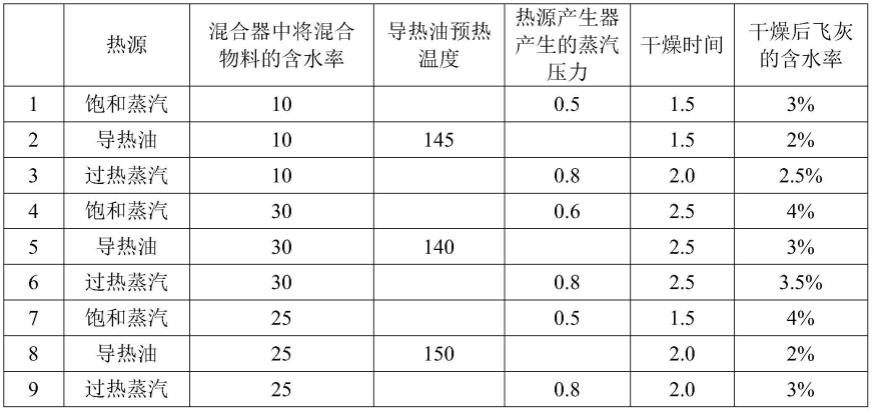
1.本发明属于生活垃圾焚烧飞灰处理技术领域,涉及一种水洗飞灰间接干燥的系统和方法。
背景技术:2.近些年来,我国生活垃圾焚烧处理量呈现逐年上升的趋势,日益增长的生活垃圾焚烧量导致其副产物——飞灰产量逐年升高,生活垃圾焚烧飞灰由于含有重金属、二噁英、呋喃等有毒物质,被多个国家认定为危险废物,因此,飞灰的处置至关重要。
3.飞灰虽然为危险废物,但飞灰的主要成分为钙、硅化合物及可溶性盐,可进行资源化处置,如水泥窑协同处置、高温烧结、等离子体熔融等。然而,飞灰中可溶性盐会对后续高温处置窑炉造成影响,需对飞灰进行脱盐预处理。飞灰水洗可有效脱除其中的可溶性盐含量,为飞灰资源化处置前必不可少的预处理环节。飞灰经过水洗预处理,可提取其中可溶性盐,进行工业化利用,水洗后飞灰可作为建材原料,节约原料、降低成本。
4.飞灰水洗预处理过程中,通常采用离心机进行固液分离,分离后的水洗飞灰含水率约为30%-40%,若直接进行高温煅烧资源化处置会对高温窑炉造成很大的影响,且能耗较大。因此,需对水洗飞灰进行干燥处理。目前,水洗飞灰通常选用直接干燥的方式,利用资源化企业的现有热源,通过与水洗飞灰的直接接触降低其含水率,此方法传热效率高,水洗飞灰干燥效率好,然而,该方式需利用资源化企业现有热源,且热源消耗量较大,易对资源化企业现有生产线造成影响。此外,水洗飞灰直接干燥的方式产生的尾气量较大,且尾气中颗粒物含量较大,后续尾气处理压力大。
5.飞灰的粒径较细(1-100μm),粘性较大,在干燥过程中容易发生挂壁的情况,且易板结,清理较为困难,且影响干燥效率;若飞灰含水率较高,在干燥过程中,易发生“抱团”现象,即“团状”飞灰表面呈干燥状态,但“团状”内部含水率仍然较高。因此,含水率较高的飞灰直接进行干燥处理难度较大。针对现有技术的不足,并结合飞灰的物理特性,本发明提出了一种水洗飞灰间接干燥的系统和方法,采用间接干燥的方式干燥水洗飞灰,可将水洗飞灰的含水率从40%降低至5%以下,解决了直接干燥方式带来的能耗高、尾气处理难的问题,并解决了间接干燥容易发生的挂壁、板结等问题,进一步优化了飞灰水洗预处理中的干燥环节,可提高飞灰资源化处置能力。
6.(一)现有技术一涉及一种低温蒸汽间接干燥褐煤的工艺和系统装置,系统装置主要包括原煤仓、给煤机、干燥机、旋转密封给料阀、埋刮板输送机、冷凝罐、疏水器、冷凝液泵、除尘器、风机。详细工艺步骤为:
①
将含水量质量百分比为35%~50%、粒度≤20mm的褐煤从原煤仓通过给煤机进入干燥机的干燥管内;
②
将低温蒸汽通入步骤
①
中的干燥机的干燥管外,使干燥管内的褐煤与干燥管外的蒸汽进行间接热交换,进而实现干燥褐煤的目的,所述低温蒸汽的压力为0.55~0.6mpag、温度为165~175℃;
③
步骤
②
中热交换后的冷凝液经疏水器进入冷凝罐;所述冷凝液最终由冷凝液泵排出;
④
步骤
②
中干燥后的褐煤从干燥机的出料口出来,经旋转密封给料阀进入埋刮板输送机;
⑤
步骤
②
所述褐煤干燥过程中,褐
煤产生的水蒸汽和带有煤粉的空气形成尾气,所述尾气在风机的抽吸下经除尘器过滤后排出;
⑥
步骤
⑤
中的除尘器过滤下的煤粉经落煤管进入埋刮板输送机。
