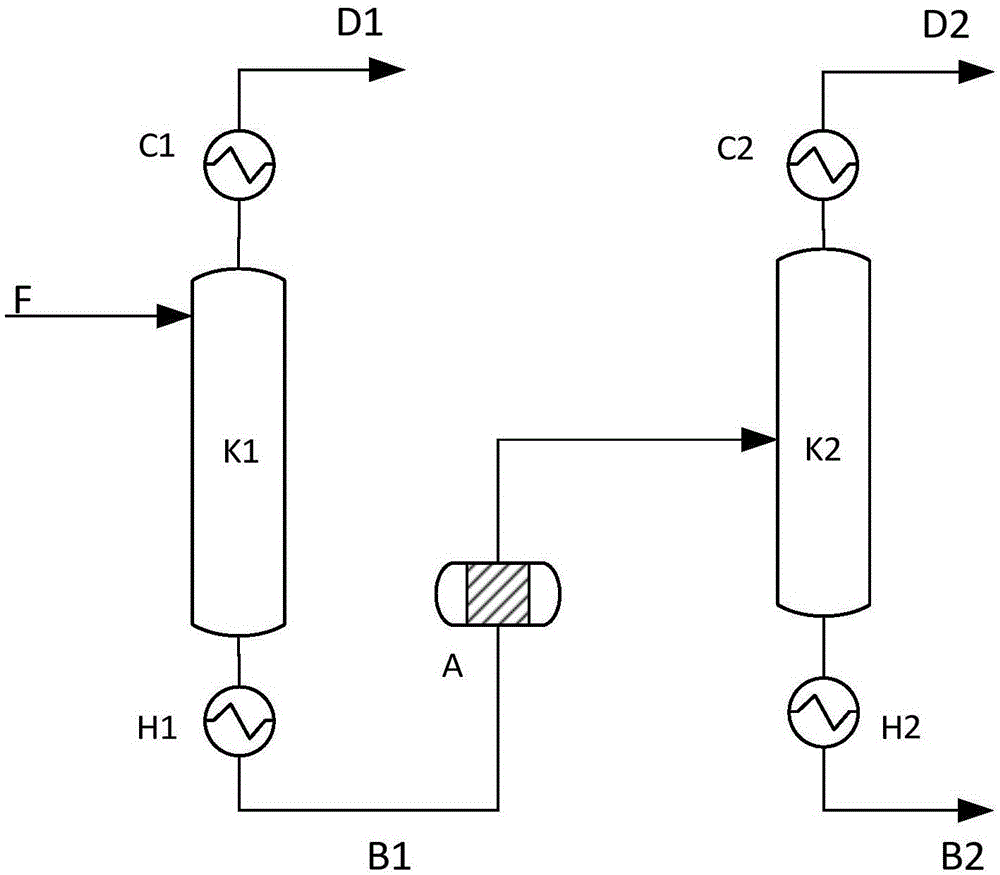
具体而言,本发明涉及将包含氯硅烷的多组分混合物分离成各组分并同时大大降低氯硅烷混合物内的杂质(硼、磷、砷)水平的方法。氯硅烷如三氯甲硅烷(TCS)被用来沉积多晶体硅。TCS主要通过三种不同的方法产生:A)Si+3HCl→SiHCl3+H2+副产物(冶金硅的氯氢化反应)B)Si+3SiCl4+2H2→4SiHCl3+副产物(冶金硅与四氯化硅/STC与氢的反应)C)SiCl4+H2→SiHCl3+HCl+副产物(四氯化硅/STC的氢化)生成的副产物尤其包含二氯甲硅烷(DCS)。当涉及包含TCS、STC、DCS和微量的其他杂质(甲基氯硅烷、烃类和高沸点化合物)的氯硅烷混合物时其是优选的。在每种情况下,高纯度三氯甲硅烷是通过实施随后的蒸馏来获得的。蒸馏的最重要目的在于除去含硼、含磷或含砷的化合物,因为此等化合物是沉积硅中不需要的p-/n-掺杂剂。就这些杂质而言,沉积中所采用的三氯甲硅烷纯度要求在仅仅一些ppta的范围之内。在化学工程中蒸馏方法通常为热分离不同相对挥发度和/或互溶物质的混合物。通常使用各种方法的版本来连续蒸馏拆分多物质混合物。在最简单的情况下,将一种由低沸馏分和高沸馏分组成的进料混合物拆分为它的两个馏分--低沸顶部馏分和高沸底部馏分。在这里,将待分离的混合物引入到蒸馏塔的底部和顶部之间。该进料将塔分为精馏段和提馏段。高沸馏分从底部的塔内提取。设置在底部区域内的加热装置(如一个自然循环蒸发器)蒸发一部分浓缩物。低沸组分随着塔上升为蒸汽,在所述塔的顶部从塔内提取,并在冷凝器中液化。部分冷凝物再次循环入塔,并与上升蒸汽逆向向下流动(回流)。然而,将由多组分混合物(A,B,C)组成的进料混合物分馏成两个馏分以上就需要使用多个常规蒸馏塔。有几个选择来实现此目的。对于a路径,低沸组分A在第一塔中作为顶部产物被除去。底部馏分是中沸组分B和高沸组分C的混合物,其在下游塔中被分馏成两种纯物质B和C。对于预分离耦接的物质(a/c路径),在第一塔进行分离,使得顶部产物不包括高沸组分C,且底部产物不包括低沸组分A。因此引起低沸组分A和高沸组分C的分离。中沸组分B存在于顶部馏分和底部馏分中。馏分AB和BC分别在独立的下游塔被分解为纯产物A、B和C。因此,该版本需要三个分离阶段。对于c路径,在第一塔内C作为纯底部产物被除去,而混合物AB作为顶部产物通常以蒸汽形式转移到第二塔。一般情况下,对于三组分混合物的分馏,合适路径的选择(a路径,c路径,a/c路径)取决于输入的组成。对于低沸组分A含量高者,优选a路径。相反,对于高沸组分C含量高者,优选c路径。当中沸组分B比例高时,其优选选择为a/c路径。对于与前置塔耦接的物料,两个塔均是物料耦接(因此双重物料耦接;故称Petlyuk设置)。US20120193214A1公开一种氯硅烷的蒸馏提纯方法,该方法包括提供包含TCS、DCS和STC之氯硅烷的含硼混合物,以及通过多个蒸馏塔蒸馏来提纯该氯硅烷的混合物,其中低沸硼化合物经由包含富含硼的DCS的顶部流从蒸馏塔流出,而相对高沸硼化合物经由包含高沸组分的富含硼的底部流从蒸馏塔流出。除了单纯的蒸馏方法,采用吸附器也是已知的。吸附器可实现各种功能。微量化合物可通过吸附机理从三氯甲硅烷中保留。这是一种有效的清除方法,尤其对于极性分子。吸附剂可进行进一步调节,以便在其表面开始用于转化这些化合物的化学反应。