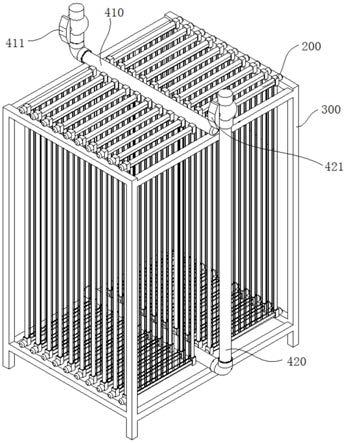
1.本实用新型涉及污水处理设备,特别是涉及一种生物膜反应器及其单元。
背景技术:2.随着中国城镇化和工业化程度的不断提高,用水量日益增加,产生的污水量也随之增加。
3.传统生化工艺,污水通过在厌氧池、缺氧池、好氧池中停留反应一定时间后,再进行后端处理,如图1所示,该方式主要的问题和限制在于,处理效果不理想,所需场地较大,然而现今大部分污水处理生化均采用该方式,面对排放标准的提升,传统工艺的劣势暴露无遗。
[0004]“提质增效”已成为污水处理的新趋势和新命题,运营者们迫在眉睫,急需寻求一种具有革新性的污水处理解决方案。
技术实现要素:[0005]
基于此,有必要针对上述问题,提供一种生物膜反应器及其单元,采用该生物膜反应单元组成的生物膜反应器,能够高效处理污水,并与传统方法相比,可减小缺氧池的大小,降低建造处理成本。
[0006]
一种生物膜反应单元,包括:
[0007]
内供氧中空透气复合膜管,包括透气膜管及覆盖于所述透气膜管外表面的纤维层,所述透气膜管由非生物降解材料制成,其上设有均匀的微孔,所述微孔的孔径为0.01
‑
30μm;所述纤维层由涤纶树脂、高密度聚乙烯中的至少一种制成,该纤维层的厚度为0.1
‑
2.6mm,该纤维层上具有孔隙结构;
[0008]
组合管装配件,包括两个倒胶件和两个连接件,若干所述内供氧中空透气复合膜管两端分别固定于两个倒胶件中,且所述内供氧中空透气复合膜管内腔开口于所述倒胶件表面,所述连接件包括壳体,所述壳体与所述倒胶件固定连接,并包覆所述倒胶件上的内供氧中空透气复合膜管内腔开口,所述壳体内设有通气腔,所述通气腔与所述内供氧中空透气复合膜管内腔连通,所述通气腔在所述壳体表面设有入气口和/或出气口;以及
[0009]
支撑管,该支撑管两端分别与两个所述连接件固定安装。
[0010]
在其中一个实施例中,所述倒胶件为条状,所述内供氧中空透气复合膜管两根一组,沿所述倒胶件长度方向均匀排列。
[0011]
在其中一个实施例中,所述支撑管为两条,分别设置于所述连接件两端。
[0012]
在其中一个实施例中,所述透气膜管的内径为0.1
‑
3mm,外径为0.3
‑
5mm。
[0013]
在其中一个实施例中,所述纤维层由线状材料在所述内管表面缠绕编织制得;或所述纤维层通过将薄膜材料缠绕在所述内管后烧结制得;或所述纤维层通过将涂覆材料涂覆于在所述内管外表面,冷却后制成。
[0014]
例如,通过编织法制备纤维层的具体步骤如下:将高密度聚乙烯和/或涤纶树脂的
线状材料通过编织机在所述透气膜管表面缠绕编织0.1
‑
2.6mm厚度的材料,即得纤维层;可以理解的,可以根据具体的工况要求,通过编织机调整编织的厚度及密度,使其表面保留需要的缝隙,可供后续生物膜反应器使用。
[0015]
通过烧结法制备纤维层的具体步骤如下:将带有微孔的聚四氟乙烯薄膜缠绕在所述内管上,加热到预定温度,使聚四氟乙烯薄膜与内管烧结成一体,即得纤维层。
[0016]
通过涂覆法制备纤维层的具体步骤如下:将涂覆材料制备为液态,以涂覆机涂覆于所述内管外表面,冷却后,即得纤维层。涂覆法中,由于材料本身存在间隙,待冷却后其表面可供气体、液体正常通过。
[0017]
本发明还公开了一种生物膜反应器,包括若干上述的生物膜反应单元。
[0018]
在其中一个实施例中,还包括框架、上气管、下气管和气源,若干所述生物膜反应单元放置于所述框架中固定,所述上气管与所述生物膜反应单元的上连接件的入气口或出气口连通,所述下气管与所述生物膜反应单元的下连接件的出气口或入气口连通,所述气源与所述上气管或下气管连通。
[0019]
