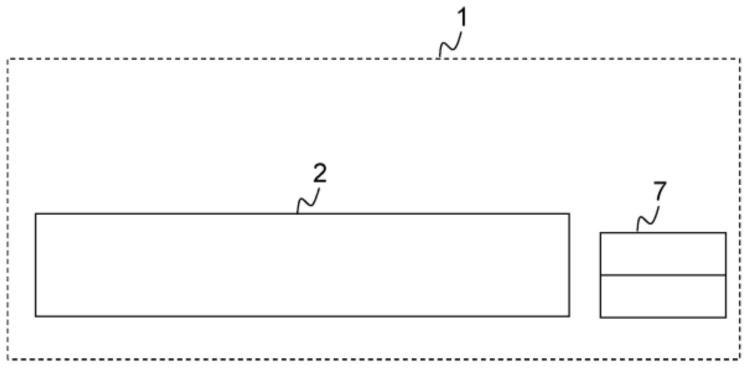
用于改造热处理设备的方法
1.本发明涉及一种用于改造热处理设备的方法。本发明尤其可用于改造现有的压淬生产线,在该压淬生产线中,压淬工具被布置在连续炉的下游,特别是辊道炉的下游。改造后的热处理生产线的好处是在需要时允许对金属组件进行部分热处理。
2.为了制造由钢板制成的与安全相关的车身部件,通常需要在形成车身组件的过程中或之后使钢板硬化。为此,建立了一种热处理方法,其被称为“压淬”。在这种情况下,通常以板材形式提供的钢板首先在炉中加热,然后在压力机中成型时冷却,从而硬化。
3.多年来,人们一直在努力通过压淬法生产机动车辆的车身组件,例如a柱和b柱、车门中的侧面碰撞保护构件、车底板、车架部件、保险杠、车底和车顶的横梁,以及前后侧梁,上述组件在子区域中具有不同的强度,从而使车身组件可以在不同的部分实现不同的功能。例如,车辆的b柱的中心区域应具有高强度,以在发生侧面碰撞时保护乘员。同时,b柱的上端区域和下端区域应具有相对较低的强度,以便在侧面碰撞期间吸收形变能,并且在b柱的装配期间便于与其它车身组件连接。
4.为了形成这种部分硬化的车身组件,硬化组件必须在子区域中具有不同的强度特性。为此,例如,在新的设备中,可以在熔炉和压淬工具之间设置一个或多个温度控制站。在这种情况下,该温度控制站被设置和设计成在组件的子区域中设定不同的温度(所述子区域最初被均匀地加热),从而在随后的压淬过程中,所述子区域产生不同的强度特性。在这种情况下,可以实现最佳循环时间,其尤其在车辆工业中发挥重要作用,特别是如果熔炉、温度控制站和压淬工具元件“成直线”排列,即直接连续地排列。
5.如果要用温度控制站对现有的设备进行改造,通常可以观察到没有足够的空间用于“串联”布置,因此所述温度控制站被放置在其他地方;例如,它必须相对于熔炉和/或压淬工具横向偏移放置(从生产量方向看)。在这样的安排下,最佳循环时间只能在困难的情况下实现,或者根本无法实现。
6.即使在改造的情况下,存在用于“成直线”排列的必要空间,也会出现问题,因为常规的压淬方法(可选地)通常仍然能够在改造的设备上进行。然而,这里的问题是,在所述熔炉出口和所述压淬工具之间的所述温度控制站(其在常规操作中被关闭)的布置导致从熔炉到压淬工具的传输延迟,这可能导致在进入压淬工具之前出现不需要的强冷却。
7.在此基础上,本发明的目的是至少部分地解决现有技术中描述的问题。特别地,提供一种用于改造热处理设备的方法,该设备既允许在工业规模上尽可能有效地对部件中的金属组件进行不同的热处理,并且特别地,允许尽可能有效地进行常规的压淬方法。
8.这些目的是通过独立权利要求的特征来实现的。在从属权利要求中具体说明了本文提出的解决方案的进一步的有利实施例。应当注意的是,在从属权利要求中单独列出的特征可以以任何技术上有意义的方式彼此组合,并且限定本发明的进一步的实施例。此外,在说明书中更详细地描述和解释了权利要求中规定的特征,从而展示了本发明的进一步的优选实施例。
9.根据本发明的用于改造热处理设备的方法至少具有以下步骤:
10.a)将连续炉分为第一炉和第二炉,
11.b)在所述热处理设备中设置温度控制站,其中所述温度控制站被设置在所述第一炉的下游和所述第二炉的上游,并且其中,所述温度控制站被进一步地设置和设计成设定待处理的金属组件的至少第一子区域和至少第二子区域之间的温差,以及
12.c)调整所述热处理设备的操作模式。
13.以常规方式执行该方法产生所示的方法步骤顺序a)、b)和c)。可以同时、顺序和/或至少部分并行地执行单个或多个所述方法步骤。
