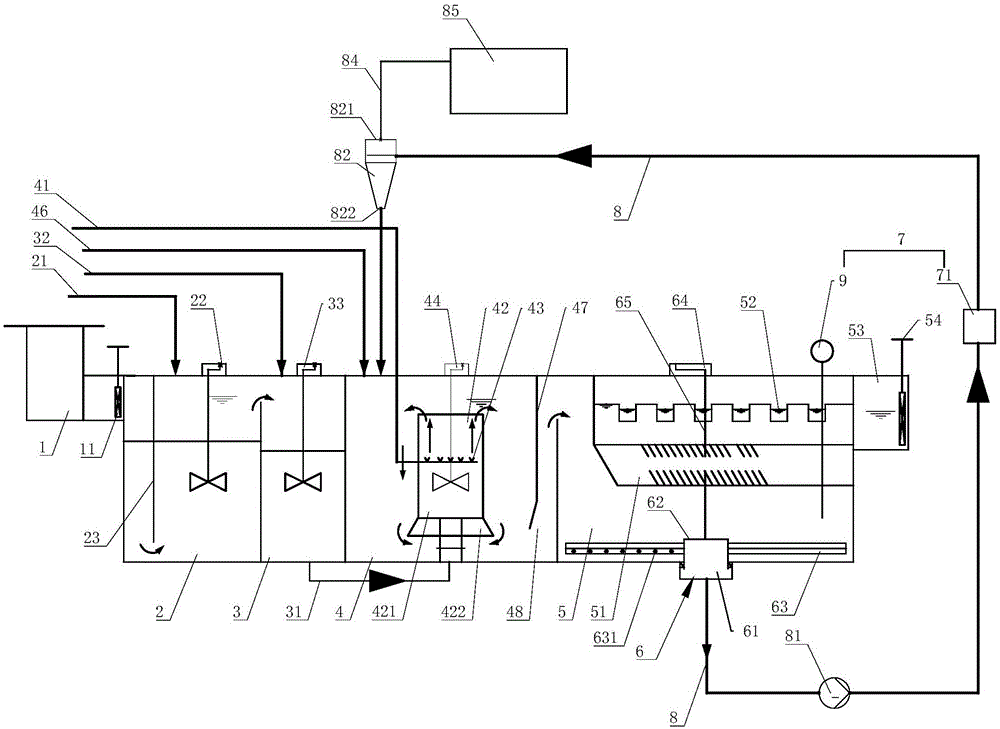
本发明涉及废水处理的
技术领域:
,尤其是涉及一种氨氮废水处理系统及氨氮废水处理方法。
背景技术:
:氮是植物和微生物的主要营养元素,当水体中n>0.2mg/l,水体就会营养化,特别是封闭水体中的氨氮造成水体富营养化。水体富营养化就会引起某些藻类的恶性繁殖,一方面有些藻类本身有藻腥味会引起水质恶化使得水体变得腥臭难闻;另一方面有些藻类所含的蛋白质毒素会富集在水产物体内,并通过食物链影响人体健康,甚至使人中毒。随着我国城市人口的增加和人口的进一步集中,及人民生活水平的提高,城市排放的垃圾量和废水量在逐步上升。城市生活废水中的氮主要由厨房洗涤、厕所冲洗、淋浴、洗衣服等带入,城市垃圾的渗滤液含有较高的氨氮。城市生活废水中含有氨氮,主要源于人体食物中蛋白质的代谢的废弃物如粪便等。我国城市废水统计含氮总量为20~85mg/l,其中氨氮约为10~35mg/l,甚至可能会更高。目前处理氨氮的技术有物化法和生物法,生物脱氮法则有很多的传统的脱氮工艺,例如a/o、sbr、氧化沟等,但是生物法运行成本低,但是微生物需要培养驯化,且生物处理占地面积大,处理时间长。物化法主要包括化学中和法、化学沉淀法、乳化液膜分离法、空气吹脱和蒸汽汽提法、折点氯化法、离子交换法以及超重力脱氮法等;吹脱法针对高浓度氨氮废水是一种有效的方法,但是该方法需要大量的化学药剂调节ph,且产水常常不能达标;化学沉淀法和折点加氯法都需要大量的化学药剂对氨氮进行转化,容易造成二次污染;膜截留法能有效去除水中氨氮,但是存在浓水处理问题,且膜法对水质要求高,易结垢堵塞,增加处理成本;离子交换法依靠其对氨氮的特性吸附,有很好的氨氮脱除效果,但是其主要缺陷在于吸附剂的再生,再生通常采用酸液洗脱,洗脱后的再生液需要经过蒸发结晶处理,增加了处理成本。传统的加砂沉淀池,会存在以下问题:(1)絮凝区采用的导流筒为光滑平整的,会导致絮凝剂、微砂、污水混合效果差,水流不稳定;(2)稳定运行后,需要定期补充损失的微砂;(3)外排的污泥量比较大,浓度比较小;(4)当沉淀分离区的污泥层厚度较大时,容易导致出水斜管翻泥;(5)传统的池型设计和刮泥机配合使用,存在刮泥不均匀,易形成死角。传统的加砂沉淀池用于污水前端的处理,一般情况下,经过处理后的污水,对于水中的氨氮基本没有什么去除效果,对cod的去除也最多只有20%~30%。而处理后的水中氨氮和cod比较高时,会增加对后端处理单元的压力,甚至可能导致总出水不达标,因此有必要前端尽可能降低氨氮和cod。技术实现要素:本发明的第一个目的是提供一种氨氮废水处理系统,其优点是:减少微砂的使用量,节约成本,而且对于氨氮和cod处理效果优异,减少后端生化处理氨氮的负荷。本发明的第二个目的是提供一种氨氮废水处理方法,其采用上述氨氮废水处理系统实现,其优点是:相较于现有技术,减少微砂的使用量,节约成本,而且对于氨氮处理效果优异,减少后端生化处理氨氮的负荷。为实现上述第一个目的,本发明是通过以下技术方案得以实现的:一种氨氮废水处理系统,包括沿废水流动方向依次连通的吸附区、混凝区、絮凝区以及沉淀分离区,所述吸附区上游连通有用于废水分配的配水井,所述吸附区内设置有改性膨润土加入管,所述絮凝区内设置有微砂加入管;所述沉淀分离区的上部连通有供处理后废水流出的出水渠,所述沉淀分离区内设置有吸泥装置和用于监测并控制沉淀分离区底部污泥厚度的泥位控制装置;该氨氮处理系统还包括一连通絮凝区和沉淀分离区的回收管线,所述回收管线上依次设有污泥回流泵以及水力旋流器,水力旋流器的底流口与絮凝区连通。通过采用上述技术方案,废水通过配水井进入吸附区内,吸附区内投加改性膨润土,然后进入到混凝区,废水中的污染物以及悬浮物进行脱稳、电中和、吸附架桥等过程,形成很多细小的矾花,然后进入到絮凝区与添加的微砂以及改性膨润土充分混合,在絮凝区内,以微砂和改性膨润土为晶核,在絮凝剂的作用下细小的矾花会迅速聚集形成较大的密实的大矾花,然后进入沉淀分离区进行泥水分离,在污泥泵的作用下,分离后的污泥被吸进集泥斗内,集泥斗的污泥回流至水力旋流器中进行改性膨润土、微砂和泥水的分离,微砂和部分改性膨润土被旋分下来进入絮凝区,再次充当矾花晶核,系统运行稳定后,以改性膨润土代替损失的微砂,不需要补充微砂。达到减少微砂的使用量,节约成本,而且对于氨氮处理效果优异。本发明进一步设置为:所述絮凝区内部安装有使絮凝区内部分污水在其中循环流动的导流筒,所述导流筒内壁设有螺旋线延伸方向与导流筒内循环污水的流动方向一致的内螺旋;所述絮凝区内部还设置有絮凝搅拌器,所述絮凝搅拌器设在导流筒内;所述导流筒内还安装有用于投入絮凝剂的絮凝投加环,所述絮凝投加环水平设在絮凝搅拌器的叶轮上方。通过采用上述技术方案,内螺旋的设置,使得污水可以沿着内螺纹螺旋流动,采用这种结构,一方面使得污水与絮凝剂接触时间更长,污水与药剂(絮凝剂、微砂以及改性膨润土)的混合效果更好,药剂的利用率更高,另一方面大大减小污水流动过程中内部循环所需要的能量,更加节能,且水流更加稳定。