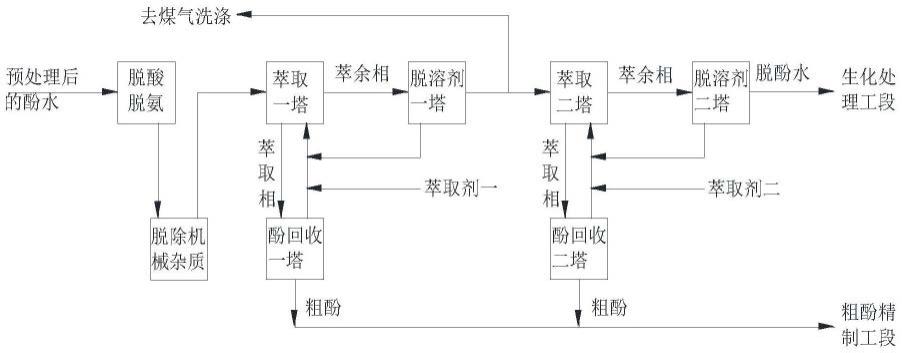
1.本发明涉及废水处理技术领域,尤其是涉及一种含酚废水萃取脱酚方法。
背景技术:2.煤化工是以煤炭为原料进行不同化学产品的加工,煤化工项目耗水量巨大,废水产生量也很高,每处理完1吨煤炭大约会产生1吨含酚废水。煤化工废水中总酚含量可高达5000mg/l以上,而且成分复杂,既有单元酚,又有多元酚,环境危害大,是必须脱除的主要污染物之一。
3.目前,萃取脱酚对单元酚的脱除率较高,可达99%以上,但受到现有萃取剂脱酚能力不足的限制,多元酚的脱除率也仅70%左右,尤其是对苯二酚,导致最终出水总酚浓度不达指标,大约350~800mg/l。所以,选择合适的萃取剂是提高废水萃取脱酚效率的关键。萃取剂必须考虑其对单元酚和多元酚的溶解度、水溶性以及能耗、价格、操作难易等问题。
4.因此,提供一种对酚的脱除效率高的含酚废水萃取脱酚方法是非常必要的。
技术实现要素:5.有鉴于此,本发明要解决的技术问题在于提供一种含酚废水萃取脱酚方法,本发明提供的脱酚方法对酚的脱除效率高。
6.本发明提供了一种含酚废水萃取脱酚方法,包括如下步骤:
7.a)含酚废水预处理后,进入汽提脱酸脱氨塔,进行脱酸、脱氨、脱除机械杂质处理,得到脱酸脱氨后的酚水;
8.b)将脱酸脱氨后的酚水采用第一萃取剂进行萃取脱酚,得到一级萃取脱酚废水;
9.c)将一级萃取脱酚废水采用第二萃取剂进行萃取脱酚,得到二级萃取脱酚废水。
10.优选的,步骤a)所述含酚废水单元酚含量为2000~8000mg/l、多元酚含量为1000~5000mg/l,总氨量为6000~20000mg/l,cod为20000~40000mg/l,ph值为10~12。
11.优选的,步骤b)所述第一萃取剂为二异丙醚dipe。
12.优选的,步骤c)所述第二萃取剂为酮-醇协同萃取剂;所述酮类选自甲基正丙基酮、甲基异丙基酮或甲基异丁基酮;所述醇类选自正丙醇、异丙醇或异丁醇的一种;
13.所述酮类和醇类的体积比为2:1~4:1。
14.优选的,所述第一萃取剂和脱酸脱氨后的酚水的体积比为1:4~1:10;所述萃取参数为:常压,萃取温度为25~40℃。
15.优选的,骤a)所述预处理具体为:含酚废水经重力沉降除油预处理;
16.步骤b)或步骤c)中所述萃取在萃取塔中进行,所述萃取塔为转盘塔、筛板塔或填料塔。
17.优选的,所述一级萃取脱酚废水总酚含量为400~1000mg/l,cod为2000~5000mg/l;
18.所述二级萃取脱酚废水总酚含量小于300mg/l。
19.优选的,步骤a)所述脱酸脱氨后的酚水的ph值为5~9。
20.优选的,所述步骤b)具体为:
21.将脱酸脱氨后的酚水采用第一萃取剂进行萃取脱酚,得到萃取相和萃余相;萃取相进入酚回收一塔,分离萃取剂和粗酚;萃余相进入溶剂回收一塔,回收溶于其中的萃取剂,得到一级萃取脱酚废水;一级萃取脱酚废水总量的1/4~3/4回流作为煤气洗涤水,剩余一级萃取脱酚废水进行第二级萃取;萃取剂循环使用。
22.优选的,所述步骤c)具体为:
23.将一级萃取脱酚废水采用采用第二萃取剂进行萃取脱酚,得到萃取相和萃余相;萃取相进入酚回收二塔,分离萃取剂和粗酚;萃余相进入溶剂回收二塔,回收溶于其中的萃取剂,得到二级萃取脱酚废水;萃取剂循环使用。
