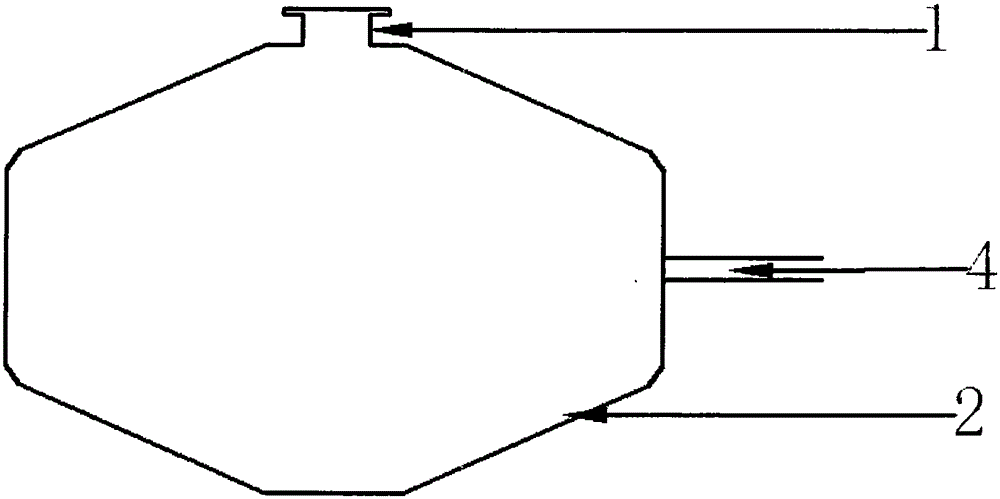
本发明涉及的时一种换热装置,具体是一种烘干设备上用的热管换热散热装置。
背景技术:
现在市场上真空干燥机的换热装置通过向换热装置的夹层内通入蒸汽或者导热油、或者热水进行加热换热的,热量通过换热装置的夹层内壁与湿物料接触,湿物料吸热后蒸发的水汽通过抽气口排出干燥仓。目前干燥仓的夹层换热装置的加热方式只是夹层内壁导热加热,散热面积小,物料的受热面积小,影响物料干燥所需热的接收速度。
本人发明一种热管式换热装置由外壁、内壁、散热立管、抽气口、进料阀门和出料阀门组成,散热立管开口的一端焊接在内壁开的口上,制作有点麻烦。散热立管在工作过程中,由于散热立管的单根独立,散热立管与内壳结合的固定性弱,旋转中物料会给散热立管形成很大的冲击,造成散热立管和内部连接处出现裂纹损伤,影响热管式换热装置的使用寿命。因此需要对散热立管做进一步的改进设计。
技术实现要素:
本发明要解决的问题是克服现有技术存在的不足,在本人申请的热管式换热装置基础上做进一步的改进,现提供一种热管换热散热装置,改散热立管一端开口为两端都开口,变两根散热立管为一根散热立管,加工制作简单,与内壳上下固定的散热立管抗冲击效果更好;增大了散热面积,提高了换热散热速度。
为了到达上述目的,本发明通过下述技术方案实现的:一种热管换热散热装置由外壳、内壳、散热立管、进出料阀门、抽气口和导热介质组成。
所述的热管换热散热装置的外观形状是双锥状的,或者是圆球状,或者是圆柱状。
所述的热管换热散热装置由内壳和外壳组成。
所述的热管换热散热装置的上有一个抽气口。
所述的抽气口通过真空泵等抽气设备,抽取热管换热散热装置内腔腔内的湿气。抽气口安装在热管换热散热装置的适合抽气的位置,抽气口在热管换热散热装置旋转的过程中还可以抽气。
所述的热管换热散热装置的上是有1-3个进出料阀门。
所述的进出料阀门在进出料后可以关闭热管换热散热装置内部,起到密封热管换热散热装置内部的作用。
所述的内壳在外壳的内部。
所述的外壳和内壳制作材质是金属板;金属板的厚度为0.5-8mm。
1、热管换热散热装置的内壳和外壳间的内腔是封闭不漏气的,内壳和外壳间的内腔有导热介质。
2、热管换热散热装置的内壳和外壳的间距是5-150mm。
所述的热管换热散热装置的内壳和外壳的间距内腔内的气压为负压,根据所需不同要求的温度设定不同的负压压力,也需要设计控制内腔内的气化蒸汽饱和度后,添加对应适量的导热介质。
所述的热管换热散热装置的内壳上开有很多和散热立管直径一样的口。
所述的散热立管的两端插在内壳的对应孔口内;将散热立管和内壳的结合位置焊接为一个整体,散热立管和内壳的结合部位牢固不透气。
1、散热立管的两端和外壳和内壳之间的内腔是贯通透气的。
2、散热立管和散热立管的管间距为30-150mm。
所述的散热立管的管是两端开口透气的金属管。
1、散热立管的管直径是5-48mm。
2、散热立管的管壁厚度是0.1-3mm。
所述的散热管是光管,或者是管外面上有翅片。
1、散热立管上的翅片的高度是2-50mm。
2、散热立管上的翅片的厚度是0.1-2mm。
3、散热立管上的翅片与翅片的间距为10-80mm。
4、散热立管上的翅片和管的结合是固定为一体的。
所述的散热立管上的翅片和管的连接形态是纵向状的,或者是环绕状的。
所述的散热立管的管横截面是三角形状,或者是圆形状,或者是方形状。