本发明进一步设置为:所述吸附区与所述混凝区之间通过一过水堰连通,且所述吸附区内靠近配水井的一侧设有与污水输送方向垂直的第一挡板,第一挡板下端高于吸附区底面;所述混凝区与所述絮凝区之间通过一引流管道连通,所述导流筒下端为喇叭口状,且所述引流管道的一端与所述混凝区底部连通,另一端自导流筒的下端伸入到导流筒内;所述絮凝搅拌器的叶轮为将污水自下而上推动的轴流式叶轮。通过采用上述技术方案,如此设置,污水从混凝区下方进入絮凝区的导流筒内,然后沿着导流筒内螺旋方向流动,减小水流流动过程中的内耗,提高药剂与污水的混合效果,同时,轴流式叶轮的设置方式使得污水在导流筒内的流动方向与叶轮推动方向相同,大大减小了所需电能,形成一个顺时针循环,大大提高了药剂的使用效率。本发明进一步设置为:所述吸附区与所述混凝区之间通过一引流管道连通,所述引流管道的一端与所述吸附区底部连通,另一端与所述混凝区底部连通;所述混凝区与所述絮凝区之间通过一过水堰连通,所述导流筒上端为喇叭口状;所述絮凝搅拌器的叶轮为将污水自上而下推动的轴流式叶轮。通过采用上述技术方案,如此设置,污水从混凝区上方进入絮凝区的导流筒内,然后沿着导流筒内螺旋方向流动。本发明进一步设置为:所述吸泥装置包括开设在沉淀分离区底部中心处的排泥孔、底部插入排泥孔并与排泥孔转动配合的集泥筒、两根沿集泥筒的中心轴线对称连通在集泥筒的外周壁上的吸泥主管以及用于驱动集泥筒转动的电机,所述集泥筒与所述回收管线连通;且所述集泥筒与排泥孔连通,所述吸泥主管朝向沉淀分离区底面一侧具有侧楞,所述吸泥主管上开有圆形的吸泥孔;吸泥主管的截面呈菱形,吸泥孔开设在吸泥主管的朝向转动方向的侧面上。通过上述技术方案,使用时,污水经配水井、混凝区、絮凝区流入沉淀分离区,并在沉淀分离区中进行沉淀分离,沉淀到沉淀分离区底部的污泥,会在吸泥泵的作用下经吸泥主管进入集泥筒中,并最终由回收管线排出。吸泥管上侧楞的设置可以在吸泥主管转动的同时起到刮泥的作用,而且有利于吸泥管吸泥,不会形成污泥死角,从而不会导致污泥沉积;相同污泥层厚度时,吸泥装置相较于传统刮泥机,电机的输出扭矩小于传统刮泥机,所需的能耗较低,投资成本也相对较低;而且受污泥层厚度的限制较小,污泥层厚度可以累积达到0.5m~1m后再进行排泥,排泥浓度高,可以达到95%,大大减少了排泥量,提高了吸泥泵单位时间的排泥效率。菱形的吸泥主管转动时所受阻力小,而且将吸泥孔开设在吸泥主管的朝向转动方向的侧面上,可以进一步减小吸泥主管转动时所受的阻力,还有利于吸泥管吸泥,不会形成污泥死角,不会导致污泥沉积。本发明进一步设置为:所述沉淀分离区呈圆形或方形,所述泥位控制装置包括配置在沉淀分离区内的污泥采样器和连接在回收管线上用于调节所述污泥回流泵的污泥流量的流量控制阀。通过上述技术方案,工作人员可以通过污泥采样器来监测沉淀分离区底部污泥厚度,操作简单,泥层监测结果直观,效果直接;还可以通过流量控制阀来控制回收管线内污泥的流量,来对沉淀分离区底部的污泥厚度进行调整。本发明进一步设置为:所述污泥采样器包括透明的取泥管、螺纹连接在取泥管一端的端盖、开设在端盖中心处的进泥口、设置在取泥管内靠近端盖一端的挡杆以及设置在取泥管内且位于端盖与挡杆之间的挡泥球;所述挡泥球的直径大于进泥口的孔径,小于取泥管的内径;所述挡泥球上固定连接有排泥杆,所述排泥杆背离挡泥球的一端由进泥口穿过端盖,所述排泥杆的直径小于进泥口的直径。通过上述技术方案,工作人员可以通过污泥采样器来监测沉淀分离区底部污泥厚度;当工作人员需要了解到沉淀分离区底部的污泥厚度时,可以将污泥采样器设有进泥口的一端插入沉淀分离区底部,当泥位计插入污泥中时,污泥会推动挡泥球朝向挡杆运动,同时污泥会经进泥口以及挡泥球与取泥管之间的缝隙进入取泥管中,当污泥计触碰到沉淀分离区底部时,工作人员应向上提起污泥采样器,这时,挡泥球在其自身重力以及取泥管中污泥的作用下,将进泥口封堵,从而使取泥管中的污泥无法从污泥采样器中流出,当工人将污泥采样器从沉淀分离区中取出后,可以对污泥采样器中的污泥厚度进行丈量,从而得到沉淀分离区底部的污泥厚度。工作人员可以将污泥采样器竖起,然后通过推动排泥杆向挡杆方向移动,从而使挡泥球离开进泥口,从而可以使泥位计中的污泥流出,以方便工作人员排放泥位计中的污泥。本发明的上述发明目的二是通过以下技术方案得以实现的:一种氨氮废水处理方法,其采用上述氨氮废水处理系统实现,包括以下步骤:吸附:废水经过配水井配水后进入吸附区内,向吸附区内投加由乙二胺四乙酸二钠改性的改性膨润土,在搅拌条件下,使废水与膨润土发生吸附作用之后使废水流向至混凝区内;混凝:向进入混凝区内的废水中投加混凝剂,在搅拌条件下使废水与混凝剂接触,之后使废水进入絮凝区;絮凝:向进入絮凝区内的废水中投加絮凝剂和微砂,在搅拌条件下使废水与絮凝剂接触,之后使废水通过引流管道进入沉淀分离区;沉淀分离:废水进入沉淀分离区后,在斜管分离区进行泥水分离,分离的清水从出水渠流出,污泥落在沉淀分离区底部,部分污泥在污泥回流泵的作用下进入水力旋流器,经过水力旋流器分离后的微砂和部分改性膨润土进入絮凝区循环使用,分离的泥水外排;在此过程中,调节污泥回流泵,使得污泥回流量为进水流量的3%~5%。通过采用上述技术方案,只有前期系统不稳定的时候加入一部分微砂,保证系统运行,系统稳定之后,依靠定量投加的改性膨润土代替损失掉的微砂,大大降低了成本,还可以去除吸附废水中的氨氮,减小后续工艺氨氮去除的负荷,而且最终通过采用本方法将废水中氨氮量处理到25mg/l。