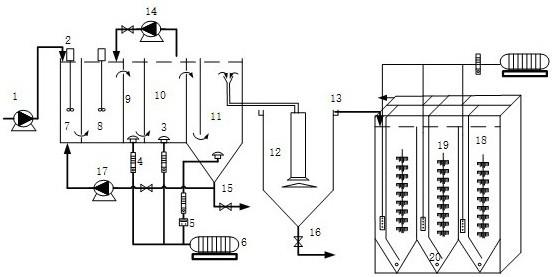
1.本发明属于工业废水处理装置及运行方法技术领域,具体涉及一种屠宰和肉类加工工业废水处理装置及其运行方法。
背景技术:2.随着肉类加工行业的迅猛发展,工业废水中屠宰及肉类加工废水所占的比例逐年上升,屠宰废水主要来自于圈栏冲洗、淋洗,屠宰后肉和内脏清洗水,屠宰设备及车间地面冲洗水等,属于高浓度有机废水,该污水具有水质水量变化大,有机物含量高,可生化性好的特点,废水中含有cod、ss、氨氮及肠胃病菌等多种污染因子,如不经无害化处理直接排放,必然对自然界氮循环和生态系统造成巨大危害。面对这一情况,经济高效的污水生物处理技术亟待开发和应用。
3.现阶段我国的工业污水处理厂脱氮除磷工艺普遍存在能耗高、去除效率低、运行不稳定的缺点,如何提高脱氮除磷的去除效果,节约能耗,以解决我国日益严重的水污染问题,在我国现阶段无论是从节省资金、提高污水处理效果和优化污水脱氮除磷工艺等方面都有重大的意义。
技术实现要素:4.本发明解决的技术问题是提供了一种能够高效低能耗去除废水中碳、氮、磷的屠宰和肉类加工工业废水处理装置及其运行方法。
5.本发明为解决上述技术问题采用如下技术方案,一种屠宰和肉类加工工业废水处理装置,其特征在于包括依次通过管道相连的改良a2/o反应器和snad自养脱氮反应器,其中改良a2/o反应器由依次通过管道相连的反应池和沉淀池组成,反应池内由隔板沿进水方向依次分隔成厌氧区、缺氧区、好氧区i、好氧区ii和间歇曝气区,相邻隔板的上部和下部分别设有通孔,用于实现废水在反应池各个反应区达到折流效果,好氧区ii通过混合液回流蠕动泵和管道与缺氧区连通实现混合液回流,间歇曝气区通过污泥回流蠕动泵和管道与厌氧区连通实现污泥回流,厌氧区和缺氧区内均设置有搅拌装置,好氧区i、好氧区ii及间歇曝气区内均设置有微孔曝气装置,该微孔曝气装置分别通过管路及流量计与空气泵连接,间歇曝气区内微孔曝气装置的进气管路上设有定时控制阀,运行期间通过空气泵及流量计控制曝气量使活性污泥处于悬浮状态,间歇曝气区通过定时控制阀控制曝气状态,间歇曝气区、沉淀池底部分别设置有排泥口、剩余污泥排放口;改良a2/o反应器中沉淀池溢流出水口通过管道与snad自养脱氮反应器进水口相连,snad自养脱氮反应器内由沿进水方向由隔板分隔成六个相互串联的折流板反应池,相邻的折流板反应池之间通过溢流堰相连通,每个折流板反应池内由折流板分隔成体积比为3:1且底部相连通的大小两个格室,其中大格室内悬挂填充有中空塑料圆环绑扎的醛化丝纤维填料,前三个小格室内设置有加热棒和微孔曝气装置,原水进入snad自养脱氮反应器后,水流在小格室内向下流动,在大格室内向上流,以达到泥水的充分混匀接触,反应过程中所产生的气体从snad自养脱氮反应器的顶部
逸出。
6.本发明所述的屠宰和肉类加工工业废水处理装置的运行方法,其特征在于具体步骤为:步骤s1:短程硝化反硝化工艺的启动以屠宰和肉类加工混合废水污水厂二次水解酸化池出水为进水原水,进水氨氮浓度为160mg/l,进水亚硝酸盐浓度小于1mg/l,进水硝酸盐浓度小于2mg/l,进水ph为6.8-7.5,进水温度为19-20℃,向改良a2/o生物反应器中接种sbr池活性污泥,污泥浓度为4000mlss/l,控制反应池好氧区i和好氧区ii的溶解氧量均为1.0mg/l,通过加热棒对反应池温度进行控制,试验运行期间,反应池厌氧区温度为20℃,反应池缺氧