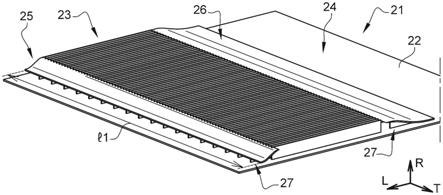
1.本发明涉及航空学的一般领域。本本发明特别针对用于涡轮机的热交换系统。
背景技术:2.涡轮机,特别是飞行器的涡轮机,包括需要润滑和/或冷却的不同构件和/或设备,例如,滚动轴承和齿轮。根据构件和/或设备的功率,这些部件释放的热量可能非常高,热量通过流体传输并且排向飞行器中可用的冷源。
3.已知为涡轮机配备有一个或多个热交换系统以在润滑流体(通常是油)和冷源(空气、燃料等)之间进行热交换。甚至存在不同类型的热交换系统,例如,燃料/油热交换器,一般以缩写fcoc(fuel cooled oil cooler,燃料冷却油冷却器)被知晓;以及空气/油热交换器,以缩写acoc(air
‑
cooled oil cooler,空气冷却油冷却器)被知晓。热交换器的示例从文献ep
‑
a2
‑
1916399、cn
‑
a
‑
109210961、wo
‑
a1
‑
2008/025136和us
‑
a
‑
4254618中获知。
4.fcoc热交换器具有双重功能,即,在涡轮机的燃烧室燃烧之前加热燃料,并且冷却被涡轮机的散热所加热的油。然而,fcoc热交换器不足以吸收所有的散热,因为出于安全原因,燃料的温度是有限的。
5.额外的冷却是通过acoc热交换器获得的,特别是那些已知被缩写为sacoc的表面类型的热交换器。表面热交换器通常位于涡轮机的次级通路中,并且利用次级气流冷却在涡轮机中流通的油。这些热交换器采用金属表面件的形式,使得油能够在通道中流过。次级气流沿着由该表面件承载的翅片被引导,并且翅片具有增加与次级气流的接触面和提取热量的作用。然而,sacoc热交换器的缺点是,因为sacoc热交换器扰乱了气流,所以它们在相关的次级通路中产生额外的压力损耗,从而影响涡轮机的性能以及特定的燃料消耗。
6.sacoc热交换器的气动热性能(热功率耗散与次级气流侧引起的压力损耗之比)较低。
7.此外,由于更高的转速以及满足涡轮机的规格趋势的功率要求,对润滑液的冷却要求也在增加。
技术实现要素:8.本发明的目的是提供一种热交换系统,该热交换系统使得能够通过控制穿过系统的气流的流量来优化热交换效率,同时避免压力损耗并且提高了稳健性。
9.根据本发明,这是通过用于涡轮机的热交换系统实现的,热交换系统包括热交换器,热交换器包括支撑壁和多个翅片,支撑壁大体沿着纵向方向l延伸,每个翅片从支撑壁的径向外表面沿着径向方向延伸并且旨在被气流扫过,热交换器包括第一成型壁和第二成型壁,第一成型壁布置在翅片的上游,并且被构造为引导和减慢穿过翅片进入热交换器的气流,第二成型壁布置在翅片的下游,并且被构造为使离开热交换器的气流加速,每个第一和第二成型壁通过从径向外表面径向延伸的支撑元件附接到支撑壁。
10.因此,该解决方案使得能够实现上述目的。具体地,通过改变热交换器中的流动条
件,确保了具有最佳气动热性能的散热,这有助于降低压力损耗。事实上,当这种热交换系统安装在涡轮机中,并且特别是安装在次级通路中时,次级气流的流动非常湍急,这对应于降低了热交换器的气动热性能的高流动雷诺数。在起飞和巡航时,流速达到大约0.6马赫值。通过在入口处和出口处增加成型壁来减慢穿过交换器的气流的速度,使得能够优化热交换器的气动热性能,从而最小化给定散热的压力损耗。此外,第一成型壁和第二成型壁使得能够更好地控制和提高绕过翅片的交换器的部分气流(即,不穿过翅片的部分气流)的空气动力学特性。此外,这些第一和第二成型壁通过支撑元件附接到热交换器,支撑元件提供了更好的组装机械强度,并且可用于以给定的回转使气流的流动变直。
11.热交换器系统还包括以下特征中的一个或多个特征,这些特征可以单独使用或彼此组合使用:
