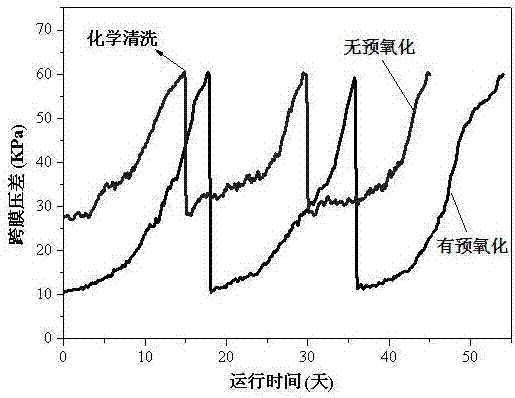
本发明涉及给水厂生产废水处理领域,特别是一种活性炭滤池反冲洗水回收装置及回收方法。
背景技术:
:作为供水企业和社会节水的重要组成部分,水厂节水尤其是排泥水再利用已成为业内节水技术发展的必然趋势。据调查,全国地表水厂拥有生产废水处理设施的不足5%,即绝大部分水厂的生产废水均未经处理直接排放,不仅浪费严重,而且对受纳水体也造成了较为严重的污染。近年来,以臭氧-生物活性炭为代表的深度处理工艺在全国得到逐渐的推广和应用,活性炭滤池反冲洗水量约占水厂日供水量的2%。以南京为例,日供水能力达200万m3,按水厂生产废水量5%~8%进行估算,生产废水量达10~16万m3/d,相当于一座50万人口左右中等城市的用水量,节水潜力可观。目前活性炭滤池反冲洗水的再利用主要是将反冲洗水回用至与原水混合,这种回用方式优点是方式简单,减少回收利用成本。然而,活性炭滤池反冲洗水中含有大量的微生物、有机物以及反冲洗过程中被冲起的颗粒物。这种反冲洗水回用与原水混合后可能会导致混凝出水中溶解性有机物含量增加以及微生物泄露等问题,对水厂供水安全性有着一定的风险。技术实现要素:本发明要解决的技术问题是针对上述现有技术的不足,而提供一种活性炭滤池反冲洗水回收装置,该活性炭滤池反冲洗水回收装置能将活性炭滤池反冲洗水中的微生物、有机物以及颗粒物进行滤除,实现了活性炭滤池反冲洗水的安全利用,提高了给水厂节水效率,并且可在低药耗的前提下有效抑制超滤膜污染。为解决上述技术问题,本发明采用的技术方案是:一种活性炭滤池反冲洗水回收装置,包括絮凝剂投加池、反冲洗水收集池、超滤膜池、臭氧发生器和清水池。絮凝剂投加池内装填有絮凝剂。反冲洗水收集池上设置有反冲洗水入口、絮凝剂投加口和收集池出水口;其中,反冲洗水入口与活性炭滤池反冲洗水相连接,絮凝剂投加口通过絮凝剂管路与絮凝剂投加池的出口相连接,收集池出水口与超滤膜池的入水口相连接。超滤膜池内设置有超滤膜组件,超滤膜组件顶部设置有超滤膜出水口和超滤膜反冲洗入水口;其中,超滤膜出水口与清水池的入水口相连接。清水池上设置有反冲洗出水口,该反冲洗出水口通过反冲洗泵与超滤膜反冲洗入水口相连接。位于超滤膜组件下方的超滤膜池内还设置有臭氧曝气盘,臭氧曝气盘通过管路与臭氧发生器相连接。超滤膜池顶部还设置有臭氧尾气排出口。反冲洗水收集池内设置有机械搅拌装置,反冲洗水收集池底部设置有机械刮泥机和排泥口。絮凝剂管路上设置有计量泵和阀门。臭氧发生器与臭氧曝气盘相连接的管路上设置有流量计。本发明还提供一种活性炭滤池反冲洗水回收方法,该活性炭滤池反冲洗水回收方法能将活性炭滤池反冲洗水中的微生物、有机物以及颗粒物进行滤除,实现了活性炭滤池反冲洗水的安全利用,提高了给水厂节水效率,并且可在低药耗的前提下有效抑制超滤膜污染。一种活性炭滤池反冲洗水回收方法,包括如下步骤。步骤1,收集活性炭滤池反冲洗水。步骤2,将步骤1收集的活性炭滤池反冲洗水进行微絮凝处理。步骤3,将步骤2微絮凝后的活性炭滤池反冲洗水进行沉淀。步骤4,将步骤3沉淀后的上清液进行臭氧预氧化后进入超滤膜组件进行超滤。