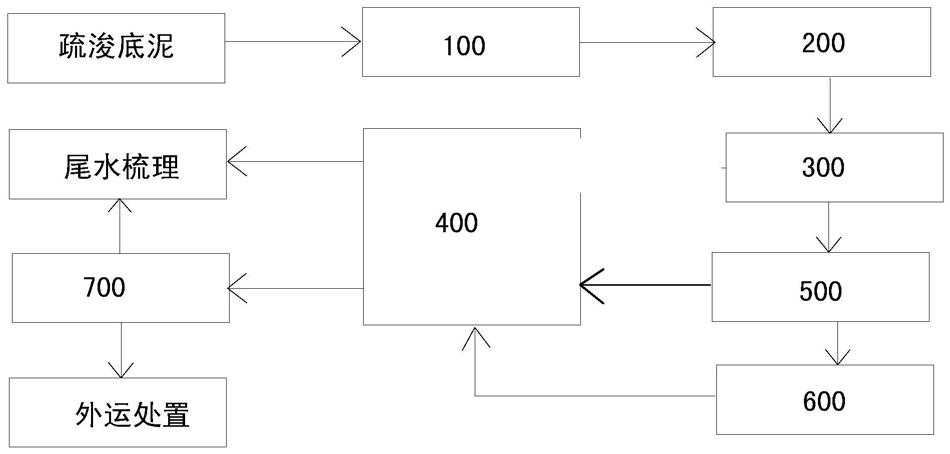
1.本发明涉及一种疏浚底泥处理设备,具体涉及一种用于疏浚底泥脱水固化的除杂系统及除杂方法。
背景技术:2.在环保疏浚底泥脱水固化施工工艺中,泥浆的除杂是生产线第一个工艺单元,也是保障整条生产线正常运转的关键环节。如泥浆中杂质不能完全清除,会导致进料泵、板框压滤机滤板损坏、等等一系列的问题,影响整条生产线的正常运转效率。
3.为了解决上述问题,我们做出了一系列改进。
技术实现要素:4.本发明的目的在于,提供一种用于疏浚底泥脱水固化的除杂系统及除杂方法,以克服现有技术所存在的上述缺点和不足。
5.一种用于疏浚底泥脱水固化的除杂系统,包括:消能沉杂池、第一格栅除污机、浓缩池、调节均化池、搅拌机、第二格栅除污机和板框压滤机,所述消能沉杂池通过排泥管与疏浚底泥连接,所述第一格栅除污机设于消能沉杂池下方,所述第一格栅除污机与浓缩池连接,所述浓缩池与搅拌机连接,所述搅拌机与第二格栅除污机和调节均化池连接,所述第二格栅除污机与调节均化池连接,所述板框压滤机与调节均化池连接。
6.进一步,所述消能沉杂池分为上层区域和下层区域,所述消能沉杂池包括:高压冲水喷头、链板除渣机、集渣斗、活动挡板和排泥管,所述高压冲水喷头设于消能沉杂池上层区域的上下两端,所述链板除渣机设于消能沉杂池上层区域的末端,所述集渣斗设于链板除渣机的下方,所述活动挡板设于消能沉杂池上层区域和下层区域之间的缺口处,所述排泥管设于消能沉杂池上层区域的前端,所述消能沉杂池的下层区域设有第一格栅除污机。
7.进一步,所述链板除渣机包括:传送带、链板和出泥口,所述传送带上设有链板,所述传送带与电机连接,所述电机设于出泥口内,所述出泥口设于链板除渣机的顶端,所述出泥口下方设有集渣斗。
8.进一步,所述第二格栅除污机设于搅拌机的出口,所述第二格栅除污机的道格栅间距为5mm。
9.进一步,所述高压冲水喷头与调节均化池连接。
10.进一步,所述活动挡板为锯齿形结构,所述消能沉杂池上层区域的池底为坡比为i=1∶40的斜坡,所述消能沉杂池下层区域的池底为坡比为i=1∶ 20的斜坡。
11.一种用于疏浚底泥脱水固化的除杂方法,包括以下步骤:
12.步骤1:运输待清洁污泥,将疏浚底泥通过排泥管进入消能沉杂池内;
13.步骤2:上层消能沉杂池除杂,通过高压冲水喷头将泥浆杂质冲刷到末端,再通过末端的链板除渣机将杂质进行收集,同时通过新增的锯齿形活动挡板用于悬浮物的去除;
14.步骤3:下层消能沉杂池除杂,泥浆通过活动挡板来到下层,通过第一格栅除污机
将细小的杂质进行除杂,泥浆在加速过程中进入浓缩池;
15.步骤4:沉淀浓缩转移,泥浆在浓缩池沉淀浓缩,通过供浆设备二次挖掘并输送至搅拌机,在搅拌机内增加清液;
16.步骤5:加入固化剂均匀搅拌后进入调节均化池,在进入均化池前通过第二格栅除污机进行二次搅拌,搅拌后泥浆进入调节均化池进行调节和均化反应;
17.步骤6:步骤5后,尾水进行处理,其他泥浆通过板框压滤机压成泥饼后运出。
18.本发明的有益效果:
