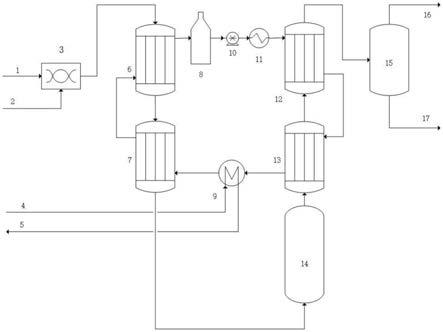
1.本实用新型属于高cod污水处理技术领域,具体为一种湿式氧化热交换网络系统。
背景技术:2.工业的快速发展必然伴随着巨大的“三废”排放问题,工业废水普遍具有有机物浓度高、含盐量高、毒性强等特点,对环境的危害极大,因此处理这类废水迫在眉睫。
3.湿式氧化技术是将待处理的物料置于密闭的容器中,在高温高压条件下通入空气作为氧化剂,使污水中有机物降解。发展至今在处理工业废水上具有相当的市场竞争力,但目前湿式氧化反应器基本为单个的填料鼓泡塔结构,存在以下几个缺点:(1)换热器的换热效率低,能耗高,设备投资大;(2)装置通气量大,氧化效率普遍较低、处理不充分,操作系统不稳定;(3)装置不方便清理维护,若废水盐浓度较高,容易造成堵塞。综上所述,针对上述问题,急需设计新型的湿式氧化处理系统。
技术实现要素:4.本实用新型针对传统湿式氧化技术存在的易堵塞、能耗高、工艺操作流程不够稳定、操作压力过高等缺点,提出了一种湿式氧化热交换网络系统。
5.为解决上述问题,本实用新型主要通过热交换网络系统来实现,技术方案如下:
6.一种湿式氧化热交换网络系统,包括依次连接的前段换热器、wao反应器14和后段换热器;所述后段换热器的壳程出口依次连接加热器9、所述前段换热器的壳程、冷却器11和所述后段换热器的壳程进口,形成换热介质循环。
7.进一步的,所述前段换热器包括依反应物料流动方向次序设置的串联的第一换热器6和第二换热器7,所述第一换热器6的壳程和所述第二换热器7的壳程串联在所述换热介质循环中。
8.进一步的,所述后段换热器包括依反应物料流动方向次序设置的串联的第三换热器13和第四换热器12,所述第三换热器13的壳程和所述第四换热器12的壳程相串联在所述换热介质循环中。
9.进一步的,所述前段换热器的入口前还设置有气液混合器3。在气液混合器中,高压空气与cod浓度为2-5*104mg/l的废水混合,使空气中的氧气与充分接触废水,也为进一步提高后续的降解效率打下基础。
10.进一步的,所述后段换热器的出口连接气液分离器15。
11.进一步的,所述前段换热器的壳程和所述冷却器11之间还设置有液体缓冲罐8。
12.进一步的,所述液体缓冲罐8与所述冷却器11之间还设置有泵。
13.进一步的,所述加热器9为蒸汽发生器。
14.进一步的,所述换热介质为导热油。
15.进一步的,所述导热油为有机硅导热油。
16.本实用新型所述湿式氧化热交换网络系统可采用本领域一般方法操作,为提高效
率,也可采用如下的操作方式:
17.将加压空气、废水形成气液混合液后流入前段换热器中,经前段换热器换热升温,达到170~280℃后流入wao反应器14进行反应形成氧化液;
18.所述氧化液经后段换热器换热降温至40~60℃后排出;
19.换热介质在后段换热器的壳程中与氧化液换热,升高温度后流入前段换热器的壳程中与气液混合液进行换热后降低温度回到后段换热器的壳程中,当导热介质升温不足时,由所述换热介质循环中的加热器补热,当导热介质温度过高时,由所述换热介质循环中的冷却器降温。
20.在上述过程中,本实用新型所述采用热交换循环系统代替传统的直接换热过程,提高了换热效率,低耗节能。
21.湿式氧化工艺需将废水和空气两相流体加热使得有机物发生氧化反应进而降解,过程中需提供大量的能量,但传统的工艺中换热效率低,工艺操作过程不够稳定可控;另外整个工艺过程中,装置成本较高且不易清理易堵塞。本实用新型所述的热交换网络系统,首先有效的提高了换热效率,多级换热装置与冷却器和蒸汽发生器结合,导热油经壳程循环,增大了换热面积,达到低耗节能的目的,同时系统更加稳定可控;其次,废水全程走管程,解决了堵塞问题。
22.作为优选,上述所述的一种湿式氧化热交换网络系统,所述wao反应器的进料量为废水进料量的2-4倍;
23.作为优选,上述所述的一种湿式氧化热交换网络系统,所述第二换热器的温度为180~290℃,第三换热器的温度为30~50℃;
24.该系统中废水经管程,低粘度的导热油经壳程,解决了传统湿式氧化处理技术中易堵塞的问题,设计了多级换热装置,解决了传统装置能耗高的问题,可在低压条件下操作,进一步提高了装置的安全系数,同时设计缓冲和冷却装置,提升了系统的稳定性。
附图说明
25.图1为本实用新型所述湿式氧化热交换网络系统的结构示意图。
