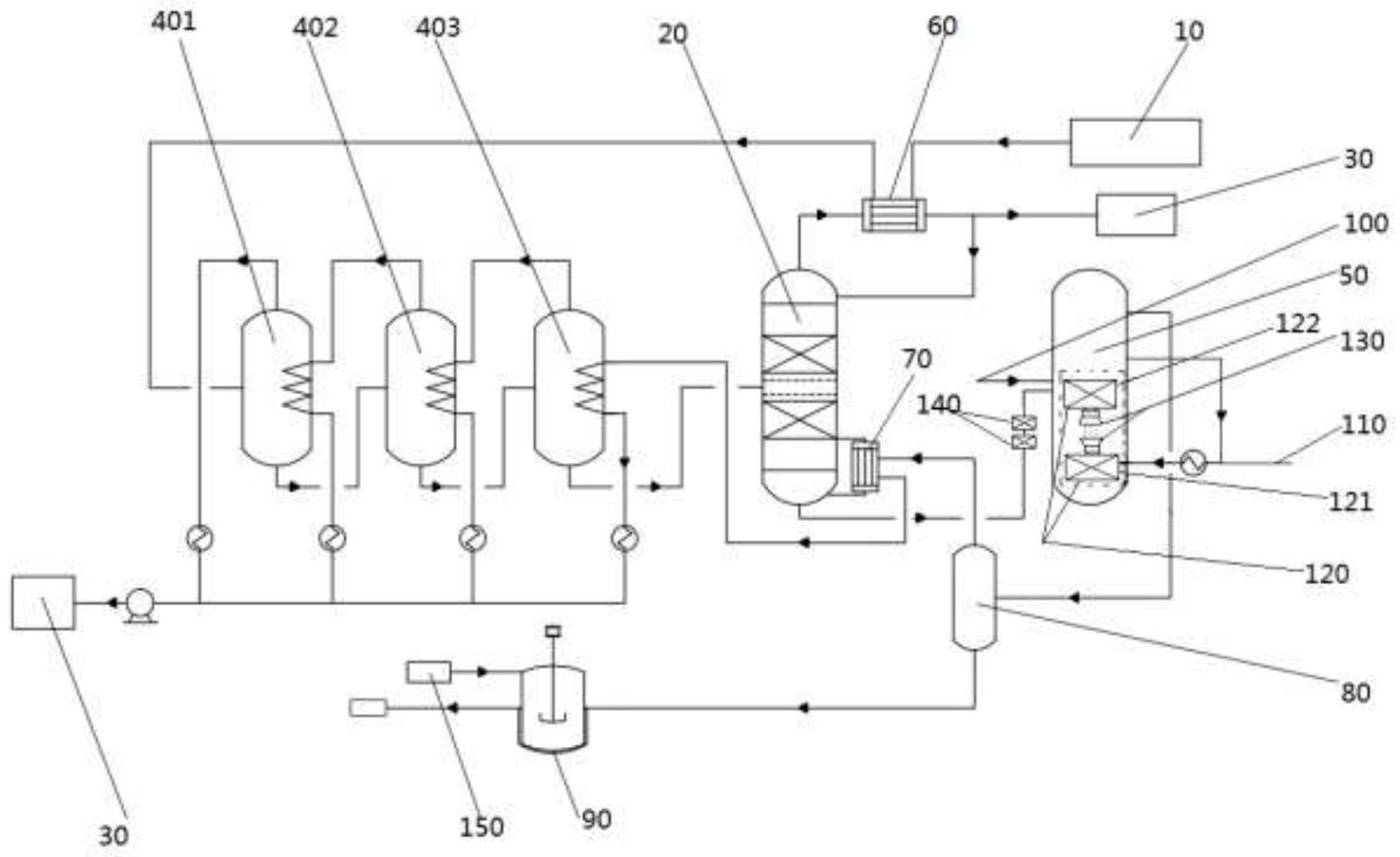
本发明属于废水处理,具体而言属于一种高盐低cod废水处理系统及方法。
背景技术:
1、随着社会经济的告诉发展,水污染日益严重,已收到社会的高度关注。工业废水排放对生态环境造成了不可估量的危害,因此消除工业污染源的排放,减少进入水环境中污染物的量,减少其造成污染的程度和范围,是水环境中污染物治理的重点。工业废水中有机污染物主要来自化工、石油、冶金、炼焦、轻工等行业,污染物种类繁多,对环境造成极大危害。
2、对于工业上高盐低cod污水的处理一直是污水处理行业的难题,原料中的cod含量不高仅为15000-18000,水以及盐(硫酸钠为代表)浓度较高,盐浓度达到8%,因此这样的污水无法直接进入生化池,高盐浓度的环境会不利于生化池内的生物降解。而如此高含水量并低cod的污水也不适合直接进入湿式氧化器,因为湿式氧化器需要高温高压并加催化剂,导致若是较低cod以及较高水含量会带来较大的能耗,因为要克服水的潜热,从而若是直接采用湿式氧化器便显得不具有经济效益。
3、有鉴于此,特提出本发明。
技术实现思路
1、本发明的第一目的在于提供一种高盐低cod废水的处理系统,该废水处理系统通过在湿式氧化器内部设置内置微界面机组,提高了两相之间的传质效果、反应效率,可以将气体打碎成微米级别的气泡,从而增加气相与液相之间的相界传质面积,使得传质空间充分满足,增加了空气与氧气在液相中的停留时间,从而降低空气与氧气的耗量,既降低了反应温度和压力,同时保证反应本身的高效性,避免高温高压带来的一些列安全隐患的发生,更有利于反应过程的节能降耗,成本低。
2、本发明的第二目的在于提供一种采用上述系统进行高盐低cod废水处理的方法,该方法操作简便、操作条件更加温和,能耗低,达到了比现有技术工艺更佳的处理效果。
3、为实现本发明的上述目的,特采用以下技术方案:
4、本发明提供一种高盐低cod废水的处理系统,包括精馏塔、多效蒸发器、湿式氧化器、生化池和气液分离罐;
5、所述精馏塔与所述多效蒸发器连通,用于将废水馏分预热后进入所述多效蒸发器;
6、所述多效蒸发器分别与所述生化池和所述精馏塔连通,用于将蒸发后的蒸汽进入所述生化池进行生物降解处理,并将蒸发后的废水进入所述精馏塔进行精馏;
7、所述精馏塔与所述湿式氧化器连接用于将精馏后的废水进行湿式氧化处理;
8、所述精馏塔与所述湿式氧化器之间设置有外置微界面机组,所述湿式氧化器内部设置有内置微界面机组用于分散破碎气体成气泡。
9、所述内置微界面机组包括气动式微界面发生器和液动式微界面发生器,所述湿式氧化器的侧壁设置有空气进口,所述空气进口通过管道延伸至所述气动式微界面发生器内部,所述湿式氧化器侧壁设置有催化剂进口,所述液动式微界面发生器中通入所述湿式氧化器内的废水和催化剂,所述液动式微界面发生器连接有导气管,所述导气管的顶端伸出所述湿式氧化器的液面用于回收空气或氧气。
