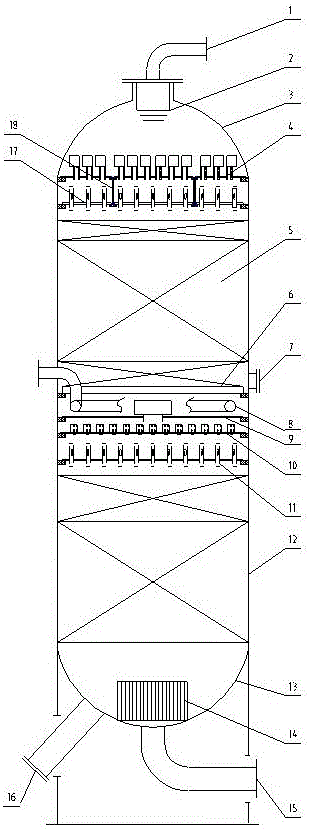
本发明涉及一种加氢反应器,属于化工设备领域。本发明的加氢反应器适用于所有加氢反应过程,特别是反应器规模较大的加氢精制或加氢裂化过程。
背景技术:
:近年来,随着经济的快速发展和环保意识的增强,对石化产品的质量和环保要求越来越高。作为生产清洁燃料的一种技术手段,加氢技术在炼油工业中发挥着越来越重要的作用。在加氢装置中,同加氢催化剂技术和加氢工艺技术一样,加氢反应器技术是反应器系统的重要组成部分,三者构成反应器性能三因素。在加氢装置中,作为关键设备的加氢反应器,按一定比例混氢后的原料油借助加氢催化剂的作用,完成了精制和裂化等反应。加氢反应器内的加氢反应能否稳定操作,加氢催化剂能否充分地发挥其作用,产品质量是否能够达到优质,很大程度上取决于气液在催化剂床层中分布的均匀性。而气液在催化剂床层中的分布是否均匀,与加氢反应器内构件的设计有着密切的关系。换言之,内构件性能的好坏直接影响到催化剂寿命、产品质量和装置的运转周期,即在加氢过程中采用一套性能优良的内构件技术所得到的效果决不亚于换用一种活性更高的催化剂。因此国内外对加氢反应器及其内构件的研究和工程开发一直非常重视,不断更新其反应器内构件,以求取得更好的效果。工业装置生产实践表明,制约加氢工艺装置平稳运行的因素主要有两个,一个是由于物料分布不均匀导致的反应器径向温差较大,一个是反应器催化剂床层压力降升高过快。加氢反应器以反应器顶部中心位置进料,尽管设置了入口扩散器,物料输送的残余动能会产生强大的冲击力;中心位置进料的另一个流态特点是,物料在反应器封头空间的形成的流线为倾斜线,物料的动能及呈倾斜线的流态,将顶部分配器塔盘上的液层向反应器四周冲送,形成物料在顶部分配盘上的“推浪”现象,即,反应器分配盘自中心位置至边缘位置的液层高度呈递增式分布:中心位区域物料液层较小,甚至没有液层,而反应器边壁处物料液层高度最大,给依赖塔盘水平度的分配器带来不利的入口条件,即使性能最好的分配器,在不同高度的液层条件下,也无法实现均匀分配物料。随著加氢反应器规模越来越大,物料进入反应器后残余动能和势能转化形成的冲击力所产生的“推浪”现象越来越严重,导致物料分布存在严重的偏差。加氢过程为放热反应,物料分布不均匀会导致催化剂润湿效果好的部位反应程度剧烈,生成热量较多;即影响反应器的径向温差。当径向温差较大时,催化剂局部温度越高,反应速率越快,形成过热点,使这部分催化剂性能过早失活,损害催化剂的性能,甚至会导致催化剂部分区域的结焦、板结,物料无法正常流过,由于固定床加氢反应器为滴流床流态,导致板结区域下方的催化剂不能发挥作用,从而大大降低催化剂的使用寿命与装置的开工周期。局部板结还导致催化剂床层压力降的升高,为了继续运行不得不提高反应器的操作压力,造成能耗的升高。喷射盘设置在冷氢盘与再分配盘(气液分配盘)之间。在冷氢箱中打入急冷氢,为了中和加氢反应放出的反应热,控制反应物温度不超过规定值,冷氢管喷出的氢气流与上床层来的反应物初步混合后进入冷氢箱,在此进行均匀混合。均匀混合的流体经喷射盘后再喷射到下层的再分配盘(气液分配盘)上,再分配盘与顶分配盘结构一样,起到对下床层截面均匀分配的作用。而由于位置高度限制,经过冷氢盘混合的流体从冷氢盘流出时呈近似水平流线流态,造成液相出现严重的推浪现象,即反应器径向液体分配不均匀,分配盘上中心位置甚至没有液相。而喷射盘一般采用均匀开孔的喷液塔盘即平塔筛孔盘结构,冷氢盘混合后的流体经过筛孔时,仅能实现从水平流态转化为垂直流态,无法实现均流,即无法改变塔盘上的推浪现象,即无法给给再分配盘时提供均匀的入口条件,给依赖塔盘水平度的分配器带来不利的入口条件,即使性能最好的分配器,在不同深度的液层条件下,也无法实现均匀分配物料,严重影响再分配器的效果,径向温差扩大不可避免。