例如,在水调节的吸附器表面上的刻意水解是一种生成硼氧化合物的已知方法,该硼氧化合物在下游蒸馏阶段明显更容易除去,例如参见US4713230A。US20110184205A1描述一种处理组合物的方法,该组合物包含至少一种硅化合物和至少一种外来金属和/或含外来金属的化合物,其中所述组合物在第一阶段接触至少一种吸附介质和/或至少一个第一过滤器,并在下一阶段任选地接触至少一个过滤器以获得一种外来金属含量减少和/或含有外来金属的化合物的含量减少的组合物。在这里,通过与无水吸附介质(活性炭、硅酸盐如硅胶、分子筛、有机树脂)接触,氯硅烷的硼含量减少。然而,这需要非常大量的吸附介质(120g/250ml的TCS)来达到预期的提纯目标。这使所述方法不经济,特别是作为连续性方法几乎是不可能的,其在半导体品质的氯硅烷的生产中在经济上是不利的。而且,使用吸附器需要进一步装置的复杂性(如过滤)以及随之而来的是在半导体级别产物中引入其它杂质的风险。US20130121907A1公开一种从包含三氯甲硅烷的混合物中除去至少一种含硼杂质从而得到纯化的包含三氯甲硅烷的产物的方法。该方法包括从混合物中部分除去含硼杂质来获得包含三氯甲硅烷的部分提纯混合物。所述部分提纯混合物通过侧面进料口被供给塔。从该塔中排出的是a)包含含硼杂质的顶部产物b)包含含硼杂质的底部产物以及c)包含三氯甲硅烷的提纯混合物。部分除去含硼杂质可包括向蒸馏塔供给混合物,排出包含含硼杂质的顶部产物以及提取作为底部产物的部分提纯混合物。该底部产物在供给第二塔之前可由诸如硅胶床的吸附器中通过。即使结合吸附器和蒸馏塔,在生产半导体品质的三氯甲硅烷中蒸馏阶段仍有巨大的能源需求。分隔壁塔技术能够提供一种可减少能源需求的有吸引力的选择方法。所述技术基于物料耦接的原理,并使能源需求减少高达50%。由于所述方法呈现两个装置的分离任务,因此这也有可能节约资本开支。传统的分隔壁塔具有沿塔纵向方向设置的垂直分隔壁,该分隔壁可防止塔分区内液体流和蒸汽流的横向混合。因此,该塔包括至少一个沿部分塔高的垂直分隔壁,所述垂直分隔壁将横断面分为至少两个区段,即位于所述分隔壁左边和右边。因此,这使得在单一塔内将例如通常需要两个常规塔的三组分混合物拆分为三个纯成分成为可能。设置在塔纵向方向上的分隔壁将塔内部分隔为进料段、提取段、上公共塔段(精馏段)和下公共塔段(提馏段)。然而,已证明将分隔壁塔与迄今已知的吸附器结合使用是昂贵的且不方便实施。分隔壁塔中的物料耦接导致在一个装置内进行两个分离任务。在装置内同时除去低沸硼化合物和高沸硼化合物。在塔进料内布置吸附器并不可取,因为此时硼化合物含量仍很高,这会导致吸附器非常快速的装载。为实现与传统分隔壁塔内吸附器相同的效果,需要使所述塔具有相应的内部构件。在分隔壁塔内采用具有催化活性的内部构件是已知的。EP1513791B1公开一种具有至少两个垂直蒸馏区段的蒸馏塔,其中至少一个区段包括催化剂,且至少一个区段部分无催化剂,其中这些区段被沿蒸馏塔垂直部分延伸的壁分开,其中所述垂直部分低于总塔高,以及这些区段在所述壁的垂直端部/末端周围是液体连通的。一种原理上类似的概念也可被考虑用于在分隔壁塔内使用吸附器。然而,由于吸附器需要定期更换(装载,调节),该版本是不利的。由于蒸馏是个连续过程,因此定期需要更换内部构件而造成的操作相当长中断是不可取的。