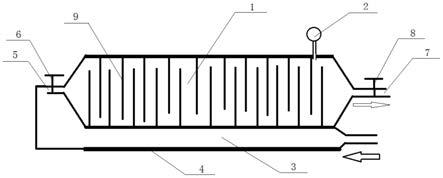
1.本发明属于废水处理技术领域,具体涉及废水中氰化物的热分解降解方法及装置,更为具体的说,在阿托伐他汀钙合成的重要原料3
‑
氧代
‑5‑
羟基
‑6‑
氰基己酸叔丁酯工业生产中,产生含氰化钠、氰化钾的废水的热分解降解方法及装置。
背景技术:[0002]3‑
氧代
‑5‑
羟基
‑6‑
氰基己酸叔丁酯,是阿托伐他汀钙合成过程中不可少的原料,其合成方法为:
[0003][0004]
氰化物毒性很大,能抑制细胞呼吸,造成呼吸障碍和组织缺氧,并还可经人体皮肤、胃肠道等迅速吸收,氰化物废水不仅能造成环境污染,还会造成人、动物及水生生物的中毒甚至死亡,严重破坏生态平衡,任意排放还会造成地下水污染。
[0005]
常用的降解废水中的氰化物的方法有化学法、物理方法及生化方法:
[0006]
次氯酸钠/漂白粉、氯气氧化法:氰化物被氧化为毒性低的氰酸盐,也可以进一步氧化为二氧化碳、氮气,但此方法的缺点是次氯酸盐用量大,且氧化剂需要过量数倍,处理过程中要保证废水ph大于10,对高浓度的氰化物废水的处理,成本昂贵,并且,处理后的废水中含氰基浓度难以达到国家要求的标准。
[0007]
双氧水氧化法:该方法一般只适用于低浓度氰离子废水的处理,并且,双氧水的来源不广,其运输、使用均有一定的危险性,成本相对较高。
[0008]
电解法:废水中的简单氰化物和配合氰化物通过电解,把氰电解氧化为二氧化碳和氮气。利用这一原理可有效去除废水中的氰污染。其缺点是:电流效率低,电解时间长,耗电量大,电极金属消耗大,目前很少采用。
[0009]
高温加压降解:是氰根离子与水反应生成无毒害的氨和碳酸盐的过程。当温度达到65℃以上时,其分解速度加快,当温度达到200℃以上时,氰化物的水解速度非常之快,该方法安全有效,处理浓度范围广,并且无二次污染。但需要特殊的高温高压设备,并且,经过一次处理,废水中氰离子浓度一般也难以达到国家要求的标准,还需要附加次氯酸盐氧化降解。
技术实现要素:[0010]
本发明的目的是在现有技术的基础上,提供一种废水中氰化物的热分解降解方法。
[0011]
本发明的另一目的是提供一种上述处理废水中氰化物的装置。
[0012]
本发明的技术方案如下:
[0013]
一种废水中氰化物的热分解降解方法,它包括如下步骤:将含氰化物的废水通入多格热分解槽中,在温度为165~200℃和压力为0.7~1.0兆帕的条件下进行热分解反应48
~60h。其中,多格热分解槽,它包括槽体和进水管,在槽体的顶部设有温度和压力控制装置,在槽体一侧封板中部设有进水口,在槽体另一侧封板设有出水口,进水管与进水口相连接,在进水管的外侧壁上设有夹套,槽体的内部设有多个交错布置的能使含氰化物的废水沿槽长方向折流通过的折流挡板。
[0014]
在进水管的外侧壁设有夹套,可以防止热量流失。
[0015]
在一种优选方案中,本装置多格热分解槽中,两邻的两个折流档板,其中一个折流档板与槽体内的上部相连接,另一个折流档板与槽体内的下部相连接,在这两个折流档板之间留有使含氰化物的废水折流通过的间隙。
[0016]
本装置可以根据实际需要设置折流档板的数量,例如,折流板的数量可以但不局限于10个、20个、30个、40个、60个、80个、100个。
[0017]