利用水力旋流器和污泥回流泵可以将改性膨润土重新进入絮凝区内进行利用,一方面,使得改性膨润土可以循环利用,大大增加了改性膨润土的利用率,减少投加量;另一方面,回流至絮凝内的改性膨润土作为晶核,形成更加密实、密度更大的矾花,使得矾花在斜管处沉降更快,最终水力上升流速高达20~30m/h,大大减小了斜管处使用面积,减小沉淀分离区的面积,减少占地,也节省了投资。本发明进一步设置为:吸附步骤中,向吸附区内投加改性膨润土,以污水中氨氮含量计,改性膨润土的投加量与所需要去除氨氮的质量比为10:1~100:1之间,且控制吸附区内废水与改性膨润土接触的驻留时间为8~10min;其中,改性膨润土的具体制备方法为:在钠基膨润土原料中加入改性剂乙二胺四乙酸二钠和蒸馏水形成原液,其中,改性剂乙二胺四乙酸二钠和钠基膨润土原料的重量比为1:3~5,改性剂乙二胺四乙酸二钠与蒸馏水的重量比为1:100~1000,然后调节原液的ph值在7~9之间,加热至30~40℃,并在此温度下反应5~10min,反应完成后离心烘干磨碎,使得改性膨润土的粒径为100~135μm;混凝步骤中,向混凝区内投加混凝剂,保持混凝区内混凝剂浓度为100~150mg/l,且控制混凝区内废水与混凝剂接触的驻留时间为2~3min。絮凝步骤中,向絮凝区内投加絮凝剂,保持絮凝区内絮凝剂浓度为1~2mg/l,在系统稳定运行之前投加微砂,保持絮凝区内微砂浓度为3~5g/l,系统稳定运行之后,不再添加微砂,且控制絮凝区内废水与絮凝剂接触的驻留时间为6~10min。本发明进一步设置为:采用以下控制沉淀分离区底部的污泥层厚度在0.5~1m之间:通过污泥取样器检测沉淀分离区内污泥层的厚度,当污泥层厚度小于0.5m时,减小污泥回流泵的流量,调整污泥回流泵的流量大于等于进水流量的1%且小于进水流量的3%,待污泥层厚度恢复在0.5~1.0m后,污泥回流泵回流量调整为进水流量的3%~5%;当污泥层厚度大于1.0m时,增大污泥回流泵的流量,使得污泥回流泵的流量大于进水流量的5%且小于等于进水流量的10%,待污泥层厚度恢复在0.5~1.0m后,污泥回流泵回流量调整为进水流量的3%~5%。通过采用上述技术方案,控制沉淀分离区内的污泥层高度始终在0.5~1.0m之间,一方面提高了排出去的污泥浓度,减少处理的污泥量,另一方面,相较于一般的加砂沉淀池,大大减小了池内的污泥量,减小了沉淀池的体积,节省污泥脱水所需要的耗电量。综上所述,本发明的有益技术效果为:1、本发明中吸附区和改性膨润土投入管的设置使得可以将改性膨润土投入吸附区内,对废水中氨氮进行吸附,减小微砂的使用量,节省成本,而且具有有效的氨氮沉淀去除能力,最终可以将废水中氨氮量处理到25mg/l,大大减小了后续处理的负荷;2、本发明中采用具有螺旋结构的导流筒,使得废水可以沿着螺纹内壁运动,过程中一方面废水与絮凝剂接触时间更长,同时大大减小废水流动过程中内部循环所需要的能量,更加节能,且水流更加稳定,使得废水与药剂的混合效果更好,药剂的利用率更高,絮凝剂、改性膨润土和水以及微砂形成一个最佳的絮凝效果,提高氨氮处理效率;3、絮凝搅拌器叶轮推动的方向与废水在导流筒内的流动方向相同,大大减小了所需电能,形成一个内部循环,大大提高了药剂的使用效率;4、本发明中吸泥装置的设置大大减小了电耗,节约了能源。除此之外,如此设置,更有利于吸泥过程的进行,使得吸泥效率更高,形成的泥流更加稳定,且不会形成污泥死角,而且回流污泥浓度高达80~90%;5、利用水力旋流器和污泥回流泵可以将改性膨润土重新进入絮凝区内进行利用,一方面,使得改性膨润土可以循环利用,大大增加了改性膨润土的利用率,减少投加量;另一方面,回流至絮凝区内的改性膨润土作为晶核,形成更加密实、密度更大的矾花,使得矾花在斜管处沉降更快,而且可使水力上升流速高达20~30m/h,大大减小了斜管处使用面积,减小沉淀分离区的面积,减少占地面积,也节省了投资。附图说明图1是本发明的整体结构示意图;图2是本发明中体现混凝区与絮凝区的连接关系示意图;图3是本发明中体现筒本体的结构示意图;图4是本发明中体现锥形筒的结构示意图;图5是本发明中体现导流筒的结构示意图;图6是本发明中体现吸泥装置的结构示意图;图7是本发明中体现污泥采样器的结构示意图;图8是本发明中体现进泥口的结构示意图。图中,1、配水井;11、进水闸板;2、吸附区;21、改性膨润土加入管;22、吸附搅拌器;23、第一挡板;3、混凝区;31、引流管道;32、混凝剂加入管;33、混凝搅拌器;4、絮凝区;41、絮凝剂加入管;42、导流筒;421、筒本体;4211、导出端;422、锥形筒;4221、导入端;43、絮凝投加环;44、絮凝搅拌器;46、微砂加入管;47、第二挡板;48、过水通道;5、沉淀分离区;51、斜管分离区;52、出水槽;53、出水渠;54、出水闸阀;6、吸泥装置;61、排泥孔;62、集泥筒;63、吸泥主管;631、吸泥孔;64、电机;65、连接轴;68、密封圈;7、泥位控制装置;71、流量控制阀;8、回收管线;81、污泥回流泵;82、水力旋流器;821、溢流口;822、底流口;84、弃污管;85、污泥浓缩池;9、污泥采样器;91、取泥管;911、透明管;912、第一连接件;913、第二连接件;914、顶紧螺栓;92、端盖;93、进泥口;94、挡杆;95、挡泥球;96、排泥杆。