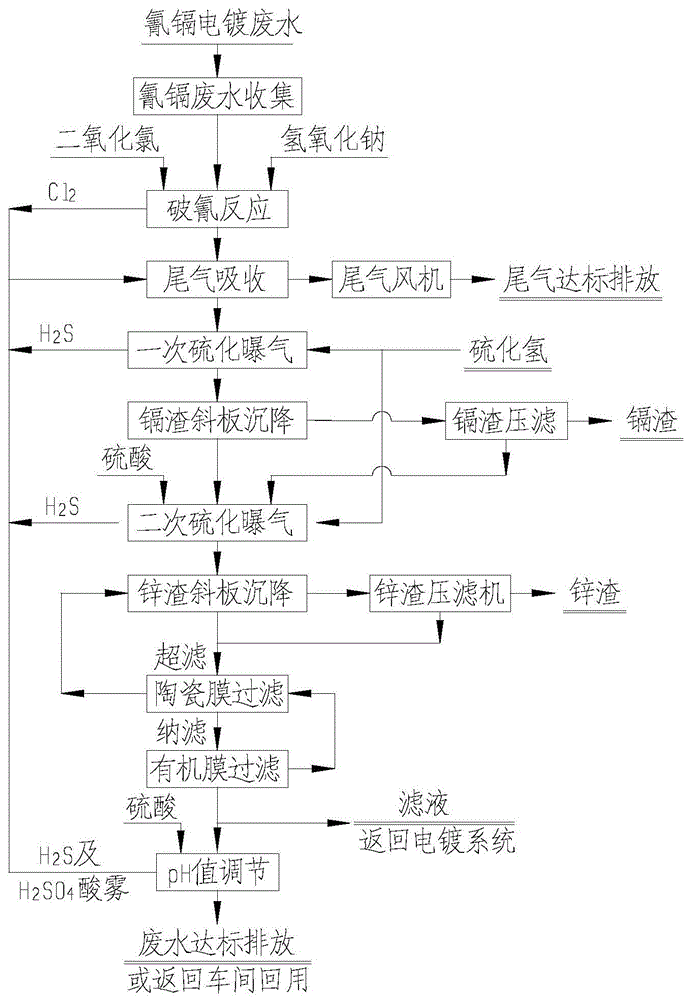
本发明涉及电镀废水处理
技术领域:
,具体是一种氰化镀镉电镀废水处理工艺及其系统。
背景技术:
:镉是高危害有毒物质和可致癌物质,被镉污染的水体、空气、土壤和食物对人体危害严重,日本曾因镉中毒出现“痛痛病”。在我国,镉被列为一类污染物,根据《gb21900-2008电镀污染物排放标准》,电镀废水总镉最高允许排放浓度为0.05mg/l。在电镀行业中,镀镉层通常用于弹性件、螺纹件、标准件以及航空航天、造船、电子及军工产品等。有氰电镀在普通电镀行业已被无氰电镀工艺所替代,但在航空航天系统等领域还没有可以替代的工艺技术。含cd废水处理的常见方法主要有化学沉淀法、电解法、离子树脂交换法、膜分离法等。工业上一般先采用化学沉淀法脱除废水中的大部分镉离子,再采用离子交换、膜处理等方法进行深度处理。化学沉淀法又分为碳酸镉沉淀法、氢氧化物沉淀法、磷酸镉沉淀法、硫化镉沉淀法、漂白粉沉淀法、铁氧体共沉淀法等。最常用的含镉废水化学沉淀法为氢氧化物沉淀法,镉离子充分沉淀的ph值为11~12,存在反应ph值高、引入过多na离子、出水含盐量大、废水回用难、沉淀产物难处理、应用范围有限、其他重金属容易返溶等问题。氰化镀镉电镀废水采用上述常规技术处理很难满足日趋严格的环保要求。技术实现要素:本发明所要解决的技术问题是提供一种处理效果好、提高废水回用率的氰化镀镉电镀废水处理工艺及其系统。本发明以如下技术方案解决上述技术问题:本发明一种氰化镀镉电镀废水处理工艺,包括如下操作步骤:a、氰化镀镉电镀废水收集:将氰化电镀车间的电镀废水汇集到氰镉废水调节池,并稳定废水水质;b、废水氧化破氰:将电镀废水的ph值调节至10.0~11.0,按质量比为clo2∶cn-=2.70~3.00∶1的比例将二氧化氯投加到电镀废水中,反应45~60min;c、废水初级硫化及尾气吸收:将破氰后的废水送入尾气吸收塔进行喷淋,控制尾气吸收塔的尾气流速1.8~2.2m/s,喷淋密度45~55m3/(m2.h),废水与尾气逆流接触进行初级硫化,废水中的锌、镉离子与尾气中的h2s发生硫化反应,脱除部分锌、镉离子,尾气中的酸性气体被吸收脱除后达标排放;d、废水一次硫化曝气:将初级硫化后的废水送入一次硫化曝气罐,将硫化氢气体与压缩空气混合后通过曝气管送入一次硫化曝气罐底部并分布成细小、均匀的气泡,废水中的锌、镉离子与曝气进入一次硫化曝气罐的h2s发生硫化反应,脱除锌、镉离子;e、镉渣沉淀、过滤:将一次硫化曝气后的废水输送到镉渣斜板沉降槽进行沉淀处理,沉淀底流送镉渣压滤机压滤,压滤产出的镉渣外运利用;f、废水二次硫化曝气:将镉渣斜板沉降槽的表面清液及镉渣压滤机压滤产出的滤液输送到二次硫化曝气罐,将硫化氢气体与压缩空气混合后通过曝气管送入二次硫化曝气罐底部并分布成细小、均匀的气泡,废水中的锌离子与曝气进入二次硫化曝气罐的h2s发生