃烧系统还包括烟气在线分析仪,烟气在线分析仪的测孔布置于二级节能器的烟气出口与psa碳氮分离装置入口连接的管路上。
[0013]
优选的,psa碳氮分离装置的氮气出口与氨合成装置氮气入口连接的管路上设有氮气缓冲罐,氮气缓冲罐的出口设有流量调节阀。
[0014]
优选的,氨合成装置的氨气出口与气体混合罐的氨气入口连接的管路上设有氨缓冲罐,氨缓冲罐的出口设有流量调节阀。
[0015]
优选的,本实用新型耦合绿氢制氨的天然气掺氨燃烧系统还包括烟气温度在线监测仪,烟气温度在线监测仪的测点布置于锅炉的炉膛出口转烟室。
[0016]
优选的,psa碳氮分离装置(4)的氮气出口连接有二氧化碳缓冲罐(20)。
[0017]
本实用新型具有以下有益效果:
[0018]
本实用新型耦合绿氢制氨的天然气掺氨燃烧系统通过配套建设由若干节能器串联而成的节能器组、psa碳氮分离装置、水电解制氢槽制绿氢制氧以及氨合成装置,在燃气锅炉上实现大比例掺烧氨气富氧燃烧的同时进行热质回收利用,实现整体节水零碳排放;本实用新型可通过监控锅炉炉膛出口烟温及尾部烟气组分来动态调节天然气掺氨比例及助燃风富氧量,实现炉内混合气稳定高效低氮燃烧;通过由若干节能器串联而成的节能器组能够将烟温降低至40~50℃;通过psa碳氮分离系统将烟气中的二氧化碳及氮气全部提纯回收,利用绿电进行电解水制氢制氧,氢气与氮气在氨合成装置中进一步合成为氨气并掺入天然气中,电解产生的氧气则作为助燃剂混入空气中。综上所述,本实用新型在实现天然气掺氨富氧降碳低氮燃烧的同时,对烟气的热质进行最大程度的综合回收利用及节水零碳排放,实现能量的梯级利用及物质的有机循环,对石油化工园区、煤化工园区以及钢铁、冶金等高碳行业发展绿色循环经济具有深远的意义。
[0019]
进一步的,通过除盐水箱与节能器组能够在加热锅炉给水的同时并回收烟气中全部冷凝水。
附图说明
[0020]
图1为本实用新型耦合绿氢制氨的天然气掺氨燃烧系统示意图。
[0021]
其中,1为天然气氨气燃烧器,2为一级节能器,3为二级节能器,4为psa碳氮分离装置,5为氨合成装置,6为水电解制氢槽,7为气体混合罐,8为锅炉,9为氧气缓冲罐,10为氨缓冲罐,11为氮气缓冲罐,12为氢气缓冲罐,13为烟气在线分析仪,14为除盐水箱,15为流量调节阀,16为水泵,17为绿电,18为烟气温度在线监测仪,19为发电装置,20为二氧化碳缓冲罐。
具体实施方式
[0022]
下面将参照附图详细地说明本实用新型的实施例。附图描述的实施例仅仅是示例性的,仅仅用于解释此实用新型,而不能解释为对本实用新型的限制。
[0023]
为了提高天然气大比例掺氨炉内燃烧稳定性,实现系统节水零碳排放,本实用新型提出一种耦合绿氢制氨的天然气掺氨燃烧系统,该系统是燃气锅炉进行大比例动态掺烧氨气富氧燃烧及热质回收综合系统,参考图1,本实用新型耦合绿氢制氨的天然气掺氨燃烧系统包括锅炉8、天然气氨气燃烧器1、一级节能器2、二级节能器3、psa碳氮分离装置4、氨合成装置5、水电解制氢槽6、气体混合罐7、氧气缓冲罐9、烟气温度在线监测仪18和烟气在线分析仪13,锅炉8的燃烧器设置为天然气氨气燃烧器1,节能器组设置于锅炉的尾部烟道末端,节能器组包括依次串联的一级节能器2与二级节能器3,烟气经二级节能器3后温度能够降至水露点以下,二级节能器3的烟气出口与psa碳氮分离装置4的入口连接,psa碳氮分离装置4的氮气出口与氨合成装置5的氮气入口连接,psa碳氮分离装置4的二氧化碳出口与二氧化碳缓冲罐20连接,水电解制氢槽6的氢气出口与氨合成装置5的氢气入口连接,水电解制氢槽6的氧气出口与氧气缓冲罐9的入口连接,氧气缓冲罐9的出口与空气源连接后