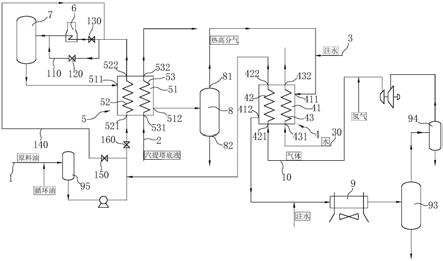
1.本实用新型属于换热技术领域,具体涉及一种采用多股流缠绕管式换热器的加氢换热系统。
背景技术:2.加氢处理是石油产品中较为重要的处理方法之一,是指在一定温度、氢分压及催化剂条件下,脱除油品中的硫、氮、氧等杂原子及金属杂质,使烯烃饱和、芳烃部分加氢饱和,以改善油品的使用性能。
3.加氢处理的过程为:油品与氢气混合后,送入加热炉加热到规定温度,再进入装有催化剂的反应器中;反应完成后,氢气在分离器中分出,并经压缩机循环使用;产品则在稳定塔中分出硫化氢、氨、水以及在反应过程中少量分解而产生的气态氢。
4.现有的加氢用的换热工艺如申请号为cn201310344264.4的发明专利申请《一种柴油加氢处理工艺》(申请公布号为cn103421542a)公开的方案,其步骤为:1)柴油与氢气混合后进第一换热器进行换热,升温到270
‑
280℃;2)从第一换热器出来的混合物进原料加热炉,待加热到320
‑
330℃后再进加氢反应器;3)从加氢反应器出来的反应产物依次经第五换热器、第一换热器、第二换热器换热后,降温到175
‑
185℃,之后注水并经第一空气冷却器冷却到45
‑
55℃后进冷高分罐,分离出含氢气体和冷高分油;4) 冷高分罐分出的含氢气体进循环氢压缩机,经循环氢压缩机提压后与新氢混合,混合后分两路,其中一路与柴油混合,另一路进加氢反应器,而从冷高分罐排出的冷高分油则经减压后进冷低分罐,在该冷低分罐中分离出低分气和低分油;5)低分气排出冷低分罐,而低分油则依次经第二换热器、第三换热器、第五换热器换热后进汽提分馏塔,此时对该汽提分馏塔注入汽提蒸汽,之后该汽提分馏塔分离出石脑油、含硫油气及产品柴油;6)石脑油和含硫油气从汽提分馏塔出来后分别往后一工序送去,而产品柴油则依次经第三换热器和第四换热器换热后进第二空气冷却器冷却,冷却到45
‑
55℃后,最终进入成品油罐区,即得。
5.加氢工艺采用的设备因操作条件苛刻,为高温、高压设备,常规换热器很难大型化生产,且随着装置规模的扩大,现有技术中同一位号只能采用多台换热器串/并联的形式来满足工艺要求,这无疑会增加成本,并增加设备的占地面积。
技术实现要素:6.本实用新型所要解决的技术问题是针对现有技术的现状,提供一种能减少换热器数量的同时提高换热效果的加氢换热系统。
7.本实用新型解决上述技术问题所采用的技术方案为:一种采用多股流缠绕管式换热器的加氢换热系统,包括:用于输送原料油的第一管线、用于输送汽提塔底液的第二管线、用于输送含有氢气的气体的第十管线、加热炉、与加热炉的输出端相连的加氢反应器、用于对加氢反应器输出的反应产物进行分离以得到热高分气和热高分油的热高分离罐、以及换热装置,其特征在于:
8.所述换热装置包括有第一换热装置和第二换热装置,所述第一换热装置与所述第十管线和热高分离罐之用于输出热高分气的热高分气输出端相连,用于使热高分气与上述第十管线内的气体进行换热;
9.所述第二换热装置为具有一个第二热介质通道和至少两个第二冷介质通道的第二缠绕管式换热器,该第二缠绕管式换热器上设有连通第二热介质通道的第二热介质通道入口接管和第二热介质通道出口接管、连通第二冷介质通道一的第二冷介质通道一入口接管和第二冷介质通道一出口接管、连通第二冷介质通道二的第二冷介质通道二入口接管和第二冷介质通道二出口接管;所述第二热介质通道入口接管与上述加氢反应器的输出端相连,所述第二热介质通道出口接管与上述热高分离罐的输入端相连,所述第一换热装置的气体输出端与第一管线相连后的混合管线的输出端与所述第二冷介质通道一入口接管相连,所述第二冷介质通道一出口接管与上述加热炉的输入端相连,所述第二冷介质通道二入口接管与上述第二管线的输出端相连,所述第二冷介质通道二出口接管连接至汽提塔。
