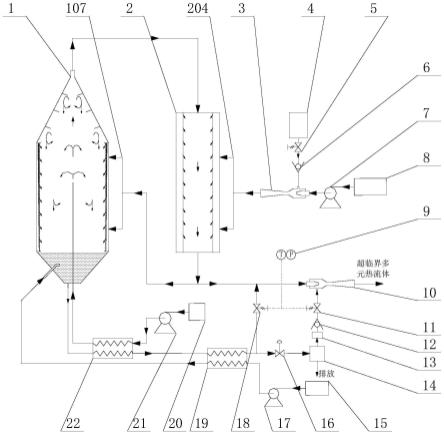
1.本发明涉及能源环境技术领域,特别是涉及一种采油废水处理及超临界多元热流体发生系统。
背景技术:2.稠油由于粘度大、流动性差而开采困难,传统的稠油开采技术包括化学剂降粘及热力降粘。利用热力降粘的开采方式主要有蒸汽驱、蒸汽吞吐等方式。该方式主要利用注汽锅炉产生蒸汽进行稠油热采,但由于蒸汽成本高,而且在水资源短缺和水价昂贵的地区,高昂的水处理费用进一步加大了蒸汽成本。
3.多元热流体开采技术是指水蒸气辅助n2、co2等气体进行的一种复合式吞吐技术,该技术利用火箭发动机高压燃烧的原理,将高压空气和柴油(或天然气)注入发生器,通过燃烧将注入其中的水进行汽化,燃烧后产生的高温高压n2、co2和水蒸汽混合后,成为多元热流体。该技术兼具气体混相驱(氮气驱、二氧化碳驱)和热力采油(蒸汽吞吐、蒸汽驱)的特点,不仅具有常规热采特征,而且具有气体降黏和膨胀的特性,可有效提高单井增产效果。
4.现有油田开采过程中会产生大量的采油废水,该类废水含有大量的有机物、无机盐,对生态产生了巨大的影响。此外,无论是陆地或海洋等开采环境,水资源的需求量大而相应的环境淡水水资源紧缺,成本高。
技术实现要素:5.针对现有技术存在的问题,本发明提供一种通过超临界水气化采油废水得到富氢燃料气体实现采油废水的高效处理,富氢燃料气体再进行超临界水氧化产生超临界多元热流体供给稠油开采,实现采油废水处理及稠油高效开采的采油废水处理及超临界多元热流体发生系统。
6.为了实现上述目的,本发明采用如下技术方案:
7.一种采油废水处理及超临界多元热流体发生系统,包括超临界水气化反应器,所述超临界水气化反应器的产物出口管连接于超临界水氧化反应器,所述超临界水气化反应器的底部设有废水注入管,采油废水由所述废水注入管注入所述超临界水气化反应器发生超临界水气化反应,气化产物由所述产物出口管进入所述超临界水氧化反应器,所述超临界水氧化反应器的侧面连接于第一引射器,所述第一引射器连接于空气储罐和纯水罐,纯水作为工作流体注入所述第一引射器,空气储罐的空气作为被引射流体进入所述第一引射器,纯水和空气在所述第一引射器内形成高压气水混合物,注入所述超临界水氧化反应器,所述超临界水氧化反应器底部分别连接于所述超临界水气化反应器和第二引射器,所述第二引射器连接于二氧化碳储罐,所述超临界水氧化反应器的氧化产物一部分作为热源进入所述超临界水气化反应器中持续补热,另一部分作为所述第二引射器的工作流体,二氧化碳作为所述第二引射器的被引射流体,氧化产物和二氧化碳在所述第二引射器内形成多元热流体,供给油田驱采。
8.进一步,所述超临界气化反应器包括同轴设置的第一承压外壳和第一多孔内壳,所述第一承压外壳的侧面设有热源注入口,所述热源注入口连接于所述超临界水氧化反应器底部,所述超临界水氧化反应器的氧化产物由所述热源注入口进入所述第一承压外壳和第一多孔内壳之间,并渗入所述第一多孔内壳内。
9.进一步,所述第一承压外壳包括从上至下连接的上锥形段、圆柱段及下锥形段,所述上锥形段内壁设有多层同轴圆锥挡板。
10.进一步,所述超临界水氧化反应器包括同轴设置的第二承压外壳和第二多孔内壳,所述第二多孔内壳和所述第二承压外壳之间的环隙形成冷却通道,所述第二承压外壳侧壁设有冷却液注入口,所述冷却液注入口连接于所述第一引射器。