硫化反应,脱除锌离子;g、锌渣沉淀、过滤:将二次硫化曝气后的废水输送到锌渣斜板沉降槽进行沉淀处理,沉淀底流送锌渣压滤机压滤,压滤产出的锌渣外运利用;h、陶瓷膜超滤处理:将锌渣斜板沉降槽的表面清夜和锌渣压滤机压滤产出的滤液输送到陶瓷膜过滤器过滤,产生的浓水返回锌渣斜板沉降槽,清液送入有机膜过滤器;i、有机膜纳滤处理:将步骤h的清液再经有机膜过滤器过滤,产生的浓水返回陶瓷膜过滤器重新过滤,过滤后的部分清液送电镀系统回用,其余清液送入ph值调节池;j、ph值调节:在ph值调节池加酸,并进行搅拌反应,调节ph值稳定为7~9,cd2+稳定达到0.05mg/l以下、zn2+≤1.5mg/l、ss≤1.0mg/l后排放,或返回电镀车间回用。本发明所述步骤b中,控制破氰反应出水的余氯稳定在2~5mg/l。本发明所述步骤d中,一次硫化曝气过程中自动维持ph值为10.0~11.0,废水一次硫化反应时间为30~50分钟。本发明所述步骤f中,二次硫化曝气过程中滴加硫酸控制废水ph值为8.5~9.5,废水二次硫化反应停留时间为30~40分钟。本发明所述步骤b、d、f、j中,产生的尾气送入尾气吸收塔处理。本发明所述步骤d和f中,所用的硫化氢气体来自硫化氢发生器或罐装硫化氢气体,硫化氢发生器生产的气体为硫化氢和二氧化碳混合气体,其中,h2s体积含量80.0~85.0%,co2体积含量15.0~20.0%。本发明所述氰化镀镉电镀废水处理工艺采用的系统,包括由前至后依次相连接的氰镉废水调节池、破氰反应池、尾气吸收塔、一次硫化曝气罐、镉渣斜板沉淀槽、镉渣压滤机、二次硫化曝气罐、锌渣斜板沉淀槽、锌渣压滤机、陶瓷膜过滤器、有机膜过滤器和ph调节池,破氰反应池顶部设有尾气出口,下部设有破氰反应池搅拌口,破氰反应池顶部的尾气出口经管道与尾气吸收塔下部的尾气入口相连接,破氰反应池下部的破氰反应池搅拌口经管道与尾气吸收塔上部的喷淋装置及破氰搅拌泵相连接;尾气吸收塔、一次硫化曝气罐、二次硫化曝气罐和ph调节池的顶部均设有与排放管道相连接的排放口,排放管道上安装有尾气排放风机;破氰反应池设有二氧化氯和氢氧化钠的投加口;一次硫化曝气罐和二次硫化曝气罐的底部均安装有曝气管,曝气管连接硫化氢气体和压缩空气的混合气输入管。本发明所述破氰反应池的下部设有破氰搅拌泵,破氰反应池搅拌口排出的废水经破氰搅拌泵返回破氰反应池内实现搅拌作用。本发明所述一次硫化曝气罐和二次硫化曝气罐的高度与直径之比均为1.0~1.2:1;一次硫化曝气罐和二次硫化曝气罐内安装有ph计用于检测的废水ph值。本发明所述ph调节池内设有ph计和搅拌装置,所述搅拌装置包括搅拌杆、设在搅拌杆上的搅拌叶以及用以驱使搅拌杆转动的驱动电机。上述处理工艺及系统应用于含氰镀镉废水处理,具有如下有益效果:1.