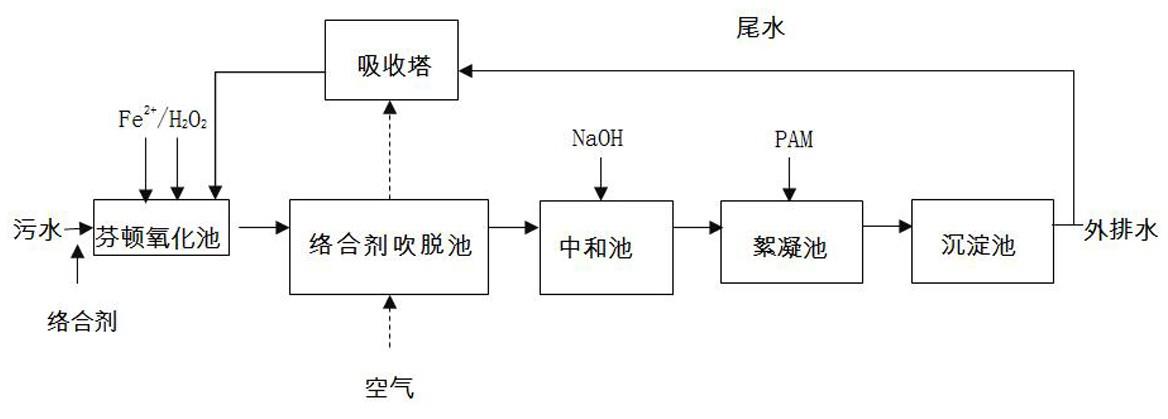
1.本发明涉及工业废水处理技术领域,具体地说是一种工业废水强化氧化处理方法。
背景技术:2.对于一些生物难降解的工业有机废水,以羟基自由基为代表的氧化工艺,如芬顿、催化臭氧、uv/h2o2等氧化工艺已成为现在污水深度处理的首选工艺,其中芬顿工艺因其投资少、运行简单而日益被受到重视。
3.常规芬顿工艺是在弱酸环境下,通过在废水中加入一定量的过氧化氢溶液和亚铁盐溶液后,在亚铁离子催化过氧化氢分解的同时生成以羟基自由基、过氧阴离子自由基等为代表的氧化物种来完成有机物的氧化和三价铁的还原,待过氧化氢分解完全后,再通过添加碱液来调节溶液ph到中性,同时加入一定量的絮凝剂,将铁泥从水中分离出来从而完成氧化反应过程。但是在在实际生产中,常规的芬顿工艺存在亚铁盐加入量大、污泥产生量多、ph调节加酸、加碱量大的问题。为解决上述问题,减少ph调节的络合芬顿和减少铁盐加入量的共催化芬顿这两种新工艺越来越得到重视。其中的络合芬顿是在ph近中性环境下,向废水中加入亚铁和过氧化氢的同时加入一定浓度的铁离子络合剂,络合剂可以在较高 ph 条件下与fe 2+ /fe 3+ 形成络合物,使其保持可溶性,从而通过 fe 2+ /fe 3+ 与 过氧化氢 的反应促进活性。络合芬顿反应降低铁源及过氧化氢的用量,达到更有效、 更经济的处理效果。
4.因此,常规芬顿中引入络合剂的络合芬顿法成为近年来芬顿反应研究的热点。但是,目前络合芬顿法在实际应用过程中,由于铁离子以稳定的络合态存在,络合剂和铁盐很难从水中分离出来,因此当过氧化氢分解完成后,铁离子和络合剂一同絮凝沉淀后排放到后续的生物处理或其它处理工艺,造成了络合剂的流失,带来不必要的经济损失。
技术实现要素:5.为解决背景技术中提到的络合芬顿应用过程中的技术问题,本发明提供了一种可循环利用络合剂的工业废水强化氧化处理方法。
6.为实现上述发明目的,本发明采用以下技术方案:一种工业废水强化氧化处理方法,具体处理步骤如下:s1、废水被送入芬顿氧化池中,在搅拌条件下向废水中加入络合剂,混合均匀后再加入硫酸,至废水的碱度控制在100
‑
200mg/l(以碳酸钙计);s2、向步骤s1得到的废水中加入硫酸亚铁,反应时间3
‑
5min;s3、向s2的废水中加入过氧化氢,反应时间4
‑
8小时;s4、待过氧化氢分解完成后,步骤s3的废水被送入络合剂吹脱池中,在一定气水比下进行空气吹脱,空气吹脱时间为15
ꢀ‑
60 min;s5、吹脱出的气体进入吸收塔,使用处理后的尾水进行吸收,被尾水吸收的络合剂
送入步骤s1中的芬顿氧化池中回用。
7.步骤s1中络合剂为edta(乙二胺四乙酸)、edds(乙二胺二琥珀酸)、柠檬酸、酒石酸(2,3
‑
二羟基丁二酸)、(顺、反)丁烯二酸、已烯酸中的一种。
8.步骤s2中所加入的络合剂与所述硫酸亚铁中二价铁离子的摩尔比为1:1
‑
15。
9.步骤s4中的吹脱过程中,气水比为1500
‑
3000:1(m3/m3),空塔流速1.0
‑
3.0m/s。
10.步骤s5中,吸收塔液气比为0.5
‑
1.0l/m3;喷淋密度为5
‑
10m3/m2·
h;空塔气速为0.5
‑
2.0m/s。
11.步骤s5中吹脱后废水依次进入中和池、絮凝池和沉淀池进行处理。
12.与现有技术相比,本发明所公开的这种废水处理方法工序简单,通过空气吹脱作用,将络合剂从水中分离出来,吸收后继续再利用,减少了络合剂的投加量,降低处理成本。
附图说明
13.图1为本发明的工艺流程框图。
具体实施方式
14.下面结合附图和实施例对本发明做进一步说明。
15.本发明所公开的这种工业废水强化氧化处理方法,通过空气吹脱作用,将络合剂从水中分离出来,吸收后继续回用,参照附图1,具体处理步骤如下。
16.s1、废水被送入芬顿氧化池中,在搅拌条件下向废水中加入络合剂,混合均匀后再加入硫酸,将废水的碱度控制在100
‑
