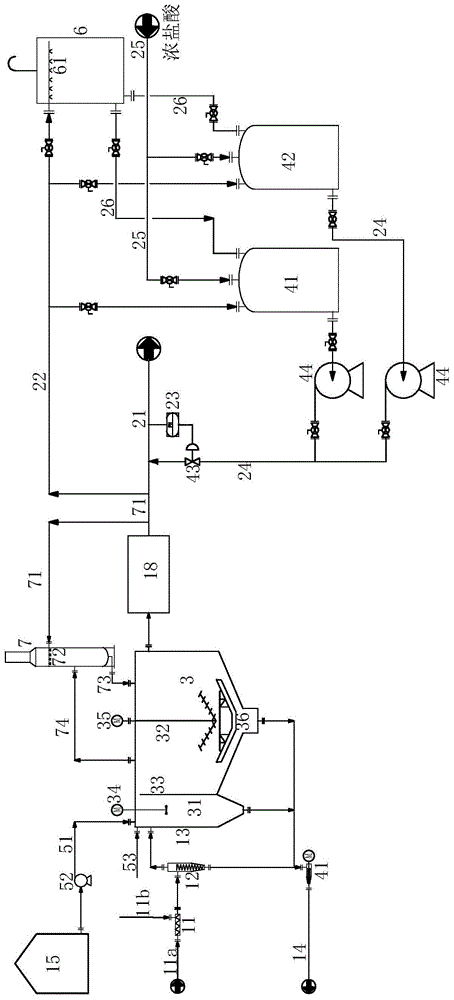
本发明涉及到废水处理领域,尤其涉及一种含氨高硬度废水预处理方法。
背景技术:
:现有的高氨氮废水处理方法通常是先利用20wt%naoh溶液调节废水ph值至12以上,同时使废水中固定铵盐解析成游离氨从而达到从废水中分离的目的。由于此措施所需naoh溶液消耗量大,造成装置操作成本与能耗较高;此外naoh溶液还能降低废水中钙镁离子浓度,即达到降低系统中总硬度的目的,但生成的ca(oh)2溶液属于微溶物质,仅利用重力沉降方法去除废水中的颗粒和悬浮物,需要消耗较长的重力沉降时间才能达到要求的分离效果,造成沉淀池或者分离器尺寸大、占地面积多、投资高,最终造成整个高氨氮废水处理装置投资较高。并且由于采用单一naoh溶液调节废水中ph值,造成化学品消耗量较大和操作成本较高。现有技术对合格污水调节ph值通常采用酸液反调工艺,用新鲜水配置酸液,将酸液加入到外排灰水中,调节灰水的ph值。酸液浓度高、用量大,导致新鲜水用量大、能耗高;并且利用高浓度酸液进行ph反调,容易导致灰水ph值波动较大,对下游生化处理装置存在安全隐患,对处理后灰水输送至下游装置的管线也存在腐蚀问题,生产操作与维护风险大;而且新鲜水的大量加入加大了下游生化处理系统的负荷。技术实现要素:本发明所要解决的技术问题是针对现有技术的现状提供一种装置投资低、运行成本低、分离效果好的含氨高硬度废水预处理方法。本发明解决上述技术问题所采用的技术方案为:一种含氨高硬度废水预处理方法,其特征在于包括下述步骤:来自上游气化装置的氨含量为700~1000ppm、caco3含量1200~1500mg/l、压力为0.3mpag~0.5mpag的灰水与浓度为15~20wt%的na2co3溶液混合均匀后进入旋流分离器进行旋流分离,其中加入的na2co3溶液量占灰水处理量的0.2~0.3wt%;分离出的污泥排入下游,分离出的清液进入第一沉降槽内进行加药沉降;向所述第一沉降槽内加入浓度为8~12wt%的聚合氯化铝和浓度为0.2~0.5wt%的聚丙烯酰胺以及浓度为15~20wt%的碱液,搅拌混合均匀后进行重力沉降;沉降后的污泥排入下游,沉降后生成的一次清液进入第二沉降槽进行二次沉降;沉降后的固相排入下游,沉降后的二次清液送去汽提系统进行汽提,分离出灰水中的氨;第一沉降槽和第二沉降槽中逸散出的氨气引入到洗氨塔中进行洗涤吸收;所述汽提系统汽提出氨后得到的净化灰水分为四股;其中第一股净化灰水引入所述洗氨塔内作为喷淋水吸收氨,第二股净化灰水送去稀盐酸罐与浓度为20~30%wt的浓盐酸混合调配成浓度为1~2%wt的稀盐酸,与第四股净化灰水混合调节第四股净化灰水的ph值为6-9后送去下游生化处理系统;第三股净化灰水送去酸雾吸收罐洗涤吸收来自稀盐酸中浓盐酸所逸散出的酸雾,吸收了酸雾的净化灰水返回所述稀盐酸罐。较好的,所述稀盐酸罐可以有两个,一个用于配制稀盐酸,一个为配制好的稀盐酸用于与第四股净化灰水混合调配ph值。两个稀盐酸罐并联设置,交替使用,一个反调灰水的ph值,一个配制稀盐酸,从而使得灰水ph值调节连续进行。作为上述各方案的进一步改进,所述第一沉降槽和所述第一沉降槽共用一个槽体,所述槽体内设有隔板将所述槽体的槽腔分隔为并列布置的第一沉降槽和第二沉降槽,第一沉降槽沉降产生的清液溢流漫过所述隔板进入所述第二沉降槽内。进一步地,可以在所述第一沉降槽的上部设有第一搅拌器;所述第一沉降槽的底部大致呈锥状结构;所述第二沉降槽内设有第二搅拌器,所述第二沉降槽的底部大致呈锥状结构,用于收集污泥的耙料机设置在第二沉降槽的底部。该结构更利于污泥的收集和排放。