和常规次氯酸钠氧化工艺相比,本发明采用二氧化氯破氰、氢氧化物及硫化氢协同沉淀重金属,氰镉废水处理效果好,可减少破氰氧化剂、碱性沉淀剂的使用及ph回调的用酸量,降低回用废水中的na盐等含盐量,有利于废水回用、减少废水排放,可满足日趋严格的环保要求,降低电镀生产的用水成本。2.通过将氢氧化物法沉淀和硫化物沉淀的结合,电镀废水镉离子沉淀的ph值由11~12降低为10~11,减少废水处理碱液和后续ph反调的硫酸用量,降低了药品使用成本。3.有利于废水回用。和硫化钠硫化沉淀相比,采用硫化氢硫化沉淀不引入na离子;废水处理中只使用很少量的氢氧化钠微调ph值,沉淀镉离子的氢氧化钠用量减少。本发明减少了处理后废水na离子的富集,有利于废水回用、减少废水排放,可满足日趋严格的环保要求,也降低了电镀的用水成本。4.有机膜处理后的废水ph值为8.5~9.5,可直接回用于电镀生产,不仅提高水回用率,还可降低电镀生产naoh碱耗。附图说明图1是本发明氰化镀镉电镀废水处理工艺的流程示意图。图2是本发明实施例1采用的处理系统结构示意图。图3是本发明实施例2采用的处理系统结构示意图。图中:1-氰镉废水调节池,2-输送泵a,3-破氰反应池,31-破氰反应池搅拌口,4-破氰搅拌泵,5-尾气吸收塔,51-一级喷淋装置,52-二级喷淋装置,6-尾吸塔循环泵,7-一次硫化曝气罐,71-一次硫化曝气管,8-输送泵b,9-镉渣斜板沉降槽,10-镉渣压滤泵,11-镉渣压滤机,111-镉渣斗,12-除镉清液池,13-输送泵c;14-二次硫化曝气罐,141-二次硫化曝气管,15-输送泵d,16-锌渣斜板沉降槽,17-锌渣压滤泵,18-锌渣压滤机,181-锌渣斗,19-除锌清液池,20-陶瓷膜过滤高压泵,21-陶瓷膜过滤器,22-陶瓷过滤清液池,23-有机膜过滤高压泵,24-有机膜过滤器,25-有机膜过滤清液池,26-输送泵e,27-ph调节池,271-搅拌装置,28-输送泵f,29-尾气排放风机,30-硫化氢发生器。具体实施方式下面结合附图对本发明的技术方案做进一步的说明。如图1所示,本发明一种氰化镀镉电镀废水处理工艺,包括如下操作步骤:a、氰化镀镉电镀废水收集:将氰化电镀车间漂洗水等电镀废水汇集到氰镉废水调节池混合均匀,并稳定废水水质;b、废水氧化破氰:通过投加少量的氢氧化纳或硫酸将电镀废水的ph值调节至10.0~11.0,并按质量比为clo2∶cn-=2.70~3.00∶1的比例将二氧化氯投加到电镀废水中,搅拌反应45~60min;并控制破氰反应出水的余氯稳定在2~5mg/l;c、废水初级硫化及尾气吸收:将破氰后的废水送入尾气吸收塔进行喷淋,控制尾气吸收塔的尾气流速1.8~2.2m/s,喷淋密度45~55m3/(m2.h),废水与尾气逆流接触进行初级硫化,废水中的锌、镉离子与尾气中的h2s发生硫化反应,脱除部分锌、镉离子,尾气中的h2s及氯气等酸性气体被吸收脱除后达标排放,控制一级尾气吸收塔的尾气流速1.8~2.2m/s,喷淋密度45~55m3/(m2.h);d、废水一次硫化曝气:将初级硫化后的废水送入一