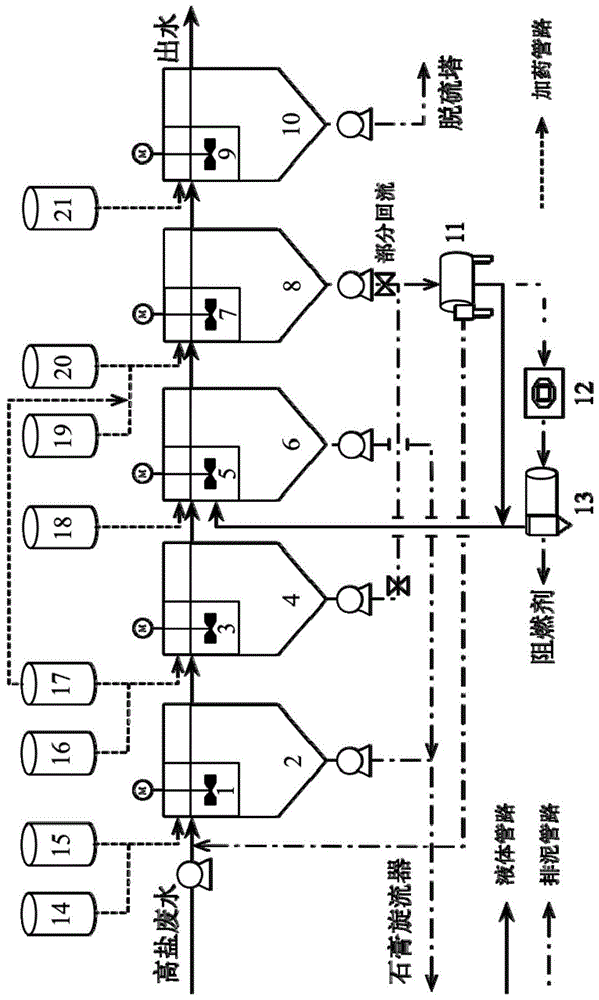
本发明属于环境保护与固废资源化
技术领域:
,涉及一种燃煤电厂脱硫废水的资源化预处理系统与方法。
背景技术:
:脱硫废水作为电厂的末端废水,用水来源复杂,水质水量特征受燃煤、石灰石以及脱硫系统运行等多因素影响,处理难度大。2015年1月,新环保法开始正式施行。随后,国家先后发布《水污染防治行动计划》(又被称为“水十条”)、《火电厂污染防治技术政策》和《火电厂污染防治可行技术指南》逐步加大对各类水体污染的治理力度,鼓励燃煤电厂实现废水零排放。目前,随着膜材料的研发与改进,膜装置的成本下降,膜分离技术在废水处理领域应用越来越广泛,基于膜集成技术和蒸发结晶的脱硫废水零排放工艺也日趋成熟。然而,脱硫废水具有较强的结垢倾向,对于采用膜浓缩和蒸发结晶的零排放工艺而言,ca2+、mg2+及so42-易造成膜污染,导致产水通量下降。对于ca2+、mg2+的软化去除难度不大,但so42-的存在极易在浓缩过程中导致膜系统(如正渗透)或蒸发系统形成永久性硫酸钙垢,降低膜材料的使用寿命。因此,在浓缩前需要对脱硫废水进行软化预处理。目前,在脱硫废水软化预处理工艺中,化学沉淀法的应用最为普遍。该方法通过投加化学药剂使水中需要去除的溶解性物质转化为难溶物质析出,但适用的难溶化合物较少,化学药剂使用量及固废生成量大,这限制了该技术的实际应用。中国专利cn108117224b公开了一种脱硫废水预处理方法,通过化学沉淀法和生物法相结合去除废水中的重金属离子、有机污染物和含氮污染物,处理后废水中总氮浓度低于15mg/l,cod浓度低于60mg/l。但该工艺主要存在两个方面的不足,一是采用化学沉淀法对脱硫废水进行预处理时,仅考虑了重金属的去除,废水中大量的硬度离子仍然存在,因此对于下游的膜法零排放工艺并不适用;二是对于处理过程中产生的化学污泥的处理处置没有给出合理的途径与方法,化学沉淀法带来的药剂使用量及固废生成量大等通病仍未解决。技术实现要素:本发明的目的就是为了提供一种燃煤电厂脱硫废水的资源化预处理系统与方法,在对脱硫废水进行深度软化处理的同时,实现系统污泥的资源化利用,以补偿预处理系统运行成本。本发明的目的可以通过以下技术方案来实现:本发明的技术方案之一提供了一种燃煤电厂脱硫废水的资源化预处理系统,包括沿脱硫废水行进方向依次连接的预沉池、除镁池、预除硫池、深度除硫池和除钙池,其中,所述除镁池和深度除硫池的底部沉淀出口还连接阻燃剂制备机构,所述除钙池的底部沉淀出口还连接外部的脱硫塔。进一步的,所述的预沉池与预除硫池的底部沉淀出口还连接外部的石膏旋流器。进一步的,所述的深度除硫池的底部沉淀出口还返回连接预沉池的入口。进一步的,所述的阻燃剂制备机构还返回连接所述预除硫池。进一步的,所述的阻燃剂制备机构包括沿沉淀物处理方向依次连接的脱水机、洗涤机和烘干机。进一步的,所述的预沉池还连接氧化钙加药器与第一絮凝剂加药器。进一步的,所述的除镁池还连接除镁剂加药器和分散剂加药器。进一步的,所述的预除硫池还连接预除硫剂加药器。进一步的,所述的深度除硫池还连接分散剂加药器、深度除硫剂加药器和第二絮凝剂加药器。进一步的,所述的除钙池还连接除钙剂加药器。进一步的,在预沉池与除镁池之间还设有第一沉淀池。进一步的,在除镁池与预除硫池之间还设有第二沉淀池。