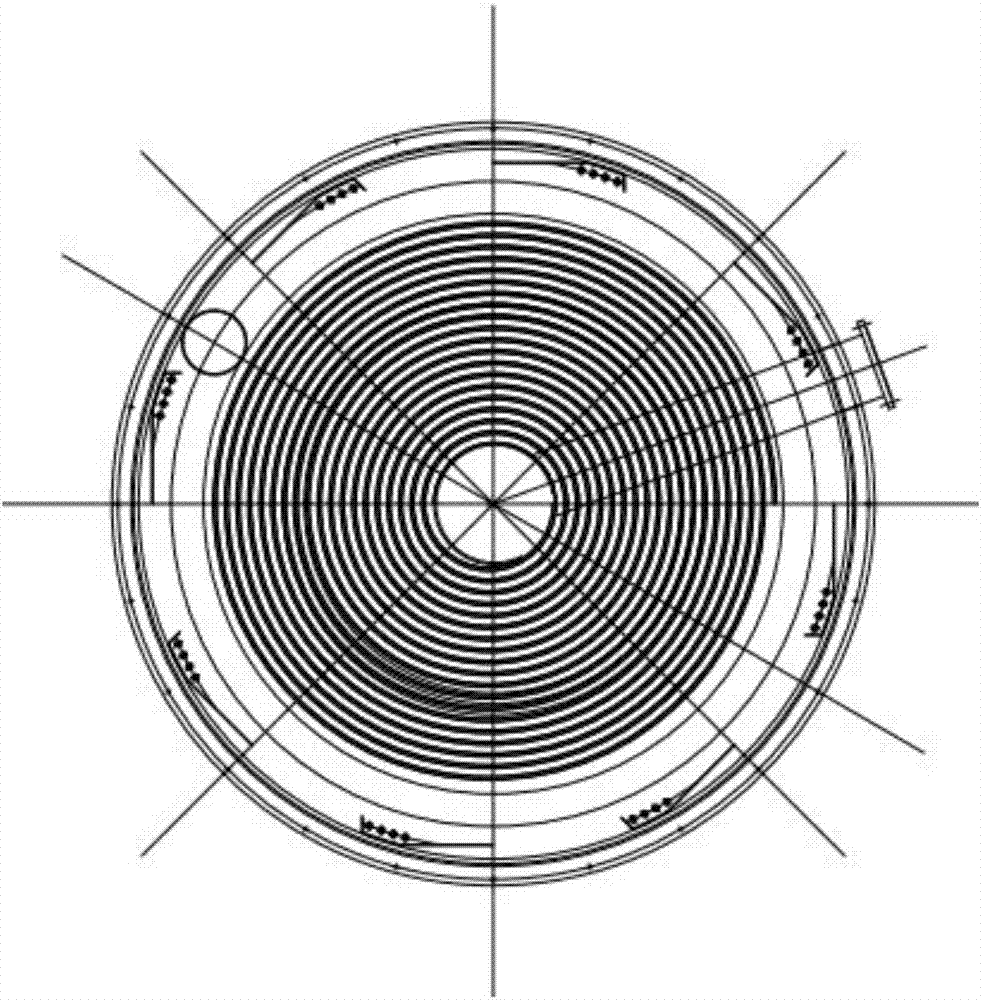
本发明涉及固定床反应器,具体涉及一种气固催化反应的均热式螺旋板固定床反应器。
背景技术:
:固定床催化反应器在化学工业以及石油工业中有着广泛的应用。固定床反应器的优点是:①返混小,流体同催化剂可进行有效接触,当反应伴有串联副反应时可得较高选择性;②催化剂机械损耗小;③结构简单。其缺点是:①壳程传热效果差,特别是对于强放热反应,容易出现飞温(反应温度失去控制,急剧上升,超过允许范围);②操作过程中催化剂不能更换,催化剂需要频繁再生的反应一般不宜使用,常代之以流化床反应器或移动床反应器。按换热方式固定床反应器可分为绝热式、换热式和自热式三种。绝热固定床反应器和自热式固定床反应器在实际工业生产中应用较少,应用较为广泛和成熟的是换热式固定床反应器中的列管式固定床反应器。它多用于强放热反应,收率对温度敏感而又要求高转化率和高选择性的反应过程。其结构与管壳式换热器相似,由管束、壳体、两端封头等组成。应用于气固催化反应时,管程装填催化剂颗粒,并由底部支撑件进行固定,壳程有换热介质流动,以与管程进行热量交换,维持管程反应温度的稳定。列管式固定床反应器的管程结构灵活,可以是单管、多管并联,也可以是U型管等,与其它形式的固定床反应器相比较,具有:①径向传热的距离小,可使反应热及时传到管壁,以准确控制催化剂床层温度;②借鉴成熟的列管式换热器制造技术,工程上易于实现等优点。但存在:①壳程传热系数小,所需的传热面积大;②催化剂床层的空间利用率低,导致反应器体积庞大,设备制作成本高,装置不易大型化等缺点。螺旋板换热器是由两张平行的金属板卷制成两个封闭的螺旋形通道,冷热流体之间通过螺旋板壁进行换热的换热器。具有体积小、设备紧凑、传热效率高、金属耗量少的优点,在化工、石油、医药、电力等行业具有广泛的应用。技术实现要素:为了解决现有列管式固定床反应器壳程传热效果差、催化剂床层的空间利用率低、装置不易大型化的技术问题,借鉴螺旋板换热器的结构和性能特点,本发明提供一种气固相接触催化反应的均热式螺旋板固定床反应器。本发明的技术方案如下:一种气固相接触催化反应的均热式螺旋板固定床反应器,包括气相和换热介质的进出口,反应器内设置一个或多个螺旋板式固定床反应段。螺旋板式固定床反应段的结构与螺旋板换热器结构相似,由两张平行的金属板卷制成两个螺旋形的通道,其中一个通道上下两端封闭,作为换热介质通道,换热介质经螺旋通道流动并通过板壁进行换热,到达反应器中心的中心管后,再由与中心管相连接的换热介质出口流出;另一个通道上下两端不密封,装填催化剂后形成固定床层,床层最上端与气体进口相连通,最下端与气体出口相连通,气体由进口进入反应器,轴向通过催化剂固定床层反应后,由气体出口排出。螺旋板固定床反应器可灵活设置一个或多个螺旋板式反应段,其具体数量可由反应所需的换热面积决定。