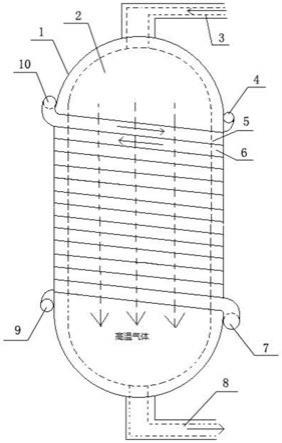
[0001]
本发明涉及工业换热设备技术领域,具体涉及一种螺旋缠绕管式锥形内凸胞换热器。
背景技术:[0002]
换热器由于其结构坚固、使用弹性大、适应性强等特点在化工、石油、电力等方面应用广泛,随着微电子、医疗、航空航天等方面的特殊要求而向小型化发展,其在设计方法、结构形式、材料参数等方面均有很大的上升空间。现阶段对于列管式换热器的研究多从管内对流换热强化入手,其机理主要是:在进行换热时,热阻主要集中在边界层,强化换热的关键是要减薄或破坏边界层,达到强化换热的目的。
[0003]
缠绕管式换热器是一种特殊的管壳式换热器,是20世纪初在管壳式换热器的基础上发展起来的高效换热结构。缠绕管式换热器结构紧凑、整体换热系数高、承压能力较强,广泛应用于lng、重烷烃液化分离以及液氮洗等装置中。近年来,由于缠绕管式换热器的良好换热性能,在石油化工等行业的应用愈加广泛,对其传热特性的研究获得了更多学者关注。如何进一步改善管程和壳程的换热性能,以获得更紧凑的结构;如何进一步创新换热器结构,以适应越来越多工业领域的应用;以及进一步优化新型换热器传热的计算模型,均是换热器传热研究的重要内容。
技术实现要素:[0004]
针对现有技术存在的上述技术问题,本申请的目的在于提供一种螺旋缠绕管式锥形内凸胞换热器。
[0005]
本发明的技术方案如下:一种螺旋缠绕管式锥形内凸胞换热器,其特征在于,包括壳体、芯管及缠绕管束,所述芯管设置在壳体中心位置处,且芯管一端设有尾气进口,另一端设有尾气出口,所述缠绕管束沿轴向螺旋缠绕在芯管的外壁上,所述缠绕管束设有两根,包括换热管一及换热管二,所述换热管一及换热管二的内壁沿水流方向设有锥形凸胞,从而提高换热效果。
[0006]
所述的一种螺旋缠绕管式锥形内凸胞换热器,其特征在于,所述换热管一与换热管二呈螺旋对向并管绕制在芯管的外壁上。
[0007]
所述的一种螺旋缠绕管式锥形内凸胞换热器,其特征在于,所述换热管一上两端分别设有进水口一、出水口一,且进水口一位于芯管上端,出水口一位于芯管下端;所述换热管二两端分别设有进水口二、出水口二,且进水口二位于芯管下端,出水口二位于芯管上端。
[0008]
所述的一种螺旋缠绕管式锥形内凸胞换热器,其特征在于,所述换热管一及换热管二内的锥形凸胞设置在管件内壁的相对两侧,且采用对排或错排分布设置。
[0009]
本发明的有益效果是:1)换热器中缠绕管采用螺旋结构,有利于湍流发展,并能产生强烈的二次环流,强化了
管内换热效率;壳程换热空间结构较复杂,流体冲刷螺旋管束进行换热,由于相邻缠绕管网之间缠绕方式相反,增强了壳程流体的扰动,而且与管内流体构成叉流换热方式,有效增大冷热源间的传热温差。
[0010]
2)换热器中缠绕管内壁设置锥形内凸胞结构结合,大大增加了换热量和换热效率。
[0011]
3)缠绕式换热器的设计不仅能够有效降低能耗,而且还能够有效降低装置的占据空间。
附图说明
[0012]
图1为本发明缠绕式换热器示意图;图2为本发明凸胞换热管几何模型示意图;图3为本发明对排凸胞换热管示意图;图4为本发明错排凸胞换热管示意图;图5为本发明nu在不同re下随无量纲半径i的变化;图6为本发明pec指数在不同re下随无量纲半径i的变化;图7为本发明nu在不同re下随着节距p的变化;图8为本发明pec指数在不同re下随节距p的变化曲线;图9为本申请不同排布方式对平均nu的影响关系图;图中:1-壳体,2-芯管,3-尾气进口,4-出水口二,5-换热管一,6-换热管二,7-出水口,8-尾气出口,9-进水口二,10-进水口一,11-锥形凸胞。
具体实施方式
[0013]
以下结合说明书附图,对本发明作进一步描述。
[0014]
如图1-9所示,一种螺旋缠绕管式锥形内凸胞换热器,包括壳体1、芯管2、尾气进口3、出水口二4、换热管一5、换热管二6、出水口7、尾气出口8、进水口二9、进水口一10及锥形凸胞11。
[0015]
实施例:芯管2设置在壳体1内部中心位置处,且芯管2一端设有尾气进口3,另一端设有尾气出口8,芯管2的外壁上沿轴向螺旋缠绕设置缠绕管束,缠绕管束设有两根,包括换热管一5及换热管二6,换热管一5与换热管二6呈螺旋对向并管绕制在芯管2的外壁上,所述换热管一5及换热管二6的内壁沿水流方向设有锥形凸胞11。