针对传统的喷射盘即平塔筛孔盘结构存在的问题,必须开发出能够为再分配盘提供均匀的液相入口条件的喷射盘结构,实现物料的初分配,用于消除冷氢盘呈倾斜流态的流体对再分配盘上液层的推浪现象,实现流体的均匀分配。随着加氢反应器规模的日益扩大,产品精度要求日益提高,物料在催化剂床层上的均匀分配十分重要。由于加氢过程是放热反应,原料油在催化剂床层径向截面上分布不均匀,会导致反应程度不同而产生径向温差,甚至会出现局部过热,损害催化剂的性能,从而大大降低催化剂的使用周期。因此选用合理设计的加氢反应器十分必要。技术实现要素:针对现有技术中的不足,本发明提供了一种提高液相均匀度的加氢反应器。本发明的一种提高液相均匀度的加氢反应器,包括物料入口管、入口扩散器、反应器上封头、折边式减冲均流盘、催化剂床层、催化剂支撑格栅、反应器筒体、反应器下封头、出口收集器、物料出口管及卸剂管构成;其中所述的折边式减冲均流盘设置在反应器上封头闲置的空间内或反应器筒体的上端;所述的折边式减冲均流盘包括塔盘和竖直设置于塔盘上的烟囱式分配器,所述的烟囱式分配器包括降液管和设置于降液管上部的翼板。在某些实施方式中,本发明的加氢反应器还包括床层卸剂管、冷氢管、冷氢盘、喷射盘和床层间分配盘。即本发明的加氢反应器包括两个以上的加氢催化剂床层。在进一步优选的实施方式中,本发明的加氢反应器还包括顶部分配盘,所述顶部分配盘位于折边式减冲均流盘的下方,而位于最上部催化剂床层的上方。本发明的加氢反应器中,折边式减冲均流盘为新增设的反应器内沟件。其中,所述的降液管为两端开口(筒状)结构,所述的翼板具有一定夹角、边长及高度。所述的翼板与降液管的轴线平行,或者所述翼板的中心线与反应器轴线成一定夹角。进一步的,折边式减冲均流盘中翼板的夹角远离塔盘的中心或圆心,或翼板夹角面对反应器最近的筒体器壁。进一步的,所述翼板夹角的中心线与反应器筒体射线重合。进一步的,所述翼板朝向距离最近的反应器器壁倾斜,且翼板的夹角的中心线与反应器轴线之间的角度为15°~80。进一步的,所述的翼板具有一定夹角、边长及高度。所述的翼板和降液管的数量相同,且翼板与降液管呈上下布置。所述翼板的底沿(下部)与降液管的上沿(上部)重叠或不重叠连接;重叠连接时,重叠部分高度为降液管高度的比例为5%~30%,优选为10%~25%。进一步的,所述的若干烟囱式分配器应当竖直设置于塔盘上。烟囱式分配器中降液管的下端开口直接开于塔盘上或贯穿塔盘开口。进一步的,所述的塔盘还包括其下方用于支撑的支撑梁以及塔盘连接件。进一步的,所述降液管的管壁上设置有若干溢流孔,以便于液体穿过溢流孔进入降液管并沿降液管往下流动。该溢流孔的中心线与塔盘板表面之间应保持有一定距离。溢流孔的设置数量一般为1~6个,优选1~2个。溢流孔的总截面积为降液管(水平)截面积的10%~100%,优选为30%~50%。当降液管上开设的溢流孔仅设置1个时,其方位设置在降液管与翼板连接点的对面;当设置溢流孔的数量为2个时,其方位设置在降液管与翼板连接点的两侧。所设置的溢流孔的形状可以为圆形、长条形、三角形及多边形,优选为圆形。所述的烟囱式分配器可以采用任何适宜的材料制成,如陶瓷、金属材质等,优选采用钢材质。所述的翼板和降液管可以为一体化制作而成,如可以由降液管及翼板一体化加工制成;或者,在具有一定高度的降液管的上部一定高度处做垂直(竖直)和水平切割,保留壁厚的不完全切割,然后将其展开一定角度制成翼板,又或者在降液管的上沿固定连接一具有一定夹角的翼板即可。所述的固定连接可以采用焊接、螺栓连接、螺丝连接、卡扣链接等各种适宜的方式。