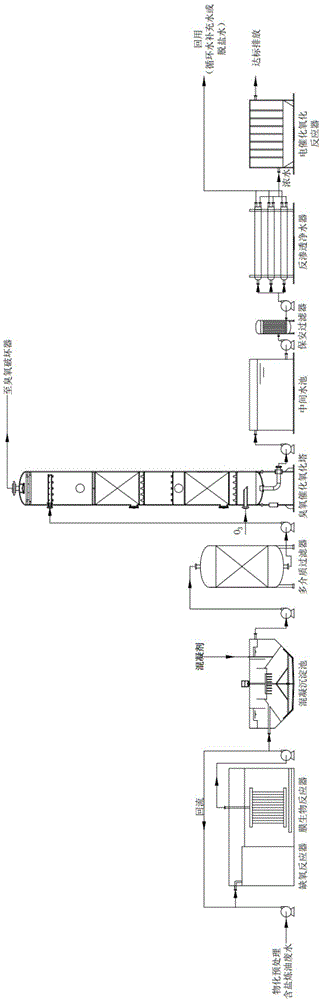
本发明涉及一种含盐炼油废水深度处理回用的方法,属于炼油废水深度处理
技术领域:
。
背景技术:
:目前我国原油加工能力近3亿吨/年,随着经济的高速发展,炼油需求量仍会不断上升,而在石油炼制加工过程中会产生大量的含盐废水,这部分废水主要包括常减压蒸馏电脱盐水、乙烯生产过程中产生的高含盐废碱液及苯酚丙酮高含盐污水等,该类废水盐含量高,有机污染物浓度大,如武汉石化的高盐废水中cod高达950mg/l~1350mg/l,此外,炼油过程中产生的含盐废水水质波动大,处理难度高,虽然采用臭氧氧化结合曝气滤池的组合工艺可以达到排放标准,但由于其中所含的cl-、so42-、ca2+、mg2+等盐份浓度高,存在腐蚀结垢风险而不能回用。现有石化企业从2017年7月1日起,开始执行新的《石油炼制工业污染物排放标准》(gb31570-2015),该标准规定加工单位原油的排水量上限为0.5m3/t,对环境承载能力差、生态脆弱的地区的排水量上限则是0.4m3/t,如果含盐炼油废水只处理到达标排放而不回用的话,很难达到新标准的耗水要求。目前全国石化炼油企业废水有两种方式,一种是将含油废水和高含盐废水分开处理,另一种是将二者混在一起处理,发展趋势是前者,含油炼油废水相对好处理,所以大多数炼油企业这部分的废水已经回用,但含盐废水主要还是通过深度处理后达标排放而没有回用。技术实现要素:本发明所要解决的技术问题是针对现有技术中存在的不足,而提供一种含盐炼油废水深度处理回用的方法,利用膜生物反应、混凝及臭氧催化氧化将含盐炼油废水中的有机污染物脱除更为完全,从源头上减轻膜污染,延长膜的反洗周期和使用寿命,攻克反渗透应用于炼油废水回用工艺中常常发生膜污染的技术瓶颈,从而实现废水回用装置长周期稳定运行,进而实现含盐炼油废水的回用。本发明方法,工艺简单、设备紧凑、膜污染程度低、工艺运行稳定、回用水水质好。为了实现上述目的,本发明采用如下技术方案:一种含盐炼油废水深度处理回用的方法,包括以下步骤:(1)缺氧处理:将经过预处理后的含盐炼油废水通过提升泵流入缺氧反应器中,在缺氧反应器中停留8~10h后完成缺氧处理;(2)膜生物处理:经过步骤(1)缺氧处理后得到的出水进入到膜生物反应器中,在膜反应器中停留15~20h后完成膜生物处理;经过膜生物生理后得到的出水一部分回流至缺氧反应器中继续按照步骤(1)操作进行缺氧处理,另一部分流入到混凝沉淀池中;(3)混凝沉淀处理:经过步骤(2)膜生物处理后得到的出水进入到混凝沉淀池后,向混凝沉淀池中投加混凝剂进行混凝反应;混凝剂的投加量为15~20mg/l,混凝反应、沉淀时间为20~30min;(4)臭氧催化氧化处理:经过步骤(3)混凝沉淀处理后得到的出水经多介质过滤器过滤后进入装填有wut-5型催化剂的臭氧催化氧化塔中,在wut-5型催化剂的催化作用下与臭氧进行催化氧化反应,反应时间为12~17min;(5)反渗透处理:经过步骤(3)臭氧催化氧化处理后得到的出水流入中间水池中,中间水池的出水经高压泵提升流入到保安过滤器中进行过滤处理,然后再经高压泵提升流入到反渗透净水器中进行反渗透处理,反渗透处理后得到浓水和产水;浓水经电催化氧化反应器进行电催化氧化反应后达标排放,产水作为循环水的补充水或脱盐水回用。上述技术方案中,步骤(1)中,所述的预处理指的是,含盐炼油废水按照传统方法依次经隔油、两级气浮处理。上述技术方案中,步骤(2)中,回流比为200~300%。