共同与天然气氨气燃烧器1的助燃风通道连接,氨合成装置5的氨气出口与气体混合罐7的氨气入口连接,气体混合罐7上还设有天然气入口,气体混合罐7的混合气出口与天然气氨气燃烧器1的燃气通道连接;二级节能器3上设有排水口,二级节能器3的排水口与除盐水箱14连接,除盐水箱14还与二级节能器3的冷端入口连接,二级节能器3的冷端出口与一级节能器2的冷端入口连接,一级节能器2的冷端出口与锅炉8的汽水系统入口连接;二级节能器3的排水口与除盐水箱14连接的管路上、除盐水箱14与二级节能器3冷端入口连接的管路上、二级节能器3的冷端出口与一级节能器2冷端入口连接的管路上以及一级节能器2的冷端出口与锅炉8汽水系统入口连接的管路上均设有水泵,除盐水箱14与二级节能器3冷端入口连接的管路上的水泵出口设有流量调节阀;除盐水箱14与水电解制氢槽6连接,除盐水箱14与水电解制氢槽6连接的管路上设有水泵,水泵的出口设有流量调节阀;烟气在线分析仪13的测孔布置于二级节能器3的烟气出口与psa碳氮分离装置4入口连接的管路上;烟气温度在线监测仪18的测点布置于锅炉8的炉膛出口转烟室;psa碳氮分离装置4的氮气出口与氨合成装置5氮气入口连接的管路上设有氮气缓冲罐11;氨合成装置5的氨气出口与气体混合罐7的氨气入口连接的管路上设有氨缓冲罐10;氨合成装置5的氢气入口、氨合成装置5的氮气入口、气体混合罐7的氨气入口、气体混合罐7的天然气入口、气体混合罐7的混合气出口、氧气缓冲罐9的出口和天然气氨气燃烧器1助燃风通道的入口均设有流量调节阀15;水电解制氢槽6与绿电17连接。
[0024]
本实用新型耦合绿氢制氨的天然气掺氨燃烧系统在工作时,锅炉尾部烟气依次流经一级节能器2与二级节能器3,逐级换热至烟气温度降低到水露点以下后,全部进入psa碳氮分离装置4,烟气中的水冷凝后自二级节能器3的排水口全部回收利用,经水处理后汇入除盐水箱14。来自除盐水箱14的低温除盐水经由水泵16与流量调节阀15依次流经二级节能器3与一级节能器2,与烟气进行换热后进入锅炉8的汽水系统,在锅炉8受热面中吸热变成蒸汽,进入发电装置19进行发电。psa碳氮分离装置4采用两段法变压吸附,将烟气中的二氧化碳和氮气组分分离提纯,并分别汇入氮气缓冲罐11及二氧化碳缓冲罐20,实现二氧化碳捕集。来自天然气管网的天然气与来自氨缓冲罐10的氨气分别进入气体混合罐7中,混合比例通过各自的流量调节阀15进行调节,混合后的燃料气进入天然气氨气燃烧器1的燃气通道,随后进入锅炉炉膛进行燃烧;来自氧气缓冲罐9的氧气通过流量调节阀15调节流量与空气进行混合,混合后的助燃风通过流量调节阀15调节流量进入天然气氨气燃烧器1的助燃风通道,随后进入锅炉炉膛参与燃烧。烟气温度在线监测仪18的测点布置于锅炉炉膛出口转烟室,实时监测烟气温度;烟气在线分析仪13的测孔布置于二级节能器3后、psa碳氮分离装置4前的烟道,实时监测烟气中的氮氧化物及二氧化碳等组分的浓度。
[0025]
具体的,本实用新型通过天然气氨气燃烧器1在过量空气系数范围为1.05~1.10、助燃风中含氧量范围为21%~30%以及锅炉炉膛出口烟气温度为800~1000℃时,可实现0~80%氨气掺混比例,且尾部烟气中的氮氧化物浓度不高于30mg/nm3。
[0026]