进一步的,在预除硫池与深度除硫池之间还设有第三沉淀池。进一步的,在深度除硫池与除钙池之间还设有第四沉淀池。进一步的,在除钙池后方还设有第五沉淀池。本发明的技术方案之二提供了一种燃煤电厂脱硫废水的资源化预处理方法,其采用如上述的资源化预处理系统实施,该资源化预处理方法包括以下步骤:(1)待处理的脱硫废水送入预沉池中,加入氧化钙与第一絮凝剂,沉降分离后,所得出水排入除镁池中,所得沉淀物排出至石膏旋流器;(2)往除镁池中加入除镁剂和分散剂,除镁处理完成后继续沉降分离,所得沉淀物排放至阻燃剂制备机构,所得出水流入预除硫池;(3)往预除硫池中加入预除硫剂进行预除硫处理,得到泥水混合液继续沉降分离,所得沉淀物送入石膏旋流器,所得出水流入深度除硫池;(4)往深度除硫池中加入深度除硫剂,并同时加入第二絮凝剂和分散剂,进行深度除硫处理,接着,继续沉降分离,所得沉淀物部分送入阻燃剂制备机构,所得出水流入除钙池;(5)往除钙池中加入除钙剂进行除钙处理,接着,再沉降分离,所得沉淀物作为脱硫剂送入脱硫塔,所得出水作为下游膜法零排放工艺的进水进行后续处理。进一步的,步骤(1)中,脱硫废水在预沉池中的停留时间为0.5-48h,所述的氧化钙的投加量为50-10000mg/l,所述的第一絮凝剂为铝盐、铁盐或聚丙烯酰胺中的一种或几种,其投加量为0.01-200mg/l。进一步的,步骤(2)中,除镁池的水力停留时间为0.5-49h,所述的除镁剂为氢氧化钾、氢氧化钠、碳酸钠、碳酸氢钠、氧化钙或氢氧化钙中的一种或几种,其投加量为0.5-100g/l,所述的分散剂为十二烷基苯磺酸钠、焦磷酸钠或聚异丁烯多丁二酰亚胺类无灰添加剂中的一种或几种,其投加量为0.01-100mg/gds(即污泥干固体含量。进一步的,步骤(3)中,预除硫池的水力停留时间为0.5-48h,所述的预除硫剂为氧化钙、氢氧化钙、氯化钙、氯酸钙、碳酸氢钙、葡萄糖酸钙、磷酸二氢钙、硝酸钙、硫酸氢钙、亚硫酸氢钙、溴化钙或碘化钙中的一种或几种,其投加量为0.05-50g/l。进一步的,步骤(4)中,深度除硫池的水力停留时间为0.5-48h,所述的深度除硫剂为氧化铝、氢氧化铝、氯化铝或铝酸钠中的一种或几种,其投加量满足除硫池反应结束后剩余的钙离子与深度除硫池中的硫的摩尔比为1-6,添加的铝离子与深度除硫池中所含硫元素的摩尔比为1-4,所述的第二絮凝剂为阳离子、阴离子或非离子型pam、季铵型絮凝剂、聚胺型-低分子量有机絮凝剂中的一种或几种。进一步的,步骤(5)中,除钙池中的水力停留时间为0.5-24h,所述的除钙剂为碳酸钠、碳酸氢钠、碳酸钾或碳酸氢氨中的一种或几种,其投加量为0.05-100g/l。进一步的,步骤(2)和步骤(4)所得沉淀物在阻燃剂制备机构中依次经脱水、洗涤提出和烘干后,得到阻燃剂或协同阻燃剂的原料,制备过程中产生的脱水液、清洗废液和冷凝液回流至预除硫池中继续处理。本发明将脱硫废水零排放预处理工艺各单元所产污泥进行资源化利用,并重点考察氢氧化镁和钙矾石作为协同阻燃剂的使用,在保障后续膜法零排放工艺稳定运行的同时,实现污泥的充分资源化利用,具有显著的经济和环境效益。与现有技术相比,本发明具有以下优点:(1)硬度离子及so42-的高效去除能够减轻后续膜法零排放工艺的运行压力,阻燃剂提纯步骤产生的脱水液和冷凝液回流以保证整个系统无废水和污泥排放,实现真正意义上的零排放。