本发明中,所述折边式减冲均流盘的塔盘通常分割为若干块,并可拼接为圆形板。在塔盘最外沿的边沿设置折边,折边向上翻折。所述折边的上沿一般应当高于降液管管壁所设置溢流孔的下沿。向上设置的折边可以维持塔盘上的一定的液面高度,从而能够在一定程度上消除现有技术中塔盘的水平存在不足给液相分配带来的影响。本发明中,折边式减冲均流盘上的若干烟囱式分配器通常按照一定规则布置,如可以在塔盘上呈三角形、四边形、菱形布置。本发明中,所述的降液管除了供液体通过外,同时也是进料中气体进料的流通通道。进一步的,本发明的加氢反应器包括两个以上的催化剂床层,因此所述反应器还包括床层卸剂管、冷氢管、冷氢盘、喷射盘和床层间分配盘。所述的喷射盘优选采用折边式喷射盘,折边式喷射盘的结构同前面所述的折边式减冲均流盘。所述折边式喷射盘设置在加氢反应器的冷氢盘与床层间分配盘之间。所述的折边式喷射盘,包括喷射塔盘和竖直设置于喷射塔盘上的烟囱式分配器;所述的烟囱式分配器包括降液管和设置于降液管上部的翼板。进一步的,折边式喷射盘的降液管为两端敞口的筒状结构。所述翼板的上沿与降液管上沿平齐或略高于降液管上沿,所述的翼板具有一定夹角、边长及高度,翼板的下沿贴附在塔盘板上表面,或与塔盘板上表面存在一定高度的缝隙。进一步的,所述折边式喷射盘的翼板夹角远离塔盘的中心或圆心。更进一步的,所述翼板夹角的中心线与反应器筒体射线重合,翼板夹角面对反应器最近的筒体器壁。本发明中,所述的翼板与降液管的轴线平行。所述翼板即为具有一定夹角,边长及高度的折边板。翼板和降液管的数量相同,且为一一对应关系。所述翼板的中下部与降液管的中上部可以部分重叠设置;重叠设置时,重叠部分高度占降液管总高度的比例为50%~90%,优选为60%~80%。所述的折边式喷射盘中,若干烟囱式分配器竖直设置于喷射塔盘上。烟囱式分配器通常通过降液管下端插置在喷射塔盘上,并可通过焊接、螺纹连接、卡扣连接等方式进行固定连接。降液管的下端开口直接开口于喷射塔盘上或贯穿喷射塔盘开口。所述的喷射塔盘还包括其下方用于支撑的支撑梁以及塔盘连接件。进一步的,折边式喷射盘中所述降液管的管壁上设置有若干溢流孔,以便于液体穿过溢流孔进入降液管并沿降液管往下流动。溢流孔的中心线与塔盘板表面之间应保持有一定距离。溢流孔的数量一般为1~6个,优选1~2个。溢流孔的总截面积为降液管(水平)截面积的10%~100%,优选为30%~50%。当降液管上开设的溢流孔仅设置1个时,其方位设置在降液管与翼板连接点的对面;当设置溢流孔的数量为2个时,其方位设置在翼板对称轴线的两侧。所设置的溢流孔的形状可以为圆形、长条形、三角形及多边形,优选为圆形。所述的折边式喷射盘中,烟囱式分配器可采用任何适宜的材料制成,如陶瓷、金属材质等,优选采用钢材质。所述的翼板和降液管可以为一体化成型制作而成;或者,翼板和降液管经组装而成,如可在降液管中上部固定连接一具有一定夹角的翼板即可。所述的固定连接可以采用焊接、螺栓连接、螺丝连接、卡扣连接等各种适宜的方式。具体应用时,所述的降液管可以采用钢管制成,所述翼板优选采用钢板折制而成。本发明中,所述的喷射塔盘通常分割为若干块,并可拼接为圆形板。在喷射塔盘最外沿的边沿设置向上翻折的折边。所述折边的上沿应当高于降液管管壁上所设置溢流孔的上沿。折边的设置可以维持喷射塔盘上的一定的液面高度,从而能够在一定程度上消除现有技术中喷射塔盘的水平存在不足给液相分配带来的影响。所述的折边式喷射盘中,若干烟囱式分配器通常按照一定规则布置,如可以在喷射塔盘上呈三角形、四边形、菱形布置。与现有技术相比,本发明加氢反应器具有如下优点:1、本发明加氢反应器所述的折边式均流盘,经过特殊的结构设计,减小分布器安装尺寸,方便安装于闲置的反应器上封头处,或设置在反应器筒体上端、顶部分配盘的上面,达到节省反应器空间的目的,提高了加氢反应器的空间利用率,便于装填更多的催化剂,或减小反应器规模。