与现有技术相比,本发明所提供的含氨高硬度废水预处理方法首先利用na2co3溶液除去大部分钙镁离子,降低废水总硬度指标,然后利用naoh溶液调节废水中ph值,分级沉淀废水中钙镁离子,降低了naoh溶液消耗量和操作成本,同时降低其固定氨比例,提高汽提效果;利用经过汽提系统处理达标后的合格灰水吸收沉降槽中逸散的氨气,避免引入新鲜水吸收逸散的氨气,降低系统操作负荷和进入下游生化处理装置的废水量;装置投资低、节能降耗效果好,减少了化学品消耗和操作成本,最大程度的降低了分离废水中颗粒和悬浮物,最终满足了装置长周期运行的要求;ph部分值调节系统利用预处理合格后的达标灰水配置稀酸液,同时进行循环反调灰水ph值,降低了装置能耗和新鲜水消耗,同时降低了下游ph值波动,解决了管线腐蚀等安全风险。附图说明图1为本发明实施例示意图。具体实施方式以下结合附图实施例对本发明作进一步详细描述。如图1所示,本发明实施例所使用的设备包括:静态混合器11,用于混合初始废水和na2co3溶液,其第一入口连接废水管线11a,其第二入口连接na2co3溶液输送管线11b,其出口连接分离器12的入口;分离器12,用于对静态混合器11送来的废水和na2co3溶液的混合液进行分离,本实施例中的分离器12为旋流分离器,强制液固旋流分离,分离效果更好;分离器12的底部出口连接污泥排放管道14,分离器的顶部出口连接沉降槽3的入口,分离后的清液由此进入沉降槽3内。沉降槽3,为二级沉降槽,其内设有隔板33将沉降槽的内腔分隔为并列布置的第一沉降槽31和第二沉降槽32,所述隔板33形成第一沉降槽31的清液的溢流隔板,第一沉降槽沉降产生的清液漫过所述隔板33进入所述第二沉降槽32内。第一沉降槽31的上部设有第一搅拌器34,用于充分混合碱液、絮凝剂和混凝剂,加快其在废水中的混合效果,强化沉降效果;第一沉降槽31的底部大致呈锥形,以方便沉降所产生的污泥的下走;第一沉降槽的底部出口连接污泥排放管道14;第一沉降槽的第一入口连接碱液输送管道51,碱液输送管道51上设有碱液泵52,碱液输送管道51连接碱液罐5。第一沉降槽的第二入口连接用于输送絮凝剂和混凝剂的药剂输送管道53。所述第一入口、第二入口均设置在所述第一沉降槽的顶部或上部。第二沉降槽的底部大致呈锥形,以便于沉降污泥下走排放;其底部出口连接污泥排放管道14;第二沉降槽的顶部出口通过氨输送管道74连接洗氨塔7的入口,其顶部入口连接洗氨塔7的排放口。第二沉降槽32内设有第二搅拌器35和污泥收集装置36,用于把沉渣淤泥导向排出口处,防止不均匀沉降;本实施例中的污泥收集装置为耙料机。第二沉降槽32沉降产生清液送至汽提系统18。洗氨塔7,对进入其内的氨气进行洗涤回收,洗氨塔的洗涤液入口连接第一回流管道71,第一回流管道71连接汽提系统18的合格废水排放口。洗氨塔7内设有喷淋器72,以使来自汽提系统的合格废水在洗氨塔内均匀喷淋;喷淋后的含氨混合液经由第二回流管道73返回第二沉降槽32。汽提系统18,用于对第二沉降槽32送来的清液汽提出其中的氨,得到净化灰水。汽提系统为常规技术,可根据需要选用现有技术中的任一种,其入口连接第二沉降槽32的清液出口,其出口分为四路。其中第一股净化灰水引入洗氨塔内作为喷淋水用于吸收氨,第二股净化灰水送去稀盐酸罐与浓盐酸混合调配成稀盐酸,第三股净化灰水送去酸雾吸收罐洗涤吸收来自稀盐酸中浓盐酸所逸散出的酸雾,吸收了酸雾的净化灰水返回所述稀盐酸罐,第四股净化灰水与来自稀盐酸罐的稀盐酸混合调节ph值后送去下游生化处理系统。