在其中一个实施例中,该生物膜反应器还包括上控制阀和下控制阀,所述上控制阀设于所述上气管上,用于控制上气管流通气量;所述下控制阀设于所述下气管上,用于控制下气管流通气量。
[0020]
在其中一个实施例中,所述生物膜反应单元为20帘,分两组排列于所述上气管和下气管两侧。
[0021]
与现有技术相比,本实用新型具有以下有益效果:
[0022]
本发明的一种生物膜反应单元及包括该反应单元制成的生物膜反应器,使用时放置于处理水池中,从一端往内供氧中空透气复合膜管内供给空气或氧气,一方面向复合膜管外包覆的纤维层上生长的生物膜扩散供氧,另一方面空气或氧气能够从复合膜管孔中经过,在水中形成微小气泡从而向活性污泥供氧。通过加工过程中控制膜管孔的大小,从而控制膜管使用过程扩散供氧或产生气泡的大小与供氧及阻力。
[0023]
由于经内供氧中空透气复合膜管内的空气或氧气可直接向复合膜管外包覆纤维层上生长的生物膜扩散供氧能够高效提高氧的利用效率,并且利用复合膜管的的供氧量,在纤维层上同时生长缺氧菌、好氧菌和/或硝化菌等,起到同时硝化反硝化脱氮作用。
[0024]
在内供氧中空透气复合膜管内的空气或氧气达到一定压力时,空气或氧气能够从复合膜管孔中经过在水中形成微小气泡,产生的气泡微小且均匀,具有巨大的表面积,在水中停留时间长,且能够与水体充分接触融合,大大提高气水供氧速率和氧的利用率,能够大幅降低能耗。
附图说明
[0025]
图1为背景技术中传统生化工艺示意图;
[0026]
图2为实施例1中传氧生物膜反应单元结构示意图;
[0027]
图3为实施例1中传氧生物膜反应单元的组装方式示意图;
[0028]
图4为实施例1中透气膜管示意图;
[0029]
图5为实施例1中制备得到的内供氧中空透气复合膜管示意图;
[0030]
图6为实施例2中生物膜反应器结构示意图;
[0031]
图7为实施例3中对污水进行好氧处理示意图;
[0032]
图8为实施例3中对污水进行脱氮处理示意图;
[0033]
图9为实施例3中对污水进行深度脱氮处理示意图;
[0034]
图10为实施例3中对污水进行好氧除磷处理示意图;
[0035]
图11为实施例3中对污水进行反硝化除磷脱氮处理示意图;
[0036]
图12为实施例3中对污水进行除磷脱氮处理示意图;
[0037]
其中:100.内供氧中空透气复合膜管;110.透气膜管;111.微孔;200.传氧生物膜反应单元;210.倒胶件;220.连接件;230.支撑管;300.框架;410.上气管;411.上控制阀;420.下气管;421.下控制阀。
具体实施方式
[0038]
为了便于理解本实用新型,下面将参照相关附图对本实用新型进行更全面的描述。附图中给出了本实用新型的较佳实施例。但是,本实用新型可以以许多不同的形式来实现,并不限于本文所描述的实施例。相反地,提供这些实施例的目的是使对本实用新型的公开内容的理解更加透彻全面。
[0039]
需要说明的是,当元件被称为“固定于”另一个元件,它可以直接在另一个元件上或者也可以存在居中的元件。当一个元件被认为是“连通”另一个元件,它可以是直接连通到另一个元件或者可能同时存在居中元件。
[0040]
除非另有定义,本文所使用的所有的技术和科学术语与属于本实用新型的技术领域的技术人员通常理解的含义相同。本文中在本实用新型的说明书中所使用的术语只是为了描述具体的实施例的目的,不是旨在于限制本实用新型。本文所使用的术语“和/或”包括一个或多个相关的所列项目的任意的和所有的组合。
[0041]
实施例1
[0042]
一种生物膜反应单元,如图2所示,包括:内供氧中空透气复合膜管100、组合管装配件和支撑管230。
[0043]
