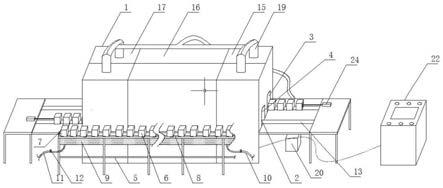
1.本发明涉及工业电窑领域,具体地说,是涉及一种对推式节能窑炉。
背景技术:2.窑炉是工业中的基础设备,各种原料烘干或成品烧结均要用到窑炉;如各种电子功能陶瓷:热敏电阻、压敏电阻,5g陶瓷滤波器,gps天线、电感、新能源电池材料等各种产品使用窑炉数量巨大。
3.窑炉是个高能耗的设备,一般常规隧道炉的功率都在100千瓦以上每小时,有的甚至达到1000千瓦以上每小时,耗能巨大;在产品原料烘干和烧结的工艺流程中,产品从低温到高温,高温保温烧结后,再缓慢降到低温;在实际生产中,产品高温后还带有很多热量,这时这个热量需要散掉;现靠增加炉体的长度来做降温区,通过自然或者风机强制排除热量让产品和窑炉辅具平缓的降到150
°
以下才能输出。
4.现有窑炉采用自然冷却方式冷却,热量损失巨大;产品出窑炉后其表面的温度还是较高带有一定的热量,搬运时不方便易损伤工具或员工,存在安全隐患,且产品上带有的热量将会损耗,使现有窑炉的能耗不能得到有效的控制,产生的热能也不能得到有效的利用。
技术实现要素:5.本发明的目的在于提供一种对推式节能窑炉,以解决现有窑炉热量损失巨大,存在安全隐患,热能不能得到有效利用的问题。
6.为了解决上述问题,本发明提供如下技术方案:一种对推式节能窑炉,包括炉体;炉体内沿其长度方向设有两条连通炉体两端的通道,两条通道相互平行,且内部之间间隔连通;炉体一端上的通道口为一条通道的进料口和另一条通道的出料口,另一端上的通道口为一条通道的出料口和另一条通道的进料口;出料口处设有l型散热机构,l型散热机构的一端与出料口连通,其长边沿炉体长度方向设置。
7.具体地,l型散热机构包括l型支架;l型支架的一端设置在出料口处,其长边沿沿炉体长度方向设置;l型支架上两边上分别设有输送机输送烧制好装有产品的匣钵;出料口和l型支架的转角处均设有推动匣钵的推缸,分别将匣钵推入l型支架和推到下一个输送机上。
8.具体地,输送机为沿l型支架的相面对的直线边上均设置有链板输送机或滚筒输送机;推缸为气缸。
9.具体地,两个相面对的链板输送机或滚筒输送机之间设有沿其l型支架两端设置的水箱,l型支架支撑水箱;水箱连通有进水管和出水管,进水管和出水管上分别设有止回阀。
10.具体地,通道内设有沿其长度方向的轨道;炉体两端外设有推进器将匣钵推入轨
道内滑动;通道内的炉体内壁上环绕轨道设有多个加热元件。
11.具体地,通道内从进料口到出料口分为三个温区,分别为升温区、高温区、降温区;相互并排的升温区和降温区之间设有至少一个通孔相互连通,所述升温区和降温区之间设有相互连通的引风管,引风管位于炉体外顶部;两个引风管相互连通后连接有引风机。
12.具体地,炉体内壁设有温度传感器;炉体外设有plc一体机,温度传感器的输出端与plc一体机的温度输入端连接。
13.具体地,炉体内壁设有各温区设有至少一个耐高温摄像机,耐高温摄像机的输出端与plc一体机的视频输入端连接。
14.具体地,炉体内铺设有耐高温隔热防火材料。
15.与现有技术相比,本发明具有以下有益效果:(1)本发明中两个通道分别向相反的方向运行,一条通道内的产品到需要降温输出时,另一条通道内的产品刚刚进入其内需要升温,两个通道相互连通,此时的热量差使两个通道能相互流通,需要升温的产品吸收需要降温产品的热量,使热量得到更有效的利用,降低了窑炉的能耗。
16.(2)本发明中l型散热机构设置在出料口,从通道出来的产品并没有得到完全的散热,产品沿l型散热机构运行,自然散热的通道更长,炉体增长会增加更多的成本,将散热通道设置在炉体外增加产品的散热路长,减少了炉体的占地,也使产品得到有效的散热,避免了因高温损伤工具或员工及因此产生安全隐患的情况。
17.(3)本发明中匣钵带出的温度及其内产品的温度均较高,水箱与匣钵接触,降低匣钵的温度,水箱中水升温后可做他用,提高了热能的利用,减少了热能的自然消耗,可通过进水管和出水管对水箱中的水进行更换。
附图说明
18.图1为本发明的结构示意图。
19.图2为炉体内部通道的结构示意图。
20.上述附图中,附图标记对应的部件名称如下:1-炉体,2-通道,3-进料口,4-出料口,5-l型支架,6-匣钵,7-推缸,8-输送机,9-水箱,10-进水管,11-出水管,12-止回阀,13-轨道,14-加热元件,15-升温区,16-高温区,17-降温区,18-通孔,19-引风管,20-引风机,21-温度传感器,22-plc一体机,23-耐高温摄像机,24-推进器。
具体实施方式
21.下面结合附图和实施例对本发明作进一步说明,本发明的实施方式包括但不限于下列实施例。