采用本装置处理废水中氰化物,折流挡板的数量不少于30时,在多格热分解槽中热分解反应后排出的废水中氰化物的降解效率可以达到95%以上。
[0018]
对于槽体的顶部设有温度和压力控制装置,可以为现有技术中常见的温度和压力传感器,为了监控含氰化物的废水在多格热分解槽中进行热分解反应时的温度和压力。
[0019]
在一种优选方案中,在进水口处的管路上设有进水控制阀,用于控制含氰化物的废水进入多格热分解槽中进行热分解反应时的速度。
[0020]
进一步地,在出水口处的管路上设有出水控制阀,用于控制在多格热分解槽中进行热分解反应后的废水的流出速度。
[0021]
对于本装置多格热分解槽,为了防止孔蚀,在槽体的内表面使用ss41与sus304复合不锈钢材料衬里。
[0022]
对于在多格热分解槽中进行热分解反应后排出的废水进行检测,当cn
‑
浓度高于1毫克/升以上时,可以将多格热分解槽的出水口排出的废水与次氯酸钠混合,在温度50~80℃的条件下进行氧化处理,进一步降低废水中cn
‑
浓度。
[0023]
在一种优选方案中,在氧化反应时,将多格热分解槽的出水口排出的废水与次氯酸钠溶液(例如,12%次氯酸钠溶液)混合,在温度50~80℃的条件下进行氧化处理。
[0024]
对于氧化反应,可以由氧化电位检测仪控制次氯酸钠的投加量。
[0025]
在一种优选方案中,氧化处理后的废水,向其中加入硫酸进行中和,调节其ph至6~8。例如,可以使用ph调节仪控制硫酸的加入量。
[0026]
对于本发明而言,在多格热分解槽中设有的折流挡板将槽体的内部分隔成多个连通的分解槽,采用本装置对含氰化物的废水进行热分解处理时,放出的热量可以传至外侧设有夹套的进水管内部,可以对待热分解处理的含氰化物的废水进行预热。与现有技术中的无分解槽的热分解装置相比,采用本装置可以缩短热分解所需的时间,并且,可以有效提高反应效率,实现cn
‑
浓度的梯度下降,如分解槽的格数增加到39个,进水管中废水氰离子的浓度10克/升,多格热分解槽的出水口中废水的cn
‑
浓度可降低到1毫克/升以下,分解效率达99.99%。而采用现有技术中的热分解装置,热处理处理后的废水中仍含有约10毫克\升的氰化物。
[0027]
采用本装置对含氰化物的废水进行热分解处理,处理后的废水中cn
‑
浓度很低,采用次氯酸钠进行氧化处理,进一步降低cn
‑
浓度时,次氯酸钠用量也大大减少。
[0028]
采用本发明的技术方案,优势如下:
[0029]
采用多格热分解槽对含氰化物的废水进行热分解处理时,在多格热分解槽中设有的折流挡板将槽体的内部分隔成多个连通的分解槽,热分解放出的热量可以传至外侧设有夹套的进水管内部,对待热分解处理的含氰化物的废水进行预热,缩短了热分解所需的时间,实现cn
‑
浓度的梯度下降,有效提高了反应效率,使cn
‑
浓度可降低到1毫克/升以下。
附图说明
[0030]
图1是本发明的装置结构示意图;
[0031]
其中,1是槽体;2是温度和压力控制装置;3是进水管;4是夹套;5是进水口;6是进水控制阀;7是出水口;8是出水控制阀;9是折流挡板。
具体实施方式
[0032]
为了更好的理解本发明,下面结合装置的示意图,通过具体的实施例对本发明装置的使用及热分解降解方法进行进一步的阐述:
[0033]
