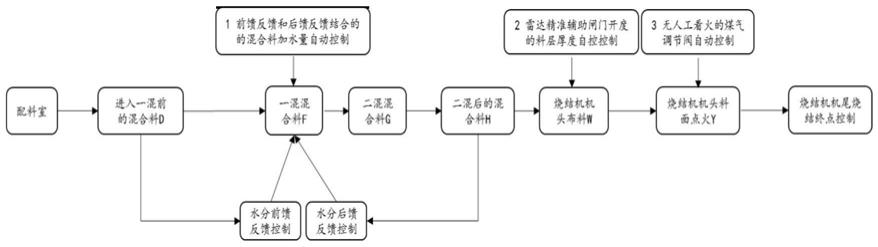
[0001]
本发明属于烧结工艺技术领域,特别涉及一种烧结机烧结终点稳定控制的提产降耗方法。
背景技术:[0002]
现有带式烧结机烧结生产过程中,烧结终点位置的控制直接影响烧结产能和质量。烧结终点位置靠前则导致烧结机的有效面积减少,降低了烧结矿产能和烧结机的利用系数;烧结终点位置靠后则导致台车上的烧结混合料不能完全燃烧,烧结矿质量差。
[0003]
常规的烧结终点位置受到混合料水分、布料厚度、料面点火质量等多因素影响,这些因素的波动范围较大,会导致烧结终点位置控制不准确。传统操作条件下为了规避终点位置偏差引起的烧结矿质量差、高温料损坏后部设备的风险,一般采用烧结机烧结终点位置前移的方法,从而造成产量下降、能耗升高、烧结烟气温度过高等一系列问题。
技术实现要素:[0004]
本发明的目的在于提供一种烧结终点稳定控制的方法,解决了水分波动、料层波动、点火温度波动条件下的烧结终点稳定控制问题。
[0005]
一种烧结终点稳定控制的方法,其特征在于:包括如下步骤,
[0006]
步骤(1),在配料室进行配料,配料完成后的混合料沿皮带进入一混进行混匀,并在一混补充水分值至目标加水量;
[0007]
步骤(2),一混混匀出来的混合料沿皮带进入二混进行混匀,二混混匀出来的混合料在皮带上进行在线水分测量;
[0008]
步骤(3),二混混匀出来的混合料沿皮带到达烧结机机头进行布料,控制料层厚度,使料层厚度按照设定值进行料面布料;
[0009]
步骤(4),布料完成后由点火器点火控制燃烧速度和烧结终点温度;通过流量调节阀自动调节煤气量,从而实现稳定控制烧结终点位置。
[0010]
在一混根据前馈控制得到的混合料水分在线实时调整一混加水量,根据后馈控制得到的水分含量进行一混加水量的微调,通过前馈反馈控制和后馈反馈控制的结合使用,使一混加水量与目标加水量控制在
±
0.2%的波动范围,从而使进入烧结机台车机头的混合料水分波动控制在
±
0.2%的范围。
[0011]
在烧结机机头设有1个主闸门,5个辅助闸门,主闸门和辅助闸门的开度可控制料层厚度,每个闸门对应有一个液压油缸伺服控制闸门开度。烧结机机头位置安装4-6个雷达测厚仪,进行料层厚度的自动测量,雷达测量出料层厚度值,并将测量值与设定目标厚度进行比对,比对结果转化为位移控制信号反馈给油缸,通过油缸位移来控制布料主闸门及辅助闸门的开度,实时在线控制烧结机料层厚度。液压油缸控制精度以丝为单位进行厚度调整,可以精确到目标值
±
5mm。通过雷达测量与液压油缸的高精度智能控制,实现了烧结料层厚度自动控制,降低了对人工经验的依赖。
[0012]
在烧结机机头点火时,设定正常生产时每平方米烧结面积通过的煤气量为煤气通量,以煤气通量为参照标准,依据生产条件及需求变化设定或调整点火时所需的煤气通量,以满足烧结料层的垂直燃烧速度需要。当煤气管网压力波动时,所检测实际煤气流量与煤气通量所需值不符合时,程序将检测比对结果转化为流量调节阀开度调节信号,重新匹配煤气通量条件下所需煤气量,完成自动调节过程。当烧结机速度发生变化时,程序依据点火器下部通过的烧结面积的变化自动计算出当前煤气通量条件下所需的煤气量,经由检测比对结果转化为流量调节阀开度调节信号,重新匹配煤气通量条件下所需煤气量,完成自动调节过程。以此稳定烧结点火温度、保证烧结料面传热及烧结机垂直燃烧速度稳定,从而避免了看火工对烧结点火温度的频繁调整,减少了料面点火的“过烧”和“欠烧”,实现了点火温度的自动调整,实现了稳定控制烧结终点位置的目的。
[0013]
本发明的优点在于:通过烧结混合料水分的自动控制、烧结机料层厚度的自动控制、烧结机点火温度的自动控制,实现了烧结混合料水分波动在
±
0.2%以内、烧结机台车料层厚度偏差
±
5mm以内、避免了看火工对烧结点火温度的频繁调整,实现了烧结终点的稳定控制,从而确保了烧结机烧结终点位置在常规条件下推后两个风箱位置,从而达到烧结机的提产降耗节能的效果。
附图说明
[0014]
