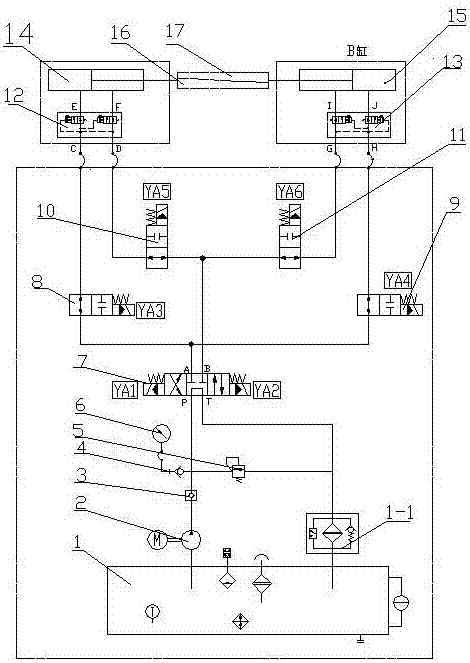
本实用新型涉及矿山破碎设备,特别是一种颚式破碎机的排料口调节装置。
背景技术:
:传统颚式破碎机排料口的调节大多采用人工手动调节,不仅费时费力,而且很不方便,尤其在进行大型颚破排料口调节时尤为明显,即便近年来一些新型的颚破采用液压调节,但也存在诸多问题,比如:两侧液压缸不同步,楔形块位置不对称;液压缸运动速度不稳定,出现卡顿和失速现象;排料口调节过程中调节量不可知,中途需人工测量,再做调整再测量等反复进行才能完成,过程耗时费力。技术实现要素:本实用新型旨在解决的技术问题提供一种颚式破碎机的排料口调节装置,实现排料口大小自动同步调节到设定值,在线调整排料口间隙,提高生产效率。采用如下技术方案:一种颚式破碎机的排料口调节装置,包括第一油缸和第二油缸,第一油缸的缸体与机架外侧的第一耳座铰接,第一油缸的活塞杆与下楔形块的外端铰接,第二油缸的活塞杆与上楔的外端铰接,第二油缸的缸体与机架外侧的第二耳座铰接,所述第一油缸通过第一调整支路与主回路的油口A和油口B连通,第二调整支路与第一调整支路并联,第二油缸通过第二调整支路与主回路的油口A和油口B连通;第一油缸安装有第一行程监测传感器,第二油缸安装有第二行程监测传感器,第一和第二行程监测传感器分别通过线路与控制系统连接;主回路、第一调整支路和第二调整支路的电磁换向阀分别通过线路与控制系统连接,控制系统包括PLC。采用上述技术方案的本实用新型与现有技术相比,有益效果是:安全可靠,操作简单,间隙调整准确,在线调整排料口间隙,提高生产效率。进一步的本实用新型的优化方案是:所述主回路包括油泵,第一单向阀,第一电磁换向阀,第一电磁换向阀是三位四通电磁换向阀,油泵与第一单向阀连通,第一单向阀与第一电磁换向阀的油口P连通,第一电磁换向阀的油口T与油箱连通。所述第一调整支路包括第二电磁换向阀,第四电磁换向阀,第一平衡阀,第二和第四电磁换向阀是两位四通电磁换向阀,第一电磁换向阀的油口A与第二电磁换向阀连通,第二电磁换向阀与第一平衡阀的油口C连通,第一平衡阀的油口E连接第一油缸的无杆腔,第一油缸的有杆腔与第一平衡阀的油口F连通,第一平衡阀的油口D与第四电磁换向阀连通,第四换向阀与第一电磁换向阀的油口B连通。所述第二调整支路包括第三电磁换向阀,第五电磁换向阀,第二平衡阀,第三和第五电磁换向阀是两位四通电磁换向阀,第一电磁换向阀的油口A与第三电磁换向阀连通,第三电磁换向阀与第二平衡阀的油口G连通,第二平衡阀的油口I连接第二油缸的无杆腔,第二油缸的有杆腔与第二平衡阀的油口J连通,第二平衡阀的油口H与第五电磁换向阀连通,第五换向阀与第一电磁换向阀的油口B连通。附图说明图1为本实用新型的结构示意图。图2为本实用新型的液压原理示意图。图中:油箱1;过滤器1-1;油泵2;第一单向阀3;第二单向阀4;溢流阀5;压力表6;第一电磁换向阀7;第二电磁换向阀8;第三电磁换向阀9;第四电磁换向阀10;第五电磁换向阀11;第一平衡阀12;第二平衡阀13;第一油缸14;第二油缸15;下楔形块16;上楔形块17;机架18;第一耳座19;第二耳座20;肘板21;动颚22;定颚23。具体实施方式下面结合附图和实施例进一步详述本实用新型。本实施例包括第一油缸14(图1所示),第一油缸14的缸体与第一耳座19铰接,第一耳座19焊接在在颚式破碎机机架18的左侧,第一油缸14的活塞杆与下楔形块16的外端铰接。第二油缸15的缸体与第二耳座20铰接,第二耳座20焊接在颚式破碎机机架18的右侧,第二油缸15的活塞杆与下楔形块17的外端铰接。下楔形块16下部与肘板21的一端固定连接,肘板21的另一端与动颚22固定连接,动颚22和定颚23相对应。第一油缸14安装有第一行程监测传感器,第一行程监测传感器包括成对配合使用的第一外行程监测传感器和第一内行程监测传感器,第一外行程监测传感器安装在第一油缸的活塞杆上,第一内行程监测传感器安装在第一油缸的缸筒的端部,通过活塞杆上的第一外行程监测传感器和缸筒端部的第一内行程监测传感器实时测算相对距离,来实时通过外监测设备实现腔内压力或负载的突变。第二油缸15安装有第二行程监测传感器,第二行程监测传感器包括成对配合使用的第二外行程监测传感器和第二内行程监测传感器,第二外行程监测传感器安装在第二油缸的活塞杆上,第二内行程监测传感器安装在第二油缸的缸筒的端部。第一油缸14的有杆腔和无杆腔通过第一调整支路与主回路的油口A和油口B连通。