具体实施方式参照图1,本发明公开的一种氨氮废水处理系统包括沿废水流动方向依次连通的吸附区2、混凝区3、絮凝区4和沉淀分离区5,吸附区2远离沉淀分离区5一侧通过一进水闸板11连接有废水分配的配水井1。吸附区2与混凝区3以及混凝区3与絮凝区4之间通过一引流管道31或一过水堰连通。絮凝区4与沉淀分离区5之间设有过水堰,过水堰一般为相邻两区的共用室壁,且该共用室壁的顶部低于池顶标高。沉淀分离区5远离絮凝区4一端连通有出水渠53,出水渠53设置有出水闸阀54。其中,吸附区2连接有投入改性膨润土的改性膨润土加入管21,混凝区3连接有投入混凝剂的混凝剂加入管32,絮凝区4连接有投入絮凝剂的絮凝剂加入管41以及投入微砂的微砂加入管46,沉淀分离区5的池形可以呈圆形也可以呈方形。采用上述系统,废水经过配水井1进行配水,然后通过进水闸板11进入吸附区2,吸附区2内投加改性膨润土,然后进入混凝区3,混凝区3内投加混凝剂,在混凝剂的作用下,水中的污染物以及悬浮物进行脱稳、电中和、吸附架桥等复杂的过程,形成很多细小的矾花,与添加的微砂充分混合,然后通过引流管道31或过水堰进入到絮凝区4,在絮凝区4投加絮凝剂,再以微砂与改性膨润土为晶核在絮凝剂的作用下细小的矾花会迅速聚集形成较大的密实的大矾花,接着污水携带大矾花进入沉淀分离区5内进行泥水分离,分离后的清水从出水渠53流出。在本发明的氨氮废水处理系统,吸附区2内设置有吸附搅拌器22,混凝区3内也设置有混凝搅拌器33。设置吸附区2,可以向进入吸附区2内的废水中加入改性膨润土,再结合吸附搅拌器22的搅拌作用,可以将废水与改性膨润土的接触混合更加充分,然后通过过水堰翻流至混凝区3内,与混凝剂进行混合。同理,混凝区3内的混凝搅拌器33可以将废水、改性膨润土以及混凝剂混合地更加充分。如图1和图2所示,絮凝区4内部安装有上、下端开口且连通的导流筒42,导流筒42的污水进入端为喇叭状。当混凝区3与絮凝区4之间通过引流管道31连通时,引流管道31的一端与所述混凝区3底部连通,另一端自导流筒42的下端伸入到导流筒42内,此时,吸附区2与混凝区3之间通过过水堰连通,且导流筒42下端为喇叭口状,污水自混凝区3下方进入絮凝区4,当采用这种方式的时候,为了防止从配水井1流向吸附区2内的水形成短流,直接从过水堰流向混凝区3内,故在吸附区2内设置有第一挡板23,第一挡板23下端高于吸附区2底面,从而在第一挡板23和吸附区2底面之间形成一个过水通道,使来自配水井1的污水自该过水通道流入吸附区2内,然后通过过水堰翻流至混凝区3内,然后在混凝搅拌器33的作用下充分与混凝剂混合接触。结合图2,当混凝区3与絮凝区4之间通过过水堰连通时,吸附区2和混凝区3之间通过引流管道31连通,且引流管道31的一端与所述吸附区2底部连通,另一端与所述混凝区3底部连通,导流筒42上端为喇叭口状,此时,污水自混凝区3上方进入絮凝区4。如图1和图3所示,所述导流筒42内壁设有螺旋线延伸方向与导流筒42内循环污水的流动方向一致的内螺旋,当导流筒42喇叭口朝下时,导流筒42内壁的内螺旋沿着远离喇叭口方向螺旋上升;结合图2和图4,当导流筒42喇叭口朝上时,导流筒42内壁的内螺旋沿着远离喇叭口方向螺旋下降。内螺旋的设置使得污水可以沿着内螺纹流动,在此过程中,可使得污水与絮凝剂接触时间更长,同时大大减小污水流动过程中内部循环所需要的能量,更加节能,且水流更加稳定,使得污水与药剂(絮凝剂、微砂以及改性膨润土)的混合效果更好,药剂的利用率更高。此时,絮凝剂、微砂和水以及改性膨润土形成一个最佳的絮凝效果。在优选的实施方案中,所述导流筒42外壁设有与所述导流筒42内螺旋的螺旋方向相反的外螺旋。外螺旋的设置使得进入导流筒42内污水进行内部循环的时候,沿着导流筒42外周面的污水也可以沿着导流筒42的外螺旋下降,减小水流流动过程中的内耗,进一步提高药剂与污水的混合效果。上述两种方式均可,为了更清楚方便阐述导流筒42的结构,以下内容中以混凝区3与絮凝区4之间通过引流管道31连通的方式(见图1)阐述导流筒42的具体结构。如图5所示,导流筒42在竖直方向上包括柱形筒本体421以及与导流筒42本体下端一体连接的锥形筒422,筒本体421上端开口处形成导出端4211,锥形筒422下端开口处形成导入端4221,导入端4221的内径大于导出端4211的内径。引流管道31自导流筒42的导入端4221处于伸入到筒本体421内。如此设置,使得引流管道31内的污水从导入端4221进入导流筒42内,然后与絮凝区4内加入的絮凝剂反应,然后沿着导出端4211流出,进而沿着导流筒42外壁面流下,再从导入端4221进入,使得污水在导流筒42处形成顺时针循环,甚至导流筒42内可以形成8~10倍的循环量,大大节约了药剂的利用效率。并且,导流筒42下端采用喇叭口状导入端4221进水,有利于导流筒42外的水进入导流筒42内。此外,导流筒42内部上部水平设有用于投入絮凝剂的絮凝投加环43,絮凝投加环43为与絮凝剂加入管41连接的环形管,环形管上开设有若干喷淋口,此为现有技术,本实施例不再详述。