所述内供氧中空透气复合膜管包括透气膜管110及覆盖于所述透气膜管外表面的纤维层,所述透气膜管由非生物降解材料制成,其上设有均匀的微孔111,所述微孔的孔径为 0.01
‑
30μm;所述纤维层由涤纶树脂、高密度聚乙烯中的至少一种制成,该纤维层的厚度为 0.1
‑
2.6mm,该纤维层上具有孔隙结构。
[0044]
所述组合管装配件包括两个倒胶件210和两个连接件220,若干所述内供氧中空透气复合膜管两端分别固定于两个倒胶件中,且所述内供氧中空透气复合膜管内腔开口于所述倒胶件表面;在本实施例中,所述倒胶件为条状,所述内供氧中空透气复合膜管两根一组,沿所述倒胶件长度方向均匀排列。所述连接件包括壳体,所述壳体与所述倒胶件固定连接,并包覆所述倒胶件上的内供氧中空透气复合膜管内腔开口,所述壳体内设有通气腔,所述通气腔与所述内供氧中空透气复合膜管内腔连通,所述通气腔在所述壳体表面设有入气口和/或出气口;
[0045]
所述支撑管两端分别与两个所述连接件固定安装。本实施例中,所述支撑管为两条,分别设置于所述连接件两端。
[0046]
上述传氧生物膜反应单元的组装方式如下:
[0047]
将内供氧中空透气复合膜管两端分别均匀分布后放入两个倒胶件中,倒入环氧树脂和固化剂混合液,待完全凝固后,切除顶部壳体,露出组合管内孔,如图3中a图所示,最后将倒胶件与连接件粘连即可,如图3中b图所示。
[0048]
上述内供氧中空透气复合膜管通过以下方法制备得到:
[0049]
1、改性聚四氟乙烯的制备。
[0050]
在聚四氟乙烯原料中加入5wt%的二氧化硅和5wt%的二氧化钛作为增强剂,可降低膜管的原料成本,同时制成后大幅提高膜管的强度,从而达到生物膜反应器的使用要求。
[0051]
2、冷挤压。
[0052]
向改性聚四氟乙烯原料加入粘合剂(10wt%的白矿油),在常温(20
‑
30℃)环境中(温度影响挤出材料的密度),利用高压从冷挤压成型机上将混合原料从挤压口中高压挤出,挤压口可通过更换或加工,使挤出内径为φ0.5
‑
φ4mm,外径为φ1.5
‑
φ5mm的管材,由于高压和常温作用,挤出透气膜管材料密度极高,此时管材上没有微孔。
[0053]
3、热拉伸。
[0054]
挤压出的高密度成型透气膜管通过加热机预热,绕过转速不同的两个传动轮,后传动轮转速为前传动轮的1.5
‑
3倍,从而将高密度的透气膜管拉伸出均匀微孔111,通过控制前后传动轮的倍速可以调整拉伸微孔径的大小,其孔径可控制范围为0.01
‑
30μm,得到透气膜管110 (也称细管),如图4所示。
[0055]
4、纤维层制备。
[0056]
编织将线状材料(pp)通过标准编织机在透气膜管表面缠绕0.1
‑
2.6mm厚度的材料,可通过编织机调整编织的厚度及密度,使其表面保留需要的缝隙,可供生物膜反应器使用。
[0057]
在实际工作中,我们发现,在透气膜管上编织时,需要解决透气膜管的材料特性造成的问题,如各种胶水均无法粘连固定的问题。
[0058]
针对该难题,使用的解决方法为:将透气膜管泡入酒精和吐温20乳化剂的混合液后拿出,表面所残留的混合剂渗透于透气膜管表面上,提高透气膜管摩擦系数,此时即可在编织机上进行编织工作,缠绕一层线状材料即可。
[0059]
编织过程中,为了给微生物生存保留空间,一般采用20s纱支、65*78密度进行编织,即20*20/65*78的线状材料编织后,其间隙较大,表面较为粗糙,形成的缝隙给微生物生存提供了空间。
[0060]
本实施例制备得到的内供氧中空透气复合膜管如图5所示。
[0061]
实施例2
[0062]
一种生物膜反应器,如图6所示,传氧生物膜反应单元200、框架300、上气管410、下气管420、气源、上控制阀411和下控制阀421。
[0063]
