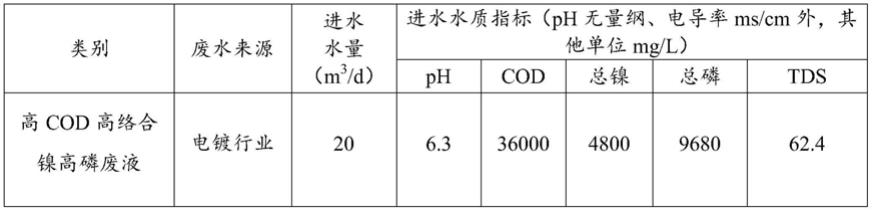
一种高cod高络合镍废水的处理工艺
技术领域
1.本发明涉及废液处理技术领域,具体涉及一种高cod高络合镍废水的处理工艺。
背景技术:2.镍是一种较昂贵的金属(价格是铜的2~4倍),此外它还是一种可致癌的重金属。电镀镍因其具有优异的耐磨性、抗蚀性、可焊性而被广泛应用于电镀生产中,其加工量仅次于镀锌,在整个电镀行业中居第二位。因此在电镀与印刷电路板制造过程中,有大量重金属废液产生,废液中的镍主要以离子形式存在,主要有游离态离子和络合态离子两种,其中络合态离子主要存在于ni
2+
与有机酸根、cn-、scn-、edta类物质、铵或胺类物质形成的络合物中。而近年来因化学镀液的大量使用,特别是化学镍废液,化学镍废液中含4~10g/l之重金属离子,且镀液中含大量螯合剂,故在废液处理上常造成相当困难。此外,因一些制程需要,电镀行业通常会有一些高cod高化学镍废液,且该废液中磷含量也较高,此种废液目前较难综合处理,大部分电镀行业都选择委外处理,且委外费用较高,另外,由于镍离子属于有价金属,有很高的回收价值,因此对电镀行业而言,不仅造成大量重金属的流失,也要承担高额的委外费用。
3.目前传统处理含重金属废水包括化学沉淀、电解、离子交换、吸附、膜分离、生物法等方法,其中最常采用的方法为沉淀法,即是于废水中加入沉淀剂,使废水中所含重金属离子形成化合物而沉淀。但此法产生大量重金属污泥,一般均以掩埋或固化法处理,但固化体可能产生稳定性不佳及流向监控不易等问题,加上污泥处理费用过高及土地取得不易等问题,因此目前重金属废液处理已朝着金属资源化回收的方向发展,不仅解决废液处理问题,而且可制造高价值的资源化产物,达到资源化回收的目的。
4.重金属离子回收方法,一般最常见的是电解法,目前技术已趋成熟,该法系利用直流电将废液中的金属离子沉积在阴极上,但只可以处理废水组成份单纯的高浓度金属废液,如废液中含螯合剂或废液成分很复杂,则无法使用电解法进行处理,其处理效率极低;此外,其它方法例如离子交换法、吸附法、膜分离技术均不适用于高浓度含镍废水的处理,而利用功能菌吸附或络合重金属离子沉淀形成污泥的生物法,目前发展不成熟,如何提高功能菌的反应效率、利用率以及降低功能菌培养成本等难题尚待解决。
技术实现要素:5.为解决上述问题,本发明提供了一种高cod高络合镍废水的处理工艺,针对废水中高cod、高络合镍进行分步高效去除:利用电化学氧化降解废水中高分子络合物,有效降废水中的cod;反应沉淀除镍,回收三氧化二镍;树脂塔去除废液中的总镍以及吸附残留的cod,使出水达到排放标准。整个工艺过程利用前后各步骤之间的关联和促进作用,使废液中的各组分得以高效去除,且可回收废液中的重金属镍,获得资源化产品三氧化二镍。
6.本发明提供了如下所述的技术方案:
7.本发明提供了一种高cod高络合镍废水的处理工艺,包括以下步骤:
8.(1)将废水通入电化学氧化槽中,加入过氧化氢,通电进行氧化还原反应;所述废水的总cod为30000~40000mg/l、总镍为4500~6000mg/l;
9.(2)将电化学氧化槽的出水进入ph调节池i,调节废水ph至8.5~9.5;
10.(3)将ph调节池i出水进入蓄热反应槽中,加入高铁酸盐和次氯酸水进行反应;
11.(4)将蓄热反应槽中反应液进入沉淀槽i中,沉淀析出三氧化二镍;
12.(5)将沉淀槽i出水进入树脂塔中,调节废水ph至5~6,经过树脂吸附处理后,将再生废液返回ph调节池i中,排放达标废水;所述达标废水的总cod<80mg/l、总镍<0.5mg/l。
13.进一步地,步骤(1)中,所述废水的ph为6~7。
14.进一步地,步骤(2)中,电化学氧化槽的出水中cod值小于2000mg/l。
15.进一步地,步骤(3)中,将高铁酸盐先溶于30%~32%的氢氧化钠溶液中得到溶解液,再将溶解液加入所述蓄热反应槽中。