11.进一步,所述空气储罐与所述第一引射器之间设有第一流量调节阀和第一单向阀。
12.进一步,所述废水注入管由所述超临界水气化反应器的底部延伸中部,所述废水注入管连接于第一预热器,所述第一预热器连接于废水增压泵,所述废水增压泵连接于废水罐,采油废水由所述废水罐经所述废水增压泵增压,通过所述第一预热器预热后进入所述废水注入管,由所述废水注入管顶部喷出进行超临界水气化反应。
13.进一步,所述超临界水气化反应器底部一侧设有浓盐水排出管,所述浓盐水排出管连接于所述第一预热器,所述第一预热器连接于第二预热器,所述第二预热器连接于气液分离器,所述气液分离器连接于所述二氧化碳储罐,所述第二预热器与所述气液分离器之间设有背压阀,浓盐水经过两次换热后通过所述背压阀降至常压时进入所述气液分离器,分离的二氧化碳气体进入所述二氧化碳储罐,分离的液体排放或后续处理。
14.进一步,所述第二预热器与所述背压阀之间设有旁路与所述第二引射器连接,所述旁路上设有第二流量调节阀。
15.进一步,所述二氧化碳储罐与所述第二引射器之间设有第二单向阀和第三流量调节阀,所述第三流量调节阀和所述第二流量调节阀与温度压力信号器连接,可单独或联动调节。
16.进一步,所述超临界水气化反应器的中下部设有冷却水注入管,所述冷却水注入管连接于所述第二预热器,所述第二预热器连接于冷却水增压泵,所述冷却水增压泵连接于冷却水罐,所述冷却水罐中的冷却水通过所述冷却水增压泵增压,并经所述第二预热器预热后从所述冷却水注入管进入所述超临界水气化反应器。
17.本发明的有益效果:
18.采油废水由废水注入管注入超临界水气化反应器发生超临界水气化反应,气化产物由产物出口管进入超临界水氧化反应器,纯水和空气在第一引射器内形成的高压气水混合物进入超临界水氧化反应器内发生超临界水氧化反应,氧化产物一部分作为气化反应的热源,另一部分作为多元热流体进行驱油,且超临界水气化反应器底部排出的低温流体和分离出的二氧化碳可与多元热流体进行混合,通过调节流量,形成不同温度、压力及组分的多元热流体,适应不同类型和条件的油田进行驱采。本发明通过超临界水气化采油废水得到富氢燃料气体实现采油废水的高效处理,富氢燃料气体再进行超临界水氧化产生超临界多元热流体供给稠油开采,实现了采油废水处理及稠油高效开采的能量循环。
附图说明
19.图1为本发明采油废水处理及超临界多元热流体发生系统的结构示意图;
20.图2为图1中超临界水气化反应器的结构示意图;
21.图3为图1中超临界水氧化反应器的结构示意图;
22.图中,1—超临界水气化反应器、101—第一承压外壳、102—第一多孔内壳、103—上锥形段、104—圆柱段、105—下锥形段、106—产物出口管、107—热源注入口、108—废水注入管、109—冷却水注入管、110—浓盐水排出管、111—圆锥挡板、112—上固定环、113—下固定环、2—超临界水氧化反应器、201—第二承压外壳、202—第二多孔内壳、203—冷却通道、204—冷却液注入口、3—第一引射器、4—空气储罐、5—第一流量调节阀、6—第一单向阀、7—纯水增压泵、8—纯水罐、9—温度压力信号器、10—第二引射器、11—第三流量调节阀、12—第二单向阀、13—二氧化碳储罐、14—气液分离器、15—冷却水罐、16—背压阀、17—冷却水增压泵、18—第二流量调节阀、19—第二预热器、20—废水罐、21—废水增压泵、22—第一预热器。
