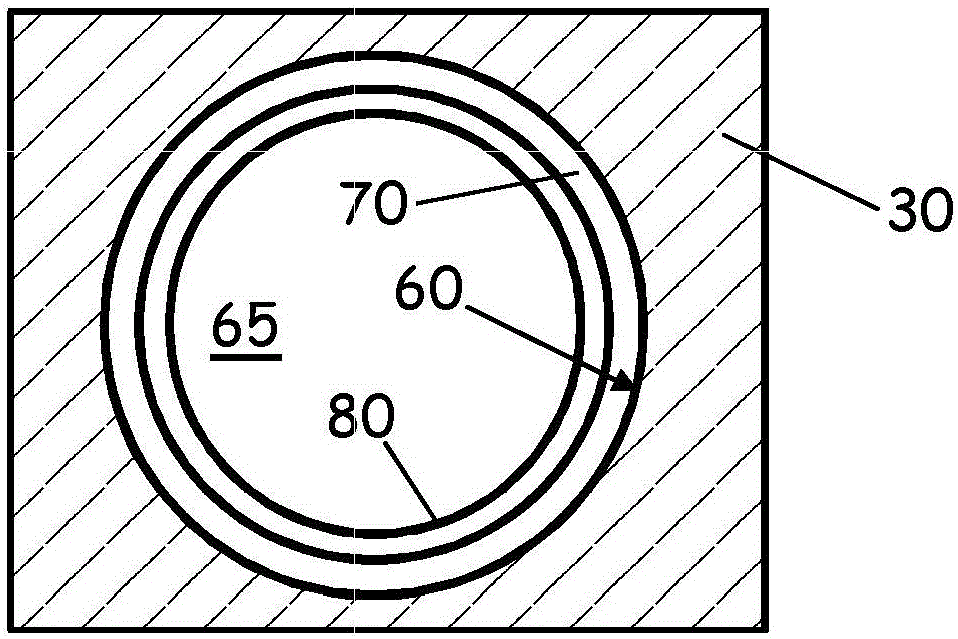
本申请根据35U.S.C.§119要求2012年6月5日提交的美国临时申请系列号61/655,692的优先权,本文以该申请的内容为基础并通过参考将其完整地结合于此。发明背景领域本发明总体涉及全蒸发(pervaporation)膜,具体来说,涉及将聚合物全蒸发膜涂覆到多孔陶瓷支架上的方法。技术背景全蒸发是衍生自包括渗透步骤和蒸发步骤的工艺的术语。在全蒸发时,可允许进料如流体(即,液体或气体)混合物渗透进入膜。可选定膜,从而流体混合物的所需组分以高于液体混合物中其它组分的速率吸附进入和穿过膜传输。然后,可蒸发渗透的流体,来从膜脱附,并形成基本上富集所需组分(相对于原始液体混合物而言)或者为纯净形式的所需组分的“渗透物”。通常通过膜的相对侧的压差来驱动蒸发。将没有穿过膜渗透的一部分进料称为“保留物”。与进料相比,保留物可包括更低量的所需组分,或者可基本上不含所需组分。因此,全蒸发已变成日益重要和感兴趣的区域,特别是在例如分离恒沸组分或沸点接近组分的无机-有机混合物以及此外用于汽油车载分离(OBS)的应用中。市售的聚合物材料通常不适于用作全蒸发膜材料,因为在连续使用之后会因为溶胀而发生膜降解和/或损失膜整体性。为此,可将含聚合物膜的复合材料施涂到稳定的多孔支架例如陶瓷例如,以提供机械支撑和对热老化和化学老化的耐受性。此外,可渗透的膜应该是真空密封的且无泄漏,从而保持对所需渗透物的选择性,但包括极少量的聚合物材料来最大化穿过全蒸发系统的流动。但是,将最佳的可渗透的聚合物膜施涂到高度多孔支架上仍然极具挑战性。因此,本领域需要方法,其中可将聚合物材料重复地涂覆到多孔支架上,从而提供无泄漏、真空密封、高通量、高选择性的全蒸发膜。发明概述根据各种实施方式,用于在多孔支架上制备聚合物膜的方法可包括提供多孔支架,其具有外壁,第一端部,第二端部,以及多孔通道表面,该多孔通道表面限定穿过多孔支架从所述第一端部到所述第二端部的多个通道。所述多个通道包括膜通道。限定膜通道的通道表面是膜-通道表面。可通过首先在所述外壁和所述多个通道之间构建压差,将所述聚合物膜涂覆到所述多孔支架上。然后,在保持压差时,可将预聚物涂层溶液施涂至膜-通道表面。这导致在膜-通道表面上形成预聚物层。然后,可固化所述预聚物层以形成所述聚合物膜。在以下的详细描述中提出了本发明的其他特征和优点,其中的部分特征和优点对本领域的技术人员而言,根据所作描述就容易看出,或者通过实施包括以下详细描述、权利要求书以及附图在内的本文所述的本发明而被认识。应理解,前面的一般性描述和以下的详细描述介绍了各种实施方式,用来提供理解要求保护的主题的性质和特性的总体评述或框架。包括的附图提供了对各种实施方式的进一步的理解,附图被结合在本说明书中并构成说明书的一部分。附图以图示形式说明了本文所述的各种实施方式,并与说明书一起用来解释要求保护的主题的原理和操作。附图简要说明图1是已根据本文所述的方法施涂了聚合物膜的多孔支架的示例性实施方式;图2是图1所述的多孔支架的膜通道的详细视图;图3是用于根据本文所述的方法将聚合物膜施涂至多孔支架的涂覆容器的示例性实施方式的横截面视图;和图4是施涂到多孔支架的各种涂覆层的孔径分布、以及制备根据本文所述的实施方式的聚合物膜所用的各种聚合物乳液的粒度分布图。发明详述下面将详细参考用于在多孔支架上制备聚合物膜的方法的实施方式。在一些实施方式中,所述方法可包括提供多孔支架,其具有外壁,第一端部,第二端部,以及多孔通道表面,该多孔通道表面限定穿过多孔支架从所述第一端部到所述第二端部的多个通道。所述多个通道包括膜通道。限定膜通道的通道表面是膜-通道表面。可通过首先在所述外壁和所述多个通道之间构建压差,将所述聚合物膜涂覆到所述多孔支架上。然后,在保持压差时,可将预聚物涂层溶液施涂至膜-通道表面以及,任选地,施涂至所述第一端部和所述第二端部。这导致在膜-通道表面以及,任选地,所述第一端部和所述第二端部上形成预聚物层。然后,可固化所述预聚物层以形成所述聚合物膜。多孔支架10的一种示例实施方式见图1。为了区分膜通道65,图1所示的多孔支架10存在用本文所述的方法施涂之后的所述聚合物膜80。多孔支架10可具有外壁20,第一端部30,和第二端部40。多孔支架还包括多孔通道表面50,60,其限定从第一端部30到第二端部40延伸穿过多孔支架10的多个通道55,65。所述多个通道55,65包括膜通道65。限定膜通道65的多孔通道表面50,60是膜-通道表面60。在一些实施方式中,所述多个通道55,65可包括非-膜通道55。在一些实施方式中,所有通道55,65可为膜通道65。应理解,在图1的非-膜通道55之间的膜通道65的构造只是示意性的,膜通道65可以任意所需方式排布在非-膜通道55(当存在时)之间。在一些实施方式中,如图1的实施方式中,多孔支架10可为蜂窝体整体件的形式。多孔支架10,例如蜂窝体整体件,可具有下述孔道密度:例如,50-600孔道/平方英寸。但是,已设想了多孔支架10可具有小于50孔道/平方英寸或大于600孔道/平方英寸的孔道密度。此外,适用于本文所述的方法的实施方式的蜂窝体整体件的示例见美国专利号3,885,977和3,790,654,该两篇文章的全部内容通过引用纳入本文。为了允许流经支架的流体流和多孔支架10自身之间的更加紧密的接触,例如当用于分离应用时,在一些未显示的实施方式中,理想地可在多孔支架10的一端堵塞至少一些通道55,65,而在多孔支架10的另一端堵塞其它通道。在一些实施方式中,可需要使堵塞和/或未堵塞的通道在多孔支架10的各端相互形成棋盘图案。