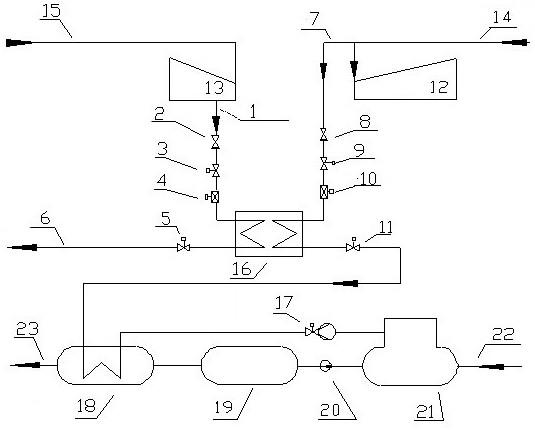
1.本发明提出了一种基于能级匹配的高参数供热的系统,涉及供热领域,尤其是涉及高参数工业供热领域。
背景技术:2.随着经济发展,我国工业体系日趋完善,工业系统集中度越来越高,各种工业园区和产业园区遍布全国。工业生产对电负荷和热负荷都有较大的需求,尤其是化工产业,不但是电力的负荷中心,也是热力的负荷中心。另一方面,由于国家节能减排战略的实施,鼓励用高效的集中供热,代替分散的小锅炉供热,提高综合能源利用效率。鉴于上述原因,在大型工业园区中采用热电联产的集中供热是最佳的选择。
3.高参数供热参数为:压力4.0mpa、温度400℃及以上,一般从电厂过热器出口抽汽。
4.由于装机容量的限制,新建热电联产集中难度较大,新增的热负荷一般通过纯凝机组改造来满足。由于已投产的机组,汽轮机膨胀曲线已经确定,各抽汽点抽汽压力和温度是相关的一组参数,而工业供热需求温度和压力随生产工艺而定,压力和温度相关性不强,因此,机组存在抽汽点压力、温度不能同时满足工艺需求的矛盾,常一般采用更高参数蒸汽减温减压供热用户使用,这样就造成了能级不匹配的浪费现象。
技术实现要素:5.本发明为了解决现有技术中存在的问题,提供一种高效、灵活,并能对供热蒸汽能量进行梯级利用的高参数供热系统。
6.为了达到上述目的,本发明提出的技术方案为:一种基于能级匹配的高参数供热系统,包括高参数供热蒸汽系统、蒸汽源再热系统和供热再热蒸汽回收系统,所述高参数供热蒸汽系统包括高压缸和与高压缸连接的高参数供热抽汽;所述蒸汽源再热系统包括汽汽换热器和与再热蒸汽连接的供热再热抽汽;所述供热再热蒸汽回收系统包括给水附加加热器和除氧器;所述高参数供热抽汽与汽汽换热器冷侧入口连接,供热再热抽汽与汽汽换热器热侧入口连接,所述给水附加加热器热侧入口与汽汽换热器热侧出口连接,给水附加加热器热侧出口与除氧器连接,除氧器出口与给水附加加热器冷侧入口连接。
7.对上述技术方案的进一步设计为:高参数供热抽汽的管道上沿蒸汽流动方向依次设有高参数供热止回阀和高参数供热调节阀。
8.所述高参数供热调节阀前后分别设有高参数供热抽汽调节阀前截止阀和高参数供热调节阀后截止阀。
9.所述高参数供热调节阀后截止阀设置于汽汽换热器冷侧出口的管道上。
10.供热再热抽汽的管道上沿蒸汽流动方向依次设有供热再热抽汽逆止阀和供热再热蒸汽调节阀。
11.所述供热再热蒸汽调节阀前后分别设有供热再热蒸汽调节阀前截止阀和供热再热抽汽调节阀后截止阀。
12.所述供热再热抽汽调节阀后截止阀设置于汽汽换热器热侧出口的管道上。
13.所述给水附加加热器热侧出口与除氧器之间设有减压器。
14.所述除氧器出口与给水附加加热器冷侧入口之间设有给水泵。
15.所述除氧器与给水泵之间设有给水加热器。
16.本发明技术方案与现有技术相比具有的有益效果为:
17.首先,本发明设计了一个独立的闭环供热再热系统,该系统能根据高参数供热加热量的需要,抽取再热蒸汽量,能够满足不同流量的高参数供热蒸汽加热需求,提高了系统的灵活性;其次,本发明供热方案,增设了给水附加加热器,实现了增温蒸汽的梯级利用,进一步提高了能源的利用效率。