(2)通过污水分步沉淀和污泥分类资源化,最大化污泥减量效果,降低电厂污泥处理处置压力,实现污泥的完全资源化利用。(3)回流部分深度除硫池沉淀物和石灰浆液的加入避免了重金属离子等对后续沉淀物纯度的影响,在实现脱硫废水中硬度离子高效去除的前提下,完成深度递级分盐目标,各单元污泥纯度可达98%以上。(4)固体沉淀物纯度较高,基本不含有杂质,脱硫石膏(caso4)及脱硫剂(caco3)无需额外的处理手段进行提纯,有利于资源化利用。(5)将氢氧化镁及钙矾石进行回收利用,既可分别单独制备阻燃剂,也可成比例掺杂进行制备,分散剂的投加使二者粒径均低于5μm,能够满足国家标准hg/t4531-2013以及hg/t4496-2013的要求。钙矾石作为骨架有利于氢氧化镁在阻燃材料中均匀分散,二者作为协同阻燃剂时效果更优。(6)本发明设计的零排放预处理工艺吨水处理成本较低(24-30元),通过污泥的资源化利用,在节省处理处置成本的前提下,脱硫石膏、脱硫剂以及阻燃剂的资源化可回收成本45-50%,具有显著的社会、经济和环境效益。附图说明图1为本发明的工艺流程图;图2为实施例2中除镁池、预除硫池、深度除硫池和除钙池生成沉淀物的电子扫描显微镜(sem)形貌;图3为实施例2中第四沉淀池中钙矾石沉淀物的ft-ir图谱;图4为实施例2中氢氧化镁以及钙矾石沉淀的粒径及热重分析;图5为实施例4中不同掺比率条件下氢氧化镁和钙矾石沉淀复配制得的协同阻燃剂极限氧指数(loi)对比以及实际阻燃效果对比(针对乙烯-醋酸乙烯共聚物,eva);图中标记说明:1-预沉池,2-第一沉淀池,3-除镁池,4-第二沉淀池,5-预除硫池,6-第三沉淀池,7-深度除硫池,8-第四沉淀池,9-除钙池,10-第五沉淀池,11-脱水机,12-洗涤机,13-烘干机,14-氧化钙加药器,15-第一絮凝剂加药器,16-除镁剂加药器,17-分散剂加药器,18-预除硫剂加药器,19-深度除硫剂加药器,20-第二絮凝剂加药器,21-除钙剂加药器。具体实施方式下面结合附图和具体实施例对本发明进行详细说明。本实施例以本发明技术方案为前提进行实施,给出了详细的实施方式和具体的操作过程,但本发明的保护范围不限于下述的实施例。下面先对本发明的资源化预处理系统进行详细说明。为在对脱硫废水进行深度软化处理的同时,实现系统污泥的资源化利用,本发明提供了一种燃煤电厂脱硫废水的资源化预处理系统,如图1所示,包括沿脱硫废水行进方向依次连接的预沉池1、除镁池3、预除硫池5、深度除硫池7和除钙池9,其中,所述除镁池3和深度除硫池7的底部沉淀出口还连接阻燃剂制备机构,所述除钙池9的底部沉淀出口还连接外部的脱硫塔。在一些实施方式中,所述的预沉池1与预除硫池5的底部沉淀出口还连接外部的石膏旋流器。在一些实施方式中,所述的深度除硫池7的底部沉淀出口还返回连接预沉池1的入口。在一些实施方式中,所述的阻燃剂制备机构还返回连接所述预除硫池5。在一些实施方式中,所述的阻燃剂制备机构包括沿沉淀物处理方向依次连接的脱水机11、洗涤机12和烘干机13。在一些实施方式中,所述的预沉池1还连接氧化钙加药器14与第一絮凝剂加药器15,用于添加第一絮凝剂。在一些实施方式中,所述的除镁池3还连接除镁剂加药器16和分散剂加药器17,分别用于添加除镁剂和分散剂。