区温度为23℃,反应池好氧区i和好氧区ii温度均为23℃,沉淀池内污泥回流比为90%,反应池好氧区ii内混合液回流比为240%,水力停留时间为8h,污泥龄为5d,排泥量为4.5l/d,沉淀池内污泥和反应池好氧区ii内混合液分别通过蠕动泵泵至厌氧区和缺氧区进行连续培养,启动后期,进水水质变化,进水氨氮平均浓度达到190mg/l,进水cod负荷增大至1000mg/l,反应池间歇曝气区和沉淀池污泥反硝化严重,对此调整工艺运行参数,控制反应池好氧区i和好氧区ii的溶解氧量均为2mg/l,向反应池厌氧区补充活性污泥,经过20天连续培养,短程硝化成功启动,随后调整水力停留时间为10h,改良a2/o生物反应器稳定运行,出水亚硝态氮平均浓度为20mg/l,出水氨氮平均浓度低于50mg/l,出水cod平均浓度为190mg/l,本生物脱氮工艺中cod和氨氮的去除主要是由于微生物生长所需,运行期间控制低溶解氧,大大降低了反应器的能耗,同时为后续的自养脱氮创造了有利条件;步骤s2:反硝化除磷工艺启动在进水cod浓度为1000mg/l,进水氨氮浓度为190mg/l,进水总磷浓度为28-32mg/l,短程硝化成功启动并稳定运行的情况下,控制进水流量为7.0l/h,通过减少排泥量至1.5l/d,控制污泥龄为15d,水力停留时间为10h,降低反应池好氧区i和好氧区ii的溶解氧量至1.0-1.5mg/l,控制反应池好氧区ii内混合液回流比300%,经过20天连续培养,成功富集反硝化聚磷菌,反硝化除磷工艺达到稳定运行,反应池缺氧区对磷的吸收量高达20.5mg/l,对磷的吸收去除率达到64%,部分磷通过好氧吸收,最终出水总磷浓度在8.9mg/l左右,由此生物除磷反应器成功启动;步骤s3:自养脱氮工艺的启动自养脱氮工艺的启动阶段进水氨氮浓度保持在50mg/l,进水cod浓度保持在50mg/l,整个反应的ph值控制在7.5-8.0,温度为30℃,具体分为两个阶段:第一阶段是canon的启动,具体操作如下:将厌氧氨氧化污泥接种到折流板反应池中,对生物膜进行挂膜培养,实验进水采用人工配水,成分为:自来水、工业氯化铵、亚硝酸铵和碳酸氢钠,进水水质保持氨氮与亚硝酸盐浓度比为1:1,水力停留时间为10h,连续培养20天,反应器稳定运行,出水氨氮浓度小于4mg/l,出水氨氮平均去除率为91%,出水总氮的去除率达到81%以上,当出水总氮去除率连续7d达到80%以上,则自养脱氮反应器中的生物膜基本稳定,折流板反应池中的厌氧氨氧化生物膜已初步培养成功,随后停止向反应器中投加亚硝酸盐,与此同时向折流板反应池的前三个小格室进行曝气,曝气方式为顺水流方向渐减曝气,控制曝气量依次为0.4l/min、0.3 l/min和0.2 l/min,经过90天的驯化,出水氨氮浓度和出水总氮浓度分别为1.9mg/l和12.0mg/l,出水氨氮和出水总氮的平均去除率分别为94.5%和75%,反应器氮的去
除负荷达到0.21kg/m3·
