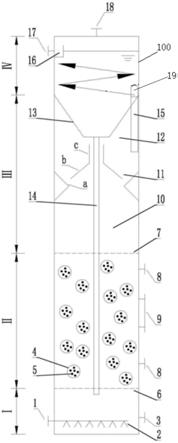
[0001]
本实用新型属污水处理技术领域,特别是涉及一种高效经济气升式自循环颗粒污泥床脱氮反应器。
背景技术:[0002]
随着环境保护意识的逐步提高以及环保政策的日益严格,对于总氮的控制与削减显得异常重要。在当前的脱氮技术中,生物脱氮技术仍然是最经济有效的选择。传统的脱氮技术从生物的存在状态来看可分为活性污泥法和和生物膜法两种形式。活性污泥法其生物以絮体形式存在,由于受到污泥混合液浓度的限制,单位容积内生物量相对较低,多用于低浓度的市政污水等低浓度污水。生物膜法由于其单位容积生物量高,污染物容积负荷较高,在高浓度的硝氮废水处理方面具有独特的优势。生物膜法固定床的反硝化负荷可以达到1~3kgno
3-n
·
m-3
·
d-1
,氮去除率90%以上,但容易堵塞引起沟流,所以无论是上流式还是下向流固定床,均需要反洗,增加了运行和管理的复杂性。流化床的反硝化负荷可以达到2~15 kgno
3-n
·
m-3
·
d-1
,但存在稳定流态化与载体再生问题。移动床集合流化床、固定床与活性污泥法的一些优点,但负荷较低,反应器出水通常需要脱膜处理与絮状污泥沉降。
[0003]
高效、节能、经济是当今废水生物处理共同追求的目标。颗粒污泥技术一直是废水处理的前沿领域,其主要特性在于污泥形态上的创新。与絮状污泥相比,颗粒污泥具有更高的生物量、更丰富的生物相和更卓越的沉降性能。厌氧颗粒污泥的成功得益于厌氧污泥的颗粒化,因此,反硝化颗粒污泥成功实现将对反硝化单级工艺实现突破性创新。颗粒污泥反应器的抗基质负荷及水力冲击的能力也大幅度增强,可大大减小占地面积,节省沉淀池及配套设施。其配套反应器如上流式污泥床,有利于小规模一体化装置的开发和应用。而相比生物膜法,颗粒污泥本身也是一种特殊的生物膜,但其依靠生物自凝聚作用,无需额外人工载体,因此在技术经济指标也更具竞争力。
[0004]
目前大量在缺氧条件下实现了反硝化微生物的颗粒化,并且具有颗粒污泥普遍具有的优点,为生物法处理高浓度硝酸盐废水创造了更多的可能,并开发了相应的反应工艺和设备。颗粒污泥是自我聚集的具有球状结构的生物膜,生物膜的形态和强度与基质负荷及剪力有关,当生物膜的生长和脱落与表面基质浓度和剪力之间达到平衡时,便可形成光滑的生物膜。较高剪切力是颗粒污泥形成的关键因素之一,在较高的基质负荷下提高水流剪切力,丝状菌易破碎并随反应器出水排走,有利于形成密实、沉降性能较好的颗粒污泥。由于运行中为了获得较好的硝化脱氮效果和污泥稳定的颗粒化程度,往往采用出水回流的方式提高反应器上升流速,减缓生物反应基质的抑制作用,另一方面,流速较高这不利于反应器内污泥的分离沉淀,会存在跑泥现象,由此造成的矛盾成为了颗粒污泥床脱氮反应器发展与应用的一个限制因素。
[0005]
因此,有必要提供一种新的高效经济气升式自循环颗粒污泥床脱氮反应器来解决上述问题。
技术实现要素:[0006]
本实用新型的主要目的在于提供一种高效经济气升式自循环颗粒污泥床脱氮反应器,通过气升式自循环颗粒污泥床脱氮反应器,强化反应液自循环,缓解了基质抑制作用;设计创新内构件,通过挤压效应消除了颗粒污泥上浮流失问题;提出并运用“低基质高流量”的操作模式,大幅提升了反应器的容积效能。
[0007]
本实用新型通过如下技术方案实现上述目的:一种高效经济气升式自循环颗粒污泥床脱氮反应器,其包括形成一封闭腔体结构的反应器本体、沿所述反应器本体从下到上依次设置的且相互连通的进水布水区、生物反应区、三相分离区和旋流分离区,所述生物反应区内填充有若干内嵌有生物颗粒污泥的生物填料,所述旋流分离区内设置有将其与所述三相分离区分隔的泥斗、连通所述泥斗最低点端向下延伸至所述进水布水区的回流管、穿过所述泥斗向下伸入所述三相分离区的导流管、以及位于上部的集水槽,所述相分离区内设置有三相分离器,所述反应器本体上设置有与所述进水布水区内部连通的进水口、与所述集水槽连通的出水口。