次硫化曝气罐,将硫化氢气体与压缩空气混合后通过曝气管送入一次硫化曝气罐底部并分布成细小、均匀的气泡,废水中的锌、镉离子与曝气进入一次硫化曝气罐的h2s发生硫化反应,脱除锌、镉离子,一次硫化曝气过程中一般可自动维持ph值为10.0~11.0,不用投加酸碱,废水一次硫化反应时间为30~50分钟;e、镉渣沉淀、过滤:将一次硫化曝气后的废水输送到镉渣斜板沉降槽进行沉淀处理,沉淀底流送镉渣压滤机压滤,压滤产出的镉渣外运利用;f、废水二次硫化曝气:将镉渣斜板沉降槽的表面清液及镉渣压滤机压滤产出的滤液输送到二次硫化曝气罐,将硫化氢气体与压缩空气混合后通过曝气管送入二次硫化曝气罐底部并分布成细小、均匀的气泡,废水中的锌离子与曝气进入二次硫化曝气罐的h2s发生硫化反应,脱除锌离子;二次硫化曝气过程中滴加硫酸控制废水ph值为8.5~9.5,废水二次硫化反应停留时间为30~40分钟;g、锌渣沉淀、过滤:将二次硫化曝气后的废水输送到锌渣斜板沉降槽进行沉淀处理,沉淀底流送锌渣压滤机压滤,压滤产出的锌渣外运利用;h、陶瓷膜超滤处理:将锌渣斜板沉降槽的表面清夜和锌渣压滤机压滤产出的滤液输送到陶瓷膜过滤器过滤,产生的浓水返回锌渣斜板沉降槽,清液送入有机膜过滤器;i、有机膜纳滤处理:将步骤h的清液再经有机膜过滤器过滤,产生的浓水返回陶瓷膜过滤器重新过滤,过滤后的部分清液送电镀系统回用,其余清液送入ph值调节池;j、ph值调节:在ph值调节池加酸,并进行搅拌反应,调节ph值稳定为7~9,cd2+稳定达到0.05mg/l以下、zn2+≤1.5mg/l、ss≤1.0mg/l后排放,或返回电镀车间回用。本发明所述步骤b、d、f、j中,产生的尾气送入尾气吸收塔处理。本发明所述步骤d和f中,所用的硫化氢气体来自硫化氢发生器或罐装硫化氢气体,硫化氢发生器生产的气体为硫化氢和二氧化碳混合气体,其中,h2s体积含量80.0~85.0%,co2体积含量15.0~20.0%。实施例1如图2所示,本发明氰化镀镉电镀废水处理工艺采用的系统,包括由前至后经工艺管道依次相接的氰镉废水调节池1、破氰反应池3、尾气吸收塔5、一次硫化曝气罐7、镉渣斜板沉淀槽9、镉渣压滤机11、除镉清液池12、二次硫化曝气罐14、锌渣斜板沉淀槽16、锌渣压滤机18、除锌清液池19、陶瓷膜过滤器21、陶瓷过滤清液池22、有机膜过滤器24、有机膜过滤清液池25和ph调节池27,氰镉废水调节池1与破氰反应池3之间的连接管道上设有输送泵a2,破氰反应池3的顶部设有尾气出口,并设有二氧化氯和氢氧化钠的投加口,破氰反应池3的下部设有破氰反应池搅拌口31,破氰反应池顶部的尾气出口经管道与尾气吸收塔5下部的尾气入口相连接,破氰反应池3的破氰反应池搅拌口31经管道与尾气吸收塔5上部的二级喷淋装置52相连接,尾气吸收塔5的下部连接尾吸塔循环泵6,通过尾吸塔循环泵6将尾气吸收塔的部分喷淋液输送至尾气吸收塔5上部的一级喷淋装置51进行环循