在一些实施方式中,一个通道一端被堵塞(称为“参比端”)但多孔支架10的相对端没有被堵塞时,理想地可在多孔支架10的这种相对端但非参比端上堵塞与其紧邻的(与所涉通道共有至少一个壁的那些通道)至少一些例如大部分的通道(或者,在某些其他实施方式中优选所有)。此外,可以各种方式堆叠或容纳单个多孔支架例如蜂窝体,以形成具有各种尺寸、使用寿命等的更大的多孔支架,以满足不同使用条件的需求。在一个实施方式中,多孔支架10可以是无机材料。合适的无机多孔支架材料包括,例如,陶瓷、玻璃陶瓷、玻璃、金属、粘土、和其组合。一些示例性的材料包括,例如,堇青石、莫来石(mullite)、粘土、氧化镁、金属氧化物、滑石、锆石、氧化锆、锆酸盐、氧化锆-尖晶石、镁铝硅酸盐、尖晶石(spinel)、氧化铝、二氧化硅、硅酸盐、硼化物、铝硅酸盐、瓷器、锂铝硅酸盐、氧化铝石英、长石、二氧化钛、熔融石英、氮化物、硼化物、碳化物如碳化硅、氮化硅或任意这些材料的组合。在一些实施方式中,多孔支架10可为选自下组的陶瓷:α-氧化铝,堇青石,莫来石,二氧化钛,氧化锆,二氧化铈和其组合。多孔支架10在限定通道55,65的通道表面50,60上可具有任意宽范围的孔隙率和孔尺寸。在一种实施方式中,在施涂所述聚合物膜80之前,通道表面50,60可具有0.5μm-100μm,例如0.5μm-10μm的中值孔径。在用任何涂覆层涂覆之前,通道表面50,60可具有的孔隙率为30%-60%,例如,如用压汞孔隙率法(mercuryintrusionporosimetry)所测。在一些实施方式中,多孔支架10可具有任何形状或尺寸,且可由可在其上涂覆或施涂涂覆层例如所述聚合物膜80的任何固体、多孔材料形成。可成形、挤出或模塑例如所述多孔支架10。虽然图1所示的多孔支架10是圆柱的,应理解这只是示例性之目的,并不是限制性的。在其他示例性实施方式中,多孔支架10可具有最高达12英寸(30.5cm)的长度、1英寸(2.54cm)到3英寸(7.62cm)的外径,例如。多孔支架10的形状的其它实施方式不仅包括圆柱,还包括但不限于,具有如椭圆、六边形、五边形、矩形、正方形、菱形、三角形、甚至不规则形状的横截面形状的形状。在一些实施方式中,多孔支架10可为过滤器,例如蜂窝体过滤器。在一些实施方式中,多孔支架10可包括任意数目的通道55,65,从单一通道到数千通道。在一些实施方式中,通道55,65可具有各种横截面形状,例如圆形、椭圆形、三角形、方形、五边形、六边形或棋盘状或这些的任意组合,例如且可以任何合适的几何构造来排布。通道55,65可具有各种尺寸或直径,其可与多孔支架10自身之内的相同或不同。在示例性实施方式中,多孔支架10可为圆柱或椭圆堇青石蜂窝体整体件,其具有圆形、椭圆或六边形通道55,65。在多孔支架10上制备聚合物膜80的方法包括将所述聚合物膜80沉积至多孔支架10上。在一些实施方式中,将所述聚合物膜80沉积至多孔支架10上包括在多孔支架10的外壁20和多个通道55,65之间构建压差,然后在保持压差时将预聚物涂层溶液施涂至膜-通道表面。在一些实施方式中,还可将预聚物涂层溶液施涂至第一端部30和第二端部40。结果是在膜-通道表面60以及,任选地,所述第一端部30和所述第二端部40上形成预聚物层。然后,可固化所述预聚物层以形成所述聚合物膜80。任选地,可在沉积和固化所述聚合物膜80之前,将一种或更多种附加的层例如预涂层70施涂至至少膜-通道表面60。参考图3,根据一些实施方式,构建压差可包括将多孔支架10置于涂覆容器100中,其具有在其中限定的腔室120。应理解,图3的涂覆容器100显示为横截面,且其中放置了多孔支架10。涂覆容器100可包括从第一端部板160到第二端部板165延伸的容器壁110,从而容器壁110、第一端部板160和第二端部板165包围多孔支架10。腔室120可在多孔支架10第一端部30处的第一密封件130以及多孔支架10第二端部40处的第二密封件140之间限定。虽然在优选的实施方式中,涂覆容器100可垂直地取向(如图3所示),但应理解,涂覆容器100可以其它方式取向,例如水平地,例如。在图3所示的实施方式中,第一密封件130和第二密封件140是合适的材料(例如橡胶)的环。第一密封件130可固定于第一密封件底座150,其适于绕着多孔支架10的外壁20靠近多孔支架10的第一端部30形成真空密封的密封件。类似地,第二密封件140可固定于第二密封件底座155,其适于绕着多孔支架10的外壁20靠近多孔支架10的第二端部40形成真空密封的密封件。任选地,可通过下述来制备第一密封件底座150和第二密封件底座155的真空密封的密封件:沿着密封件底座150,155接触多孔支架10的外壁20的任何边缘,施涂密封材料例如填缝材料。第一密封件130和第二密封件140接触涂覆容器100的容器壁110。在沉积所述聚合物膜80时,多孔支架10的至少部分的外壁20设置在腔室120之中,且多孔支架10的第一端部30和第二端部40在腔室120之外。这样,该部分的外壁20与第一端部30和第二端部40分离,从而多个通道65和腔室120之间的流体连通只能通过外壁20进行,如图3所示。只要多个通道65的通道表面60保留一些孔隙率,就能进行这种多个通道65和腔室120之间的流体连通,并且当将足够真空密封的聚合物膜设置在通道表面60上和任选地设置在第一端部30和第二端部40上时可切断流体连通。涂覆容器100可包括结合到多孔支架10第一端部30的第一端口170,以结合到多孔支架10第二端部40的及第二端口180,从而所述第一端口170和第二端口180之间的流体连通可之间通过多个通道65进行。