14.所提出的方法优选地用于改造具有连续炉和压淬工具的热处理设备或热处理生产线。所述压淬工具被设置在(待改造)连续炉的下游。特别地,所述压淬工具被设置和设计成同时或至少部分并行地使所述组件成型并且(至少部分地)对其进行淬火。所述连续炉可以是辊道炉。优选地,待改造的所述热处理设备和/或改造后的所述热处理设备“成直线”排列。所述待改造的热处理设备的连续炉和压淬工具,即所述第一炉、所述温度控制站、所述第二炉和所述压淬工具(按所述顺序)优选地直接依次排列。
15.金属组件(待通过热处理设备进行处理)优选地为金属板、钢板或至少部分预成型的半成品。优选地,所述金属组件由(可硬化的)钢制成,例如硼(锰)钢,如22mnb5钢。更优选地,所述金属组件至少大部分设置有或预涂有(金属)涂层。所述金属涂层可以是例如(主要)含锌涂层或(主要)含铝和/或含硅涂层,特别是所谓的铝/硅(al/si)涂层。
16.在步骤a)中,将(现有的)连续炉,特别是辊道炉,划分为第一炉和第二炉。优选地,所述划分以所述第一炉和所述第二炉各自形成连续炉,特别是形成辊道炉这样的方式进行。可选地,所述划分可以以所述第一炉形成连续炉,所述第二炉形成箱室炉这样的方式进行。所述划分可以通过机械和/或热分裂的方式进行。
17.根据一个有利的实施例,建议在步骤a)中移除连续炉的区域。这尤其是以这样的方式实现的,即,(在连续炉中)形成用于温度控制站的自由空间。
18.在步骤b)中,在所述热处理设备中设置温度控制站,其中所述温度控制站被(直接)设置在所述第一炉的下游并且被(直接)设置在所述第二炉的上游。所述温度控制站被设置和设计成设定待(通过热处理设备)处理的金属组件的至少第一子区域和至少第二子区域之间的温度差。为此,所述温度控制站可具有一个或多个喷嘴,所述喷嘴被设置和设计成用于向所述组件的所述至少第一子区域排放(冷却)流体。
19.根据一个有利的实施例,建议在步骤b)中所述温度控制站被设置在所述第一炉和所述第二炉之间。优选地,所述温度控制站以这样的方式被设置,即所述第一炉、所述温度控制站和所述第二炉(按所述顺序)以尤其是直接连续的方式排列。“直接连续”是指在这种情况下,尤其是在所述温度控制站和所述相应的炉之间不设置用于热处理的其他部件。然而,在所述温度控制站与所述第一炉和/或所述第二炉之间可以设置至少0.5m(米)的(最小)距离。换句话说,优选地,在步骤b)中,所述温度控制站与所述第一炉和所述第二炉成直线式排列。
20.在步骤c)中,调整所述热处理设备的操作模式。如果在待改造的所述热处理设备中提供了多个操作模式,则在可以步骤c)中调整或改变热处理设备的一个或多个所述操作模式,或者甚至所有操作模式。
21.根据一个有利的实施例,建议在步骤c)中,对所述热处理设备的所述操作模式进行调整,以便与通过所述连续炉的生产速度相比,通过所述第一炉的生产速度降低,尤其是
如果部分热处理,特别是淬火,通过所述(改造的)热处理设备进行或所述(改造的)热处理设备在第一操作模式下操作,其中至少一个金属组件的第一子区域和第二子区域之间的温度差通过所述温度控制站在组件中进行设置。优选地,通过所述第一炉的所述生产速度降低到0.01至1m/s[米/秒]范围内的速度,特别是0.08至0.3m/s范围内的速度。
[0022]
优选地,在使用(改造的)热处理设备进行部分热处理时优选设置的所述降低的生产速度增加了可完成的循环时间;然而,如果只有相对较少的组件要进行部分热处理,如果该过程能够“成直线”实施,这会是一个非常明智的解决方案。
[0023]