26.其中1是加压空气,2是废水,3是企业混合器,4是水,5是蒸汽,6是第一换热器,7是第二换热器,8是液体缓冲罐,9是蒸汽发生器,10是泵,11是冷却器,12是第四换热器,13是第三换热器,14是wao反应器,15是气液分离器,16是尾气,17是出水。
具体实施方式
27.下面结合附图1和具体实施方式对所述湿式氧化热交换网络系统作进一步详细描述:
28.实施例1
29.一种湿式氧化热交换网络系统,包括依次连接的前段换热器、wao反应器14和后段换热器;所述后段换热器的壳程出口依次连接加热器9、所述前段换热器的壳程、冷却器11和所述后段换热器的壳程进口,形成换热介质循环。
30.所述前段换热器包括依反应物料流动方向次序设置的串联的第一换热器6和第二换热器7,所述第一换热器6的壳程和所述第二换热器7的壳程串联在所述换热介质循环中。
31.所述后段换热器包括依反应物料流动方向次序设置的串联的第三换热器13和第四换热器12,所述第三换热器13的壳程和所述第四换热器12的壳程相串联在所述换热介质循环中。
32.所述前段换热器的入口前还设置有气液混合器3。在气液混合器中,高压空气与cod浓度为2-5*104mg/l的废水混合,使空气中的氧气与充分接触废水,也为进一步提高后续的降解效率打下基础。
33.所述后段换热器的出口连接气液分离器15。
34.所述前段换热器的壳程和所述冷却器11之间还设置有液体缓冲罐8。
35.所述液体缓冲罐8与所述冷却器11之间还设置有泵。
36.所述加热器9为蒸汽发生器。
37.所述换热介质为导热油。
38.所述导热油为有机硅导热油。
39.工艺中水相均经管程,其步骤如下:
40.s1:气液混合:空气加压至5.5mpa,将加压空气1在气液混合器3中与废水2进行混合,所述废水的cod为2.5*104mg/l,气液充分混合形成两相流体;
41.s2:换热-升温:接着两相流体经管程进入第一换热器6中,所述第一换热器6的壳程中装载导热油,壳程的液体出口与液体缓冲罐8、壳程的进口与第二换热器7相连接,所述两相流体经第一换热器6和第二换热器7温度升高,进入wao反应器14;
42.s3:湿式氧化反应:有机废水在wao反应器14中被氧化生成水和二氧化碳,反应完成后生成氧化液,温度达到230℃,随后经出口至第三换热器13;
43.s4:换热-降温:氧化液经管程进入第三换热器13,所述第三换热器13的壳程分别与第四换热器12的壳程、蒸汽发生器9连接,氧化液经第三换热器13,第四换热器12与壳程中的导热油换热,完成后温度保持在40℃;
44.s5:气液分离:随后氧化液进入气液分离器15中,液体中的气体经形成尾气16和出水17排出;
45.s6:热交换循环系统:导热油经壳程在第一换热器6,第二换热器7, 液体缓冲罐8,第三换热器13,第四换热器12之间循环,当所述第一换热器6,第二换热器7中温度过低,第三换热器13中的导热油经蒸汽发生器9加热后依次循环至第二换热器7、第一换热器6;而当第四换热器12中导热油温度过高时,导热油经泵10,冷却器11降温循环至第四换热器12。
46.所述wao反应器对的进料量为废水进料量的2.5倍;
47.所述wao反应器输出氧化液的温度为230℃,第三换热器输出氧化液的温度为40℃;
48.所述第二换热器的温度为240℃,第三换热器的温度为39℃;
49.实施例2
50.采用与实施例1相同的热交换网络系统,工艺中水相均经管程,与实施例1的区别仅在于:
51.s1中将空气加压至9mpa,废水的cod为4*104mg/l。
52.s3中氧化液温度为270℃。
53.s4中导热油换热后温度保持在50℃。
[0054] wao反应器对的进料量为废水进料量的2倍;
[0055]
wao反应器输出氧化液的温度为270℃,换热器4输出氧化液的温度为50℃;
[0056]
第二换热器7的温度为280℃,第三换热器13的温度为45℃;
[0057]
实施例3
[0058]
取一工厂废水样品,废水中cod含量为2*104mg/l,密度1100kg/m 3
,废水温度40℃,小时日排放量为15m 3 /h。现采用传统的湿式氧化工艺和本发明实施例1的工艺分别处理上述废水,并对比降解率,其中本发明实施例1采用湿式氧化热交换网络系统,现有的湿式氧化工艺仅采用传统的换热方式,两项工艺相比:湿式氧化热交换网络系统降解率在40min时达到96%,运行成本(能物耗为45元/吨);湿式氧化工艺降解率在40min时为90%,运行成本(能物耗为85元/吨,与电价相关)。
[0059]
总之,以上所述仅为本发明的较佳实施例,凡依本发明申请专利的范围所作的均等变化与修饰,皆应属本发明的涵盖范围。