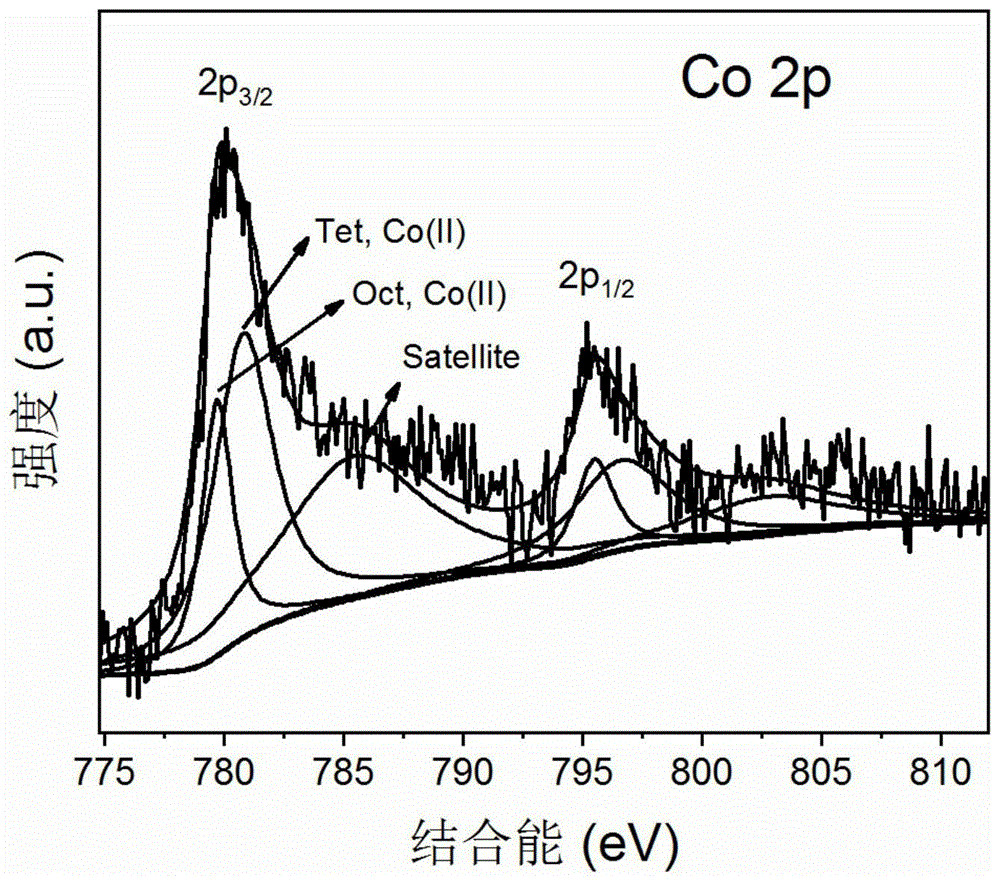
本发明属于废水处理
技术领域:
,特别涉及一种有机废水即时在线处理方法。
背景技术:
:随着社会的快速发展,大量的工业、农业和生活废弃物排入江河中,使水受到严重污染,不仅会影响饮用水源,而且会造成水生生物的灭绝,破坏生态平衡。有机废水是水域的重要污染源,具有量大、面积广、成分复杂、毒性大、不易净化、难处理等特点。有机废水进入环境会对生物造成深远的影响。目前,对有机废水的处理
技术领域:
,在以钴离子作为均相催化剂活化过一硫酸氢盐的反应体系中,钴离子难以被分离并回收利用,这不仅对环境造成二次污染,并且经济成本较高;而纳米级金属氧化物等异相催化剂则容易发生团聚现象,严重影响催化剂的制备及应用。目前常见的高级氧化处理废水过程是将废水分批次置于含有催化剂的容器中反应一段时间后完成降解,而在线可即时处理废水的高级氧化工艺仍很少被研究。技术实现要素:本发明的目的在于克服上述现有技术的不足,提供了一种有机废水即时在线处理方法,在以cofe2o4、co3o4或fe2o3作为异相催化剂活化过一硫酸氢盐的反应体系中,硫酸根自由基和羟基自由基的生成速率快、且催化剂无团聚现象,处理效果好。本发明提供的有机废水即时在线处理方法,是在反应器内填充负载有催化剂的填料,使加入有过一硫酸氢盐的废水在流经反应器时,与所述催化剂接触并发生反应,生成的强氧化性的硫酸根自由基和羟基自由基与有机废水中的有机污染物即时反应,从而使有机污染物在线被降解。作为上述方法优选的方案,废水通过蠕动泵流入反应器,其流量为2~20ml/min。作为上述方法优选的方案,所述催化剂选用无定型结构的cofe2o4、co3o4或fe2o3,优选无定型结构的cofe2o4。作为上述方法优选的方案,所述过一硫酸氢盐包括过一硫酸氢钾、过一硫酸氢钠中的一种或一种以上;所述过一硫酸氢盐在有机废水中的投加量依据有机污染物的质量浓度为10-1000mg/l。作为上述方法优选的方案,向有机废水中加入过一硫酸氢盐后,调节有机废水溶液的ph值为3.0~9.0。作为上述方法优选的方案,所述填料上催化剂的负载量为填料的1%-5%。作为上述方法优选的方案,所述在填料上负载无定型结构cofe2o4的制备过程为:s1取直径为0.5~1.5mm的填料,超声波清洗并干燥后过筛;s2将过筛后的填料置于容器中,并加入去离子水;s3按配比分别取co(no3)2·6h2o和fe(no3)3·9h2o,溶解在上述去离子水中,然后将尿素加入到容器中溶解,然后陈化一段时间;s4将装有上述混合液的容器置于烘箱中,水被烘干后将容器中的初步产物置于马弗炉中,高温烧结一段时间后,得到负载了cofe2o4的填料。上述无定型结构的cofe2o4的制备过程之步骤s3中,co(no3)2·6h2o和fe(no3)3·9h2o的配比为3:7-7:3范围之间,尿素的加入量为co(no3)2·6h2o和fe(no3)3·9h2o总量的40%-60%。上述无定型结构的cofe2o4的制备过程之步骤s3中,将co(no3)2·6h2o和fe(no3)3·9h2o加入到容器中溶解后,将容器置于100-120r/min的振荡器中振荡30-60min;将尿素加入到容器中溶解后,再将容器置于100-120r/min的振荡器中振荡60-90min后,陈化30-60min。上述无定型结构的cofe2o4的制备过程之步骤s4中,将容器中的初步产物置于马弗炉中,以10-15℃/min的速度升温到300-700℃,并维持3-5小时。本发明具有以下技术效果:(1)本发明在反应器内填充负载cofe2o4、co3o4或fe2o3的填料作为非均相催化剂,能够有效地活化过一硫酸氢盐,产生硫酸根自由基和羟基自由基,可以持续在线处理有机废水,对难降解的污染物的去除效果好。