若干所述生物膜反应单元放置于所述框架中固定,所述上气管与所述生物膜反应单元的上连接件的入气口或出气口连通,所述下气管与所述生物膜反应单元的下连接件的出气口或入气口连通,所述气源与所述上气管或下气管连通。所述上控制阀设于所述上气管上,用于控制上气管流通气量;所述下控制阀设于所述下气管上,用于控制下气管流通气量。
[0064]
在本实施例中,所述生物膜反应单元为20帘,分两组排列于所述上气管和下气管
两侧。
[0065]
实施例3
[0066]
一种生物膜反应器在在污水处理中的应用,包括以下步骤:
[0067]
一、设备安装。
[0068]
将组装测试完成的实施例2的生物膜反应器放入生化水池(根据需要,可以设置1
‑
3个生化水池),固定。
[0069]
在本实施例中,生物膜反应器占所述生化水池容积的10
‑
75%。
[0070]
二、通气。
[0071]
将上气管、下气管分别连接至上控制阀和下控制阀后,下气管连接至气源。本实施例中,通过调节所述上控制阀和下控制阀的开度,使所述通气腔内的压力稳定。
[0072]
三、水处理。
[0073]
按照不同的处理要求,分别选用不同的水处理方法进行处理。
[0074]
1、好氧处理:采用一个生化水池(第一生化水池)配合二沉池进行处理,如图7所示。
[0075]
1)好氧处理:控制通气腔内供气压力稳定,使所述第一生化水池中溶解氧量>1mg/l;好氧菌在污水中有机物及氧作用下生长附着于所述纤维层,形成生物膜污泥,对污水进行好氧处理;
[0076]
2)活性污泥沉淀:经好氧处理的污水进入二沉池沉淀,部分生物膜污泥脱落后被水携带进入二沉池沉淀,沉淀后上层尾水排放,下层沉淀回流至所述第一生化水池和/或作为剩余污泥排放;
[0077]
2、脱氮处理:采用一个生化水池(第一生化水池)配合二沉池进行处理,如图8所示。
[0078]
1)缺氧处理:控制通气腔内供气压力稳定,使所述第一生化水池中溶解氧量为 0.1
‑
1.0mg/l;好氧菌和硝化菌在污水中有机物及氧作用下生长附着于所述纤维层,所述纤维层内层生长好氧菌及硝化菌,所述纤维层外层生长反硝化菌,形成生物膜污泥,对污水进行脱氮处理;
[0079]
2)活性污泥沉淀:经脱氮处理的污水进入二沉池沉淀,部分生物膜污泥脱落后被水携带进入二沉池沉淀,沉淀后上层尾水排放,下层沉淀回流至所述第一生化水池和/或作为剩余污泥排放。
[0080]
3、深度脱氮处理:采用两个生化水池(第一生化水池和第二生化水池)配合二沉池进行处理,如图9所示。
[0081]
1)缺氧处理:将污水导入所述第一生化水池,控制通气腔内供气压力稳定,使所述第一生化水池中溶解氧量为0.1
‑
0.6mg/l;好氧菌、硝化菌和反硝化菌在污水中有机物及氧作用下生长附着于所述纤维层,所述纤维层内层生长好氧菌及硝化菌,所述纤维层外层生长反硝化菌,形成生物膜污泥,对污水进行深度脱氮处理;
[0082]
2)好氧处理:将经所述第一生化水池处理后的污水导入所述第二生化水池,控制通气腔内供气压力稳定,使所述第二生化水池中溶解氧量大于1.5mg/l;好氧菌在污水中有机物及氧作用下生长附着于所述纤维层,形成生物膜污泥,对污水进行好氧处理;
[0083]
3)活性污泥沉淀:经好氧处理的污水进入二沉池沉淀,部分生物膜污泥脱落后被
水携带进入二沉池沉淀,沉淀后上层尾水排放,下层沉淀回流至所述第一生化水池和/或作为剩余污泥排放;
[0084]
4、好氧除磷处理:采用两个生化水池(第一生化水池和第二生化水池)配合二沉池进行处理,如图10所示。
[0085]
1)厌氧处理:将污水导入所述第一生化水池,使所述第一生化水池中溶解氧量为< 0.2mg/l,并同时进行脉冲配水或设有搅拌系统,使厌氧菌处于悬浮状态,对污水进行厌氧处理;