12.‑
第一成型壁包括第一壁部分,第一壁部分与支撑壁形成具有第一径向高度的空气入口,以及第二成型壁包括第一壁部分,第二成型壁的第一壁部分与支撑壁形成具有第二径向高度的空气出口,第一高度与第二高度之间的比值介于0.5至1之间。
13.‑
热交换器包括覆盖翅片的成型面板,成型面板在第一壁和第二壁之间沿着纵向方向延伸,成型面板附接到第一壁和第二壁。
14.‑
成型面板大体是平坦的或弯曲的。
15.‑
成型面板从径向外表面以最大径向距离延伸,该最大径向距离大于第一成型壁和第二成型壁分别的第一高度和第二高度。
16.‑
交换系统包括流体流通回路,流体流通回路中流通的流体旨在冷却和/或润滑涡轮机的构件和/或设备,流体流通回路包括第一管道和第二管道,第一管道布置在支撑壁中,第二管道布置在成型面板中。
17.‑
流体流通回路包括将第一管道和第二管道彼此连接的两个通道。
18.‑
热交换器包括盖子,盖子径向布置在成型面板的外侧。
19.‑
盖子具有外周表面,外周表面与第一成型壁和第二成型壁的径向外表面具有表面连续性。
20.‑
盖子包括第一部分,盖子的第一部分限定在倾斜平面中,该倾斜平面与限定支撑壁的径向外表面的平面形成预定角度。
21.‑
成型盖子具有第二壁部分,第二壁部分是曲线的并且布置在第一部分的上游。
22.‑
第二曲线壁部分具有曲率半径。
23.‑
曲率半径是成型面板沿着与径向方向垂直的纵向方向的长度的函数,成型面板的长度与曲率半径之间的比值介于0.5mm至1.5mm之间。
24.‑
翅片各自沿着纵向方向是连续且直线的,或是不连续的并且以交错的方式布置或是波纹状的。
25.‑
至少一个翅片沿着径向方向具有不同的高度,并且该高度发生变化以符合盖子的轮廓。
26.‑
翅片包括沿着与径向方向垂直的横向方向布置在径向外表面上的第一类型的翅片和第二类型的翅片,第一类型的翅片中的每个翅片在支撑壁和盖子之间径向延伸,并且每个翅片附接到盖子,以便在它们的整个径向高度上支承盖子。
27.‑
翅片被横向地布置,使得每三个翅片有一个第一类型的翅片。
28.‑
第一类型的翅片具有径向高度小于或等于盖子的高度的中心部分。
29.‑
热交换器由增材制造制成。
30.‑
面板与第一成型壁和第二成型壁制成一体件。
31.‑
盖子和面板制成一体件。
32.‑
翅片附接到面板。
33.‑
翅片与面板制成一体件。
34.‑
热交换系统旨在布置在涡轮机的次级通路中。
35.‑
热交换器是空气/流体类型的热交换器,并且优选地是表面热交换器。
36.‑
流体是润滑油。
37.‑
支撑元件布置在与纵向方向垂直的横向方向上并且在与纵向方向垂直的横向方向上均匀分布。
38.本发明还涉及一种具有纵向轴线x的用于涡轮机的模块,该模块包括围绕纵向轴线的环形壳体和具有任何前述特征的热交换系统,气流在环形壳体中流通,热交换系统布置在环形壳体中,环形壳体包括环形壁,环形壁至少部分地引导气流,并且环形壁具有开口或凹部,在开口或凹部中安装有具有成型面板的热交换器,第一壁在成型面板的上游连接到环形壁的一部分,并且第二壁在成型面板的下游连接到环形壁的一部分。
39.热交换器嵌入在环形壳体的壁中。
40.本发明进一步涉及一种涡轮机,该涡轮机包括至少一个具有前述任何特征的热交换系统和/或如上所述的涡轮机模块。
附图说明
41.通过参照附图阅读以下以仅说明性和非限制性示例的方式给出的本发明的实施例的详细解释性描述,本发明将被更好地理解,并且本发明的其他目的、细节、特征和优点将变得明显,在附图中:
42.[图1]图1是本发明所应用的涡轮机的示例的轴向横截面视图;
[0043]
[图2]图2是根据本发明的旨在装备涡轮机的热交换系统的透视图和局部视图;
[0044]