24.与现有技术相比,本发明提供了一种含酚废水萃取脱酚方法,包括如下步骤:a)含酚废水预处理后,进入汽提脱酸脱氨塔,进行脱酸、脱氨、脱除机械杂质处理,得到脱酸脱氨后的酚水;b)将脱酸脱氨后的酚水采用第一萃取剂进行萃取脱酚,得到一级萃取脱酚废水;c)将一级萃取脱酚废水采用采用第二萃取剂进行萃取脱酚,得到二级萃取脱酚废水。本发明以两种不同的溶剂作为萃取剂分别作用于所述两级萃取脱酚。在提高脱酚效率的基础上降低系统能耗,具有脱酚率高、溶剂用量小、能耗低的优点,能提高对多元酚的脱除效率,降低溶剂回收能耗,使脱酚废水达到生化处理的水质要求,总酚浓度控制到300mg/l以内。
附图说明
25.图1为本发明具体实施例的工艺流程示意图。
具体实施方式
26.本发明提供了一种含酚废水萃取脱酚方法,本领域技术人员可以借鉴本文内容,适当改进工艺参数实现。特别需要指出的是,所有类似的替换和改动对本领域技术人员来说是显而易见的,它们都属于本发明保护的范围。本发明的方法及应用已经通过较佳实施例进行了描述,相关人员明显能在不脱离本发明内容、精神和范围内对本文的方法和应用进行改动或适当变更与组合,来实现和应用本发明技术。
27.本发明提供了一种含酚废水萃取脱酚方法,包括如下步骤:
28.a)含酚废水预处理后,进入汽提脱酸脱氨塔,进行脱酸、脱氨、脱除机械杂质处理,得到脱酸脱氨后的酚水;
29.b)将脱酸脱氨后的酚水采用第一萃取剂进行萃取脱酚,得到一级萃取脱酚废水;
30.c)将一级萃取脱酚废水采用第二萃取剂进行萃取脱酚,得到二级萃取脱酚废水。
31.本发明提供的含酚废水萃取脱酚方法首先对含酚废水预处理。
32.本发明对于所述含酚废水不进行限定,优选为高浓度含酚废水,单元酚含量为2000~8000mg/l、多元酚含量为1000~5000mg/l,总氨量为6000~20000mg/l,cod为20000~40000mg/l,ph值为10~12。也可以为其它的高浓度含酚废水。
33.所述预处理具体为:含酚废水经重力沉降除油预处理。
34.含酚废水预处理后,进入汽提脱酸脱氨塔,进行脱酸、脱氨、脱除机械杂质处理,得到脱酸脱氨后的酚水;所述脱酸脱氨后的酚水的ph值为5~9。
35.本发明对于所述汽提脱酸脱氨塔不进行限定,本领域技术人员熟知的即可。
36.将脱酸脱氨后的酚水采用第一萃取剂进行萃取脱酚,得到一级萃取脱酚废水。所述萃取在萃取塔中进行,所述萃取塔为转盘塔、筛板塔或填料塔。
37.本发明将脱酸脱氨后的酚水采用第一萃取剂进行萃取脱酚,得到萃取相和萃余相;萃取相进入酚回收一塔,分离萃取剂和粗酚;萃余相进入溶剂回收一塔,回收溶于其中的萃取剂,得到一级萃取脱酚废水;一级萃取脱酚废水总量的1/4~3/4回流作为煤气洗涤水,剩余一级萃取脱酚废水进行第二级萃取;萃取剂循环使用。
38.一级萃取脱酚后,部分脱酚废水回流作为煤气洗涤水,从而使废水中的酚得到富集,减少煤气洗涤新鲜水用量,同时减少了二级萃取处理量。
39.具体的,所述第一萃取剂为二异丙醚dipe。
40.所述第一萃取剂和脱酸脱氨后的酚水的体积比优选为1:4~1:10;具体可以为1:4、1:5、1:6、1:7、1:8、1:9或1:10。
41.所述萃取参数为:常压,萃取温度为25~40℃。
42.按照本发明,所述一级萃取脱酚废水总酚含量为400~1000mg/l,cod为2000~5000mg/l;
