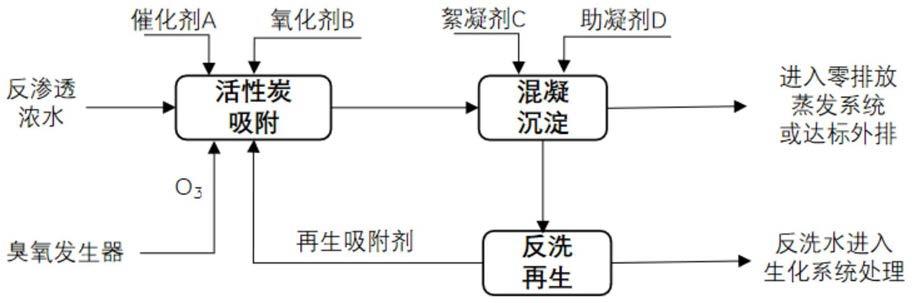
1.本发明涉及一种用于处理反渗透浓水的工艺方法,尤其涉及工业企业采用纳滤或反渗透生产循环回用水过程中产生的浓水的处理,属于工业废水处理领域。
背景技术:2.近年来,由于煤化工项目及其他工业项目的快速建设和发展,耗水量和废水排放量也飞速增加,尤其是煤化工项目所在地大多缺水且生态环境十分脆弱,因此,水资源的回收利用和废水排放问题十分突出,高含盐浓水的零排放问题已成为制约煤化工产业发展的限制因素之一。
3.目前多数企业采用双膜法(超滤+反渗透)处理生产过程中产生的工业废水和循环冷却水,以实现水资源回收利用。由此产生的高含盐浓水则采用蒸发结晶手段,进行水资源回收和溶解性盐类固体的分离处理与处置。但是在蒸发结晶后的固体盐分会出现发黄发黑的现象,导致分离得到的盐类难以资源化利用,这是由于在蒸发结晶之前废水中含有的有机物污染物导致蒸发结晶后的盐类颜色变黑,无法做到完全的零排放,同时降低了蒸发结晶盐的品质,甚至只有当作危废进行处置,增大了企业的处理处置投资。
4.对于反渗透浓水中有机污染物(不仅仅限于煤化工,也包含其他工业领域废水处理过程中产生的反渗透浓水)的脱除处理,目前工程上通常采用的方法包括吸附法、化学氧化法、高级氧化法、生物氧化法、离子交换树脂法、电渗析法、高压膜浓缩等手段。高级氧化工艺如臭氧催化氧化法、臭氧催化氧化法、光电fenton试剂氧化法、超声fenton试剂氧化法、湿式空气催化氧化法、湿式过氧化氢氧化法、超临界水氧化法、电催化氧化法等。
5.单一的处理工艺对反渗透浓水中有机污染物的脱除效率不高,而组合处理工艺是处理反渗透浓水的常用工艺。专利cn201611120857.2公开了一种煤化工废水回用中反渗透产生浓盐水的组合处理工艺,针对煤化工废水回用过程中反渗透单元产生的浓盐水,提出一种高效的组合处理工艺,包括除氨单元、催化过氧化氢氧化单元、浓缩结晶单元和淡水回用单元四个操作单元,该工艺将除氨技术与催化湿式过氧化氢氧化技术耦合,可高效处理反渗透单元产生的浓盐水中残留的酚类等有机化合物以及氨氮等污染类物质,保证经浓缩结晶蒸发后生成的固体盐呈白色,淡水可回用。专利cn202010036545.3公开了一种实现煤化工反渗透浓水零排放及资源化利用方法,该方法先将反渗透浓水进行除硬除硅处理,出水经次氯酸钠氧化去除反渗透浓水中的有机物,再进入纳滤系统分盐,得到硫酸钠浓水和氯化钠产水。专利cn201410145735.3公开了工业废水反渗透浓排水回用工艺和装置,采用氧化
‑
生物膜多孔吸附技术降低所述反渗透浓排水中的cod含量。专利cn201610016854.8提供了一种处理双膜法系统中反渗透浓水和超滤反洗水的方法,采用“预涂膜抵抗超滤膜污染+好氧池处理沸石粉+臭氧处理反渗透浓水”的综合处理方法处理“超滤膜+反渗透”工艺,在臭氧处理过程中进行双氧水+臭氧的优化控制,处理后的废水进入污水厂前端生化循环处理,能够有效的脱除废水中的cod、氨氮等污染物,反渗透的出水达到回用标准,很好的利用了水资源。专利cn202010938000.1公开了一种反渗透高盐废水零排及资源化利用工艺,