稀盐酸罐,有两个,包括第一稀盐酸罐41和第二稀盐酸罐42,两个稀盐酸罐并联设置,交替使用,一个反调灰水的ph值,一个配制稀盐酸;每个稀盐酸罐的顶部均设有三个连接口,其中第一连接口连接合格灰水旁管22,第二连接口连接浓盐酸输送管道25,第三连接口通过气液连接管道26连接酸雾吸收罐6的第二料口。酸雾吸收罐6的上部设有使灰水均匀喷洒的喷淋器61,喷淋器61连接第一料口。本实施例中气液连接管道33为不满流管道,气相在管道内上行,液相在管道内下行。各稀盐酸罐的下部或底部还设有第四料口,所述第四料口通过稀盐酸泵44连接稀盐酸输送管道24。稀盐酸输送管道24上设有控制阀43,灰水排放管道21上设有用于检测管道内灰水ph值的ph值检测装置23。控制阀43和ph值检测装置23均连接控制系统(图中未示出);控制系统根据ph值检测装置的实时检测结果控制控制阀43的开度,从而使输送到生化处理系统的灰水ph值在设计范围内。以处理煤制360万吨/年甲醇规模产生600m3/h高氨、高硬度灰水为例进行说明。来自水煤浆气化装置氨含量为700~1000ppm、caco3含量1200~1500mg/l废水首先与浓度为15~20wt%碳酸钠溶液经过静态混合器1混合后,除去大部分钙镁离子,降低废水总硬度后进入液固分离器2离心分离液固相,液相流入第一沉降槽3后加入0.4~0.5m3/h聚合氯化铝混凝剂和0.5~0.6m3/h聚丙烯酰胺絮凝剂进行混凝、絮凝沉降废水中剩余的钙镁离子和悬浮物。来自碱液罐5浓度为15~20%wt碱液利用碱液泵6送入沉降槽3中调节废水的ph值至10~11左右,废水中的氨得到最大程度解析并产生富氨气从沉降槽3顶部溢出后进入洗氨塔7进行洗涤处理,洗涤水为处理合格后的废水,洗涤后的含氨废水再返回沉降槽3进行循环利用。来自液固分离器2和沉降槽3底部的污泥经过污泥泵14送入污泥处理装置或真空抽滤机。经过除硬达标后的废水进入汽提装置进行脱氨和余热回收,除硬脱氨后废水抽出约1~3%wt进入稀盐酸储罐1或2,与来自界区外浓盐酸进行混合配置成1~2%wt稀盐酸溶液,然后利用稀盐酸泵输送至达标的灰水管线中。利用处理达标的灰水进行喷淋吸收稀盐酸罐1或2中挥发出的酸雾生成盐酸溶液自流至稀盐酸罐1或2中,因此灰水可以循环利用,避免外界需引新鲜水管线。配置合格后的稀盐酸利用稀盐酸泵44送入达标后的灰水管线中进行反调满足下游生化处理装置所要求的ph值(6~9)。投加稀盐酸具体量需利用灰水管线在线分析ph仪进行自动调节控制,避免投加稀盐酸量过多造成灰水反调后ph值发生较大波动。将本申请与同规模的常规处理装置进行比较,如表1所示。表1废水预处理工艺常规预处理工艺本发明预处理工艺氢氧化钠消耗kg/h115708000碳酸钠消耗kg/h01400化学品消耗成本万元/a46283500新鲜水消耗kg/h130000下游装置操作负荷增加2.2%~0从上表可以看出:若采用常规预处理工艺反调处理合格后灰水ph值,消耗的新鲜水较多,达到13000kg/h。而本发明所采用的预处理工艺无需消耗新鲜水,降低了公用工程消耗,提高了装置的经济性,同时未对下游全厂生化处理装置增加负荷和投资。若采用常规氢氧化钠溶液沉淀和调节ph值,消耗碱液较多,达到11570kg/h,每年氢氧化钠溶液消耗成本为4628万元。而本发明所采用的预处理工艺,降低了氢氧化钠溶液消耗,新增较少碳酸钠溶液,此两种碱液消耗的总成本较低,为3500万元,较常规配碱沉淀工艺节省近1100万元/年。此外采用碳酸钠溶液沉淀钙镁离子,提高了钙镁离子的去除率,而且生产的沉淀物都具有难溶特性,降低了液固分离的停留时间,避免带入下游汽提系统造成结垢,影响装置的长周期稳定运行。因此本发明降低了化学品消耗成本,提高了装置的经济效益,延长了装置的操作周期。当前第1页12