10、现有技术的废水处理工艺中,湿式氧化处理法往往需要较高的反应温度、压力和较长的停留时间,究其原因是因为为空气或氧气在液相中的停留时间短,传质时间不足,气泡直径大,反应器内形成的气液相界面积较小,传质空间不足,从而导致了反应时间过长、能耗高、反应效率低下的问题。
11、上述废水处理系统中,在进行湿式氧化处理之前先进行一定的预处理,预处理系统包括依次连接的精馏塔和多效蒸发器,在精馏塔塔顶进行馏分预热,通过多效蒸发器进行蒸发处理,经过多效蒸发器的蒸发后废水的cod含量升高,蒸发出大量水和少量醋酸,直接进入生化池生物降解,将预处理后的废水返回精馏塔进行精馏,塔顶馏分与原料换热后进入生化池生物降解,塔底馏分提浓得到提浓后的废水。
12、废水在上述预处理系统中经过初步的馏分、蒸发等预处理措施后,在进行后续的湿式氧化处理以达到更深层次的废水处理效果。
13、需要强调的是,该废水处理系统通过在精馏塔与湿式氧化器之间设置外置微界面机组,使得废水在进入湿式氧化器之前先分散破碎成微米级气泡,增大与湿式氧化器内氧气的接触面积;通过在湿式氧化器内部设置内置微界面机组,将进入湿式氧化器的空气或氧气打碎分散成气泡,与废水接触,从而增加了气体与废水之间的相界传质面积,进一步提高了反应相界面的传质效果后,操作温度与压力也不需要太高,实现了能耗低,操作成本低的效果。
14、在本发明的内置微界面机组中包括了气动式微界面发生器,将湿式氧化器的空气进口进入的空气或氧气通入气动式微界面发生器内部,通过微界面发生器的破碎分散作用,将气体分散破碎成微气泡,从而减小液膜厚度,有效的增大了空气或氧气与废水之间的传质面积,降低传质阻力,提高反应效率。
15、更优选的,所述内置微界面机组还包括液动式微界面发生器,所述液动式微界面发生器中通入从所述湿式氧化器内循环回来的废水,所述液动式微界面发生器连接有导气管,所述导气管的顶端伸出所述湿式氧化器内的液面上方用于回收空气或氧气。因为反应过程中大量未反应完的空气和或氧气会大量积聚在湿式氧化器内的上方,为了充分回收,通过导气管再次进入底部多次循环反应,从而提高传质效率,通入的循环废水可以达到给液动式微界面发生器提供动力的效果。
16、进一步的,所述液动式微界面发生器的出口与所述气动式微界面发生器的出口均设有喷嘴,所述喷嘴将微气泡和微液泡喷出并提供动力,将内置微界面机组内的废水与空气循环搅拌,优选的,喷头为喇叭型,喷嘴将气泡喷射出以提供动力,并通过喷头扩散开,从而进一步增大接触面积,加快反应速率。
17、内置微界面机组的气动式微界面发生器设置在下方,液动式微界面发生器设置在上方,两个微界面发生器的出口处均设置有喷嘴。两个微界面发生器的出口相对设置,上方的液动式微界面发生器将废水自上而下流动,下方的气动式微界面发生器将气体分散破碎成微气泡自下而上与废水充分接触,通过喷嘴为气泡增加动力,进而增大废水和气体的相界传质面积,提高空气或氧气的利用率。