19.本发明与传统技术相比,在除杂的流程上进行了改进,增强其消能沉杂效果,避免损坏格栅除污机;根据流程的变化,对除杂系统的结构部件进行改进。
附图说明:
20.图1为本发明的系统结构示意图。
21.图2为消能沉杂池的结构示意图。
22.图3为活动挡板的结构示意图。
23.图4为链板除渣机的结构示意图。
24.图5为传统除杂系统结构示意图。
25.图6为传统消能沉杂池的结构示意图。
26.附图标记:
27.消能沉杂池100、高压冲水喷头110、链板除渣机120、传送带121、链板122和出泥口123。
28.集渣斗130、活动挡板140和排泥管150。
29.第一格栅除污机200、浓缩池300、调节均化池400、搅拌机500、第二格栅除污机600和板框压滤机700。
具体实施方式
30.以下结合具体实施例,对本发明作进步说明。应理解,以下实施例仅用于说明本发明而非用于限定本发明的范围。
31.实施例1
32.图1为本发明的系统结构示意图。图2为消能沉杂池的结构示意图。图3为活动挡板的结构示意图。图4为链板除渣机的结构示意图。图5为传统除杂系统结构示意图。图6为传统消能沉杂池的结构示意图。
33.如图1-4所示,一种用于疏浚底泥脱水固化的除杂系统,包括:消能沉杂池100、第一格栅除污机200、浓缩池300、调节均化池400、搅拌机 500、第二格栅除污机600和板框压滤机700,消能沉杂池100通过排泥管与疏浚底泥连接,第一格栅除污机200设于消能沉杂池100下方,第一格栅除污机200与浓缩池300连接,浓缩池300与搅拌机500连接,搅拌机500与第二格栅除污机600和调节均化池400连接,第二格栅除污机600 与调节均化池100连接,板框压滤机700与调节均化池400连接。
34.消能沉杂池100分为上层区域和下层区域,消能沉杂池100包括:高压冲水喷头110、链板除渣机120、集渣斗130、活动挡板140和排泥管150,高压冲水喷头110设于消能沉
杂池100上层区域的上下两端,链板除渣机 120设于消能沉杂池100上层区域的末端,集渣斗130设于链板除渣机120 的下方,活动挡板140设于消能沉杂池100上层区域和下层区域之间的缺口处,排泥管150设于消能沉杂池100上层区域的前端,消能沉杂池100 的下层区域设有第一格栅除污机200。
35.链板除渣机120包括:传送带121、链板122和出泥口123,传送带121 上设有链板122,传送带121与电机连接,电机设于出泥口123内,出泥口 123设于链板除渣机120的顶端,出泥口123下方设有集渣斗130。
36.第二格栅除污机600设于搅拌机500的出口,第二格栅除污机600的道格栅间距为5mm。
37.高压冲水喷头110与调节均化池400连接。
38.活动挡板140为锯齿形结构,消能沉杂池100上层区域的池底为坡比为i=1∶40的斜坡,消能沉杂池100下层区域的池底为坡比为i=1∶20的斜坡。
39.一种用于疏浚底泥脱水固化的除杂方法,包括以下步骤:
40.步骤1:运输待清洁污泥,将疏浚底泥通过排泥管150进入消能沉杂池 100内;