涂覆容器100还可包括结合到腔室120的第三端口190,从而第三端口190和第一和第二端口170,180之间的流体连通只能通过多孔支架10的外壁20进行。在一些实施方式中,可通过第一端口170或者从第二端口180,将涂层材料和/或洗涤溶剂引入多个通道65。可将真空或者背压应用到腔室120,使用连接到第三端口190的合适的泵(未显示)或者增压气源(未显示)。由此,当将涂层溶液例如预聚物涂层溶液施涂至膜-通道表面60时可构建外壁20和多个通道65之间的压差,如下文所更加详细描述。图3所示构造的涂覆容器100不仅适用于通道表面60,还适用于第一端部30和第二端部40。用于制备所述聚合物膜80的方法还可包括当保持所述外壁20和多个通道65之间的压差时,将预聚物涂层溶液施涂至膜-通道表面60以在膜-通道表面60上以及任选地第一端部30和第二端部40上形成预聚物层。在一些实施方式中,预聚物涂层溶液可通过粉浆涂覆来施涂。在其他实施方式中,预聚物涂层溶液可通过乳液涂覆来施涂。现在将描述预聚物涂层溶液。下面将描述两种涂覆施涂方法。在一些实施方式中,预聚物涂层溶液可选自各种固化以形成所述聚合物膜80的单体或低聚物。就这一点而言,预聚物涂层溶液可包括能在膜-通道表面60和任选地第一端部30和第二端部40上形成均匀涂层的单体或低聚物。在优选的实施方式中,预聚物涂层溶液不会大量渗透进入膜-通道表面60的孔,从而保持通道之间的足够的孔隙率,其中在例如全蒸发的应用中可发生渗透,例如。在示例性实施方式中,预聚物涂层溶液可包括当固化时形成聚合物材料的单体或低聚物例如,聚(乙烯丁缩醛)树脂、聚丙烯酸酯类、聚腈类(包括羧化-丙烯腈-共聚-丁二烯类)、聚氯丁二烯(氯丁二烯)、聚(氯乙烯)、聚(偏二氟乙烯)、聚烯烃类(例如聚乙烯或聚丙烯)、聚(四氟乙烯)、硅酮类、聚氨酯类,环氧树脂、聚乙烯醇类、聚硅氧烷类、多糖(例如,纤维素)、含有上述一种或多种的复合物,以及上述两种或更多种的混合物。所示实施方式的材料特别适合用于由陶瓷(例如,沸石、堇青石、碳化硅(SiC)、钛酸铝、莫来石、尖晶石、钙钛矿、硅酸盐、碳或氧化铝及其混合物)制造的蜂窝基材。在优选的实施方式中,预聚物涂层溶液可包括能形成交联的聚合物膜的单体或低聚物。例如,预聚物涂层溶液可包括形成交联的环氧-胺聚合物的环氧化物和二胺的混合物。在一种示例实施方式中,预聚物涂层溶液可包括环氧-二胺混合物例如DENO/D400,其包括1,2,7,8-二环氧辛烷(DENO)和O,O′-二(2-氨基丙基)聚丙二醇(D400)。在一些实施方式中,理想地将功能化微米颗粒或纳米颗粒结合进入所述预聚物涂层溶液。例如,为了无需多次施涂预聚物层来形成不含缺陷的聚合物膜,可将胺化氧化硅(即,用一种或更多种基团-NH2功能化的SiO2微米颗粒)微米颗粒添加至聚合物前体例如DENO/D400来修复裂纹和缺陷。在一示例实施例中,所述胺化氧化硅可包括标称粒度为约0.01μm-约0.05μm的氧化硅,通过使氧化硅颗粒与硅烷例如氨基丙基二甲基乙氧基硅烷(“APDMES”)反应来用胺功能化该氧化硅。在这种实施方式中,氧化硅颗粒可在缺陷区域有效地滤出,然后当固化预聚物层时,结合进入交联的聚合物网络。进而,氧化硅颗粒和聚合物网络的这种粘合可实施密封,同时最小化在聚合物膜80的表面上形成其它聚合物材料。可需要最小化聚合物的形成,来避免降低涂覆的多孔支架的流动容量。如上所述,预聚物涂层溶液可通过粉浆涂覆乳液涂覆来施涂。当预聚物涂层溶液通过粉浆涂覆来施涂时,在一些实施方式中,该预聚物涂层溶液只包括单体或低聚物材料,该材料当固化时形成所述聚合物膜,至少部分地溶于适当的有机溶剂中。在一些实施方式中,所述有机溶剂例如可为不与水互溶的溶剂例如甲苯。在预聚物涂层溶液将通过乳液涂覆来施涂的实施方式中,可将预聚物涂层溶液制备成水包油乳液。水包油乳液可包括水相、油相且该油相分散于水相中并包括聚合物前体(即,当固化时形成聚合物膜80的单体或低聚物),以及表面活性剂。在一些实施方式中,可通过将表面活性剂和水相添加到预聚物涂层溶液(例如如上所述的用于通过粉浆涂覆施涂预聚物层时那些)来制备水包油乳液。水相可包括水和一种或更多种水溶性或与水互溶的有机溶剂的混合物,或者水相可由水优选的去离子水组成。油相可主要由聚合物前体组成,或者可包括至少部分地溶于不与水互溶的有机溶剂例如甲苯的聚合物前体,例如。表面活性剂可为任意类型的表面活性剂,例如阴离子表面活性剂,阳离子表面活性剂,非离子表面活性剂,或其混合物,例如,其促进形成油相在水相中的水包油乳液。在一些实施方式中,水包油乳液可包括约0.1重量%-约10重量%油相,优选地约1重量%-约8重量%油相,例如约3.0重量%,约4.0重量%,或约5.0重量%油相,以该水包油乳液的总重量为基准计。在一些实施方式中,油相可包括约10重量%-约50重量%在有机溶剂中的聚合物前体,或者约15重量%-约35重量%在有机溶剂中的聚合物,例如20重量%或25重量%或30重量%在有机溶剂中的聚合物前体,以该油相的总重量为基准计。在一些实施方式中,水包油乳液可包括约0.01重量%-约20重量%,或者约0.05重量%-约10重量%,或者约0.1重量%-约0.5重量%表面活性剂,以水包油乳液的总重量为基准计。合适的表面活性剂的一个示例是十二烷基硫酸钠(SDS)。在一种示例实施方式中,水包油乳液可包括约2重量%-约6重量%的油相,该油相包括约15重量%-约35重量%溶解于甲苯(以油相的总重量为基准计)的DENO/D400低聚物;0.1重量%-10重量%SDS;和至100重量%的余量去离子水。