d,当出水总氮去除率连续10天达到75%以上,认为canon启动成功;第二阶段是snad的启动,snad即短程硝化-厌氧氨氧化-反硝化在一个反应器内实现,试验原水模拟改良a2/o短程硝化反硝化除磷反应器的出水水质,为保证进水水质的稳定,用生活污水进行稀释,并按特定比例向生活污水中加入工业氯化铵、亚硝酸钠和小苏打,启动阶段控制前四个折流板反应池小格室曝气量依次为0.35l/min、0.3l/min、0.15l/min和0.1l/min,hrt为6h,试验连续进行130天,成功启动snad反应器,最终在出水稳定后,出水氨氮、出水总氮、出水cod的平均浓度分别为2mg/l、6mg/l、15mg/l,出水氨氮、出水总氮、出水cod的平均去除率分别为95%、85%、70%;步骤s4:短程硝化反硝化工艺和自养脱氮工艺的联用试验以屠宰和肉类加工工业废水综合调节池出水为原水,在综合调节池之前还有水解酸化池和隔油池,经过隔油池的油水分离,以及水解酸化池的水解作用,对来水的波动起到缓冲作用,进而实现反应器的进水水质相对比较稳定,从而保证改良a2/o与snad组合工艺的稳定运行,进水氨氮浓度为190mg/l左右,进水亚硝酸盐浓度小于1mg/l,进水总磷浓度为28-32mg/l,进水cod浓度为1000mg/l,进水ph为7.0左右,进水温度为23℃,改良a2/o短程硝化反硝化除磷反应器在处理污水的脱氮、除cod过程中起主要作用,snad反应器起到强化去除总氮、氨氮和cod的作用,进而有效保证出水水质,改良a2/o与snad组合工艺出水氨氮、出水cod的平均浓度分别为8.9mg/l、35mg/l,出水cod的平均去除率为96%,出水氨氮的平均去除率为95%,出水总氮的平均去除率为91.1%,出水总磷的平均去除率为65.7%。
7.本发明与现有技术相比具有以下优点和有益效果:本发明所述的屠宰和肉类加工工业废水处理装置包括改良a2/o反应器、snad自养脱氮反应器,在改良a2/o反应器中运行短程硝化反硝化除磷工艺,通过控制溶解氧和污泥龄完成aob的筛选和聚集,实现短程硝化的稳定运行,通过延长污泥龄富集反硝化聚磷菌,启动反硝化除磷工艺,最终使得大部分的氨氮、cod、tp在改良a2/o反应器除去。在snad反应器中运行短程硝化、厌氧氨氧化以及反硝化工艺,通过控制适宜的溶解氧和温度,实现氨氮和总氮的强化去除以及部分cod的去除。
8.本发明所述的屠宰和肉类加工工业废水处理装置以屠宰和肉类加工工业废水综合调节池出水为原水,通过改良a2/o与snad组合工艺后,出水氨氮、cod平均浓度分别为8.9mg/l、35mg/l,cod的平均去除率为96%,氨氮的平均去除率为95%,总氮的去除率为91.1%,总磷的平均去除率为65.7%,其中氨氮和cod的去除效果达到《肉类加工工业水污染物排放标准》(gb13457-92)的行业一级标准。
附图说明
9.图1是本发明中屠宰和肉类加工工业废水处理装置的结构示意图。
10.图中:1-进水泵,2-搅拌装置,3-微孔曝气装置,4-流量计,5-定时控制阀,6-空气泵,7-厌氧区,8-缺氧区,9-好氧区i,10-好氧区ii,11-间歇曝气区,12-沉淀池,13-溢流出水口,14-混合液回流蠕动泵,15-排泥口,16-剩余污泥排放口,17-污泥回流蠕动泵,18-折流板反应池,19-醛化丝纤维填料,20-加热棒。
具体实施方式
11.结合附图详细描述本发明的具体内容。如图1所示,一种屠宰和肉类加工工业废水