步骤5,将步骤4中的超滤膜出水进入清水池回用。步骤1中,收集的活性炭滤池反冲洗水是指活性炭滤池反冲洗开始1min后的反冲洗水。步骤2中的微絮凝及步骤3中的沉淀均在反冲洗水收集池中进行,反冲洗水收集池中设机械搅拌装置,活性炭滤池反冲洗水收集结束后,投加絮凝剂并进行搅拌;然后,静置沉淀。所述絮凝剂为聚合氯化铝,投加量2~10mg/l,絮凝剂投加及搅拌完毕后,应使絮凝后的活性炭滤池反冲洗水的zeta电位为-0.15~0.15mv;絮凝剂投加后的搅拌时间为0.5-2min,絮凝后的静置时间不少于30min。步骤4中,臭氧预氧化与超滤膜超滤均在超滤膜池中进行,臭氧曝气盘设置在超滤膜池的底部,超滤膜组件设置在臭氧曝气盘上方的超滤膜池中,臭氧曝气盘与臭氧发生器相连接。臭氧预氧化时,臭氧与步骤3沉淀后的上清液的接触时间不少于10min,臭氧投加量需满足要求为:臭氧与沉淀后上清液接触10min后,采用静滴法,测得超滤膜池中的胶体与纯水的接触角小于60°。本发明具有的有益效果是:能将活性炭滤池反冲洗水中的微生物、有机物以及颗粒物进行滤除,实现了活性炭滤池反冲洗水的安全利用,提高了给水厂节水效率,并且可在低药耗的前提下有效抑制超滤膜污染。附图说明图1显示了本发明一种活性炭滤池反冲洗水回收装置的结构示意图。图2显示了超滤膜组件在有预氧化和无预氧化运行时跨膜压差对比图。其中有:10.絮凝剂投加池;11.计量泵;12.阀门;20.反冲洗水收集池;21.反冲洗水入口;22.絮凝剂投加口;23.机械搅拌装置;24.机械刮泥机;25.排泥口;26.离心泵;27.收集池出水口;30.超滤膜池;31.超滤膜组件;311.超滤膜出水口;312.超滤膜反冲洗入水口;32.臭氧曝气盘;33.臭氧尾气排出口;40.臭氧发生器;41.流量计;50.清水池;51.压力计;52.产水泵;53.反冲洗泵;54.反冲洗出水口;60.臭氧破坏装置。具体实施方式下面结合附图和具体较佳实施方式对本发明作进一步详细的说明。如图1所示,一种活性炭滤池反冲洗水回收装置,包括絮凝剂投加池10、反冲洗水收集池20、超滤膜池30、臭氧发生器40和清水池50。絮凝剂投加池内装填有絮凝剂。反冲洗水收集池20上设置有反冲洗水入口21、絮凝剂投加口22和收集池出水口27。反冲洗水入口与活性炭滤池反冲洗水相连接。絮凝剂投加口通过絮凝剂管路与絮凝剂投加池的出口相连接,絮凝剂管路上优选设置有计量泵11和阀门12。收集池出水口优选通过离心泵26和阀门与超滤膜池的入水口相连接。另外,上述反冲洗水收集池内还优选设置有机械搅拌装置23,活性炭滤池反冲洗水收集结束后,投加絮凝剂时用于搅拌。进一步,反冲洗水收集池底部优选设置有机械刮泥机24和排泥口25,用于定期排放反冲洗水收集池内的沉淀污泥。超滤膜池30内设置有超滤膜组件31,超滤膜组件顶部设置有超滤膜出水口311和超滤膜反冲洗入水口312。超滤膜出水口优选通过阀门、压力计51和产水泵52与清水池的入水口相连接。清水池50上设置有反冲洗出水口54,该反冲洗出水口通过反冲洗泵53与超滤膜反冲洗入水口相连接。