2、本发明的加氢反应器,所述的折边式减冲均流盘和折边式喷射盘均设置有翼板,可以阻挡因中心进入导致呈斜线流态喷射而来的流体,将其冲击力消减;失去动能的流体被阻挡后在重力作用下,由原来的倾斜线流态转化为了垂直流态,并实现自然坠落,在塔盘上形成深度一致的液层,消除了倾斜线冲击力给塔盘上液层形成的“推浪”现象,并给烟囱式分配器创造了均匀的入口条件,通过烟囱式分配器将物料分布到催化剂床层或顶部分配盘上,实现初分配功能,给催化剂床层或分配器提供友好、平稳液层、均匀的入口条件。即本发明折边式减冲均流盘改善了第一床层分配盘的入口工况,提高了顶部分配盘的分布效果,优化顶部床层的物料分布,提高第一床层催化剂的利用率。本发明折边式喷射盘改善了床层中间的物料分布情况,提高了床层间分配盘的分布效果。3、本发明的加氢反应器,所述的折边式减冲均流盘和折边式喷射盘,通过设置的翼板及烟囱式分配器实现液相分布,相比较通用的抽吸原理的泡帽分配器,液相分配的分散动力由气相抽吸改为利用势能,形成喷溅,从而减小压降。4、本发明的加氢反应器,所述的折边式减冲均流盘和折边式喷射盘,设置烟囱分配器管壁上溢流孔位置与形状,形成合理的塔盘存液深度,降低塔盘水平度偏差与液位波动带来的宏观分配不均匀。5、本发明的加氢反应器,所述的折边式减冲均流盘和折边式喷射盘,采用独特的设计原理及流体力学特点,实现物料的均匀分配,使催化剂床层径向温差降低,催化剂床层径向温差≤3℃,由于径向温差反映了流体的分布效果,这充分说明了本发明折边式减冲均流盘对反应进料物流的分配和气液混合效果较好,对加氢催化反应过程和催化剂结焦控制具有一定的辅助作用。6、与现有技术相比,本发明的加氢反应器,其折边式均流盘和折边式喷射盘为新增设的加氢反应器内构件,具有结构简单,安装方便,操作弹性大,可以提高加氢反应器空间利用率、改善反应器内物料分布情况,有效消除反应器径向温差,消除催化剂床层因物料分布不均匀引起的过热点,为加氢反应器中催化剂的有效使用提供优良的入口条件,减少催化剂撇头或换剂次数,延长装置的开工周期,提高加氢工艺效果,具有良好的经济效益。附图说明图1是本发明一种提高液相均匀度的加氢反应器的结构示意图。图2是本发明中折边式减冲均流盘的示意图。图3是本发明折边式减冲均流盘中烟囱式分配器4-1的结构示意图。图4是本发明折边式减冲均流盘中烟囱式分配器4-1的结构俯视图。图5是本发明折边式减冲均流盘工作时的液体流向示意图。图6是本发明折边式喷射盘的分配器示意图。图7是本发明折边式喷射盘中烟囱式分配器10-1的分配器示意图。图8是本发明折边式喷射盘中烟囱式分配器10-1的分配器结构俯视图。图9是本发明折边式喷射盘工作时液体流向示意图。图10是本发明实施例和比较例中同一床层截面上不同测温点的方位示意图。具体实施方式下面结合附图和实施例对本发明的实施方式作进一步详细描述。以下实施例用于说明本发明,但不能用来限制本发明的范围。在本发明的描述中,需要说明的是,除非另有说明,“若干”的含义是一个或者一个以上,“多个”的含义是两个或两个以上;术语“上”、“下”、“内”、“外”、“顶部”、“底部”等指示的方位或位置关系为基于附图所示的方位或位置关系,仅是为了便于描述本发明和简化描述,而不是指示或暗示所指的装置或元件必须具有特定的方位、以特定的方位构造和操作,因此不能理解为对本发明的限制。在本发明的描述中,还需要说明的是,除非另有明确的规定和限定,术语“安装”、“相连”、“连接”应做广义理解,例如,可以是固定连接,也可以是可拆卸连接,或一体地连接;可以是直接相连,也可以通过中间媒介间接相连。