处理装置,其包括依次通过管道相连的改良a2/o反应器和snad自养脱氮反应器,其中改良a2/o反应器由依次通过管道相连的反应池和沉淀池12组成,反应池内由隔板沿进水方向依次分隔成厌氧区7、缺氧区8、好氧区i 9、好氧区ii 10和间歇曝气区11,相邻隔板的上部和下部分别设有通孔,用于实现废水在反应池各个反应区达到折流效果,好氧区ii 10通过混合液回流蠕动泵14和管道与缺氧区8连通实现混合液回流,间歇曝气区11通过污泥回流蠕动泵17和管道与厌氧区7连通实现污泥回流,厌氧区7和缺氧区8内均设置有搅拌装置2,好氧区i 9、好氧区ii 10及间歇曝气区11内均设置有微孔曝气装置3,该微孔曝气装置3分别通过管路及流量计4与空气泵6连接,间歇曝气区11内微孔曝气装置3的进气管路上设有定时控制阀5,运行期间通过空气泵6及流量计4控制曝气量使活性污泥处于悬浮状态,间歇曝气区11通过定时控制阀5控制曝气状态,间歇曝气区11、沉淀池12底部分别设置有排泥口15、剩余污泥排放口16;改良a2/o反应器中沉淀池溢流出水口通过管道与snad自养脱氮反应器进水口相连,snad自养脱氮反应器内由沿进水方向由隔板分隔成六个相互串联的折流板反应池18,相邻的折流板反应池18之间通过溢流堰相连通,每个折流板反应池18内由折流板分隔成体积比为3:1且底部相连通的大小两个格室,其中大格室内悬挂填充有中空塑料圆环绑扎的醛化丝纤维填料19,前三个小格室内设置有加热棒20和微孔曝气装置,原水进入snad自养脱氮反应器后,水流在小格室内向下流动,在大格室内向上流,以达到泥水的充分混匀接触,反应过程中所产生的气体从snad自养脱氮反应器的顶部逸出。
12.本发明所述的屠宰和肉类加工工业废水处理装置的运行方法,其具体步骤为:步骤s1:短程硝化反硝化工艺的启动以屠宰和肉类加工混合废水污水厂二次水解酸化池出水为进水原水,进水氨氮浓度为160mg/l,进水亚硝酸盐浓度小于1mg/l,进水硝酸盐浓度小于2mg/l,进水ph为6.8-7.5,进水温度为19-20℃,向改良a2/o生物反应器中接种sbr池活性污泥,污泥浓度为4000mlss/l,控制反应池好氧区i和好氧区ii的溶解氧量均为1.0mg/l,通过加热棒对反应池温度进行控制,试验运行期间,反应池厌氧区温度为20℃,反应池缺氧区温度为23℃,反应池好氧区i和好氧区ii温度均为23℃,沉淀池内污泥回流比为90%,反应池好氧区ii内混合液回流比为240%,水力停留时间为8h,污泥龄为5d,排泥量为4.5l/d,沉淀池内污泥和反应池好氧区ii内混合液分别通过蠕动泵泵至厌氧区和缺氧区进行连续培养,启动后期,进水水质变化,进水氨氮平均浓度达到190mg/l,进水cod负荷增大至1000mg/l,反应池间歇曝气区和沉淀池污泥反硝化严重,对此调整工艺运行参数,控制反应池好氧区i和好氧区ii的溶解氧量均为2mg/l,向反应池厌氧区补充活性污泥,经过20天连续培养,短程硝化成功启动,随后调整水力停留时间为10h,改良a2/o生物反应器稳定运行,出水亚硝态氮平均浓度为20mg/l,出水氨氮平均浓度低于50mg/l,出水cod平均浓度为190mg/l,本生物脱氮工艺中cod和氨氮的去除主要是由于微生物生长所需,运行期间控制低溶解氧,大大降低了反应器的能耗,同时为后续的自养脱氮创造了有利条件;步骤s2:反硝化除磷工艺启动在进水cod浓度为1000mg/l,进水氨氮浓度为190mg/l,进水总磷浓度为28-32mg/l,短程硝化成功启动并稳定运行的情况下,控制进水流量为7.0l/h,通过减少排泥量至1.5l/d,控制污泥龄为15d,水力停留时间为10h,降低反应池好氧区i和好氧区ii的溶解氧量至1.0-1.5mg/l,控制反应池好氧区ii内混合液回流比300%,经过20天连续培养,成功富