18、本领域所属技术人员可以理解的是,本发明所采用的微界面发生器在本发明人在先专利中已有体现,如申请号cn201610641119.6、cn201610641251.7、cn201710766435.0、cn106187660、cn105903425a、cn109437390a、cn205833127u及cn207581700u的专利。在先专利cn201610641119.6中详细介绍了微米气泡发生器(即微界面发生器)的具体产品结构和工作原理,该申请文件中记载了“微米气泡发生器包括本体和二次破碎件、本体内具有空腔,本体上设有与空腔连通的进口,空腔的相对的第一端和第二端均敞开,其中空腔的横截面积从空腔的中部向空腔的第一端和第二端减小;二次破碎件设在空腔的第一端和第二端中的至少一个处,二次破碎件的一部分设在空腔内,二次破碎件与空腔两端敞开的通孔之间形成一个环形通道。微米气泡发生器还包括进气管和进液管。”从该申请文件中公开的具体结构可以知晓其具体工作原理为:液体通过进液管切向进入微米气泡发生器内,超高速旋转并切割气体,使气体气泡破碎成微米级别的微气泡,从而提高液相与气相之间的传质面积,而且该专利中的微米气泡发生器属于气动式微界面发生器。
19、另外,在先专利201610641251.7中有记载一次气泡破碎器具有循环液进口、循环气进口和气液混合物出口,二次气泡破碎器则是将进料口与气液混合物出口连通,说明气泡破碎器都是需要气液混合进入,另外从后面的附图中可知,一次气泡破碎器主要是利用循环液作为动力,所以其实一次气泡破碎器属于液动式微界面发生器,二次气泡破碎器是将气液混合物同时通入到椭圆形的旋转球中进行旋转,从而在旋转的过程中实现气泡破碎,所以二次气泡破碎器实际上是属于气液联动式微界面发生器。其实,无论是液动式微界面发生器,还是气液联动式微界面发生器,都属于微界面发生器的一种具体形式,然而本发明所采用的微界面发生器并不局限于上述几种形式,在先专利中所记载的气泡破碎器的具体结构只是本发明微界面发生器可采用的其中一种形式而已。
20、此外,在先专利201710766435.0中记载到“气泡破碎器的原理就是高速射流以达到气体相互碰撞”,并且也阐述了其可以用于微界面强化反应器,验证本身气泡破碎器与微界面发生器之间的关联性;而且在先专利cn106187660中对于气泡破碎器的具体结构也有相关的记载,具体见说明书中第[0031]-[0041]段,以及附图部分,其对气泡破碎器s-2的具体工作原理有详细的阐述,气泡破碎器顶部是液相进口,侧面是气相进口,通过从顶部进来的液相提供卷吸动力,从而达到粉碎成超细气泡的效果,附图中也可见气泡破碎器呈锥形的结构,上部的直径比下部的直径要大,也是为了液相能够更好的提供卷吸动力。
21、由于在先专利申请的初期,微界面发生器才刚研发出来,所以早期命名为微米气泡发生器(cn201610641119.6)、气泡破碎器(201710766435.0)等,随着不断技术改进,后期更名为微界面发生器,现在本发明中的微界面发生器相当于之前的微米气泡发生器、气泡破碎器等,只是名称不一样。综上所述,本发明的微界面发生器属于现有技术。
22、进一步的,所述高盐低cod废水的处理系统还包括换热器,所述换热器上设置有第一进口、第一出口、第二进口、第二出口,所述第一进口与原料进口连接,所述第一出口与所述精馏塔顶端连接,所述第二进口与所述精馏塔顶端连接,所述第二出口分别与所述多效蒸发器和所述生化池连接。