包括原水箱、三联箱、管式过滤装置、离子交换装置、预处理产水水箱、低压反渗透装置、一级纳滤分盐装置、二级纳滤分盐装置、高压反渗透装置、大孔树脂吸附装置、电催化氧化装置、厌氧消化装置、好氧装置、冷冻结晶装置、离心压滤装置、酸碱液再生液箱等,解决了高盐废水中有机物低成本难生化降解的行业难题,使产品中氯化钠溶液的水质标准达到氯碱行业化盐水的水质要求,可以直接作为氯碱厂化盐水使用,以节约氯碱厂原料成本,提高了产水的经济效益,使用的厌氧消化会降低此类废水去除难降解有机物的运行成本,近零排放的废水回收会极大的提高电厂和化工厂的原水使用效率。专利cn202011422831.x公开了一种高盐废水结晶过程中副产盐白度、有机物含量的控制方法,将高盐废水依次通过膜碳反应器、色度检测器,然后蒸发结晶。膜碳反应器可以有效吸附高盐废水中的有机物,色度检测器实时监测膜碳反应器过滤后的出水色度,保证有颜色的有机物不会进入后续蒸发系统中。专利cn201810456731.5和专利cn201820712136.9公开了一种用于反渗透浓水有机物去除处理工艺,通过臭氧催化氧化矿化反渗透浓水中有机物,同时提高可生化性,然后通过活性炭吸附有机物,再采用生化方式降解活性炭吸附有机物,使活性炭再生,开辟了采用生化方式降解浓盐水中有机物的方法。专利cn202011189556.1公开了一种冶金行业高浓盐水零排放处理方法,采用“高效沉淀+臭氧接触氧化+曝气生物滤池”组合工艺,将高浓盐水预先进入高效澄清池,以去除水中的暂时硬度和永久硬度,去除水中悬浮物,然后澄清水进入臭氧接触氧化池,进行臭氧催化氧化;臭氧接触氧化池出水进入后续曝气生物滤池处理。专利cn202010071570.5公开了一种利用冶金反渗透浓盐水同时制备盐酸和氢氧化钠的方法,在调节池中预先投加氢氧化钙溶液、聚丙烯酰胺,后投加无水碳酸钠,沉淀后上清液流入反硝化生物滤池,在反硝化生物滤池中加甲醇,反硝化生物滤池出水进入第一臭氧氧化塔;第一臭氧氧化塔出水进入砂滤池;随后废水进入超滤装置,超滤产水进入二段反渗透系统ro进行浓缩分离,二段反渗透系统ro产生的高盐水打入到螯合型离子交换树脂,出水进入第二臭氧氧化塔;纳滤装置将废水分成产水和浓水,浓水送高炉冲渣或焚烧炉,纳滤产水送双极膜电渗析装置。
6.组合工艺脱除处理反渗透浓水中有机污染物的方法工艺流程长,涉及到的处理单元比较复杂,尤其是涉及生化处理过程的,占地面积大,投资较高,操作比较复杂,运行成本相对较高。
7.在脱除反渗透浓水中有机污染物的技术中,基于臭氧催化氧化的高效、清洁、成本较低及无二次污染的优点,臭氧氧化或者臭氧催化氧化技术的应用是比较广泛的。专利cn201610028809.4公开了一种焦化反渗透浓水的深度处理方法,所述焦化反渗透浓水cod为23~36mg/l,经过臭氧催化,先从臭氧催化塔的上部进入塔内,在塔内进行臭氧催化氧化反应,然后再经过除氟沉淀池、斜板沉淀池后,进入多介质过滤塔。在多介质过滤塔通过多介质滤料的截留、沉降和吸附作用,去除焦化反渗透浓水中的颗粒和有机物后排放。整体工艺处理后,焦化反渗透浓水出水水质为:ph为6~9,cod是13~27mg/l,悬浮物是7~17mg/l,电导率是12700~19200us/cm,可减少环境污染。专利cn201610578713.5公开了一种反渗透浓水的蒸发前处理方法,采用臭氧氧化处理及电化学氧化处理,再经过混凝、沉淀、过滤后,有效脱除反渗透浓水中的有机物,有利于提高蒸发处理的效率。专利cn201810450189.2及专利cn201820706387.6公开了一种浓盐水中的有机物与盐的分离工艺及其专用设备,将浓盐水进行预处理、反渗透膜分离、有机分离膜分离、臭氧氧化处理的处理过程。通过多种工