通过该絮凝投加环43在絮凝区4内投入絮凝剂,以微砂为晶核,再结合絮凝剂的作用,细小的矾花能迅速聚集形成较大的密实的大矾花。絮凝投加环43的设置使得絮凝剂和微砂的作用更完全,且投加环的方式使得絮凝剂的投加方向与水流的方向相反,絮凝剂与污水以及污水中的微砂充分混合。另外,导流筒42内设置有絮凝搅拌器44,絮凝搅拌器44的叶轮设置为将污水自下而上推动的轴流式叶轮,且叶轮位于絮凝投加环43下方。絮凝搅拌器44的设置增大对污水的扰动效果,使得污水更充分地与絮凝剂接触形成矾花,叶轮的设置使得污水在导流筒42内的流动方向与叶轮推动方向相同,大大减小了所需电能,配合导流筒42的设置,使得导流筒42周围的污水流动方向形成一个顺时针循环,大大提高了药剂的使用效率。相应地,当采用图2所示的污水通过过水堰进入絮凝区4的这种方式中,所述絮凝搅拌器44的叶轮为将污水自上而下推动的轴流式叶轮。另外,如图5所示,絮凝区4内还设置有第二挡板47,第二挡板47处于导流筒42与絮凝区4靠近沉淀分离区5的一侧的室壁之间,第二挡板47下端处于絮凝区4底部上方,从而第二挡板47下端与絮凝区4底部形成供絮凝区4内的污水流向沉淀分离区5的过水通道48,且第二挡板47底端朝向絮凝区4一侧倾斜。第二挡板47的设置使得絮凝区4内的污水流向沉淀分离区5的过程中,对水流具有一定的稳流效果。为加速泥水分离,回看图1,沉淀分离区5的中部设置有由斜管填料构成的斜管分离区51,沉淀分离区5的上部架设有若干个带溢流孔或溢流堰的出水槽52,出水槽52与出水渠53连通。絮凝区4内的污水和大矾花通过第二挡板47下端的过水通道48流入沉淀分离区5,由于矾花较重,在斜管分离区51中很快地进行了泥水分离,清水进入出水槽52内,最终进入出水渠53流出,而较重的矾花形成污泥落入沉淀分离区5的底部。参照图1和图6,在沉淀分离区5内设置有吸泥装置6和用于监测并控制沉淀分离区5底部污泥厚度的泥位控制装置7,吸泥装置6包括开设在沉淀分离区5底部中心处的排泥孔61、底部插入排泥孔61中并与排泥孔61转动配合的集泥筒62、两根沿集泥筒62的中心轴线对称连通在集泥筒62的外周壁上的吸泥主管63、架设在沉淀分离区5中心处上方的电机64以及连接电机64输出端与集泥筒62的连接轴65,吸泥主管63的末端通过连接线连接在连接轴65上;集泥筒62的底部与排泥孔61连通;吸泥主管63远离集泥筒62的一端封闭,且吸泥主管63上开有圆形的吸泥孔631;在集泥筒62与排泥孔61内侧壁之间设有密封圈68,密封圈68与排泥孔61固定连接,以避免污泥从集泥筒62与排泥孔61之间的缝隙进入排泥孔61内,导致吸泥主管中的负压变小,使吸泥主管的吸泥效果变差。此外,该氨氮废水处理系统还包括一连通絮凝区4和沉淀分离区5底部的回收管线8,其用于对沉淀分离区5底部的污泥混合物进行收集并循环利用。回收管线8的一端与排泥孔61连通,另一端与絮凝区4连通。回收管线8上依次设有污泥回流泵81以及水力旋流器82。水力旋流器82包括溢流口821和底流口822,水力旋流器82的底流口822连接到絮凝区4,溢流口821通过弃污管84连接有污泥浓缩池85。值得注意的是,在本发明中,吸泥主管63朝向沉淀分离区5底部一侧具有侧楞,这样可以在吸泥主管63转动的同时起到刮泥作用。优选情况下,吸泥主管63的截面呈菱形,在吸泥主管63朝向沉淀分离区5底部且位于转动方向的一侧开有吸泥孔631,吸泥孔631的直径自吸泥管末端至吸泥主管63中心方向逐渐减小,以提高吸泥效率,保证泥流在吸泥主管63中流动的稳定性,避免吸泥死角。打开电机64和污泥回流泵81后,电机64会带动集泥筒62转动,从而带动吸泥主管63绕集泥筒62转动,从而使污泥回流泵81可以将沉淀分离区5底部的污泥经吸泥主管63吸入集泥筒62内,从而使电机64在驱动吸泥主管63转动时所需的扭矩更小,沉淀分离区5底部的污泥厚度对电机64驱动吸泥主管63转动的影响变小,如此,当沉淀分离区5底部的污泥厚度达到0.5m~1m时,电机64依然可以顺畅的带动吸泥主管63转动,这时,沉淀分离区5底部的污泥浓度较高,可以达到80-90%,从而导致经吸泥主管63进入集泥筒62内的污泥浓度得以提高。当污泥进入集泥筒62后会在污泥回流泵81的作用下会回流至水力旋流器82中进行砂、改性膨润土和泥水的分离,大部分微砂和改性膨润土从底流口822流出进入絮凝区4,再次充当矾花晶核,这样系统运行稳定后,不需要补充微砂,大大减少了微砂的使用,提高了微砂的利用率。参照图1,泥位控制装置7包括配置在沉淀分离区5内的污泥采样器9和连接在回收管线8上的流量控制阀71。工作人员可以通过污泥采样器9来监测沉淀分离区5底部污泥厚度,操作简单,泥层监测结果直观,效果直接;还可以通过流量控制阀71来控制回收管线8内污泥的流量,来对沉淀分离区5底部的污泥厚度进行调整。结合图7和图8,污泥采样器9包括透明的取泥管91、螺纹连接在取泥管91一端的端盖92、开设在端盖92中心处的进泥口93、垂直于取泥管91轴线固定在取泥管91内靠近端盖92一端的挡杆94以及设置在取泥管91内且位于端盖92与挡杆94之间的挡泥球95。值得注意的是挡泥球95的直径大于进泥口93的孔径,小于取泥管91的内径,在挡泥球95上固定连接有排泥杆96,排泥杆96背离挡泥球95的一端由进泥口93穿过端盖92,暴露在取泥管91外,排泥杆96的直径要小于进泥口93的直径,以使排泥杆96可以在进泥口93中自由滑动。