(2)本发明催化剂中的cofe2o4是无定型结构,与cofe2o4晶体结构相比,无定型结构活化过一硫酸氢盐产生硫酸根自由基和羟基自由基的速率快,有机废水的处理效果更好。(3)本发明将cofe2o4、co3o4或fe2o3负载到填料上,有效解决了cofe2o4、co3o4或fe2o3颗粒的团聚现象,提高了cofe2o4的制备效率和应用效果。(4)本发明中所使用的cofe2o4用量较少,并且其成分中fe和co之间的相互作用较强,不仅提高了降解效果,而且有效抑制了金属离子的浸出,环境友好,二次污染大大降低。(5)本发明制备方法简单,使用的设备成本低,对外界环境条件无特殊要求,不需要消耗额外能量,操作简单,重复性强,持久性好,易于实现。(6)本发明的有机废水处理方法能在较宽的ph范围内有效降解有机废水,大大降低了酸碱调节费用,节约了废水处理时的使用成本,具有很大应用前景。附图说明图1为本发明方法使用流程图;图2为本发明柱形反应器示意图(反应器内装有负载了催化剂的填料);图3为本发明实施例1.1之在300℃高温烧结后石英砂的sem图(3万倍);图4为本发明实施例1.1之在300℃高温烧结后制备的催化剂的sem图(3万倍);图5为本发明实施例1.1之在300℃高温烧结后石英砂的xrd图;图6为本发明实施例1.1之在300℃高温烧结后制备的催化剂的xrd图;图7有机废水处理前反应器内填料负载的催化剂之钴元素的xps图;图8有机废水处理前反应器内填料负载的催化剂之铁元素的xps图;图9有机废水处理前反应器内填料负载的催化剂之钴元素的eds图;图10有机废水处理前反应器内填料负载的催化剂之铁元素的eds图;图11有机废水处理前反应器内填料负载的催化剂之氧元素的eds图;为了更清楚地说明本发明实施例中的技术方案,下面将对实施例中所需要使用的附图作简单地介绍,显而易见地,下面描述中的附图仅仅是本发明的一些实施例,对于本领域普通技术人员来讲,在不付出创造性劳动的前提下,还可以根据这些附图获得其他的附图。具体实施方式为了使本发明的目的、技术方案及优点更加清楚明白,以下结合附图及实施例,对本发明进行进一步详细说明。应当理解,此处所描述的具体实施例仅仅用以解释本发明,并不用于限定本发明。参见图1,本发明提供了一种有机废水即时在线处理方法,是在反应器内填充负载有催化剂的填料,并在有机废水中加入过一硫酸氢盐,然后将混合后的有机废水流动进入反应器,使有机废水中的过一硫酸氢盐与反应器内填料上的催化剂接触并即时发生反应,生成强氧化性的硫酸根自由基和羟基自由基,以分解废水中的有机污染物,从而使有机污染物在线被降解。本发明上述处理方法将催化剂负载到填料上,在以cofe2o4、co3o4或fe2o3作为异相催化剂活化过一硫酸氢盐的反应体系中,活化过一硫酸氢盐产生硫酸根自由基和羟基自由基的反应时间短、速率快,且催化剂无团聚现象,可以持续在线处理有机废水,提高了催化剂的催化效率和应用效果。进一步地,本发明提供的上述处理方法中,反应器可选用图2所示的柱形反应器或反应槽,只要能够将负载有催化剂的填料装入其内且能够使有机废水在一定的时间内流出并完成反应的容器皆可。待处理的有机废水可通过蠕动泵流动进入反应器内,其流量参数选为2~20ml/min。通过蠕动泵以该流量速度流入反应器的有机废水,可保证有机废水中的污染物、过一硫酸氢盐和填料上负载的催化剂充分接触并即时发生反应,使废水中污染物去除率达到80%以上。进一步地,本发明提供的上述处理方法中,所述催化剂为无定型结构的cofe2o4、co3o4或fe2o3,优选无定型结构的cofe2o4。