根据另一个有利的实施例,建议在步骤c)中,对所述热处理设备的所述操作模式进行调整,使得所述第二炉中的炉内温度高于(待改造的)所述连续炉的(最大或最高)炉内温度,特别地,如果没有通过所述(改造的)热处理设备进行部分热处理,或者所述(改造的)热处理设备以第二操作模式操作,在所述第二操作模式中,所述组件的第一子区域和第二子区域之间没有设置温度差。优选地,与所述(待改造的)连续炉的所述(最大)炉内温度相比,所述第二炉中的炉内温度增加了至少10k,或甚至至少20k。
[0024]
在所述第二炉中提高所述炉内温度具有特殊优势,即可以使用(改造的)热处理设备以尽可能少的循环时间损失继续实施传统的压淬过程。由于所述温度控制站的原因,经常会损失大量可用炉子长度。为了弥补这一点,提高所述第二炉中的温度是优选的方法。通过这种方式,尽管减少了炉子的长度,但仍可以达到所需的最终温度。此外,(仅)提高所述第二炉中的温度有一个优点,即在停止的情况下,在温度升高的炉子中的组件可能达到过高的温度,只有位于所述第二炉中的这一些组件必须被丢弃,因此损害可以得到限制。如果所述第一炉和所述第二炉中的温度由于炉长的整体缩短而增加,则必须丢弃整个炉料。除了材料损失外,还必须考虑炉子“排空”过程中的停止时间。
[0025]
可选地,在步骤c)中,优选地对热处理设备的操作模式进行调整,使得所述第二炉中的炉内温度低于或刚好等于所述(待改造)连续炉的(最大)炉内温度。
[0026]
优选地,假设如果在(调整后的)操作模式中,在(有意)中断的情况下,以所述第二炉为空炉的方式选择循环的结束。然后,如有必要,不必丢弃任何组件。特别优选地使用来自例如设置在所述第一炉和/或所述第二炉下游的高温计的温度测量数据来确定循环的结束。
[0027]
在所述第一炉和/或所述第二炉中的相关的炉子长度上设定不均匀的温度分布或不同的温度区是有用的,所述第一炉和/或所述第二炉中的每一个都可以被设计为连续炉。优选地,在所述第一炉中(在生产量方向上)设置不同的温度区,而在所述第二炉中设置基本均匀的炉内温度。
[0028]
还提出了一种用于操作根据本文提出的方法改造的热处理设备的方法,其中,在所述热处理设备的第一操作模式中,通过所述温度控制站在组件中设定至少一个金属组件的第一子区域和第二子区域之间的温差,并且其中,在所述热处理设备的第二操作模式中,通过所述温度控制站在组件中没有(有意或故意设定)至少另一个金属组件的第一子区域和第二子区域之间的温差。
[0029]
通常,所述温度控制站配备有特定于组件的插入件,该插入件可以实现对组件中具有不同强度的部件的第一区域和第二区域进行不同的温度控制。如果要生产的组件不具有不同的第一区域和第二区域,而是在整个组件上具有近似均匀的强度,则可以由通道元
件代替单元,所述通道元件将所述部件与周围环境隔热。这减少了来自所述部件的热辐射,并且因此减少了所述部件在从所述第一炉到所述第二炉途中的温度损失。优选地,可以设置额外的加热装置,所述加热装置将通道元件的内部保持在升高的温度,以便显著减少由于与周围环境相比的温差较小而导致的热损失。特别优选地,所述通道元件可以被加热,使得内部温度大致对应于所述第一炉或所述第二炉的内部温度。因此,可以在很大程度上避免部件中的温度下降。
[0030]
可选地,建议将通道元件的内部温度设置为略高于所述第一炉中的温度,以进一步缩短循环时间。与所述第二炉中可能的温度升高类似,应该使用所述控制器中的适当的组件跟踪来监测在这种情况下,不会超过在所述通道元件中组件的最大允许停留时间,这可能导致组件本身不允许的温度升高。根据这种方法,与原始设备相比,可以不需要增加所述第一区域和第二区域中不需要不同温度控制的组件的生产时间。如有必要,通过提高所述通道元件和/或所述第二炉的内部温度,与原始设备相比还可以减少总生产时间。