[0008]
进一步的,所述三相分离区被所述三相分离器分隔形成一清水区和一气室,所述清水区位于生物反应区上方0.5~1.0m的空间。
[0009]
进一步的,所述三相分离器包括环绕所述回流管设置且将气体导入所述气室内的导气筒、自所述导气筒底部圆周向下向外延伸的第一反射斜板、沿所述反应器本体内壁一圈的且位于所述第一反射斜板下方的第二反射斜板。
[0010]
进一步的,所述导流管的顶端高于所述泥斗表面且顶部斜向上弯折形成有一导流部使得水流沿所述反应器本体内壁旋转向上流动;所述导流管的底端低于所述导气筒的顶端至少50mm。
[0011]
进一步的,所述进水布水区、所述生物反应区、所述三相分离区和所述旋流分离区的高度之比为1:(5~9):(2~5):(2~3),并依次连通形成所述反应器本体。
[0012]
进一步的,所述反应器本体上设置有与所述进水布水区内部连通的排泥放空口、在所述生物反应区上部位置和下部位置均设置有与所述生物反应区连通的排泥取样口、在所述生物反应区中部位置设置有与所述生物反应区连通的填料安装入口、在顶部位置设置有与所述旋流分离区连通的排气口。
[0013]
进一步的,所述生物反应区内还设置有一用于支撑所述生物填料的承托支架、顶部设置有一稳定所述生物填料位置的填料稳定栅,所述承托支架位于所述进水布水区与所述生物反应区分界面,所述填料稳定栅位于所述三相分离区与所述生物反应区的分界面,所述承托支架和所述填料稳定栅布置于所述反应器本体的整个横截面。
[0014]
进一步的,所述生物填料为中空球形填料,密度为1g/cm
3
,比表面积大于或等于500m
2
/m
3
,孔隙率介于60%~85%,所述生物颗粒污泥镶嵌在所述生物填料内部。
[0015]
进一步的,所述第一反射斜板、所述第二反射斜板的倾角范围为55
°
~60
°
,所述第一反射斜板与所述第二反射斜板的水平投影区域有重叠部分,且重叠遮盖间距为100~200mm。
[0016]
与现有技术相比,本实用新型一种高效经济气升式自循环颗粒污泥床脱氮反应器的有益效果在于:将反硝化脱氮污泥颗粒化并与生物填料相结合,提高了反硝化颗粒污泥的稳定性,填料系统丰富了生物链的种类,大大提高了单位容积内的生物量,提高了反硝化
的容积效能,进而能够节省反应器建造投资;通过反硝化产生的气体气提废水强化了反应液自回流循环,缓解了基质抑制,同时节省了现有技术的循环回流所需能耗;设计创新旋流分离构件,强化泥水分离能力,消除了颗粒污泥上浮流失的问题,提高了系统的稳定性;通过回流反应液,稀释了进水基质的浓度,提高了反应器内部上升流量,较高的表面流速更利于改善颗粒污泥的性质,大幅提升了反应器的抗冲性能。
[0017]
【附图说明】
[0018]
图1为本实用新型实施例的结构原理示意图;
[0019]
图中数字表示:
[0020]
进水布水区-、生物反应区-、三相分离区-、旋流分离区-;
[0021]
反应器本体100、进水口1、布水管2、排泥放空口3、生物填料4、颗粒污泥5、承托支架6、填料稳定栅7、排泥取样口8、安装人孔9、清水区10、三相分离器11、气室12、泥斗13、回流管14、导流管15、集水槽16、出水口17、排气口18、导流部19。
[0022]
【具体实施方式】
[0023]
实施例一:
[0024]