集反硝化聚磷菌,反硝化除磷工艺达到稳定运行,反应池缺氧区对磷的吸收量高达20.5mg/l,对磷的吸收去除率达到64%,部分磷通过好氧吸收,最终出水总磷浓度在8.9mg/l左右,由此生物除磷反应器成功启动;步骤s3:自养脱氮工艺的启动自养脱氮工艺的启动阶段进水氨氮浓度保持在50mg/l,进水cod浓度保持在50mg/l,整个反应的ph值控制在7.5-8.0,温度为30℃,具体分为两个阶段:第一阶段是canon的启动,具体操作如下:将厌氧氨氧化污泥接种到折流板反应池中,对生物膜进行挂膜培养,实验进水采用人工配水,成分为:自来水、工业氯化铵、亚硝酸铵和碳酸氢钠,进水水质保持氨氮与亚硝酸盐浓度比为1:1,水力停留时间为10h,连续培养20天,反应器稳定运行,出水氨氮浓度小于4mg/l,出水氨氮平均去除率为91%,出水总氮的去除率达到81%以上,当出水总氮去除率连续7d达到80%以上,则自养脱氮反应器中的生物膜基本稳定,折流板反应池中的厌氧氨氧化生物膜已初步培养成功,随后停止向反应器中投加亚硝酸盐,与此同时向折流板反应池的前三个小格室进行曝气,曝气方式为顺水流方向渐减曝气,控制曝气量依次为0.4l/min、0.3 l/min和0.2 l/min,经过90天的驯化,出水氨氮浓度和出水总氮浓度分别为1.9mg/l和12.0mg/l,出水氨氮和出水总氮的平均去除率分别为94.5%和75%,反应器氮的去除负荷达到0.21kg/m3·
d,当出水总氮去除率连续10天达到75%以上,认为canon启动成功;第二阶段是snad的启动,snad即短程硝化-厌氧氨氧化-反硝化在一个反应器内实现,试验原水模拟改良a2/o短程硝化反硝化除磷反应器的出水水质,为保证进水水质的稳定,用生活污水进行稀释,并按特定比例向生活污水中加入工业氯化铵、亚硝酸钠和小苏打,启动阶段控制前四个折流板反应池小格室曝气量依次为0.35l/min、0.3l/min、0.15l/min和0.1l/min,hrt为6h,试验连续进行130天,成功启动snad反应器,最终在出水稳定后,出水氨氮、出水总氮、出水cod的平均浓度分别为2mg/l、6mg/l、15mg/l,出水氨氮、出水总氮、出水cod的平均去除率分别为95%、85%、70%;步骤s4:短程硝化反硝化工艺和自养脱氮工艺的联用试验以屠宰和肉类加工工业废水综合调节池出水为原水,在综合调节池之前还有水解酸化池和隔油池,经过隔油池的油水分离,以及水解酸化池的水解作用,对来水的波动起到缓冲作用,进而实现反应器的进水水质相对比较稳定,从而保证改良a2/o与snad组合工艺的稳定运行,进水氨氮浓度为190mg/l左右,进水亚硝酸盐浓度小于1mg/l,进水总磷浓度为28-32mg/l,进水cod浓度为1000mg/l,进水ph为7.0左右,进水温度为23℃,改良a2/o短程硝化反硝化除磷反应器在处理污水的脱氮、除cod过程中起主要作用,snad反应器起到强化去除总氮、氨氮和cod的作用,进而有效保证出水水质,改良a2/o与snad组合工艺出水氨氮、出水cod的平均浓度分别为8.9mg/l、35mg/l,出水cod的平均去除率为96%,出水氨氮的平均去除率为95%,出水总氮的平均去除率为91.1%,出水总磷的平均去除率为65.7%,其中氨氮和cod的去除效果达到《肉类加工工业水污染物排放标准》(gb13457-92)的行业一级标准。
13.以上显示和描述了本发明的基本原理,主要特征和优点,在不脱离本发明精神和范围的前提下,本发明还有各种变化和改进,这些变化和改进都要求落入本发明的保护范围之内。