41.步骤2:上层消能沉杂池除杂,通过高压冲水喷头110将泥浆杂质冲刷到末端,再通过末端的链板除渣机120将杂质进行收集,同时通过新增的锯齿形活动挡板140用于悬浮物的去除;
42.步骤3:下层消能沉杂池除杂,泥浆通过活动挡板140来到下层,通过第一格栅除污机200将细小的杂质进行除杂,泥浆在加速过程中进入浓缩池300;
43.步骤4:沉淀浓缩转移,泥浆在浓缩池300沉淀浓缩,通过供浆设备二次挖掘并输送至搅拌机,在搅拌机内增加清液;
44.步骤5:加入固化剂均匀搅拌后进入调节均化池400,在进入均化池前通过第二格栅除污机600进行二次搅拌,搅拌后泥浆进入调节均化池400 进行调节和均化反应;
45.步骤6:步骤5后,尾水进行处理,其他泥浆通过板框压滤机700压成泥饼后运出。
46.目前存在的问题,在本实施例中,疏浚底泥内杂质含量主要分两类,一类是长纤维状的,如塑料袋、编制袋、衣物等;另一类是硬质固体颗粒,如石块、砖块、玻璃等。为避免长纤维的杂质进入进料泵叶轮以及满足进入板框压滤机的泥浆中硬质固体杂质的直径需小于5mm的要求,因此需对疏浚底泥进行除杂。如图6所示,优化前除杂系统主要由消能沉杂池和格栅除污机共同组成,本实施例在未使用本发明技术之前,使用的是传统的沉杂池,其长20米,宽6米,高2米,池底面积约120平方米。疏浚挖泥船将挖掘后的泥浆泵送至消能沉杂池内,泥浆从泵送形式转变为平流的形式,消除了泥浆因泵送产生的冲击能量,同时大块杂质在沉杂池内沉淀,以此来达到消能和沉杂的目的,防止泥浆流过格栅除污机时对其产生冲击损坏。沉杂池出口处设置的宽为1.7米的第一级格栅间距为10毫米、第二级格栅间距为5毫米的回转式格栅除污机,主要用于清除泥浆中的悬浮物和直径大于5mm的硬质固体颗粒。湖内生活垃圾和杂质较多,沉杂池内沉积的杂质需采用挖机定期清捞,以确保沉杂池沉积杂质的空间。
47.目前这个系统存在以下缺陷:根据传统的环保疏浚施工工艺,为达到消能和沉杂效果,消能沉杂池一般设计为长条型,占地面积大,对场地要求较高。在本实施例中,由于场地空间有限,消能沉杂池尺寸设计较小,消能和沉杂效果相对较差,被输送至沉杂池的泥浆
及杂质对格栅除污机的冲击能量未能良好的消除。由于大块杂质的冲击,导致格栅除污机受冲击损坏,杂质直接流入浓缩池,影响工程施工进度和质量。
48.同时,消能沉杂池主要用于消除泥浆因泵送产生的能量,并将其转变为平流的形式以达到消能和沉杂的目的,因此大量的底泥和杂质在消能沉杂池内一并沉淀淤积。为不影响格栅机的正常工作,需定期(正常情况每周一次,泥土易堆积时增加频次)对消能沉杂池进行清理。大量底泥的沉淀增加了消能沉杂池的清理频次,由于消能沉杂池清理过程中需要绞吸挖泥船停止作业,并且每次清杂时,需人工使用高压水枪对淤积的底泥和杂质进行冲洗分离,被分离的杂质才能进行外运处理,所以高频次的清理过程不仅影响了施工的连续性而且增加了消能沉杂池的清理费用。
49.再者,本工程消能沉杂池长20米,宽6米,高2米,受消能沉杂池宽度及高度的影响,挖掘机在其外侧进行挖掘清理时,不仅清理困难、效率较低,而且清理效果不佳。消能沉杂池每次清理完毕后,池内依旧残留不少杂质和垃圾未清理干净,需要额外的人工将其清理干净,耗时长,影响工程施工进度。