16.高铁酸盐是一种集氧化、吸附、絮凝于一体的粉末状强氧化剂,直接添加不利于其与废水充分混合,且其适宜反应的条件为弱碱性,将高铁酸盐先溶于一定量液碱(30%~32%的氢氧化钠溶液)中再加入反应槽,有利于高铁酸盐与废水混合,使其能与废水中的ni充分反应,提高铁酸盐的利用效率。
17.进一步地,步骤(3)中,加入的高铁酸盐和次氯酸水的质量比为1.2~1.5:1。
18.蓄热反应槽中加入分子态次氯酸水,可增强高铁酸盐与废水中镍的反应速率以及提高镍的转化率。
19.进一步地,步骤(3)中,所述反应的温度为60~70℃;所述反应的时间不低于0.5h。
20.进一步地,步骤(4)中,所述三氧化二镍的质量占比为70%~75%,含水率《10%。
21.进一步地,步骤(5)中,沉淀槽i出水中总镍值小于80mg/l。
22.进一步地,步骤(5)中,当沉淀槽i的出水中总磷值为30~10000mg/l,将沉淀槽i的出水调节ph至9~10进入沉淀槽ii中,加入除磷剂进行絮凝沉淀,再将沉淀槽ii的出水进入树脂塔中。
23.进一步地,沉淀槽ii出水中总磷值小于30mg/l。
24.进一步地,步骤(5)中,所述树脂塔中树脂为含磺酸基的强酸性树脂或含羧酸基的弱酸树脂;采用树脂吸附处理含镍废水,操作简单,对环境无污染,吸附过程可逆,可实现水资源和金属镍的回收利用。
25.进一步地,上述工艺中,通过加入30%~32%的氢氧化钠溶液或盐酸溶液调节废水ph。
26.与现有技术相比,本发明的有益效果在于:
27.1.本发明提供了一种高cod高络合镍废水的处理工艺,针对废水中高cod、高络合镍进行分步高效去除:第一步是针对废液中高分子络合物(络合镍及其他高分子有机络合物)破络,释放废液中的镍为下一步除镍提供游离镍,同时将大部分cod降解为co2和h2o,还可降解部分总镍;第二步将废液中释放出来的大部分游离镍氧化为ni2o3,去除镍的同时还可以氧化分解部分cod;第三步将第二步反应得到的黑色沉淀物(主成分为ni2o3)分离出来,若废水中磷含量较高,采用除磷剂在碱性条件下高效除磷,去除废液中大部分磷,但出水总磷还不能达到排放标准;最后采用树脂吸附法,在酸性条件下去除废液中总镍,同时对废液中总磷、cod进一步吸附,使得出水达标排放。通过上述工艺中各步骤之间的关联和促进作
用,使废液中的高分子有机物、络合物镍及磷得以高效去除。
28.2.本发明提供的一种废水处理工艺,可有效回收废液中的重金属镍,得到资源化产品三氧化二镍,大幅度降低危废处理成本,同时实现资源利用最大化。
附图说明
29.图1为高cod高络合镍高磷废水治理工艺路线图。
具体实施方式
30.下面结合附图和具体实施例对本发明作进一步说明,以使本领域的技术人员可以更好地理解本发明并能予以实施,但所举实施例不作为对本发明的限定。
31.除非另有定义,本文所使用的所有的技术和科学术语与属于本发明的技术领域的技术人员通常理解的含义相同。本文中在本发明的说明书中所使用的术语只是为了描述具体的实施例的目的,不是旨在于限制本发明。本文所使用的术语“及/或”包括一个或多个相关的所列项目的任意的和所有的组合。
32.下述实施例中所使用的实验方法如无特殊说明,均为常规方法,所用的材料、试剂等,如无特殊说明,均可从商业途径得到。
33.本发明实施例中所处理的废水水质的各指标如下表1所示:
34.表1电镀废水水质指标
[0035][0036]
电镀水污染物排放标准中规定:cod<80mg/l,总镍<0.5mg/l,总磷<1mg/l。
[0037]
实施例1
[0038]
本实施例对上述电镀废水进行处理,主要包含以下步骤:
[0039]
(1)水量为20m3/d的高cod高络合镍高磷废液进入电化学氧化槽,向电化学氧化槽中加入533.3kg/d30%h2o2,通电发生电化学反应,反应完成后,出水cod可降至2000mg/l以下,总镍可降至3600mg/l左右,总磷可降至6000mg/l左右;