[图3]图3是根据本发明的热交换系统的示例的轴向截面示意图;
[0045]
[图4]图4是根据本发明的热交换系统的实施例的透视图;
[0046]
[图5]图5示意性地示出了图4所示的热交换系统的变型的轴向横截面视图;
[0047]
[图6]图6是根据图4的热交换系统的另一实施例的透视图;
[0048]
[图7]图7表示根据本发明的具有流体管道的热交换系统的示例,该流体管道布置在覆盖翅片的壁中的一个壁中;
[0049]
[图8]图8根据透视图和剖视图示出了根据本发明的与流体流通回路配合的热交换系统的热交换器的翅片布置的示例;
[0050]
[图9]图9示出了根据本发明的具有盖子的热交换系统的另一实施例的透视图;
[0051]
[图10]图10是根据图9的实施例的轴向横截面视图;
[0052]
[图11]图11是具有热交换器的热交换系统的另一实施例的示意性侧视图,该热交换器的翅片具有不同的高度;
[0053]
[图12]图12示出了根据本发明的交换系统的热交换器的另一实施例的透视图和
局部视图,该热交换器包括覆盖翅片的盖子;
[0054]
[图13]图13是根据本发明的没有盖子的图12的热交换器的透视图;
[0055]
[图14]图14是根据本发明的另一实施例的轴向截面示意图,其中,热交换器嵌入在涡轮机的壁中;
[0056]
[图15]图15是根据本发明的嵌入在涡轮机的壁中的热交换器的另一实施例的另一轴向截面示意图;
[0057]
[图16]图16是根据本发明的嵌入在涡轮机的壁中的热交换器的另一实施例的轴向截面示意图;以及
[0058]
[图17]图17是根据本发明的嵌入在涡轮机的壁中的热交换器的另一实施例的示意性轴向横截面视图。
具体实施方式
[0059]
图1示出了本发明所应用的具有纵向轴线x的涡轮机的轴向横截面视图。所示的涡轮机是旨在安装在飞行器上的双流式涡轮机1。当然,本发明不限于该类型的涡轮机。
[0060]
该双流式涡轮机1通常包括气体发生器2,气体发生器2的上游安装有风扇或风扇模块3。
[0061]
在本发明中,术语“上游”和“下游”是相对于涡轮机中的气体流动而定义的,在此是沿着纵向轴线x。
[0062]
气体发生器2包括气体压缩机组件(在此包括低压压缩机4a和高压压缩机4b)、燃烧室5和涡轮组件(在此包括高压涡轮6a和低压涡轮6b)。通常,涡轮机包括低压轴7和高压轴8,低压轴连接低压压缩机和低压涡轮以形成低压本体,高压轴连接高压压缩机和高压涡轮以形成高压本体。以纵向轴线为中心的低压轴7在此通过齿轮箱10驱动风扇轴9。旋转导向轴承15还使得能够引导低压轴7相对于涡轮机的固定结构旋转。
[0063]
风扇3由风扇壳体11覆盖,风扇壳体由发动机舱12承载,并且风扇产生主气流和次级气流,主气流在主通路v1中流通穿过气体发生器2,次级气流围绕气体发生器2在次级通路v2中流通。次级气流由终止发动机舱的次级喷嘴13喷射,而主气流通过位于气体发生器2下游的喷射喷嘴14喷射到涡轮机外部。在下文的描述中,风扇壳体和发动机舱被视为一体件。
[0064]
在涡轮机构造的该示例中,导向轴承15和减速器10必须被润滑和/或冷却,以确保涡轮机的性能。由导向轴承和减速器产生的功率在来自安装在涡轮机中的流体供应源的流体中耗散,并且这使得能够润滑和/或冷却涡轮机的不同构件和/或设备。当然,涡轮机的其他设备产生了大量热量,必须从其环境中提取这些热量。
[0065]
为此,涡轮机包括热交换系统20,热交换系统使得能够对旨在润滑和/或冷却这些构件和/或设备的流体进行冷却。在本示例中,流体是油,并且旨在冷却油的冷源是在涡轮机中流通的气流,特别是次级气流。
[0066]
