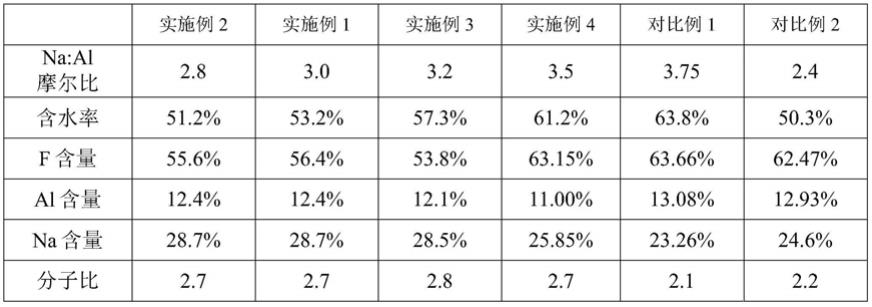
1.本发明涉及废水处理技术领域,更具体地说,涉及一种含氟废水中砂状冰晶石回收反应装置、回收装置及回收工艺。
背景技术:2.光能是一种清洁能源,光伏产业是基于半导体技术和新能源需求而兴起的朝阳产业,也是未来全球先进产业竞争的制高点。随着政策支持和技术进步,我国光伏产业成长迅速,装机量、发电量均不断提高。2020 年我国光伏发电量为2605kwh,同比增长16.2%,占总发电量比重3.5%,累计装机量为 253gw,光伏累计装机量连续六年居全球首位。然而,在光伏电池在制造过程中,会产生大量的含氟废水。含氟工业废水具有高毒性,高环境风险,对含氟废水的排放各国均有严格限制。各类光伏行业的含氟废水中,氟浓度从数百mg/l到数万mg/l,主要来源于晶圆蚀刻及石英清洗过程。
3.目前,常见的含氟废水处理方法主要沉淀法、吸附法、电絮凝法等、超滤-反渗透等。其中最常用的方法是钙盐沉淀法,使废水中的f-以caf2形式沉淀下来,然而通过钙盐沉淀法出水往往很难达标(低于10mg/l),出水f-在20mg/l~100mg/l左右,需要进一步处理,此外该过程中产生大量的氟化钙污泥,造成二次污染。絮凝法和吸附法常被用于钙盐中和沉淀之后,进一步处理低浓度的含氟废水,保证出水达标,但是絮凝法存在二次污染问题,吸附法存在再生频繁,处理水量小,操作要求高,处理成本高等问题,不适于处理水量较大和氟含量高的工业废水,只适用于低浓度含氟废水或经处理后氟离子浓度低于20mg/l的废水。近年来,纳滤、超滤、反渗透技术也被用于低浓度含氟废水处理,可以达到废水回用的目的,但也存在运行成本高,浓缩液处理难度大等问题,如中国专利:一种光伏废水处理系统及方法(cn109824166a),一种电子行业含氟废水深度处理及回用系统和工艺 (cn111268830a)。
4.氟资源作为一种宝贵的战略资源,氟的排放造成了氟资源的严重浪费。因此,如何实现氟资源的回收越来越受到人们的关注。如中国专利:一种含氟废水的处理及装置 (cn101941752b),一种高浓度含氟废水多级处理原位制备高纯caf2的方法 (cn105836783b)报告了从含氟废水中回收caf2的方法。与caf2相比,冰晶石价值更高,尤其适用于高浓度含氟废水中氟的回收。如中国专利:以含氟废水生产冰晶石之方法(申请号:cn01123585.3)报道了通过添加氢氧化铝和氢氧化钠,实现从废水中回收冰晶石的方法;中国专利:一种冰晶石生产方法(申请号:cn201010232877.5),采用氢氧化钠和氢氧化铝反应得到铝酸钠,然后再与含氟废水反应得到冰晶石产品等。所见报道中,主要以钠盐和铝盐与含氟废水直接反应,但是该方法所得的冰晶石粒径小,含水率高,回收成本高,限制了在工业中的推广应用。中国专利:一种利用含氟废水制备砂状冰晶石的方法及装置(申请号:cn201710071481.9),利用诱导结晶原理,采用流化床的方式,利用可溶性的钠盐、可溶性的铝盐与废水中的氟反应生成冰晶石,但是该方法采用流化床方式,采用废水大循环方式使
结晶颗粒流态化,一方面会导致处理能力变小,另一方面会使运行成本升高,不利于大规模推广应用。
技术实现要素:5.本发明针对现有技术含氟废水回收砂状冰晶石品质较差的技术问题,提供了一种含氟废水中砂状冰晶石回收反应装置、回收装置及回收工艺,通过回收反应装置中反应区、沉淀区以及回流管的合理布置,改善上述的技术问题。