7.该现有技术处理的原料为褐煤,粒度远远大于飞灰粒径,现有的间接干燥设备大多数应用于污泥、煤化工干燥行业,极少用于水洗飞灰干燥处理。虽说整体干燥工艺、设备类似,但由于飞灰的危废属性,以及飞灰特性,飞灰的间接干燥技术仍需解决一些问题,如飞灰粒径较细,设备磨损等问题,因此,水洗飞灰间接干燥技术属于一个全新的技术领域。
8.(二)现有技术二涉及一种污泥热干化系统及方法(发明申请)(cn 113371975 a)
9.(1)一种污泥热干化系统,包括空气压缩系统、换热系统及污泥干化系统,其特征在于,空气压缩系统,包括螺杆热泵,其用于将整个系统中循环的纯净蒸汽再次加热;
10.换热系统,包括降膜蒸发器,为纯净蒸汽的冷凝水换热蒸发;
11.污泥干化系统,包括干化机,用于降低污泥的含水率,将低水率的污泥排至燃料棒制作设备;
12.其中,空气压缩系统还包括气液分离器,经过螺杆热泵升温的高温蒸汽经过气液分离器后,进入干化机的换热机构中,将干化机内的污泥干化,换热机构中产生的冷凝水进入降膜蒸发器的壳程内,干化机产生的污泥蒸汽进入降膜蒸发器的管程内,将干化机的换热机构产生的冷凝水蒸发,蒸汽通过螺杆热泵升温后在系统内形成自循环,干化机的污泥蒸汽出口与降膜蒸发器之间设有水洗塔,水洗塔自循环洗气,水洗塔排出的废水至污水处理装置,降膜蒸发器的管程产生的不凝气至尾气处理装置。
13.(2)污泥热干化方法
[0014]ⅰ、设备预热:气液分离器中加入纯净水,纯净水经过管路进入降膜蒸发器中,降膜蒸发器内设置的加热装置先将纯净水蒸发形成洁净蒸汽,洁净蒸汽由降膜蒸发器的蒸汽出口进入螺杆热泵内压缩升温,形成高幅值的压缩热蒸汽,压缩热蒸汽经过气液分离器进入干化机的换热机构,将干化机预热;
[0015]ⅱ、污泥干化:将含水率为70%-90%的污泥通过螺旋给料机送入干化机内,在干化机的驱动轴的作用下,污泥在干化机内部受热逐渐干化,干化后的污泥沿干化机的排料口至燃料棒制作装置;
[0016]ⅲ、蒸汽循环:污泥干化过程中产生的污泥蒸汽沿干化机的污泥蒸汽出口经过水洗塔进入降膜蒸发器的管程内,同时,由干化机的换热装置外排的蒸馏水进入降膜蒸发器的壳程的喷淋口,喷淋口喷出的蒸馏水在换热管高温作用下蒸发形成洁净蒸汽循环;
[0017]
污泥蒸汽进过换热管换热后,形成的水进入水洗塔内,水洗塔将存储进来的水通过循环泵循环至水洗塔的水洗进水口,洗涤由干化机进来的污泥蒸汽中的杂质;
[0018]ⅳ、废弃物处理:降膜蒸发器在对纯净水蒸发的过程中,换热管内的部分污泥蒸汽转化为水进入水洗塔中,部分不凝气进入尾气处理管路至尾气处理装置,尾气处理管路连接板式换热器,为不凝气降温,板式换热器利用气液分离器的水进行降温;
[0019]
由水洗塔排出的污水进入螺旋给料机的套筒结构内,并经过料仓的预热层后,排出至污水处理装置。
[0020]
(3)技术不足
[0021]
利用降膜蒸发器产生蒸汽干化污泥,降低污泥含水率。未明确指出干化装置为间接干燥,但从描述可知干化设备为间接干燥设备,且提出了冷凝水以及二次蒸汽的循环利