热交换系统包括热交换器21,热交换器21布置在涡轮机的风扇壳体中,如图1所示。热交换器为空气/油表面类型的热交换器。
[0067]
参照图2,热交换器21包括支撑壁22,支撑壁沿着纵向方向l延伸。支撑壁在此大体平坦地延伸。该壁可以不是完全平坦的,而是弯曲的,以遵循风扇壳体的壁的轮廓,风扇壳
体的壁的轮廓旨在承载热交换器并且大体是(纵向轴线x的)圆筒形。热交换器可以占据风扇壳体的整个壁,或者可以布置在风扇壳体的部分上。
[0068]
热交换器21还包括多个翅片23,每个翅片在此沿着径向方向r从支撑壁22的径向外表面24升高。我们特别使用术语“方向”来描述热交换器。这些翅片旨在被进入风扇壳体11的次级气流扫过。
[0069]
如图2所示,翅片23是直的,并且每个翅片都在纵向方向l(特别是在热交换器中平行于涡轮机中气流的流通或流动)上延伸。在安装情况下,纵向方向平行于纵向轴线。更准确地,每个翅片都是平坦的。翅片沿着与纵向方向l垂直的横向方向t连续且规则地布置在径向外表面上。翅片仍然大体彼此平行。每个翅片具有沿着气流方向彼此相对的前缘ba和后缘bf(见图3)。替代地,翅片可以是不连续的,并且在径向方向或纵向方向上以交错的方式和/或波纹状地布置。
[0070]
在图2和图3中,热交换器21包括第一成型壁25,第一成型壁布置在翅片的上游(沿着径向外表面的气流的方向),第一成型壁被构造为指引和引导进入热交换器的流。第一壁25还被构造为减慢进入热交换器的气流。第一壁具有不同的轮廓。第一壁25延伸的距离l1至少等于翅片所布置的距离。具体地,第一成型壁25的宽度l1大于翅片(在横向方向t上)所布置在其上的宽度。
[0071]
热交换器21还设置有第二成型壁26,第二成型壁布置在翅片的下游,以减少翅片的下游发生的再流通现象。第二成型壁还被构造为加速热交换器的出口处的流动。
[0072]
具体地,在图3中,每个第一成型壁25和第二成型壁26在与支撑壁22的平面lt垂直的平面rl(由竖直的纵向方向l和径向方向r形成)中具有大体波纹或弯曲的形状。更具体地,第一壁25包括上游的第一壁部分25a,第一壁部分25a与支撑壁22形成空气入口,空气入口沿着径向方向具有第一预定高度he。第一高度he小于翅片的径向高度hi。第一壁25包括第二壁部分25b(在第一壁部分25a的下游),第二壁部分25b(沿着纵向方向l)覆盖翅片的至少一部分。根据图3,壁部分25b延伸过重叠距离re,以便更好地控制和提高径向穿过翅片23上方(外侧)的气流的空气动力学特性。该第二壁部分25覆盖沿着横向方向t排列的所有翅片23的前缘ba。
[0073]
第二壁26具有与第一壁25大体相同的构型。然而,第二壁有收敛的轮廓。第二壁的宽度l1与第一壁25的宽度相同。第二壁26还包括下游壁部分26a,下游壁部分26a与支撑壁22形成空气出口,空气出口沿着径向方向具有第二预定高度hs。第二高度hs小于翅片的高度hi。
[0074]
在本实施例中,第一高度he和第二高度hs之间的比值介于0.5到1之间。
[0075]
类似地,第二壁26包括第二壁部分26b,第二壁部分(沿着纵向方向l)覆盖翅片的至少一部分。第二壁部分26b延伸过重叠距离rs,这是出于控制和提高穿过热交换器的气流的空气动力学特性的相同目的。该第二壁部分25覆盖沿着横向方向t排列的所有翅片23的后缘bf。
[0076]
参照图3,热交换器21包括多个支撑元件27,多个支撑元件使得能够将翅片附接到支撑壁22。换句话说,支撑元件27从支撑壁22的径向外表面24沿着径向方向延伸。支撑元件27分别沿着第一壁25和第二壁26均匀分布。这些确保了第一壁和第二壁的更好的机械强度。
[0077]