50.最后,疏浚底泥脱水固化施工主要采用高压离心泵将均化池内调制好的泥浆输送至高效隔膜板框压滤机内,待板框压滤机内泥浆充盈率达到设计量的90%停止进料,并启动压榨系统,通过气压进行压榨深度脱水,直至泥饼含水率合格。实际生产过程中,进入板框压滤机滤板间的泥浆中依然存在不少杂质,由于杂质中含有硬质固体颗粒粒径大于滤板压榨过程中可接受的空间,导致压板无法压紧,甚至刺破滤布滤板,经常发生滤板之间跑料现象,不仅增加了设备维修成本,而且严重影响了泥饼的压榨效果。
51.而针对以上情况,本发明在工程后续进行了一系列的技术改造,主要包括:(1)克服消能沉杂池场地受限的问题,并增强其消能沉杂效果,避免损坏格栅除污机。(2)减少底泥在消能沉杂池内的淤积,降低对施工的影响和杂质的清理费用。(3)进一步过滤调制好的泥浆,防止杂质损坏板框压滤机滤板和滤布,保证供浆泵和压滤机正常运转。
52.首先,如图2所示,根据现场消能和沉杂情况分析,在原有消能沉杂池100的基础上进行结构优化。首先将格栅通道从右侧中间移至右侧下方位置,并向沉杂池内部延长,与消能沉杂池100最左侧围墙留有1.7米的距离,并在该处加设锯齿形的活动挡板140,将消能沉杂池分隔为上下层两个区域,以此来克服消能沉杂池因场地受限无法达到理想使用面积而未能充分消能的问题。上层区域为初次除杂区域:主要用于泥浆消能和大块杂质沉淀。中间加设的锯齿形的活动挡板140,主要用于悬浮物的去除,也可以根据杂质的沉淀情况,对挡板进行高度调节,加强泥浆过滤除杂的效果,避免了大块杂质损坏第一格栅除污机200。下层区域为二次除杂区域,泥浆从上层区域经过锯齿形的活动挡板140溢流至下层区域,再通过格栅除污机将细小的杂质进行除杂。本发明改变原有平底池底,将上层区域池底改成坡比为i=1∶40的斜坡,以便于杂质流向上层区域右侧并沉淀,下层区域池底改造成坡比为i=1∶20斜坡,增加上层区域溢流至下层区域的泥浆加速流过第一格栅除污机200并流入浓缩池300,以防止泥浆在通道内沉淀淤积。
53.为解决消能沉杂池100内淤泥沉淀过多和挖掘机清杂困难问题,现将消能沉杂池100做如下优化,如图1所示,首先,在上层区域底部两侧布设两排高压冲水喷头110,高压冲水水源取调节均化池400内的上清液,设计后由于形成了闭式循环,不会增加尾水处理量。其次,在上层区域右侧加装一台链板除渣机120,在其外侧放置可移动式的集渣斗130。高压
冲水对底部沉积的底泥和杂质混合物进行冲刷、稀释,使底泥和杂质在冲刷下分离的同时将杂质冲入链板除渣机120,杂质再通过链板除渣机120自动清杂至集渣斗130,集渣斗130盛满时可以及时运走处理。
