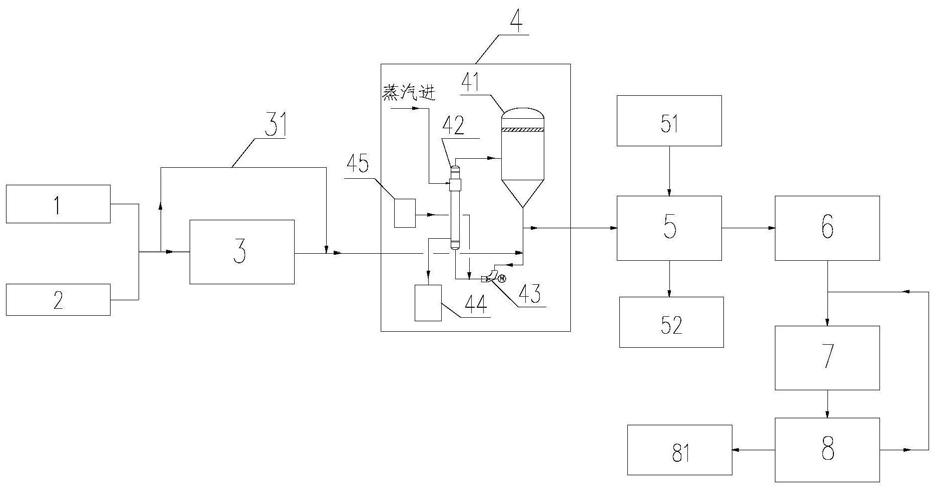
1.本实用新型涉及高盐废水处理的技术领域,更具体地讲,涉及一种高盐废水零排放资源化处理设备。
背景技术:2.高盐废水通常是指tds大于1%的废水。高盐废水的产生途径广泛,水量也逐年增加。目前,高盐废水中有很多成分都是我国环保标准中必须严格把控的污染物,常见的高盐废水零排放处理技术路线是分盐处理技术路线与杂盐处理技术路线。
3.分盐处理路线又以膜法分盐及热法分盐为主。膜法技术采用的技术路线为:预处理软化>nf分盐>膜浓缩>分质结晶。该技术路线流程长,投资及运行成本较高(投资成本按每小时水量计每吨水高于200万,每吨水运行费用在100元以上),尤其是在预处理软化阶段需投加大量药剂,以降低脱硫废水的硬度,整体经济性差且膜的后期维护困难,最终分质结晶产出的nacl、na2so4盐经济性较差。此外,该路线最终还存在少量的杂盐需要单独处理。目前,此部分杂盐被判为危废,处理成本高。热法分盐也需要深度软化预处理,根据nacl、na2so4在不同温度下溶解度差异实现分盐结晶,整体投资及运行成本也非常高。
4.杂盐处理路线主要以热法技术为主,为低温多效蒸发与烟气蒸发。低温多效蒸发技术为高盐废水软化后再采用蒸汽作为热源将高盐废水浓缩或蒸发成杂盐。蒸发过程中为避免caso4结垢,需进行完善的软化预处理,系统整体运行成本将高于60元/吨水。多效蒸发最终得到杂盐,后续处理困难且caso4在蒸发过程中很容易结垢而堵塞换热管,一般需要2~3个月清洗一次。
5.另外一种热法工艺路线是采用高温烟气旁路蒸发处理高盐废水。对于电厂,抽取空预器前300℃以上烟气,将高盐废水直接干燥成杂盐,最终杂盐混入粉煤灰中实现高盐废水零排放。但高温烟气旁路蒸发对空气预热器及锅炉效率有一定的影响。同时,经旁路烟道蒸发后,浓水中的盐分随烟气中的粉尘一起被除尘器捕捉,最终进入粉煤灰中,影响粉煤灰的资源化利用率,最终又以难以控制的途径进入自然环境。通常情况下,高温旁路烟气蒸发的运行成本在40元/吨水左右。
技术实现要素:6.针对现有技术中高盐废水零排放处理技术普遍存在的预处理成本高和最终产物资源化利用率低两大问题,本实用新型提出了一种优化的高盐废水零排放资源化处理技术,不仅能实现高盐废水的零排放,而且优化了预处理工艺且运行成本低,同时最终产物为酸、碱等化工原料,资源化利用率高。
7.本实用新型提供了一种高盐废水零排放资源化处理设备,所述设备包括:
8.蒸发单元,对高盐废水与脱硫废水的混合原水进行多效强制循环蒸发浓缩处理;
9.加药处理单元,对蒸发单元输出的浓水进行加药沉淀处理;
10.过滤单元,对加药沉淀处理之后的废水进行预过滤处理;
11.后处理单元,将预过滤处理之后的废水加工得到资源化产品。
12.根据本实用新型高盐废水零排放资源化处理设备的一个实施例,所述设备还包括设置在蒸发单元上游的预处理单元,所述预处理单元包括预处理箱和与预处理箱并联设置的超越管路。
13.根据本实用新型高盐废水零排放资源化处理设备的一个实施例,所述蒸发单元为多效强制循环蒸发浓缩装置并且包括串联连接的二至四效循环蒸发器,所述蒸发单元的浓水出口与加药处理单元的浓水箱相连。
14.根据本实用新型高盐废水零排放资源化处理设备的一个实施例,所述多效强制循环蒸发浓缩装置中的每一效循环蒸发器包括晶种罐、加热器、分离室和冷凝水罐,所述加热器的上部蒸汽出口与分离室相连且分离室的下部循环水出口通过循环管路和设置在循环管路上的循环泵与加热器的下部循环水入口相连,所述晶种罐通过晶种泵与所述循环管路相连,所述加热器的下部冷凝水出口还与冷凝水罐相连,分离室的浓水出口与加药处理单元的浓水箱相连。