根据替代实施例,支撑元件27被构造为使穿过第一成型壁进入热交换器的气流变直。在本示例中,每个支撑元件27分别附接到第一壁和第二壁的中心壁部分25c、26c。中心壁部分25c、26c各自具有相对于纵向方向的倾斜度。为此,每个支撑元件27在此具有梯形形状。
[0078]
布置在热交换器入口处的支撑元件27可能比翅片23更厚,以便使支撑壁22上的第一壁25具有更好的机械强度。事实上,由于上游气流的流动旋转以及通过这些相同的支撑元件使气流变直,局部施加的力可能更重要。此外,这些较厚的支撑元件27沿着横向方向被进一步间隔开,以减少热交换不是最佳的该区域(较高的流速)中的相关压力损耗。
[0079]
替代地,支撑元件27和翅片23具有相同的厚度。
[0080]
图4和图5示出了本发明的另一实施例。与前述实施例相同的元件由相同的附图标记表示。如图所示,热交换器21包括成型面板28,成型面板覆盖翅片23,以便控制气流在热交换器内流动而没有气流绕过热交换器的风险。因此,翅片23径向布置在支撑壁22和成型面板28之间。进入次级通路v2的气流被分离成绕过热交换器的气流部分f1和穿过翅片的气流部分f2。
[0081]
在该示例实施例中,面板28在第一壁25和第二壁26之间沿着纵向方向l延伸,并且还与第一壁25和第二壁26具有相同的宽度。面板28大体是圆形或弯曲的(安装在涡轮机中时,围绕纵向轴线x)。具体地,面板包括第一纵向边缘28a和第二纵向边缘28b(图6),第一纵向边缘连接第一成型壁的第一纵向端部25d,第二纵向边缘连接第二壁26的第一端部26d。如图5所示,面板28的外周表面29与第一壁25和第二壁26的径向外表面42、43具有表面连续性。
[0082]
有利地,壁25、26和面板28例如通过增材制造方法(例如,粉末床激光融熔方法)(或3d打印)被制成一体件。
[0083]
面板28所延伸的径向距离等于或大于翅片23的径向距离。换句话说,该径向距离大于第一壁25的第一高度he和第二壁26的第二高度hs。有利地但非限制性地,翅片例如通过钎焊附接到面板28和/或支撑壁22。替代地,翅片23和支撑壁22形成为一体件(即,由一种材料一体成形),并且有利地通过增材制造形成。类似地,翅片和面板28可以制成一体件。沿着图5所示的方向fa,从热交换器的上游到下游进行增材制造。在这种情况下,为了便于增材制造,并且特别是在没有支撑的情况下,翅片23的前缘ba与径向方向具有角度α。
[0084]
当然,热交换器整体可以通过其他制造方法(例如,锻造)来制造。
[0085]
此外,将面板28布置在翅片上的事实使得能够提高热交换器的机械强度,从而减小翅片23的厚度。然而,翅片23的厚度减小也使得能够减少热交换器21的质量。
[0086]
类似地,在有支撑元件27的情况下,支撑元件比翅片厚并且沿着横向方向t在支撑元件和翅片之间布置有具有较大间隙,这些支撑元件可以在气流的流动出口区域中用作面板28的支撑件。
[0087]
根据图6所示的、前述实施例的替代,热交换器21具有多个翅片23,多个翅片以交错的方式布置在支撑壁23的径向外表面24上,并且沿着气流f的流动方向布置。在纵向方向的方向和横向方向的方向t上具有多排翅片23。与前述实施例一样,翅片被中心成型面板28覆盖,中心成型面板通过第一壁25向上游延伸,并且通过第二壁26向下游延伸。以这种方式布置的翅片使得能够通过中断和重建热边界层来加强,这使得能够显著减小用于给定耗散
功率的交换表面或增加在给定面积内可以耗散的功率。
[0088]
根据图7至图9所示的另一实施例,热交换系统包括流体流通回路,旨在冷却和/或润滑涡轮机的构件和/或设备的流体在流体流通回路中流通。通常,使用油的流体流通回路一方面连接到供应源(例如,储液器),另一方面连接到一个或多个泵,一个或多个泵被设计为促进向构件和/或设备输送油。