用,整个系统较为成熟。然而,飞灰与污泥物理、化学性质均有很大差异,飞灰的粒径较细(1-100um),粘性较大,在干燥过程中容易发生挂壁的情况,且易板结,清理较为困难;若飞灰含水率较高,在干燥过程中,易发生“抱团”现象,即“团状”飞灰表面呈干燥状态,但“团状”内部含水率仍然较高。因此,含水率较高的飞灰不能直接进行干燥处理。
[0022]
综上所述,水洗飞灰的间接干燥系统和方法,需要结合飞灰的特性进行设计和实施。
技术实现要素:[0023]
针对现有技术的不足,本发明提出了一种水洗飞灰间接干燥的系统和方法,采用间接干燥的方式干燥水洗飞灰,为后续飞灰资源化利用提供技术保障。
[0024]
为解决上述技术问题,本发明提供的第一个技术方案如下:
[0025]
一种水洗飞灰间接干燥的系统,主要包括混料单元、热源产生单元、间接干燥单元、烟气处理单元、成品飞灰储存单元。
[0026]
所述混料单元为水洗飞灰间接干燥系统的入口,所述混料单元的出口与所述间接干燥单元的进料口相连,所述热源产生单元的出口与所述间接干燥单元的热源进口相连,所述间接干燥单元的粉尘气体出口与所述烟气处理单元的入口相连,所述间接干燥单元的出料口与所述成品飞灰储存单元的入口相连,所述成品飞灰储存单元的出口为水洗飞灰间接干燥系统的出口。
[0027]
所述混料单元包括混合器、飞灰输送装置。所述混合器设置两个进料口,分别为水洗飞灰进料口和干燥飞灰进料口,在所述混合器内干燥飞灰和水洗飞灰进行均质混合,降低物料整体含水率,并使物料保持均匀状态。
[0028]
进一步地,所述混合器的干燥飞灰进料口与所述成品飞灰暂存仓的出口相连。
[0029]
进一步地,所述混合器优选为卧式混合器,以便于进料,并易于控制混合时间。
[0030]
进一步地,所述飞灰输送装置优选为螺旋输送器,以便于控制干燥飞灰的混合量。
[0031]
所述热源产生单元包括软水器、热源产生器、冷凝水收集器、换热器。所述软水器的入口即所述热源产生单元的入口,所述软水器的出口与所述热源产生器的入口相连,所述热源产生器的出口与所述间接干燥机的热源进口相连。
[0032]
进一步地,所述软水器的入口与自来水管道相连,为热源产生器提供软水,防止热源产生器结垢、堵塞。
[0033]
进一步地,所述冷凝水收集器的入口与所述间接干燥机的冷凝水出口相连,所述冷凝水收集器的出口与所述热源产生器的入口相连,以稳定收集冷凝水,实现冷凝水的循环利用。
[0034]
进一步地,所述换热器的入口与所述烟气处理单元的出口相连,所述换热器的出口与所述间接干燥机的夹套进汽口相连,以便于间接干燥机外部夹套的保温,进一步提高飞灰的干燥效率。
[0035]
进一步地,所述换热器为烟气处理单元排出的高温烟气进行二次加热,以更好的实现热量的循环利用,降低系统能耗。
[0036]
进一步地,所述热源产生单元中输送饱和蒸汽的管道均设置保温层,以减少热量损失。
[0037]
所述间接干燥单元包括定量给料机、间接干燥机。所述定量给料机的出口与所述间接干燥机的进料口相连,所述间接干燥机的出料口与所述成品飞灰储存单元入口相连,所述间接干燥机的粉尘气体出口与所述烟气处理单元相连。
[0038]
进一步地,所述间接干燥机可选用转盘式干燥机、回转式干燥机、桨叶干燥机,以上间接干燥设备换热效率均较高,均可以满足本发明工艺系统要求。
[0039]