艺组合,有效提高设备处理浓盐水的效率,实现浓盐水中有机物与盐的有效分离,得到不含或极少含有机物的浓盐水。再经过后续工艺处理后,能够得到品质较高的氯化钠盐与硫酸钠盐,实现资源化利用,从而实现了废水的零排放。专利cn201811022668.0公开了一种垃圾渗滤液的反渗透浓水处理方法,反渗透浓水再进行絮凝催化处理后,出水通过沉淀池进行泥水分离,将上清液进行内置式超滤后,出水进入ed系统进行脱盐,得到的脱盐水进入臭氧催化氧化装置后将出水回流至原垃圾渗滤液生化系统,得到的浓盐水进入活性炭吸附罐后外排或蒸干零排。该发明不仅可将反渗透浓水中的有机物和盐分进行有效分离,还可大幅提高有机物的可生物降解性,有效降低反渗透浓水中污染物浓度。专利cn201610094307.1公开了一种反渗透浓盐水的催化氧化处理方法,将反渗透浓盐水通入到臭氧接触氧化塔中,向塔中加入复合多元氧化剂,反渗透浓盐水在臭氧接触氧化塔内与连续曝气的臭氧、流态化臭氧氧化催化剂和复合多元氧化剂进行充分接触反应,反应时间为10~80min,增强了气、液、固三相之间的传质效果,大幅提高臭氧氧化催化剂的催化效率。专利cn201911283303.8公开了一种焦化废水反渗透浓盐水的处理方法,该方法首先向焦化废水反渗透浓盐水加入预处理剂以进行预处理,过滤后将澄清液进行臭氧催化氧化,降低废水中的有机污染物。
8.反渗透浓水含盐量高,电导率较大,电催化氧化或强化的电催化氧化技术也是一种处理反渗透浓水的有效技术,专利cn201510711239.4公开了一种超声波强化电催化氧化处理反渗透浓水的装置及方法,该方法通过强化电催化氧化系统降解反渗透浓水中的有机污染物,电解过程中产生垢渣通过沉淀区实现泥水分离,该发明强化了电催化氧化处理反渗透浓水中的有机污染物的能力,提高了系统运行效率和稳定性。
9.采用臭氧催化氧化法、臭氧催化氧化法、光电fenton试剂氧化法、超声fenton试剂氧化法、湿式空气催化氧化法、湿式过氧化氢氧化法、超临界水氧化法、电催化氧化法等高级氧化法,虽然能够有效去除反渗透浓水中的难降解有机污染物,但是资源和能量消耗较高,工程设备投资相对较大、运行成本相对较高。同时,有些添加了氧化剂的高级氧化法中,氧化剂的残留对出水cod的指标测定存在很大的干扰。
10.虽然反渗透浓水的含盐量高,一般性的微生物比较难以存活和繁殖,但生物氧化在反渗透浓水的深度处理中也有应用,专利cn201610144524.7公开了一种反渗透浓盐水的蒸发前处理方法,采用在反渗透浓盐水中加入固定化高耐盐cod降解菌进行氧化处理,成本相对较低。专利cn201610145038.7公开了一种反渗透浓盐水的生物处理方法,采用在反渗透浓盐水中加入固定化高耐盐cod降解菌的同时,再加入复合增效组分,进行曝气处理,提高了反渗透浓盐水中有机污染物的处理效率。专利cn201410179127.4公开了一种冷轧反渗透浓盐水的处理系统和处理方法,冷轧反渗透浓盐水经过板式换热器降温后进入纳米零价铁渣反应器除重金属,然后通过ph曝气还原调节池进入一体化反硝化脱cod生化池去除总氮和有机物,最后进入混凝沉淀池,混凝沉淀后的冷轧反渗透浓盐水可达标排放。专利cn201410505690.6提供了一种冷轧反渗透浓盐水的净化处理方法,采用混凝沉淀结合黄花鸢尾生物反应器对反渗透浓盐水进行处理,提高了反渗透浓盐水中cod、tn、tp的去除率。采用生物氧化工艺降解处理反渗透浓水中的有机污染物,主要是曝气生物滤池,生物接触氧化池等,处理成本相对较低,但是在高盐环境中,微生物很难存活及生长,对反渗透浓水中的难降解有机污染物的去除效率不高。