[0089]
在本示例中,流体流通回路包括第一管道30,第一管道30布置在支撑壁22中并且位于支撑壁的径向内表面侧。该径向内表面与径向外表面24径向相对。第一管道30具有进油口和出油口(未示出)。此外,第一管道30呈各自沿着横向方向延伸并相互平行的第一管路31a和第二管路31b的形式。第一管路31a包括进油口,而第二管路31b包括出油口,进油口和出油口彼此相邻放置。
[0090]
流体流通回路还包括第二管道32,第二管道布置在成型面板28的壁中。换句话说,油沿着径向方向在翅片的两侧流通,这使得能够增加对流交换,并且因此增加从热流体(在此是油)到冷源(次级通路中的气流)的功率耗散。有利地,第二管道32是中空的或者形成在材料中。如图7所示,面板包括双壁,我们称之为第一隔板和第二隔板,双壁彼此径向间隔开,然后形成第二管道32。第二管道具有呈u形形状的横截面(在平面lt中),u形形状的横截面大体占据面板28的整个区域。沿着横向方向延伸的股线33径向上升到管道32中以形成u的两个分支。股线33的宽度小于面板28本身的宽度(沿着横向方向t)。
[0091]
在图8中,流体流通回路进一步包括两个通道34a、34b,两个通道将第一管道30和第二管道32彼此连接。通道34a、34b径向布置在支撑件22的壁和面板28之间。第一通道34a在两侧(在端部35的水平处)通向第一管路31a并且(在u分支的第一尖端36的水平处)通向第二管道。至于第二通道31b,也在两侧(在端部37的水平处)通向第二管路31b并且(在u分支的第二尖端38的水平处)通向第二管道。
[0092]
有利地,通道34a、34b形成在将面板28与支撑壁22连接的隔板39中。这样,“热”油穿过第一管路31a的入口进入,通过第一通道34a进入第二管道32,围绕第二管道流通,然后穿过第二通道34b在第二管路31b中流通,并且最后作为“冷”油穿过出油口流出。因此,热交换器的性能得到提高,因为翅片的温度将增加,并且温度在翅片表面上更加均匀,从而有利于通过传导来传播热量。
[0093]
替代地,每个第一管道30和第二管道32可以独立地连接到供应源。在这种情况下,我们理解第一管道30和第二管道32中的每个管道分别包括进油口和出油口。热交换器不具有通道34a、34b。
[0094]
在该实施例(图8)中示出的翅片23是不连续的(交错排列),即,在大体平行于纵向方向的一排翅片中有多个翅片。有利地,翅片以交错的方式布置。根据另一替代方案,翅片23沿着纵向方向或沿着径向方向呈波纹状。
[0095]
根据图9和图10所示的另一实施例,热交换器配备有盖子40,盖子40具有空气动力学轮廓,盖子径向布置在面板28的外部。与前述实施例相同的元件由相同的附图标记表示。换句话说,面板28沿着径向方向位于翅片23和盖子40之间。这样的构造使得能够进一步改善热交换器的空气动力学特性,并且不会由于热交换器的集成而扰乱气流。尤其在图9中可以看出,盖子40具有外周表面41,外周表面41与第一成型壁25的径向外表面42和第二成型壁26的径向外表面43具有表面连续性。
[0096]
具体地,盖子40具有第一部分44和第二部分45,第二部分沿着热交换器中的气流的流动方向布置在第一部分44的上游。第一部分44被限定在相对于纵向方向l具有倾斜度的平面中。该倾斜的平面与限定支撑壁22的径向外表面24的平面(平行于平面lt)形成预定角度β(参见图10)。对于第二部分45,第二部分在平面rl中具有曲线形状。在此,曲线部分是凹形的。该曲线部分大约是四分之一的圆。该曲线部分的曲率半径取决于面板28的长度(沿着纵向方向l)。长度与曲率半径之间的比值介于0.5mm至1.5mm之间。盖子40的宽度与成型面板的宽度大致相同。具有空气动力学轮廓的盖子使得热交换器能够更好地融入到气流中,特别是融入到次级气流中,而不扰乱气流,而此处的内部面板28提高了热交换器内部的气流流动的气动热性能。每个盖子40和面板28都针对气流的部分进行了优化。