其中无定型结构的cofe2o4与常态的晶体结构的cofe2o4相比,无定型结构的cofe2o4活化过一硫酸氢盐产生硫酸根自由基和羟基自由基的能力更强,有机废水的处理效果更好。而且,将cofe2o4、co3o4或fe2o3负载到填料上,有效解决了cofe2o4、co3o4或fe2o3颗粒的团聚现象,提高了cofe2o4的制备效率,同时也提高了有机废水的净化效果。进一步地,本发明提供的上述处理方法中,所述过一硫酸氢盐包括过一硫酸氢钾、过一硫酸氢钠中的一种或一种以上。本发明在有机废水中加入上述过一硫酸氢盐,并通过催化剂产生硫酸自由基,进而产生羟基自由基,可分解废水中的有机污染物。进一步地,本发明提供的上述处理方法中,所述过一硫酸氢盐在有机废水中的加入量依据有机污染物的浓度而定,一般加入的质量浓度为10-1000mg/l。当有机废水的浓度为20mg/l时,所述过一硫酸氢盐在有机废水中的加入量优选为50-150mg/l。上述质量浓度参数范围能够保证较好的去除效果,过多的投入会导致使用成本的增加,且降解的效果增加不大,投入过少则达不到使用要求。进一步地,本发明提供的上述处理方法中,向有机废水中加入过一硫酸氢盐后,可用0.1mmol/l的naoh或hcl调节有机废水溶液的ph值为3.0~9.0。这样,无论有机废水是呈酸性、中性还是弱碱性,均能对废水具有非常好的降解效果,从而大大节省了酸碱调节的费用,缩短了废水处理过程,降低了使用成本,有利于本发明方法的推广和实际应用。进一步地,本发明提供的上述处理方法中,所述填料可选择石英砂或沸石,只要能稳定负载催化剂,并能填充反应器的材料皆可。所述催化剂的负载量可为填料的1%-5%。负载量过多会带来材料成本的提高,过少会导致处理效果的降低,达不到使用要求。本发明还提供了无定型结构的cofe2o4的制备方法,其步骤为:s1取直径为0.5~1.5mm的填料,超声波清洗并干燥后过筛。该步骤中,采用超声波清洗10-30分钟,可有效清除填料表面的杂质,有利于填料在其表面的负载。过筛后,可筛去细小的砂砾。s2将过筛后的填料置于容器中,并加入去离子水。s3按配比分别取co(no3)2·6h2o和fe(no3)3·9h2o,溶解在上述去离子水中,然后将尿素加入到容器中溶解,然后陈化一段时间。该步骤中,co(no3)2·6h2o和fe(no3)3·9h2o的配比为3:7-7:3范围之间,此配比符合尖晶石(ab2o4)中两种金属元素的比例范围;尿素的加入量为co(no3)2·6h2o和fe(no3)3·9h2o总量的40%-60%,以保证尿素和金属元素的配位数在3左右。将co(no3)2·6h2o和fe(no3)3·9h2o加入到容器中溶解后,将容器置于100-120r/min的振荡器中振荡30-60min,以保证硝酸盐均匀的溶解到溶液中;将尿素加入到容器中溶解后,再将容器置于100-120r/min的振荡器中振荡60-90min后,以保证尿素和金属离子配位反应完全;陈化30-60min,以稳定尿素和金属离子形成的配合物。s4将装有上述混合液的容器置于90℃烘箱中,水被烘干后将容器中的初步产物均匀分散至蒸发皿内,置于马弗炉中,高温烧结一段时间后,得到负载了cofe2o4的填料。该步骤中,容器中的初步产物置于马弗炉中后,以10-15℃/min的速度升温到300-700℃,并维持3-5小时,使催化剂稳定负载于填料上。最后,将负载了催化剂的填料清洗后作为填充材料,填充于反应器内,并可在填充物的顶端放置一层无菌棉。需要说明的是,负载co3o4或fe2o3的制备过程与负载cofe2o4的过程基本一致,只是以各对应的一种金属硝酸盐作为原料。下面结合多组对比的实施例对本发明做进一步详述。需要说明的是,下述实施例为优选的实施例,填料选用石英砂,催化剂选用cofe2o4。