11.随着材料科学与工程的进步,进一步的膜浓缩过滤技术也得到工程应用,研究者采用电渗析或高压膜浓缩工艺对反渗透浓水进行深度处理,专利cn201811200967.9公开了一种高盐高cod废水处理零排放工艺及装置,采用超滤膜过滤装置对高盐高cod废水进行过滤,除去废水中悬浮物,然后采用电渗析处理装置,对超滤膜过滤装置的产水进行电渗析处理,分离得到高浓盐水和高cod淡水。专利cn201910393273.x公开了一种浓盐水零排放过程中高浓度有机物与盐的分离工艺及专用设备,将浓盐水进行预处理、有机分离膜分离、膜浓缩、冷冻结晶及二次有机分离膜分离过程,可有效提高设备处理浓盐水的效率,实现浓盐水零排放过程中有机物与盐的有效分离。专利201710763177.0公开了一种膜法、热法组合工艺处理煤化工高浓盐水的盐硝分离方法,该方法创造性地采用蒸汽冷凝液作为电渗析浓室进水,实现了煤化工高含盐废水中的有机物和盐的分离。采用高压膜浓缩工艺,难以解决膜污染和膜结垢的问题,并且有机物没有得到根本去除,只能做到近零排放,不利于零排放技术中废水的最终处理和资源的有效回收。
12.吸附技术基本不受反渗透浓水中高含盐量的影响,能够普适性或有针对性的吸附反渗透浓水中的有机污染物,处理过程容易控制,应用越来越广泛。专利cn201810808500.6公开了一种冷轧废水反渗透浓盐水处理装置和方法,主体装置包括树脂吸附柱、活性炭吸附
‑
再生装置、树脂再生液储罐以及树脂脱附液储罐。采用选择性离子交换树脂吸附去除废水中的硝酸盐,采用颗粒状椰壳活性炭吸附去除废水中的有机物,实现了出水的cod和总氮量满足排放标准的要求,不受浓盐水中高含盐量、高硬度等因素的影响。专利cn201510450713.2公开了一种煤化工浓盐废水的净化处理和纯盐回收工艺,在污水回用多级反渗透处理工艺后增设了吸附处理工序,对高浓度盐水中的有机物大分子和重金属进行吸附处理,在吸附处理工序后废水进入蒸发冷冻脱盐工序,最终达到零排放和资源有效化利用的目的。吸附法虽然对有机物去除效率较高,但存在吸附剂消耗量大和吸附剂二次污染的问题。
13.而且活性炭比表面积大,具有丰富的孔道结构,活性炭吸附技术可以有效的对反渗透浓水中的有机物进行吸附,但活性炭对反渗透浓水中的有机物饱和吸附量较小,活性炭更换周期频繁、投加量相对较大,运行费用高。同时,如果饱和的活性炭当作废物处理,还需要较高的处置费用。在高含盐环境中,臭氧催化氧化效率低,生成的羟基自由基被水体中大量的氯离子消耗掉,造成臭氧催化氧化反渗透浓水的效率很低。
14.综上所述,现有的反渗透浓水中有机污染物的脱除处理方法,一般存在工艺流程相对复杂,工程投资大、能耗大、操作难度大以及降解效率低、运行成本高等缺点。因此,亟需寻找一种操作相对简单、投资及运行成本低的处理工艺对反渗透浓水进行处理。
技术实现要素:15.本发明的目的是针对现有反渗透浓水中有机污染物的脱除技术中存在的缺点和不足,提供了一种臭氧催化氧化强化活性炭吸附的反渗透浓水处理工艺。
16.为了实现上述目的,本发明采用了如下技术方案:
17.一种臭氧催化氧化强化活性炭吸附的反渗透浓水处理工艺,其特征在于,采用的具体步骤如下:
18.步骤1,强化活性炭吸附:将一定量活性炭吸附剂投加到反渗透浓水中,搅拌均匀,
使活性炭充分分散到反渗透浓水中。同时将催化剂a和氧化剂b同时投加到反渗透浓水中;
