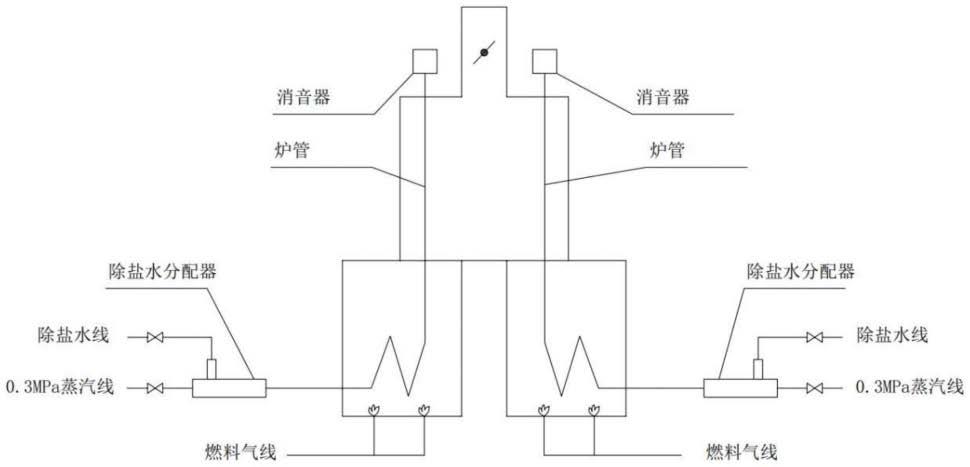
1.本发明涉及一种设施及方法,更具体一点说,涉及一种双炉膛加热炉烘炉设施及方法,属于加热炉设施领域。
背景技术:2.化工装置中,加热炉是一种常见的设备,其中,管式加热炉广泛应用于炼油化工装置,加热炉在施工过程中,内衬砖砌体及耐火浇注料含大量游离水、结晶水及残余结合水,这些水分在加热炉点火投用后,会快速汽化膨胀,可能导致炉墙胀裂、鼓泡、变形甚至炉墙倒塌,因此必须在投产前对加热炉进行烘炉,使游离水、结晶水及残余结合水缓慢蒸发析出,并在高温下对炉墙浇注料进行烧结。烘炉过程中需要根据浇注料产品特性所对应的烘炉曲线进行缓慢和均匀地加热,整个过程通常需要5至7天,目前普遍采用的烘炉方法:以装置油运物料或者氮气作为烘炉携热介质。因此必须等到燃料气系统等公用工程系统建设结束投用后才可以进行,而现在新建装置都要求建设投用时间尽量短,现有的烘炉设施及方法无法满足压缩投产时间的要求。
技术实现要素:3.为了解决上述现有技术问题,本发明提供具有结构简单,实用性强,可在1.0mpa蒸汽不具备的条件下实施烘炉,提前进行烘炉操作,可以提前检查发现问题,预留充足的整改时间,保证了烘炉效果,投产过程中可以跨过烘炉操作,节约了开工时间,提高了经济效益等技术特点的一种双炉膛加热炉烘炉设施及方法。
4.为了实现上述目的,本发明是通过以下技术方案实现的:
5.一种双炉膛加热炉烘炉设施,包括除盐水分配器、消音器以及带有燃料气线的加热炉,所述加热炉内设有炉管,所述炉管一端伸出加热炉连接有除盐水分配器,所述炉管另一端伸出加热炉连接有消音器,所述加热炉上端连接有烟道。
6.优选的,所述炉管通过法兰连接除盐水分配器,所述炉管通过法兰连接消音器。
7.优选的,所述除盐水分配器包括本体,所述本体内部设有主通道,所述本体上端连接有除盐水入口,所述主通道左端设有0.3mpa蒸汽入口,所述主通道的右端设有除盐水出口。
8.优选的,自左而右所述主通道包括依次连接且连通的第一通道、第二通道、第三通道、第四通道、第五通道,所述第一通道小于第二通道直径,所述第三通道直径逐渐减小,所述第四通道直径与第三通道最右端处直径相同,所述第五通道直径逐渐增大;所述除盐水入口与第二通道连通。
9.优选的,所述第一通道的右端延伸有直径逐渐变小的锥形管,所述锥形管伸进第三通道内,所述第三通道出口端处形成有混合室,所述锥形管出口端的蒸汽、除盐水入口的除盐水在混合室内混合并且流向第四通道。
10.优选的,所述除盐水入口连接临时的除盐水线,所述0.3mpa蒸汽入口连接临时的
0.3mpa蒸汽线。
11.优选的,所述加热炉设有多个且相互独立。
12.优选的,多个加热炉连接于同一个烟道上。
13.优选的,所述除盐水入口为法兰结构,便于与临时的除盐水线连接,所述0.3mpa蒸汽入口为法兰结构,便于与临时的0.3mpa蒸汽线连接,所述除盐水出口为法兰结构,便于与炉管连接。
14.本发明一种的双炉膛加热炉烘炉设施本烘炉的方法,该方法包括如下步骤:
15.步骤一:加热炉施工完成后,在环境温度下自然通风干燥5天以上,或在5℃以上环境自然通风干燥10天以上,打开除盐水分配器上的0.3mpa蒸汽线,向炉管内通入蒸汽,投用炉管顶部连接的消音器;