下述实施例以磺胺氯哒嗪钠(scp)为典型的有机废水,为了证明本发明对目标污染物的无选择性,也选择了罗丹明b作为目标为污染物。实施例组1:本组实施例为不同烧结温度条件下制备的负载了cofe2o4的石英砂分别填充柱形反应器时,对活化过一硫酸氢钾降解scp的去除率的影响。实施例1.1:1、负载了cofe2o4的石英砂的制备。s1取10g直径为0.9~1.0mm的石英砂,超声波清洗10分钟后干燥过筛,除去细小的砂砾;s2将余下的石英砂转移到150ml容器中并加入100-300ml去离子水。s3取0.145gco(no3)2·6h2o和0.404gfe(no3)3·9h2o溶解在上述载有石英砂的去离子水中,将容器置于120r/min的振荡器中振荡30min。然后取0.270g尿素加入到容器中溶解,再次将容器置于120r/min的振荡器中振荡60min后,陈化30min。s4将容器置于90℃烘箱中,当去离子水被烘干时,将容器中的初步产物均匀地分散到蒸发皿中,然后将其置于马弗炉中,以10℃/min的速度升温到300℃,并维持4小时,得到负载了cofe2o4的石英砂(见图4)。由图4可以看到,经过为300℃灼烧后,石英砂表面均匀覆盖了一层颗粒物。经过xrd分析,负载后催化剂的xrd图(图6)和负载前的石英砂xrd图(图5)相比,没有新的衍射峰出现,经过xps分析(图7和图8),co的化合价为2价,fe的化合价为3价,并且结合eds分析(图9-11),co、fe、o元素在催化剂的表面均匀分布,从而确认负载物为无定型的cofe2o4。2、有机废水scp处理。将制备的负载了cofe2o4的石英砂清洗后作为填充材料,填充于柱形反应器内,填充量为10g,并在石英砂填充物的顶端放置一层无菌棉。然后在容器中现用现配20mg/l的scp溶液200ml,同时加入过一硫酸氢钾使其浓度为75mg/l,并调节溶液的ph值为6.8,在室温下将该溶液通过蠕动泵以6ml/min的流速流经柱形反应器,完成第一组200mlscp的降解,并记录scp的去除率。然后再连续重复上述过程4次,分别记为第二、三、四、五组scp的降解,使得被处理的scp废水的总体积为1l。本实施例scp去除率结果见表1。实施例1.2:1、负载了cofe2o4的石英砂的制备。本实施例s1、s2、s3步骤同实施例1.1,所不同的是下述步骤s4。s4将容器置于90℃烘箱中,当去离子水被烘干时,将容器中的初步产物均匀地分散到蒸发皿中,然后将其置于马弗炉中,以10℃/min的速度升温到400℃,并维持4小时,得到负载了cofe2o4的石英砂。2、有机废水scp的处理。处理过程同实施例1.1。本实施例scp去除率结果见表1。实施例1.3:1、负载了cofe2o4的石英砂的制备。本实施例s1、s2、s3步骤同实施例1.1,所不同的是下述步骤s4。s4将容器置于90℃烘箱中,当去离子水被烘干时,将容器中的初步产物均匀地分散到蒸发皿中,然后将其置于马弗炉中,以10℃/min的速度升温到500℃,并维持4小时,得到负载了cofe2o4的石英砂。2、有机废水scp的处理。处理过程同实施例1.1。本实施例scp去除率结果见表1。实施例1.4:1、负载了cofe2o4的石英砂的制备。本实施例s1、s2、s3步骤同实施例1.1,所不同的是下述步骤s4。s4将容器置于90℃烘箱中,当去离子水被烘干时,将容器中的初步产物均匀地分散到蒸发皿中,然后将其置于马弗炉中,以10℃/min的速度升温到600℃,并维持4小时,得到负载了cofe2o4的石英砂。2、有机废水scp的处理。处理过程同实施例1.1。本实施例scp去除率结果见表1。实施例1.5:1、负载了cofe2o4的石英砂的制备。本实施例s1、s2、s3步骤同实施例1.1,所不同的是下述步骤s4。