43.将一级萃取脱酚废水采用第二萃取剂进行萃取脱酚,得到二级萃取脱酚废水。所述萃取在萃取塔中进行,所述萃取塔为转盘塔、筛板塔或填料塔。
44.优选具体为:将一级萃取脱酚废水采用采用第二萃取剂进行萃取脱酚,得到萃取相和萃余相;萃取相进入酚回收二塔,分离萃取剂和粗酚;萃余相进入溶剂回收二塔,回收溶于其中的萃取剂,得到二级萃取脱酚废水;萃取剂循环使用。
45.本发明所述第二萃取剂为酮类和醇类的复合萃取剂;所述酮类选自甲基正丙基酮、甲基异丙基酮或甲基异丁基甲酮;所述醇类选自正丙醇、异丙醇、异丁醇的一种;所述酮类和醇类的体积比为2:1~4:1;具体可以为2:1、3:1、4:1;或者上述任意二者之间的比例。
46.在本发明一些具体实施例中,所述第二萃取剂为体积比2:1的甲基异丙基酮和正丙醇的混合物;
47.在本发明一些具体实施例中,所述第二萃取剂为体积比3:1的甲基异丁基酮和异丙醇的混合物;
48.在本发明一些具体实施例中,所述第二萃取剂为体积比4:1的甲基正丙基酮和异丁醇的混合物。
49.所述第二萃取剂和一级萃取脱酚废水的体积比为1:4~1:10;所述萃取参数为:常压,萃取温度为25~40℃。
50.本发明所述二级萃取脱酚废水总酚含量小于300mg/l。
51.本发明上述第二萃取剂通过酮类和醇类的复合,同时结合第一萃取剂使得最终萃取效果好,提高对酚的脱除率。
52.二级萃取脱酚废水进行生化处理阶段,粗酚进行精制阶段。本发明对于所述生化处理和粗酚的精制不进行限定,本领域技术人员熟知的即可。
53.本发明经一级萃取脱酚后,部分脱酚废水回流作为煤气洗涤水,从而使废水中的酚得到富集,减少煤气洗涤新鲜水用量,同时减少了二级萃取处理量;采用二异丙醚和协同萃取剂(酮类+醇类)分别作为一级和二级萃取剂,可以实现对单元酚和多元酚的高效脱除,
处理后废水达到生化处理要求,同时还可以降低溶剂回收的能耗和损失。具有脱酚率高、溶剂用量小、能耗低的优点。
54.本发明提供了一种含酚废水萃取脱酚方法,包括如下步骤:a)含酚废水预处理后,进入汽提脱酸脱氨塔,进行脱酸、脱氨、脱除机械杂质处理,得到脱酸脱氨后的酚水;b)将脱酸脱氨后的酚水采用第一萃取剂进行萃取脱酚,得到一级萃取脱酚废水;c)将一级萃取脱酚废水采用采用第二萃取剂进行萃取脱酚,得到二级萃取脱酚废水。本发明以两种不同的溶剂作为萃取剂分别作用于所述两级萃取脱酚。在提高脱酚效率的基础上降低系统能耗,具有脱酚率高、溶剂用量小、能耗低的优点,能提高对多元酚的脱除效率,降低溶剂回收能耗,使脱酚废水达到生化处理的水质要求,总酚浓度控制到300mg/l以内。
55.为了进一步说明本发明,以下结合实施例对本发明提供的一种含酚废水萃取脱酚方法进行详细描述。
56.实施例1
57.煤化工过程产生的高浓度含酚废水经重力沉降除油预处理后,进入汽提脱酸脱氨塔,经过脱酸脱氨脱除机械杂质后,使废水ph值控制在5~9。
58.脱酸脱氨除机械杂质后的酚水进入萃取一塔,以萃取剂1为萃取剂,进行一级萃取脱酚。萃取相进入酚回收一塔,分离萃取剂和粗酚。萃余相进入溶剂回收一塔,回收溶于其中的萃取剂。萃取剂循环使用;一级萃取脱酚废水总量的1/4~3/4回流作为煤气洗涤水,剩余废水进入萃取二塔,以萃取剂2为萃取剂,进行二级萃取脱酚,萃取相进入酚回收二塔,分离萃取剂和粗酚。萃余相进入溶剂回收二塔,回收溶于其中的萃取剂。萃取剂循环使用;脱酚水送入生化处理工段,粗酚送至粗酚精制工段。