16.步骤二:点燃加热炉火嘴提高加热炉内的炉膛温度,通过控制炉膛火嘴燃料气量来控制炉膛温度,炉膛按照不大于15℃/h的升温速度升至150℃;
17.步骤三:炉膛温度控制150℃,恒温24小时,脱除自然水;
18.步骤四:150℃恒温脱水完毕后,炉膛按不大于15℃/h速度升温到350℃,升温过程中,监控好炉管表面温度,如果炉管表面温度接近400℃,则开大除盐水分配器上的0.3mpa蒸汽线手阀,增加向炉管内通入的蒸汽量;
19.步骤五:炉膛温度控制350℃,恒温24小时;
20.步骤六:350℃恒温完毕后,炉膛按不大于15℃/h速度升温到500℃,升温过程中,监控好炉管表面温度,如果炉管表面温度接近400℃,则开大除盐水分配器上的除盐水手阀,向炉管内通入除盐水;
21.步骤七:炉膛温度控制500℃,恒温24小时脱除结晶水;
22.步骤八:500℃恒温脱水完毕后,控制炉膛按不超过15℃/h速度升温到550℃,升温过程中,监控好炉管表面温度,如果炉管表面温度接近400℃,则开大除盐水分配器上的除盐水手阀,加大向炉管内通入的除盐水量;
23.步骤九:炉膛控制550℃恒温24小时烧结;
24.步骤十:炉膛550℃恒温烧结完毕后,控制炉膛按不超过25℃/h的速度降温至150℃,此阶段控制炉管表面温度不超过400℃,炉膛降温至150℃后,熄灭加热炉火嘴,停除盐水及0.3mpa蒸汽,关闭烟道挡板、停鼓风机/引风机,闷炉;
25.步骤十一:炉膛温度降到100℃时,打开风门、烟道挡板自然冷却至常温,烘炉完毕。
26.有益效果:结构简单,操作便捷,市场前景广阔,能够使新建加热炉可在1.0mpa蒸汽不具备的条件下实施烘炉,提前进行烘炉操作,可以提前检查发现问题,预留充足的整改时间,保证了烘炉效果,投产过程中可以跨过烘炉操作,节约了开工开工时间,额外投资小,操作灵活可控,提高了经济效益。
附图说明
27.图1是本发明整体结构示意图。
28.图2是本发明除盐水分配器的结构图。
具体实施方式
29.以下结合说明书附图,对本发明作进一步说明,但本发明并不局限于以下实施例。
30.实施例1:加热炉设有两个,分别为加热炉a、加热炉b,炉管分别为炉膛a炉管、炉膛b炉管;除盐水分配器分为除盐水分配器a、除盐水分配器b;消音器分分为消音器a、消音器b。实施例1中只是选择采用两个加热炉,具体情况下可以根据实际情况进行增加或减少。
31.具体的:加热炉a的炉膛a炉管出口(法兰处)安装有除盐水分配器a;加热炉b的炉膛b炉管出口(法兰处)安装除盐水分配器b;加热炉a的炉膛a炉管入口(法兰处)安装消音器a;加热炉b的炉膛b炉管入口(法兰处)安装消音器b;除盐水分配器a/b的除盐水入口处连接临时除盐水线;除盐水分配器a/b的0.3mpa入口连接临时0.3mpa蒸汽线;
32.除盐水分配器包括除盐水入口、0.3mpa蒸汽入口、除盐水出口;除盐水入口为法兰结构,便于与临时的除盐水线连接,0.3mpa蒸汽入口为法兰结构,便于与临时的0.3mpa蒸汽线连接;除盐水出口为法兰结构,法兰规格与加热炉的炉管出口的临时烘炉法兰规格一致,除盐水出口与加热炉炉管的临时烘炉法兰连接。