请参照图1,本实施例一种高效经济气升式自循环颗粒污泥床脱氮反应器,其包括形成一封闭腔体结构的反应器本体100、沿反应器本体100从下到上依次设置的进水布水区-、生物反应区-、三相分离区-和旋流分离区-,进水布水区-底部封闭,所述旋流分离区-顶部封闭,进水布水区-、生物反应区-、三相分离区-和旋流分离区-的高度之比为1:(5~9):(2~5):(2~3),并依次连通成为反应器本体100。
[0025]
进水布水区-位于反应器底部,主要包括位于一侧的进水口1、与进水口1连通的布水管2、以及位于另一侧的排泥放空口3,布水管2由布水干管和布水支管组成,布水支管上斜向下45
°
方向设置有若干出水孔,孔径9~12mm,单孔服务面积2~4m
2
,进水布水区-上部与生物反应区-下部连通。
[0026]
生物反应区-位于进水布水区-的上部,生物反应区-内填充有若干生物填料4,生物填料4内镶嵌有若干生物颗粒污泥5。生物反应区-的底部设置有一用于支撑生物填料4的承托支架6、顶部设置有一稳定生物填料4位置的填料稳定栅7,生物反应区-在靠近底部和顶部位置均设置有一排泥取样口8、中部位置设置有一填料安装入口9;所述生物填料4为中空球形填料,密度为1g/cm
3
,比表面积大于或等于500m
2
/m
3
,孔隙率介于60%~85%,生物颗粒污泥5镶嵌在生物填料4内部;承托支架6位于进水布水区-与生物反应区-分界面,填料稳定栅7位于三相分离区-与生物反应区-的分界面,承托支架6和填料稳定栅7布置于反应器整个横截面;生物反应区-上部与三相分离区-下部连通。
[0027]
三相分离区-位于生物反应区-的上部,包括位于中部的三相分离器11、被三相分离器11分隔并连通起来的清水区10与气室12,清水区11的高度为填料稳定栅7以上0.5~1.0m的空间;三相分离器11包括导气筒c、自导气筒c底部轮廓向外向下扩展的反射斜板b、沿反应器本体100内壁一圈的且位于反射斜板b下方的环形状反射斜板a,反射斜板a呈对接的双喇叭口结构,反射斜板a、b的倾角范围在55
°
~60
°
之间,反射斜板a与反射斜板b的水平投影重叠遮盖间距在100~200mm,确保良好的固液分离效果,反射斜板b和导气筒c连接;导气筒c直径300~500mm,与回流管14中心同轴,将气体导入气室12顶部。
[0028]
旋流分离区-位于反应器本体顶部,其下部与三相分离区-的气室12通过一泥斗
13隔断;旋流分离区-中的泥斗13呈倒锥形,锥体母线与水平面夹角55
°
~60
°
之间,使得沉淀污泥能过顺利的从泥斗13内壁向下滑落至回流管14中;泥斗13的最低点设置有回流管14、一侧设置有导流管15。所述回流管14的直径大于100mm,回流管14的下端延伸至进水布水区-的上部;所述导流管15位于泥斗13边缘处并贯穿泥斗13,导流管15下端向下延伸至三相分离区-,导流管15的底端低于导气筒c顶部至少50mm,使得气室12内的气体不会直接从导流管15中导出,而是通过不断的向气室12内输入气体增加其内部压力,将气室12内的清液向上挤压出去,当气液分界面低于导流管15底部时,气室12内的气体才从导流管15中导出,从而更好的实现气液分离;导流管15上端至泥斗13以上的旋流分离区-进水点,上端弯折呈45
°
斜向上形成导流部19,导流部19将导流管15喷涌出来的水柱在设定角度上带有一定的初速度,然后打在反应器本体100内壁表明,然后呈螺旋向上的路径流动,形成漩涡形式,更好的实现固液分离;旋流分离区-上部有出水集水槽16,集水槽16上设置有三角出水堰,集水槽16与旋流分离区-外壁内侧连接,与出水口17连通;旋流分离区-顶部设置有盖板,盖板上设置有排气口18。回流管14贯穿导气筒c。
