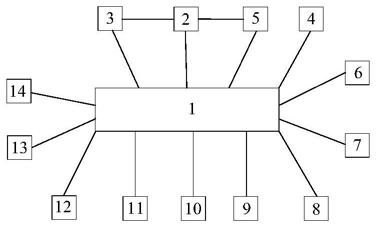
1.本发明涉及油罐清洗和油气回收技术领域,具体涉及一种卧式地埋罐自动清洗控制系统。
背景技术:2.加油站是石油产业链和价值链的重要环节。目前,中国对埋地储油罐主要采用人工清洗的方式,人工清罐方法存在作业危险性高、清洗效率低、清洗效果差、工作强度大及油气和有毒有害气体无组织排放等问题。
3.原有的埋地油罐的清洗处理方式采用撇油槽,依据最简单的隔油池重力沉降的原理进行污油回收,但此类设备在撇油过程中均存在控制不稳定、自动化程度低、劳动强度大、能耗大、露天作业和容易污染环境等缺陷。现有技术中有卧式容器罐、浮油回收系统和液位控制系统组成的自动密闭撇油装置,虽然卧式容器罐综合采用了重力沉降和填料粗粒化的技术,但仍存在着体积大、分离效率低等问题。
4.例如,中国专利申请号cn201710252604.9公开了一种加油站地埋罐清洗系统,包括地埋罐、清洗回收装置、清洗机、油水分离装置、污泥脱水机、反应罐、气浮机、过滤装置、加药装置、惰性气体发生器和真空泵,地埋罐下方设有排水阀和出口,排水阀和出口通过回收管线连接在清洗回收装置中,清洗回收装置包括真空罐和回收罐,真空罐与回收罐连接,且真空罐与回收罐之间设有油水分离装置,油水分离装置设有回油出口和回水出口,回油出口通过回油管道连接在油罐上,回水出口通过回水管道连接在回收管线上,回收管线上设有水泵,真空泵设置在回收罐与污泥脱水机之间并通过污泥管道连接,污泥脱水机依次通过污水管道连接有反应罐和气浮机,加药装置与反应罐连接,气浮机通过水泵与过滤装置连接,过滤装置的出口连接有净水储罐,净水储罐下方设有换热器,净水储罐通过高压水管和清洗机与地埋罐连接。该发明专利申请存在的缺陷是自动化程度低、劳动强度大、能耗大,缺乏液位计、密度计、气体检测机、激光甲烷检测仪、氧气含量分析仪、碳化氢分析仪、检测探头、流量计、清洗水流量计、污水流量计及压力显示器等量化设备,使得对卧式地埋罐自动清洗控制效果差,自动化程度低。
技术实现要素:5.针对现有技术的不足,本发明提供一种卧式地埋罐自动清洗控制系统。
6.所述清洗控制系统包括:可编程逻辑控制器、清洗机、驱动器、回收机、净化器、制氮机、液位计、密度计、电动调节阀、气体检测机、补水泵、流量计、延时器、压力显示器,其中,清洗机、驱动器、回收机、净化器、制氮机、液位计、密度计、电动调节阀、气体检测机、补水泵、流量计、延时器、压力显示器均与可编程逻辑控制器电连接,清洗机分别与驱动器、净化器电连接。
7.进一步地,可编程逻辑控制器包括中央处理器、触摸屏、i/o模块、pid模块、存储器、通信模块、转换器,其中,中央处理器接收清洗机、驱动器、回收机、净化器、制氮机的状
态信息和反馈数据并显示于触摸屏上,i/o模块接收清洗机、驱动器、回收机、净化器、制氮机、液位计、密度计的信号并将接收的信号发送至中央处理器,中央处理器向清洗机、驱动器、回收机、净化器、制氮机、液位计、密度计反馈控制指令,pid模块将收集的压力、流量、液位的信息发送至中央处理器并将处理的结果输出至液位计和密度计,存储器存储i/o模块与pid模块接收的信息,转换器包括手动/自动转换按键、手动启停按键,手动启停按键与手动/自动转换按键电连接,手动/自动转换按键均与中央处理器、清洗机、驱动器、回收机、净化器、制氮机、液位计、密度计、电动调节阀、气体检测机、补水泵、流量计、延时器电连接。
8.进一步地,清洗机包括洗灌器、清洗泵、供水罐,洗灌器、清洗泵与供水罐通过清洗管路连接,洗灌器、清洗泵之间的清洗管路上设有电动调节阀,洗灌器包括清洗头、罐洗阀。
9.进一步地,驱动器包括推进杆、增压缸。
10.进一步地,回收机包括液体回收泵、气体回收泵、回收罐,液体回收泵、气体回收泵、回收罐之间通过回收管路连接。
11.进一步地,净化器包括分离机、油渣罐、过滤罐、分离水罐、分离油罐,油渣罐通过净化管路与分离机连通,过滤罐、供水罐并排地设置在地面上,过滤罐与供水罐通过净化管路连通,分离水罐的输出口通过净化管路与分离机的进水口连通,分离机的出油口通过净化管路与分离油罐的输油口连通,过滤罐的输入端与供水罐连通。