s4将容器置于90℃烘箱中,当去离子水被烘干时,将容器中的初步产物均匀地分散到蒸发皿中,然后将其置于马弗炉中,以10℃/min的速度升温到700℃,并维持4小时,得到负载了cofe2o4的石英砂。2、有机废水scp的处理。处理过程同实施例1.1。本实施例scp去除率结果见表1。表1不同温度条件下制备的填充材料对scp去除率的影响上述结果表明,填充材料的制备温度对scp去除率的影响较大,在300-700℃的范围内,填充材料的制备温度越高,scp的去除率越低。温度在300℃时制备的填充材料对scp的处理效果最好。实施例2:本组实施例用于比较采用柱形反应器活化过一硫酸氢钾、单独使用柱形反应器和单独应用过一硫酸氢钾三种方式下scp的去除率。实施例2.1:1、负载了cofe2o4的石英砂的制备。本实施例负载了cofe2o4的石英砂的制备与实施例1.1相同。2、有机废水scp的处理。在柱形反应器内填充制备的负载有cofe2o4的石英砂10g,制备时的烧结温度为300℃。在容器中现用现配20mg/l的scp溶液200ml,同时加入过一硫酸氢钾使其浓度为75mg/l,并调节溶液的ph值为6.8,在室温下将该溶液通过蠕动泵以6ml/min的流速流经柱形反应器,完成第一组200mlscp的降解,并记录scp的去除率。然后再连续重复上述过程4次,分别记为第二、三、四、五组scp的降解,使得被处理的scp废水的总体积为1l。特别地,第一组scp废水被处理时,需在线监测scp的去除率并记录。在线监测scp去除率的结果见表2,最终scp去除率结果见表3。表2在线监测scp去除率从表2可以看到,柱形反应器的在线处理能力较强,在scp有机废水流经柱形反应器时,就已经完成了降解过程。实施例2.21、负载了cofe2o4的石英砂的制备。本实施例负载了cofe2o4的石英砂的制备与实施例1.1相同。2、有机废水scp的处理。在容器中现用现配20mg/l的scp溶液200ml,调节溶液的ph值为6.8,在室温下将该溶液通过蠕动泵以6ml/min的流速流经柱形反应器,然后记录scp的去除率。重复上述过程4次,分别记为第二、三、四、五组scp的降解,使得被处理的scp废水的总体积为1l。该实施例中scp溶液没有加入过一硫酸氢钾,其他条件同实施例2.1。本实施例scp去除率结果见表3。表3柱形反应器活化过一硫酸氢钾的反应体系和单独使用柱形反应器的反应体系对scp的去除率对比实验去除率(%)第一组第二组第三组第四组第五组实施例2.194.593.090.288.187.2实施例2.24.42.41.31.01.0从表3可以看到,实施例2.1利用柱形反应器活化过一硫酸氢钾体系对scp的处理效果非常明显,scp的去除率达到85%以上;而实施例2.2单独使用柱形反应器未能对scp进行有效降解去除。实施例2.3在容器中现用现配20mg/l的scp溶液200ml,同时加入过一硫酸氢钾使其浓度为75mg/l,并调节溶液的ph值为6.8。每30min记录一次scp的去除率。本实施例scp去除率结果见表4。表4单独使用过一硫酸氢钾的反应体系对scp的去除率时间(min)30min60min90min120min150min去除率(%)8.717.724.529.431.2表4结果表明,单独使用过一硫酸氢钾未能对scp进行有效降解去除。实施例3:本组实施例用于比较柱形反应器活化过一硫酸氢钾反应体系中,不同的过一硫酸氢钾投加量对scp降解的影响。实施例3.1:1、负载了cofe2o4的石英砂的制备。本实施例负载了cofe2o4的石英砂的制备与实施例1.1相同。2、有机废水scp的处理。将制备的负载了cofe2o4的石英砂清洗后作为填充材料,填充于柱形反应器内,填充量为10g,并在石英砂填充物的顶端放置一层无菌棉。