对于本领域的普通技术人员而言,可视具体情况理解上述术语在本发明中的具体含义。如图1至图4所示,本发明公开了一种加氢反应器,包括物料入口管1、入口扩散器2、反应器上封头3、折边式减冲均流盘4、催化剂床层5、催化剂支撑格栅6反应器筒体12、反应器下封头13、出口收集器14、物料出口管15和卸剂管16。在某些实施方式中,加氢反应器还包括床层卸剂管7、冷氢管8、冷氢盘9、折边式喷射盘10、床层间分配盘11。在进一步优选的实施方式中,加氢反应器还包括顶部分配盘17,顶部分配盘17位于折边式减冲均流盘4下方,最上层催化剂床层的上方。所述折边式减冲均流盘包括塔盘4-2和竖直设置于塔盘上的若干烟囱式分配器4-1。烟囱式分配器4-1包括降液管4-1-2和和设置于降液管4-1-2顶部的翼板4-1-1。降液管4-1-2为两端开口结构。翼板4-1-1与降液管4-1-2呈上下布置。翼板4-1-1具有一定夹角、边长及高度,一般由钢板折制而成。翼板4-1-1与降液管4-1-2的轴线平行。其中,翼板4-1-1与降液管4-1-2数量相同且一一对应。翼板4-1-1的夹角一般为15°~180°,优选为90°~120°;翼板4-1-1的边长一般为20mm~200mm,优选为60mm~120mm;翼板4-1-1的高度一般为30mm~200mm,优选为60mm~120mm。翼板4-1-1的底沿与降液管4-1-2上沿连接,也可与降液管4-1-2部分重叠布置。当翼板4-1-1底沿与降液管4-1-2上沿重叠布置时,重叠部分高度可为降液管4-1-2高度的10%~100%,优选为5%~20%。翼板4-1-1夹角中心线与反应器筒体12射线重合,其夹角面对反应器最近的筒体器壁。本发明加氢反应器中,降液管4-1-2一般由金属管制成。降液管4-1-2的高度一般20~300mm,优选为50~120mm。降液管4-1-2上在水平方向设置1~6个溢流孔4-1-3,优选1~2个;其溢流孔的总截面积为降液管截面积的10%~100%,优选为30%~50%。当降液管上开设的溢流孔设置1个时,其方位设置在降液管4-1-2与翼板4-1-1连接点的对面;当设置溢流孔4-1-3的数量为2个时,其方位设置在降液管4-1-2与翼板4-1-1连接点的两侧。溢流孔的形状可以为圆形、长条形、三角形及多边形,优选为圆形。溢流孔中心线距塔盘上表面5~100mm,优选为30~50mm。本发明加氢反应器中,一层折边式减冲均流盘包括若干数量的烟囱式分配器4-1。若干烟囱式分配器4-1在塔盘上呈三角形、四边形、菱形布置。烟囱式分配器4-1通常通过降液管4-1-2下端插置在塔盘上,并可以通过焊接、螺纹连接、卡扣连接等方式进行固定连接。本发明加氢反应器中,塔盘4-2通常分割为若干块,并可拼接为圆形板。塔盘4-2最外沿的边沿设置向上翻折的折边,折边高度一般为5~80mm,优选为30~50mm。如图1、图6、图7及图8所示,本发明的一种加氢反应器,包括物料入口管1、入口扩散器2、反应器上封头3、折边式减冲均流盘4、顶部分配盘17、催化剂床层5、催化剂支撑格栅6、床层卸剂管7、冷氢管8、冷氢盘9、折边式喷射盘10、床层间分配盘11、反应器筒体12、反应器下封头13、出口收集器14、物料出口管15、和卸剂管16。其中,折边式喷射盘10设置在加氢反应器冷氢盘9与床层间分配盘11之间。折边式喷射盘10包括塔盘板10-2和竖直设置于塔盘板上的烟囱式分配器10-1;所述的烟囱式分配器10-1包括降液管10-1-2和设置于降液管上部的翼板10-1-1。其中,所述降液管10-1-2为两端敞口(筒状)结构,翼板10-1-1的上沿与降液管10-1-2上沿平齐或略高于降液管10-1-2上沿。