上述技术方案中,步骤(3)中,所述的混凝剂为复合混凝剂,为无机混凝剂和有机混凝剂复合后得到的复合混凝剂;优选为聚硅硫酸铝铁(psafs)与聚丙烯酰胺(pam)的复合后得到的复合混凝剂,其中pam占复合混凝剂总质量的8~12wt%。上述技术方案中,步骤(4)中,臭氧催化氧化塔中,填充的wut-5型催化剂的有效容积为20~30vol%,臭氧投加量为25~35mg/l。上述技术方案中,步骤(4)中,所述的wut-5型催化剂为球状颗粒固体催化剂,粒径为3~5mm;是以活性组分、载体为原料,经传统的圆盘造粒法造粒后在1050~1150℃的高温下烧结15~35min后制成的。上述技术方案中,所述的活性组分为硫酸锰、醋酸锰、高锰酸钾、硝酸铁、硝酸铜、硫酸铜、二氧化钛中的任意两种或两种以上以任意比例混合而成的混合物,活性组分的总质量百分含量为5~8wt%。上述技术方案中,所述的载体为粘性载体和其他载体以任意比例混合而成的混合物,其中:粘性载体为黏土;其他载体为粉煤灰、钢渣中的任意一种,或两种以任意比例混合而成的混合物。本发明所述的缺氧反应器、膜生物反应器、多介质过滤器、臭氧催化氧化塔、保安过滤器、反渗透净水器、电催化氧化反应器均为本领域市售的、传统的设备,如果没有本发明的特殊要求外,均可按照本领域常规操作方法操作。由于采用上述技术方案,本发明与现有技术相比具有如下积极效果:(1)本发明以膜生物反应器(mbr)替代传统的活性污泥生物反应器,污泥浓度高,污泥龄长,抗冲击负荷性能好,运行稳定,有机污染物去除效率高。(2)本发明通过投加复合无机/有机混凝剂,充分发挥无机混凝剂的脱稳凝聚及有机絮凝剂的桥连絮凝耦合作用,并通过多介质过滤器过滤,进一步脱除废水中残余的有机物和少量的悬浮物,有利于发挥臭氧催化氧化的催化功效,并利用高活性的wut-5型臭氧催化剂的催化作用,废水中有机物矿化更完全。(3)本发明利用膜生物反应、混凝及臭氧催化氧化将含盐炼油废水中的有机污染物脱除更为完全,从源头上减轻了膜污染,延长了膜的反洗周期和使用寿命,攻克了反渗透应用于炼油废水回用工艺中常常发生膜污染的技术瓶颈,实现了废水回用装置长周期稳定运行,且反渗透脱盐率高、回用水水质好。预处理后的含盐炼油废水经本方法处理后,得到的回用水水质为:cod13~25mg/l、石油类0.2~~0.5mg/l、电导率130~165μs/cm、总硬度-13~25mg/l、氯离子15~25mg/l,表明该方法得到的回用水的水质完全满足循环水的补充水和脱盐水的水质标准要求。因此,本发明具有工艺简单、设备紧凑、膜污染程度低、工艺运行稳定、回用水水质好等优点。附图说明图1为本发明含盐炼油废水深度处理回用的方法的工艺流程示意图。具体实施方式以下对本发明技术方案的具体实施方式详细描述,但本发明并不限于以下描述内容:以下实施例中,预处理,指的是含盐炼油废水按照传统方法依次经隔油、两级气浮处理,施例中不再赘述。实施例1:一种含盐炼油废水深度处理回用的方法,包括以下步骤:(1)缺氧处理:预处理后的含盐炼油废水先通过提升泵流入缺氧反应器,停留8h;(2)膜生物处理:经过步骤(1)缺氧处理后得到的出水进入膜生物反应器,停留15h,膜生物反应器出水的一部分回流至缺氧反应器,回流比为200%,出水的另一部分流入混凝池;(3)混凝沉淀处理:经过步骤(2)膜生物处理后得到的出水进入到混凝沉淀池后,向混凝沉淀池中投加混凝剂进行混凝沉淀,混凝剂的投加量为15mg/l,混凝反应、沉淀