其中多段螺旋板式反应段的气体通道在轴向上串联,气体依次通过每一反应段的催化剂固定床层,反应后由气体出口排出;对于多段螺旋板式反应段的换热介质通道可通过设置换热介质分布装置或多个换热介质进口,以实现换热介质多段并联进入每一螺旋板式反应段,由换热介质通道螺旋进入反应器中心的中心管后从换热介质出口流出,每一螺旋板式反应段换热介质的进出口温度相同,有利于反应床层温度的均一和控制。螺旋板式反应段两侧通道的间距可灵活设计。换热介质一侧的通道间距可根据换热介质的流量设置,通过提升换热介质的流动速度,提高传热系数,强化传热效果;催化剂固定床层一侧的通道间距在确保换热效果前提下,尽量增大,以提升反应器容积的利用率。螺旋板固定床反应器的气体进口一般设置在反应器顶部,出口一般设置在反应器底部,有利于催化剂颗粒的固定,但在某些特定情况下,气体进口也可设置在反应器底部,出口设置在反应器顶部。当螺旋板固定床反应器只需一个换热介质入口时,可将其设置在反应器顶部法兰一侧,入口管插入设备内部与换热介质分布装置相连;若需多个换热介质入口时,可在每一段螺旋板式反应段设置一换热介质入口,多个入口并联设置在反应器外侧,实现分段控温;出口设置在反应器上部一侧,出口管插入反应器内与中心管相连接。换热介质分布装置为设置在出口管下方的环形管式分布器,环形管式分布器通过分布管连通至各段螺旋板式反应段,实现各反应段进口换热介质温度和流量的一致;反应段换热介质出口与中心管连通,换热介质换热后,在中心管汇集,再由换热介质出口流出。螺旋板固定床反应器底部和顶部均由惰性磁球支撑和固封催化剂床层。螺旋板固定床反应器侧壁环隙亦填充惰性磁球,以避免局部飞温。螺旋板固定床反应器的制作采用单段制作、反应段和分布器及分布管器外组装的模式进行;当两段以上并联时,在反应段的中心管上下端预留坡口,外部组装完毕后,内部中心管的焊接方式有两种:当中心管直径较小时,可采用自动焊杆深入中心管内进行焊接;若中心管直径满足进人条件,焊接人员可由中心管进入各反应段,进行内部中心管的焊接,将多段反应段组成一个整体。再与顶部换热介质分布器连接后,整体吊装放入反应器内组装,完成反应器的加工制作。本发明顶部换热介质分布器与各螺旋板反应器换段介质入口之间可采用焊接、螺纹连接或管箍连接的方式进行连接。本发明的优点:1)显著增大壳程换热系数,使总传热系数增大,强化了传热效果,减小了传热温差;2)可灵活控制传热距离与传热面积,有利于反应床层温度的均一与控制;3)容积利用率大(最大可达70%以上,列管式反应器最大为40%左右),单套设备产能高,占地面积与投资显著降低;4)换热介质通道具有自清洗作用,不易产生污垢与堵塞。附图说明图1是本发明的结构示意图,图2是图1的俯视图。其中:1换热介质进口,2换热介质出口,3气体进口,4气体出口,5环形管式分布器,6液体分布管,7中心管,8-N为螺旋板反应段。图3是本发明实施例1的结构示意图,图4是图3的俯视图。