12.进一步地,过滤罐包括依次连通的第一级过滤罐、第二级过滤罐、第三级过滤罐,第一级过滤罐设置pp棉层,第二级过滤罐设置颗粒活性炭层,第三级过滤罐设置压缩活性炭层。
13.进一步地,制氮机与注氮导管通过输送管路连接。
14.进一步地,液位计分别设置在供水罐、回收罐、分离水罐内。
15.进一步地,密度计设置在地埋罐与回收罐之间的回收管路上。
16.进一步地,电动调节阀分别设置在清洗管路、回收管路上。
17.进一步地,气体检测机包括激光甲烷检测仪、氧气含量分析仪、碳化氢分析仪、检测探头,检测探头的一端插入地埋罐内,另一端分别与激光甲烷检测仪、氧气含量分析仪、碳化氢分析仪连接。
18.进一步地,补水泵设置在补水管路上,分离水罐、供水罐通过补水管路连接。
19.进一步地,流量计包括清洗水流量计、污水流量计,清洗水流量计、污水流量计分别安装在清洗管路、净化管路上。
20.进一步地,清洗管路、回收管路、净化管路、电动调节阀上分别设置延时器。
21.进一步地,气体回收泵与储物罐之间设置压力显示器。
22.进一步地,通信模块采用rs485通信接口、modbus通信协议中的至少一种。
23.进一步地,所述清洗控制系统安装于移动车辆的负压防爆柜内。
24.进一步地,可编程逻辑控制器1采用simatic s7
‑
1200可编程控制器。
25.与现有技术相比,本发明具有以下显著的优越效果:
26.1,本发明所述的清洗控制系统采用全自动化清洗方式,能够提高清洗效率,降低劳动强度。
27.2,本发明所述的清洗控制系统能够回收较高的原油,回收的原油可进行多次分离回收,最大限度地回收了储油罐中沉积的油渣中的油分,杜绝人工清理中污染和浪费。
28.3,本发明采用净化器对回收罐中回收液进行油水分离,分离水可再循环利用,分离油可再回收,回收的分离油无污染。
29.4,本发明采用回收机、制氮机、气体检测机对注氮过程中挤出的油气进行回收,消除了人员中毒及油罐爆炸的问题。
30.5,本发明所述的清洗控制系统的稳定性较好、抗干扰较强、清洗效果良好。
附图说明
31.图1为本发明所述清洗控制系统的可编程逻辑控制器与相关构件之间连接示意图;
32.图2为本发明所述清洗控制系统的结构连接关系示意图。
33.附图标记说明:
[0034]1‑
可编程逻辑控制器;2
‑
清洗机,2.1
‑
洗灌器,2.2
‑
清洗泵,2.3
‑
供水罐,2.4
‑
清洗管路;3
‑
驱动器,3.1
‑
推进杆,3.2
‑
增压缸;4
‑
回收机,4.1
‑
液体回收泵,4.2
‑
气体回收泵,4.3
‑
回收罐,4.4
‑
回收管路;5
‑
净化器,5.1
‑
分离机,5.2
‑
油渣罐,5.3
‑
过滤罐,5.4
‑
净化管路,5.5
‑
分离水罐,5.6
‑
分离油罐;6
‑
制氮机;7
‑
液位计;8
‑
密度计;9
‑
电动调节阀;10
‑
气体检测机,10.1
‑
激光甲烷检测仪,10.2
‑
氧气含量分析仪,10.3
‑
碳化氢分析仪,10.4
‑
检测探头;11
‑
补水泵;12
‑
流量计,12.1
‑
清洗水流量计,12.2
‑
污水流量计;13
‑
延时器;14
‑
压力显示器;15
‑
地埋罐;16
‑
补水管路;17
‑
储物罐;18
‑
注氮导管;19
‑
输送管路;20
‑
补水管路。
具体实施方式
[0035]
为了使本技术领域的人员更好地理解本发明的技术方案,下面结合说明书附图和具体实施方式对本发明所述清洗控制系统作进一步的详细说明。
[0036]
如图1所示,本发明提供一种卧式地埋罐自动清洗控制系统,所述清洗控制系统包括可编程逻辑控制器1、清洗机2、驱动器3、回收机4、净化器5、制氮机6、液位计7、密度计8、电动调节阀9、气体检测机10、补水泵11、流量计12、延时器13、压力显示器14,其中,清洗机2、驱动器3、回收机4、净化器5、制氮机6、液位计7、密度计8、电动调节阀9、气体检测机10、补水泵11、流量计12、延时器13、压力显示器14均与可编程逻辑控制器1电连接,清洗机2分别与驱动器3、净化器5电连接。
[0037]