进一步地,所述定量给料机优选螺旋加料器,以保证进料均匀。
[0040]
进一步地,所述间接干燥机转轴为变频可调,以便于控制间接干燥时间,以更好地保证出料含水率。
[0041]
进一步地,所述间接干燥机的热源可选用饱和蒸汽、过热蒸汽或导热油,蒸汽和导热油为间接干燥设备常用的热源,均具有良好的热力学特性,热利用率高。
[0042]
进一步地,水洗飞灰间接干燥的系统建立在资源化处置企业时,可利用厂区内现有热源,以进一步节约能耗。若资源化企业有可利用饱和蒸汽热源,可通过降温降压装置对饱和蒸汽进行预处理,作为水洗飞灰间接干燥系统热源;
[0043]
进一步地,所述间接干燥机内部气体环境为微负压,以便于内部产生的携湿烟气排出,同时防止气体泄漏。
[0044]
进一步地,所述间接干燥机内部设有构筑件,以防止飞灰粘壁,并有利于保持飞灰的松散程度。
[0045]
进一步地,所述间接干燥机出料口设有下料阀,可自动控制下料速度。
[0046]
所述烟气处理单元包括除尘器、引风机、监测仪表。所述除尘器入口即所述烟气处理单元的入口,所述除尘器出口与所述引风机入口相连,所述引风机出口即所述烟气处理单元的出口。
[0047]
进一步地,所述除尘器优选为脉冲布袋除尘器,以去除烟气中颗粒物。
[0048]
进一步地,所述脉冲布袋除尘器的布袋材质优选为ptfe覆膜,除尘效率高,透气性强。
[0049]
进一步地,所述监测仪表为温度、压力仪表,设置于除尘器前后,以更好的监测系统烟气数据。
[0050]
进一步地,所述除尘器底部捕集的飞灰送入成品飞灰储仓中。
[0051]
所述成品飞灰储存单元包括成品飞灰储仓、成品飞灰暂存仓、成品飞灰输送管道。所述成品飞灰储仓的入口即为飞灰储存单元的入口,所述成品飞灰储仓的出口即为所述飞灰储仓单元的出口,与后续飞灰资源化处置系统相连。
[0052]
进一步地,所述成品飞灰暂存仓的入口与所述成品飞灰储仓的入口相连,飞灰采用斜槽输送至所述成品飞灰储仓和所述成品飞灰暂存仓中。
[0053]
进一步地,所述成品飞灰储仓和所述成品飞灰暂存仓底部设有助流气嘴,以使下料通畅。
[0054]
本发明的第二个技术方案是一种水洗飞灰间接干燥的方法,步骤如下:
[0055]
①
混料制备:水洗飞灰(含水率约40%)输送至混合器的水洗飞灰入口,飞灰暂存仓中的干燥飞灰经定量加料器输送至混合器的干燥飞灰入口,在混合器内水洗飞灰与干燥飞灰进行搅拌、混合,将混合物料的含水率降低至10%-30%,物料混合时间为2-3min。
[0056]
②
设备预热:打开自来水开关,经软水器软化后进入热源产生器,随后,产生的饱
和蒸汽经保温管道输送至间接干燥机的热源进口,为间接干燥机进行预热;
[0057]
其中,饱和蒸汽的条件为0.5-0.8mpa。
[0058]
③
间接干燥:饱和蒸汽对间接干燥机进行预热后,步骤
①
中混合后的飞灰经螺旋输送至间接干燥器进料口,物料通过干燥器内部转盘转动向出料端移动,在物料移动过程中,通过与热源的间壁接触传热,达到降低飞灰含水率的目的,此外,干燥机内部设有构筑件,可有效防止飞灰粘壁、抱团,有利于保持飞灰出料的均匀和松散程度。其中,干燥后飞灰的含水率≤5%,干燥时间可设定为1.5-2.5小时。
[0059]
