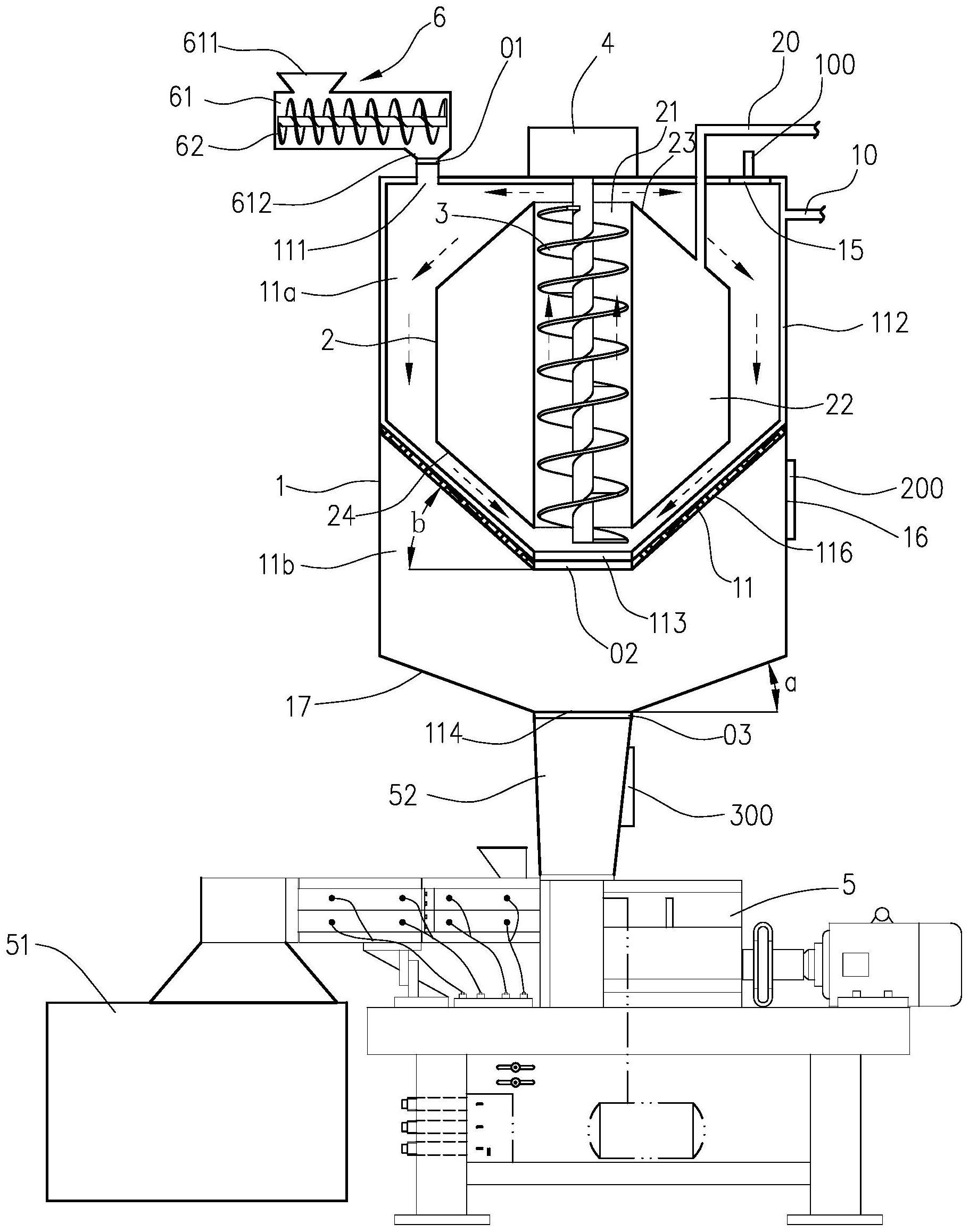
1.本发明涉及硫磺处理技术领域,具体指一种硫磺干燥及成型装置。
背景技术:2.硫磺为不良导体,在储运过程中易产生静电荷而导致硫尘起火,并且,干散硫磺由于极易污染环境、产生粉尘,在装卸和运输过程中存在爆炸危险。因此,必须将干散的硫磺转化为成型的硫磺进行储运,即把熔融状态的硫磺加工成具有一定尺寸和形状的固体颗粒。同时,溶剂萃取法获得的硫磺中含有大量的溶剂(甲苯、煤油、二硫化碳、四氯乙烯等),在硫磺成型之前必须对硫磺进行干燥,以获得更加优质的硫磺。
3.目前,工厂多采用硫磺干燥机对湿硫磺粉进行干燥处理,干燥机对硫磺粉处理的时间长,同时烘干的时间也较长,不仅降低了硫磺粉干燥处理的效率,也降低了工厂生产硫磺粉的效率;而在干燥机中设置搅拌结构,则由于硫磺分散度太高而容易引起爆炸。在成型硫磺时,市场上多通过熔硫釜熔融后将硫磺浇筑成锭子,然后用破碎机破碎得到合适大小颗粒的硫磺,采用这样的处理方式,由于破碎机无法得到大小均一的颗粒,增加了工艺步骤和操作步骤,而且在破碎的过程中,不可避免的会污染到硫磺,影响硫磺的品质。
4.因此,对于目前的硫磺干燥及成型装置,有待于做进一步的改进。
技术实现要素:5.本发明所要解决的技术问题是针对现有技术的现状,提供一种既能提高干燥效率及干燥效果,又安全性高、便于成型出特定大小颗粒的硫磺干燥及成型装置。
6.本发明解决上述技术问题所采用的技术方案为:
7.一种硫磺干燥及成型装置,包括:
8.箱体,所述箱体中部设置有隔板,该隔板将所述箱体内腔分隔为上下相对独立的上腔体、下腔体,所述上腔体的顶部开有进料口,所述上腔体内设置有贴近内壁布置的第一加热空腔;所述隔板上开有供上腔体中的物料落入下腔体中的开口,所述箱体底部开有供下腔体中的物料输出的出料口;
9.套筒,设于所述上腔体中,所述套筒中部设置有上下贯通从而供物料自下而上输送的送料通道,所述套筒内部中空形成有围绕送料通道外周布置的第二加热空腔;
10.提升叶轮,能转动地设于所述送料通道中,用于将物料自下而上提升;
11.驱动件,设于所述箱体之上且输出端与提升叶轮的顶部相连接;
12.第一热源通道,与所述第一加热空腔相连通,用以为第一加热空腔输送热源;
13.第二热源通道,与所述第二加热空腔相连通,用以为第二加热空腔输送热源;
14.第一呼吸阀,所述箱体顶部开有与上腔体相连通的第一排气口,所述第一呼吸阀设于第一排气口处,供干燥过程中产生的一类溶剂蒸汽输出、并保持上腔体内的微负压环境;
15.第二呼吸阀,所述箱体侧部开有与下腔体相连通的第二排气口,所述第二呼吸阀
设于该第二排气口处,供干燥过程中产生的二类溶剂蒸汽输出;
16.挤出成型装置,设于所述下腔体之下且与出料口相连通,用以将干燥后的物料成型为特定大小的颗粒。