在一些实施方式中,所述的预除硫池5还连接预除硫剂加药器18,用于添加除硫剂。在一些实施方式中,所述的深度除硫池7还连接分散剂加药器17、深度除硫剂加药器19和第二絮凝剂加药器20,分别用于添加分散剂、深度脱硫剂和第二絮凝剂。在一些实施方式中,所述的除钙池9还连接除钙剂加药器21,用于添加除钙剂。在一些实施方式中,在预沉池1与除镁池3之间还设有第一沉淀池2。在一些实施方式中,在除镁池3与预除硫池5之间还设有第二沉淀池4。在一些实施方式中,在预除硫池5与深度除硫池7之间还设有第三沉淀池6。在一些实施方式中,在深度除硫池7与除钙池9之间还设有第四沉淀池8。在一些实施方式中,在除钙池9后方还设有第五沉淀池10。接着对本发明的资源化预处理方法进行详细说明。本发明的提供的一种燃煤电厂脱硫废水的资源化预处理方法,其采用如上述的资源化预处理系统实施,具体可参见图1所示,该资源化预处理方法包括以下步骤:(1)待处理的脱硫废水送入预沉池1中,加入氧化钙与第一絮凝剂,沉降分离后,所得出水排入除镁池3中,所得沉淀物排出至石膏旋流器;(2)往除镁池3中加入除镁剂和分散剂,除镁处理完成后继续沉降分离,所得沉淀物排放至阻燃剂制备机构,所得出水流入预除硫池5;(3)往预除硫池5中加入预除硫剂进行预除硫处理,得到泥水混合液继续沉降分离,所得沉淀物送入石膏旋流器,所得出水流入深度除硫池7;(4)往深度除硫池7中加入深度除硫剂,并同时加入第二絮凝剂和分散剂,进行深度除硫处理,接着,继续沉降分离,所得沉淀物部分送入阻燃剂制备机构,所得出水流入除钙池9;(5)往除钙池9中加入除钙剂进行除钙处理,接着,再沉降分离,所得沉淀物作为脱硫剂送入脱硫塔,所得出水作为下游膜法零排放工艺的进水进行后续处理。在一些实施方式中,步骤(1)中,脱硫废水在预沉池1中的停留时间为0.5-48h,优选的,所述的氧化钙(其可以以石灰浆液的形式添加)的投加量为50-10000mg/l,所述的第一絮凝剂优选为铝盐、铁盐或聚丙烯酰胺中的一种或几种,其投加量优选为0.01-200mg/l。在一些实施方式中,步骤(2)中,除镁池3的水力停留时间为0.5-49h,沉淀处理的时间为0.5-48h,优选的,所述的除镁剂为氢氧化钾、氢氧化钠、碳酸钠、碳酸氢钠、氧化钙或氢氧化钙中的一种或几种,其投加量优选为0.5-100g/l,所述的分散剂优选为十二烷基苯磺酸钠、焦磷酸钠、聚异丁烯多丁二酰亚胺类无灰添加剂或硬脂酸类分散剂等中的一种或几种,其投加量优选为0.01-100mg/gds(即污泥干固体含量)。在一些实施方式中,步骤(3)中,预除硫池5的水力停留时间优选为0.5-48h,优选的,所述的预除硫剂为氧化钙、氢氧化钙、氯化钙、氯酸钙、碳酸氢钙、葡萄糖酸钙、磷酸二氢钙、硝酸钙、硫酸氢钙、亚硫酸氢钙、溴化钙或碘化钙中的一种或几种,其投加量优选为0.05-50g/l。在一些实施方式中,步骤(4)中,深度除硫池7的水力停留时间为0.5-48h,优选的,所述的深度除硫剂为氧化铝、氢氧化铝、氯化铝或铝酸钠中的一种或几种,其投加量优选满足除硫池反应结束后剩余的钙离子与深度除硫池7中的硫的摩尔比为1-6,添加的铝离子与深度除硫池7中所含硫元素的摩尔比优选为1-4,所述的第二絮凝剂优选为阳离子、阴离子或非离子型pam、季铵型絮凝剂、聚胺型-低分子量有机絮凝剂中的一种或几种,所用分散剂与步骤(2)中相同。