200mg/l(以碳酸钙计);所述的络合剂除常规的edta(乙二胺四乙酸)、edds(乙二胺二琥珀酸)、柠檬酸、酒石酸(2,3
‑
二羟基丁二酸)外,还包括(顺、反)丁烯二酸、已烯酸。
17.s2、向步骤s1得到的废水中加入硫酸亚铁,反应时间3
‑
5min;络合剂与所述二价铁离子的摩尔比为1:1
‑
15。作为优选的技术方案,络合剂与二价铁离子的摩尔比为1:5
‑
10。
18.s3、向s2的废水中加入过氧化氢,反应时间4
‑
8小时;过氧化氢投加量为进水cod的1
‑
5倍(以质量计),过氧化氢与二价铁离子的摩尔比为1
‑
8:1。
19.s4、待过氧化氢分解完成后,步骤s3的废水被送入络合剂吹脱池中,在一定气水比下进行空气吹脱,空气吹脱时间为15
ꢀ‑
60 min;吹脱过程中,气水比为1500
‑
3000:1(m3/m3),空塔流速1.0
‑
3.0m/s。
20.s5、吹脱出的气体进入吸收塔,使用处理后的尾水作为吸收液回收气体中的络合剂。含有络合剂的吸收液被送入步骤s1中的芬顿氧化池,从而达到络合剂回收利用的目的。吸收塔液气比为0.5
‑
1.0l/m3;喷淋密度为5
‑
10m3/m2·
h;空塔气速为0.5
‑
2.0m/s,络合剂回收率可达85%以上。
21.步骤s5中吹脱后废水依次进入中和池、絮凝池和沉淀池进行处理。在中和池中加入碱液将废水ph值调节至中性;在絮凝池中加入一定量的聚丙烯酰胺提高固液分离效率。
22.反应过程中,药剂投加量确定方法为:过氧化氢投加浓度为废水codcr值的1
‑
3倍,硫酸亚铁投加浓度为过氧化氢投加浓度的1/3
‑
1/5。
23.实施例1:取codcr值为100mg/l的废水5l,搅拌条件下向废水中投加柠檬酸作为络合剂,柠
檬酸投加为0.2mmol;混合均匀后向废水中投加硫酸至废水碱度为100mg/l(以碳酸钙剂);随后向废水中投加硫酸亚铁,投加量为1mmol;混合均匀后投加过氧化氢,投加量为5mmol,搅拌条件下反应4h后,过氧化氢分解完全;将废水送入吹脱池,以气水比1500:1进行吹脱,吹脱时间为1h,吹脱出的气体用处理后的尾水作为吸收液回收络合剂,吸收液用量为4l,测得吸收液中柠檬酸总量为0.169mmol,计算可得柠檬酸的回收率为84.5%;向吹脱后的废水中加入氢氧化钠溶液调节ph至中性,投加聚丙烯酰胺反应15min,沉降1h后收集上清液,部分作为吸收液回用。
24.实施例2:取codcr值为150mg/l的废水15l,搅拌条件下向废水中投加edta作为络合剂,edta的投加量为0.5mmol;混合均匀后,再向废水中投加硫酸,至废水碱度为150mg/l(以碳酸钙剂);随后向废水中投加硫酸亚铁,投加量为2mmol;混合均匀后投加过氧化氢,投加量为7mmol,搅拌条件下反应8h后,过氧化氢分解完全;将废水送入吹脱池,以气水比3000:1进行吹脱,吹脱时间为45min,吹脱出的气体用处理后的尾水作为吸收液回收络合剂,吸收液用量为15l,测得吸收液中edta总量为0.43mmol,计算可得edta的回收率为86%;向吹脱后的废水中加入氢氧化钠溶液调节ph至中性,投加聚丙烯酰胺反应25min,沉降2h后收集上清液,部分作为吸收液回用。
25.实施例3:取codcr值为175mg/l的废水20l,搅拌条件下向废水中投加酒石酸作为络合剂,酒石酸的投加量为1mmol;混合均匀后,再向废水中投加硫酸,至废水碱度为150mg/l(以碳酸钙剂);随后向废水中投加硫酸亚铁,投加量为4mmol;混合均匀后投加过氧化氢,投加量为10 mmol,搅拌条件下反应8h后,过氧化氢分解完全;将废水送入吹脱池,以气水比3000:1进行吹脱,吹脱时间为45min,吹脱出的气体用处理后的尾水作为吸收液回收络合剂,吸收液用量为15l,测得吸收液中edta总量为3.43mmol,计算可得edta的回收率为85.75%;向吹脱后的废水中加入氢氧化钠溶液调节ph至中性,投加聚丙烯酰胺反应25min,沉降2h后收集上清液,部分作为吸收液回用。