10.优选地,所述第一换热装置为具有一个第一热介质通道和至少两个第一冷介质通道的第一缠绕管式换热器,该第一缠绕管式换热器上设有连通第一热介质通道的第一热介质通道入口接管和第一热介质通道出口接管、连通第一冷介质通道一的第一冷介质通道一入口接管和第一冷介质通道一出口接管、连通第一冷介质通道二的第一冷介质通道二入口接管和第一冷介质通道二出口接管;
11.所述第一热介质通道入口接管与上述热高分离罐之用于输出热高分气的热高分气输出端相连,所述第一热介质通道出口接管连接至下游设备二,所述第一冷介质通道一入口接管与上述第十管线的输出端相连,所述第一冷介质通道一出口接管与所述第一管线的输出端相连;还包括有用于输送水的第四管线,所述第一冷介质通道二入口接管与上述第四管线的输出端相连,所述第一冷介质通道二出口接管连接至下游设备一。
12.同样优选地,所述第一换热装置包括具有一个第三热介质通道和至少一个第三冷介质通道的第三缠绕管式换热器、具有一个第四热介质通道和至少一个第四冷介质通道的第四缠绕管式换热器,该第三缠绕管式换热器上设有连通第三热介质通道的第三热介质通道入口接管和第三热介质通道出口接管、连通第三冷介质通道的第三冷介质通道入口接管和第三冷介质通道出口接管,该第四缠绕管式换热器上设有连通第四热介质通道的第四热介质通道入口接管和第四热介质通道出口接管、连通第四冷介质通道的第四冷介质通道入口接管和第四冷介质通道出口接管;
13.所述第三冷介质通道入口接管与上述第十管线的输出端相连,所述第三冷介质通道出口接管与所述第一管线相连,所述第三热介质通道入口接管与上述热高分离罐之用于输出热高分气的热高分气输出端相连,所述第三热介质通道出口接管与所述第四热介质通道入口接管相连,所述第四热介质通道出口接管连接至下游设备二;还包括有用于输送水的第四管线,所述第四冷介质通道入口接管与上述第四管线的输出端相连,所述第四冷介质通道出口接管连接至下游设备一。
14.在上述各方案中,作为优选,所述第二热介质通道为上述第二缠绕管式换热器的壳程,所述第二冷介质通道为上述第二缠绕管式换热器的管程,所述第二换热装置为具有一个壳程和两个管程的双股流缠绕管式换热器。当然,作为替换,第二热介质通道也可为上述第二缠绕管式换热器的管程,第二冷介质通道为上述第二缠绕管式换热器的壳程,第二
换热装置为具有二个壳程和一个管程的缠绕管式换热器。
15.作为优选,所述第一热介质通道为上述第一缠绕管式换热器的壳程,所述第一冷介质通道为上述第一缠绕管式换热器的管程,所述第一换热装置为具有一个壳程和两个管程的双股流缠绕管式换热器。当然,作为替换,第一热介质通道也可为上述第一缠绕管式换热器的管程,第一冷介质通道为上述第一缠绕管式换热器的壳程,第一换热装置为具有一个管程和两个壳程的缠绕管式换热器。
16.作为优选,所述第三热介质通道为上述第三缠绕管式换热器的管程,所述第三冷介质通道为上述第三缠绕管式换热器的壳程,所述第三缠绕管式换热器为具有一个壳程和一个管程的单股流缠绕管式换热器。作为替换方案,第三热介质通道也可为上述第三缠绕管式换热器的壳程,第三冷介质通道为上述第三缠绕管式换热器的管程。
17.优选地,所述第四热介质通道为上述第四缠绕管式换热器的管程,所述第四冷介质通道为上述第四缠绕管式换热器的壳程,所述第四缠绕管式换热器为具有一个壳程和一个管程的单股流缠绕管式换热器。作为替换方案,第四热介质通道也可为上述第四缠绕管式换热器的壳程,第四冷介质通道为上述第四缠绕管式换热器的管程。
18.在上述各方案中,还包括有用于输送水的第三管线,所述热高分离罐之用于输出热高分气的热高分气输出端与所述第三管线的输出端相连后与所述第一换热装置相连。如此,水能溶解热高分气中的硫化氢、铵盐等部分介质,以降低热高分气中的部分介质腐蚀换热器的现象出现。第三管线可间歇输水。
19.优选地,所述下游设备二为高压空冷器;该高压空冷器的输入端与所述第一换热装置之供换热后的热高分气输出的输出端相连,该高压空冷器的输出端连接至冷高分离罐;