本发明实现的目的是基于所述问题的。本发明的目的通过一种用于蒸馏分离多组分混合物的方法来实现,所述混合物包含:包含二氯甲硅烷和至少一种含硼、含磷或含砷杂质的低沸组分,包含三氯甲硅烷和至少一种含硼、含磷或含砷杂质的中沸组分,和包含四氯化硅的高沸组分,其中向第一蒸馏塔供给所述多组分混合物以除去至少一种作为底部馏分的包含四氯化硅的高沸组分,并且向第二蒸馏塔供给包含二氯甲硅烷、三氯甲硅烷和至少一种含硼、含磷或含砷杂质的顶部馏分,其中在所述第二蒸馏塔中,经由侧线馏分除去所述至少一种包含三氯甲硅烷的中沸组分,并且除去所述至少一种作为顶部馏分的包含二氯甲硅烷的低沸组分,其中至少一种来自所述第二蒸馏塔的底部馏分由吸附器中通过,以除去所述至少一种含硼、含磷或含砷杂质的,并且随后作为回流返回到所述第一蒸馏塔,其中两个蒸馏塔都包括垂直分隔壁。当存在两个来自第二蒸馏塔的底部馏分时,液体流的任一股或两股液体流由所述吸附器通过,并且随后作为回流供给第一蒸馏塔。替代第一和第二蒸馏塔之间的液体流内的吸附器,该吸附器也可安置在从第一到第二蒸馏塔通过的产物蒸汽流中。来自第一蒸汽塔的顶部馏分优选经由两股蒸汽流供给第二蒸馏塔的提馏段。可以在供给到第二蒸馏塔前使得只有一股蒸汽流通过吸附器。优选两股蒸汽流都通过吸附器。在一个实施方案中存在两个吸附器,其中一股或两股蒸汽流在第一和第二蒸馏塔之间通过第一吸附器,而来自第二蒸馏塔的一股或两股液体流通过第二吸附器进入到第一蒸馏塔的回流中。特别优选的是,在各种情况下,全部液体流和全部蒸汽流在两个蒸馏塔之间通过吸附器。所述目的进一步通过用于蒸馏分离多组分混合物的装置来实现,该装置包括通过以下方式相互物料耦接的两个蒸馏塔:第一蒸馏塔的蒸汽与所述第二蒸馏塔的底部连通连接以及所述第二蒸馏塔的底部馏分与所述第一蒸馏塔的回流段连通连接,其中用于除去含硼、含磷或含砷杂质的吸附器在第二蒸馏塔的底部馏分与第一蒸馏塔的回流段之间连通连接地设置,其中两个蒸馏塔都包括垂直分隔壁,其中所述第二蒸馏塔包括一个或多个位于所述顶部馏分下方及所述底部馏分上方的侧线馏分。优选的是,用于除去含硼、含磷或含砷杂质的吸附器设置在第一和第二蒸馏塔之间的两个连通连接处的任一处。本发明提供相互物料耦接的蒸馏塔。此外,垂直分隔壁设置于每一个蒸馏塔内,并将该分隔壁定义为使液体和蒸汽不能混合的壁。因此,第一蒸馏塔的分隔壁延伸直到该蒸馏塔的上端,而第二蒸馏塔的分隔壁延伸直到该蒸馏塔的下端。在第一蒸馏塔内沿塔纵向方向设置的分隔壁将塔内部划分为进料段、提取段和较低公共塔段(提馏段),且因此,该蒸馏塔各区域经由底部段互相是液体连通的。在第二蒸馏塔内沿塔纵向方向设置的分隔壁将塔内部划分为进料段、提取段和较高公共塔段(精馏段),且因此,该蒸馏塔各区域经由顶部段互相是液体连通的。两个蒸馏塔的物料耦接实现了两个蒸馏塔的理论塔板的增加。因此,如果采用两个相同构造的蒸馏塔,则理论塔板数会增加一倍。每个蒸馏塔分别与相应的另一个塔在空间独立的位置处具有至少两处连接,由此实现物料耦接。在能源需求方面,两个这样的物料耦接蒸馏塔相当于单个分隔壁塔。因此,与传统单分隔壁塔的新认知相比,可以认为节省大量能量,同时引起较低的资本成本,这是由于传统的现有蒸馏塔可转变为经过改造的分隔壁塔并且互相连接,使得这两个带有分隔壁的引用蒸馏塔实现了现有技术分隔壁塔的功能。每个物料耦接蒸馏塔均可装备用于蒸发液体底部流的蒸发器和/或用于凝结蒸汽流的冷凝器。