15.根据本实用新型高盐废水零排放资源化处理设备的一个实施例,所述加药处理单元包括浓水箱以及与浓水箱的加药口相连的加药子单元,所述加药子单元中储存有药剂并且设置有计量加料器。
16.根据本实用新型高盐废水零排放资源化处理设备的一个实施例,所述浓水箱包括入水口、出水口、加药口和污泥出口,所述浓水箱的污泥出口与污泥处理系统相连。
17.根据本实用新型高盐废水零排放资源化处理设备的一个实施例,所述后处理单元为蒸发结晶系统,所述预过滤处理之后的废水进入所述蒸发结晶系统后处理得到nacl结晶盐。
18.根据本实用新型高盐废水零排放资源化处理设备的一个实施例,所述后处理单元包括串联设置的超滤系统和ed双极膜电渗析系统,所述预过滤处理之后的废水依次进入超滤系统和ed双极膜电渗析系统后处理得到hcl溶液及naoh溶液。
19.与常规方案相比,本实用新型针对高盐废水处理,提供一种优化的高盐废水零排放资源化处理设备,真正实现高盐废水零排放,实现了废物的再利用,运行成本低,产品经济性好,整体资源化零排放的运行成本在20~50元/吨水,同时投资成本也将降低20~40%。
附图说明
20.图1示出了根据本实用新型一个示例性实施例的高盐废水零排放资源化处理设备的结构示意图。
21.图2示出了根据本实用新型另一个示例性实施例的高盐废水零排放资源化处理设备的结构示意图。
22.附图标记说明:
[0023]1‑
脱硫废水、2
‑
高盐废水、3
‑
预处理箱、31
‑
超越管路、4
‑
蒸发单元、41
‑
分离室、42
‑
加热器、43
‑
循环泵、44
‑
冷凝水罐、45
‑
晶种罐、5
‑
浓水箱、51
‑
加药子单元、52
‑
污泥处理系统、6
‑
过滤单元、7
‑
超滤系统、8
‑
ed双极膜电渗析系统、81
‑
hcl及naoh溶液、9
‑
蒸发结晶系统、91
‑
nacl结晶盐。
具体实施方式
[0024]
本说明书中公开的所有特征,或公开的所有方法或过程中的步骤,除了互相排斥的特征和/或步骤以外,均可以以任何方式组合。
[0025]
本说明书中公开的任一特征,除非特别叙述,均可被其他等效或具有类似目的的替代特征加以替换。即,除非特别叙述,每个特征只是一系列等效或类似特征中的一个例子而已。
[0026]
下面先对本实用新型的高盐废水零排放资源化处理设备的设计思路进行详细说明。
[0027]
本实用新型的整体工艺流程为高盐废水根据需要经过简单预处理控制悬浮物后,进入晶种法多效蒸发系统进行浓缩,浓缩后的浓水经过沉淀软化及药剂处理后成为以nacl为主的混盐溶液,之后采用蒸发结晶系统产生nacl结晶盐或者采用ed双极膜系统转化为hcl溶液及naoh溶液,基于该工艺流程本实用新型提供了相应的资源化处理设备。
[0028]
图1示出了根据本实用新型一个示例性实施例的高盐废水零排放资源化处理设备的结构示意图,图2示出了根据本实用新型另一个示例性实施例的高盐废水零排放资源化处理设备的结构示意图。
[0029]
如图1和图2所示,根据本实用新型的示例性实施例,所述高盐废水零排放资源化处理设备包括蒸发单元4、加药处理单元、过滤单元6和后处理单元,依次对废水进行相应的处理。
[0030]
具体地,蒸发单元4对高盐废水与脱硫废水的混合原水进行多效强制循环蒸发浓缩处理。优选地,设备还包括设置在蒸发单元4上游的预处理单元,预处理单元包括预处理箱3和与预处理箱3并联设置的超越管路31。
[0031]