[0097]
面板28和盖子40可以制成一体件(整体),以便简化热交换器的制造和组装。增材制造是使得能够实现该目标的制造方法。可以假设,翅片23也与面板和盖子制成一体件,并且遵循相同的制造方法。
[0098]
图11示出了热交换系统又一实施例,该热交换系统具有热交换器21,热交换器包括具有不同高度的翅片。具体地,翅片从支撑壁22的径向外表面24延伸并且由具有空气动力学轮廓的盖子40覆盖,以提高绕过热交换器的气流的空气动力学特性。盖子40在上游包括第一壁25和第二壁26,第一壁具有发散轮廓,第二壁具有收敛轮廓。与前述情况一样,气流f2在进入气流时被减慢,并且在离开热交换器21时被加速。外周表面41与第一壁25和第二壁26的径向外表面42、43具有表面连续性。在本示例中,翅片230符合覆盖它们的盖子40的形状。实际上,盖子40包括第一倾斜部分44和第二曲线部分45。以这种方式,翅片230根据热交换器中的流动方向从(第一壁25的)上游到(第二壁26的)下游以先增大后减小的方式分别具有变化的高度。翅片的高度增加到第一倾斜部分44和第二曲线部分45之间的纵向接合点j处。高度从接合点j处开始减小。因此,在翅片和盖子之间没有径向的面板28。
[0099]
图11所示的翅片是不连续的,并且以交错的方式布置,但是每个翅片都可以沿着盖子的轮廓沿着纵向方向延伸,并且翅片具有与盖子一致的变化的径向高度。所示位于j接合点处的翅片具有径向外弯曲(凹形)或大体呈倒v端的形状。翅片还可以沿着纵向方向和沿着径向方向呈波纹状。
[0100]
根据图12和图13中示意性示出的另一实施例,热交换器包括翅片230,翅片从支撑壁22径向延伸并且由盖子40覆盖。盖子包括上游的第一壁部分和下游的第二壁部分。如在图11所示的实施例中,翅片230遵循盖子40的轮廓,翅片的高度从上游到下游先增大再减小。具体地,参照图13,翅片230沿着纵向方向是连续的且笔直的。我们还看到,在该实施例中有两种类型的翅片形状,第一类型的翅片支撑盖子,以及第二类型的翅片不支承盖子。
[0101]
第一类型的翅片230a包括延伸到盖子的前缘ba1和后缘bf1。前缘ba1和后缘bf1具有与支撑壁22一体的径向内端和与盖子一体的径向外端。这些前缘ba1和bf1通过第一表面231、第二表面232和第三表面233连接。这些表面与支撑壁22的径向外表面24径向相对。第一表面213和第三表面233相对于与平面lt平行的平面倾斜,并且第二表面在大体平行于平面lt的平面中延伸。
[0102]
第二类型的翅片230b包括前缘ba2和后缘bf2,前缘ba2和后缘bf2在径向内端和径向外端之间测量到的各自的高度小于第一类型的翅片230a的前缘和后缘的高度。前缘ba2和后缘bf2分别倾斜,并且从支撑壁22增长到与第一类型的翅片的第二表面232的高度相对
应的高度。每个翅片具有中心部分,中心部分具有相同径向高度的第二表面232。我们理解,所有翅片(或至少第一类型的翅片230a)在它们的中心部分的水平处连接到盖子。
[0103]
在该实施例中,翅片沿着横向方向布置,使得三个翅片中有第一类型的翅片。换句话说,两个第二类型的翅片布置成与两个第一类型的翅片相邻,并布置在两个第一类型的翅片之间。当然,布置方式可以不同,例如,使得每五个翅片都是第一类型的翅片。
[0104]
第一类型的翅片和第二类型的翅片使得能够进行热传递。
[0105]