在一些实施方式中,步骤(5)中,除钙池9中的水力停留时间为0.5-24h,所述的除钙剂优选为碳酸钠、碳酸氢钠、碳酸钾或碳酸氢氨等中的一种或几种,其投加量优选为0.05-100g/l。在一些实施方式中,步骤(2)和步骤(4)所得沉淀物在阻燃剂制备机构中依次经脱水、洗涤提出和烘干后,得到阻燃剂或协同阻燃剂的原料,制备过程中产生的脱水液、清洗废液和冷凝液回流至预除硫池5中继续处理。优选的,沉淀物经分散处理后,得到沉淀物混合液进入脱水机11,脱水后的沉淀物采用去离子水进行冲洗,再以液固比5-30进行浸泡,浸泡后的沉淀物颗粒再于30-100℃下烘干1-48h,重复上述操作1-5次,即可以得到。上述步骤(2)和步骤(4)所得沉淀物经阻燃剂制备机构得到的粉末可以单独作为阻燃剂使用,也可以将两者以质量比0.1-100:1混合均匀,复配协同使用以提高阻燃效果。本发明系统上各部分的反应原理如下:1)预沉阶段:首先对脱硫废水中固体悬浮物进行去除,少量石灰和助凝剂的投加能够起到絮凝与调节ph的作用,使部分重金属离子形成氢氧化物沉淀去除并回流至旋流器,保证后续得到的固体沉淀物纯度,满足回用要求,反应式见(1)。am++m(oh)-→a(oh)m↓(1)其中,am+为脱硫废水中重金属离子。2)除镁阶段:除镁剂的投加能够将脱硫废水中镁离子形成氢氧化镁沉淀去除,分散剂的投加或其他物理分散方法的使用,能够使氢氧化镁颗粒满足阻燃剂标准。反应式见(2)。mg2++2oh-→mg(oh)2↓(2)3)预除硫阶段:通过投加价格较低的预除硫剂,尽可能去除废水中的硫酸根离子。反应式见(3)。4)深度除硫阶段:通过投加深度除硫剂,使废水中剩余的硫酸根以钙矾石形式沉淀,分散剂的投加能够使钙矾石颗粒满足阻燃剂标准。反应式见(4)。5)除钙阶段:由于预除硫剂含钙离子,使废水中硬度略有提升,因此除钙剂的投加能够高效去除残留的钙离子。反应式见(5)。其中,钙矾石中的结晶水含量会随着反应条件改变而改变。另外,若预沉池1中第一絮凝剂投加量小于本发明限定范围,会导致絮凝效果不明显,使沉降性能与脱水性能较差。若预沉池1中第一絮凝剂投加量大于本发明限定范围,会发生胶体保护作用,导致沉淀物颗粒絮凝效果也较差,污泥混合液粘度过高脱水性能变差。若除镁剂投加量小于本发明限定范围,会导致镁离子去除不彻底,后段沉淀物中杂质含量高。若预除硫剂投加量小于本发明限定范围,会导致剩余硫酸根浓度过高。若深度除硫剂投加量过大则会导致沉淀物中杂质含量过高,纯度降低,且处理成本提高。若深度除硫剂投加量小于本发明限定范围,会导致硫酸根去除不彻底。以上各实施方式可以任一单独实施,也可以任意两两组合或更多的组合实施。为了更清楚的说明本发明实例或现有技术中的实施方法,下面对实施例与脱硫废水除硫沉淀物的阻燃性能进行简单介绍,下面描述中的实施例与附图仅是本发明的一些实施例,对于本领域普通技术人员来讲,在不付出创造性劳动型的前提下,还可以根据这些附图获得其他实施例或附图。实施例1:一种利用脱硫废水零排放预处理系统污泥制备阻燃剂的方法,其预处理流程如附图1所示,包括依次连接的预沉池1、第一沉淀池2、除镁池3、第二沉淀池4、预除硫池5、第三沉淀池6、深度除硫池7、第四沉淀池8、除钙池9、第五沉淀池10。