取泥管91包括若干连接在一起的透明管911,相邻两根透明管911在轴向相对的一端分别插接有第一连接件912和第二连接件913,第一连接件912与第二连接件913之间采用螺纹连接,在第一连接件912和第二连接件913的侧壁上均插设有顶紧螺栓914,以加固第一连接件912或第二连接件913与透明管911的连接。当工作人员需要了解到沉淀分离区5底部的污泥厚度时,可以根据沉淀分离区5的深度来调整污泥采样器9的长度,随后将污泥采样器9设有进泥口93的一端插入沉淀分离区5底部,当污泥采样器插入污泥中时,污泥会推动挡泥球95朝向挡杆94运动,同时污泥会经进泥口93以及挡泥球95与取泥管91之间的缝隙进入取泥管91中,当污泥采样器9触碰到沉淀分离区5底部时,工作人员应向上提起污泥采样器9,这时,挡泥球95在其自身重力以及取泥管91中污泥的作用下,将进泥口93封堵,从而使取泥管91中的污泥无法从污泥采样器9中流出,当工人将污泥采样器9从沉淀分离区5中取出后,可以对污泥采样器9中的污泥厚度进行丈量,从而得到沉淀分离区5底部的污泥厚度,随后工作人员可以向挡杆94所在方向推动排泥杆96,使污泥从污泥采样器9中流出。本发明还提供了采用上述氨氮废水处理系统实现氨氮废水处理的方法,包括以下步骤:吸附:废水经过配水井1配水后进入吸附区2内,向吸附区2内投加改性膨润土,搅拌,且控制吸附区2内废水与改性膨润土接触的驻留时间为8~10min后,流至混凝区3内;其中,以污水中氨氮含量计,改性膨润土的投加量与所需要去除氨氮的质量比为10:1~100:1之间,改性膨润土的具体制备方法为:在钠基膨润土原料中加入改性剂乙二胺四乙酸二钠和蒸馏水形成原液,然后调节原液的ph值在7~9之间,加热至30~40℃,并在此温度下反应5~10min,反应完成后离心烘干磨碎,使得改性膨润土的粒径为100~135μm,其中,改性剂乙二胺四乙酸二钠和钠基膨润土原料的重量比为1:3~5,改性剂乙二胺四乙酸二钠与蒸馏水的重量比为1:100~1000;混凝:向混凝区3内投加混凝剂,保持混凝区3内混凝剂浓度为100~150mg/l之间,控制混凝区3内废水反应时间为2~3min,废水的污染物以及悬浮物与混凝剂混合后形成小矾花,然后与改性膨润土混合后进入絮凝区4;絮凝:向絮凝区4内投加1~2mg/l的絮凝剂,保持絮凝区4内絮凝剂浓度为1~2mg/l之间,在系统未稳定之前向絮凝区4内投加微砂并保持絮凝区4内微砂浓度为3~5g/l,待系统稳定之后不再添加微砂,同时,控制污水与絮凝剂和微砂反应6~10min,以微砂和改性膨润土为晶核,混凝区3内形成的小矾花和废水通过引流管道31或过水堰进入设置有内螺旋的导流筒42内,然后在添加入导流筒42内的絮凝剂的作用下,小矾花聚集形成密实的大矾花后进入沉淀分离区5;沉淀分离:含有大矾花的废水进入沉淀分离区5后,进入斜管分离区51进行泥水分离,然后清水通过斜管填料进入出水槽52,然后汇合从出水渠53流出,矾花形成污泥落在沉淀分离区5底部,当沉淀分离区5底部的污泥累计达到0.5~1m的厚度时,打开电机64和污泥回流泵81,污泥在吸泥装置6的作用下进入集泥筒62内,然后在污泥回流泵81的作用下进入水力旋流器82,经过水力旋流器82分离后的改性膨润土进入絮凝区4再次吸附;过程中,调节污泥回流泵81,控制污泥回流量为进水流量的3%~5%,使得集泥筒62内污泥全部通过污泥回流泵81进入水力旋流器82内,进入水力旋流器82的污泥中约80%污泥通过弃污管84进入污泥浓缩池85,约20%污泥进入絮凝区4内,其中进入水力旋流器82的污泥中微砂和大部分的改性膨润土进入絮凝区4;除此之外,通过控制污泥回流量和检测污泥层厚度,使得沉淀分离区5底部污泥厚度保持在0.5~1m之间。在污泥从沉淀分离区5内排出的过程中,若出现污泥厚度大于1m的情况,此时沉淀分离区5内出现翻泥,很多污泥直接从出水渠流出,导致出水水质变差,此时,调整流量控制阀71,使污泥回流泵81的流量大于进水流量的5%且小于等于进水流量的10%,加快排泥速度;若污泥厚度小于0.5m,则污泥回流泵81的流量减小,此时,调整流量控制阀71,使污泥回流泵81的流量大于等于进水流量的1%且小于进水流量的3%,减慢排泥速度。通过上述两种方法来保持沉淀分离区5底部的污泥厚度保持在0.5~1m之间。本发明中,改性膨润土的粒径为100~135μm;混凝剂可为铝盐、铁盐、高分子聚合铝盐、聚合铁盐中的一种或几种;微砂的粒径为100~135μm;絮凝剂采用聚丙烯酰胺,或其它本领域常用絮凝剂。