喷淋,部分喷淋液输送至一次硫化曝气罐7,一次硫化曝气罐7的底部设有一次硫化曝气管71,一次硫化曝气罐7的底部与镉渣斜板沉淀槽9的进料口之间的连接管道上设有输送泵b8,镉渣斜板沉淀槽9的底部出料口与镉渣压滤机11的进料口之间的连接管道上设有镉渣压滤泵10,镉渣压滤机11的底部设有镉渣斗111,镉渣压滤机11的出液口以及镉渣斜板沉淀槽9的出液口经管道与除镉清液池12相接,除镉清液池12的底部经管道与二次硫化曝气罐14相连接,该管道上设有输送泵c13,二次硫化曝气罐14的底部设有二次硫化曝气管141,二次硫化曝气罐14的底部与锌渣斜板沉淀槽16之间的连接管道上设有输送泵d15,锌渣斜板沉淀槽16的底部与锌渣压滤机18的进料口之间的连接管道上设有锌渣压滤泵17,锌渣压滤机18的底部设有锌渣斗181,锌渣压滤机18的出液口以及锌渣斜板沉淀槽16的出液口经管道与除锌清液池19相接,除锌清液池19的底部经管道与陶瓷膜过滤器21的进口相连接,该管道上设有陶瓷膜过滤高压泵20,陶瓷膜过滤器21的浓水经管道返回锌渣压滤机18,清液经管道输送至陶瓷过滤清液池22,陶瓷过滤清液池22的底部经连接管道与有机膜过滤器24的进口连接,该连接管道上设有有机膜过滤高压泵23,有机膜过滤器24的浓水经管道返回除锌清液池19,清液经管道输送至有机膜过滤清液池25,有机膜过滤清液池25的底部经连接管道与ph调节池27的进口或回用车间的管道相连接,该连接管道上设有输送泵e26,ph调节池27的顶部设有硫酸加入口,ph调节池27内设有ph计和搅拌装置271,该搅拌装置271包括搅拌杆、设在搅拌杆上的搅拌叶以及用以驱使搅拌杆转动的驱动电机,ph调节池27的底部连接输送泵f28,通过输送泵f28将达标废水回用或排放。所述尾气吸收塔5、一次硫化曝气罐7、二次硫化曝气罐14和ph调节池27的顶部均设有与排放管道相连接的排放口,排放管道上安装有尾气排放风机29。一次硫化曝气罐7的一次硫化曝气管71和二次硫化曝气罐14的二次硫化曝气管141均与硫化氢气体和压缩空气的混合气输入管相连接,硫化氢气体可来自硫化氢发生器30,也可采用罐装硫化氢气体。所述破氰反应池3的下部连接破氰搅拌泵4,破氰反应池搅拌口31排出的废水经破氰搅拌泵4返回破氰反应池3内实现搅拌作用。所述一次硫化曝气罐7和二次硫化曝气罐14的高度与直径之比均为1.0~1.2:1;一次硫化曝气罐和二次硫化曝气罐内安装有ph计用于检测的废水ph值。所述尾气吸收塔5可以采用多层喷淋空塔形式,塔内安装管式压力分布器和喷头。