其中:1换热介质进口,2换热介质出口,3气体进口,4气体出口,5环形管式分布器,6液体分布管,7中心管,8-15为螺旋板反应段。图5是本发明实施例2的结构示意图,图6是图5的俯视图。其中:1换热介质出口,2换热介质进口,3气体进口,4气体出口,5-1换热介质进口,6-1中心管,7-17为螺旋板反应段。具体实施方式实施例115万吨/年草酸二甲酯(DMO)加氢反应器本发明的反应器用作15万吨/年DMO加氢反应器时,经核算需8段螺旋板式反应段,其结构见图3和图4。换热介质入口1设置在反应器顶部一侧,出口2设置在反应器上部一侧。气体由顶部进气口3进入反应器,穿过催化剂固定床层(8~15)发生反应后与产物一起由底部气体出口4离开反应器;换热介质经反应器顶部环形管式分布器5,由若干分布管6按比例分配至各段螺旋板式反应段(08~15)外侧进口,由换热介质通道螺旋换热,进入反应段中心的中心管7汇总后,从换热介质出口2流出。15万吨/年DMO加氢反应器采用本发明反应器与列管式固定床反应器的性能指标对比见表1.表1150kt/aDMO反应器对比项目本发明固定床反应器列管式固定床反应器设备直径(mm)36004000催化剂床层高度(mm)80008000催化剂装填量(m3)4436从上表可以看出,两种反应器催化剂床层的容积利用率分别为:54.06%和35.83%,本发明催化剂装填量提升50%以上,可大幅提升装置的产能,且设备直径小,占地面积和投资少;同时通过控制换热介质通道宽度,提高换热介质流动速度,增大了总传热系数,减小了传热温差,便于反应床层温度的控制。实施例23.5万吨/年醋酸乙烯合成反应器本发明的反应器用作3.5万吨/年醋酸乙烯合成反应器时,经核算需10段螺旋板式反应段,其结构见图5和图6。为进一步增强换热效果,每一段螺旋板式反应段设置一股换热介质,实现分段控温,具体为:换热介质入口2、5-1(介质温度可以相同,也可以不同)设置在螺旋板式反应段下部,与反应段内部换热介质通道的外侧相连,由换热介质通道螺旋换热,进入反应段中心的中心管6-1汇总后,从换热介质出口1流出。气体由顶部进气口3进入反应器,穿过催化剂固定床层(7~17)发生反应后与产物一起由底部气体出口4离开反应器.3.5万吨/年醋酸乙烯合成反应器采用本发明反应器与列管式固定床反应器的性能指标对比见表2。表23.5万吨/年醋酸乙烯合成反应器对比项目本发明固定床反应器列管式固定床反应器设备直径(mm)38004200催化剂床层高度(mm)1000010000催化剂装填量(m3)61.549.6从上表可以看出,两种反应器催化剂床层的容积利用率分别为:54.25%和35.81%,本发明催化剂装填量提升50%以上,可大幅提升装置的产能,且设备直径小,占地面积和投资少;同时通过控制换热介质通道宽度,提高换热介质流动速度,增大了总传热系数,减小了传热温差,便于反应床层温度的控制。当前第1页1 2 3