具体实施方式
23.下面将结合本发明实施例中的附图,对本发明实施例中的技术方案进行清楚、完整地描述,显然,所描述的实施例仅仅是本发明的一部分实施例,而不是全部的实施例。基于本发明中的实施例,本领域普通技术人员在没有作出创造性劳动前提下所获得的所有其他实施例,都属于本发明保护的范围。
24.需要说明,本发明实施例中所有方向性指示(诸如上、下、左、右、前、后
……
)仅用于解释在某一特定姿态(如附图所示)下各部件之间的相对位置关系、运动情况等,如果该特定姿态发生改变时,则该方向性指示也相应地随之改变。
25.如图1,本发明提供一种采油废水处理及超临界多元热流体发生系统,包括超临界水气化反应器1,超临界水气化反应器1的产物出口管106连接于超临界水氧化反应器2,超临界水气化反应器1的底部设有废水注入管108,采油废水由废水注入管108注入超临界水气化反应器1发生超临界水气化反应,气化产物(富氢燃料气体)由产物出口管106进入超临界水氧化反应器2,在超临界氧化反应器2内发生超临界水氧化反应,氧化产物一部分作为热源进入超临界水气化反应器1中持续补热,另一部分作为多元热流体进行驱油,且超临界水气化反应器1底部排出的低温流体和分离出的二氧化碳可与多元热流体进行混合,通过调节流量,形成不同温度、压力及组分的多元热流体,适应不同类型和条件的油田进行驱采,实现了采油废水处理及稠油高效开采的能量循环。
26.如图1及图2,超临界水气化反应器1包括同轴设置的第一承压外壳101和第一多孔内壳102,第一承压外壳101包括从上至下连接的上锥形段103、圆柱段104及下锥形段105,其中下锥形段105为倒锥形。上锥形段103顶部中心设有产物出口管106,圆柱段104的侧壁设有热源注入口107,热源注入口107连接于多个热源注入管,热源注入管均匀设置于圆柱段的轴向和圆周方向,在本实施例中,热源注入口在圆柱段的轴向和圆周方向分别均匀布置2-4根热源注入管,使热源均匀注入超临界水气化反应器1内。下锥形段105的中下部设有冷却水注入管109,冷却水注入管109的出口朝下。下锥形段105底部中心设有废水注入管108,废水注入管108向上延伸至圆柱段104的上部,由于废水注入管108深入超临界水气化
反应器1的长度,使得废水在超临界水气化反应器1内进一步预热后喷出,进而进行初步超临界水气化反应。下锥形段105一侧还设有浓盐水排出管110。
27.第一多孔内壳102设置于圆柱段104内侧,与圆柱段104上下端平齐,第一多孔内壳102的壳壁均匀设有多个小孔,热源由热源注入口107进入第一承压外壳101和第一多孔内壳102之间,并由第一多孔内壳102的小孔渗入内部。第一多孔内壳102的顶部通过上固定环112连接于圆柱段104的顶部,第一多孔内壳102的底部通过下固定环113连接于圆柱段104的底部,圆柱段104、第一多孔内壳102、上固定环112及下固定环113之间形成加热保护环隙。优选的,上固定环112和下固定环113为弹性件,便于实现第一多孔内壳102的安装、固定和密封。在本实施例中,第一多孔内壳102材质包含耐温防腐蚀的陶瓷、钛合金、奥氏体合金等,可为粉末烧结、编织型,第一多孔内壳102的孔隙率为10-40%,孔径为10-50μm,以实现热源沿圆周均匀分布,且避免沉积无机盐和焦炭堵塞多孔通道。