其中,脱硫废水1与其他高盐废水2汇合后,可以经预处理单元后再进入蒸发单元4进行蒸发浓缩。本实用新型的预处理单元可以采用简单混凝沉淀的方法对废水进行预处理以去除大部分悬浮物,当混合后的混合原水悬浮物含量较低时,也可以不进行预处理箱的处理而直接经由超越管路31进入蒸发单元4中。
[0032]
本实用新型的蒸发单元4为多效强制循环蒸发浓缩装置并且包括串联连接的二至四效循环蒸发器,蒸发单元4的浓水出口与加药处理单元的浓水箱5相连。具体地,本实用新型的蒸发单元采用晶种法蒸发,在蒸发过程中通过晶种防止系统结垢,其效数可以根据具体水量及水质确定。
[0033]
多效强制循环蒸发浓缩装置中的每一效循环蒸发器包括晶种罐45、加热器42、分离室41和冷凝水罐44,加热器42的上部蒸汽出口与分离室41相连且分离室41的下部循环水出口通过循环管路和设置在循环管路上的循环泵43与加热器42的下部循环水入口相连,晶种45罐通过晶种泵与循环管路相连,加热器42的下部冷凝水出口还与冷凝水罐44相连,分离室41的浓水出口与加药处理单元的浓水箱5相连。
[0034]
蒸发单元4为强制循环蒸发形式,混合原水在循环过程中经加热器42加热后进入分离室41闪蒸,闪蒸得到的二次蒸汽进入下一效加热器继续加热废水,从而将二次蒸汽的热量重复利用。加热器中的蒸汽冷凝后进入冷凝水罐44,闪蒸后的浓水经循环泵43继续循环蒸发,分离室中浓水浓度达到设定值后,经由出料泵送至浓水箱5。在系统启动时,晶种罐45中的晶种经晶种泵送至循环管路,末效分离室排出的二次蒸汽则通过冷凝器凝结成蒸馏
水。整个蒸发单元优选地在微负压的状态下运行,通过真空泵维持系统真空度。
[0035]
加药处理单元则对蒸发单元输出的浓水进行加药沉淀处理。具体地,加药处理单元包括浓水箱5以及与浓水箱5的加药口相连的加药子单元,加药子单元中储存有药剂并且设置有计量加料器。其中,浓水箱5还包括入水口、出水口、加药口和污泥出口,浓水箱5的污泥出口与污泥处理系统52相连,则浓水箱5产生的污泥可以由污泥处理系统52处理。
[0036]
多效蒸发产生的浓水进入浓水箱5后,通过加药子单元51去除浓水中的硬度、悬浮物、硫酸根等杂质。加药子单元51依次向浓水箱5中的浓水中加入石灰、na2co3、氯化钡、pam等药剂,由于采用多效蒸发后原水被成倍浓缩,原水中的硫酸钙含量成倍增加,超过其饱和溶解度后析出为硫酸钙晶体。由于硫酸钙溶解度较低,在浓缩过程中大部分将析出成晶体,浓水中仅剩可溶部分的钙离子与硫酸根。由于浓水量相对原水量将成倍减少,则处理浓水中的钙离子及硫酸根所需药剂耗量相比原水处理也将成倍降低,整体软化、沉淀加药量将成倍的减少,将大幅度降低系统加药成本。
[0037]
本实用新型的过滤单元对加药沉淀处理之后的废水进行预过滤处理,通过预过滤处理之后便于后续处理得到资源化产品。
[0038]
具体地,通过后处理单元将预过滤处理之后的废水加工得到资源化产品。如图2所示,后处理单元可以为蒸发结晶系统9,预过滤处理之后的废水进入蒸发结晶系统9后处理得到nacl结晶盐91。如图1所示,后处理单元还可以包括串联设置的超滤系统7和ed双极膜电渗析系统8,预过滤处理之后的废水依次进入超滤系统7过滤去除悬浮物及胶体等杂质后并在ed双极膜电渗析系统8中处理得到hcl溶液及naoh溶液81。上述过滤单元、超滤系统7和ed双极膜电渗析系统8等均可以采用现有技术中已有结构的相应产品。
[0039]
本实用新型采用的此技术路线相对于电厂减少了传统三联箱系统,对于其他高盐废水而言减少了大规模化学软化系统。整体系统简单,解决了目前其他高盐废水处理技术普遍存在的运行成本高、杂盐无法处理、系统容易结垢等诸多问题,主要特点如下:
[0040]