19.步骤2,臭氧催化氧化强化活性炭吸附:在已经投加了催化剂a和氧化剂b的活性炭吸附单元中,投加通过臭氧发生器产生的臭氧,臭氧曝气搅拌,反应后混合溶液进入混凝沉淀池;
20.步骤3,混凝沉淀:在混凝沉淀池中,添加絮凝剂c和助凝剂d到反应后的混合溶液中,进行反应,通过絮凝、脱色、沉淀使固液分离,上清液进入后续的零排放蒸发系统进行处理处置或达标外排;
21.步骤4,活性炭再生:将混凝沉淀出的活性炭移送到反洗再生池,经过再生处理后循环回用于臭氧催化氧化强化活性炭吸附单元。
22.优选地,所述步骤1中的反渗透浓水的ph值6~9,cod
cr
含量为50~300mg/l,tds含量1000~10000mg/l。
23.优选地,所述步骤1中活性炭可以采用颗粒活性炭、粉末活性炭、煤质活性炭、椰壳活性炭、颗粒活性焦、粉末活性焦等中的一种或多种,投加量为反渗透浓水质量的0.1%~3.0%,反应时间为10min~120min。
24.优选地,所述步骤1中催化剂a可以是氯化亚铁、氯化铁、硫酸亚铁、硫酸铁、硝酸亚铁、硝酸铁、载铁的活性炭、载铁的活性三氧化二铝中的一种或多种,投加量30~300mg/l;氧化剂b可以是过氧化氢、过氧化钙、过氧化钠、过氧化钾、过硫酸钠、过硫酸铵、过硫酸钾中的一种或多种,投加量0~200mg/l。
25.优选地,所述步骤2中臭氧投加量为50~500mg/l,臭氧曝气反应停留时间为30~180min。
26.优选地,所述步骤3中混凝沉淀过程采用的絮凝剂c可以是聚合氯化铝、聚合氯化铁、聚合硫酸铁、聚合氯化铝铁、聚合硫酸铝铁中的一种或多种;助凝剂d可以是阳离子聚丙烯酰胺、阴离子聚丙烯酰胺、两性离子聚丙烯酰胺、非离子聚丙烯酰胺、聚丙烯酸钠、羧甲基纤维素钠中的一种或多种。絮凝剂c投加浓度为10~100mg/l,搅拌时间为2~10min,助凝剂d投加浓度为1~10mg/l,搅拌时间为10~60min。
27.优选地,所述步骤4中混凝沉淀出的活性炭再生方式可以是清水反洗再生、稀硝酸反洗再生、稀柠檬酸反洗再生、稀氢氧化钠反洗再生中的一种;反洗水含盐量相对较低,可以循环到厂区污水处理生化系统进行处理。
28.本发明通过臭氧催化氧化技术和活性炭吸附技术相结合,充分利用活性炭的吸附能力,将反渗透浓水中的有机物扩散吸附到活性炭的微孔孔道结构中,然后臭氧催化氧化产生的羟基自由基可以被吸附到低盐度的活性炭微孔结构孔道中,进行富集并高效降解有机污染物以。因此,臭氧催化氧化强化活性炭吸附可以起到良好的协同效应,提高活性炭的饱和吸附量、延长活性炭的使用周期及使用寿命、提高吸附效率以及提高反渗透浓水的深度处理效率,反洗水含盐量低,可以循环到生化系统进行处理。本发明能够高效的对反渗透浓水中有机污染物进行脱除,工艺流程相对简单,工程投资低、能耗低、操作容易、运行成本低等优点。
附图说明
29.图1为本发明提出的一种臭氧催化氧化强化活性炭吸附的反渗透浓水处理工艺流
程示意图;
30.图2为不同h2o2投加浓度下臭氧催化氧化强化活性炭吸附处理反渗透浓水的效果图。
具体实施方式
31.下面将结合本发明实施例中的附图,对本发明实施例中的技术方案进行清楚、完整地描述,显然,所描述的实施例仅仅是本发明一部分实施例,而不是全部的实施例。
32.如图1所示,本发明公开了一种臭氧催化氧化强化活性炭吸附的反渗透浓水处理工艺,具体步骤如下:
33.步骤1,强化活性炭吸附:将一定量活性炭吸附剂投加到反渗透浓水中,搅拌均匀,使活性炭充分分散到反渗透浓水中。同时将催化剂a和氧化剂b同时投加到反渗透浓水中;