以下为改性膨润土的原料制备例制备例1在钠基膨润土原料中加入改性剂乙二胺四乙酸二钠和蒸馏水形成原液,其中,改性剂乙二胺四乙酸二钠和钠基膨润土原料的重量比为1:3,改性剂乙二胺四乙酸二钠与蒸馏水的重量比为1:100,然后调节原液的ph值为7,加热至30℃,并在此温度下反应5min,反应完成后离心烘干磨碎,使得改性膨润土的粒径为100~135μm;制备例2在钠基膨润土原料中加入改性剂乙二胺四乙酸二钠和蒸馏水形成原液,其中,改性剂乙二胺四乙酸二钠和钠基膨润土原料的重量比为1:4,改性剂乙二胺四乙酸二钠与蒸馏水的重量比为1:600,然后调节原液的ph值为8,加热至35℃,并在此温度下反应8min,反应完成后离心烘干磨碎,使得改性膨润土的粒径为100~135μm;制备例3在钠基膨润土原料中加入改性剂乙二胺四乙酸二钠和蒸馏水形成原液,其中,改性剂乙二胺四乙酸二钠和钠基膨润土原料的重量比为1:5,改性剂乙二胺四乙酸二钠与蒸馏水的重量比为1:1000,然后调节原液的ph值为9,加热至40℃,并在此温度下反应10min,反应完成后离心烘干磨碎,使得改性膨润土的粒径为100~135μm;实施例1将上述氨氮处理系统和方法应用用于沈阳某污水处理厂。水质进出水要求如下表1所示。表1:水质总磷(mg/l)氨氮(mg/l)ss(mg/l)cod(mg/l)进水水质635300200出水水质32530100具体处理操作如下:吸附:废水(氨氮含量为35mg/l)经过配水井1配水后进入吸附区2内,以污水中氨氮含量计,向吸附区2内投加制备例2中制得的改性膨润土,改性膨润土的投加量与所需要去除氨氮的质量比为50:1,搅拌,且控制吸附区(2)内废水与改性膨润土接触的驻留时间为9min后,流至混凝区3内;混凝:向混凝区3内投加混凝剂(pac,即聚合氯化铝),保持混凝区3内混凝剂浓度为125mg/l,控制混凝区3内废水反应时间为2min,废水的污染物以及悬浮物与混凝剂混合后形成小矾花,然后与改性膨润土混合后进入絮凝区4;絮凝:向絮凝区4内投加絮凝剂(聚丙烯酰胺),保持絮凝区4内絮凝剂浓度为1.5mg/l,在系统未稳定之前向絮凝区4内投加微砂并保持絮凝区4内微砂浓度为4g/l,待系统稳定之后不再添加微砂,同时,控制污水与絮凝剂和微砂反应8min,以微砂和改性膨润土为晶核,混凝区3内形成的小矾花和废水通过引流管道31或过水堰进入设置有内螺旋的导流筒42内,然后在添加入导流筒42内的絮凝剂的作用下,小矾花聚集形成密实的大矾花后进入沉淀分离区5;沉淀分离:含有大矾花的废水进入沉淀分离区5后,进入斜管分离区51进行泥水分离,然后清水通过斜管填料进入出水槽52,然后汇合从出水渠53流出,矾花形成污泥落在沉淀分离区5底部,当沉淀分离区5底部的污泥累计达到0.5~1m的厚度时,打开电机64和污泥回流泵81,污泥在吸泥装置6的作用下进入集泥筒62内,然后在污泥回流泵81的作用下进入水力旋流器82,经过水力旋流器82分离后的改性膨润土进入吸附区2再次吸附,过程中,调节污泥回流泵81,控制污泥回流量为进水流量的3%,使得集泥筒62内污泥全部通过污泥回流泵81进入水力旋流器82内,进入水力旋流器82的污泥中约80%污泥通过弃污管84进入污泥浓缩池85,约20%污泥进入絮凝区4内,其中进入水力旋流器82的污泥中大部分的改性膨润土和微砂进入絮凝区4。除此之外,控制污泥回流量和检测污泥层厚度,使得沉淀分离区5底部污泥厚度保持在0.5~1m之间,在污泥从沉淀分离区5内排出的过程中,若出现污泥厚度大于1m的情况,调整流量控制阀71,使污泥回流泵81流量为进水流量的6%,待污泥层厚度恢复在0.5~1.0m后,污泥回流泵81回流量改为进水流量的3%;若污泥厚度小于0.5m,调整流量控制阀71,使污泥回流泵81流量为进水流量的2%,待污泥层厚度恢复在0.5~1.0m后,污泥回流泵81回流量改为进水流量的3%。在处理过程中对于不同厚度时出水的水质如下表2所示。表2:从上表2可以看出,当控制在泥层厚度在0.5~1.0m之间时,出水水质达标,排出去的污泥浓度达到50g/l左右,当泥层厚度小于0.5m时出水达标但是排出去的污泥浓度较小,当污泥层厚度大于1.0m时,斜管上端出现翻泥,出水水质不达标。实施例2将上述氨氮处理系统和方法应用用于安徽某污水处理厂。水质进出水要求如下表3所示。表3:水质氨氮(mg/l)ss(mg/l)cod(mg/l)进水水质30300200出水水质2530100按照实施例1中的方法对上述污水处理厂进行处理,不同之处在于,吸附步骤中,改性膨润土的投加量与所需去除的氨氮质量比为10:1;沉淀分离步骤中,污泥回流泵回流量为进水流量的5%;污泥层的厚度控制0.5~1m;当污泥层厚度低于0.5m时,污泥回流泵81的流量调整为进水流量的1%,待污泥层厚度恢复在0.5~1.0m后,污泥回流泵81的流量调整为进水流量的5%;当污泥层厚度高于1.0时,污泥回流泵81的流量调整为进水流量的8%,待污泥层厚度恢复在0.5~1.0m后,污泥回流泵81的流量调整为进水流量的5%。在处理过程中对于不同厚度时出水的水质如下表4所示。表4:从上表4可以看出,当控制在泥层厚度在0.5~1.0m之间时,出水水质达标,排出去的污泥浓度达到50g/l左右,当泥层厚度小于0.5m时出水达标但是排出去的污泥浓度较小,当污泥层厚度大于1.0m时,斜管上端出现翻泥,出水水质不达标。实施例3将上述氨氮处理系统和方法应用用于广州某污水处理厂。水质进出水要求如下表5所示。