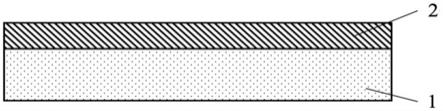
一种dsa电极及其制作方法
技术领域
1.本发明涉及电解技术领域,具体涉及一种dsa电极及其制作方法。
背景技术:2.电絮凝处理技术作为一种绿色工艺,在水处理方面具有独特的优势。电絮凝技术的核心是电极的制备。考虑到贵金属一般具有良好的催化活性,且具有稳定性高、导电性好、耐腐蚀性强等特点,因此一般选择贵金属来制作电絮凝技术所需的电极。
3.钛基涂层电极是金属氧化物电极的一种主要形式,在钛金属基体表面涂覆催化涂层已成为了一个庞大的工业体系,一般将这种电极称为dsa电极。dsa电极不但克服了传统石墨电极、铂电极、铅基合金电极、二氧化铅电极等存在的一些不足,而且可以根据电极反应的要求,设计电催化材料的组成及结构,有效诱导或控制表面副反,发展到现在,已经被广泛应用于污水处理、阴极保护、有机合成、冶金等领域。但将dsa电极应用于电化学水处理时,在处理过程中,极板会受到极大的腐蚀,寿命短,需要频繁更换,运行成本高。
4.专利cn102560561a公开了一种dsa电极及其制作方法。dsa电极由金属基体、中间保护层和表面活性涂层构成;金属基体选自金属ti、金属ta或表面覆ta的金属复合材料中的一种;中间保护层由铂族金属氧化物与其它金属氧化物组成的多元化合物构成;表面活性涂层由iro2·
ta2o5构成。dsa电极包括基体的处理、中间保护层的制备和表面活性涂层的制备。该专利仅改善了dsa电极在使用过程中阳极钝化和涂层脱落的问题,并没能提高电极的电化学性能,而本发明提高了dsa电极的析氧电位,提高了电催化活性和性能。
5.专利cn103147093a提供了一种长寿命dsa电极的制备方法,以金属钛或钛合金为基体,将其进行一定的表面处理,作为阴极在含有sn
4+
、sb
3+
的溶液中恒电流电镀一定时间,得到致密的电镀中间层,最后在其表面均匀涂覆上活性层。表面活性层可以是sno2、pbo2、ruo2、iro2、sb2o5、ta2o5、cr2o3等金属氧化物中的一种或几种。表面活性层可以通过浸渍法、溶胶凝胶法、喷涂法、电沉积法、气相沉积法、溅射法等方法制得。专利cn103147093a中的中间保护层使用了电沉积法制备,而电沉积法工序复杂,且难以实现较大面积电极的制备,此外,电沉积过程中要调整电压和电流的大小,并且要控制沉积的时间。在通过调整电压和电流,控制晶核的生成和晶粒成长的速度时,若晶粒成长的速度大于晶核生成的速度,晶粒就会长大变粗,使电极的电催化活性降低;另一方面,若电沉积的时间太短,镀层太薄,就会达不到提高电极寿命的目的。而且此专利也仅仅是改变了电极的寿命,并不具备提高电极的性能的功效。而本发明采用的工艺设备简单,在应用上提高了dsa电极的电催化活性。
技术实现要素:6.本发明的目的就是提供一种dsa电极及其制作方法。
7.本发明的目的通过以下技术方案实现:
8.一种dsa电极,所述dsa电极包括金属基体以及涂覆在金属基体表面的表面活性层
涂层,所述表面活性层涂层的材质为sio2·
ta2o5。
9.所述金属基体的材质为ti。
10.表面活性层由铂族金属氧化物与其他金属化合物组成的多元化合物构成。
11.一种如上述所述的dsa电极,所述制作方法具体包括以下步骤:
12.(a)金属基体的处理:取金属原材进行预处理,得到表面呈均匀平整并且为麻面的金属基体;
13.(b)表面活性层涂层的制备:取含si元素和ta元素的有机溶液均匀涂布在步骤(a)得到的金属基体表面,干燥之后煅烧,重复涂布
‑
干燥
‑
煅烧数次,在金属基体表面形成与金属基体结合紧密的表面活性层涂层,得到所述dsa电极。
14.步骤(a)中,预处理过程具体为:将金属原材依次进行打磨去除氧化膜、碱洗去油、酸洗和水洗。
15.步骤(a)中,所述的碱洗过程具体为:将打磨至呈银白色金属光泽的金属基体放入质量百分比为5~20%的naoh中,超声波清洗50~70min。
16.优选地,所述的碱洗过程具体为:将打磨至呈银白色金属光泽的金属基体放入质量百分比为10%的naoh中,超声波清洗60min。