34.步骤2,臭氧催化氧化强化活性炭吸附:在已经投加了催化剂a和氧化剂b的活性炭吸附单元中,投加通过臭氧发生器产生的臭氧,臭氧曝气搅拌,反应后混合溶液进入混凝沉淀池;
35.步骤3,混凝沉淀:在混凝沉淀池中,添加絮凝剂c和助凝剂d到反应后的混合溶液中,进行反应,通过絮凝、脱色、沉淀使固液分离,上清液进入后续的零排放蒸发系统进行处理处置或达标外排;
36.步骤4,活性炭再生:将混凝沉淀出的活性炭移送到反洗再生池,经过再生处理后循环回用于臭氧催化氧化强化活性炭吸附单元。
37.进一步,所述步骤1中的反渗透浓水的ph值6~9,cod
cr
含量为50~300mg/l,tds含量1000~10000mg/l。
38.进一步,所述步骤1中活性炭可以采用颗粒活性炭、粉末活性炭、煤质活性炭、椰壳活性炭、颗粒活性焦、粉末活性焦等中的一种或多种,投加量为反渗透浓水质量的0.1%~3.0%,反应时间为10min~120min。
39.进一步,所述步骤1中催化剂a可以是氯化亚铁、氯化铁、硫酸亚铁、硫酸铁、硝酸亚铁、硝酸铁、载铁的活性炭、载铁的活性三氧化二铝中的一种或多种,投加量30~300mg/l;氧化剂b可以是过氧化氢、过氧化钙、过氧化钠、过氧化钾、过硫酸钠、过硫酸铵、过硫酸钾中的一种或多种,投加量0~200mg/l。
40.进一步,所述步骤2中臭氧投加量为50~500mg/l,臭氧曝气反应停留时间为30~180min。
41.进一步,所述步骤3中混凝沉淀过程采用的絮凝剂c可以是聚合氯化铝、聚合氯化铁、聚合硫酸铁、聚合氯化铝铁、聚合硫酸铝铁中的一种或多种;助凝剂d可以是阳离子聚丙烯酰胺、阴离子聚丙烯酰胺、两性离子聚丙烯酰胺、非离子聚丙烯酰胺、聚丙烯酸钠、羧甲基纤维素钠中的一种或多种。絮凝剂c投加浓度为10~100mg/l,搅拌时间为2~10min,助凝剂d投加浓度为1~10mg/l,搅拌时间为10~60min。
42.进一步,所述步骤4中混凝沉淀出的活性炭再生方式可以是清水反洗再生、稀硝酸反洗再生、稀柠檬酸反洗再生、稀氢氧化钠反洗再生中的一种;反洗水含盐量相对较低,可以循环到厂区污水处理生化系统进行处理。
43.实施例1
44.一种臭氧催化氧化强化活性炭吸附的反渗透浓水处理工艺,本实施例所采用的主体处理单元为活性炭氧化吸附、混凝沉淀以及活性炭的反洗再生。实验用反渗透浓水水质指标为,ph值为8.09,水温25℃,codcr含量为82.16mg/l,tds含量3250mg/l,包括的盐类主要为氯化钠和硫酸钠。
45.包括如下步骤:
46.(1)氧化吸附:取1000ml反渗透浓水进行实验,实验反应柱直径50mm,高度1500mm。分别往反渗透浓水中投加粉末活性炭量为1.0g/l,同时投加七水合硫酸亚铁(feso4·
7h2o)投加量为60mg/l,往反渗透浓水水样中投加20mg/l的h2o2(过氧化氢溶液采用质量百分比浓度27.5%的工业级双氧水,使用时稀释到配置溶液的质量百分比浓度为10%)。采用空气源的臭氧发生器,产生的臭氧与空气的混合气体流量为1l/min,臭氧在混合气体中的含量2mg/l,开始反应,反应时间分别为45min,臭氧总投加量为90mg/l,反应结束后取上清液测cod
cr
值,反渗透浓水水样处理后的cod
cr
为23.42mg/l。