如图1所示,本装置包括槽体1和进水管3,在槽体1的顶部设有温度和压力控制装置2,在槽体1一侧封板中部设有进水口5,在槽体1另一侧封板设有出水口7,进水管3与进水口5相连接,在进水管3的外侧壁上设有夹套4,槽体1的内部设有多个交错布置的能使含氰化物的废水沿槽长方向折流通过的折流挡板9。
[0034]
对于本装置的两邻的两个折流档板9,其中一个折流档板与槽体内的上部相连接,另一个折流档板与槽体内的下部相连接,在这两个折流档板之间留有使含氰化物的废水折流通过的间隙。在图1中,与槽体1内的下部相连接的折流档板有11个,与槽体1内的上部相连接的折流档板有10个。
[0035]
对于槽体1的顶部设有温度和压力控制装置2为常见的温度和压力传感器,为了监控含氰化物的废水在多格热分解槽中进行热分解反应时的温度和压力。
[0036]
本装置的槽体1为圆形卧式结构,为了防止孔蚀,在槽体的内表面使用ss41与sus304复合不锈钢材料衬里。
[0037]
在进水口5处的管路上设有进水控制阀6,用于控制含氰化物的废水进入多格热分解槽中进行热分解反应时的速度。
[0038]
进一步地,在出水口7处的管路上设有出水控制阀8,用于控制在多格热分解槽中进行热分解反应后的废水的流出速度。
[0039]
本装置的使用过程如下:由温度和压力控制装置2预先设置槽体1内的温度和压力,将贮存槽中含氰化物的废水通入外侧设有夹套4的进水管3中,与分解槽中进行热分解反应时放出的热量进行热交换,从而对向槽体1内部输送的含氰化物的废水进行预热,预热后的废水由进水口5进入槽体1内的第一级分解槽进行热分解反应,再沿着槽长的方向依次进入第二级分解槽至最后一级分解槽中分别进行热分解反应,废水中的cn
‑
浓度逐渐下降,最后由出水口7排出。调节进水控制阀6和出水控制阀8,控制进水和排出的速度,可以实现连续出样,保证合适的反应压力。
[0040]
本装置的使用过程如下:
[0041]
启动多格热分解槽,将贮存槽中含氰化物的废水通入外侧设有夹套的进水管中,由进水口进入槽体内的第一级分解槽进行热分解反应,再沿着槽长的方向依次进入第二级
分解槽至最后一级分解槽中分别进行热分解反应,废水中的cn
‑
浓度逐渐下降,最后由出水口排出。调节进水控制阀和出水控制阀,控制进水和排出的速度,可以实现连续出样,保证合适的反应压力。多格热分解槽中由折流挡板分隔成39个分解槽,在进行热分解反应时,控制温度为165~200℃和压力为0.7~1.0兆帕,反应时间为48~60h。贮存槽中含氰化物的废水的浓度9500毫克/升,进入槽体的速度和排出热分解后的速度9000公斤/时。
[0042]
待热分解反应完成后,检测出水口中排出的废水中cn
‑
的浓度,其cn
‑
浓度低于1毫克/升。对热分解反应后排出的废水,与浓度为12%次氯酸钠溶液混合,在温度50~80℃的条件下进行氧化处理2h,由氧化电位检测仪控制次氯酸钠的投加量为废水中总氰的10倍。氧化处理后的废水,向其中加入硫酸进行中和,调节其ph至6~8,氧化后的废水cn
‑
浓度低于0.12毫克/升。
[0043]
实施例1:
[0044]
启动多格热分解槽,将贮存槽中含氰化物的废水通入外侧设有夹套的进水管中,由进水口进入槽体内的第一级分解槽进行热分解反应,再沿着槽长的方向依次进入第二级分解槽至最后一级分解槽中分别进行热分解反应,废水中的cn
‑