预沉池1还分别与氧化钙加药器14和第一絮凝剂加药器15连接,除镁池3还分别与除镁剂加药器16和分散剂加药器17连接,预除硫池5还与预除硫剂加药器18连接,深度除硫池7还分别与深度除硫剂加药器19、第二絮凝剂加药器20和分散剂加药器17连接,除钙池9还与除钙剂加药器21连接。具体步骤如下:(1)待处理的脱硫废水进入预沉池1,通过氧化钙加药器14和第一絮凝剂加药器15分别将石灰浆液(即氧化钙)和第一絮凝剂投加入预沉池1,通过深度除硫池7回流的沉淀物以及石灰浆液的加入实现重金属离子吸附和沉降,并实现悬浮物的去除。经第一沉淀池2沉降分离后,沉淀物经污泥输送泵回流至石膏旋流器。(2)第一沉淀池2出水进入除镁池3,通过除镁剂加药器16投加除镁剂去除脱硫废水中的镁离子。通过分散剂加药器17投加分散剂,经第二沉淀池4沉降分离后,产生的高纯度氢氧化镁经脱水、提纯及烘干步骤作为阻燃剂原料进行回收。(3)第二沉淀池4出水进入预除硫池5,通过预除硫剂加药器18投加预除硫剂,实现硫酸根的初步去除。泥水混合液经第三沉淀池6沉降分离后,产生的硫酸钙沉淀脱水后作为脱硫石膏进行回用。(4)第三沉淀池6出水进入深度除硫池7,通过深度除硫剂加药器19投加深度除硫剂,实现硫酸根的进一步去除,由分散剂加药器17投加分散剂,第二絮凝剂加药器20投加第二絮凝剂,经第四沉淀池8沉降分离后,部分钙矾石沉淀物回流至预沉池1吸附重金属离子,剩余的钙矾石沉淀经脱水、提纯及烘干步骤作为阻燃剂原料进行回收。(5)第四沉淀池8出水进入除钙池9,通过除钙剂加药器21投加除钙剂,实现残留钙离子的深度去除。泥水混合液经由第五沉淀池10沉降分离后,产生的碳酸钙沉淀脱水后作为脱硫剂回用于脱硫塔。第五沉淀池10出水作为后续膜法零排放工艺进水进行后续处理。(6)除镁池3产生的粗氢氧化镁以及深度除硫池7产生的粗钙矾石,经污泥脱水机11脱水后排入洗涤机12,通过反复的冲洗和浸泡实现二者的高效提纯,最终由烘干机13进行烘干。提纯过程产生的污泥脱水液、清洗废液以及冷凝液回流至预除硫池5。通过控制排泥阀能够实现氢氧化镁阻燃剂和合成水滑石阻燃剂的复配生产或单独生产。实施例2:在实施例1的资源化处理工艺的基础上,本实施例的操作工艺参数如下:待处理脱硫废水中固体悬浮物浓度为5g/l,硫酸根浓度为5500mg/l,镁离子浓度为2500mg/l,ph为6.88。处理后需达到ca2+<20mg/l,mg2+<20mg/l,so42-<50mg/l,分别单独制备的氢氧化镁和合成水滑石阻燃剂需分别满足hg/t4531-2013和hg/t4496-2013的要求。本实施例中,预沉池1中所用氧化钙投加量为0.25g/l,其水力停留时间为24h,第一絮凝剂选用阴离子聚丙烯酰胺,分子量大于106da,投加量为0.5mg/l,深度除硫池7的沉淀物回流比为10%。经第一沉淀池2沉降分离后,废水中悬浮物被高效去除,出水浊度为86ntu,上清液排入除镁池3。按照《固体废物浸出毒性浸出方法硫酸硝酸法》对第一沉淀池2污泥(hj/t299-2007)进行重金属离子测定,结果显示仅锌和汞离子有检出,分别为0.017mg/l和0.00016mg/l,其他重金属离子均未检出(表1)。因此,第一沉淀池2产生的污泥属于普通固废,可回流至石膏旋流器。表1第一沉淀池2污泥重金属含量分析第一沉淀池2出水进入除镁池3,其水力停留时间为24h,所用除镁剂为氢氧化钠,投加量为8g/l。