47.其他反应条件不变,改变不同h2o2投加浓度分别为0mg/l、2.5mg/l、5.0mg/l、7.5mg/l、10.0mg/l、12.5mg/l、15.0mg/l、17.5mg/l的情况下,臭氧催化氧化强化活性炭吸附处理反渗透浓水的效果图。实验结果证明了臭氧催化氧化能够有效地强化活性炭对反渗透浓水中的有机物的脱除效率。
48.(2)混凝沉淀:对氧化吸附反应后的水样进行混凝沉淀反应,聚合氯化铝投加浓度为30mg/l,搅拌时间为2min,阴离子聚丙烯酰胺(分子量为1600万)投加浓度为5.0mg/l,搅拌时间为30min,沉淀时间为30min,废水出水cod
cr
为21.11mg/l。混凝沉淀后的废水可以进入零排放蒸发系统或在对含盐量没有限制要求的区域环境中直接外排。
49.(3)反洗再生:上述混凝沉淀出的活性炭沉淀物,采用100ml清水进行反洗,反洗后的活性炭吸附孔道结构得到恢复,可以循环回用;反洗水含盐量低,tds含量47mg/l,可以循环到生化系统进行处理。
50.实施例2
51.一种臭氧催化氧化强化活性炭吸附的反渗透浓水处理工艺,本实施例所采用的主体处理单元为活性炭氧化吸附、混凝沉淀以及活性炭的反洗再生。实验用反渗透浓水水质指标为,ph值为6.99,水温25℃,cod
cr
含量为150.32mg/l,tds含量4550mg/l,包括的盐类主要为氯化钠和硫酸钠。
52.包括如下步骤:
53.(1)氧化吸附:取1000ml反渗透浓水进行实验,实验反应柱直径50mm,高度1500mm。分别往反渗透浓水中投加粉末活性炭量为0.5g/l加上1.5g/l粉末活性焦,同时投加七水合硫酸亚铁(feso4·
7h2o)投加量为90mg/l,往反渗透浓水水样中投加60mg/l的h2o2(过氧化氢溶液采用质量百分比浓度27.5%的工业级双氧水,使用时稀释到配置溶液的质量百分比浓度为10%)。采用空气源的臭氧发生器,产生的臭氧与空气的混合气体流量为3l/min,臭氧在混合气体中的含量2mg/l,开始反应,反应时间分别为35min,臭氧投加量为210mg/l。反应结束后取上清液测cod
cr
值,反渗透浓水水样处理后的cod
cr
为29.33mg/l。实验结果证明了臭氧催化氧化能够有效地强化活性炭对反渗透浓水中的有机物的脱除效率。
54.(2)混凝沉淀:对氧化吸附反应后的水样进行混凝沉淀反应,聚合硫酸铁投加浓度为50mg/l,搅拌时间为5min,阳离子聚丙烯酰胺(分子量为1000万)投加浓度为5.0mg/l,搅
拌时间为30min,沉淀时间为30min,废水出水cod
cr
为27.53mg/l。混凝沉淀后的废水可以进入零排放蒸发系统或在对含盐量没有限制要求的区域环境中直接外排。
55.(3)反洗再生:上述混凝沉淀出的活性炭沉淀物,采用100ml清水进行反洗,反洗后的活性炭吸附孔道结构得到恢复,可以循环回用;反洗水含盐量低,tds含量68mg/l,可以循环到生化系统进行处理。
56.实施例3
57.一种臭氧催化氧化强化活性炭吸附的反渗透浓水处理工艺,本实施例所采用的主体处理单元为活性炭氧化吸附、混凝沉淀以及活性炭的反洗再生。实验用反渗透浓水水质指标为,ph值为7.86,水温25℃,cod
cr
含量为230.11mg/l,tds含量6872mg/l,包括的盐类主要为氯化钠和硫酸钠。
58.包括如下步骤:
59.(1)氧化吸附:取1500ml反渗透浓水进行实验,实验反应柱直径50mm,高度1500mm。分别往反渗透浓水中投加粉末活性炭量为1.0g/l加上1.5g/l粉末活性焦,同时投加七水合硫酸亚铁(feso4·