23、其中,精馏塔塔顶馏分出的废水作为热源预热原料进口进来的废水,再通入生化池进行生物降解,减小后续多效蒸发器的热负荷。
24、进一步的,所述高盐低cod废水的处理系统还包括再沸器,所述再沸器设置在所述精馏塔侧壁与所述多效蒸发器和所述精馏塔连接。
25、其中,湿式氧化器的反应液的高热量通过再沸器的作为精馏塔塔釜的热源,并且提供多效蒸发器的热源,如此设置充分利用了此工艺流程中的热量,降低能耗。
26、进一步的,所述多效蒸发器包括依次连接的一效蒸发器、二效蒸发器和三效蒸发器,所述一效蒸发器的底端与所述二效蒸发器的侧壁连接,所述二效蒸发器的底端与所述三效蒸发器连接,所述三效蒸发器的底端与所述精馏塔侧壁连接。
27、其中,二效蒸发器的蒸汽作为一效蒸发器的热源来源,三效蒸发器的蒸汽作为二效蒸发器的热源,从而达到充分利用能源的效果。
28、进一步的,所述一效蒸发器、二效蒸发器和三效蒸发器的顶端分别与所述生化池连接。
29、进一步的,所述处理系统还包括深度氧化反应器,所述深度氧化反应器连接所述气液分离罐的出水口用于对分离后的废水进行深度氧化处理,所述深度氧化反应器侧壁上设置有臭氧或过氧化氢进口。
30、除此之外,本发明还提供了一种高盐低cod废水的处理方法,包括如下步骤:废水先进入精馏塔馏分预热,而后进入多效蒸发器蒸发处理,经过多效蒸发器的蒸发后的蒸汽直接进入生化池进行生物降解处理,蒸发后的污水进入精馏塔进行精馏,塔顶馏分与原料换热后进入生化池,塔底馏分提浓得到提浓后的废水;
31、将塔底馏分后的提浓后的废水直接进入湿式氧化器进行湿式氧化处理,反应得到的反应液通入气液分离罐分离,分离后的气体作为精馏塔塔釜再沸器的热源换热后再作为三效蒸发器的热源进行换热至低温污水,最后进入生化池;分离后的液体则进入深度氧化反应器,经臭氧或过氧化氢深度氧化分解大分子后通过后处理分离降低盐浓度后进入生化池生物降解。
32、优选的,所述馏分预热的反应温度为100-120℃,所述湿式氧化处理的反应温度为230-265℃。
33、本发明的废水处理方法操作简便,操作条件更加温和,能耗低,达到了比现有工艺更佳的处理效果。
34、与现有技术相比,本发明的有益效果在于:
35、(1)本发明的高盐低cod废水的处理系统通过在湿式氧化器内部设置内置微界面机组,提高了两相之间的传质效果、反应效率,可以将气体打碎成微米级别的气泡,从而增加气相与液相之间的相界传质面积,使得传质空间充分满足,增加了空气与氧气在液相中的停留时间,从而降低空气与氧气的耗量,既降低了反应温度和压力,同时保证反应本身的高效性,避免高温高压带来的一些列安全隐患的发生,更有利于反应过程的节能降耗,成本低。
36、(2)本发明的高盐低cod废水的处理系统通过设置换热器和再沸器,充分利用反应过程中产生的热量,湿式氧化过程中有机物氧化产生较多热量,通过再沸器作为精馏塔塔釜和多效蒸发器的热源,降低能耗,节约成本,具有经济效益。