使用十二烷基苯磺酸钠作为分散剂,其投加量为1mg/gds。经第二沉淀池4沉降分离后,废水中mg2+浓度仅为2.8mmol/l,上清液排入预除硫池5。根据x射线荧光光谱分析(表3)可知,第二沉淀池4产生的污泥不含重金属,沉淀物中氢氧化镁质量分数为98.8%,故可作为氢氧化镁阻燃剂原料进行回收。第二沉淀池4出水进入预除硫池5,其水力停留时间为24h,所用预除硫剂为氧化钙,投加量为5.5g/l。经第三沉淀池6沉降分离后,so42-浓度为14mmol/l,上清液排入深度除硫池7。根据化学平衡计算可知,第三沉淀池6产生的污泥中硫酸钙、氢氧化钙和氢氧化镁质量分数分别为82.9%,15.6%和1.4%,符合《火力发电厂石灰石-石膏湿法烟气脱硫系统设计规程》(dl/t5196-2016)的要求,可作为脱硫石膏回流至旋流器。第三沉淀池6进入深度除硫池7,其水力停留时间为24h,所用深度除硫剂为偏铝酸钠,按al/s比为2.5进行投加,分散剂种类及投加量与除镁池3所用相同,所用絮凝剂种类与预沉池1相同,投加量为2.5mg/gds。经第四沉淀池8沉降分离后,so42-浓度为0.4mmol/l,上清液排入除钙池9。根据x射线荧光光谱分析(表3)可知,第四沉淀池8产生的污泥不含重金属,沉淀物中钙矾石质量分数为88.1%,因此可作为合成水滑石阻燃剂原料进行回收。第四沉淀池8出水进入除钙池9,其水力停留时间为12h,所用除钙剂为碳酸氢钠,投加量为0.28g/l。经第五沉淀池10沉降分离后,ca2+浓度仅为0.04mmol/l,上清液可作为后续零排放工艺进水。通过x射线能谱分析(eds)(表2)可知,沉淀物不含重金属,符合dl/t5196-2016的要求,因此可作为脱硫剂排至脱硫塔。表2第五沉淀池10污泥eds除镁池3产生的粗氢氧化镁以及深度除硫池7产生的粗钙矾石,分别排至污泥脱水机11以2000r/min的转速进行脱水,差速分别为1.8%和2.3%。随后排入工业洗涤机12,通过反复冲洗3次后浸泡30min以实现二者的高效提纯,最终由烘干机13在60℃条件下烘干8h得到固体阻燃剂颗粒。进行烘干。表3沉淀物的xrf分析(以元素计,wt%)元素caalmgohs粗mg(oh)20.65040.8840.883.440精mg(oh)20.37041.1041.103.440粗钙矾石20.315.70062.364.886.75精钙矾石19.284.68063.525.067.46通过xrf分析(表3)可知,氢氧化镁及钙矾石含量均有提升。提纯过程产生的污泥脱水液、清洗废液以及冷凝液回流至预除硫池5。本实施例得到的沉淀物性质与国家阻燃剂标准对比表见表4和5。表4氢氧化镁阻燃剂标准与hg/t4531-2013对比氢氧化镁阻燃剂标准获得的氢氧化镁沉淀物氢氧化镁质量分数/%≥97.599.8氧化钙质量分数/%≤0.100.084水分/%≤0.50.47氯化物质量分数/%≤0.100.09激光粒径/μm0.5-1.51.28灼烧失量/%≥30.037.1白度≥9595.9表5合成水滑石阻燃剂标准与hg/t4496-2013对比图3为实施例2中第四沉淀池8中钙矾石沉淀物的ft-ir图谱,ft-ir图谱说明沉淀物存在-oh、ca-oh-ca、ca-oh-al和al-oh-al键位,这些键位在材料燃烧时断裂,起到阻燃的效果;图4为实施例2中氢氧化镁以及钙矾石沉淀的粒径及热重分析,由图4(a)可知,二者粒径均小于5μm。