[0086]
2)好氧处理:将经所述第一生化水池处理后的污水导入所述第二生化水池,控制通气腔内供气压力稳定,使所述第二生化水池中溶解氧量大于1.5mg/l;好氧菌在污水中有机物及氧作用下生长附着于所述纤维层,形成生物膜污泥,对污水进行好氧处理;
[0087]
3)活性污泥沉淀:经好氧处理的污水进入二沉池沉淀,部分生物膜污泥脱落后被水携带进入二沉池沉淀,沉淀后上层尾水排放,下层沉淀回流至所述第一生化水池和/或作为剩余污泥排放;
[0088]
5、反硝化除磷脱氮处理:采用两个生化水池(第一生化水池和第二生化水池)配合二沉池进行处理,如图11所示。
[0089]
1)厌氧处理:将污水导入所述第一生化水池,使所述第一生化水池中溶解氧量为< 0.2mg/l,并同时进行脉冲配水或设有搅拌系统,使厌氧菌处于悬浮状态,对污水进行厌氧处理;
[0090]
2)缺氧处理:将经所述第一生化水池处理后的污水导入所述第二生化水池,控制通气腔内供气压力稳定,使所述第二生化水池中溶解氧量为0.1
‑
0.6mg/l;好氧菌、硝化菌和反硝化菌在污水中有机物及氧作用下生长附着于所述纤维层,所述纤维层内层生长好氧菌及硝化菌,所述纤维层外层生长反硝化菌,形成生物膜污泥,对污水进行缺氧处理;
[0091]
3)活性污泥沉淀:经缺氧处理的污水进入二沉池沉淀,部分生物膜污泥脱落后被水携带进入二沉池沉淀,沉淀后上层尾水排放,下层沉淀回流至所述第一生化水池和/或作为剩余污泥排放。
[0092]
6、除磷脱氮处理:采用三个生化水池(第一生化水池、第二生化水池和第三生化水池) 配合二沉池进行处理,如图12所示。
[0093]
1)厌氧处理:将污水导入所述第一生化水池,使所述第一生化水池中溶解氧量为< 0.2mg/l,并同时进行脉冲配水或设有搅拌系统,使厌氧菌处于悬浮状态,对污水进行厌氧处理;
[0094]
2)缺氧处理:将经所述第一生化水池处理后的污水导入所述第二生化水池,控制通气腔内供气压力稳定,使所述第二生化水池中溶解氧量为0.1
‑
0.6mg/l;好氧菌、硝化菌和反硝化菌在污水中有机物及氧作用下生长附着于所述纤维层,所述纤维层内层生长好氧菌及硝化菌,所述纤维层外层生长反硝化菌,形成生物膜污泥,对污水进行缺氧处理;
[0095]
3)好氧处理:将经所述第二生化水池处理后的污水导入所述第三生化水池,控制通气腔内供气压力稳定,使所述第三生化水池中溶解氧量大于1.5mg/l;好氧菌在污水中有机物及氧作用下生长附着于所述纤维层,形成生物膜污泥,对污水进行好氧处理;
[0096]
4)活性污泥沉淀:经好氧处理的污水进入二沉池沉淀,部分生物膜污泥脱落后被水携带进入二沉池沉淀,沉淀后上层尾水排放,下层沉淀回流至所述第一生化水池和/或作
为剩余污泥排放。
[0097]
四、清洁:提高所述通气腔中的气压至2
‑
3mpa的清洁气压,将附着于所述纤维层外的污泥冲散脱落。
[0098]
本发明的内供氧中空透气复合膜管,使用时放置于处理水池中,从一端往中空透气膜管内供给空气或氧气,一方面向复合膜管外包覆的纤维层上生长的生物膜扩散供氧,另一方面空气或氧气能够从复合膜管孔中经过,在水中形成微小气泡从而向活性污泥供氧。通过加工过程中控制膜管孔的大小,从而控制膜管使用过程扩散供氧或产生气泡的大小与供氧及阻力。
[0099]
由于经中空透气膜管内的空气或氧气可直接向复合膜管外包覆纤维上生长的生物膜扩散供氧能够高效提高氧的利用效率,并且利用复合膜管外包覆纤维层上生长的生物膜内侧贴近膜管部分由于膜管扩散供氧生长的是好氧菌,生物膜外测贴近水体部分依据中空透气膜管内供给空气或氧气压力的不同可生长缺氧菌,形成内部好氧外部缺氧的生物膜,起到同时硝化反硝化脱氮作用。
[0100]