59.萃取剂1:二异丙基醚,萃取剂一和含酚废水的体积比1:10;
60.萃取剂2:甲基异丙基酮:正丙醇=2:1(体积分数),萃取剂二和含酚废水的体积比1:4;
61.萃取参数:温度25℃,ph=8;
62.经除油、脱酸脱氨预处理后的酚水:总酚5840mg/l,其中,单元酚3510mg/l,多元酚2330mg/l;
63.处理后脱酚水:
64.总酚146mg/l,单元酚19mg/l,多元酚127mg/l,单元酚脱除率99.46%,多元酚脱除率94.55%,总酚脱除率97.83%。
65.实施例2
66.煤化工过程产生的高浓度含酚废水经重力沉降除油预处理后,进入汽提脱酸脱氨塔,经过脱酸脱氨脱除机械杂质后,使废水ph值控制在5~9。
67.脱酸脱氨除机械杂质后的酚水进入萃取一塔,以萃取剂1为萃取剂,进行一级萃取脱酚。萃取相进入酚回收一塔,分离萃取剂和粗酚。萃余相进入溶剂回收一塔,回收溶于其中的萃取剂。萃取剂循环使用;一级萃取脱酚废水总量的1/4~3/4回流作为煤气洗涤水,剩余废水进入萃取二塔,以萃取剂2为萃取剂,进行二级萃取脱酚,萃取相进入酚回收二塔,分离萃取剂和粗酚。萃余相进入溶剂回收二塔,回收溶于其中的萃取剂。萃取剂循环使用;脱酚水送入生化处理工段,粗酚送至粗酚精制工段。
68.萃取剂1:二异丙基醚,萃取剂一和含酚废水的体积比1:7;
69.萃取剂2:甲基异丁基酮:异丙醇=3:1(体积分数),萃取剂二和含酚废水的体积比1:7;
70.萃取参数:温度30℃,ph=7;
71.经除油、脱酸脱氨预处理后的酚水:总酚7450mg/l,其中,单元酚4350mg/l,多元酚3100mg/l;
72.处理后脱酚水:
73.总酚244mg/l,单元酚35mg/l,多元酚209mg/l,单元酚脱除率99.20%,多元酚脱除率93.26%,总酚脱除率97.19%。
74.实施例3
75.煤化工过程产生的高浓度含酚废水经重力沉降除油预处理后,进入汽提脱酸脱氨塔,经过脱酸脱氨脱除机械杂质后,使废水ph值控制在5~9。
76.脱酸脱氨除机械杂质后的酚水进入萃取一塔,以萃取剂1为萃取剂,进行一级萃取脱酚。萃取相进入酚回收一塔,分离萃取剂和粗酚。萃余相进入溶剂回收一塔,回收溶于其中的萃取剂。萃取剂循环使用;一级萃取脱酚废水总量的1/4~3/4回流作为煤气洗涤水,剩余废水进入萃取二塔,以萃取剂2为萃取剂,进行二级萃取脱酚,萃取相进入酚回收二塔,分离萃取剂和粗酚。萃余相进入溶剂回收二塔,回收溶于其中的萃取剂。萃取剂循环使用;脱酚水送入生化处理工段,粗酚送至粗酚精制工段。
77.萃取剂1:二异丙基醚,萃取剂一和含酚废水的体积比1:4;
78.萃取剂2:甲基正丙基酮:异丁醇=4:1(体积分数),萃取剂二和含酚废水的体积比1:10;
79.萃取参数:温度35℃,ph=6;
80.经除油、脱酸脱氨预处理后的酚水:总酚9990mg/l,其中,单元酚6230mg/l,多元酚3760mg/l;
81.处理后脱酚水:
82.总酚197mg/l,单元酚24mg/l,多元酚173mg/l,单元酚脱除率99.61%,多元酚脱除率95.40%,总酚脱除率98.27%。
83.以上所述仅是本发明的优选实施方式,应当指出,对于本技术领域的普通技术人员来说,在不脱离本发明原理的前提下,还可以做出若干改进和润饰,这些改进和润饰也应视为本发明的保护范围。