然后在容器中现用现配20mg/l的scp溶液200ml,同时加入过一硫酸氢钾使其浓度为10mg/l,并调节溶液的ph值为6.8,在室温下将该溶液通过蠕动泵以6ml/min的流速流经柱形反应器,完成第一组200mlscp的降解,并记录scp的去除率。然后再连续重复上述过程4次,分别记为第二、三、四、五组scp的降解,使得被处理的scp废水的总体积为1l。本实施例scp去除率结果见表5。实施例3.2:本实施例与实施例3.1基本相同,不同的是加入容器中的过一硫酸氢钾的投加量浓度是25mg/l。本实施例scp去除率结果见表5。实施例3.3:本实施例与实施例3.1基本相同,不同的是加入容器中的过一硫酸氢钾的投加量浓度是50mg/l。本实施例scp去除率结果见表5。实施例3.4:本实施例与实施例3.1基本相同,不同的是加入容器中的过一硫酸氢钾的投加量浓度是75mg/l。本实施例scp去除率结果见表5。实施例3.5:本实施例与实施例3.1基本相同,不同的是加入容器中的过一硫酸氢钾的投加量浓度是100mg/l。本实施例scp去除率结果见表5。表5不同的过一硫酸氢钾投加量浓度对scp去除率的影响由表5可以看到,当scp的浓度为20mg/l时,随着过一硫酸氢钾的投加量增加,scp的去除率呈现上升趋势;但当过一硫酸氢钾的投加量达到75mg/l以后,继续增加过一硫酸氢钾的投加量对scp的去除率影响不大,从降解效果和成本方面考虑,当scp的浓度是20mg/l时,过一硫酸氢钾的浓度选为75mg/l较为合适。实施例4:本组实施例用于比较scp废水进入柱形反应器时,不同流速对其去除率的影响。实施例4.1:1、负载了cofe2o4的石英砂的制备。本实施例负载了cofe2o4的石英砂的制备与实施例1.1相同。2、有机废水scp的处理。将制备的负载了cofe2o4的石英砂清洗后作为填充材料,填充于柱形反应器内,填充量为10g,并在石英砂填充物的顶端放置一层无菌棉。然后配制20mg/l的scp溶液200ml,同时加入过一硫酸氢钾使其浓度为75mg/l,并调节溶液的ph值为6.8,在室温下将该溶液通过蠕动泵以6ml/min的流速流经柱形反应器,完成第一组200mlscp的降解,并记录scp的去除率。然后再连续重复上述过程4次,分别记为第二、三、四、五组scp的降解,使得被处理的scp废水的总体积为1l。本实施例scp去除率结果见表6。实施例4.2:本实施例与实施例4.1基本相同,不同的是将蠕动泵的流速调整为10ml/min。本实施例scp去除率结果见表6。实施例4.3:本实施例与实施例4.1基本相同,不同的是将蠕动泵的流速调整为16ml/min。本实施例scp去除率结果见表6。表6scp溶液进入柱形反应器的不同流速对其去除率的影响去除率(%)第一组第二组第三组第四组第五组实施例4.194.593.090.288.187.2实施例4.291.388.384.682.581.1实施例4.386.581.377.875.373.5实验结果表明,随着scp溶液进入柱形反应器的流速增加,scp的去除率逐渐降低。当流速为10ml/min时,1l的scp废水在100分钟内即可处理完全,并且scp的去除率仍在80%以上;然而当scp溶液进入柱形反应器的流速为16ml/min时,scp的去除率将会低于80%。实施例组5:本组实施例用于柱形反应器活化过一硫酸氢钾反应体系中,ph值条件对scp去除率的影响。实施例5.1:1、负载了cofe2o4的石英砂的制备。本实施例负载了cofe2o4的石英砂的制备与实施例1.1相同。2、有机废水scp的处理。将制备的负载了cofe2o4的石英砂清洗后作为填充材料,填充于柱形反应器内,填充量为10g,并在石英砂填充物的顶端放置一层无菌棉。