同时,间接干燥机中排出的冷凝水进入冷凝水收集器以循环利用。
[0060]
④
飞灰存储:步骤
③
中干燥后的物料通过出料端输送至成品飞灰储仓及成品飞灰暂存仓中。其中,成品飞灰储仓中飞灰供后续资源化处置利用,成品飞灰暂存仓中飞灰返回至混料单元循环利用。
[0061]
⑤
烟气处理:步骤
③
中间接干燥机内部产生的携湿烟气进入烟气处理单元,经布袋除尘器去除其中粉尘,保证烟气中颗粒物浓度≤10mg/m3。其中,布袋除尘器前端设置温度、压力监测仪器,通过数据监测,防止携湿烟气结露,造成布袋除尘器堵塞的问题。经布袋除尘器捕集的飞灰进入成品飞灰储仓中。
[0062]
⑥
余热利用:步骤
⑤
中除尘后的高温烟气经过换热器再次加热后,可重新作为热源进入间接干燥机中夹套中二次利用。
[0063]
有益效果:
[0064]
与现有技术相比,具有以下的技术效果:
[0065]
(1)采用间接干燥的方式,利用间壁传热降低飞灰中的含水率,传热效率高,可充分满足干燥工艺的需求。
[0066]
(2)采用间接干燥的方式,利用间壁传热降低飞灰中的含水率,热源与飞灰不直接接触,产生的烟气量少且粉尘含量少,后续烟气处理工艺压力较小。
[0067]
(3)采用混料预处理的方式,将水洗飞灰与干燥后的成品灰进行混合,以降低干燥机进料的含水率,在提高干燥效率的同时,实现了物料的均匀打散,有利于飞灰混合物料在间接干燥设备中的流动性,有利于保证出料的松散状态。
[0068]
(4)水洗飞灰的间接干燥,改变了以往的利用资源化企业现有热源的直接干燥方式,减少了对资源化企业设备的影响,且有利于降低整个系统的能源消耗。
附图说明
[0069]
图1水洗飞灰间接干燥的系统流程图;
[0070]
图2水洗飞灰间接干燥的工艺流程图(饱和蒸汽)。
[0071]
图3水洗飞灰间接干燥的工艺流程图(导热油)。
具体实施方式
[0072]
下面对本发明作进一步的说明,以下进行清晰、完整的描述,实施例中不能穷举本发明所有的实施方式。
[0073]
(1)饱和蒸汽
[0074]
①
混料制备:含水率40%的水洗飞灰输送至混合器的水洗飞灰进料口,飞灰暂存
仓中的干燥飞灰经螺旋输送器输送至混合器的干燥飞灰进料口,在混合器内水洗飞灰与干燥飞灰进行搅拌、混合,物料混合时间为2min,混合后物料的含水率降低至20%。
[0075]
②
设备预热:打开自来水开关,经软水器软化后进入热源产生器,随后,产生的0.6mpa饱和蒸汽经保温管道输送至间接干燥机的热源进口,为间接干燥机进行预热。
[0076]
③
间接干燥:饱和蒸汽对间接干燥机进行预热后,步骤
①
中含水率20%的混合飞灰经螺旋输送至间接干燥器进料口,物料通过干燥器内部转盘转动向出料端移动,干燥时间设定为2小时,干燥后飞灰的含水率≤5%。同时,间接干燥机中排出的冷凝水进入冷凝水收集器以循环利用。
[0077]
④
飞灰存储:步骤
③
中含水率≤5%的物料通过出料端输送至成品飞灰储仓及成品飞灰暂存仓中。
[0078]
⑤
烟气处理:步骤
③
中间接干燥机内部产生的携湿烟气进入烟气处理单元,经布袋除尘器去除其中粉尘,处理后烟气中颗粒物浓度≤10mg/m3。通过监测布袋除尘器前端的温度、压力监测器,防止携湿烟气结露。经布袋除尘器捕集的飞灰进入成品飞灰储仓中。