6.为达到上述目的,本发明提供的技术方案为
7.本发明的一种含氟废水中砂状冰晶石回收反应装置,包括外筒、内筒和回流管;外筒套设于内筒的外部,外筒的底部密封设置,形成沉淀区;内筒空腔内形成反应区,所述反应区对应连通设置于沉淀区的上方;内筒的顶部设置有加药管和进水管连通至反应区,所述外筒内的底部,内筒的底部与外筒之间设置有连通部,外筒与内筒之间形成外流通道,连通部将反应区与外流通道之间进行连通;外流通道的顶部设置有出水管,出水管用于外流通道顶部的出水;所述回流管的回流入口设置于反应区底部位置,回流管的回流出口设置于反应区的上部;通过上述的反应装置,在反应区中可以进行稳定的反应,并且通过将反应区底部位置所形成的较小粒度的晶粒通过回流管回流至反应区的上部,使其作为晶核在反应区内进行诱导结晶,使得反应过程与诱导结晶过程在同一个反应器中完成,有利于最终回收粒径大、含水率低的冰晶石。
8.优选地,所述反应区内设置有搅拌器,所述搅拌器的设置有利于反应区内的充分反应,并且搅拌器有利于优化反应区内反应体系中结晶分布状态,有利于回收后的冰晶石具有较好的性质。
9.优选地,所述外流通道顶部的外筒上设置有出水堰,所述出水堰相对于外筒的外侧设置有出水管。
10.优选地,所述沉淀区的底部设置有放料管。
11.本发明的一种含氟废水中砂状冰晶石回收装置,包括加药罐、反应装置和集水箱,所述反应装置为上述的反应装置;所述加药罐通过管道与反应装置的加药管相连,集水箱通过管道与反应装置的进水管相连。
12.优选地,所述加药罐包括第一加药罐和第二加药罐,第一加药罐和第二加药罐分别通过管道与反应装置的进水管相连。
13.本发明的一种含氟废水中砂状冰晶石回收工艺,工艺中使用的反应装置为权利要求1~4 任一项所述的一种含氟废水中砂状冰晶石回收反应装置,先将含氟废水、铝酸钠溶液和碱溶液通入至反应区内进行反应,使回流管开始工作,将反应区底部的冰晶石通过回流管回流至反应区的上部进行诱导结晶,对沉淀至沉淀区的冰晶石进行回收;含氟废水处理后由外流通道排出。
14.优选地,通过碱溶液的加入量控制反应区内的溶液ph值在2~6。
15.优选地,所述碱溶液为氢氧化钠溶液,反应区内的溶液中na:al摩尔比为2.8~3.5,通过改变铝酸钠溶液与氢氧化钠的配比,实现回收冰晶石具有较好地分子比及粒径。
16.优选地,所述含氟废水的加入流量与回流管中回流流量之比为1:。
17.优选地,反应体系中固液比大30%
±
1%时,对沉淀区中的沉淀物进行放料,放料
至反应体系中固液比为10%
±
0.5%为止。
18.本发明中,利用诱导结晶的原理,采用铝酸钠溶液和氢氧化钠溶液为沉淀剂,与废水中的氟进行连续反应,反应过程中产生的结晶物作为晶种,自诱导产生砂状冰晶石进行回收。进一步地通过改变铝酸钠溶液与碱液的配比,实现回收冰晶石分子比及粒径的控制。本发明反应器采用一体化设计,使得反应过程与诱导结晶过程在同一个反应器中完成,克服了传统化学反应和结晶过程分离导致冰晶石回收含水率高、粒径小等技术难题。回收的冰晶石粒径大、含水率低,产品质量符合国家标准;可以实现含氟废水如光伏废水中氟资源的回收,且回收的冰晶石粒径大、含水率低,产品质量达到国家标准,可适用于不同浓度的含氟废水。
附图说明
19.图1是本发明中一种含氟废水中砂状冰晶石回收装置的结构示意图及其工艺流程图;