在一种优选的实施方式中,水包油乳液可包括约4重量%的油相,该油相包括约25重量%DENO/D400低聚物和约75重量%甲苯(以油相的总重量为基准计);约0.1重量%-约5重量%的表面活性剂例如SDS(例如,0.1重量%-0.5重量%,0.2重量%-1.0重量%,0.3重量%-1.0重量%,约0.3重量%SDS,约0.4重量%SDS,或者约0.5重量%SDS);和至100重量%的余量去离子水。水包油乳液的油相可包括颗粒,该颗粒的中值粒度为0.1μm-500μm或者0.1μm-300μm,或者0.8μm-100μm,例如。在一些实施方式中,中值粒度可为1μm-20μm。不限于理论,据信选择在水包油乳液中的表面活性剂以及添加到水包油乳液的表面活性剂的量,可高度影响粒度。结果,可将水包油乳液的粒度定制为接近待施涂预聚物涂层溶液的膜-通道表面的孔径。在一些实施方式中,膜-通道表面可具有膜-通道孔径分布,以及可定制水包油乳液从而水包油乳液中的油相颗粒可具有油相粒度分布,其基本上重叠膜-通道孔径分布。就这一点而言,“基本上重叠”指油相粒度分布曲线下和膜-通道孔径分布曲线下的至少20%总面积是两种尺寸分布曲线重叠的区域。在一些实施方式中,水包油乳液可包括约0.1重量%-约15重量%表面活性剂,或0.2重量%-约10重量%表面活性剂,或约0.5重量%-约10重量%表面活性剂,或约0.5重量%-约5重量%表面活性剂,以水包油乳液的总重量为基准计。在一些实施方式中,水包油乳液可包括通式为R(OC2H4)nOH的乙氧基化非离子表面活性剂,其中R选自下组:含约8-约15碳原子的脂肪族烃基,以及烷基苯基基其中烷基包含约8-约12碳原子,n是约3-约9。合适的乙氧基化非离子表面活性剂是直链或支链构造的具有含约8-约15碳原子烷基的烷基苯酚和环氧乙烷的缩合产物,环氧乙烷以等于约3-约9摩尔环氧乙烷每摩尔烷基苯酚的量存在。其它可用的非离子表面活性剂包括伯或仲脂肪醇和约3-约9摩尔环氧乙烷每摩尔醇的缩合产物。脂肪醇的烷基链可以是直链或支链,且包括约8-约15碳原子。在一些实施方式中,表面活性剂可包括乙氧基化非离子表面活性剂例如:(1)环氧乙烷与疏水性碱的缩合产物,其通过环氧丙烷和丙二醇的缩合来形成,和/或(2)环氧乙烷与由环氧丙烷和乙二胺反应所得产物的缩合产物。这些表面活性剂由巴斯夫万道特(BASFWyandotte)出售,商标分别为和水包油乳液可具有宽范围的粘度例如25℃下为50cP-5000cP。除非另有说明,本文所述的粘度指使用布氏(Brookfield)粘度计所测的粘度,其中LVF第3号纺锤在25℃下以30rpm旋转。在一些实施方式中,水包油乳液可具有下述固含量:0.1重量%-10重量%,例如约1重量%-约5重量%以重量计,以乳液的总重量为基准计。如本文所使用,术语“固含量”指聚合物前体的重量,以水包油乳液的总重量为基准计。不限于理论,据信根据上文所述的实施方式通过乳液涂覆来施涂预聚物涂层溶液,只导致具有足够尺寸和稳定性的油相颗粒保留在膜-通道表面,而其它颗粒(例如较小或较不稳定的油相颗粒,例如,)穿过膜-通道表面的孔和穿过多孔支架10。因为油相颗粒通常不与已经在膜-通道表面上的陶瓷颗粒兼容,所以可发生非常少的预聚物涂层溶液沉积。在一些实施方式中,可通过下述来稀释水包油乳液:在水包油溶液穿过以后,将水添加至膜通道。据信,这种稀释可有助于形成更加均匀的预聚物层,还可稀释表面活性剂相对于油相的相对浓度。当洗掉表面活性剂时,据信水包油乳液可在膜-通道表面上去稳定,导致油相合并且形成均匀的膜。据信,一旦油相合并,油相不太可能回到水相,因为油-水相是不兼容的。为了通过粉浆涂覆施涂预聚物层,在一些实施方式中,可为膜通道65填充预聚物涂层溶液,通过第二端口180(例如,抵抗重力,从下往上)。在通过粉浆涂覆进行施涂时,可通过下述来保持外壁20和多个通道65之间的压差:通过涂覆容器100的第三端口190,施加约5kPa-约80kPa或约10kPa-约60kPa的背压。可通过将第三端口190连接到压缩气源(未显示)例如氮气或其它惰性气体的来源来施加背压,例如。不限于理论,据信背压可将预聚物涂层溶液的液体组分压入多孔支架10,从而使预聚物涂层溶液的固体组分留在膜-通道表面60上,还避免任何预聚物涂层溶液渗透进入膜-通道表面60,这种渗透可能不利地导致流动容量下降的较厚的聚合物膜。粉浆涂覆的预聚物涂层溶液可允许浸入至少膜-通道表面60并保持适当的时间例如30秒-5分钟,例如,在此之后,可通过第二端口180从膜通道65排放预聚物涂层溶液。任选地,可通过第一端口170或第二端口180施加短暂的真空(5秒-2分钟,例如),从而从膜通道65去除任何过量的预聚物涂层溶液。在一些实施方式中,在引入预聚物涂层溶液之前,可用水性或有机溶剂预填充膜通道65。不限于理论,据信溶剂预填充可防止预聚物涂层溶液大量渗透进入膜-通道表面60的孔或空穴中,并由此保留聚合物膜80的高通量容量。为了通过乳液涂覆施涂预聚物层,在一些实施方式中,可通过第一端口170(例如,借助重力,从上到下)用预聚物涂层溶液(其为乳液)填充膜通道65,如下文所更加详细描述。任选地,当填充膜通道65时,第一端部30和第二端部40可中的一种或两种可暴露于预聚物涂层溶液以形成在膜通道65,第一端部30,和第二端部40上的预聚物层。和如上所述的粉浆涂覆相对,在进行乳液涂覆时,可通过下述来保持外壁20和多个通道65之间的压差:通过涂覆容器100的第三端口190,施加约-5kPa到约-100kPa或约-10kPa到约-50kPa的真空。