33.本技术创造性的采用如下除盐水分配器的结构:自左而右除盐水分配器上的主通道包括依次连接且连通的第一通道、第二通道、第三通道、第四通道、第五通道,第一通道小于第二通道直径,所述第三通道直径逐渐减小,第四通道直径与第三通道最右端处直径相同,第五通道直径逐渐增大;除盐水入口与第二通道连通,第一通道的右端延伸有直径逐渐变小的锥形管,锥形管伸进第三通道内,第三通道出口端出形成有混合室,锥形管出口端的蒸汽、除盐水入口的除盐水在混合室内混合并且流向第四通道,使得混合后流动更高效,结构新颖。
34.基于实施例1中的结构,进行烘炉,该烘炉方法包括以下步骤:
35.步骤一:加热炉施工完成后,在环境温度下自然通风干燥5天以上,或在5℃以上环境自然通风干燥10天以上,打开除盐水分配器a、除盐水分配器b上的0.3mpa蒸汽线,向炉膛a炉管、炉膛b炉管内通入蒸汽,投用炉管顶部连接的消音器;
36.步骤二:点燃加热炉火嘴提高炉膛温度,通过控制a/b炉膛火嘴燃料气量来控制炉膛温度,a/b炉膛按照不大于15℃/h的升温速度升至150℃;
37.步骤三:a/b炉膛温度控制150℃,恒温24小时,脱除自然水;
38.步骤四:150℃恒温脱水完毕后,a/b炉膛按不大于15℃/h速度升温到350℃。升温过程中,监控好炉管表面温度,如果炉管表面温度接近400℃,则开大除盐水分配器上的0.3mpa蒸汽线手阀,增加向炉管内通入的蒸汽量;
39.步骤五:a/b炉膛温度控制350℃,恒温24小时;
40.步骤六:350℃恒温完毕后,a/b炉膛按不大于15℃/h速度升温到500℃;升温过程中,监控好炉管表面温度,如果炉管表面温度接近400℃,则开大除盐水分配器上的除盐水手阀,向炉管内通入一定的除盐水;
41.步骤七:a/b炉膛温度控制500℃,恒温24小时脱除结晶水;
42.步骤八:500℃恒温脱水完毕后,控制a/b炉膛按不超过15℃/h速度升温到550℃,升温过程中,监控好炉管表面温度,如果炉管表面温度接近400℃,则开大除盐水分配器上的除盐水手阀,加大向炉管内通入的除盐水量;
43.步骤九:a/b炉膛控制550℃恒温24小时烧结;
44.步骤十:a/b炉膛550℃恒温烧结完毕后,控制a/b炉膛按不超过25℃/h的速度降温至150℃,此阶段控制炉管表面温度不超过400℃。炉膛降温至150℃后,熄灭加热炉火嘴,停除盐水及0.3mpa蒸汽,关闭烟道挡板、停鼓风机/引风机,闷炉;
45.步骤十一:a/b炉膛温度降到100℃时,打开风门、烟道挡板自然冷却至常温,烘炉完毕;
46.步骤四至步骤十中,需要根据炉管表面温度调节除盐水分配器的蒸汽量和除盐水量。通过通入炉管的除盐水量,控制a/b炉膛两根炉管的表面温度不超过400℃。
47.需要注意的是:针对不同浇筑料,各升温阶段升温速率、降温阶段降温速率可以相应变化。针对不同浇筑料,各恒温阶段恒温温度可以相应变化。针对不同浇筑料,各恒温阶段恒温时间可以相应变化。
48.最后,需要注意的是,本发明不限于以上实施例,还可以有很多变形。本领域的普通技术人员能从本发明公开的内容中直接导出或联想到的所有变形,均应认为是本发明的保护范围。