1)可省去电厂传统三联箱,在蒸发浓缩系统后端析出沉淀后再进行浓水软化,节省投资成本,运行成本也大大降低。
[0041]
2)以晶种法蒸发技术实现废水浓缩,避免系统结垢,同时避免了原水化学软化系统,减少系统投资及运行成本。
[0042]
3)采用先浓缩,后加药软化的处理方式,浓缩后水量成倍降低,从而在很大程度节省了加药系统的投资成本及运行费用。
[0043]
4)通过药剂对废水进行提纯,针对目前高盐废水普遍存在的氯离子含量高,硫酸根含量低的特点,采用氯化钡将硫酸根去除,将废水转化为纯度较高的nacl溶液。
[0044]
5)采用双极膜电渗析技术,将浓缩后高浓度nacl溶液转化为hcl及naoh溶液,不仅解决了废水杂盐的处理问题,同时制备出的hcl溶液及naoh溶液为化工原料,既可用于本系统加药处理,同时其资源化利用及销售的经济性也比较好。
[0045]
下面结合具体实施例对本实用新型作进一步说明。
[0046]
本实施例中脱硫废水1与其他高盐废水2汇合后的混合原水进水总量为30t/h,硬度为3000mg/l,经预处理单元预处理后的悬浮物控制在500mg/l以下,再进入蒸发单元4(如原水中悬浮物含量较低,可直接通过超越管路31进入蒸发单元4进行蒸发浓缩)。其中,预处理为简单混凝沉淀以去除大部分悬浮物,蒸发单元4采用强制循环蒸发形式并且采用晶种
法蒸发,在蒸发过程中通过晶种防止系统结垢。蒸发单元4的效数根据具体水量及水质确定,本实施例中确定为三效。
[0047]
蒸发单元4为强制循环蒸发形式,废水在循环过程中经加热器42加热后进入分离室41闪蒸,闪蒸得到的二次蒸汽进入下一效加热器继续加热废水,从而将二次蒸汽的热量重复利用。加热器中蒸汽冷凝后进入蒸汽冷凝水罐44。闪蒸后的浓水经循环泵43继续循环蒸发,分离室中浓水浓度达到设定值后,经由出料泵送至浓水箱5。在系统启动时,晶种罐45中的晶种经晶种泵送至循环管路并维持系统合适的晶种量,废水中蒸发结晶产生的caso4优先在晶种上生长,避免换热管及系统结垢的同时,降低了浓水上清液的硬度。同时,强制循环系统管路流速控制在2~3m/s,进一步避免换热管壁面结垢。原水在多效蒸发系统中将浓缩5~10倍。末效分离室排出的二次蒸汽通过冷凝器凝结成蒸馏水。蒸发系统在微负压的状态下运行,通过真空泵维持系统真空度。
[0048]
多效蒸发产生的浓水进入浓水箱5后,通过加药子单元51加入药剂去除浓水中的硬度、悬浮物、硫酸根等杂质。加药子单元51中依次采用石灰、na2co3、氯化钡、pam等药剂,由于采用多效蒸发后原水浓缩5~10倍,原水中的硫酸钙含量成倍增加,超过其饱和溶解度后析出为硫酸钙晶体。由于硫酸钙溶解度较低,在浓缩过程中大部分将析出成晶体,浓水中仅剩可溶部分的钙离子与硫酸根。由于浓水量仅为原水量的0.2~0.1倍,则处理浓水中的钙离子及硫酸根所需药剂耗量相比原水处理也将成倍降低,整体软化、沉淀加药量将成倍的减少,将大幅度降低系统加药成本。澄清出的上清液为nacl为主的混盐溶液,nacl纯度90%以上。浓水箱5产生的污泥则由污泥处理系统52处理。
[0049]
废水经浓水箱5处理后溶液中主要成分为nacl,经过过滤单元6过滤以后进入超滤系统7进行过滤去除悬浮物及胶体等杂质然后出水进入ed双极膜电渗析系统8,将废水最终转化为产品81,产品81为浓度5~20%的酸碱溶液。或者经过过滤单元6以后进入蒸发结晶系统9,结晶出产品盐91,产品91为nacl结晶盐,纯度可达到工业二级盐标准。
[0050]
本实用新型并不局限于前述的具体实施方式。本实用新型扩展到任何在本说明书中披露的新特征或任何新的组合,以及披露的任一新的方法或过程的步骤或任何新的组合。