不限于理论,据信以这种方式施加真空可将聚合物乳液的水性组分拉入膜-通道表面的孔中,于是它们穿过多孔支架10的外壁20移动并进入腔室120。在一些实施方式中,可用预聚物涂层溶液(即,聚合物乳液)填充膜通道65,然后用水冲洗膜通道65。可真空干燥膜通道来去除任何残留的水,例如通过用第三端口190,通过穿过膜通道65形成独立的真空(例如,从第一端口170和第二端口180),或两者,来保持真空。用于在多孔支架上制备聚合物膜的方法还可包括固化预聚物层以形成所述聚合物膜。在一些实施方式中,可通过热处理来固化预聚物层,例如将多孔支架加热到约120℃-约180℃的固化温度,取决于选定作为聚合物膜的材料。固化可在约2小时-约24小时的固化时间下进行,也取决于选定作为聚合物膜的材料。在一些实施方式中,固化可在惰性气氛例如氮气下进行。一旦聚合物膜的固化完成,可测试涂覆的多孔基片的真空密封性和质量增加。这些是有用的价值数据,因为全蒸发性能例如可通过聚合物膜选择性和透过聚合物膜的通量进行控制。这些参数高度取决于对聚合物膜沉积工艺的控制。总的来说,涂覆的多孔膜的真空密封性可直接与它在全蒸发应用中的选择性相关。质量增加可与聚合物膜的厚度以及渗透进入膜-通道壁孔中的聚合物材料(如有)的量相关。由此,质量增加还可预测涂覆的多孔支架的流动容量。在一些实施方式中,如果发现真空密封性低于涂覆的聚合物膜在所需应用例如全蒸发中所用的最佳水平,例如,可将一种或更多种附加的层的聚合物膜施涂到现有聚合物膜上。一种或更多种附加的层可为缺陷修复层,其堵塞任何缺陷例如在聚合物膜中的针孔。一种或更多种附加的层可通过下述来形成:重复施涂预聚物涂层溶液以形成预聚物层(缺陷修复层),固化预聚物层(缺陷修复层)的步骤,从而增加所述聚合物膜的真空密封性,由此形成修复的聚合物膜。在一些实施方式中,在施涂一种或更多种缺陷修复层时,构建压差的步骤可为优选地但通常是任选的。虽然在一些实施方式中,根据本文所述的方法施涂单层聚合物膜可提供适当真空密封的聚合物膜,但在其他实施方式中可在2-10沉积之后取得最佳真空密封性。即使如此,应认识通过多次沉积增加所述聚合物膜厚度的益处,可被任何潜在地降低涂覆的多孔支架在其预期应用中的流动容量所抵消。在一些实施方式中,当施涂附加的层时,可按需构建压差例如背压(对于粉浆涂覆)或施加的真空(对于乳液涂覆),何时施涂附加的层取决于所述聚合物膜80已经有多真空密封。用于在多孔支架10上制备所述聚合物膜80的方法的其它实施方式可包括:在构建压差和施涂预聚物涂层溶液之前,将预涂层70(见图2)施涂至膜-通道表面60和任选地施涂至第一端部30和第二端部40。预涂层可具有预涂层平均孔径,其小于多孔支架的通道表面的平均孔径。一般来说,据信在孔径小于现成提供的多孔支架的孔径的表面上制备聚合物膜80,可促进形成更加均匀的聚合物膜,其更不容易包括可能损坏真空密封性的针孔缺陷。虽然现成提供的多孔支架的通道表面的平均孔径可为约0.5μm-100μm,例如,如果施涂了预涂层70,预涂层平均孔径可为约0.3μm-约1μm,由此提供更加适于在其上施涂真空密封的聚合物膜的、更小多孔表面。还据信施涂预涂层70可促进具有理想厚度例如小于20μm例如以保留流动容量膜通道60的真空密封的聚合物膜80的能力。具体来说,聚合物膜的厚度控制膜通道60的流动容量,且如果所述聚合物膜80太厚,在应用例如全蒸发中可穿过膜-通道壁65的渗透物的量可大量降低,例如。因此,由预涂层70提供的较小无机孔径可使得能密封膜-通道壁65,至少部分地放置所述聚合物膜80的聚合物大量渗透进入多孔支架10。一般来说,聚合物的渗透可导致无优势的厚聚合物膜(例如大于20μm),其得到具有较小流动的多孔支架。在一些实施方式中,可通过粉浆涂覆来施涂预涂层70。粉浆涂覆可通过如上所述的涂覆容器100来实现,或者可通过任何其它常规技术来实现。一般来说,预涂层70的粉浆涂覆可包括将涂覆粉浆制备成无机颗粒在载体液体中的分散体、泥浆或悬浮液,例如。载体液体可为水性的或有机的。涂覆粉浆可包含额外的成分如分散剂、润滑剂、增塑剂、粘合剂、抗裂剂、消泡剂、或混合物。各种无机颗粒可用于预涂层70的涂覆粉浆,其包括,但不限于:堇青石、氧化铝(如α-氧化铝和γ-氧化铝)、莫来石、钛酸铝、二氧化钛、氧化锆、二氧化铈颗粒和组合。可取决于多孔支架的孔径来选择无机颗粒的尺寸。例如,无机颗粒的中值粒度可为0.02μm-10μm。在一些实施方式中,涂覆粉浆可包括0.1重量%-50重量%无机颗粒,以涂覆粉浆的总重量为基准计。一般来说,据信较高的无机颗粒浓度可制备更厚、更粘的粉浆,这依次趋于在多孔支架上制备更厚的预涂层。涂覆粉浆还可包括,例如分散剂、粘结剂、防裂剂、消泡剂或其组合,可能包括水性或有机载体且可为淤浆或悬浮液的形式。描述了用于在多孔支架上制备聚合物膜的各种方法的实施方式。根据如上所述的一种或更多种实施方式制备的聚合物膜可重复制备,且可具有适用于例如全蒸发的应用的特征,其需要基本上无泄漏、真空密封的、高通量的和高选择性的涂覆的多孔支架。因此,其它实施方式包括涂覆的多孔支架,其通过本文所述的用于在多孔支架上制备聚合物膜的任何方法来制备。其它实施方式包括全蒸发系统或设备,其包括通过本文所述的用于在多孔支架上制备聚合物膜的任何方法来制备的至少一个涂覆的多孔支架。实施例通过以下实施例进一步阐述本发明的实施方式。实施例1制备预聚物乳液溶液为了用于乳液沉积中,制备预聚物涂层溶液。制备聚合物前体溶液,其包括25重量%溶于甲苯的DENO/D400低聚体。然后,将8g聚合物前体溶液和10克的水性10重量%十二烷基硫酸钠(SDS)溶液结合。