20.图2是本发明中一种含氟废水中砂状冰晶石回收反应装置的结构示意图;
21.图3是本发明中一种含氟废水中砂状冰晶石回收反应装置的俯视图;
22.图4是通过本发明装置及工艺回收的冰晶石产品电镜图。
23.示意图中的标号说明:
24.1、第一加药罐;2、第二加药罐;
25.3、反应装置;4、集水箱;5、加药管;6、进水管;7、外筒;7-1、沉淀区;8、内筒;8-1、反应区;9、出水管;10、放料管;11、回流管;11-1、回流入口;11-2、回流出口;12、出水堰;13、连通部;14、外流通道;15、搅拌器。
具体实施方式
26.为进一步了解本发明的内容,结合附图和实施例对本发明作详细描述。
27.本说明书附图所绘示的结构、比例、大小等,均仅用以配合说明书所揭示的内容,以供熟悉此技术的人士了解与阅读,并非用以限定本发明可实施的限定条件,故不具技术上的实质意义,任何结构的修饰、比例关系的改变或大小的调整,在不影响本发明所能产生的功效及所能达成的目的下,均应仍落在本发明所揭示的技术内容得能涵盖的范围内。同时,本说明书中所引用的如“上”、“下”、“左”、“右”、“中间”等用语,亦仅为便于叙述的明了,而非用以限定可实施的范围,其相对关系的改变或调整,在无实质变更技术内容下,当亦视为本发明可实施的范畴;除此之外,本发明的各个实施例之间并不是相互独立的,而是可以进行组合的。
28.实施例1
29.如图2~3所述,本发明的一种含氟废水中砂状冰晶石回收反应装置,其包括外筒7、内筒8和回流管11;外筒7套设于内筒8的外部,外筒7的底部密封设置,形成沉淀区7-1;内筒8空腔内形成反应区8-1,所述反应区8-1对应连通设置于沉淀区7-1的上方;内筒8的顶部设置有加药管5和进水管6连通至反应区8-1。本实施例中,所述内筒与外筒体积比为 1:1.3~1.8,本实施例中为1:1.5。
30.在反应过程中,将铝酸钠溶液和碱溶液通过加药管5加入至内筒8中,含氟废水通
过进水管6加入至内筒8中,当内筒8内反应体系充满后,铝酸钠溶液和碱溶液通过加药管5加入至反应区8-1后,与体系中由进水管6加入的含氟废水立即进行反应,生成冰晶石成分。
31.而反应区8-1中的冰晶石结晶后,会向下方沉降,在沉降过程中晶粒会不断地长大,直至沉淀区7-1。另外,本实施例中所述反应区8-1内设置有搅拌器15,所述搅拌器15的设置有利于反应区8-1内的充分反应,并且搅拌器15有利于优化反应区8-1内反应体系中结晶分布状态,有利于回收后的冰晶石具有较好的性质。本实施例中在反应区8-1上部设置有搅拌叶,在反应区8-1下部设置有搅拌叶,可以对反应区8-1中的反应体系进行搅拌均化,有利于反应以及诱导结晶的效果。所述反应区8-1上部设置的搅拌叶搅拌尺寸大于反应区8-1下部设置的搅拌叶。
32.本发明中,所述回流管11的回流入口11-1设置于反应区8-1底部位置,回流管11的回流出口设置于反应区8-1的上部,所述回流管11上设置有泵,通过所述泵的驱动,将反应区8-1底部位置含有小粒度晶粒的反应体系通过回流管11回流至反应区8-1的上部,使得反应区8-1的上部反应体系中进行诱导结晶,进而有利于冰晶石晶粒的长大,进行诱导结晶后的晶粒会向下方沉降,直至沉降至沉淀区7-1,沉淀区7-1呈圆锥形,所述沉淀区7-1的底部设置有放料管10,用于沉淀区7-1内冰晶石产品的放料。