20.或,所述下游设备二为具有一个热介质通道和至少一个冷介质通道的缠绕管式换热器,还包括有用于输送冷水的冷水管线,所述冷水管线的输出端与所述下游设备二的冷介质通道的入口接管相连,所述下游设备二的热介质通道的入口接管与所述第一换热装置之供换热后的热高分气输出的输出端相连,所述热介质通道的出口接管连接至冷高分离罐。
21.即可用缠绕管式换热器替代高压空冷器,加氢装置通常需要多片高压空冷器,而每片空冷的尺寸约10.5*3m,体积较大,占地面积较大;而一台立式安装的缠绕管式换热器即能满足工艺要求,进而大大减小占地面积。
22.进一步地,还包括有缓冲罐,所述缓冲罐的输入端与所述冷高分离罐顶部的输出端相连,所述缓冲罐的输出端与所述第十管线的输入端相连。如此,能实现含有氢气的气体的循环。
23.在上述方案中,还包括有用于输送冷水的冷水管线,所述第一换热装置的第一冷介质通道有至少三个,且该第一换热装置上还设有连通第一冷介质通道三的第一冷介质通道三入口接管和第一冷介质通道三出口接管;所述第一冷介质通道三入口接管与所述冷水管线的输出端相连,所述第一冷介质通道三出口接管连接至下游设备三;所述下游设备二为冷高分离罐。如此,无需另设高压空冷器或者单股流缠绕管式换热器,即可使从第一换热装置的热介质通道出来的介质直接进入冷高分离罐进行分离。
24.在上述各方案中,优选地,还包括有旁路管线、第一阀门和第二阀门,所述旁路管
线的输出端连接在所述加热炉的输出端和加氢反应器的输入端之间,所述旁路管线的输入端连接在所述加热炉的输入端和第二换热装置的第二冷介质通道一出口接管之间,所述第一阀门设于旁路管线上,所述第二阀门设于加热炉的输入端和旁路管线的输入端之间。即本技术中的加热炉为开工加热炉,只需在开工阶段(即系统运行初期)进行加热工作,其余阶段不需要工作。这主要是采用本技术的换热装置可实现更好的换热效果带来的,能大大降低加热炉的运行负荷,采用体积较小,加热能力较小的加热炉即可实现。
25.优选地,还包括有第五管线、第三阀门和第四阀门,所述第五管线的输入端与所述混合管线相连,输出端与所述第二换热装置的第二冷介质通道二出口接管相连;所述第三阀门设于第五管线上,所述第四阀门设于第五管线的输入端和混合管线的输出端之间。
26.与现有技术相比,本实用新型的优点在于:通过将换热装置设计为包括有用于对含有氢气的气体进行换热的第一换热装置、用于对换热后的气体与原料油的混合物以及汽提塔底液进行换热的第二换热装置,且第二换热装置为具有一个第二热介质通道和至少两个第二冷介质通道的第二缠绕管式换热器,如此,可减小换热器数量,进而减少设备占地、框架投资、高压管道用量、配管工作以及设备的维护成本等;且本技术中第一、第二换热装置配合能实现且提高现有的若干台换热器组合后的换热效果,运行稳定后无需采用加热炉也可进行加氢反应,且热端温差和介质压降小;且本技术换热装置的旁路调节手段与现有技术一致;同时,本技术还能减小整个装置的压降,其优势明显;且本技术结构简单、便于实施。
附图说明
27.图1为本实用新型实施例一的结构示意图;
28.图2为本实用新型实施例二的结构示意图;
29.图3为本实用新型实施例三的结构示意图;
30.图4为本实用新型实施例四的结构示意图;
31.图5为本实用新型实施例五中第一换热装置的结构示意图;
32.图6为本实用新型实施例六中第一换热装置的结构示意图。
具体实施方式
33.以下结合附图实施例对本实用新型作进一步详细描述。
34.实施例一:
35.如图1所示,为本实用新型的一种采用多股流缠绕管式换热器的加氢换热系统的优选实施例一,该加氢换热系统包括第一管线1、第二管线2、第三管线3、第四管线30、第十管线10、冷水管线100、第五管线150、第三阀门150、第四阀门160、旁路管线 110、第一阀门120、第二阀门130、第一换热装置4、第二换热装置5、加热炉6、加氢反应器7、热高分离罐8。
36.其中,第一管线1用于输送原料油;且第一管线1上连接有第一缓冲罐95以及用于输送循环油的循环油管线。第二管线2用于输送汽提塔底液。第三管线3用于输送水。第四管线30用于输送水。第十管线用于输送含有氢气的气体。冷水管线100用于输送冷水。