28.优选的,第一多孔内壳102的壁厚从上至下逐渐降低,形成倒锥形,倾斜角度β为75~85
°
,以实现高温热源的注入量从上至下逐渐增压,弥补反应温度从上至下逐渐下降的趋势。
29.优选的,上锥形段103设有多层同轴圆锥挡板111,圆锥挡板111与水平方向的夹角α为20~80
°
,采油废水由废水注入管108喷出后,进行初步超临界水气化反应,反应产物经重力及圆锥挡板111的惯性分离作用,实现气固分离,富含氢气的燃料产物从产物出口管106排出。通过超临界水气化反应器1实现高效的气固分离并形成清洁的富氢气体燃料,便于后续超临界水氧化反应过程高效和清洁的进行。
30.如图1及图3,超临界水氧化反应器2包括同轴设置的第二承压外壳201和第二多孔内壳202,第二多孔内壳202和第二承压外壳201之间的环隙形成冷却通道203,第二承压外壳201侧壁设有冷却液注入口204,冷却液注入口204连接于第一引射器3。第一引射器3分别连接于空气储罐4和纯水罐8,空气储罐4与第一引射器3之间设有第一流量调节阀5和第一单向阀6,纯水罐8与第一引射器3之间设有纯水增压泵7,纯水罐8中的纯水经纯水增压泵7增压后作为工作流体注入第一引射器3,纯水增压后的压力比废水增压后的压力大1-5mpa。空气储罐4中的空气经第一调节阀5和第一单向阀6后作为被引射流体进入第一引射器3,纯水和空气在第一引射器3内形成高压气水混合物,从超临界水氧化反应器2侧面的冷却液注入口204注入,通过第二多孔内壳202实现径向流体的均匀分布及输入。空气中的氧气流量为废水中有机物完全氧化所需氧气的1-1.2倍,富氢燃料产物和氧气在超临界水氧化反应器2内逐步发生超临界水氧化反应,形成高温高压的混合产物从超临界水氧化反应器2底部出口排出。出口反应产物温度为500-700℃,形成超临界水并含有大量二氧化碳、氮气和少量氧气的混合介质。空气从径向输入,即氧化所需的氧气沿轴向均匀分布并注入,有机物的氧化反应也沿着轴线逐步开展,使有机物的反应热有序释放,避免反应热的集中释放。双壳结构避免第二承压外壳201的过热,且富含空气的冷却水对第二多孔内壳202壁面进行冲刷冷却防护,进一步控制超临界水氧化反应器2的安全。
31.超临界水氧化反应器2底部分别连接于超临界水气化反应器1侧面的热源注入口107和第二引射器10,第二引射器10连接于二氧化碳储罐13,二氧化碳储罐13与第二引射器10之间设有第二单向阀12和第三流量调节阀11,超临界水氧化反应器2的氧化产物一部分作为热源进入超临界水气化反应器1中持续补热,另一部分作为第二引射器10的工作流体,
二氧化碳作为第二引射器10的被引射流体,氧化产物和二氧化碳在第二引射器10内形成多元热流体,供给油田驱采。
32.一部分反应产物通过热源注入口107的若干根热源注入管注入加热保护环隙,并通过第一多孔内壳102均匀渗入超临界水气化反应器1内部。该侧面注入的热源流体,一方面通过冲刷对第一多孔内壳102内部进行保护,避免反应过程的腐蚀、盐沉积及超临界水气化反应的结焦等问题。另一方面由于超临界水气化反应的吸热特性,反应温度会逐渐下降影响反应效率和速率,而侧面注入流体的高温特性,可对超临界水气化反应进行均匀持续补热,促进有机物的气化反应。再者,由于侧面注入流体的径向速度,与反应物的轴向速度耦合,进而可强化中心气化反应的传热传质,进一步加快反应。最后,由于热源流体中含有少量的氧气,在超临界水条件下可提供更多的活性反应基团(如oh.