所述蒸馏塔优选包括一个或多个蒸发器系统,其采用具有不同压力和温度等级的蒸汽或热油作为操作介质。所述蒸馏塔优选包括一个或多个冷凝系统,其采用具有不同压力和温度等级的冷却水或冷却盐水作为操作介质。优选的是,将不能在第一冷凝阶段凝结的顶部流组分供给到下一个冷凝阶段和/或洗涤系统。两个蒸馏塔优选在尾气压力为-1到+10巴且沸腾温度处在-20℃到+200℃的范围内运行。低沸组分馏分和高沸组分馏分从不同的蒸馏塔内提取。设置蒸馏塔的操作压力使其遵循规定的流动方向。也可在蒸发器中使来自第一蒸馏塔的底部流发生部分或全部汽化,并且随后将所述流以双相形式或以气体流和液体流的形式进入第二蒸馏塔。该实施方式使在两个蒸馏塔间的连接流中方便地采用吸附器变为可能。适于吸附器安置的位置是两个蒸馏塔间的产物蒸汽流和两个蒸馏塔间的液体流。分隔壁塔和两个耦接蒸馏塔的实施使得可以更加容易地整合吸附器。这些吸附器可在预期的时间间隔内进行更换和调节。可进一步以一式两联的形式实施吸附器,以避免对分隔壁塔操作模式的任何限制。因此,并未出现因更换吸附器引起的分隔壁塔停机时间。所述目的进一步通过一种用于蒸馏分离多组分混合物的方法来实现本,所述混合物包含:包含二氯甲硅烷和至少一种含硼、含磷或含砷杂质的低沸组分,包含三氯甲硅烷和至少一种含硼、含磷或含砷杂质的中沸组分,和包含四氯化硅的高沸组分,其中所述方法包括向物料耦接于第二蒸馏塔的第一蒸馏塔供给所述多组分混合物,其中该第二蒸馏塔包括分开所述第二蒸馏塔的提馏段和精馏段的水平分隔壁,其中该第二蒸馏塔物料耦接于第三蒸馏塔,从而从第二蒸馏塔除去包含四氯化硅的底部馏分和包含二氯甲硅烷的顶部馏分,经由所述第三蒸馏塔的侧线馏分除去三氯甲硅烷,其中用于除去至少一种含硼、含磷或含砷杂质的吸附器放置于用于物料耦接该第二蒸馏塔和所述第三蒸馏塔的连接处,并且使物料流通过所述吸附器。优选的是,将用于除去所述至少一种含硼、含磷或含砷杂质的吸附器设置在用于物料耦接第二蒸馏塔与第一和第三蒸馏塔的所述两个连接处的每一处,其中物料流通过所述吸附器。在本发明的上下文中,物料耦接理解为在各种情况下,在各蒸馏塔间存在合适的进料和回流线。三个蒸馏塔是物料耦接的,其中一个蒸馏塔包括分开该蒸馏塔的提馏段和精馏段的水平分隔壁,从而两个不包括分隔壁的蒸馏塔可被认为是分隔壁塔的左手段和右手段。向被认为是分隔壁塔的左手段的第一蒸馏塔供给多组分混合物。来自第一蒸馏塔的蒸汽进入到第二蒸馏塔,在该第二蒸馏塔中提馏段和精馏段被水平分隔壁(例如分隔板)所分开。在该第二蒸馏塔内,包含至少一种低沸组分的顶部产物和包含至少一种高沸组分的底部产物均被除去。在被认为是分隔壁塔的右手段的第三蒸馏塔内,包含至少一种中沸组分的目标产物经由侧线馏分排出。蒸馏塔优选在尾气压力为-1到+10巴且沸腾温度处在-20℃到+200℃的范围内运行。优选的是,至少第二蒸馏塔包括一个或多个用于蒸发液体底部流的蒸发系统,其使用具有不同压力和温度等级的蒸汽或热油作为操作介质。优选的是,至少第二蒸馏塔包括一个或多个用于冷凝蒸汽流的冷凝系统,其使用具有不同压力和温度等级的冷却水或冷却盐水作为操作介质。优选的是,将不能在第一冷凝阶段凝结的顶部流组分供给进一步冷凝阶段和/或洗涤系统。第一和第三蒸馏塔优选包括1-200个理论塔板。