本发明与现有烘干机的换热装置相比有如下有益效果:一种热管换热散热装置内的导热介质受到热能加热而相变气化,气化的导热介质通过热管换热散热装置的内壁及散热立管的立体散热进行导热散热,立体散热增大了散热面积,提高了热能的散热导热速度,加强了物料干燥效率,达到了快速物料的干燥目的。两头固定在内壳上的散热立管具备搅 拌功能,真空烘干的状态下,湿物料不易结块,有效提高了物料的干燥质量。
附图说明:
图1、为本发明热管换热散热装置的结构示意图;
图2、为本发明热管换热散热装置的外观示意图。
具体实施方式:
下面结合附图和实施例对本发明做进一步的说明。
实施例:
如图1所示的热管式换热装置由外壳(2)、内壳(3)、散热立管(5)、进出料阀门(1)、抽气口(4)和导热介质(6)组成。
所述的热管换热散热装置由内壳(3)和外壳(2)组成。
所述的热管换热散热装置的上有一个抽气口(4)。
所述的热管换热散热装置的上有一个进出料阀门(1)。
所述的内壳(3)在外壳(2)的内部。
所述的外壳(2)、内壳(3)制作材质是金属板,金属板的厚度为1mm。
1、内壳(3)和外壳(2)间的内腔是封闭不漏气的。
2、内壳(3)和外壳(2)置的内腔有导热介质。
3、内壳(3)和外壳(2)的间距是15mm。
所述的热管换热散热装置的内壳(3)和外壳(2)的间距内腔内的气压为负压,根据所需不同要求的温度设定不同的负压压力,也需要设计控制内腔内的气化蒸汽饱和度后,添加对应适量的导热介质(6)。
所述的热管换热散热装置的内壳(3)上开有很多和散热立管(53)直径一样的口。
所述的散热立管(5)的两端插在内壳(3)的对应孔口内。
所述的散热立管(5)和内壳(3)的结合位置焊接为一个整体,散热立管(5)和内壳(3)的结合部位牢固不透气。
1、散热立管(5)的两端和外壳(2)和内壳(3)之间的内腔是贯通透气的。
2、散热立管(5)和散热立管(5)的管间距为80mm。
3、散热立管(5)的管横截面是圆形状。
所述的散热立管(5)的管是两端开口透气的金属管。
1、散热立管(5)的管直径是28mm。
2、散热立管(5)的管壁厚度是1mm。
所述的散热立管(5)是管外面上有翅片。
1、散热立管(5)上的翅片的高度是30mm。
2、散热立管(5)上的翅片的厚度是0.8mm。
3、散热立管(5)上的翅片与翅片的间距为40mm。
4、散热立管(5)上的翅片和管的结合是固定为一体的。
所述的散热立管(5)上的翅片和管的连接形态是环绕状的。
如图2所示的热管式换热装置的外观形状是圆柱形状的。
热管换热散热装置的换热散热工作工艺流程:
1、物料通过热管换热散热装置的进出料阀门(1)进出热管换热散热装置的内部后,关闭进出料阀门(1)。
2、热能给热管换热散热装置的外壁(2)加热;热管式换热装置外壁(2)与内壁(3)间内的导热介质(6)受热后汽化。
3、汽化后后的导热介质(6)通过热管换热散热装置的内壁(3)、散热立管(5)散热、冷凝。
4、冷凝后的导热介质(6)再次吸收到热管换热散热装置的外壁(2)外的热能面汽化,周而复始的进行吸热、散热、冷凝,吸热、散热、冷凝。
5、热管换热散热装置内部的物料,干燥所产生的湿气由抽气口(4)排出热管换热散热装置的仓外。
6、物料烘干后,物料通过热管换热散热装置的进出料阀门(1)排出热管换热散热装置的仓外。
以上实施例只是用于帮助理解本发明的制作方法及其核心思想,具体实施不局限于上述具体的实施方式,本领域的技术人员从上述构思出发,不经过创造性的劳动,所作出的变化,均落在本发明的保护范围。