17.优选地,所述箱体底部的出料口与挤出成型装置的进口之间通过竖向布置的导向通道连接,所述导向通道的长度为出料口直径的2~3倍,所述导向通道的侧壁上开有第三排气口,该第三排气口处安装有供二类溶剂蒸汽进一步输出的第三呼吸阀。在本发明中,导向通道的长度大于出料口的直径,以使物料在经过导向通道的过程中,挥发出的溶剂能进一步通过第三呼吸阀排出,进一步降低产品中的溶剂含量。
18.进一步优选,所述箱体底壁自边缘向出料口处逐渐向下倾斜形成第一导向锥面,所述箱体底壁与水平面之间的夹角a为15~30度。第一导向锥面有利于向出料口处引导物料,便于物料输出,而将第一导向锥面的坡度设置的较小,以避免物料输出太快,为物料下行提供一定的时间余量,便于使物料在经过导向通道过程中将挥发出的溶剂排出。
19.优选地,所述隔板自边缘向中央部位逐渐向下倾斜形成第二导向锥面,所述隔板与水平面之间的夹角b为35~50度。该结构便于在上腔体干燥物料完毕后,将物料快速经开口输往下腔体中。
20.优选地,所述套筒顶壁成形为自中央向边缘逐渐向下倾斜的第一导向斜面,相应的,所述套筒底壁成形为自边缘向中央逐渐向下倾斜的第二导向斜面;所述上腔体中形成有沿第二导向锥形面及第二导向斜面向下、经送料通道自下而上、沿第一导向斜面向外、经套筒与上腔体内壁之间的间隙向下的物料循环通道。本发明以提升方式使物料进行循环流动干燥,上述第一导向斜面、第二导向斜面一方面便于在上下位置处对物料进行引导,提高物料流动稳定性及顺畅性,另一方面,对应第一导向斜面、第二导向斜面的第二加热空腔热蒸汽源的流动及分布,提高加热均匀性。
21.优选地,所述下腔体中设置有贴近第二导向锥面布置的隔热板,所述第二排气口及第二呼吸阀在水平方向上对应该隔热板布置。由于本发明要求上腔体中具有较高的温度、下腔体中具有较低的温度,采用上述结构,以避免上腔体的高温环境对下腔体的环境造成影响。
22.为了更好的控制干燥及成型过程,所述进料口处设置有用以控制其开关的第一阀门;所述开口处设置有用以控制其开关的第二阀门;所述出料口处设置有用以控制其开关的第三阀门。
23.在本发明中,所述箱体之上设置有用于进料的进料结构,该进料结构包括横向布置的进料筒,该进料筒的顶部设置有靠近第一端布置的进料端口、底部设置有靠近第二端布置的出料端口,该出料端口与所述箱体的进料口相连接,所述进料筒中设置有用于输送物料的螺杆。所述挤出成型装置包括有沿物料输送方向依次布置的熔融部分、挤出成型部分、切粒部分、快速风冷部分及成品接收部分。
24.本发明在干燥过程中,所述上腔体控温在70~85℃,干燥时间为2~3h,不超过3h;所述下腔体内温度为30~55℃。控温对本发明的干燥效果极为关键,这是因为:溶剂萃取法获得的硫磺所含有的溶剂中,大多沸点较高,需要以较高的温度进行干燥,而二硫化碳沸点很低,在以较高温度进行干燥时,二硫化碳反而会与硫磺结合性更好,从而降低二硫化碳的去除效果,因此,需要在上腔体中采用较高的干燥温度,主要用于去除大部分溶剂,在下腔