进一步地,可编程逻辑控制器1包括中央处理器、触摸屏、i/o模块、pid模块、存储器(图中均未示出),中央处理器接收清洗机2、驱动器3、回收机4、净化器5、制氮机6的状态信息和反馈数据并显示于触摸屏上;i/o模块接收清洗机2、驱动器3、回收机4、净化器5、制氮机6、液位计7、密度计8的信号并将接收的信号发送至中央处理器;中央处理器向清洗机2、驱动器3、回收机4、净化器5、制氮机6、液位计7、密度计8反馈控制指令,pid模块将收集的压力、流量、液位的信息发送至中央处理器并将处理的结果输出至液位计7和密度计8;存储器存储i/o模块与pid模块接收的信息。
[0038]
进一步地,可编程逻辑控制器1还包括通信模块(图中未示出),通信模块采用rs485通信接口和modbus通信协议。
[0039]
进一步地,可编程逻辑控制器1还包括转换器(图中未示出),转换器包括手动/自动转换按键、手动启停按键(图中均未示出),手动/自动转换按键均与中央处理器、清洗机
2、驱动器3、回收机4、净化器5、制氮机6、液位计7、密度计8、电动调节阀9、气体检测机10、补水泵11、流量计12、延时器13电连接;手动启停按键与手动/自动转换按键电连接,手动启停按键对清洗机2、驱动器3、回收机4、净化器5、制氮机6、液位计7、密度计8、电动调节阀9、气体检测机10、补水泵11、流量计12、延时器13实施手动控制。
[0040]
进一步地,如图2所示,清洗机2包括洗灌器2.1、清洗泵2.2、供水罐2.3,洗灌器2.1、清洗泵2.2与供水罐2.3通过清洗管路2.4连接,洗灌器2.1包括清洗头和罐洗阀(图中均未示出),供水罐2.3通过清洗管路2.4向洗灌器2.1输送清洗水,洗灌器2.1、清洗泵2.2之间的清洗管路2.4上设有电动调节阀9,洗灌器2.1、清洗泵2.2分别接收可编程逻辑控制器1发送的控制指令以启动清洗头和罐洗阀清洗地埋罐15。
[0041]
进一步地,驱动器3包括推进杆3.1、增压缸3.2,可编程逻辑控制器1向液压泵(图中未示出)发送液压开启指令并向推进杆3.1发送推进指令,液压泵向推进杆3.1、增压缸3.2输出的液压动力,推进杆3.1驱动洗灌器2.1沿水平方向清洗地埋罐15。
[0042]
进一步地,回收机4包括泵送液体的回收泵4.1、气体回收泵4.2以及回收罐4.3,液体回收泵4.1、气体回收泵4.2、回收罐4.3之间通过回收管路4.4连接,液体回收泵4.1、气体回收泵4.2接收可编程逻辑控制器1发送的回收指令回收地埋罐15中的清洗液和油气混合物,回收的清洗液和油气混合物经过压力显示器14显示符合储物罐17承载的压力值后输送至储物罐17内。
[0043]
进一步地,净化器5包括分离机5.1、油渣罐5.2、过滤罐5.3、分离水罐5.5、分离油罐5.6,油渣罐5.2通过净化管路5.4与分离机5.1连通,可编程逻辑控制器1发送净化指令至分离机5.1,分离机5.1接收净化指令并对回收罐4.3内回收液进行水、油、油渣分离,经分离后的水、油、油渣分别输送至分离水罐5.5、分离油罐5.6、油渣罐5.2,过滤罐5.3、供水罐2.3并排地设置在地面上,过滤罐5.3与供水罐2.3通过净化管路5.4连通,分离水罐5.5的输出口通过净化管路5.4与分离机5.1的进水口连通,分离机5.1的出油口通过净化管路5.4与分离油罐5.6的输油口连通。
[0044]
进一步地,制氮机6与注氮导管18通过输送管路19连接,制氮机6接收可编程逻辑控制器1发送的气体置换信号指令后,将制氮机6内氮气通过输送管路19注入地埋罐15内。
[0045]
进一步地,液位计7分别设置在供水罐2.3、回收罐4.3、分离水罐5.5内,液位计7发送供水罐2.3、回收罐4.3、分离水罐5.5的液位高度信息至可编程逻辑控制器1,可编程逻辑控制器1根据液位高度信息调节供水罐2.3、回收罐4.3、分离水罐5.5内清洗水、回收水、分离水的水量。
[0046]
进一步地,密度计8设置在地埋罐15与回收罐4.3之间的回收管路4.4上,密度计8对回收管路4.4中的残油密度进行检测,并将检测的残油密度信息发送至可编程逻辑控制器1,经可编程逻辑控制器1分析后,将残油密度信息发送至回收机4,回收机4在液体回收或气体回收的模式下相应地切换。