摇晃和涡旋所述混合物以形成白色粘性浆料,然后用182克的去离子水稀释该混合物,得到200mL的预聚物涂层溶液,其包括0.5重量%SDS和4重量%有机相。添加磁力搅拌棒,在用于涂覆多孔支架之前,将乳液剧烈搅拌3-16小时。实施例2表面活性剂含量对乳液涂覆的聚合物膜的影响在图3的涂覆容器中,使用如实施例1所述制备的乳液,在多孔支架上制备DENO/D400的聚合物膜。具体来说,测试了含0.1重量%SDS,0.5重量%SDS,和5.0重量%SDS的乳液,来评估乳液中表面活性剂含量对所述聚合物膜质量的影响。将乳液涂层施涂到两个预涂覆的多孔支架,其平均孔径为0.2μm和0.01μm。0.01μm和0.2μm的平均孔径是通过将不同粒度的预涂层粉浆涂覆至大块未经处理直接使用的多孔支架上来获得的。用乳液从上到下填充多孔支架的膜通道,且允许乳液穿过多孔支架过滤。通过将多孔支架在室温下(25℃)放置16小时来干燥多孔支架,然后进行真空测试来评估涂层。如表1所示,发现虽然0.1重量%SDS和5重量%SDS乳液得到只有中等水平真空密封性的聚合物膜,但用0.5重量%SDS稳定的乳液提供特别水平的真空密封性。虽然所有3种乳液都是牛奶白,但需指出0.5重量%SDS乳液一致地比其它两种更不透明。表1样品乳液中的SDS含量增加的质量真空测试10.1重量%0.236g抽吸到-35kPa20.5重量%0.149g抽吸到-80kPa35.0重量%0.137g抽吸到-35kPa不限于理论,据信乳液中油相的粒度可与所得聚合物膜的真空密封性相关联。进行了粒度分析。如图4所示,粒度分析表明0.5重量%SDS乳液(峰B)的乳液粒度分布集中于约2微米,而0.1重量%SDS乳液(峰C)和5重量%SDS乳液(峰D)的乳液粒度分布分别居中于约30微米和100微米。应指出,0.5重量%SDS乳液(峰B)的乳液粒度分布基本上重叠施涂至0.2-μm多孔支架的预涂层(峰C)的孔径分布。平均孔径为0.01μm的多孔支架的密封方式和平均孔径为0.2μm多孔支架的密封方式非常相同,且0.5重量%SDS乳液显示增加的真空密封性。尽管0.2微米支架的表面比0.01微米支架的表面粗糙得多,但结果和0.2微米支架的类似,可能是因为孔径分布相似。从图4可知,0.01-μm支架的孔径分布(峰A)也基本上重叠0.5重量%SDS乳液(峰B)的乳液粒度分布,特别是在集中于约0.3微米的宽度中。实施例3粉浆涂覆聚合物膜通过粉浆涂覆,将额外的DENO/D400聚合物膜施涂到平均孔径为0.2μm和0.01μm的多孔支架。用预聚物涂层溶液涂覆粉浆(12.5重量%在甲苯中的DENO/D400),从下到上填充多孔支架的通道。从外壁将约60kPa的背压施加进入通道。使涂覆粉浆在通道中保留2分钟,然后排空。施加短暂的真空(10秒)来从通道驱出过量的涂层溶液。从涂覆容器取出多孔支架,允许过夜干燥(16小时),并在150℃(4-18小时,氮气中)下固化。检查多孔支架,以测定质量增加和聚合物膜的真空密封性。实施例4表征DENO/D400聚合物膜表征在实施例2和3中制备的各种聚合物膜。通过SEM,聚合物膜显示为在通道壁上的连续的膜,没有证据表明其渗透穿过块体陶瓷。在0.2微米多孔支架上的聚合物膜厚度在一次乳液处理后是约1-2微米。在较粗糙的预涂覆的样品上,有些聚合物渗透是明显的,可能是因为表面粗糙度增加。发现使用第一乳液涂覆涂覆的聚合物膜是稳定的且对芳香族化合物(汽油)相对于乙醇具有中等选择性,但发现选择性比使用粉浆涂覆形成的聚合物膜的选择性更低。乳液涂覆的膜的选择性降低可能源自不受限制的溶胀(当膜与汽油接触时),因为膜停留在陶瓷涂层的顶部,而不是像粉浆涂覆的聚合物膜那样插层在颗粒之间。即,颗粒可用作限制溶胀的机械阻挡。发现用粉浆涂覆工艺涂覆的聚合物膜显示聚合物膜显著地渗透进入陶瓷。因此,虽然发现粉浆涂覆的膜具有更高的选择性,但增加的选择性可被流动容量的牺牲而抵消。相反,发现用乳液涂覆的聚合物膜显示更少的渗透。就这一点而言,乳液-涂覆的多孔支架可与下述应用更加兼容:其需要高通量容量且选择性不那么重要。实施例5使用胺功能化的热解二氧化硅制备DENO/D400制备胺功能化的热解二氧化硅,用于添加至用于将聚合物膜施涂到多孔支架的预聚物乳液。为了制备功能化的二氧化硅,在具有搅拌棒的50毫升螺旋帽离心管中,将标称粒度为0.014微米、聚集体尺寸为几微米且表面积为200m2/g的0.2克的热解二氧化硅(西格玛奥德里奇公司(Sigma-Aldrich))与20毫升甲苯结合。添加0.1毫升的催化剂乙二胺,将内容物混合2小时。添加硅烷,即0.1毫升的氨基丙基二甲基乙氧基硅烷(“APDMES”)并连续搅拌。将该密封的管加热到80℃保持2小时,然后冷却至室温。然后在6000rpm下将悬浮液离心15分钟,进行倾滗(decanted)。将所得凝胶洗涤两次,用10毫升甲苯再次悬浮,且每次洗涤都包括离心。在氮气下储存胺功能化的凝胶即“APDMES-SiO2,”。过夜干燥小样品,发现包括6.05%固体。通过将1.81g凝胶悬浮在17.21g如实施例1所述的12.5重量%DENO/D400在甲苯中的聚合物前体溶液中,来制备胺功能化的凝胶悬浮液。将悬浮液超声振动3分钟。最终悬浮液的粘度是1.6cP,包括0.577重量%APDMES-SiO2,11.3重量%在甲苯中的D400-DENO。将2克样品分布在铝称重盘中,干燥并在150℃下固化3小时,得到无明显裂纹的0.23克浑浊聚合物。计算的二氧化硅在固化聚合物中的浓度是4.9%。