[0016]
换热管一5上两端分别设有进水口一10、出水口一7,且进水口一10位于芯管2上端,出水口7一位于芯管2下端;所述换热管二6两端分别设有进水口二9、出水口二4,且进水口二9位于芯管2下端,出水口二4位于芯管2上端。
[0017]
换热管一5及换热管二6内的锥形凸胞11设置在管件内壁的相对两侧,且采用对排或错排分布设置。
[0018]
性能实验:取实际工程中换热管的5个周期作为研究对象,采用锥形凸胞换热管,换热管长度为400 mm,换热管半径r为10mm,壁厚为2 mm,凸胞直径d=2r,r为凸胞深度(mm);同侧凸胞节距
为p,为了使管内流体充分发展,在进出口分别接了80 mm的圆直管,定义无量纲半径i=r/r,通过改变无量纲半径i、凸胞节距p对换热特性进行分析,并且有两种排列方式:对排和错排。
[0019]
选取工业环境中边界条件:以水为工质,入口采用速度入口,速度值为0.48 m/s,入口温度为353.15 k,壁面设置为恒壁温273.15 k,出口为压力出口。并且流体介质重力忽略不计;将流体视为牛顿流体,不可压缩,且流体物性参数为常数;换热管入口处截面的流体速度、温度均匀。锥形凸胞的存在提高换热性能的同时,也会相应地引起流动阻力的增加,因此采用pec 指数来综合考虑换热性能和流动阻力。
[0020]
式中:nu—凸胞管的努塞尔数;nu0—光滑管的努塞尔数;f—凸胞管的摩擦阻力系数;f0—光滑管的摩擦阻力系数。
[0021]
图5是在re为13 136~52 544的范围内,不同无量纲尺寸i对平均努塞尔数nu的影响。
[0022]
由图5可知,凸胞管的换热特性明显大于光滑管,其换热特性随着无量纲尺寸的增加而增加,较光滑管相比最少提高15%。无量纲半径i为0.1、0.2时,换热性能相差不大,换热性能从无量纲半径i=0.3之后增加的幅度较明显。无量纲半径i一定时,换热性能随着雷诺数的增加而增加,但增加的幅度逐渐减小。这种现象说明当re数较小时,凸胞管的换热性能较光滑管更优,同时结合pec来进行比较,图6为pec指数在不同re下随无量纲半径i的变化曲线。由图6可知,在re一定时,pec随无量纲半径i的增大而减小,且减小的趋势越来越大。凸胞管i=0.1~0.6时,其综合性能优于光滑管,当i=0.2,re=17 514时,pec值达到最大,最大值为1.246,其综合换热性能最佳;无量纲半径i大于0.6之后,其相较光滑管的优势逐渐消失,甚至差于光滑管,此时的凸胞管无量纲半径i已不适用于强化换热,这是因为随着无量纲半径i的增加,流动阻力的增加起主要作用。所以最终确定无量纲半径为0.2。
[0023]
再来考虑节距p,图7为nu在不同re下随节距p的变化曲线。由图7可知,nu受凸胞节距p的影响较弱,在同一re下,其随着节距p的增加而逐渐减小,这是因为凸胞之间的距离加大,上一个凸胞产生的扰动作用不能有效地延续到下一个凸胞,且这种扰动作用逐渐减弱,甚至消失,因此换热性能下降;当凸胞节距p相同时,nu随着re的增加而增加,这是因为随着re的增加,流体的湍流程度增大,对边界层的破坏作用加大,从而提高了换热性能。
[0024]
同时结合pec来进行比较,图8为pec指数在不同re下随节距p的变化曲线。由于pec值随re整体变化规律不显著,故本图仅展示了变化规律较明显的几个re值。由图可知,同一节距时,pec随re的增大而减小,可见其湍流程度增大引起阻力增大的幅度大于换热性能增加的幅度。re相同时,随着节距的增大,其流动阻力呈现减小的趋势,pec值依然随节距的增大而减小,说明传热性能比流动阻力减小得更快。综上所述结合经济成本因素选择节距p为30mm。
[0025]
最后根据排列方式不同,图9是研究的re范围内,无量纲半径i=0.2、节距p=30 mm时,对排、错排两种排列方式对平均nu、f的影响。由图7可知,两种排列方式的平均努塞尔数
nu非常接近,最多相差1.19%;对排的平均摩擦系数f比错排略大,最大不超过1.65%。因此,就综合换热型能而言,错排与对排在实际使用中并无较大区别,这也就为实际使用中提供的更大的选择空间。