体中采用较低的干燥温度,主要用于去除二硫化碳;同时,由于硫磺呈粉尘状,如果上腔体中的干燥温度过高、干燥时间过长,容易引起爆炸,因此,将干燥温度控制在70~85℃,干燥时间不超过3时间;在下腔体中,不存在加热过程,仅依靠物料余热提供烘干热量,温度一般在30~55℃,消除了高温下二硫化碳与硫磺的结合力,从而进一步挥发并去除;由于挤出成型装置需要涉及吸热的熔融过程,本发明的下腔体还起到保温作用,降低热量流失,从而降低能耗。
25.与现有技术相比,本发明的优点在于:本发明提供了一种集干燥、成型为一体的硫磺处理装置,其中,干燥装置分为可高温干燥的上腔体及余热干燥的下腔体,上腔体中通过提升叶轮使物料形成上下循环的流动路径,从而使物料能均匀接触热源,起到更好的干燥效果、提高干燥效率;并且,向上主动提升、向下自然流动的方式,使分散性高的硫磺流动稳定而和缓,从而避免爆炸、提高了安全性;干燥完毕后直接借助硫磺余热进入成型装置,能在节约能耗的基础上,快速成型出特定大小的硫磺颗粒,便于生产。
附图说明
26.图1为本发明实施例的结构示意图。
具体实施方式
27.以下结合附图实施例对本发明作进一步详细描述。
28.如图1所示,本实施例的硫磺干燥及成型装置包括箱体1、套筒2、提升叶轮3、驱动件4、第一热源通道10、第二热源通道20、第一呼吸阀100、第二呼吸阀200、第三呼吸阀300、挤出成型装置5。
29.其中,箱体1中部设置有隔板11,该隔板11将箱体1内腔分隔为上下相对独立的上腔体11a、下腔体11b,上腔体11a的顶部开有进料口111,上腔体11a内设置有贴近内壁布置的第一加热空腔112;隔板11上开有供上腔体11a中的物料落入下腔体11b中的开口113,箱体1底部开有供下腔体11b中的物料输出的出料口114。进料口111处设置有用以控制其开关的第一阀门01,开口113处设置有用以控制其开关的第二阀门02,出料口114处设置有用以控制其开关的第三阀门03,第一阀门01、第二阀门02、第三阀门03均为电磁阀,以便于控制。
30.套筒2设于上腔体11a中,套筒2可以在底部、侧部设置支撑在上腔体11a内壁上的连接臂,用以固定套筒2。套筒2中部设置有上下贯通从而供物料自下而上输送的送料通道21,套筒2内部中空形成有围绕送料通道21外周布置的第二加热空腔22。
31.提升叶轮3为轴流叶轮,能转动地设于送料通道21中,用于将物料自下而上提升。提升叶轮3的上端与送料通道21的上边缘相齐平、下端伸出于送料通道21的下端口之下。驱动件4为电机,设于箱体1的顶部之上,驱动件4的输出端与提升叶轮3顶部中央的轴相连接,用以驱动提升叶轮3转动。