37.上述加氢反应器7的输入端与加热炉6的输出端相连,热高分离罐8用于对加氢反应器7输出的反应产物进行分离以得到热高分气和热高分油,该热高分离罐8具有用于输出
热高分气的热高分气输出端81、用于输出热高分油的热高分油输出端82,热高分油输出端82连接下游装置。
38.上述的第一换热装置4为具有一个第一热介质通道41和两个第一冷介质通道的第一缠绕管式换热器,该第一缠绕管式换热器上设有连通第一热介质通道41的第一热介质通道入口接管411和第一热介质通道出口接管412、连通第一冷介质通道一42的第一冷介质通道一入口接管421和第一冷介质通道一出口接管422、连通第一冷介质通道二43的第一冷介质通道二入口接管431和第一冷介质通道二出口接管432;本实施例中,第一热介质通道41为上述第一缠绕管式换热器的壳程,第一冷介质通道为上述第一缠绕管式换热器的管程,第一换热装置4为具有一个壳程和两个管程的双股流缠绕管式换热器。
39.上述第二换热装置5为具有一个第二热介质通道51和两个第二冷介质通道的第二缠绕管式换热器,该第二缠绕管式换热器上设有连通第二热介质通道51的第二热介质通道入口接管511和第二热介质通道出口接管512、连通第二冷介质通道一52的第二冷介质通道一入口接管521和第二冷介质通道一出口接管522、连通第二冷介质通道二53 的第二冷介质通道二入口接管531和第二冷介质通道二出口接管532;第二热介质通道 51和第二冷介质通道为上述第二缠绕管式换热器的管程和壳程;本实施例中,第二热介质通道51为上述第二缠绕管式换热器的壳程,第二冷介质通道为上述第二缠绕管式换热器的管程,第二换热装置5为具有一个壳程和两个管程的双股流缠绕管式换热器。
40.第一换热装置4、第二换热装置5与上述的各管线、加热炉6、加氢反应器7、热高分离罐8之间的连接结构为:热高分气输出端81与第三管线3的输出端相连后与第一换热装置4中第一热介质通道入口接管411相连,第一热介质通道出口接管412连接至下游设备二9,第一冷介质通道一入口接管421与上述第十管线10的输出端相连,第一冷介质通道一出口接管422与第一管线1相连后的混合管线的输出端与上述第二换热装置5中第二冷介质通道一入口接管521相连,第一冷介质通道二入口接管431与上述第四管线30的输出端相连,第一冷介质通道二出口接管432连接至下游设备一。上述第二换热装置5中第二热介质通道入口接管511与上述加氢反应器7的输出端相连,第二热介质通道出口接管512与上述热高分离罐8的输入端相连,第二冷介质通道一出口接管522与上述加热炉6的输入端相连,第二冷介质通道二入口接管531与第二管线2 的输出端相连,第二冷介质通道二出口接管532连接至汽提塔。
41.本实施例中,下游设备二9为高压空冷器,由第一热介质通道出口接管412出来的热介质经过高压空冷器后连接至冷高分离罐93,以分离出含有氢气的气体。还包括有缓冲罐94,缓冲罐94的输入端与冷高分离罐93顶部的输出端相连,缓冲罐94顶部的输出端与第十管线10的输入端相连,实现气体的循环利用。当然,第十管线10上还可连接用于补充氢气的氢气管线。且第一热介质通道出口接管412与下游设备二9的输入端之间可连接用于连续输送水的管线。
42.上述旁路管线110的输出端连接在加热炉6的输出端和加氢反应器7的输入端之间,旁路管线110的输入端连接在加热炉6的输入端和第二换热装置5的第二冷介质通道一出口接管522之间,第一阀门120设于旁路管线110上,第二阀门130设于加热炉 6的输入端和旁路管线110的输入端之间。上述第五管线140的输入端与混合管线相连,输出端与第二换热装置5的第二冷介质通道一出口接管522相连;第三阀门150设于第五管线140上,第四
阀门160设于第五管线140的输入端和混合管线的输出端之间。上述旁路管线110、第五管线140及各阀门的设置能满足装置各个阶段、各个工况变动的工艺条件。各管线的通断根据实际工况进行选择。