实施例6用在D400/DENO中的APDMES-SiO2涂覆多孔支架用在实施例5制备的APDMES-SiO2/D400/DENO溶液粉浆涂覆单通道、2-英寸长氧化铝涂覆的莫来石,其通道直径为1.6mm-1.8mm且孔隙率为0.2μm,以获得二氧化硅-聚合物-陶瓷膜复合材料。通过用致密环氧-陶瓷填料填充来堵塞整体件的所有通道的端部,但中央通道除外其两端仍然保持开口。对抗16kPa的氮气背压,用聚合物溶液填充开口的通道,并超声振动30秒。没有观察到气体的气泡。排放聚合物溶液,在环境条件下过夜干燥多孔支架,并在150℃下固化3小时。在第一次涂覆之后,只观察到0.02克的重量增加,且涂覆的整体件不能保持真空。使用相同的步骤进行3次附加涂覆,最终的总重量增加为0.13克。真空测试得到在10分钟内从10kPa起6.3kPa/分钟的压力增加,表明膜是真空密封的。实施例7全蒸发测试评估实施例6制备的二氧化硅-聚合物涂覆的支架用于全蒸发。使用进料模型来评估膜,其组成包括10重量%乙醇,45重量%甲苯,和45重量%n-庚烷。水平地安装测试支架。以1.0毫升/分钟提供进料,与在约500毫升/分钟下回收的保留物混合,并加热在膜之前获得操作温度。通过在650kPa(abs)压力下的1.0毫升/分钟加料和140℃膜温下构建全蒸发测试条件。通过真空泵施加真空来获得~0.5kPa的渗透压。在干冰上收集渗透产物,并用气相色谱分析。在140℃下测定膜的初始性能和稳定性。在540小时的时段内进行测试。在各每天运行结束时将膜冷却到环境温度,并停止加料速率。在140℃下花费的总时间约为43小时。在初始的边缘周期之后,流动速率温度在约0.89g/s·m2。进料的渗透物产率是1.8%(重量/重量)。测定的渗透物组成(重量/重量)是9.2%n-庚烷,37.7%甲苯和53.2%乙醇。甲苯相对于n-庚烷的选择性是4.1,乙醇和甲苯相对于n-庚烷的选择性之和是8.1。实施例8表征具有在D400/DENO中的APDMES-SiO2的多孔支架从测试装置取下实施例7所用的复合材料膜,并用光学显微镜和SEM表征。光学显微镜表明在整体件的开口中央通道的表面上有深色膜涂层。在横截面中,发生至少部分的聚合物前体溶液的渗透。所用膜的SEM显示约4微米厚度的聚合物膜,其极小的表明在下面的支架颗粒上有渗透的聚合物。聚合物膜上的许多小颗粒(二氧化硅的)是明显的。颗粒看起来完全被聚合物包封。在第一方面中,本发明提供用于在多孔支架10上制备聚合物膜80的方法。所述方法包括提供多孔支架10,其具有外壁20,第一端部30,第二端部40,和多孔通道表面50,60,该多孔通道表面限定从第一端部30到第二端部40穿过多孔支架10的多个通道55,65。所述多个通道55,65包括由膜-通道表面60限定的膜通道65。所述方法还可包括在所述外壁20和多个通道55,65之间构建压差。所述方法可包括当保持压差时,将预聚物涂层溶液施涂到至少膜-通道表面60以在膜-通道表面60上形成预聚物层。所述方法可包括固化预聚物层以形成所述聚合物膜80。在第二方面中,本发明提供第一方面所述的在多孔支架10上制备聚合物膜80的方法,其中所述多孔支架10是蜂窝体整体件。在第三方面中,本发明提供第一方面或第二方面所述的在多孔支架10上制备聚合物膜80的方法,其中所述多孔支架10包括选自下组的陶瓷:堇青石,α-氧化铝,莫来石,二氧化钛,氧化锆,二氧化铈和其组合。在第四方面中,本发明提供第一方面到第三方面中任一项所述的在多孔支架10上制备聚合物膜80的方法,其中所述方法还包括在构建压差和施涂预聚物涂层溶液之前,将预涂层70施涂到至少膜-通道表面60。预涂层70可具有预涂层平均孔径,其小于支架膜-通道表面60的平均孔径。在第五方面中,本发明提供第四方面所述的在多孔支架10上制备聚合物膜80的方法,其中所述预涂层包括选自下组的陶瓷颗粒:堇青石,α-氧化铝,莫来石,钛酸铝,二氧化钛,氧化锆,二氧化铈和其组合。在第六方面中,本发明提供第一方面到第五方面中任一项所述的在多孔支架10上制备聚合物膜80的方法,其中将预聚物涂层溶液施涂至膜-通道表面60,第一端部30,和第二端部40,以及在膜-通道表面60,第一端部30,和第二端部40上形成预聚物层。在第七方面中,本发明提供第一方面到第六方面中任一项所述的在多孔支架10上制备聚合物膜80的方法,其中构建压差包括将多孔支架10置于涂覆容器100中,其具有在其间且在多孔支架10第一端部30处的第一密封件130以及多孔支架10第二端部40处的第二密封件140之间限定的腔室120。至少部分的多孔支架10的外壁20设置在腔室120之中,且多孔支架10的第一端部30和第二端部40在腔室120之外。由此,多个通道55,65和腔室120之间的流体连通只通过外壁20来进行。如第七方面所述的方法还可包括将真空或背压施加到腔室120。在第八方面中,本发明提供第七方面所述的在多孔支架10上制备聚合物膜80的方法,其中所述涂覆容器100包括结合到多孔支架10的第一端部30的第一端口170。第二端口180结合到多孔支架10的第二端部40,从而第一端口170和第二端口180之间的流体连通通过多个通道55,65进行。第三端口190结合到腔室120,从而第三端口190和第一和第二端口170,180之间的流体连通只能通过多孔支架10的外壁20进行。在第九方面中,本发明提供第一方面到第八方面中任一项所述的在多孔支架10上制备聚合物膜80的方法,其中所述预聚物涂层溶液包括在不与水互溶的有机溶剂中的聚合物前体。在第十方面中,本发明提供第一方面到第九方面中任一项所述的在多孔支架10上制备聚合物膜80的方法,其中所述预聚物涂层溶液包括在不与水互溶的有机溶剂中的聚合物前体。