54.如图5所示,传统的脱水固化施工工艺中只有消能沉杂池100一个除杂环节,然而即使消能沉杂池100能完全过滤所有的杂质,但在脱水固化环节中依旧存在杂质的风险。首先,因为泥浆需先经消能沉杂池100除杂后进入浓缩池300沉淀浓缩,再由供浆设备二次挖掘并输送至搅拌机500 加入固化剂均匀搅拌后进入调节均化池400,最后通过高压离心泵输送至板框压滤机内进行脱水固化。如果供浆设备操作不当,超挖扰动浓缩池底部的原状土。原状土内的杂质将导致泥浆发生二次污染。其次,在施工过程中对固化剂取样检验时发现,固化剂中含有小颗粒杂质存在。现根据工程实际情况,为避免消能沉杂池除杂不净、供浆设备超挖带来的二次污染以及加药过程中固化剂中含有杂质,本发明优化方案在搅拌机500出口至、调节均化池400中间加设一道格栅间距为5mm的第二格栅除污机600进行二次除杂,以确保所有进入板框压滤机的泥浆中无粒径大于滤板压榨过程中可接受的硬质固体存在,保证板框压滤机施工运转正常。
55.效果数据:本发明通过除杂池结构、功能优化和搅拌机出口加设格栅除污机后,使整个脱水固化工艺流程除杂系统得到了进一步的提升,降低了除杂池的清杂费用和板框压滤机的维修费用。
①
除杂池清杂费用优化前: 2020年4月-5月,除杂池共清杂8次,每次清杂需要1台挖机进行清理,耗时约6个小时,需3名工人进行协助。以挖掘机200元/小时,人工费40 元/小时,合计产生清杂费用为(200
×1×
6+40
×3×
6)
×
8=15360元,清杂耗时6
×
8=48小时。因此平均每月产生清杂费用15360
÷
2=7680元/月,每月清杂耗时约48
÷
2=24小时优化后:通过加设高压冲水系统和链板除杂机,使除杂池具备自动冲洗和清杂功能,节省了清杂所产生的台班费用和人工清理费用,清杂费用每月可节省7680元。绞吸船效率以每小时300m3进行计算,每月可增加产能约300
×
24=7200m3。
56.②
压滤机维修费用共投入使用10台hmzgf600/2000-u型板框压滤机,每台板框压滤机含滤板85块,滤布85套。优化前:2020年4月-5月,因破损而更换的滤板共计24块,滤布78套,滤板每次更换耗时约2小时,滤布每次更换耗时约0.5小时,以滤板5500元/块,滤布250元/套,合计产生压滤机维修费用5500
×
24+250
×
78=150750元,累计修理耗时约24
×ꢀ
2+78
×
0.5=87小时,平均每月产生压滤机维修费用为150750
÷
2=75375元/ 月,平均每月修理耗时约43.5小时。优化后:通过对泥浆的二次过滤,保证进入板框压滤机中的泥浆无杂质存在,避免了板框压滤机滤板和滤布损坏的风险,每月可节省压滤机维修费用75375元/月。板框压滤机效率以每小时9m3进行计算,每月可增加产能约9
×
43.5=391.5m3。工程工期为10 个月,除杂池的清杂费用和板框压滤机的维修费用可节省约(7680+75375)
ꢀ×
10≈84万元,节省清杂时间24
×
10=240小时,修理时间43.5
×
10=435 小时。而整个除杂系统的除杂池结构、功能优化和搅拌机出口加设格栅除污机所需投资费用约20万元。固本发明节省约64万元,并且绞吸船时间利用率提高约4.4%,绞吸船产能可增加约72000m3。平均每台板框压滤机完好率可提高0.6%,板框压滤机产能可增加约3915m3。
57.以上对本发明的具体实施方式进行了说明,但本发明并不以此为限,只要不脱离本发明的宗旨,本发明还可以有各种变化。