32.第一热源通道10与第一加热空腔112相连通,用以为第一加热空腔112输送蒸汽作为热源;第二热源通道20与第二加热空腔22相连通,用以为第二加热空腔22输送蒸汽热源。本实施例采用蒸汽作为加热热源,当然,也可以采用热水作为加热热源。
33.箱体1顶部开有与上腔体11a相连通的第一排气口15,第一呼吸阀100设于第一排气口15处,供干燥过程中产生的一类溶剂蒸汽输出、并保持上腔体11a内的微负压环境。一
类溶剂指的是沸点较高的溶剂。箱体1外可以设置用于抽气形成微负压的结构,以保持上腔体11a中压力在-80~-250kpa范围内,以降低溶剂的沸点,提升蒸馏效率。箱体1侧部开有与下腔体11b相连通的第二排气口16,第二呼吸阀200设于该第二排气口16处,供干燥过程中产生的二类溶剂蒸汽输出。二类溶剂是指沸点较低的溶剂,本实施例中主要是二硫化碳。
34.挤出成型装置5设于下腔体11b之下且与出料口114相连通,用以将干燥后的物料成型为特定大小的颗粒。挤出成型装置5包括有沿物料输送方向依次布置的熔融部分、挤出成型部分、切粒部分、快速风冷部分及成品接收部分51,本实施例的挤出成型装置5为双螺杆造粒设备,是现有成熟设备,具体结构及作用原理在此不做赘述。
35.在本实施例中,箱体1底部的出料口114与挤出成型装置5的进口之间通过竖向布置的导向通道52连接,导向通道52的长度为出料口114直径的2~3倍,导向通道52的侧壁上开有第三排气口,该第三排气口处安装有供二类溶剂蒸汽进一步输出的第三呼吸阀300。导向通道52的长度大于出料口114的直径,以使物料在经过导向通道52的过程中,挥发出的溶剂能进一步通过第三呼吸阀300排出,进一步降低产品中的溶剂含量。
36.本实施例的箱体1底壁自边缘向出料口114处逐渐向下倾斜形成第一导向锥面17,箱体1底壁与水平面之间的夹角a为15~30度。第一导向锥面17有利于向出料口114处引导物料,便于物料输出,而将第一导向锥面17的坡度设置的较小,以避免物料输出太快,为物料下行提供一定的时间余量,便于使物料在经过导向通道过程中将挥发出的溶剂排出。隔板11自边缘向中央部位逐渐向下倾斜形成第二导向锥面115,隔板11与水平面之间的夹角b为35~50度。该结构便于在上腔体11a干燥物料完毕后,将物料快速经开口输往下腔体11b中。
37.套筒2顶壁成形为自中央向边缘逐渐向下倾斜的第一导向斜面23,相应的,套筒2底壁成形为自边缘向中央逐渐向下倾斜的第二导向斜面24。上腔体11a中形成有沿第二导向锥形面115及第二导向斜面24向下、经送料通道21自下而上、沿第一导向斜面23向外、经套筒2与上腔体11a内壁之间的间隙向下的物料循环通道。本实施例以提升方式使物料进行循环流动干燥,上述第一导向斜面、第二导向斜面一方面便于在上下位置处对物料进行引导,提高物料流动稳定性及顺畅性,另一方面,对应第一导向斜面、第二导向斜面的第二加热空腔热蒸汽源的流动及分布,提高加热均匀性。