[0040]
(2)经电化学氧化槽处理后的出水进入ph调节池i,向ph调节池i
[0041]
中加入1430kg/d液碱(浓度为30%~32%)调节废水ph至9左右,然后进入蓄热反应槽,在蓄热反应槽中加入高铁酸盐溶解液(33.3kg/d高铁酸盐溶解于50kg/d 30~32%的液碱中)和24kg/d分子态次氯酸水,在60~70℃下反应0.5h;
[0042]
(3)经蓄热反应槽反应完成后进入沉淀槽i,沉淀析出黑色沉淀物,其主要成分为ni2o3,产生量约为280~310kg/d,纯度约70%~75%,含水率<10%。沉淀槽i出水中总镍<80mg/l,然后出水进入ph调节池ii,向ph调节池ii中加入164.4kg/d液碱(浓度为30%~32%)调节废水ph至9~10;
[0043]
(4)经ph调节池ii出水进入沉淀槽ii,然后向沉淀槽ii中加入467kg/d的高效除磷
剂,反应0.5h,沉淀槽ii出水中总磷<30mg/l;
[0044]
(5)经沉淀槽ii出水进入除镍树脂塔,向除镍树脂塔中加入470kg/d盐酸(浓度为30%~32%)调节废水ph至5~6,经树脂塔处理后再生废液量约为进水量的2%~3%,再生液返回ph调节池i再次循环提取镍,经树脂塔处理后出水水质各指标如下表2所示,满足达标排放要求。
[0045]
表2出水水质指标
[0046][0047]
实施例2调节高铁酸盐和分子态次氯酸水的添加量对沉淀槽ⅰ出水中总镍含量的影响
[0048]
本实施例在实施例(1)的基础上通过调节实施例1步骤(2)中高铁酸盐和分子态次氯酸水的添加量,其它条件不变,观察沉淀槽i出水总镍的含量,相应实施例的高铁酸盐和分子态次氯酸水的添加量以及对应沉淀槽i出水总镍的含量如表3所示:
[0049]
表3物质添加量及对应的出水总镍
[0050]
高铁酸盐添加量kg/m3次氯酸水添加量kg/m3沉淀槽ⅰ出水中总镍mg/l0.83250.66471.250.93051.6651.2782.081.572
[0051]
由上表可知,通过增加高铁酸盐和分子态次氯酸水的添加量,可降低沉淀槽i出水中总镍的含量;但添加量增加至一定量时,再增加添加量,对沉淀槽i出水总镍量的影响减小,推测是有与废水中总镍含量降低后,低浓度的镍与高铁酸盐反应速率大大降低;本实施例中当高铁酸盐的添加量为1.665kg/m3、分子态次氯酸水的添加量为1.2kg/m3时,效果与成本控制最佳。
[0052]
对比例1不添加分子态次氯酸水
[0053]
本实施例在实施例1基础上,在步骤(2)中仅加入高铁酸盐,不添加分子态次氯酸水,其它条件不变,反应后沉淀槽i出水中总镍约230mg/l,镍转化率不高,对后续的废水处理增加负担,且尾水无法达标排放。
[0054]
对比例2添加其它氧化剂取代高铁酸盐
[0055]
本实施例在实施例1基础上,在步骤(2)中加入30%h2o2或次氯酸钠,其它条件不变,反应后沉淀槽i出水中总镍>1000mg/l。
[0056]
对比例3调整反应温度
[0057]
本实施例在实施例1基础上,在步骤(2)中不加热在20~30℃下反应0.5h,其它条件不变,反应后沉淀槽i出水中总镍>2800mg。
[0058]
对比例4不对进入树脂塔内的废液ph进行调节
[0059]
本实施例在实施例1基础上,在步骤(5)中不加盐酸调节树脂塔中废水的ph,由沉
淀槽ii出水直接进入树脂塔中废水的ph为8.5~9.0,树脂塔处理后的出水不满足电镀水污染物排放标准。
[0060]
以上所述实施例仅是为充分说明本发明而所举的较佳的实施例,本发明的保护范围不限于此。本技术领域的技术人员在本发明基础上所作的等同替代或变换,均在本发明的保护范围之内。本发明的保护范围以权利要求书为准。