所述目的可进一步通过一种用于蒸馏分离多组分混合物的装置来实现,其包括通过以下方式相互物料耦接的三个蒸馏塔:第一蒸馏塔的蒸汽与第二蒸馏塔的精馏段连通连接、第二蒸馏塔的精馏段与第三蒸馏塔的蒸汽连通连接、第一蒸馏塔的底部馏分与第二蒸馏塔的提馏段连通连接、且第二蒸馏塔的提馏段与第三蒸馏塔的底部连通连接,其中所述第二蒸馏塔包括水平分隔壁,其中第三蒸馏塔包括一个或多个位于所述顶部馏分下方和所述底部馏分上方的侧线馏分,其中用于除去含硼、含磷或含砷杂质的吸附器设置在用于物料耦接第二蒸馏塔和第三蒸馏塔的连接处,所述各个物料流通过所述吸附器。优选的是,将用于除去含硼、含磷或含砷杂质的吸附器设置在用于物料耦接第二蒸馏塔与第一和第三蒸馏塔的两个连接处中的每一处,各个物料流通过所述吸附器。在本发明的上下文中,可将连通连接理解为在各种情况下,在蒸馏塔间存在合适的进料和回流线。因此,本发明涉及一种装置设置,其中将附加的蒸馏塔连接到现有两个蒸馏塔上,从而实现热力和物料耦接。优选的是通过水平的不渗透板将第二蒸馏塔内的精馏段与提馏段分开。就操作模式而言,本发明符合分隔壁塔的原理,尽管其在装置实施方式方面有所不同,特别是因为由于使用具有水平分隔板的插入式蒸馏塔,在蒸馏塔内垂直分隔板并非是必须的。一个蒸馏塔与另一个蒸馏塔在空间独立的位置具有至少两个连接,由此实现两个蒸馏塔的物料耦接。在能源需求方面,此类塔配置相当于具有相同塔板数的单个分隔壁塔。由于可使用现有蒸馏塔且只需要获得一个比新分隔壁塔尺寸相对小的附加蒸馏塔,因此相比传统单分隔壁塔的新认知,这可以节约大量能源,并耗费较低资本。究其原因在于分隔壁塔的提馏段和精馏段通常塔板数较少。此外,在此构造中,旨在对应于分隔壁段的这两个蒸馏塔保持该构造的全直径。与分隔壁塔相比,这显著增加该设备的容量,所述分隔壁塔的直径仅相当于两个单个塔中一个的直径。在大多数情况下,该构造的资本成本由此低于在具有相同分离效能和容量的等效分隔壁塔中的新投资。本发明在设备的容量增加的同时减少了比能量的需求,这使其在改造上具有吸引力。从具有水平分隔壁的蒸馏塔内提取低沸组分馏分和高沸组分馏分。具有水平分隔壁的第二蒸馏塔优选设有专用蒸发器和冷凝器。优选调节该蒸馏塔的操作压力从而保持规定的流动方向。优选的是,将吸附器安装在从具有水平分隔壁的第二蒸馏塔的精馏段流向第三蒸馏塔的液体流中。特别优选的是,将吸附器安装在从具有水平分隔壁的第二蒸馏塔的精馏段流向第一和第三蒸馏塔的每股液体流中。优选的是,将吸附器放置在从第一和第三蒸馏塔流向具有水平分隔壁的第二蒸馏塔的提馏段的每股液体流中。一个实施方案采用两个吸附器,且在第一蒸馏塔和具有水平分隔壁的第二蒸馏塔之间的全部液体流均通过第一吸附器,而在第三蒸馏塔和具有水平分隔壁的第二蒸馏塔之间的全部液体流均通过第二吸附器。对具有本文概述的装置的分隔壁塔的概念的实现有以下作用:使得在使用除去硼成分的吸附器时没有限制。本文概述的概念允许持续操作该设备,即使当吸附器材料需要更换或调节时。所述吸附器优选以至少一式两联的形式实施,且因此其更换并不导致设备停机。基于分隔壁塔操作模式,分离液体流和产物蒸汽流给予在经典设置中不存在的额外的吸附器操作自由度。这有利于除去来自含氯硅烷产物流的含硼化合物。参考附图将本发明的优选实施方式版本以及所述版本和现有技术的不同之处进行如下阐明。与上述的根据本发明的方法的实施方案相关的引用特征均可应用到根据本发明的相应装置。