由图4(b)知,在热重分析过程中深度除硫单元沉淀物会在80℃以上即会出现吸热峰,这是由于沉淀物向单硫性水化硫铝酸钙转化时的变化;在80℃时沉淀物中自由水分也会逐渐失去;在150℃时沉淀物中的ca-so4键位将发生分解;之后al-oh-al键位在250℃断裂,转化为al2o3;在300-500℃下发生的化学变化主要是沉淀物中的-oh、ca-oh-ca、ca-oh-al等键位断裂,这些性质都说明了脱硫废水除硫沉淀物具备成为阻燃剂的条件。实施例3:与实施例2相比,绝大部分都相同,除了本实例中:预沉池1中氧化钙投加量为300mg/l;除镁池3中投加氢氧化钠,投加量为10g/l;预除硫池5投加6g/l的氢氧化钙;深度除硫池7以摩尔比al/s=0.8投加氢氧化铝,回流比为15%;每10g粗氢氧化镁或钙矾石沉淀物使用去离子水冲洗4次,再以按液固比为4用去离子水浸泡10min。表6和7证明了脱硫废水处理产生的沉淀物能够满足阻燃剂标准,进一步说明不同反应条件对沉淀物纯度有一定的影响,需要严格控制工艺的反应条件,使得到的沉淀物满足国家阻燃剂标准。表6氢氧化镁阻燃剂标准与hg/t4531-2013对比表7合成水滑石阻燃剂标准与hg/t4496-2013对比钙矾石阻燃剂标准获得的钙矾石沉淀物团聚指数≤5046氧化铝质量分数/%14.6-18.914.8重金属(以pb计)/%≤0.0010.0005铁质量分数/%≤0.050.012ph(20g/l)悬浮液7.0-9.08.5白度≥9092.6干燥减量(105℃)/%≤0.50.44而同样,若本实施例中,在除镁池3中采用不同药剂,将脱硫废水调节至11.0,得到的氢氧化镁质量分数大于等于97.5%,但沉淀物中杂质可能增加,需增加洗涤次数,以满足实际生产的需求。在深度除硫池7中,采用其他药剂,沉淀物能够满足阻燃剂标准,但纯度可能较低,氯离子质量分数可能增大,需要加大投加量提高沉淀物含量才可能达到生产需求。实施例4:与实施例2相比,绝大部分都相同,除了本实施例中生产的阻燃剂由氢氧化镁与钙矾石按质量比1:2复配制得。通过极限氧指数(loi)(图5)分析可知,由预处理系统制备的氢氧化镁阻燃剂loi值略高于合成水滑石阻燃剂。二者复配的协同阻燃剂loi值更高,且loi值随着掺比率的增加而不断增大,当掺比率达到60%时,loi值增至34%。通过对eva材料的实际阻燃效果验证可知,随着协同阻燃材料掺比率的增加,eva材料融化滴落的现象消失,形成的碳层更加密实,阻燃效果更佳,与loi分析结果一致。综上所述,本发明提出一种利用脱硫废水零排放预处理系统污泥制备阻燃剂的方法,将脱硫废水零排放预处理工艺各单元所产污泥进行资源化利用,并重点考察氢氧化镁和钙矾石作为协同阻燃剂的使用,在保障后续膜法零排放工艺稳定运行的同时,实现污泥的充分资源化利用,具有显著的经济和环境效益。上述的对实施例的描述是为便于该
技术领域:
的普通技术人员能理解和使用发明。熟悉本领域技术的人员显然可以容易地对这些实施例做出各种修改,并把在此说明的一般原理应用到其他实施例中而不必经过创造性的劳动。因此,本发明不限于上述实施例,本领域技术人员根据本发明的揭示,不脱离本发明范畴所做出的改进和修改都应该在本发明的保护范围之内。当前第1页12