20min;(4)臭氧催化氧化处理:经过步骤(3)混凝沉淀处理后得到的出水经多介质过滤器过滤后进入装填有wut-5型催化剂的臭氧催化氧化塔中,在wut-5型催化剂的催化作用下与臭氧进行催化氧化反应,反应时间为12min;臭氧催化氧化塔中填充的wut-5型催化剂的有效容积20vol%,臭氧投加量为25mg/l;(5)反渗透处理:经过步骤(3)臭氧催化氧化处理后得到的出水流入中间水池中,中间水池的出水经高压泵提升流入到保安过滤器中进行过滤处理,然后再经高压泵提升流入到反渗透净水器中进行反渗透处理,反渗透处理后得到浓水和产水;浓水经电催化氧化反应器进行电催化氧化反应后达标排放,产水作为循环水的补充水或脱盐水回用。本实施例中所述的混凝剂为聚硅硫酸铝铁(psafs)与聚丙烯酰胺(pam)的复合药剂,其中pam占复合混凝剂总质量的8wt%;本实施例中所述的wut-5型催化剂为球状催化陶粒固体催化剂,粒径为3~5mm,是以活性组分、载体为原料,经传统的圆盘造粒法造粒后在1080℃的高温下烧结25min后制成的;其中:其活性组分为硫酸锰和高锰酸钾,硫酸锰与高锰酸钾的质量比为2:3,活性组分的总质量百分含量为5wt%,余量为载体;载体为黏土、粉煤灰,质量比为2:3。预处理后的含盐炼油废水经传统方法处理后的废水水质和预处理后的含盐炼油废水经本实施例所述的方法处理后得到的回用水水质如表1所示:表1不同处理方法处理后的水质指标对比实施例2:一种含盐炼油废水深度处理回用的方法,包括以下步骤:(1)缺氧处理:预处理后的含盐炼油废水先通过提升泵流入缺氧反应器,停留9h;(2)膜生物处理:经过步骤(1)缺氧处理后得到的出水进入到膜生物反应器中,停留17h,膜生物反应器出水的一部分回流至缺氧反应器,回流比为250%,出水的另一部分流入混凝池;(3)混凝沉淀处理:经过步骤(2)膜生物处理后得到的出水进入到混凝沉淀池后,向混凝沉淀池中投加混凝剂进行混凝沉淀,混凝剂的投加量为17mg/l,混凝反应、沉淀25min;(4)臭氧催化氧化处理:经过步骤(3)混凝沉淀处理后得到的出水经多介质过滤器过滤后进入装填有wut-5型催化剂的臭氧催化氧化塔中,在wut-5型催化剂的催化作用下与臭氧进行催化氧化反应,反应时间为15min;臭氧催化氧化塔中填充的wut-5型催化剂的有效容积为25vol%,臭氧投加量为30mg/l;(5)反渗透处理:经过步骤(3)臭氧催化氧化处理后得到的出水流入中间水池中,中间水池的出水经高压泵提升流入到保安过滤器中进行过滤处理,然后再经高压泵提升流入到反渗透净水器中进行反渗透处理,反渗透处理后得到浓水和产水;浓水经电催化氧化反应器进行电催化氧化反应后达标排放,产水作为循环水的补充水或脱盐水回用。本实施例中所述的混凝剂为聚硅硫酸铝铁(psafs)与聚丙烯酰胺(pam)的复合药剂,其中pam占复合混凝剂总质量的10wt%。本实施例中所述的wut-5型催化剂为球状催化陶粒固体催化剂,粒径为3~5mm,是以活性组分、载体为原料,经传统的圆盘造粒法造粒后在1100℃的高温下烧结20min后制成的;其中:活性组分为硝酸铜和硫酸铜,硝酸铜与硫酸铜的质量比为7:13,活性组分的总质量百分含量为6wt%,余量为载体;载体为黏土、钢渣,质量比为2:3。