33.所述外筒7内的底部,内筒8的底部与外筒7之间设置有连通部13,外筒7与内筒8之间形成外流通道14,连通部13将反应区8-1与外流通道14之间进行连通;外流通道14的顶部设置有出水管9,出水管9用于外流通道14顶部的出水;本实施例中,所述外流通道 14顶部的外筒7上设置有出水堰12,所述出水堰12相对于外筒7的外侧设置有出水管9,经过内筒8中的反应,氟离子浓度较低的处理后废水会由连通部13进入至外流通道14,再由外流通道14到达出水堰12,翻过出水堰12后到达出水管9,由出水管9排出。
34.通过上述的反应装置,在反应区8-1中可以进行稳定的反应,并且通过将反应区8-1底部位置所形成的较小粒度的晶粒通过回流管11回流至反应区8-1的上部,使其作为晶核在反应区8-1内进行诱导结晶,使得反应过程与诱导结晶过程在同一个反应器中完成,有利于最终回收粒径大、含水率低的冰晶石。需要说明的是,通过上述方式,在反应区8-1内,反应区8-1的底部的反应体系中含有大量生长到一定程度的冰晶石晶粒,反应区8-1的上部主要会发生大量的诱导反应,使得冰晶石开始大量结晶。
35.如图1所示,本发明的一种含氟废水中砂状冰晶石回收装置,包括加药罐、反应装置3 和集水箱4,所述反应装置3为上述的反应装置;所述加药罐通过管道与反应装置3的加药管5相连,集水箱4通过管道与反应装置3的进水管6相连。
36.本实施例中,所述加药罐包括第一加药罐1和第二加药罐2,第一加药罐1和第二加药罐2分别通过管道与反应装置3的进水管6相连,第一加药罐1和第二加药罐2中够可以分别放置铝酸钠与氢氧化钠。
37.所述集水箱4中放置有大量的含氟废水,由于本实施例中的反应装置3具有较高的反应效率,为提高处理效率,本实施例所述集水箱4中含氟废水水f-浓度为不低于2000mg/l。
38.本发明的一种含氟废水中砂状冰晶石回收工艺,工艺中使用的反应装置为上述的一种含氟废水中砂状冰晶石回收反应装置,使用的回收装置为上述的一种含氟废水中砂状冰晶石回收装置,先将含氟废水、铝酸钠溶液和碱溶液通入至反应区8-1内进行反应,使回
流管11 开始工作,将反应区8-1底部的冰晶石通过回流管11回流至反应区8-1的上部进行诱导结晶,对沉淀至沉淀区7-1的冰晶石进行回收;含氟废水处理后由外流通道14排出。
39.具体步骤为:
40.步骤一、待处理的含氟废水首先进入集水箱4,通过提升泵打入到反应装置3内部反应区8-1;
41.步骤二、同时向反应装置3反应区8-1投加铝酸钠和氢氧化钠溶液进行搅拌混合反应;回流管11开始回流工作,部分反应产生的冰晶石通过回流管11进入到反应区8-1上部,进行诱导结晶,促进晶核长大,另一部分反应产生的冰晶石通过底部沉淀区7-1的放料管10 进行冰晶石回收;上述过程中,通过碱溶液的加入量控制反应区8-1内的溶液ph值在 2~6,同时搅拌混合反应,转速不高于400r/min,反应时间为不低于20min;铝酸钠和氢氧化钠混合溶液中na:al摩尔比为2.6~4.0,本实施例中为na:al摩尔比为3.0。
42.另外,所述含氟废水的加入流量与回流管11中回流流量之比为1:0.8~1.2,本实施例中为1:1。
43.步骤三、对沉淀至沉淀区7-1的冰晶石进行回收;出水通过反应装置3的出水堰12经出水管9排出。需要说明的是,反应体系中固液比大30%
±
1%时,对沉淀区7-1中的沉淀物进行放料,放料至反应体系中固液比为10%
±