[0079]
⑥
余热利用:步骤
⑤
中除尘后的高温烟气经过换热器再次加热后,温度达到160℃,重新作为热源进入间接干燥机中夹套中二次利用。
[0080]
(2)导热油
[0081]
①
混料制备:含水率40%的水洗飞灰输送至混合器的水洗飞灰进料口,飞灰暂存仓中的干燥飞灰经螺旋输送器输送至混合器的干燥飞灰进料口,在混合器内水洗飞灰与干燥飞灰进行搅拌、混合,物料混合时间为2min,混合后物料的含水率降低至20%。
[0082]
②
设备预热:打开电加热装置,对导热油进行加热,导热油加热温度设定为140℃,随后,导热油经保温管道输送至间接干燥机的热源进口,为间接干燥机进行预热。
[0083]
③
间接干燥:导热油对间接干燥机进行预热后,步骤
①
中含水率20%的混合飞灰经螺旋输送至间接干燥器进料口,物料通过干燥器内部转盘转动向出料端移动,干燥时间设定为2小时,干燥后飞灰的含水率≤5%。同时,间接干燥机中排出的导热油返回至电加热装置以循环利用。
[0084]
④
飞灰存储:步骤
③
中含水率≤5%的物料通过出料端输送至成品飞灰储仓及成品飞灰暂存仓中。
[0085]
⑤
烟气处理:步骤
③
中间接干燥机内部产生的携湿烟气进入烟气处理单元,经布袋除尘器去除其中粉尘,处理后烟气中颗粒物浓度≤10mg/m3。通过监测布袋除尘器前端的温度、压力监测器,防止携湿烟气结露。经布袋除尘器捕集的飞灰进入成品飞灰储仓中。
[0086]
⑥
余热利用:步骤
⑤
中除尘后的高温烟气经过换热器再次加热后,温度达到160℃,重新作为热源进入间接干燥机中夹套中二次利用。
[0087]
实施例3-11的工艺参数
[0088][0089]
首先,水洗飞灰通过间接干燥后,可将飞灰的含水率从40%降低至5%以下,以便于后续资源化处置,减少对资源化处置设备的影响,从而有效保证飞灰的资源化处置能力;
[0090]
第二,采用间接干燥的方式,利用间壁传热降低飞灰中的含水率,热源与飞灰间接接触,产生的烟气量少且粉尘含量少,后续烟气处理工艺较为简单;
[0091]
第三,间接干燥前,采用混料预处理的方式,将水洗飞灰(含水率40%)与干燥后的成品灰进行混合,以降低干燥机进料的含水率,进一步的提高了干燥效率,充分保证干燥后的飞灰含水率≤5%;
[0092]
第四,混料预处理在降低进料含水率的同时,实现了物料的均匀打散,有利于飞灰混合物料在间接干燥设备中的流动性,并可减少物料粘壁的发生,有利于保证出料的松散状态;
[0093]
第五,水洗飞灰的间接干燥,改变了以往的利用资源化企业现有热源的直接干燥方式,减少了对资源化企业设备的影响,且有利于降低整个系统的能源消耗;
[0094]
第六,对干燥过程中产生的冷凝水和二次蒸汽,进行循环利用,节约蒸汽消耗量,并可提高整体经济效益;
[0095]
第七,本发明中整套水洗飞灰间接干燥的系统中安装有温度、流量监测仪器,通过实时在线数据监测干燥系统运行的稳定情况,以便于调节系统内的各项工艺控制条件,充分保证水洗飞灰的干燥效率。
[0096]
本发明对水洗飞灰利用间接干燥的方式进行干燥处理,改变了传统的直接干燥技术,减少了烟气的产生量,降低了烟气的含尘量,并降低了系统的整体能耗。