[0047]
进一步地,电动调节阀9分别设置在清洗管路2.4、回收管路4.4上,电动调节阀9接收可编程逻辑控制器1发送的控制指令后调节清洗管路2.4、回收管路4.4上的阀门(图中未示出)开度。
[0048]
进一步地,气体检测机10包括激光甲烷检测仪10.1、氧气含量分析仪10.2、碳化氢分析仪10.3、检测探头10.4,检测探头10.4的一端插入地埋罐15内,另一端分别与激光甲烷
检测仪10.1、氧气含量分析仪10.2、碳化氢分析仪10.3连接,激光甲烷检测仪10.1、氧气含量分析仪10.2、碳化氢分析仪10.3分别将检测到的有害气体的检测结果发送至可编程逻辑控制器1,可编程逻辑控制器1通过报警器(图中未示出)提示用户。
[0049]
进一步地,补水泵11设置在补水管路20上,分离水罐5.5、供水罐2.3通过补水管路20连接,补水泵11接收到可编程逻辑控制器1发送的补水指令后自动向供水罐2.3补充清洗水。
[0050]
进一步地,流量计12包括清洗水流量计12.1、污水流量计12.2,清洗水流量计12.1、污水流量计12.2分别安装在清洗管路2.4、净化管路5.4上,清洗水流量计12.1、污水流量计12.2分别将采集到的液体流量信息发送至pid模块进行比较,比较的结果通过中央处理器向清洗水流量计12.1、污水流量计12.2输出控制指令,对清洗水和回收水的水量进行平衡。
[0051]
进一步地,清洗管路2.4、回收管路4.4、净化管路5.4、电动调节阀9上分别设置延时器13,延时器13控制清洗管路2.4、回收管路4.4、净化管路5.4、电动调节阀9的阀门的开启。
[0052]
进一步地,压力显示器14分别设置在气体回收泵4.2与储物罐17之间,压力显示器14对进入储物罐17内的清洗液和油气混合物的压力进行检测与显示。
[0053]
进一步地,可编程逻辑控制器1采用simatic s7
‑
1200可编程控制器。
[0054]
进一步地,过滤罐5.3采用三级过滤单元,三级过滤的过滤罐5.3包括第一级过滤罐5.3.1、第二级过滤罐5.3.2、第三级过滤罐5.3.3,过滤罐5.3的输入端与供水罐2.3连通,供水罐2.3中的水依次经过第一级过滤罐5.3.1、第二级过滤罐5.3.2、第三级过滤罐5.3.3进行过滤,过滤后的水通过输出端流回至供水罐2.3内,从而使供水罐2.3内的水获得补充和循环过滤。
[0055]
进一步地,第一级过滤罐5.3.1设置采用pp棉层,祛除水中的泥沙、铁锈,第二级过滤罐5.3.2设置颗粒活性炭层,祛除水中的油,第三级过滤罐5.3.3设置压缩活性炭层,祛除水中的异色、异味、余氯、卤代烃。
[0056]
进一步地,所述清洗控制系统安装于移动车辆的负压防爆柜内。
[0057]
进一步地,制氮机采用纤维膜式制氮。
[0058]
进一步地,油渣罐5.2对分离机5.1的输出油渣处理的步骤如下:
[0059]
步骤1,油渣罐5.2内加入适量的水;
[0060]
步骤2,启动油渣罐5.2,采用搅拌机将水和油渣进行混合搅拌,混合搅拌的转速为500r/min;
[0061]
步骤3,向油渣罐5.2中加入破乳剂,破乳剂的重量为的油渣重量的0.02%,搅拌机以450r/min混合搅拌50min;
[0062]
步骤4,向油渣罐5.2中加入絮凝剂,絮凝剂的重量为油渣重量的0.5%,搅拌机以800r/min进行混合搅拌;
[0063]
步骤5,絮凝后的油渣送至三相分离机内进行油、水、泥渣的三相分离,分离后的油输送至分离油罐5.6内,分离后的水送至分离水罐5.5内,分离水罐5.5中的水送至供水罐2.3内进行二次利用;分离后的泥渣输送至干燥机内干燥,作为制砖原料。
[0064]
以上所述的具体实施方式,对本发明的目的、技术方案和有益效果进行了进一步
详细说明,所应理解的是,以上所述仅为本发明的具体实施方式而已,并不用于限定本发明的保护范围,凡在本发明的精神和原则之内,所做的任何修改、等同替换、改进等,均应包含在本发明的保护范围之内。