18.因此,通过本发明,既能满足灵活地高参数供热压力和温度匹配的问题,又提高了能源利用效率,具有良好的社会效益和经济效益。
附图说明
19.图1为本发明实施例的高参数供热系统结构示意图;
20.图2为常规减温减压高参数供热系统结构示意图。
21.图中:高参数供热抽汽1、高参数供热止回阀2、高参数供热抽汽调阀前截止阀3、高参数供热调节阀4、高参数供热调阀后截止阀5、高参数供热蒸汽6、供热再热抽汽7、供热再热抽汽逆止阀8、供热再热蒸汽调节阀前截止阀9、供热再热蒸汽调节阀10、供热再热抽汽调节阀后截止阀11、中压缸12、高压缸13、再热蒸汽14、主蒸汽15、汽汽换热器16、减压器17、给水附加加热器18、给水加热器19、给水泵20、除氧器21、凝结水22、给水23、供热减温水24、供热减温减压阀25。
具体实施方式
22.下面结合附图以及具体实施例对本发明进行详细说明。
23.实施例
24.如图1所示,本实施例的高参数供热系统中,主蒸汽15进入高压缸13,再热蒸汽14进入中压缸12;该高参数供热系统包括高参数供热蒸汽系统、蒸汽源再热系统和供热再热蒸汽回收系统。
25.高参数供热蒸汽系统在高压缸13上开设供热抽气点,并通过管道抽取高参数供热抽汽1,高参数供热抽汽的特点是蒸汽具有较高压力,能满足供热压力需求,但蒸汽做功后,温度下降,达不到供热温度需求,因此,需要对其蒸汽进行加热。供热抽汽点位置供热抽汽压力pe应满足:
26.pe≥pu+∑δpn27.式中pe为抽汽点压力,mpa;
28.pu为用户端压力,mpa;
29.∑δpn为供热管网总压损,即设计抽汽流量下抽汽口到热用户端蒸汽输送的全部压损,mpa。
30.抽汽口的尺寸设计根据供热流量的确定,保证能够抽取足量的供热蒸汽。
31.在高参数供热抽汽的管道上沿蒸汽流动方向依次设有高参数供热止回阀2和高参
数供热调节阀4,高参数供热止回阀2用于提高机组甩负荷时安全性,高参数供热调节阀4用于调节供热蒸汽流量,为了保证机组安全性,该调节阀具有快关功能;在高参数供热调节阀4前后分别设置高参数供热抽汽调节阀前截止阀3和高参数供热调节阀后截止阀5,用于事故状态下对系统进行隔离。
32.在再热蒸汽14的管道上开设供热再热抽气点,并通过管道抽取供热再热抽汽7,供热再热抽汽特点为蒸汽具有较高的温度,且热源温度稳定、可控,用于提高高参数供热抽汽1的温度;在再热抽汽7的管道上沿蒸汽流动方向依次设有供热再热抽汽逆止阀8和供热再热蒸汽调节阀10,供热再热抽汽逆止阀8用于提高机组甩负荷时安全性,供热再热蒸汽调节阀10用于调节增温蒸汽的流量,为了保证机组安全性,该调节阀具有快关功能;供热再热蒸汽调节阀10前后分别设置了供热再热蒸汽调节阀前截止阀9和供热再热抽汽调节阀后截止阀11,用于对系统进行隔离;本实施例为了实现能量交换,设置了汽汽换热器16,由于两种蒸汽压力不同,该换热器采用间壁式换热器,能量从低压、高温的再热热源蒸汽向高压、低温的高参数供热蒸汽传递,提高高参数供热蒸汽温度;高参数供热抽汽1和供热再热抽汽7分别进入汽汽换热器16的冷侧入口和热侧入口,在汽汽换热器16内完成换热后,汽汽换热器16的冷侧出口通过管道引出高参数供热蒸汽6,高参数供热调节阀后截止阀5设置在高参数供热蒸汽6的管道上;汽汽换热器16的热侧出口通过管道与供热再热蒸汽回收系统连接,供热再热抽汽调节阀后截止阀11设置于该管道上。