反之,与以上描述的根据本发明装置的实施方案相关的引用特征均可应用到按照本发明的相应方法。在附图和权利要求书内阐明根据本发明的实施方案的这些和其它特征。在本发明实施方案的单独或组合的形式下,可以了解每一种情况下的单独特征。所述特征可以进一步描述可以适于保护它们自身权利的有利实施方式。附图简述图1显示根据现有技术包括具有吸附器的多个蒸馏塔的设置。图2显示根据现有技术无吸附器的分隔壁塔。图3显示根据现有技术无吸附器的活性分隔壁塔。图4显示根据本发明通过耦接两个具有吸附器的现有分隔壁塔所形成的分隔壁塔。图5显示根据本发明由用于分馏三组分混合物且具有吸附器的三个分馏塔构成的塔构造。图1显示具有冷凝器C1和蒸发器H1的第一塔K1,其经由物料流D1主要除去低沸组分。液体物料流B1进入吸附器A。气体物料流B2可经由侧线馏分选择性地供入吸附器内。在吸附器A内,按照预期吸附或转化含硼组分。在具有冷凝器C2和蒸发器H2的第二塔K2内,经由物料流B3主要除去高沸组分。在塔顶获得产物D2,且该产物或由其他蒸馏阶段中通过,或可直接沉淀为多晶体硅。在图2的布置中,原料流F进入具有蒸发器H和冷凝器C的塔TWK中。经由物料流D主要除去挥发化合物。物料流B主要包括高沸化合物。经由侧线馏分获得产物P,且该产物或由其他蒸馏阶段中通过,或可直接沉淀为多晶体硅。在图3的布置中,原料流F进入具有蒸发器H和冷凝器C的塔RTWK中。经由物料流D主要除去挥发化合物。物料流B主要包括高沸化合物。经由侧线馏分获得产物P,且该产物或由其他蒸馏阶段中通过,或可直接沉淀为多晶体硅。因此,在内部构件RP1-4表面涂覆有吸附材料,且因此按预期在所述内部构件表面吸附或转化含硼组分。图4显示原料流F进入具有蒸发器H和分隔壁的第一塔TWK1。在该塔内,经由底部产物流B主要除去高沸化合物。来自TWK1的蒸汽流V1和V2现在可由塔外面的吸附器A1中通过。两股流或者两股流中的一股可同时通过吸附器A1。在吸附器的下游将蒸汽流引入到分隔壁塔TWK2。塔TWK2具有冷凝器C和分隔壁。经由物料流D主要除去低沸化合物。经由侧线馏分除去物料流P内的目标产物,该物料流或由其他蒸馏阶段中通过,或可直接沉积为多晶体硅。在底部离开TWK2的两股液体物料流L1和L2进入到吸附器A2。这两股流或者两股流中只有一股可同时通过吸附器A2。在吸附器的下游,两股物料流作为回流被引入到塔TWK1。根据图5,进料流F进入第一塔K1。来自K1的底部馏分流L11通过吸附器A1供给。在吸附器A1的下游,物料流L11进入具有蒸发器H、冷凝器C和水平分隔壁的塔K3,其水平分隔壁将提馏段和精馏段彼此分开。物料流L11作为回流引入到塔K3的提馏段。来自塔K2的底部馏分流L21通过吸附器A2供给。在吸附器A2的下游,物料流L21同样作为回流引入到塔K3的提馏段。在该塔K3的提馏段内,经由底部产物流B主要除去高沸化合物。向两个塔K1和K2供给从蒸汽流G分离出来的蒸汽流V11和V21。在两个塔K1和K2的顶部,蒸汽流V12和V22被提取并供给塔K3的精馏段。离开K3的蒸汽流被冷凝,并经由支流D主要除去低沸化合物。回流R进入K3的精馏段,并以特定的比率以液体流L12和L22的形式通过吸附器A1和A2供给。在吸附器下游,向两个塔K1和K2供给这些物料流。在塔K2,经由侧线馏分除去物料流P,且该物料流或由其他蒸馏阶段中通过,或可直接沉淀为多晶体硅。