位于超滤膜组件下方的超滤膜池内还设置有臭氧曝气盘32,臭氧曝气盘通过管路与臭氧发生器40相连接;臭氧发生器与臭氧曝气盘相连接的管路上优选设置有流量计41。超滤膜池顶部还优选设置有臭氧尾气排出口33,与臭氧尾气排出口33相连接的排气管路上优选设置有臭氧破坏装置60。一种活性炭滤池反冲洗水回收方法,包括如下步骤。步骤1,收集活性炭滤池反冲洗水。由于活性炭滤池在反冲洗初期的活性炭滤池反冲洗水中含有大量的杂质与微生物,为减轻回收系统负担,同时考虑回用水质安全性,反冲洗开始后1min内的反冲洗水不收集,1min后,收集活性炭滤池反冲洗水,移入收集容器中。因此,本步骤1中,收集的活性炭滤池反冲洗水是指活性炭滤池反冲洗开始1min后的反冲洗水。步骤2,将步骤1收集的活性炭滤池反冲洗水进行微絮凝处理。步骤3,将步骤2微絮凝后的活性炭滤池反冲洗水进行沉淀。上述步骤2中的微絮凝及步骤3中的沉淀均在反冲洗水收集池中进行,反冲洗水收集池中设机械搅拌装置,活性炭滤池反冲洗水收集结束后,投加絮凝剂并进行搅拌;然后,静置沉淀。投加的絮凝剂优选为聚合氯化铝,投加量优选为2~10mg/l,絮凝剂投加量的依据为:絮凝剂投加及搅拌完毕后,应使絮凝后的活性炭滤池反冲洗水的zeta电位为-0.15~0.15mv。另外,絮凝剂投加后的搅拌时间优选为0.5-2min,进一步优选为2min,絮凝后的静置时间不少于30min,优选为30min。步骤4,将步骤3沉淀后的上清液进行臭氧预氧化后进入超滤膜组件进行超滤。沉淀结束后,取反冲洗水收集池中的上清液进入超滤膜池。本试验中超滤膜组件采用pvc中空纤维膜,切割分子量为50000da,膜孔径0.01μm。臭氧预氧化与超滤膜超滤均在超滤膜池中进行,臭氧曝气盘设置在超滤膜池的底部,超滤膜组件设置在臭氧曝气盘上方的超滤膜池中,臭氧曝气盘与臭氧发生器相连接。制备的臭氧通过臭氧曝气盘进入水中,臭氧投加量1mg/l。臭氧预氧化时,臭氧与步骤3沉淀后的上清液的接触时间不少于10min,臭氧投加量需满足要求为:臭氧与沉淀后上清液接触10min后,采用静滴法,测得超滤膜池中的胶体与纯水的接触角小于60°。本发明中,臭氧接触10min后,采用静滴法(sessiledropmethod)测量水中的胶体与纯水的接触角,接触角实测为57.3°。超滤膜组件中的超滤膜每1h进行一次反冲洗,反冲洗水采用膜池产水,也即清水池中的水。当运行跨膜压差达到60kpa进行化学清洗,化学清洗采用次氯酸钠溶液。超滤膜运行跨膜压差见图2,由图2可以看出,臭氧预氧化可以显著降低膜污染,延长化学清洗周期。步骤5,将步骤4中的超滤膜出水进入清水池回用。本实施例回用前后的水质数据见表1。表1指标炭池反冲洗水超滤出水浊度(ntu)42.30.08>2μm颗粒物(个/ml)6993231细菌总数(cfu/ml)31800高锰酸盐指数(mg/l)4.221.33从表1可以看出,本实施方式药耗低、处理效率高,且出水水质优良,可以直接进入清水池实现回用。以上详细描述了本发明的优选实施方式,但是,本发明并不限于上述实施方式中的具体细节,在本发明的技术构思范围内,可以对本发明的技术方案进行多种等同变换,这些等同变换均属于本发明的保护范围。当前第1页12