在容器中配制20mg/l的scp溶液200ml,同时加入过一硫酸氢钾使其浓度为75mg/l,并调节溶液的ph值为10.0,在室温下将该溶液通过蠕动泵以6ml/min的流速流经柱形反应器,完成第一组200mlscp的降解,并记录scp的去除率。然后再连续重复上述过程4次,分别记为第二、三、四、五组scp的降解,使得被处理的scp废水的总体积为1l。本实施例scp去除率结果见表7。实施例5.2:本实施例与实施例5.1基本相同,不同的是,在投加过一硫酸氢钾后将溶液的ph值调为9.0。本实施例scp去除率结果见表7。实施例5.3:本实施例与实施例5.1基本相同,不同的是,在投加过一硫酸氢钾后将溶液的ph值调为6.8。本实施例scp去除率结果见表7。实施例5.4:本实施例与实施例5.1基本相同,不同的是,在投加过一硫酸氢钾后将溶液的ph值调为5.0。本实施例scp去除率结果见表7。实施例5.5:本实施例与实施例5.1基本相同,不同的是,在投加过一硫酸氢钾后,没有调节溶液的ph,溶液初始的ph值为4.2。本实施例scp去除率结果见表7。表7:各ph条件下反应体系对scp去除率去除率(%)第一组第二组第三组第四组第五组实施例5.156.751.751.053.152.3实施例5.295.093.991.390.488.5实施例5.394.593.090.288.187.2实施例5.493.189.286.585.383.8实施例5.590.987.183.881.880.2实验结果表明,柱形反应器活化过一硫酸氢钾的方法在酸性、中性、弱碱性条件下均能对scp具有非常好的降解效果,这有利于在实际应用中节省酸碱调节的费用。在不同的ph条件下,以中性和弱碱性的处理效果最佳。然而当scp废水溶液的ph值大于等于10.0时,柱形反应器活化过一硫酸氢钾降解scp的效率将大大降低,去除率低于60%。实施例组6:本实施例为柱形反应器在线持续降解scp及催化剂再生的实验。实施例6.1:本实施例利用柱形反应器活化过一硫酸氢钾的反应体系中,柱形反应器由10g负载了cofe2o4的石英砂填充制得。配制20mg/l的scp溶液200ml,同时加入过一硫酸氢钾使其浓度为75mg/l,并调节溶液的ph值为6.8,在室温下将该溶液通过蠕动泵以6ml/min的流速流经柱形反应器,完成第一组200mlscp的降解,并记录scp的去除率。然后再连续重复上述过程15次,使被处理的scp废水的总体积为3.2l。柱形反应器持续降解scp实验的结果如表8所示。表8柱形反应器持续降解scp废水时,scp的去除率组数12345678去除率(%)95.293.089.688.286.387.480.581.3组数910111213141516去除率(%)80.080.880.179.576.776.877.076.3实施例6.2:将实施例6.1中使用过的负载cofe2o4的石英砂回收,将其置于马弗炉中,以10℃/min的速度升温到300℃,维持4小时以完成催化剂的再生,并取10g填充柱形反应器,测试再生催化剂的活性。然后在容器中现用现配20mg/l的scp溶液200ml,同时加入过一硫酸氢钾使其浓度为10mg/l,并调节溶液的ph值为6.8,在室温下将该溶液通过蠕动泵以6ml/min的流速流经填充了再生催化剂的柱形反应器,完成第一组200mlscp的降解,并记录scp的去除率。然后再连续重复上述过程4次,分别记为第二、三、四、五组scp的降解,使得被处理的scp废水的总体积为1l。本实施例对scp的降解结果如表9所示。