所述的翼板10-1-1具有一定夹角、边长及高度,翼板10-1-1的下沿贴附在塔盘板10-2上表面,或与塔盘板10-2上表面存在一定高度的缝隙。翼板10-1-1的夹角远离塔盘10-2的中心或圆心。更进一步的,所述翼板10-1-1夹角的中心线与反应器筒体12射线重合,翼板10-1-1夹角面对反应器最近的筒体器壁。所述的翼板10-1-1与降液管10-1-2的轴线平行。所述的翼板10-1-1具有一定夹角、边长及高度。翼板10-1-1即具有一定夹角,边长及高度的折边板。所述的翼板10-1-1和降液管10-1-2的数量相同,且为一一对应关系。所述翼板10-1-1的中下部与降液管10-1-2的中上部可以部分重叠连接;重叠连接时,重叠高度占降液管10-1-2总高度的比例为50%~90%,优选为60%~80%。所述的若干烟囱式分配器10-1应当竖直设置于塔盘板10-2上。烟囱式分配器10-1通常通过降液管10-1-2下端插置在塔盘板10-2上,并可以通过焊接、螺纹连接、卡扣连接等方式进行固定连接。所述降液管10-1-2的下端开口直接开口于塔盘板10-2上或贯穿塔盘板10-2开口。所述的塔盘还包括其下方用于支撑的支撑梁10-4以及塔盘连接件10-3。所述降液管的管壁上设置有若干溢流孔10-1-3,以便于液体穿过溢流孔10-1-3进入降液管10-1-2并沿降液管10-1-2往下流动。该溢流孔10-1-3的中心线与塔盘板10-2表面之间应保持有一定距离。溢流孔10-1-3的设置数量一般为1~6个,优选1~2个。溢流孔10-1-3的总截面积为降液管10-1-2(水平)截面积的10%~100%,优选为30%~50%。当降液管10-1-2上开设的溢流孔10-1-3仅设置1个时,其方位设置在降液管10-1-2与翼板10-1-1连接点的对面;当设置溢流孔10-1-3的数量为2个时,其方位设置在翼板10-1-1对称轴线的两侧。所设置的溢流孔10-1-3的形状可以为圆形、长条形、三角形及多边形,优选为圆形。所述的烟囱式分配器10-1可以采用任何适宜的材料制成,如陶瓷、金属材质等,优选采用钢材质。所述的翼板10-1-1和降液管10-1-2可以为一体化成型制作而成;或者,翼板10-1-1和降液管10-1-2经组装而成,如可在降液管10-1-2中上部固定连接一具有一定夹角的翼板10-1-1即可。所述的固定连接可以采用焊接、螺栓连接、螺丝连接、卡扣连接等各种适宜的方式。具体应用时,所述的降液管10-1-2可以采用钢管制成,所述翼板10-1-1优选采用钢板折制而成。所述的折边式喷射盘的塔盘10-2通常分割为若干块,并可拼接为圆形板。在塔盘10-2最外沿的边沿设置折边10-5,折边10-5向上翻折。折边10-5的上沿一般应当高于降液管10-1-2上所设置溢流孔10-1-3的上沿。折边10-5的设置可以维持塔盘10-2上的一定的液面高度,从而能够在一定程度上消除现有技术中塔盘的水平存在不足给液相分配带来的影响。所述的折边式喷射盘中,若干烟囱式分配器10-1通常按照一定规则布置,如可以在塔盘板10-2上呈三角形、四边形、菱形布置。结合图5,进一步说明本发明加氢反应器中折边式减冲均流盘的工作过程:所述折边式减冲均流盘工作时,物料由反应器的入口扩散器进入反应器内,因机泵输送,流体具有残余动能,因而物料具有强大的冲击力。由于物料自反应器中心位置进料,虽然现有的反应器均设置入口扩散器,但物料仍然呈斜线流态向四周喷射。当在反应器内设置本发明提供的折边式减冲均流盘后,流体首先撞击到烟囱式分配器4-1的翼板4-1-1,翼板4-1-1可有效阻挡呈斜线流态喷射而来的物料流体,将其冲击力消减掉,通过设置翼板4-1-1将物料的流态进行了改变,流体被阻挡、失去动能后在重力的作用下,由斜线流态变为垂直流态坠落到塔盘4-2上。