本实例氰镉电镀废水处理的操作步骤如下:a、氰化电镀车间的漂洗水等电镀废水汇集到氰镉废水调节池1混合均匀,稳定废水水质;b、用输送泵a2将氰化废水调节池1内的废水输送到破氰反应池3进行氧化破氰处理:投加少量氢氧化纳将废水ph值调节到10.0~11.0,并按clo2∶cn-=2.70~3.00∶1(质量比)投加二氧化氯到废水中,启动破氰搅拌泵4搅拌反应45~60min;c、废水初级硫化及尾气吸收:破氰后的废水通过破氰搅拌泵4旁路输送到尾气吸收塔5的二级喷淋装置52,尾吸塔循环泵6输送尾吸塔塔底的破氰废水到尾气吸收塔5的一级喷淋装置51,两级喷淋装置的循环液与尾气逆流接触进行初级硫化,废水中的锌、镉离子与尾气中的h2s发生硫化反应,脱除部分锌、镉离子;尾气中的h2s及氯气等酸性气体被吸收脱除后达标排放,一级吸收塔尾气流速1.8~2.2m/s,总喷淋密度45~55m3/(m2.h);d、初级硫化后的氰镉废水被尾吸塔循环泵6通过旁路送入一次硫化曝气罐7,硫化氢发生器30产出的硫化氢气体(也可采用罐装硫化氢气体)与曝气所用的压缩空气混合后,通过安装在一次硫化曝气罐底部的一次硫化曝气管71分布成细小、均匀的气泡,废水中的锌、镉离子与曝气进入一次硫化曝气罐7的h2s发生硫化反应,脱除锌、镉离子;一次硫化曝气过程中一般可自动维持ph值为10.0~11.0,不用投加酸碱,废水一次硫化反应时间为30~50分钟;e、一次硫化曝气后的废水通过输送泵b8输送到镉渣斜板沉降槽9进行沉淀处理,沉淀底流通过镉渣压滤泵10输送镉渣压滤机11压滤,压滤产出的镉渣经镉渣斗111暂存后送综合利用;f、镉渣斜板沉淀产出的清液及镉渣斜板沉降底流压滤产出的滤液汇集到除镉清液池12后,用输送泵c13输送到二次硫化曝气罐14,硫化氢发生器30产出的硫化氢气体(也可采用罐装硫化氢)与曝气所用的压缩空气混合后,通过安装在二次硫化曝气罐14底部的二次硫化曝气管141分布成细小、均匀的气泡,废水中的锌离子与曝气进入二次硫化曝气罐14的h2s发生硫化反应,脱除锌离子;二次硫化曝气罐14的高度/直径比为1.0~1.2;二次硫化曝气过程中滴加硫酸控制ph值为8.5~9.5,废水二次硫化反应时间为30~40分钟;g、二次硫化曝气后的废水用输送泵d15输送到锌渣斜板沉降槽16进行沉淀处理,沉淀底流用锌渣压滤泵17输送到锌渣压滤机18压滤,压滤产出的锌渣送综合利用;h、锌渣斜板沉降槽16的表面清夜和锌渣压滤机18滤液汇合进入除锌清液池19后,用陶瓷膜过滤高压泵20输送到陶瓷膜过滤器21过滤,浓水返回锌渣斜板沉降槽16沉淀,清液送陶瓷过滤清液池22;i、汇集到陶瓷过滤清液池22内的清液用有机膜过滤高压泵23输送到有机膜过滤器24深度去锌、镉离子,有机膜过滤器24处理后得到的浓水返回陶瓷膜过滤器21过滤,有机膜过滤器24产出的清液送至有机膜过滤清液池25,再经输送泵e26输送至电镀系统回用或ph值调节池27;j、在ph值调节池27加硫酸、搅拌反应,调节ph值稳定为7~9,cd2+稳定达到0.05mg/l以下,zn2+≤1.5mg/l,ss≤1.0mg/l,达到电镀废水排放指标要求排放;处理后的废水也可返回电镀车间回用。