图14至图17示出了嵌入在涡轮机的次级通路v2的环形壁中并且至少部分地引导次级气流的热交换器的实施例。热交换器21在其布置中被涡轮机的次级气流扫过和/或穿过。次级通路由径向内环形壁50和径向外环形壁51界定。径向外环形壁至少部分地由风扇壳体11承载。
[0106]
根据图14中的实施例,径向外环形壁51包括开口510,热交换器安装在开口中。在这种情况下,热交换器21包括翅片,(沿着涡轮机的径向轴线)翅片一方面被面板28覆盖,另一方面被支撑壁22覆盖。热交换器21还包括第一成型壁25和第二壁26,第一成型壁在上游连接到径向外壁51的一部分并且还连接到面板28,第二壁在下游连接到径向外壁51的一部分并且还连接到面板28。面板28从径向外壁51径向向外偏移。以这种方式,翅片23至少部分地嵌入在次级通路的壁51中,这使得能够最小化对次级通路中的气流流动的扰乱。有利地,径向外壁51、第一壁25、面板28和第二壁26具有连续的表面。支撑壁22远离径向外壁51径向延伸。(具有第一壁25的次级通路的)壁部分与支撑壁22形成空气入口,空气入口沿着涡轮机的径向轴线具有第一预定高度he,第一预定高度使得能够减慢热交换器的入口处的气流的流动速度。(具有第二壁26的次级通路的)壁部分与支撑壁22形成空气出口hs,空气出口沿着径向轴线具有第二预定高度hs。第一高度he和第二高度hs之间的比值介于0.5到1之间。
[0107]
根据图13中的另一实施例,径向外壁51包括集成热交换器的阶部或凹部53。因此,翅片23至少部分地嵌入在次级通路的壁51中,这使得能够最小化对次级通路中的气流流动的扰乱。如图4至图6所示的实施例中,翅片从凹壁52延伸并且被壁54径向覆盖。凹壁53在上游形成圆角55a或第一弯曲壁并且在下游形成圆角55b或第二弯曲壁,圆角55a或第一弯曲壁连接次级通路的径向外壁51,圆角55b或第二弯曲壁连接次级通路的径向外壁51。我们认为,前述实施例的面板28以及第一壁25和第二壁26由凹壁53、弯曲壁55a、55b和次级(大体圆柱形)通路的壁部分51a、51b形成。支撑壁22由板54形成。板54延伸到次级通路中。板具有圆形或弯曲(围绕纵向轴线)的形状。(次级通路的)壁部分与支撑壁54形成空气入口,空气入口沿着涡轮机的径向轴线具有第一预定高度he,第一预定高度使得能够减慢热交换器的入口处的气流的流动速度。(次级通路的)壁部分与壁54形成空气出口hs,空气出口沿着径向轴线具有第二预定高度hs。第一高度he和第二高度hs之间的比值介于0.5到1之间。当然,面板28可以由板54和由支撑壁形成,支撑壁由凹部53形成。
[0108]
在图14和图15的示例中,油管56布置在凹壁53中(或面板28中)。进入次级通路的气流的一部分f2穿过空气入口进入热交换器,并且在穿过空气出口离开热交换器并且被加速之前穿过翅片23。气流的另一部分f1在热交换器的外部并且沿着壁22、54的外表面流动。在外部流通的气流不会遇到任何障碍。
[0109]
图16所示的实施例与图14和图15的前述实施例的不同之处在于,油管56布置在延
伸到次级通路中的壁28、54中。气流在油管56的两侧(即,热交换器内部和热交换器外部)流通,从而使得能够提高油和空气之间的热交换。
[0110]
在图17中,所示的实施例与图12至图14的实施例的不同之处在于,第一油管30布置在延伸到次级通路中的壁22、54中,以及第二油管32布置在承载翅片的径向外壁的部分中。在第一管道30中流通的油在一侧与穿过翅片23的气流交换,并且在另一侧与绕过翅片23的气流(在热交换器的外部流通并且进入次级通路v2)交换。
[0111]
图14至图17的嵌入式的热交换器还可以包括具有空气动力学轮廓的盖子40。