[0031]
根据一个有利的实施例,建议在第一操作模式期间至少执行以下步骤:
[0032]
a1)在所述第一炉中加热(整个)部件,特别是通过辐射热和/或对流的方式,优选地至少500k[开尔文],特别优选地至少650k或甚至至少750k,
[0033]
b1)将所述组件移入所述温度控制站,
[0034]
c1)冷却,特别是对流地冷却所述温度控制站中的组件的至少第一子区域,其中,所述组件的所述至少第一子区域和所述至少第二子区域之间的温差优选地设置为至少50k或甚至至少100k,
[0035]
d1)将所述部件从所述温度控制站移至所述第二炉,以及
[0036]
e1)在所述第二炉中,特别是通过辐射热和/或对流的方式,对所述组件的至少第一子区域进行加热,优选地至少100k,特别是至少150k或甚至至少200k。
[0037]
根据另一个有利的实施例,建议(在步骤a1中)所述组件以0.01至1m/s[米/秒]范围内的速度移动通过所述第一炉。所述部件优选地以0.08至0.3m/s范围内的速度移动通过所述第一炉。
[0038]
根据另一个有利的实施例,建议在第二操作模式期间至少执行以下步骤:
[0039]
a2)在所述第一炉中加热所述组件,特别是通过辐射热和/或对流的方式,以及
[0040]
e2)在所述第二炉中加热所述组件,特别是通过辐射热和/或对流的方式。根据又一个有利的实施例,建议在步骤a2和e2之间至少执行以下步骤:
[0041]
b2)将所述部件移入所述温度控制站,
[0042]
c2)降低所述组件的冷却速率或在所述温度控制站中加热所述组件,特别是通过辐射热的方式,以及
[0043]
d2)将所述组件从所述温度控制站移至所述第二炉。
[0044]
结合与在开始时提出的方法相关讨论的细节、特征和有利实施例也可以根据这里提出的方法进行,反之亦然。在这方面,为了更好地表征特征而完全参考这里的陈述。
[0045]
将参照附图更详细地解释本发明和技术环境。应该注意的是,本发明不应受到所示实施例的限制。特别地,除非另有明确说明,否则还可以从附图中解释的事实中提取部分方面,并将它们与其他组件和/或来自其他附图和/或来自本说明书的见解相组合。在附图中,示意性地示出:
[0046]
图1:示出了可以使用本文提出的方法进行改造的已知的热处理设备,以及
[0047]
图2:示出了根据图1的热处理设备,该设备使用本文提出的方法进行了改装。
[0048]
图1示意性地示出了可以使用本文提出的方法进行改造的已知热处理设备1。热处理设备1具有压淬工具7,该压淬工具7(直接)布置在连续炉2的下游。因此,热处理设备1在这里表示压淬生产线。
[0049]
图2示出了根据图1的热处理设备1,该热处理设备1使用本文提出的方法进行了改造。为此,将连续炉分为第一炉3和第二炉4。然后,温度控制站5被设置在热处理设备1中,其中温度控制站5被(直接)设置在第一炉3的下游和第二炉4的上游。温度控制站5被设置和设计成用于设定待处理的金属组件6的至少第一子区域和至少第二子区域之间的温差。
[0050]
因此,提供了一种用于改造热处理设备的方法,该方法至少部分地解决了参考现有技术概述的问题。特别地,该方法允许改造热处理设备,这既能够在工业规模上尽可能有效地对部件中的金属组件进行不同的热处理,并且特别地,可以尽可能有效地进行常规的压淬方法。
[0051]
参考符号列表
[0052]
1热处理设备
[0053]
2连续炉
[0054]
3第一炉
[0055]
4第二炉
[0056]
5温度控制站
[0057]
6组件
[0058]
7压淬工具