17.步骤(a)中,所述的酸洗过程具体为:将金属基体放入质量百分比为10%的草酸溶液中在85~95℃下恒温浸煮90~110min。酸洗的作用为:通过低浓度的草酸,将dsa电极基体蚀刻,使得基体表面呈现均匀平整的裂纹结构,增大基体的表面积。
18.优选地,所述的酸洗过程具体为:将金属基体放入质量百分比为10%的草酸溶液中在90℃下恒温浸煮100min。
19.步骤(a)中,所述的水洗过程具体为:将酸洗完成的金属基体从草酸溶液中取出,再用水反复冲洗,直至冲洗水的ph为7~8,之后放入(ch2oh)2中保存。
20.步骤(b)中,按比例取c8h
20
o4si和tacl5溶于有机溶剂中,配置成含si元素和ta元素的有机溶液。
21.步骤(b)中,所述有机溶剂由体积比为1:1的c3h8o和c2h5oh混合而成。
22.步骤(b)中,含si元素和ta元素的有机溶液中,si:ta的摩尔比为1:1,且总离子的浓度为0.2mol/l。
23.步骤(b)中,每次涂布的涂布量为60~200ml/m2。
24.步骤(b)中,所述的干燥过程具体为:将涂布后的金属基体置于75~85℃的烘箱中烘干5~15min,使金属基体表面的液体挥发。
25.优选地,所述的干燥过程具体为:将涂布后的金属基体置于80℃的烘箱中烘干5~15min,使金属基体表面的液体挥发。
26.步骤(b)中,所述的煅烧过程具体为:将干燥完成的金属基体放入马弗炉内缓慢加热至400~500℃,然后在400~500℃下煅烧6.5~9.5min。
27.优选地,所述的煅烧过程具体为:将干燥完成的金属基体放入马弗炉内缓慢加热至450℃,然后在450℃下煅烧8min。
28.步骤(b)中,所述的涂布
‑
干燥
‑
煅烧的总次数为11~15次,且最后一次干燥完成后在马弗炉中加热高温回火0.8~1.2h。
29.优选地,所述的涂布
‑
干燥
‑
煅烧的总次数为11~15次,且最后一次干燥完成后在
马弗炉中加热高温回火1h。高温回火可以提高表面活性层的稳定性,保持其性能的稳定。
30.本发明采用了在金属基体表面烧结一层金属氧化物作为表面活性层的方法,改善了电极寿命使用短的问题。
31.本发明的有益效果是:本发明的dsa电极表面涂有金属氧化层,并且金属氧化层耐腐蚀性较高,在有了这些金属氧化物的保护后,dsa电极的使用寿命提高;dsa电极拥有表面活性层涂层后,可形成裂泥结构,裂纹增多,使得电极表面积增大,活性提高,提高了电极的催化效率,使用效率得到提升。
附图说明
32.图1是一种dsa电极的剖视示意图;
33.图2是实施例1制得的dsa电极在葡萄糖和氯化钠的混合溶液中的极化曲线图;
34.图3是实施例1制得的dsa电极的电镜示意图;
35.图4是实施例1制得的dsa电极的eds能谱图;
36.图5为和图4关联的分布数总数谱图。
37.图中:1
‑
金属基体;2
‑
表面活性层涂层。
具体实施方式
38.下面结合附图和具体实施例对本发明进行详细说明。
39.一种dsa电极,包括金属基体以及涂覆在金属基体表面的表面活性层涂层,所述表面活性层涂层的材质为sio2·
ta2o5,金属基体的材质为ti。
40.一种如上述所述的dsa电极,所述制作方法具体包括以下步骤:
41.(a)金属基体的处理:取金属原材进行预处理,得到表面呈均匀平整并且为麻面的金属基体,预处理过程具体为:将金属原材依次进行打磨、碱洗去油、酸洗和水洗,碱洗过程具体为:将打磨至呈银白色金属光泽的金属基体放入质量百分比为5~20%的naoh中,超声波清洗50~70min,酸洗过程具体为:将金属基体放入质量百分比为10%的草酸溶液中在85~95℃下恒温浸煮90~110min,水洗过程具体为:将酸洗完成的金属基体从草酸溶液中取出,再用水反复冲洗,直至冲洗水的ph为7~8,之后放入(ch2oh)2中保存;
42.(b)表面活性层涂层的制备:按比例取c8h
20
o4si和tacl5溶于有机溶剂中,配置成含si元素和ta元素的有机溶液,取含si元素和ta元素的有机溶液均匀涂布在步骤(a)得到的金属基体表面,干燥之后煅烧,重复涂布