预处理后的含盐炼油废水经传统方法处理后的废水水质和预处理后的含盐炼油废水经本实施例所述的方法处理后得到的回用水水质如表2所示:表2不同处理方法处理后的水质指标对比实施例3:一种含盐炼油废水深度处理回用的方法,包括以下步骤:(1)缺氧处理:预处理后的含盐炼油废水先通过提升泵流入缺氧反应器,停留10h;(2)膜生物处理:经过步骤(1)缺氧处理后得到的出水进入到膜生物反应器中,停留20h,膜生物反应器出水的一部分回流至缺氧反应器,回流比为300%,出水的另一部分流入混凝池;(3)混凝沉淀处理:经过步骤(2)膜生物处理后得到的出水进入到混凝沉淀池后,向混凝沉淀池中投加混凝剂进行混凝沉淀,混凝剂的投加量为20mg/l,混凝反应、沉淀30min;(4)臭氧催化氧化处理:经过步骤(3)混凝沉淀处理后得到的出水经多介质过滤器过滤后进入装填有wut-5型催化剂的臭氧催化氧化塔中,在wut-5型催化剂的催化作用下与臭氧进行催化氧化反应,反应时间为17min;臭氧催化氧化塔中填充的wut-5型催化剂的有效容积为30vol%,臭氧投加量为35mg/l;(5)反渗透处理:经过步骤(3)臭氧催化氧化处理后得到的出水流入中间水池中,中间水池的出水经高压泵提升流入到保安过滤器中进行过滤处理,然后再经高压泵提升流入到反渗透净水器中进行反渗透处理,反渗透处理后得到浓水和产水;浓水经电催化氧化反应器进行电催化氧化反应后达标排放,产水作为循环水的补充水或脱盐水回用。本实施例中所述的混凝剂为聚硅硫酸铝铁(psafs)与聚丙烯酰胺(pam)的复合药剂,其中pam占复合混凝剂总质量的12wt%。本实施例中所述的wut-5型催化剂为球状催化陶粒固体催化剂,粒径为3~5mm,是以活性组分、载体为原料,经传统的圆盘造粒法造粒后在1120℃的高温下烧结15min后制成的;其中:其活性组分为硫酸锰、硫酸铜和二氧化钛,硫酸锰、硫酸铜、二氧化钛的质量比为5:9:6,,活性组分的总质量百分含量为8wt%,余量为载体;载体为黏土、粉煤灰、钢渣,质量比为1:1:1。预处理后的含盐炼油废水经传统方法处理后的废水水质和预处理后的含盐炼油废水经本实施例所述的方法处理后得到的回用水水质如表3所示:表3不同处理方法处理后的水质指标对比传统方法本实施例方法cod75~110mg/l13~18mg/l石油类1.5~3.5mg/l0.2~0.4mg/l电导率1500~3500μs/cm130~155μs/cm总硬度95~200mg/l13~18mg/l氯离子165~250mg/l15~20mg/l本具体实施方式与现有技术相比具有如下积极效果:(1)本发明以膜生物反应器(mbr)替代传统的活性污泥生物反应器,污泥浓度高,污泥龄长,抗冲击负荷性能好,运行稳定,有机污染物去除效率高。(2)本发明通过投加复合无机/有机混凝剂,充分发挥无机混凝剂的脱稳凝聚及有机絮凝剂的桥连絮凝耦合作用,并通过多介质过滤器过滤,进一步脱除废水中残余的有机物和少量的悬浮物,有利于发挥臭氧催化氧化的催化功效,并利用高活性的wut-5型臭氧催化剂的催化作用,废水中有机物矿化更完全。(3)本发明利用膜生物反应、混凝及臭氧催化氧化将含盐炼油废水中的有机污染物脱除更为完全,从源头上减轻了膜污染,延长了膜的反洗周期和使用寿命,攻克了反渗透应用于炼油废水回用工艺中常常发生膜污染的技术瓶颈,实现了废水回用装置长周期稳定运行,且反渗透脱盐率高、回用水水质好。因此,本具体实施方式具有工艺简单、设备紧凑、膜污染程度低、工艺运行稳定、回用水水质好等优点。上述实例只是为说明本发明的技术构思以及技术特点,并不能以此限制本发明的保护范围。凡根据本发明的实质所做的等效变换或修饰,都应该涵盖在本发明的保护范围之内。当前第1页12