在中空透气膜管内的空气或氧气达到一定压力时,空气或氧气能够从复合膜管孔中经过在水中形成微小气泡,产生的气泡微小且均匀,具有巨大的表面积,在水中停留时间长,且能够与水体充分接触融合,大大提高气水供氧速率和氧的利用率,能够大幅降低能耗。
[0101]
并且,随着工作时间的加长,15天后附着微生物的表面会逐渐吸附着无用的污泥(不含微生物的死泥),需定期对专用膜管进行反冲清洗,才可使其稳定工作。
[0102]
例如,可定期打入2
‑
3mpa的气体,即控制通气腔内的压力为2
‑
3mpa,将附着在表面的污泥冲散并由于重力作用快速沉淀于水池底部,附着于表面的部分微生物散开后又重新附着于膜管的各个环境内,解决了污泥过度堆积造成反应不充分及表面过重等问题,相比传统附着养菌,该方式为生物膜反应器特有的优势,解决了传统附着养菌一直存在的难题。
[0103]
实施例4
[0104]
一种生物膜反应器采用好氧处理在改造10t/h的污水处理中的应用,包括以下步骤:
[0105]
一、反应器安装
[0106]
将组装测试完成的实施例3的生物膜反应器放入原有好氧生化水池内固定,填充密度约为水池总容积的70%。
[0107]
二、连接。
[0108]
将上气管、下气管分别连接至上控制阀和下控制阀后,下气管连接至气源。本实施例中,通过调节所述上控制阀和下控制阀的开度,使所述通气腔内的压力稳定。
[0109]
三、处理。
[0110]
该方案采用好氧处理的方式,旨在提高生化效率及效果,同时减少其能源损耗,减低处理成本;
[0111]
好氧处理:控制通气腔内供气压力稳定,使所述第一生化水池中溶解氧量>1mg/l;好氧菌在污水中有机物及氧作用下生长附着于所述纤维层,形成生物膜污泥,对污水进行好氧处理;
[0112]
活性污泥沉淀:经好氧处理的污水进入二沉池沉淀,部分生物膜污泥脱落后被水
携带进入二沉池沉淀,沉淀后上层尾水排放,下层沉淀回流至所述第一生化水池和/或作为剩余污泥排放;
[0113]
四、清洁。
[0114]
工作15天后,对反应器进行清洗,提高所述通气腔中的气压至3mpa的清洁气压,将附着于所述纤维层外的污泥冲散脱落,恢复其原有工作效率。
[0115]
五、效果评价。
[0116]
1、好氧菌存活量。
[0117]
传统工艺生化池中各菌种总含量为5000mg/l,采用实施例5的生物膜反应器,各菌种的总含量可达20000mg/l。
[0118]
2、污水处理效率。
[0119]
采用传统工艺,10t/h污水的生化处理,需要分别在40m3厌氧池停留1小时、10m3缺氧池停留1小时、30m3好氧池中停留1小时,共3个小时,才能符合排放标准;
[0120]
相比传统工艺,采用内供氧生物膜反应单元,只需在30m3水池内停留1.5小时即可达到排放标准;时间和空间上均有巨大的优势;
[0121]
3、能耗对比。
[0122]
采用传统工艺,好氧池内气水比为15~20:1,即每m3水需要供入15
‑
20m3气体,采用内供氧生物膜反应单元,可通过控制供氧量,调节气水比至其所需的3~5:1,能耗仅为传统工艺的20
‑
25%。
[0123]
以上所述实施例的各技术特征可以进行任意的组合,为使描述简洁,未对上述实施例中的各个技术特征所有可能的组合都进行描述,然而,只要这些技术特征的组合不存在矛盾,都应当认为是本说明书记载的范围。
[0124]
以上所述实施例仅表达了本实用新型的几种实施方式,其描述较为具体和详细,但并不能因此而理解为对实用新型专利范围的限制。应当指出的是,对于本领域的普通技术人员来说,在不脱离本实用新型构思的前提下,还可以做出若干变形和改进,这些都属于本实用新型的保护范围。因此,本实用新型专利的保护范围应以所附权利要求为准。