[0029]
基于上述高效经济气升式自循环颗粒污泥床脱氮反应器,本实用新型还提供了高效经济气升式自循环颗粒污泥床脱氮方法,其步骤如下:
[0030]
待处理废水经由进水口1和布水管2输入反应器,使废水充满水进水布水区-后向上进入生物反应区-,废水中的硝酸盐在生物反应区-内生物填料4上颗粒污泥5中反硝化菌的反硝化作用下生成气体;废水流经生物反应区-后进入三相分离区-,废水中从生物反应区-携带出来的少量污泥以及反硝化产生的气体在三相分离器11的分离作用下实现气、固、液三相分离,气体由导气筒c导入气室12,污泥固体回落到下部生物反应区-,液体通过旋流分离区-的导流管15进入旋流分离区-,在旋流作用下进一步分离细小的颗粒污泥,污泥沉入底部泥斗13并通过回流管14沉降至进水布水区-,水流由三角出水堰进入集水槽16,最终通过连出水口17排出反应器;收集在气室12内的气体逐渐增多,体积变大,气室12内气液分界面逐渐下降,直到降至导流管15下端等高时,气体开始从导流管15逸出,形成气提作用,形成气液混合体从导流管15上升至旋流分离区-完成气、液、固三相分离,固体下沉至泥斗13,气体上升至顶部由排气口18排出反应器;由于气提的抽吸作用,气提提升至旋流分离区-的液体以及沉淀至泥斗13的污泥会通过回流管14回流至进水布水区-,形成上清液自回流。
[0031]
本实施例高效经济气升式自循环颗粒污泥床脱氮反应器,其自下而上包括进水布水区、生物反应区、三相分离区、旋流分离区四个部分,进水布水区设置进水回流管并与内部布水装置相连,填料反应区装填有高效颗粒污泥及专性球形填料,旋流分离区设置有导流管和回流管,三相分离区与旋流分离区配合实现混合液及污泥强化内循环,缓解了基质抑制作用,消除了颗粒污泥上浮流失问题,同时降低了运行能耗和设备成本,提出并运用“低基质高流量”的操作模式,大幅提升了反应器的容积效能。
[0032]
本实施例中,各设备部件及方法参数可优选设计如下:
[0033]
1)进水布水区-、生物反应区-、三相分离区-和旋流分离区-的高度之比为1:(5~9):(2~5):(2~3)。
[0034]
2)布水管2由布水干管和布水支管组成,布水支管上斜向下45
°
方向设置有出水孔,孔径9~12mm,单孔服务面积2~4m
2
。
[0035]
3)生物填料4直径为80~100mm,密度为1g/cm
3
,比表面积大于500m
2
/m
3
,孔隙率介于60%~85%。
[0036]
4)清水区10高度为填料稳定栅7以上0.5~1.0m的空间;三相分离器11反射斜板a和反射斜板b与水面面倾角范围55
°
~60
°
之间,反射斜板a和反射斜板b水平投影重叠遮盖间距在100mm~200mm,导气筒c直径300~500mm。
[0037]
5)旋流分离区-泥斗13锥体母线与水平面夹角55
°
~60
°
之间;回流管14直径大于100mm;导流管15下端向下延伸至三相分离区-中导气筒c的上部以下100mm,上端弯折呈45
°
斜向上。
[0038]
6)进水布水区-中布水管2干管流速控制1~1.5m/s,支管流速2~2.5m/s,孔眼流速4~6m/s;反应器本体上升流速5~7m/h,生物反应区-容积负荷15~20kgno
3-n/(m
3
·
d);集水槽16出水堰上水头应大于25mm,水位在三角堰齿1/2处,出水堰口负荷宜小于1.7 l/(s
·
m)。
[0039]
以上所述的仅是本实用新型的一些实施方式。对于本领域的普通技术人员来说,在不脱离本实用新型创造构思的前提下,还可以做出若干变形和改进,这些都属于本实用新型的保护范围。