由于降液管4-1-2设置有溢流孔4-1-3,即物料通道呈水平布置,且溢流孔4-1-3距离塔盘4-2具有一定高度差,因而物料会在塔盘4-2上形成具有一定深度的液层,即使塔盘4-2水平度存在偏差,仍可确保每个烟囱式分配器4-1均有液相存在。由于烟囱式分配器4-1数量多,可以保证反应器内催化剂床层表面任意一个点均有一定数量的烟囱式分配器4-1工作,使得烟囱式分配器4-1均匀度得到保障。流体自降液管4-1-2管壁上开设的溢流孔4-1-3流入反应器内最顶部分配盘上,实现物料的初步分配。由于经过折边式减冲流盘后的物料在分配到顶部分配盘上时已经转化为垂直流态,且动能消失,因此对顶部分配盘塔盘表面上的液层不再有推力,消除了物料对分配盘上液层的“推浪”作用,给顶部分配盘提供了友好、平稳、均匀的入口条件,与顶部分配盘一起实现了物料在催化剂床层上的均匀分布。结合图9,进一步说明本发明加氢反应器中折边式喷射盘的工作过程:工作时,经过冷氢盘9混合后的、呈近似水平流线的倾斜流态的流体,撞击到翼板10-1-1上,因翼板10-1-1具有一定夹角布置,可有效阻挡呈斜线流态喷射而来的流体,将其冲击力削减掉;利用翼板10-1-1阻挡作用,迫使气相夹带液滴向四周分散,实现物料较大扩散角,流体待动能耗尽后在重力作用下自然滴落,形成垂直下降流态,液相势能转化为自由落体的动能,并坠落到喷射盘的塔盘板10-2上,由于降液管10-1-2设置的物料通道呈水平布置且距离塔盘板10-2具有一定高度差,因而物料会在喷射盘的塔盘板10-2上形成一定深度的液层,即使塔盘10-2水平度存在偏差,仍可确保每个降液管10-1-2均有液相存在。由于经过折边式喷射盘后的物料分配到喷射盘10-2上时已经转化为垂直流态,且动能消失,因此对喷射盘塔盘板10-2表面上的液层不再有推力,消除了物料对分配盘上液层的“推浪”现象,给再分配器提供了友好、平稳液层、均匀的入口条件,与再分配盘一起实现了物料在催化剂床层上的均匀分布。本发明的折边式喷射盘,可取代再分配盘,实现减冲、均流及分配一体化,大大简化反应器内部结构、降低投资。以下通过具体实施例对本发明折边式减冲均流盘和折边式喷射盘的效果进行描述。比较例1某加氢反应器,直径4.6m,上封头内闲置,最上层催化剂床层入口处设置有顶分配盘,顶分配盘内使用本领域常规的eri型泡帽式气液分配器,所述反应器的工艺条件为:氢分压2.0mpa、体积空速2.0h-1、氢油体积比为300:1,反应器入口温度280℃,该反应器包括三个催化剂床层。其第一、第二催化剂床层间在冷氢箱与再分配盘之间采用现有的均匀开孔的喷液塔盘,即平塔筛孔盘结构;同样在第二、第三催化剂床层间在冷氢箱与再分配盘之间亦采用平塔筛孔盘结构,塔盘开设直径为3mm的均布圆孔,塔盘开孔率为8%。加氢原料为蜡油(硫含量2.0wt%),催化剂为3936加氢处理催化剂,工艺条件为:氢分压9.0mpa(g)、体积空速为1.5h-1、氢油体积比为700:1,反应器入口温度260℃。改造前,第二床层、第三床层入口径向温度及温差见表1。实施例1同实施例1相比,在加氢反应器的上封头内用本发明的折边式减冲均流盘取代了泡帽式气液分配器,用本发明的折边式喷射盘取代了平塔筛盘孔结构。折边式减冲均流盘的主要参数为:翼板夹角为120°;翼板边长为120mm;翼板高度为60mm。其翼板与烟囱分配器轴线平行。其翼板底沿与烟囱分配器上沿重合,重合点为分配器高度20%。烟囱分配器高度为120mm;在烟囱分配器管壁上,呈水平方向设置2个溢流口。溢流孔的总截面积为烟囱分配器管截面积的30%;烟囱分配器管壁上开设的溢流孔,其形状为圆形;烟囱分配器管壁上设置的溢流孔中心线距塔盘上表面50mm;本发明的折边式减冲均流盘中,烟囱式分配器在塔盘上呈三角形布置。