浓度逐渐下降,最后由出水口排出。调节进水控制阀和出水控制阀,控制进水和排出的速度,可以实现连续出样,保证合适的反应压力。多格热分解槽中由折流挡板分隔成39个分解槽,在进行热分解反应时,控制温度为185℃和压力为0.9兆帕,反应时间为55h。贮存槽中含氰化物的废水的浓度9500毫克/升,进入槽体的速度和排出热分解后的速度9000公斤/时。
[0045]
待热分解反应完成后,检测出水口中排出的废水中cn
‑
的浓度,其cn
‑
浓度为0.65毫克/升。对热分解反应后排出的废水,与浓度为12%次氯酸钠溶液混合,在温度70℃的条件下进行氧化处理2h,由氧化电位检测仪控制次氯酸钠的投加量为废水中总氰的10倍。氧化处理后的废水,向其中加入硫酸进行中和,调节其ph至7,氧化后的废水cn
‑
浓度低于0.06毫克/升。
[0046]
实施例2:
[0047]
启动多格热分解槽,将贮存槽中含氰化物的废水通入外侧设有夹套的进水管中,由进水口进入槽体内的第一级分解槽进行热分解反应,再沿着槽长的方向依次进入第二级分解槽至最后一级分解槽中分别进行热分解反应,废水中的cn
‑
浓度逐渐下降,最后由出水口排出。调节进水控制阀和出水控制阀,控制进水和排出的速度,可以实现连续出样,保证合适的反应压力。多格热分解槽中由折流挡板分隔成30个分解槽,在进行热分解反应时,控制温度为185℃和压力为0.9兆帕,反应时间为55h。贮存槽中含氰化物的废水的浓度9500毫克/升,进入槽体的速度和排出热分解后的速度9000公斤/时。
[0048]
待热分解反应完成后,检测出水口中排出的废水中cn
‑
的浓度,其cn
‑
浓度为0.83毫克/升。对热分解反应后排出的废水,与浓度为12%次氯酸钠溶液混合,在温度70℃的条件下进行氧化处理2h,由氧化电位检测仪控制次氯酸钠的投加量为废水中总氰的10倍。氧化处理后的废水,向其中加入硫酸进行中和,调节其ph至7,氧化后的废水cn
‑
浓度低于0.09毫克/升。
[0049]
实施例3:
[0050]
启动多格热分解槽,将贮存槽中含氰化物的废水通入外侧设有夹套的进水管中,由进水口进入槽体内的第一级分解槽进行热分解反应,再沿着槽长的方向依次进入第二级
分解槽至最后一级分解槽中分别进行热分解反应,废水中的cn
‑
浓度逐渐下降,最后由出水口排出。调节进水控制阀和出水控制阀,控制进水和排出的速度,可以实现连续出样,保证合适的反应压力。多格热分解槽中由折流挡板分隔成39个分解槽,在进行热分解反应时,控制温度为170℃和压力为0.8兆帕,反应时间为48h。贮存槽中含氰化物的废水的浓度9500毫克/升,进入槽体的速度和排出热分解后的速度9000公斤/时。
[0051]
待热分解反应完成后,检测出水口中排出的废水中cn
‑
的浓度,其cn
‑
浓度为0.89毫克/升。对热分解反应后排出的废水,与浓度为12%次氯酸钠溶液混合,在温度60℃的条件下进行氧化处理2h,由氧化电位检测仪控制次氯酸钠的投加量为废水中总氰的10倍。氧化处理后的废水,向其中加入硫酸进行中和,调节其ph至7,氧化后的废水cn
‑
浓度低于0.11毫克/升。
[0052]
以上实施例仅用以说明本发明的技术方案,而非对其限制;尽管参照前述实施例对本发明进行了详细的说明,本领域的普通技术人员应当理解:其依然可能对前述各实施例所记载的技术方案进行修改,或者对其中部分技术特征进行等同替换;而这些修改或者替换,并不使相应技术方案的本质脱离本发明各实施例技术方案的范围。