‑
干燥
‑
煅烧数次,在金属基体表面形成与金属基体结合紧密的表面活性层涂层,得到所述dsa电极,其中,所述有机溶剂由体积比为1:1的c3h8o和c2h5oh混合而成,含si元素和ta元素的有机溶液中,si:ta的摩尔比为1:1,且总离子的浓度为0.2mol/l,干燥过程具体为:将涂布后的金属基体置于75~85℃的烘箱中烘干5~15min,使金属基体表面的液体挥发,煅烧过程具体为:将干燥完成的金属基体放入马弗炉内缓慢加热至400~500℃,然后在400~500℃下煅烧6.5~9.5min,所述的涂布
‑
干燥
‑
煅烧的总次数为11~15次,且最后一次干燥完成后在马弗炉中加热高温回火0.8~1.2h。
43.实施例1
44.如图1所示,一种dsa电极,包括金属基体2以及涂覆在金属基体2表面的表面活性层涂层1,表面活性层涂层1的材质为sio2·
ta2o5,可对电极形成一种保护作用,增加了电极
的耐腐蚀性能,金属基体2的材质为ti。
45.一种dsa电极,具体包括以下步骤:
46.(ⅰ)选用长200mm,宽200mm,厚1mm的钛板原材,加工成长宽均为50mm的正方形(厚度不变)。使用砂纸对钛板原材的表面进行打磨,除去表面的氧化膜,然后放入10%的naoh溶液中,用超声波清洗机清洗60min,将碱洗完成的钛基体放入质量百分比为10%的草酸溶液中在90℃恒温浸煮100min,使钛基板表面呈均匀平整的麻面,然后用去离子水反复冲洗,直至冲洗水的ph为7~8,之后放入(ch2oh)2中保存。
47.(ⅱ)配置含si化合物和ta化合物的混合有机溶液。将0.01mol c8h
20
o4si和0.01moltacl5溶于由体积比为1:1的c3h8o和c2h5oh混合得到的混合液中,并控制其中si:ta的摩尔比为1:1,且总离子浓度为0.2mol/l。
48.(ⅲ)将含si化合物和ta化合物的混合有机溶液均匀涂布在处理后的钛基板表面,每次涂布的涂布量为150ml/m2,将涂布后的钛基板放入80℃的烘箱中烘干8min,使钛基板的表面干燥,然后放入马弗炉中加热至450℃,然后在450℃下煅烧8min,重复涂布
‑
干燥
‑
煅烧13次,且最后一次在450℃的马弗炉中高温回火1h,完成dsa电极的制作。
49.如图2所示,对本实施例制得的dsa电极进行测试,将该电极置于9g/l的葡萄糖溶液和2g/l氯化钠溶液的混合溶液中,混合比为1:1,以铂为参比电极,得到极化曲线图,可以看出,改性后的电极具有较高的析氧电位,为3.03v,增加了降解效率,在进行了一系列的实验发现,此dsa电极应用于电絮凝处理垃圾渗滤液中,原先的总磷约为36.35mg/l,处理后的总磷含量为1.17mg/l,其去除总磷的效率最高可达到96.78%。
50.如图3所示,本实施例制得的dsa电极在电镜下放大2000倍后的表面形貌呈“裂泥”状,比表面积增大,提高了电极催化活性。
51.如图4、5所示,本实施例制得的dsa电极的eds能谱表明,在最高峰处为ta和si元素,在其他峰处还含有少量的ta元素,图5说明,其中ta的含量超过50%,si的含量超过10%,o的含量超过20%,说明表面活性层主要由ta的氧化物和si的氧化物构成。而其中还有少量的cl和ca元素,cl元素来源于涂层原料使用的为ta2cl,而ca元素来源于基体中含有少量的ca元素。
52.对比例1
53.一种钛基ce掺杂sno2‑
ruo2dsa电极,析氧电位约为2.5v。而本发明的dsa电极的析氧电位为3.03v,吸氧电位的提高有效地抑制了析氧副反应,意味着阳极氧化的电流效率越高,增加了对污染物的降解效率。
54.上述的对实施例的描述是为便于该技术领域的普通技术人员能理解和使用发明。熟悉本领域技术的人员显然可以容易地对这些实施例做出各种修改,并把在此说明的一般原理应用到其他实施例中而不必经过创造性的劳动。因此,本发明不限于上述实施例,本领域技术人员根据本发明的揭示,不脱离本发明范畴所做出的改进和修改都应该在本发明的保护范围之内。