在第十一方面中,本发明提供第七方面到第十方面中任一项所述的在多孔支架10上制备聚合物膜80的方法,其中构建压差包括将背压施加到腔室120。在第十二方面中,本发明提供第十方面或第十一方面所述的在多孔支架10上制备聚合物膜80的方法,其中所述聚合物前体包括1,2,7,8-二环氧辛烷和O,O′-二(2-氨基丙基)丙二醇单体或低聚物的环氧-二胺混合物。在第十三方面中,本发明提供第十二方面所述的在多孔支架10上制备聚合物膜80的方法,其中聚合物前体还包括悬浮于环氧-二胺混合物中的胺功能化的氧化硅颗粒。在第十四方面中,本发明提供第一方面到第十方面中任一项所述的在多孔支架10上制备聚合物膜80的方法,其中所述预聚物涂层溶液是水包油乳液,其包括水相;油相,该油相分散于水相中且包含在不与水互溶的有机溶剂中的聚合物前体;以及表面活性剂。在第十五方面中,本发明提供第七方面到第十方面中任一项所述的在多孔支架10上制备聚合物膜80的方法,其中构建压差包括将真空施加到腔室120。在第十六方面中,本发明提供第十四方面或第十五方面所述的在多孔支架10上制备聚合物膜80的方法,其中膜-通道表面60具有膜-通道孔径分布,水包油乳液包括油相颗粒,该油相颗粒的油相粒度分布基本上重叠膜-通道孔径分布。在第十七方面中,本发明提供第十四方面到第十六方面所述的在多孔支架10上制备聚合物膜80的方法,其中所述聚合物前体包括1,2,7,8-二环氧辛烷和O,O′-二(2-氨基丙基)丙二醇单体或低聚物的环氧-二胺混合物。在第十八方面中,本发明提供第十四方面到第十七方面中任一项所述的在多孔支架10上制备聚合物膜80的方法,其中表面活性剂包括十二烷基硫酸钠或者乙氧基化非离子表面活性剂。在第十九方面中,本发明提供第十四方面到第十八方面中任一项所述的在多孔支架10上制备聚合物膜80的方法,其中水包油乳液包括0.1重量%-10重量%油相,以水包油乳液总重量为基准计,其中油相包括10重量%-50重量%聚合物前体,以油相总重量为基准计。水包油乳液还包括0.1重量%-10重量%表面活性剂,以水包油乳液总重量为基准计。在第二十方面中,本发明提供第十四方面到第十九方面中任一项所述的在多孔支架10上制备聚合物膜80的方法,其中所述聚合物前体包括1,2,7,8-二环氧辛烷和O,O′-二(2-氨基丙基)丙二醇单体或低聚物的环氧-二胺混合物;所述水包油乳液包括0.2重量%-1重量%表面活性剂,以水包油乳液总重量为基准计;和表面活性剂包括十二烷基硫酸钠。在第二十一方面中,本发明提供第十四方面到第二十方面中任一项所述的在多孔支架10上制备聚合物膜80的方法,其中表面活性剂包括乙氧基化非离子表面活性剂。在第二十二方面中,本发明提供第二十一方面所述的在多孔支架10上制备聚合物膜80的方法,其中所述乙氧基化非离子表面活性剂选自下组:(a)使环氧乙烷与由环氧丙烷和丙二醇缩合形成的疏水性碱反应得到的缩合产物;(b)使环氧乙烷与由环氧丙烷和乙二胺反应形成的分子的缩合产物;以及(c)即(a)和(b)的混合物。在第二十三方面中,本发明提供第十五方面到第二十二方面中任一项所述的在多孔支架10上制备聚合物膜80的方法,其中将约-5kPa到约-100kPa的真空施加到腔室120。在第二十四方面中,本发明提供第一方面到第二十三方面中任一项所述的在多孔支架10上制备聚合物膜80的方法,其中在固化所述聚合物膜80之后,通过重复施涂预聚物涂层溶液和固化预聚物层的步骤,来将2-10附加的层的聚合物膜施涂至所述聚合物膜80。在第二十五方面中,本发明提供第一方面到第二十三方面中任一项所述的在多孔支架10上制备聚合物膜80的方法,其中所述方法还包括在构建压差和施涂预聚物涂层溶液之前,将预涂层70施涂到至少膜-通道表面60。在第二十六方面中,本发明提供第二十五方面所述的在多孔支架10上制备聚合物膜80的方法,其中支架平均孔径是约0.5μm-约100μm和预涂层平均孔径是约0.3μm-约1μm。在第二十七方面中,本发明提供第一方面到第二十六方面中任一项所述的在多孔支架10上制备聚合物膜80的方法,其中用所述方法形成的聚合物膜80对对施加到涂覆的多孔支架10的第一端部30和第二端部40的至少-50kPa真空是不可渗透的。在第二十八方面中,本发明提供第一方面到第二十七方面中任一项所述的在多孔支架10上制备聚合物膜80的方法,其中固化包括将多孔支架10加热到约120℃-约180℃的固化温度,保持约4小时-约18小时的固化时间。在第二十九方面中,本发明提供第一方面到第二十八方面中任一项所述的在多孔支架10上制备聚合物膜80的方法,其中所述方法还包括在施涂预聚物溶液和固化预聚物层之间,用水淋洗通道表面(50,60)。在第三十方面中,本发明提供第一方面到第二十九方面中任一项所述的在多孔支架10上制备聚合物膜80的方法,其中聚合物膜80小于20微米厚。在第三十一方面中,本发明提供第一方面到第三十方面中任一项所述的在多孔支架10上制备聚合物膜80的方法,其中在施涂预聚物涂层溶液之前,用溶剂预填充至少膜通道65。在第三十二方面中,本发明提供使用第一方面到第三十一方面中任一项所述的方法制备的聚合物膜涂覆的多孔支架。在第三十三方面中,本发明提供包括至少一个如第三十二方面所述的聚合物膜涂覆的多孔支架的全蒸发系统或设备。本领域的技术人员显而易见的是,可以在不偏离要求专利权的主题的精神和范围的情况下,对本文所述的实施方式进行各种修改和变动。因此,本说明书旨在涵盖本文所述的各种实施方式的修改和变化形式,只要这些修改和变化形式落在所附权利要求及其等同内容的范围之内。当前第1页1 2 3