43.采用本实施例的加氢换热系统进行换热的方法如下:
44.将第十管线10中的气体、第四管线30中的水作为冷介质分别输入第一换热装置4 中各自对应的管程内,第十管线10中气体的温度为60~80℃,第四管线30中水的温度为60~75℃;由第一换热装置4出来的气体、水的温度分别为220~250℃、95~125℃。由第一换热装置4出来的气体与第一管线1中的原料油混合,气体与原料油组成的混合物、第二管线2中的汽提塔底液作为冷介质分别输入第二换热装置5中各自对应的管程内,第一管线1中的原料油的温度为160~210℃,第二管线2中的汽提塔底液的温度为 220~250℃;由第二换热装置5的管程出来的混合物、汽提塔底液的温度分别为 350~395℃、270~290℃,且由第二换热装置5的管程出来的混合物进入加氢反应器7进行加氢反应后从加氢反应器7输出,输出的反应产物的温度为370~440℃,该反应产物作为第二换热装置5的热介质走第二换热装置5的壳程,与第二换热装置5中的冷介质进行换热,由第二换热装置5的壳程出来的反应产物的温度降低至250℃,并进入热高分离罐8分离出热高分气和热高分油,分离出的热高分气与第三管线3中的水混合后作为第一换热装置4的热介质走第一换热装置4的壳程,与第一换热装置4管程中的冷介质进行换热,然后从第一换热装置4输出,由第一换热装置4的壳程出来的热高分气与水的温度降低至80~105℃,然后进入下游设备二9,由下游设备二9出来的介质温度为 50℃,然后进入冷高分离罐93进行分离,由冷高分离罐93顶部出来的气体进入缓冲罐 94,由缓冲罐94顶部出来的气体进入第十管线10,实现气体的循环。本实施例中混合管线内气体与原料油之间的含量比根据实际工况设计。
45.本实施例的加氢换热系统由于换热效率高,使得从第二换热装置5出来的混合物无需加热炉加热就能直接进入加氢反应器7内进行反应,加热炉仅需在运行初期使用,其他运行阶段均可走旁路管线110。
46.实施例二:
47.如图2所示,为本实用新型的一种采用多股流缠绕管式换热器的加氢换热系统的优选实施例二,本实施例与实施例一基本相同,区别在于本实施例中第一换热装置4与实施例一中不同,本实施例的第一换热装置4包括具有一个第三热介质通道45和一个第三冷介质通道46的第三缠绕管式换热器4a、具有一个第四热介质通道47和一个第四冷介质通道48的第四缠绕管式换热器4b,该第三缠绕管式换热器4a上设有连通第三热介质通道45的第三热介质通道入口接管451和第三热介质通道出口接管452、连通第三冷介质通道46的第三冷介质通道入口接管461和第三冷介质通道出口接管462,该第四缠绕管式换热器4b上设有连通第四热介质通道47的第四热介质通道入口接管471和第四热介质通道出口接管472、连通第四冷介质通道48的第四冷介质通道入口接管481和第四冷介质通道出口接管482。本实施例中,第三热介质通道45为上述第三缠绕管式换热器4a的管程,第三冷介质通道46为上述第三缠绕管式换热器4a的壳程,第三缠绕管式换热器4a为具有一个壳程和一个管程的单股流缠绕管式换热器。第四热介质通道47 为上述第四缠绕管式换热器4b的管程,第四冷介质通道48为上述第四缠绕管式换热器 4b的壳程,第四缠绕管式换热器4b为具有一个壳程和一个管程的单股流缠绕管式换热器。
48.本实施例中第一换热装置4与各管线、第二换热装置5、热高分气输出端81之间的连接结构为:第三缠绕管式换热器4a中第三冷介质通道入口接管461与上述第十管线10的输出端相连,第三冷介质通道出口接管462与上述第一管线1相连后的混合管线的输出端与第二换热装置5中的第二冷介质通道一入口接管521相连,热高分气输出端81与第三管线3的输出端相连后与第三热介质通道入口接管451相连,第三热介质通道出口接管452与第四缠绕管式换热器4b中第四热介质通道入口接管471相连,第四热介质通道出口接管472连接至下游设备二9,第四冷介质通道入口接管481与上述第四管线30的输出端相连,第四冷介质通道出口接管482连接至下游设备一。