表5:水质氨氮(mg/l)ss(mg/l)进水水质35250出水水质2530按照实施例1中的方法对上述污水处理厂进行处理,不同之处在于,吸附步骤中,改性膨润土的投加量与所需去除的氨氮质量比为100:1;沉淀分离步骤中,污泥回流泵回流量为进水流量的4%;污泥层的厚度控制0.5~1m;当污泥层厚度低于0.5m时,污泥回流泵81的流量调整为进水流量的1%,待污泥层厚度恢复在0.5~1.0m后,污泥回流泵81的流量调整为进水流量的4%;当污泥层厚度高于1.0时,污泥回流泵81的流量调整为进水流量的10%,待污泥层厚度恢复在0.5~1.0m后,污泥回流泵81的流量调整为进水流量的4%。在处理过程中对于不同厚度时出水的水质如下表6所示。表6:从上表6可以看出,当控制在泥层厚度在0.5~1.0m之间时,出水水质达标,排出去的污泥浓度达到50g/l左右,当泥层厚度小于0.5m时出水达标但是排出去的污泥浓度较小,当污泥层厚度大于1.0m时,斜管上端出现翻泥,出水水质不达标。实施例4对于实施例1中相同的水质进行实施例1中相同的操作方法,不同之处在于,本实施例中选用的改性膨润土为制备例1制备的改性膨润土。实施例5对于实施例1中相同的水质进行实施例1中相同的操作方法,不同之处在于,本实施例中选用的改性膨润土为制备例3制备的改性膨润土。实施例6对于实施例1中相同的水质进行实施例1中相同的操作方法,不同之处在于,吸附步骤中,向吸附区2内投加的改性膨润土与所需要去除氨氮的质量比为50:1,搅拌,且控制吸附区(2)内废水与改性膨润土接触的驻留时间为8min后,流至混凝区3内;混凝步骤中:向混凝区3内投加混凝剂(pac,即聚合氯化铝),投加混凝剂浓度为100mg/l,控制混凝区3内废水反应时间为2min;絮凝:向絮凝区4内投加絮凝剂(聚丙烯酰胺),投加絮凝剂浓度为1mg/l,在系统未稳定之前向絮凝区4内投加微砂并保持絮凝区4内微砂浓度为3g/l,待系统稳定之后不再添加微砂,同时,控制污水与絮凝剂和微砂反应6min。实施例7对于实施例1中相同的水质进行实施例1中相同的操作方法,不同之处在于,吸附步骤中,向吸附区2内投加改性膨润土后,控制吸附区(2)内废水与改性膨润土接触的驻留时间为10min后,流至混凝区3内;混凝步骤中:向混凝区3内投加混凝剂(pac,即聚合氯化铝),投加混凝剂浓度为150mg/l,控制混凝区3内废水反应时间为3min;絮凝:向絮凝区4内投加絮凝剂(聚丙烯酰胺),投加絮凝剂浓度为2mg/l,在系统未稳定之前向絮凝区4内投加微砂并保持絮凝区4内微砂浓度为5g/l,待系统稳定之后不再添加微砂,同时,控制污水与絮凝剂和微砂反应10min。上述实施例4~7中进出水水质要求如下表7所示。表7:水质总磷(mg/l)氨氮(mg/l)ss(mg/l)cod(mg/l)进水水质635300200出水水质32530100在上述实施例中污水处理过程中,对于不同污泥厚度时出水水质进行检测,实施例4~7的检测结果如下表8~表11所示。表8实施例4中污水处理检测表9实施例5中污水处理检测表10实施例6中污水处理检测表11实施例7中污水处理检测综上所述:相较于传统的加砂沉淀池稳定运行后,需要定期补充损失的微砂,本发明使用过程中,只有前期系统不稳定的时候加入微砂,保证系统运行稳定之后,依靠定量投加的改性膨润土代替损失的微砂,大大降低了成本,还可以去除吸附废水中的氨氮以及cod,减小后续工艺氨氮、cod去除的负荷。除此之外,利用水力旋流器82和污泥回流泵81可以将污泥中的部分改性膨润土重新进入絮凝区进行利用,一方面,使得改性膨润土可以循环利用,大大增加了改性膨润土的利用率,减少投加量;另一方面,回流至絮凝区4内的改性膨润土作为晶核,形成更加密实、密度更大的矾花,使得矾花在斜管处沉降更快,最终水力上升流速高达20~30m/h,大大减小了斜管处使用面积,减小沉淀分离区5的面积,减少占地,也节省了投资。相较于传统的加砂沉淀池外排的污泥量比较大,浓度比较小,且当沉淀分离区的污泥层厚度较大时,容易导致出水斜管翻泥,本发明中通过污泥取样器检测沉淀分离区污泥层厚度,而且通过控制污泥回流泵81的污泥流量,控制沉淀分离区5内的污泥层高度始终维持在0.5~1m,一来提高了排出去的污泥浓度,减少处理的污泥量,大大提高了排泥量,减小了沉淀池的体积,节省污泥脱水所需要的耗电量;相较于现有技术中采用刮泥机,当污泥形成较厚的污泥层的时候,需要更大扭矩的刮泥机,则投资成本随之增加,本发明中采用吸泥装置6,克服了上述问题,且大大减小了电耗,节约了能源。除此之外,相较于传统的加砂沉淀池统的池型设计和刮泥机配合使用,存在刮泥不均匀,易形成死角,本发明中采用的吸泥装置6更有利于吸泥过程的进行,使得吸泥效率更高,形成的泥流更加稳定,且不会形成污泥死角,而且回流污泥浓度高达80~90%。相较于现有技术,如授权公告号为cn101641297b公开的发明名称为“采用压载絮凝和倾析处理水的方法与装置”的文献中记载的微砂经过沉淀区沉淀后经过中间槽然后在泵的作用下进入絮凝槽中继续反应,本发明中利用泵直接将沉淀分离区5中沉淀的污泥泵入水力旋流器82,减少了工艺流程,使得流程更加简洁,而且最终进入水力旋流器82中的改性膨润土大部分进入絮凝区4重新利用。最终,通过采用本系统和方法,可将废水中氨氮量处理到25mg/l,cod处理到100mg/l以下,大大减小了后续处理的负荷。本具体实施方式的实施例均为本发明的较佳实施例,并非依此限制本发明的保护范围,故:凡依本发明的结构、形状、原理所做的等效变化,均应涵盖于本发明的保护范围之内。当前第1页12