所述的塔盘分割为9块,并可拼接为圆形板,每块切割板上设置3个烟囱式分配器,塔盘最外沿的边沿设置折边,折边的高度为50mm。折边式喷射盘的主要参数:翼板和降液管的数量相同,翼板由钢板折制而成,翼板夹角为90°,翼板边长为60mm。翼板高度等于降液管高度,翼板1-1的夹角中心线与反应器筒体射线重合,其夹角面对反应器器壁距离最近的筒体器壁。降液管的高度为60mm。降液管管壁上设置2个圆形溢流孔,且呈水平方向设置。在降液管管壁上设置的溢流孔,其总截面积为降液管截面积的30%。降液管上所设置溢流孔的中心线距塔盘表面为20mm。本发明的折边式喷射盘中,其塔盘分割为9块小塔盘,并可拼接为圆形板,烟囱式分配器在折边式喷射塔盘上呈三角形布置,每块小塔盘上设置3个烟囱式分配器。最外沿的塔盘边沿设置向上翻折的折边,折边的高度为50mm。改造后,第一催化剂床层入口、第二催化剂床层、第三催化剂床层入口径向温度分布及温差见表1。实施例2同实施例1相比,在加氢反应器的上封头内泡帽式气液分配器的上方设置本发明的折边式减冲均流盘,用本发明的折边式喷射盘取代了平塔筛盘孔结构。折边式减冲均流盘的主要参数为:翼板夹角为120°;翼板边长为120mm;翼板高度为60mm。其翼板与烟囱分配器轴线平行。其翼板底沿与烟囱分配器上沿重合,重合点为分配器高度20%。烟囱分配器高度为120mm;在烟囱分配器管壁上,呈水平方向设置2个溢流口。溢流孔的总截面积为烟囱分配器管截面积的30%;烟囱分配器管壁上开设的溢流孔,其形状为圆形;烟囱分配器管壁上设置的溢流孔中心线距塔盘上表面50mm;本发明的折边式减冲均流盘中,烟囱式分配器在塔盘上呈三角形布置。所述的塔盘分割为9块,并可拼接为圆形板,每块切割板上设置3个烟囱式分配器,塔盘最外沿的边沿设置折边,折边的高度为50mm。折边式喷射盘的主要参数:翼板和降液管的数量相同,翼板由钢板折制而成,翼板夹角为90°,翼板边长为60mm。翼板高度等于降液管高度,翼板1-1的夹角中心线与反应器筒体射线重合,其夹角面对反应器器壁距离最近的筒体器壁。降液管的高度为60mm。降液管管壁上设置2个圆形溢流孔,且呈水平方向设置。在降液管管壁上设置的溢流孔,其总截面积为降液管截面积的30%。降液管上所设置溢流孔的中心线距塔盘表面为20mm。本发明的折边式喷射盘中,其塔盘分割为9块小塔盘,并可拼接为圆形板,烟囱式分配器在折边式喷射塔盘上呈三角形布置,每块小塔盘上设置3个烟囱式分配器。最外沿的塔盘边沿设置向上翻折的折边,折边的高度为50mm。改造后,第一催化剂床层入口、第二催化剂床层、第三催化剂床层入口径向温度分布及温差见表1。表1应用结果比较例1实施例1实施例2第一催化剂床层入口径向温度a266.6265.2265.1径向温差b265.5264.5265.5径向温度c270.3264.9265.9径向温度d276.0265.0265.0径向温差e278.4265.8265.8最大床层径向温差12.91.30.9第二催化剂床层入口径向温度a276.6275.2275.1径向温差b279.5274.5274.5径向温度c280.3274.9274.8径向温度d286.0275.0275.2径向温差e288.4275.8275.6最大床层径向温差,℃11.81.31.1第三催化剂床层入口径向温度a281.3282.9282.9径向温差b283.6283.5283.4径向温度c292.5284.5284.3径向温度d286.7284.3284.5径向温差e289.6283.7283.9最大床层径向温差,℃11.21.61.4当前第1页12