33.供热再热蒸汽回收系统包括给水附加加热器18、除氧器21、给水泵20和给水加热器19,给水附加加热器18热侧入口与汽汽换热器16热侧出口连接,给水附加加热器18热侧出口与除氧器21连接,给水附加加热器18热侧出口与除氧器21之间的管道上设有减压器17,用于调节再热蒸汽系统压力,防止除氧器21超压。
34.除氧器21出口处依次连接给水泵20、给水加热器19和给水附加加热器冷侧入口,凝结水22进入除氧器21,然后通过给水泵20泵入给水加热器19进行加热,然后进入给水附加加热器18与汽汽换热器16热侧出口引出的供热再热蒸汽换热,回收供热再热蒸汽加热高参数供热蒸汽后的余热,换热后的工质,即供热再热蒸汽,进入除氧器21,实现再热加热蒸汽能量和工质的回收,完成工质循环的闭环;而换热后的给水23回到锅炉给水中,完成循环。
35.本实施例中供热蒸汽由高压缸抽出,蒸汽压力为6.07mpa,蒸汽温度为386℃;蒸汽再热系统蒸汽自热再蒸汽,蒸汽压力为3.2mpa,温度为538℃;高参数热用户所需蒸汽温度为430℃;汽汽换热器端差取10℃,蒸汽源再热系统(抽汽口至换热器出口)压损均取0.3mpa,采用本发明系统供热方案见表2:
36.表2本发明供热方案
37.项目压力(mpa)温度(℃)焓值(kj/kg)流量(t/h)高参数供热蒸汽(抽汽口)6.073863142.61100高参数供热蒸汽(换热后)4.34303280.90100供热加热抽汽口3.25383539.2244.03供热加热蒸汽(换热后)2.93963225.1244.03
38.由表中数据可以看出供热需要抽取100t/h高参数供热蒸汽,再抽取加热需要44.03t/h增温热源蒸汽,可以满供热需求。此方案供热蒸汽经过做功后再供热,对供热蒸汽
进行了能量梯级利用,回收供热蒸汽做功能力;对供热加热蒸汽也进行了梯级利用,减少供热损失,实现梯级利用,提高能源利用效率。
39.对比例
40.如图1所示,为常规减温减压高参数供热系统,采用主蒸汽15减温减压后供热,在主蒸汽15上设置抽气点抽取高参数供热抽汽1,高参数供热抽汽1经供热减温减压阀25喷入供热减温水24进行减温减压后形成高参数供热蒸汽6。
41.本对比例中主蒸汽15压力为16.67mpa,蒸汽温度为538℃,高参数供热蒸汽6蒸汽压力为4.3mpa,蒸汽温度为430℃;减温水压力为18mpa,温度为158℃,则其供热方案见表1:
42.表1常规减温减压供热方案
43.项目压力(mpa)温度(℃)焓值(kj/kg)流量(t/h)主蒸汽供热抽汽压力16.675383397.2695.72减温水18158677.314.28高参数供热蒸汽4.34303280.90100
44.由上表可以看出,采用常规供热方案,需要抽取95.7t/h的供热蒸汽和4.28t/h的减温水混合,满足100t/h供热蒸汽,此时供热蒸汽未进行做功,直接供热,属于热电分产,所以造成了很大的浪费。
45.由上述实施例和对比例可以看出,本发明通过改造可以灵活满足供热需求,且可以提高能源利用效率,具有良好的节能效果。
46.本发明的技术方案不局限于上述各实施例,凡采用等同替换方式得到的技术方案均落在本发明要求保护的范围内。