38.下腔体11b中设置有贴近第二导向锥面115布置的隔热板116,第二排气口16及第二呼吸阀200在水平方向上对应该隔热板116布置。由于本实施例要求上腔体11a中具有较高的温度、下腔体11b中具有较低的温度,采用上述结构,以避免上腔体11a的高温环境对下腔体11b的环境造成影响。
39.在本实施例中,箱体1之上设置有用于进料的进料结构6,该进料结构6包括横向布置的进料筒61,该进料筒61的顶部设置有靠近第一端布置的进料端口611、底部设置有靠近第二端布置的出料端口612,该出料端口612与箱体1的进料口111相连接,进料筒61中设置有用于输送物料的螺杆62。
40.本实施例在使用时:
41.初始状态下,第三阀门03将出料口114关闭、第二阀门02将开口113关闭;待干燥硫磺经进料结构6输入上腔体11a中,在进料过程中,电机驱动提升叶轮3旋转,第一加热空腔112中通入蒸汽初步加热;进料完毕后,第二加热空腔22中通入蒸汽辅助加热,使上腔体11a
中的温度升至70~80℃,在提升叶轮3不断提升物料状态下进行干燥;干燥时间为120min,在0-40min内,提升叶轮3的转速为70r/min,在40-100min内,提升叶轮3的转速调整为50r/min,在100-120min内,提升叶轮3的转速调整为30r/min,随着硫磺的干燥度提高,降低转速可减少扬尘,以减少硫磺损失及爆炸风险;干燥过程中,始终通过第一排气口15将去除的溶剂蒸汽排出,并通过抽负压使上腔体11a中压力保持在-100~-110kpa;
42.第二阀门02将开口113打开,上腔体11a中的物料输往下腔体11b中,下料完毕后,第二阀门02将开口113关闭;此时,进料结构6可再次进行,上腔体11a中继续干燥下一批硫磺;进入下腔体11b中的硫磺降温、并利用余热继续干燥,溢出的气体通过第二呼吸阀200排出;干燥完毕后的硫磺湿度小于0.8%;
43.第三阀门03将出料口114打开,硫磺输往挤出成型装置5进行造粒,在输往挤出成型装置5的过程中,未经排出的溶剂蒸汽再次经第三呼吸阀300排出;挤出成型装置5运行完毕后得到2~6mm的硫磺颗粒。
44.在本发明的说明书及权利要求书中使用了表示方向的术语,诸如“前”、“后”、“上”、“下”、“左”、“右”、“侧”、“顶”、“底”等,用来描述本发明的各种示例结构部分和元件,但是在此使用这些术语只是为了方便说明的目的,是基于附图中显示的示例方位而确定的。由于本发明所公开的实施例可以按照不同的方向设置,所以这些表示方向的术语只是作为说明而不应视作为限制,比如“上”、“下”并不一定被限定为与重力方向相反或一致的方向。