0.5%为止。本实施例回收后的冰晶石电镜图如图4所示,其相关性能参数为:f含量为56.4%,al含量为12.4%,na含量为28.7%,含水率为53.2%,分子比为2.7。
44.实施例2
45.本实施例基本同实施例1,不同之处在于:na:al摩尔比为2.8,本实施例最终生产得到的冰晶石参数为:f含量为55.6%,al含量为12.4%,na含量为28.7%,含水率为51.2%,分子比为2.7。
46.实施例3
47.本实施例基本同实施例1,不同之处在于:na:al摩尔比为3.2,本对比例最终生产得到的冰晶石参数为:f含量为53.8%,al含量为12.1%,na含量为28.5%,含水率为57.3%,分子比为2.8。
48.实施例4
49.本实施例基本同实施例1,不同之处在于:na:al摩尔比为3.5,本对比例最终生产得到的冰晶石参数为:f含量为63.15%,al含量为11.00%,na含量为25.85%,含水率为 61.2%,分子比为2.7。
50.对比例1
51.实施例基本同实施例1,不同之处在于:na:al摩尔比为3.75,本对比例最终生产得到的冰晶石参数为:f含量为63.66%,al含量为13.08%,na含量为23.26%,含水率为 63.8%,分子比为2.1。
52.对比例2
53.本对比例基本同实施例1,不同之处在于:na:al摩尔比为2.4,本对比例最终生产得到的冰晶石参数为:f含量为62.47%,al含量为12.93%,na含量为24.6%,含水率为50.3%,分子比为2.2。
54.将上述分别采用不同na:al摩尔比的实施例与对比例所生产的冰晶石参数如表1
所示。
[0055][0056]
由上表中的数据可见,na:al摩尔比的设置对最终所回收冰晶石的参数具有较大的影响,当na:al摩尔比选择在2.8~3.5时,整体冰晶石的参数较为优异,在该范围内,选择 2.8~3.5时,可以看出冰晶石的分子比为2.7~2.8,而超过3.5以后,情况发生改变,冰晶石的分子比出现下降。申请人通过大量试验以及机理分析后认为:提高na:al摩尔比有利于反应向正冰晶石方向进行,所以有利于分子比的提高,当na:al过高时,体系中naoh含量增高,反应体系ph升高,不利于正冰晶石的生成,总体上呈现分子比下降,因此na:al摩尔比需要在合理范围内进行设置。
[0057]
在上文中结合具体的示例性实施例详细描述了本发明。但是,应当理解,可在不脱离由所附权利要求限定的本发明的范围的情况下进行各种修改和变型。详细的描述和附图应仅被认为是说明性的,而不是限制性的,如果存在任何这样的修改和变型,那么它们都将落入在此描述的本发明的范围内。此外,背景技术旨在为了说明本技术的研发现状和意义,并不旨在限制本发明或本技术和本发明的应用领域。
[0058]
更具体地,尽管在此已经描述了本发明的示例性实施例,但是本发明并不局限于这些实施例,而是包括本领域技术人员根据前面的详细描述可认识到的经过修改、省略、例如各个实施例之间的组合、适应性改变和/或替换的任何和全部实施例。权利要求中的限定可根据权利要求中使用的语言而进行广泛的解释,且不限于在前述详细描述中或在实施该申请期间描述的示例,这些示例应被认为是非排他性的。在任何方法或过程权利要求中列举的任何步骤可以以任何顺序执行并且不限于权利要求中提出的顺序。因此,本发明的范围应当仅由所附权利要求及其合法等同物来确定,而不是由上文给出的说明和示例来确定。