图1为烧结终点稳定控制示意图。
[0015]
图2为烧结终点稳定控制实施示例图。
具体实施方式
[0016]
一种烧结终点稳定控制的方法,其特征在于:包括如下步骤,
[0017]
步骤(1),在配料室进行配料,配料完成后的混合料沿皮带进入一混进行混匀,并在一混补充水分值至目标加水量;
[0018]
步骤(2),一混混匀出来的混合料沿皮带进入二混进行混匀,二混混匀出来的混合料在皮带上进行在线水分测量;
[0019]
步骤(3),二混混匀出来的混合料沿皮带到达烧结机机头进行布料,控制料层厚度,使料层厚度按照设定值进行料面布料;
[0020]
步骤(4),布料完成后由点火器点火控制燃烧速度和烧结终点温度;通过流量调节阀自动调节煤气量,从而实现稳定控制烧结终点位置。
[0021]
如图1-2所示,具体步骤及参数如下:
[0022]
设烧结配料室有物料a1、a2、
……
、an,每种物料的配料量分别为b1、b2、
……
、bn,每种物料的水含量分别为c1、c2、
……
、cn。每班对烧结配料室混合料及各物料ai的水分ci进行一次检测。
[0023]
ti时刻,烧结配料室配料完成后的混合料水分di=b1*c1+b2*c2+
……
+bn*cn。
[0024]
按照烧结生产的前后顺序,首先根据烧结配料室配料完成后进入一混前的混合料水分计算值di在线实时调整一混加水量δei,再根据二混后的混合料水分含量在线实测值hj进行一混加水量δej的微调,通过前馈反馈控制和后馈反馈控制的结合使用,使一混混合料水分含量ei与一混混合料水分含量目标值eo控制在
±
0.2%的波动范围。以每班烧结
配料室的水分检测结果bi为基础,以进入一混的混合料水分测算值di为基准初始值,结合实时的各物料配比及对应的各物料配料量bi,测算实时的配料完成后的混合料水分di,以一混水分目标值eo为目标,在线实时计算所需加水量δei=eo-di,实时修正打水管的电动调节阀开度,满足所需水量的配加,结合在线测量水分含量值hj对加水量δej进行微调,完成自动加水过程,解决了检测和调整滞后的问题,保证了混合料目标水分yo的稳定控制,实现了烧结混合料水分加水量由手工控制变为全自动控制,,使进入烧结机台车机头的混合料水分波动控制在
±
0.2%的范围,满足了烧结过程需求。
[0025]
其次在烧结机机头设有1个主闸门,5个辅助闸门,主闸门和辅助闸门的开度可控制料层厚度,每个闸门对应有一个液压油缸伺服控制闸门开度。烧结机机头位置安装4-6个雷达测厚仪,进行料层厚度的自动测量,雷达测量出料层厚度值,并将测量值wi与料层设定目标厚度wo进行比对,将比对结果δw1(δw1=wo-wi)转化为液压油缸位移量δw2反馈给油缸,通过油缸位移来控制布料主闸门及辅助闸门的开度,实时在线控制烧结机料层厚度。液压油缸控制精度以丝为单位进行厚度调整,可以精确到目标值
±
5mm。通过雷达测量与液压油缸的高精度智能控制,实现了烧结料层厚度自动控制,降低了对人工经验的依赖。
[0026]
再次在烧结机机头点火时,设定正常生产时每平方米烧结面积通过的煤气量为煤气通量yo,其对应的煤气调节阀开度为zo,以煤气通量yo为参照标准,依据生产条件变化时,实时的煤气通量yi与煤气通量yo比较,将比对结果δy(δy=(yo-yi)/yo)反馈给煤气调节阀,实时调整煤气调节阀开度zi,使煤气通量对比值δy≤
±
5%。当煤气管网压力波动时,所检测实际煤气流量yi与煤气通量所需值yo不符合时,程序将检测比对结果δy转化为流量调节阀开度调节信号,重新匹配煤气通量条件下所需煤气量,完成自动调节过程。当烧结机速度发生变化时,程序依据点火器下部通过的烧结面积的变化自动计算出当前生产条件下所需的煤气通量yo,经由比对结果δy转化为流量调节阀开度调节信号,重新匹配煤气通量yi条件下所需煤气量,完成自动调节过程。以此稳定烧结点火温度、保证烧结料面传热及烧结机垂直燃烧速度稳定,从而避免了看火工对烧结点火温度的频繁调整,减少了料面点火的“过烧”和“欠烧”,实现了点火温度的自动调整,实现了稳定控制烧结终点位置的目的。