具体的,本实用新型耦合绿氢制氨的天然气掺氨燃烧系统在运行时,天然气锅炉冷态启动时先控制天然气氨气燃烧器1仅投运天然气进行升负荷及炉膛升温,其余设备同步开始运转,待锅炉负荷达到20%以上及炉膛温度升高至650℃以上后,开始逐步提高氨气掺混比例以及助燃风中的氧含量,最终实现天然气掺氨富氧稳定燃烧;天然气锅炉热态启动时,可以直接投运低比例(~10%)混合气;在锅炉运行阶段,蒸汽进入发电装置19进行发电,烟气经二段降温冷凝,全部冷凝水经水处理后汇入除盐水箱14,psa碳氮分离装置4将全部低温烟气中的氮气和二氧化碳进行变压吸附,产生的高纯二氧化碳送入二氧化碳缓冲罐20实现二氧化碳捕集,产生的高纯氮气送入氮气缓冲罐11;与此同时水电解制氢槽6利用绿电17将除盐水电解成氢气汇入氢气缓冲罐11,氧气汇入氧气缓冲罐9;与此同时氨合成装置5利用氢气与氮气在高温高压条件下催化合成氨气汇入氨缓冲罐10;在锅炉变负荷过程或提高燃气掺氨比例过程中,根据烟气在线分析仪13实时反馈的烟气中氮氧化物浓度及氧量等数据,控制流量调节阀15来调整气体混合罐7中的氨气掺混比例,控制流量调节阀15来调整助燃风中的含氧量,协同实现烟气中氮氧化物浓度满足超低排放要求。水电解制氢槽6利用绿电17进行电解制氢,所需除盐水由除盐水箱14提供,电解水量由流量调节阀15控制,电解产生的氢气进入氢气缓冲罐12,产生氧气进入氧气缓冲罐9。
[0027]
以一台50t/h的szs50-1.3/310-q天然气蒸汽锅炉为例,其给水温度为25℃,设计锅炉效率为≮92%,保持锅炉满负荷出力不变条件下,在1.05过量空气系数、30%氧含量下掺烧80%氨气,所需氨气流量约为6200nm3/h,所需电解水流量为9323kg/h(按碱性电解效率80%算),掺入空气中的氧气流量约为928nm3/h,烟气中共可回收冷凝水流量为9973kg/h,减少补水650kg/h。按年运行小时数2500h计算,年可消纳可再生能源产绿电0.93亿度,年可对外供氧气930万标方,年可对外供氮气1494万标方,年可捕集二氧化碳7620吨。较不掺氨年可减少二氧化碳排放12743吨,社会及环保效益显著。
[0028]
本实用新型通过耦合烟气热质回收系统、psa碳氮分离系统、水电解制氢氧系统及氨合成系统,将制得的氨气掺入燃气锅炉中,结合烟气温度在线监测仪18和烟气在线分析仪13实时动态反馈,来达到高的负荷调节性、炉膛及燃料适应性,以实现零碳运行的同时控制氮氧化物排放浓度不超标。在具体实施时,本实用新型为燃气锅炉提供了一种零碳节水的改造技术路线,在大规模消纳可再生能源额定同时提高锅炉效率,减少运行燃料成本。本实用新型所述的耦合绿氢制氨的天然气掺氨燃烧系统在不同的氨气掺混比例下实现了炉内燃烧工况稳定和氮氧化物低排放的动态匹配,同时对烟气的热质进行最大程度的综合回收利用及节水零碳排放,实现能量的梯级利用及物质的有机循环。
[0029]
本实用新型耦合绿氢制氨的天然气掺氨燃烧系统通过配套建设烟气深度热质回收系统、psa碳氮分离系统、水电解制绿氢制氧系统以及氨合成系统,在燃气锅炉上实现大比例掺烧氨气富氧燃烧的同时进行热质回收利用,实现整体节水零碳排放;通过监控炉膛出口烟温及尾部烟气组分来动态调节天然气掺氨比例及助燃风富氧量,实现炉内混合气稳定高效低氮燃烧;通过两级节能器加热锅炉给水的同时将烟温降低至40~50℃,并回收烟气中全部冷凝水;通过psa碳氮分离系统将烟气中的二氧化碳及氮气全部提纯回收,利用绿电进行电解水制氢制氧,氢气与氮气在氨合成子系统中进一步合成为氨气并掺入天然气中,电解产生的氧气则作为助燃剂混入空气中。综上所述,本实用新型在实现天然气掺氨富氧降碳低氮燃烧的同时,对烟气的热质进行最大程度的综合回收利用及节水零碳排放,实现能量的梯级利用及物质的有机循环,对石油化工园区、煤化工园区以及钢铁、冶金等高碳行业发展绿色循环经济具有深远的意义。
[0030]
以上所述仅为本实用新型的较佳实施例而已,并不用以限制本实用新型,凡在本实用新型的精神和原则之内,所作的任何修改、等同替换、改进等,均应包含在本实用新型的保护范围之内。