表9填充了再生催化剂的柱形反应器持续降解scp实验的结果去除率(%)第一组第二组第三组第四组第五组实施例6.293.287.984.782.581.7本实施例实验在9.5小时内,柱形反应器持续降解scp废水3.2l,总的scp去除率达83%。随着持续降解过程的进行,柱形反应器对scp的去除率有所降低,但在处理完3.0l废水后,继续在线降解scp的去除率仍能高于75%。这表明柱形反应器的稳定性良好,有利于循环使用。同时,负载cofe2o4的石英砂作为催化剂,在持续使用9.5小时后,可以通过简单的灼烧过程实现催化剂的再生,并且再生催化剂的活性与新制得的催化剂活性相差不大。实施例组7:本组实施例为负载cofe2o4的石英砂、负载co3o4的石英砂和负载fe2o3的石英砂分别填充柱形反应器,对活化过一硫酸氢钾降解scp的去除率的影响。实施例7.1:1、负载了cofe2o4的石英砂的制备。本实施例负载了cofe2o4的石英砂的制备与实施例1.1相同。2、有机废水scp的处理。首先配制20mg/l的scp溶液200ml,同时加入过一硫酸氢钾使其浓度为75mg/l,并调节溶液的ph值为6.8,在室温下将该溶液通过蠕动泵以6ml/min的流速流经柱形反应器,完成第一组200mlscp的降解,并记录scp的去除率。然后再连续重复上述过程4次,分别记为第二、三、四、五组scp的降解,使得被处理的scp废水的总体积为1l。本实施例scp去除率结果见表10。实施例7.2:本实施例反应体系与实施例7.1基本相同,不同的是柱形反应器的填充材料改为负载了co3o4的石英砂,其中co3o4负载量的金属摩尔数和cofe2o4负载量的总金属摩尔数相同,其他条件同反应体系实施例7.1。本实施例scp去除率结果见表10。实施例7.3本实施例反应体系与实施例7.1基本相同,不同的是柱形反应器的填充材料改为负载了fe2o3的石英砂,其中fe2o3负载量的金属摩尔数和cofe2o4负载量的总金属摩尔数相同,其他条件同反应体系实施例7.1。本实施例scp去除率结果见表10。表10不同负载材料对活化过一硫酸氢钾降解scp的去除率的影响去除率(%)第一组第二组第三组第四组第五组实施例7.194.593.090.288.187.2实施例7.284.684.680.579.376.2实施例7.370.564.564.663.161.5由表10可知:三种填充材料中负载cofe2o4的石英砂对scp的降解效果最好,其次是负载co3o4的石英砂。这表明了cofe2o4的fe和co之间具有强的相互作用,可以促进对过一硫酸氢钾的活化,使得scp的去除率明显增高。实施例8:本实施例为柱形反应器在线持续降解罗丹明b(rhb)的实验。本实施例利用柱形反应器活化过一硫酸氢钾的反应体系中,柱形反应器由10g负载了cofe2o4的石英砂填充制得。配制10mg/l的rhb溶液200ml,同时加入过一硫酸氢钾使其浓度为120mg/l,并调节溶液的ph值为6.8,在室温下将该溶液通过蠕动泵以6ml/min的流速流经柱形反应器,完成第一组200mlscp的降解,并记录scp的去除率。然后再连续重复上述过程4次,分别记为第二、三、四、五组rhb的降解,使得被处理的rhb废水的总体积为1l。本实施例rhb去除率结果见表11。表11柱形反应器活化过一硫酸氢钾降解废水中的rhb去除率(%)第一组第二组第三组第四组第五组实施例895.896.595.294.695.1由表11可以看出,柱形反应器活化过一硫酸氢钾的降解rhb的效果在95%以上。这表明该降解体系对有机物是非选择性的,适用范围广,对抗生素、染料等多种有机物废水均有良好的去除效果。本发明的上述实施例所示仅为本发明较佳实施例之部分,并不能以此局限本发明,在不脱离本发明精髓的条件下,本领域技术人员所作的任何修改、等同替换和改进等,都属本发明的保护范围。当前第1页12