处理效果:处理前氰化含镉电镀废水成分如下(ph值无量纲):项目cn-cd2+zn2+ph水量含量mg/l600~100050~12090~120≥1015m3/h处理后废水电镀废水成分如下(ph值无量纲)项目cn-cd2+zn2+clo2ph含量mg/l0.009~0.0300.03~0.041.0~1.2<2.07~9处理后废水残留clo2<2.0mg/l,实际生产消耗clo216.95~28.2kg/h;生产中消耗硫化氢发生器产出的含硫化氢气体(含h2s80%)0.6~0.7m3/h;处理后废水含cn-、含cd2+和zn2+分别为0.009~0.030mg/l、0.03~0.04mg/l和1.0~1.2mg/l,完全达到《gb21900-2008电镀污染物排放标准》电镀废水总镉、总氰化物和总锌最高允许排放浓度0.05mg/l、0.3mg/l和1.5mgl的最高限值要求,可回用或达标排放。实施例2:如图3所示,本发明氰化镀镉电镀废水处理工艺采用的系统结构与实施例1采用的结构基本相同,区别在于,尾吸塔循环泵6同时将尾气吸收塔的喷淋液输送至一级喷淋装置51和二级喷淋装置52进行环循喷淋。本实例氰镉电镀废水处理的操作步骤如下:a、氰化电镀车间的漂洗水等电镀废水汇集到氰镉废水调节池1混合均匀,稳定废水水质;b、用输送泵a2将氰化废水调节池1内的废水输送到破氰反应池3进行氧化破氰处理:投加少量氢氧化纳将废水ph值调节到10.0~11.0,按clo2∶cn-=2.70~3.00∶1(质量比)投加二氧化氯到废水中,启动破氰搅拌泵4搅拌反应45~60min;c、废水初级硫化及尾气吸收:破氰后的废水通过破氰搅拌泵4旁路输送到尾气吸收塔5的二级喷淋装置52,尾吸塔塔底的破氰废水通过尾吸塔循环泵6输送到尾气吸收塔5的一级喷淋装置51和二级喷淋装置52,两级喷淋装置的循环液与尾气逆流接触进行初级硫化,废水中的锌、镉离子与尾气中的h2s发生硫化反应,脱除部分锌、镉离子;尾气中的h2s及氯气等酸性气体被吸收脱除后达标排放,一级吸收塔尾气流速1.8~2.2m/s,总喷淋密度45~55m3/(m2.h);采用双层喷淋装置,可以更好保证二级喷淋装置52的喷淋密度和吸收效果;d、初级硫化后的氰镉废水被尾吸塔循环泵6通过旁路送入一次硫化曝气罐7,硫化氢发生器产的硫化氢气体(也可采用罐装硫化氢)与曝气所用的压缩空气混合后,通过安装在一次硫化曝气罐底部的一次硫化曝气管71分布成细小、均匀的气泡,废水中的锌、镉离子与曝气进入一次硫化曝气罐7的h2s发生硫化反应,脱除锌、镉离子;一次硫化曝气过程中一般可自动维持ph值为10.0~11.0,不用投加酸碱,废水一次硫化反应时间为30~50分钟;e、一次硫化曝气后的废水通过输送泵b8输送到镉渣斜板沉降槽9进行沉淀处理,沉淀底流通过镉渣压滤泵10输送镉渣压滤机11压滤,压滤产出的镉渣经镉渣斗111暂存后送综合利用;f、镉渣斜板沉淀产出的清液及镉渣斜板沉降底流压滤产出的滤液汇集到除镉清液池12后,用输送泵c13输送到二次硫化曝