22.实施例1如图1和图2所示,一种对推式节能窑炉包括炉体1;炉体1内沿其长度方向设有两条连通炉体1两端的通道2,两条通道2相互平行,且内部之间间隔连通;炉体1一端上的通道2口为一条通道2的进料口3和另一条通道2的出料口4,另一端上的通道2口为一条通道2的出料口4和另一条通道2的进料口3;出料口4处设有l型散热机构,l型散热机构包括l型支架
5;l型支架5的一端设置在出料口4处,其长边沿沿炉体1长度方向设置;l型支架5上两边上分别设有输送机8输送烧制好装有产品的匣钵6;出料口4和l型支架5的转角处均设有推动匣钵6的推缸7,分别将匣钵6推入l型支架5和推到下一个输送机8上;通道2内设有沿其长度方向的轨道13;炉体1两端外设有推进器将匣钵6推入轨道13内滑动;通道2内的炉体1内壁上环绕轨道13设有多个加热元件14;炉体1内壁设有温度传感器21;炉体1外设有plc一体机22,温度传感器21的输出端与plc一体机22的温度输入端连接;炉体1内壁设有各温区设有至少一个耐高温摄像机23,耐高温摄像机23的输出端与plc一体机22的视频输入端连接;炉体1内铺设有耐高温隔热防火材料,减少经炉体1自身散去的热量。
23.两个通道2分别向相反的方向运行,一条通道2内的产品到需要降温输出时,另一条通道2内的产品刚刚进入其内需要升温,两个通道2相互连通,此时的热量差使两个通道2能相互流通,需要升温的产品吸收需要降温产品的热量,使热量得到更有效的利用,降低了窑炉的能耗;l型散热机构设置在出料口4,从通道2出来的产品并没有得到完全的散热,产品沿l型散热机构运行,自然散热的通道2更长,炉体1增长会增加更多的成本,将散热通道2设置在炉体1外增加产品的散热路长,减少了炉体1的占地,也使产品得到有效的散热,避免了因高温损伤工具或员工及因此产生安全隐患的情况;加热元件14环绕轨道13设置在炉体1内壁上,使热量更加均匀,产品受热更均匀,节约能耗,使产品的质量更好;plc一体机22用于设置参数及根据数据了解炉体1内的情况;l型支架5为较优配合炉体1形状也可延长散热路长的形状,也可选择其他形状的支架。
24.本实施例中,输送机8为沿l型支架5的相面对的直线边上均设置有链板输送机8,也可选择滚筒输送机8;推缸7为气缸;也可根据实际使用需要选择其他具有相同功能的其他部件。
25.实施例2如图1和图2所示,本实施例与实施例1的不同点在于,两个相面对的链板输送机8或滚筒输送机8之间设有沿其l型支架5两端设置的水箱9,l型支架5支撑水箱9;水箱9连通有进水管10和出水管,进水管10和出水管上分别设有止回阀12;匣钵6带出的温度及其内产品的温度均较高,水箱9与匣钵6接触,降低匣钵6的温度,水箱9中水升温后可做他用,提高了热能的利用,减少了热能的自然消耗,水箱9为导热材质制成,可通过进水管10和出水管对水箱9中的水进行更换。
26.实施例3如图1和图2所示,本实施例与实施例1和2的不同点在于,通道2内从进料口3到出料口4分为三个温区,分别为升温区15、高温区16、降温区17;相互并排的升温区15和降温区17之间设有至少一个通孔18相互连通,所述升温区15和降温区17之间设有相互连通的引风管19,引风管19位于炉体1外顶部;两个引风管19相互连通后连接有引风机20;引风管19加速了相互并排的升温区15和降温区17之间热量的互换,加速了升温度产品的升温,也加速了降温度产品的降温,使热能得到更有效的利用,也降低了炉体1的能耗。
27.本发明的使用原理:从炉体1两端的进料口3进料,一个通道2内的产品到降温区17时,另一个通道2内的产品到升温区15,相互连通的升温区15和降温区17及相互连通的引风管19,加速了两者之间的热量互换,产品从出料口4出料后进入l型支架5上在输送机8的作用下运行,自然散热,产品匣钵6的下方设有的水箱9也会吸收匣钵6的温度,变成热水做其
他用途,提高了热能的利用,完全散热后的产品即可进入下一工序。
28.本发明中两个通道2相向而行,同时利用相互连通的并排的升温区15和降温区17进行热能互换及l型支架5上水箱9及输送机8的使用,有效的降低了炉体1的能耗,并能产生热水,经实际使用证明,本发明比同向而行的窑炉节约能源至少45%左右,窑炉是工业基础环节中常用的设备,经济效益巨大,本发明可推广使用到板式隧道炉,网带炉,辊道炉等炉体中。
29.按照上述实施例,便可很好地实现本发明。值得说明的是,基于上述结构设计的前提下,为解决同样的技术问题,即使在本发明上做出的一些无实质性的改动或润色,所采用的技术方案的实质仍然与本发明一样,故其也应当在本发明的保护范围内。