实施例和对比例在对比例以及实施例1和2中,物料流F由含氯硅烷的混合物和l1组成,该含氯硅烷的混合物包含一种低沸组分馏分,该低沸组分馏分由MCS和DCS(单氯甲硅烷和二氯甲硅烷)组成,其中l1代表包含硼、磷和砷的低沸微量组分,例如BCl3、PH3或AsH3。在标准条件下,这些组分的沸点低于32℃。所述流还包括一种由TCS(三氯甲硅烷)和l2组成的中沸组分馏分,其中l2代表包含硼、磷和砷的中沸微量组分,例如B2Cl4。在标准条件下,这些组分的沸点大约为32℃。所述流还包括由STC(四氯甲硅烷)、高沸组分(其中高沸组分代表乙硅烷和低聚硅烷)和l3组成的高沸组分馏分,其中l3代表包含硼、磷和砷的高沸微量组分,例如B-O化合物。在标准条件下,这些组分的沸点高于32℃。对比例-经典设置图1显示由具有蒸发器H1和冷凝器C1的提馏塔K1以及具有蒸发器H2和冷凝器C2的精馏塔K2组成的经典蒸馏布置。将吸附器A放置在两塔之间。在塔K1中,经由物料流D1除去低沸组分馏分。物料流B1/B2通过吸附器A供给。在该吸附器内,以微量存在的包含硼、磷和砷的杂质被吸附并部分水解。在第二塔K2中,经由物料流B3提取高沸组分馏分,并经由物料流D2提取目标产物(中沸组分馏分)。表1显示根据对比例在各自支流内各个组分的质量比。表1物料流FD1B1D2B2组分TCS98.960%90.000%99.999%99.999%99.999%DCS1%10%---l13000ppbw30ppmw900ppta--l21000ppta-1100ppta1200ppta-l3100.0ppba-110ppba-10ppbaSTC100ppmw-110ppmw-1500ppmw高沸组分200ppmw-220ppmw-3000ppmw目标产物流D2主要包括TCS和中沸杂质l2。实施例1-具有吸附器的分隔壁塔图4显示根据本发明具有吸附器的分隔壁塔的优选实施方案,其包括以分隔壁塔实施且包括蒸发器H的第一蒸馏塔TWK1和同样以分隔壁塔实施且包括冷凝器C的第二蒸馏塔TWK2。将吸附器A1和A2放置在两塔之间。在塔TWK1中,经由物料流B除去高沸组分馏分。在第二塔TWK2中,经由物料流D提取低沸组分馏分,并经由物料流P提取目标产物(中沸组分馏分)。液体流L1和L2及产物蒸汽流V1和V2中的每股均可通过吸附器A1和A2供给,以从这些物料流内除去以微量存在的并包含硼、磷和砷的杂质,或者水解上述杂质。根据本发明的实施方式产生以下影响:同时采用吸附器A1和A2的操作模式可使吸附器容量加倍。表2显示根据实施例1中只操作吸附器A2的情况下,在各自支流内的各组分的质量比。表2物料流FDBP组分TCS98.960%85%99.999%99.999%DCS1%15%--l13000ppbw45ppmw--l21000ppta-4ppba1200pptal3100ppba-2000ppba-STC100ppmw-2000ppmw-HB200ppmw-4000ppmw-目标产物流P主要包括TCS和中沸杂质l2。在实施例1中这些化合物所占的比例比对比例低。浓度较高的微量组分出现在两股二次流中。生成的副产物的量减少,且在更大程度上消减杂质。表3显示根据施例1中操作吸附器A1和A2的情况下,在各自支流内的各组分的质量比。