等),可促使有机物发生部分氧化反应,加速有机物的分解进而形成更多的富氢燃料气体产物。超临界水氧化反应器2中产生的二氧化碳,结合空气中的氮气共同进入超临界水气化反应器1,后续进一步富集再循环返回超临界水氧化反应器2,由于自身的不反应和稀释冷却特性,可减缓超临界水氧化反应器2中的反应热释放,避免超临界水氧化反应器2的过热。而氧气的循环利用不仅加速气化,而且使整体系统在低过氧量系数条件下高效运行,可大大降低系统的运行成本。
33.超临界水气化反应器1的底部的废水注入管108连接于第一预热器22,第一预热器22连接于废水增压泵21,废水增压泵21连接于废水罐20,采油废水由废水罐20经废水增压泵21增压至23mpa以上,通过第一预热器22预热后进入废水注入管108,由废水注入管108顶部喷出进行超临界水气化反应。废水有机物浓度在1-30wt.%,无机盐含量在1-10wt.%。由于废水注入管106深入超临界水气化反应器1的长度,使得废水可在超临界水气化反应器1内进一步预热后喷出,进行超临界水气化反应。反应产物经重力及圆锥挡板111的惯性分离作用,实现气固分离,形成富含氢气的燃料产物,从产物出口管106排出。
34.超临界水气化反应器1中下部的冷却水注入管109连接于第二预热器19,第二预热器19连接于冷却水增压泵17,冷却水增压泵17连接于冷却水罐15,冷却水罐15中的冷却水通过冷却水增压泵17增压至23mpa以上,并经第二预热器19预热后从冷却水注入管109进入超临界水气化反应器1,超临界水气化反应器1下部进而形成冷却区,冷却区可实现无机盐的冷却和溶解,避免超临界水气化反应器1的堵塞并有利于后续的分离。
35.超临界水气化反应器1冷却区的浓盐水排出管110连接于第一预热器22,第一预热器22连接于第二预热器19,第二预热器19连接于气液分离器14,气液分离器14连接于二氧化碳储罐13,第二预热器19与气液分离器14之间设有背压阀16,废水中的无机盐在反应过程中析出并落入超临界水气化反应器1下部的冷却区,且下部冷却区会溶解吸收部分氧化产生的二氧化碳,共同形成浓盐水,浓盐水先进入第一预热器22对废水进行预热,然后经过第二预热器19对冷却水进行预热,将剩余热量回收,经过两次换热后通过背压阀16降至常压时进入气液分离器14,分离的高纯度二氧化碳气体进入二氧化碳储罐13进行后续利用,分离的液体排放或后续处理。
36.第二预热器19与背压阀16之间设有旁路与第二引射器10连接,旁路上设有第二流量调节阀18。第二流量调节阀18和第三流量调节阀11与温度压力信号器9连接,可单独或联动调节,实现多元热流体的温度、压力和组分的协同调节,进而形成不同参数的多元热流体,可针对不同类型和条件的油田进行驱采。
37.本发明通过超临界水气化采油废水得到富氢燃料气体实现采油废水的高效处理,富氢燃料气体再进行超临界水氧化反应产生超临界多元热流体,供给稠油开采,另外一部分作为热源补充超临界水气化反应,其剩余能量通过溶盐水排出分别作为废液的预热和冷却水的预热热源,形成高效的能量利用系统。
38.以上实施例仅用以说明本发明的技术方案而非限制,尽管参照较佳实施例对本发明进行了详细说明,本领域技术人员应当理解,可以对本发明的技术方案进行修改或者等同替换,而不脱离本技术方案的宗旨和范围,其均应涵盖在本发明的权利要求范围内。