49.且本实施例中,第三热介质通道出口接管452与第四热介质通道入口接管471之间连接有用于连续输送水或者间歇输送水的管线。
50.采用本实施例的加氢换热系统进行换热的方法如下:
51.将第十管线10中的气体作为冷介质输入第三缠绕管式换热器4a的壳程,第十管线 10中气体的温度为60~80℃,由第三缠绕管式换热器4a的壳程出来的气体的温度为 220~250℃;将第四管线30中的水作为冷介质输入第四缠绕管式换热器4b的壳程,第四管线30中水的温度为60~75℃,由第四缠绕管式换热器4b的壳程出来的水的温度为 95~125℃。由第三缠绕管式换热器4a的壳程出来的气体与第一管线1中的原料油混合,气体与原料油组成的混合物、第二管线2中的汽提塔底液作为冷介质分别输入第二换热装置5中各自对应的管程内,第一管线1中的原料油的温度为160~210℃,第二管线2 中的汽提塔底液的温度为220~250℃;由第二换热装置5的管程出来的混合物、汽提塔底液的温度分别为350~395℃、270~290℃,且由第二换热装置5的管程出来的混合物进入加氢反应器7进行加氢反应后从加氢反应器7输出,输出的反应产物的温度为 370~440℃,该反应产物作为第二换热装置5的热介质走第二换热装置5的壳程,与第二换热装置5中的冷介质进行换热,由第二换热装置5的壳程出来的反应产物的温度降低至250℃,并进入热高分离罐8分离出热高分气和热高分油,分离出的热高分气与第三管线3中的水混合后作为热介质依次走第三缠绕管式换热器4a的管程、第四缠绕管式换热器4b的管程,与第三缠绕管式换热器4a、第四缠绕管式换热器4b的壳程中的冷介质进行换热,然后从第四缠绕管式换热器4b的管程输出,由第四缠绕管式换热器4b 的管程出来的热高分气与水的温度降低至80~105℃,然后进入下游设备二9,由下游设备二9出来的介质温度为50℃,然后进入冷高分离罐93进行分离,由冷高分离罐93 顶部出来的气体进入缓冲罐94,由缓冲罐94顶部出来的气体进入第十管线10,实现气体的循环。
52.本实施例的加氢换热系统由于换热效率高,使得从第二换热装置5出来的混合物无需加热炉加热就能直接进入加氢反应器7内进行反应,加热炉仅需在运行初期使用,其他运行阶段均可走旁路管线110。
53.实施例三:
54.如图3所示,为本实用新型的一种采用多股流缠绕管式换热器的加氢换热系统的优选实施例三,本实施例与实施例二基本相同,区别在于本实施例中的下游设备二9为具有一个热介质通道92和一个冷介质通道91的缠绕管式换热器,且本实施例还包括有用于输送冷水的冷水管线100,冷水管线100的输出端与下游设备二9的冷介质通道91 的入口接管相连,冷介质通道91的出口接管连接至下游设备三,下游设备二9的热介质通道92的入口接管
与第一换热装置4之供换热后的热高分气输出的输出端相连(本实施例中第一换热装置4之供换热后的热高分气输出的输出端为第四热介质通道出口接管472),热介质通道92的出口接管连接至冷高分离罐93。且第四热介质通道出口接管 472与下游设备二9的热介质通道92的入口接管之间连接有用于连续输送水或者间歇输送水的管线。
55.本实施例的换热方法与实施例二基本相同,区别在于本实施例中冷水管线100中的冷水温度为小于35℃,由下游设备二9的冷介质通道91输出的冷水的温度为小于45 摄氏度,且进入下游设备二9的热介质通道92前的介质温度为80~105℃,由下游设备二9的热介质通道92输出的介质温度为50℃。
56.实施例四:
57.如图4所示,为本实用新型的一种采用多股流缠绕管式换热器的加氢换热系统的优选实施例四,本实施例与实施例一基本相同,区别在于本实施例中的第一换热装置4与实施例一中的第一换热装置略有不同,本实施例的第一换热装置4具有一个第一热介质通道41和三个第一冷介质通道,三个第一冷介质通道分别为第一冷介质通道一42、第一冷介质通道二43和第一冷介质通道三44,且该第一换热装置4上还设有连通第一冷介质通道三44的第一冷介质通道三入口接管441和第一冷介质通道三出口接管442。同时,本实施例还包括有用于输送冷水的冷水管线100,第一冷介质通道三入口接管441 与冷水管线100的输出端相连,第一冷介质通道三出口接管442连接至下游设备三。如此,可加热冷水管线100中的水,且下游设备三可为需要用到水的设备或者是输送水的管线。且本实施例中第一热介质通道出口接管412直接连接至冷高分离罐93,而无需另设下游设备二9。
58.采用本实施例的加氢换热系统进行换热的方法如下:
59.将第十管线10中的气体、第四管线30中的水、冷水管线100中的冷水作为冷介质分别输入第一换热装置4中各自对应的管程内,第十管线10中气体的温度为60~80℃,第四管线30中水的温度为60~75℃,冷水管线100中冷水的温度为小于35℃;由第一换热装置4的管程出来的气体、水、冷水的温度分别为220~250℃、95~125℃、小于45℃。由第一换热装置4的管程出来的气体与第一管线1中的原料油混合,气体与原料油组成的混合物、第二管线2中的汽提塔底液作为冷介质分别输入第二换热装置5中各自对应的管程内,第一管线1中的原料油的温度为160~210℃,第二管线2中的汽提塔底液的温度为220~250℃;由第二换热装置5的管程出来的混合物、汽提塔底液的温度分别为 350~395℃、270~290℃,且由第二换热装置5的管程出来的混合物进入加氢反应器7进行加氢反应后从加氢反应器7输出,输出的反应产物的温度为370~440℃,该反应产物作为第二换热装置5的热介质走第二换热装置5的壳程,与第二换热装置5中的冷介质进行换热,由第二换热装置5的壳程出来的反应产物的温度降低至250℃,并进入热高分离罐8分离出热高分气和热高分油,分离出的热高分气与第三管线3中的水混合后作为第一换热装置4的热介质走第一换热装置4的壳程,与第一换热装置4管程中的冷介质进行换热,然后从第一换热装置4输出,由第一换热装置4的壳程出来的热高分气与水的温度降低至50℃,然后进入冷高分离罐93进行分离,由冷高分离罐93顶部出来的气体进入缓冲罐94,由缓冲罐94顶部出来的气体进入第十管线10,实现气体的循环。
60.本实施例的加氢换热系统由于换热效率高,使得从第二换热装置5出来的混合物无需加热炉加热就能直接进入加氢反应器7内进行反应,加热炉仅需在运行初期使用,其他
运行阶段均可走旁路管线110。
61.实施例五:
62.如图5所示,为本实用新型的一种采用多股流缠绕管式换热器的加氢换热系统的优选实施例五,本实施例与实施例一基本相同,区别在于本实施例中的第一换热装置与实施例一中的第一换热装置略有不同,本实施例中第一热介质通道41为第一换热装置4 的管程,第一冷介质通道为第一换热装置4的壳程,该第一换热装置4为具有二个壳程和一个管程的缠绕管式换热器。
63.本实施例中的第二换热装置可参考本实施例中的第一换热装置的结构设计,也可同实施例一中第一换热装置的结构设置,具体根据实际工况选择。
64.实施例六:
65.如图6所示,为本实用新型的一种采用多股流缠绕管式换热器的加氢换热系统的优选实施例六,本实施例与实施例四基本相同,区别在于本实施例中的第一换热装置与实施例四中的第一换热装置略有不同,本实施例中的第一热介质通道41为第一换热装置4 的管程,第一冷介质通道为第一换热装置4的壳程,该第一换热装置4为具有三个壳程和一个管程的缠绕管式换热器。
66.上述各实施例中的原料油、气体和汽提塔底液等的温度可以根据实际工况采用不同的温度,示出这些数据,仅为了表明采用上述各实施例中的换热装置后,与现有加氢工艺中的换热装置比较,换热效果好,从而可减小换热器数量,减少设备占地、设备投资、高压管道用量、配管工作以及设备的维护成本等,且还能减小整个装置的压降,整体结构简单、便于实施。