表3物料流FDBP组分TCS98.960%85%99.999%99.999%DCS1%15%--l13000ppbw45ppmw--l21000ppta-19ppba20pptal3100ppba-2000ppba-STC100ppmw-2000ppmw-HB200ppmw-4000ppmw-目标产物流P主要包括TCS和中沸杂质l2。对于具有两个吸附器A1和A2的操作模式,这些化合物所占比例甚至比只有一个吸附器的操作模式还要低。在副产物流B中,中沸杂质所占比例同样较高。实施例2-具有吸附器的塔构造图5显示有吸附器的本发明塔构造的优选实施方案,其包括第一蒸馏塔K1、第二塔K2及具有蒸发器H和冷凝器C的第三塔K3。将吸附器A1和A2放置在塔K1和K3之间以及在塔K2和K3之间。引入物料流到塔K1。在塔K3的提馏段中,经由物料流B除去高沸组分馏分。在塔K3的精馏段中,经由物料流D除去低沸组分馏分。液体流L11、L12、L21和L22中的每股均通过吸附器A1和A2供给,以从这些物料流内除去以微量存在的包含硼、磷和砷的杂质,或者水解上述杂质。表4显示根据实施例1只有吸附器A2起作用的情况下,在各自支流内的各组分的质量比。表4物料流FDBP组分TCS98.960%85%99.999%99.999%DCS1%15%--A3000ppbw45ppmw--B1000ppta-4ppba1200pptaC100.0ppba-2000ppba-STC100ppmw-2000ppmw-HB200ppmw-4000ppmw-目标产物流P主要包括TCS和中沸杂质B。实施例1中这些化合物所占比例要低于对比例。浓度较高的微量组分出现在两股二次流中。生成的副产物的量减少,且在更大程度上消减杂质。表5显示根据实施例1中操作吸附器A1和A2的情况下,在各自支流内的各组分的质量比。表5物料流FDBP组分TCS98.960%85%99.999%99.999%DCS1%15%--A3000ppbw45ppmw--B1000ppta-19ppba20pptaC100.0ppba-2000ppba-STC100ppmw-2000ppmw-HB200ppmw-4000ppmw-目标产物流P主要包括TCS和中沸杂质B。对于具有两个吸附器A1和A2的操作模式,这些化合物所占比例甚至比只有一个吸附器的操作模式还要低。在副产物流B中,中沸杂质所占比例同样较高。因此,可以注意到:根据实施例1和实施例2的本发明实施方式的两个版本与对比例相比有两个优势。对于相同的分离任务,根据实施例1和实施例2的两个版本的比能输入比对比例中的比能输入低50%。在工艺工程方面,两个实施例是等效的,且它们仅代表装置的不同实施方案。除了节约能源外,按照实施例1和实施例2的这两个版本中,除去中沸杂质B比对比例中更为有效。只有约20ppta的组分B留在目标产物流P中,而对比例的相应产物D2包含1200ppta。由于实施例1和实施例2在工艺工程方面是等效的,所以这两个版本在除去以微量存在的杂质的方面同样是相同的。根据本发明,这两个实施方式可以更为有效地除去组分B的原因在于在气相和液相中均选择使用双倍吸附器。伴随能量需求的减少可以显著更有效地除去组分l2。应将上述说明性实施方案的描述理解为示例性的。由此所作的本公开可以使本领域技术人员了解本发明及其相关优势,且其也包括对所述的结构和方法的改变和修改,这些对本领域技术人员都是显而易见的。因此,全部这些改变和修改及其等效物应在权利要求书的保护范围内。当前第1页1 2 3