7h2o)投加量为120mg/l及载铁的活性三氧化二铝固体粉末100mg/l,往反渗透浓水水样中投加100mg/l的h2o2(过氧化氢溶液采用质量百分比浓度27.5%的工业级双氧水,使用时稀释到配置溶液的质量百分比浓度为10%)。采用空气源的臭氧发生器,调节反应用的臭氧与空气的混合气体流量为3l/min,臭氧在混合气体中的含量2mg/l,开始反应,反应时间分别为90min,臭氧投加量为360mg/l。反应结束后取上清液测cod
cr
值,反渗透浓水水样处理后的cod
cr
为31.16mg/l。实验结果证明了臭氧催化氧化能够有效地强化活性炭对反渗透浓水中的有机物的脱除效率。
60.(2)混凝沉淀:对氧化吸附反应后的水样进行混凝沉淀反应,聚合氯化铝铁投加浓度为80mg/l,搅拌时间为3min,阴离子聚丙烯酰胺(分子量为1200万)投加浓度为5.0mg/l,搅拌时间为20min,沉淀时间为30min,废水出水cod
cr
为28.75mg/l。混凝沉淀后的废水可以进入零排放蒸发系统或在对含盐量没有限制要求的区域环境中直接外排。
61.(3)反洗再生:上述混凝沉淀出的活性炭沉淀物,采用200ml清水进行反洗,反洗后的活性炭吸附孔道结构得到恢复,可以循环回用;反洗水含盐量低,tds含量65mg/l,可以循环到生化系统进行处理。
62.如图2所示,为不同h2o2投加浓度下臭氧催化氧化强化活性炭吸附处理反渗透浓水的效果图。本发明能够高效的对反渗透浓水中有机污染物进行脱除,工艺流程相对简单,工程投资低、能耗低、操作容易、运行成本低等优点。活性炭比表面积大,具有丰富的孔道结构,活性炭吸附技术可以有效的对反渗透浓水中的有机物进行吸附,但活性炭对反渗透浓水中的有机物饱和吸附量较小,活性炭更换周期频繁、投加量相对较大,运行费用高。同时,如果饱和的活性炭当作废物处理,还需要较高的处置费用。在高含盐环境中,臭氧催化氧化效率低,生成的羟基自由基被水体中大量的氯离子消耗掉,造成臭氧催化氧化反渗透浓水的效率很低。本发明创新性的将臭氧催化氧化技术和活性炭吸附技术相结合,充分利用活性炭的吸附能力,将反渗透浓水中的有机物扩散吸附到活性炭的微孔孔道结构中,然后臭氧催化氧化产生的羟基自由基可以被吸附到低盐度的活性炭微孔结构孔道中,进行富集并高效降解有机污染物以。因此,臭氧催化氧化强化活性炭吸附可以起到良好的协同效应,提高活性炭的饱和吸附量、延长活性炭的使用周期及使用寿命、提高吸附效率以及提高反渗
透浓水的深度处理效率,反洗水含盐量低,可以循环到生化系统进行处理。
63.本发明通过臭氧催化氧化技术和活性炭吸附技术相结合,充分利用活性炭的吸附能力,将反渗透浓水中的有机物扩散吸附到活性炭的微孔孔道结构中,然后臭氧催化氧化产生的羟基自由基可以被吸附到低盐度的活性炭微孔结构孔道中,进行富集并高效降解有机污染物以。因此,臭氧催化氧化强化活性炭吸附可以起到良好的协同效应,提高活性炭的饱和吸附量、延长活性炭的使用周期及使用寿命、提高吸附效率以及提高反渗透浓水的深度处理效率,反洗水含盐量低,可以循环到生化系统进行处理。本发明能够高效的对反渗透浓水中有机污染物进行脱除,工艺流程相对简单,工程投资低、能耗低、操作容易、运行成本低等优点。
64.以上所述,仅为本发明较佳的具体实施方式,但本发明的保护范围并不局限于此,任何熟悉本技术领域的技术人员在本发明揭露的技术范围内,根据本发明的技术方案及其发明构思加以等同替换或改变,都应涵盖在本发明的保护范围之内。