气罐14,硫化氢发生器30产出的硫化氢气体(也可采用罐装硫化氢)与曝气所用的压缩空气混合后,通过安装在二次硫化曝气罐14底部的二次硫化曝气管141分布成细小、均匀的气泡,废水中的锌离子与曝气进入二次硫化曝气罐14的h2s发生硫化反应,脱除锌离子;二次硫化曝气罐14的高度/直径比为1.0~1.2;二次硫化曝气过程中滴加硫酸控制ph值为8.5~9.5,废水二次硫化反应时间为30~40分钟;g、二次硫化曝气后的废水用输送泵d15输送到锌渣斜板沉降槽16进行沉淀处理,沉淀底流用锌渣压滤泵17输送到锌渣压滤机18压滤,压滤产出的锌渣送综合利用;h、锌渣斜板沉降槽16的表面清夜和锌渣压滤机18滤液汇合进入除锌清液池19后,用陶瓷膜过滤高压泵20输送到陶瓷膜过滤器21过滤,浓水返回锌渣斜板沉降槽16沉淀,清液送陶瓷过滤清液池22;i、汇集到陶瓷过滤清液池22内的清液用有机膜过滤高压泵23输送到有机膜过滤器24深度去锌、镉离子,有机膜过滤器24处理后得到的浓水返回陶瓷膜过滤器21过滤,有机膜过滤器24产出的清液送至有机膜过滤清液池25,再经输送泵e26输送至电镀系统回用或ph值调节池27;j、在ph值调节池27加硫酸、搅拌反应,调节ph值稳定为7~9,cd2+稳定达到0.05mg/l以下,zn2+≤1.5mg/l,ss≤1.0mg/l,达到电镀废水排放指标要求后排放;处理后的废水也可返回电镀车间回用。处理效果:处理前氰化含镉电镀废水成分如下(ph值无量纲):项目cn-cd2+zn2+ph水量含量mg/l1500~1800120~150150~180≥1012m3/h处理后废水电镀废水成分如下(ph值无量纲)项目cn-cd2+zn2+clo2ph含量mg/l0.015~0.0250.03~0.041.0~1.2<2.07~9处理后废水残留clo2<2.0mg/l,实际生产消耗clo233.81~40.56kg/h;生产中消耗硫化氢发生器产出的含硫化氢气体(含h2s80%)0.7~0.8m3/h;处理后废水含cn-、含cd2+和zn2+分别为0.02~0.05mg/l、0.03~0.04mg/l和1.0~1.2mg/l,完全达到《gb21900-2008电镀污染物排放标准》电镀废水总镉、总氰化物和总锌最高允许排放浓度0.05mg/l、0.3mg/l和1.5mgl的最高限值要求,可回用或达标排放。本发明采用上述工艺及处理系统处理氰化镀镉电镀废水,不仅能确保处理后的废水指标、提高水回用率、减少电镀污水排放,还可降低电镀废水处理碱耗和酸耗,且有利于满足日趋严格的环保要求。最后应说明的是:以上实施例仅用以说明本发明的技术方案而非对其进行限制,尽管参照较佳实施例对本发明进行了详细的说明,本领域的普通技术人员应当理解:其依然可以对本发明的技术方案进行修改或者等同替换,而这些修改或者等同替换亦不能使修改后的技术方案脱离本发明技术方案的精神和范围。当前第1页12