主回路(图所示)包括油泵2,油泵2与第一单向阀3连通,第一单向阀3用于防止压力油回流,第一单向阀3与第一电磁换向阀的油口P连通,第一电磁换向阀7是三位四通电磁换向阀,第一电磁换向阀7的油口T与过滤器1-1连通,过滤器1-1与油箱1连通。第一调整支路包括第二电磁换向阀8,第一电磁换向阀7的油口A与第二电磁换向阀8连通,第二电磁换向阀8与第一平衡阀12的油口C连通,第一平衡阀12的油口E连接第一油缸14的无杆腔,第一油缸14的有杆腔与第一平衡阀12的油口F连通,第一平衡阀12的油口D与第四电磁换向阀10连通,第四换向阀10与第一电磁换向阀7的油口B连通。第二电磁换向阀8和第四电磁换向阀10是两位四通电磁换向阀第二油缸15的有杆腔和无杆腔通过第二调整支路与主回路的油口A和油口B连通,第二调整支路与第一调整支路并联。第二调整支路包括第三电磁换向阀9,第一电磁换向阀7的油口A与第三电磁换向阀9连通,第三电磁换向阀9与第二平衡阀13的油口G连通,第二平衡阀13的油口I连接第二油缸15的无杆腔,第二油缸的有杆腔与第二平衡阀的油口J连通,第二平衡阀13的油口H与第五电磁换向阀连通,第五换向阀与第一电磁换向阀13的油口B连通。第三磁换向阀9和第五电磁换向阀11是两位四通电磁换向阀。第一单向阀3、第二单向阀4、溢流阀5、压力表6、第一电磁换向阀7、第二电磁换向阀8、第三电磁换向阀9、第四电磁换向阀10和第五电磁换向阀11安装在液压站上,第一平衡阀12安装在第一油缸14上,第二平衡阀13安装在第二油缸15上,第一平衡阀12和第二平衡阀13与液压站之间通过管路连接。平衡阀在液压缸腔内压力或所受负载突然发生变化时,液压缸可保持稳定运动速度。溢流阀5的进油口与第一单向阀3的出油口连通,溢流阀5的出油口与过滤器的进油口连通。第二单向阀4的进油口与第一单向阀3的出油口连通,第二单向阀4的出油口连接压力表6。第一行程监测传感器和第二行程监测传感器分别通过线路与控制系统连接,第一电磁换向阀7、第二电磁换向阀8、第三电磁换向阀9、第四电磁换向阀10和第五电磁换向阀11分别通过线路与控制系统连通,控制系统由液压站的PLC控制。液压站上所装元件配合PLC内置程序实现排料口大小自动调节到设定值,并保证两侧液压缸同步运动,并在调节过程中实时显示调节结果。本实施例的工作过程是:需要调节排料口大小时,在中控或液压站的控制箱操作界面输入需调节的数值,启动液压站,液压油通过管路进入液压缸腔体内推动缸杆运动。液压缸上的行程监测传感器,将两个液压缸实时运动的数据传输到液压站的PLC中,通过对比,PLC调节液压站上的相关阀门,达到两个液压缸同步运动,且最终调节到设定值。各个电磁换向阀的动作见下表:序号动作MYA1YA2YA3YA4YA5YA61液压站启动、待机+------2排料口调大(第一、第二油缸同时工作)++-----3排料口调大(第一油缸单独工作)++--+-+4排料口调大(第二油缸单独工作)++-+-+-5排料口调小(第一、第二油缸同时工作)+-+----6排料口调小(第一油缸同时工作)+-+-+-+7排料口调小(第二油缸同时工作)+-++-+-8调整完毕、保压-------具体动作过程是:1、排料口调大1)确定调节行程L,执行动作1、2;2)观察第一、第二油缸的标尺读数,当第一、第二油缸的行程相差5毫米时:①若第二油缸的行程大于第一油缸,执行动作3,直至第一、第二油缸的行程相同,停止执行动作3,继续执行动作2;②若第一油缸的行程大于第二油缸,执行动作4,直至直至第一、第二油缸的行程相同,停止执行动作4,继续执行动作2;2、排料口调小1)确定调节行程L,执行动作1、5;2)观察第一、第二油缸的标尺读数,当第一、第二油缸的行程相差5毫米时:①若第二油缸的行程大于第一油缸,执行动作6,直至第一、第二油缸的行程相同,停止执行动作6,继续执行动作5;②若第一油缸的行程大于第二油缸,执行动作7,直至直至第一、第二油缸的行程相同,停止执行动作7,继续执行动作5;3、如工作时,第一、第二油缸行程存在差异,可根据具体差值,执行动作3、4、6、7,单独调节某个油缸,使第一、第二油缸行程相同。本实用新型应用于矿山破碎设备复摆颚式破碎机的颚板间隙自动同步调整,以满足补偿衬板磨损或适时调节排料粒度的要求。本实用新型比传统颚破排料口的手动调节省时省力,实现液压自动调节排料口,调节时两侧调节液压缸保持同步、液压缸运动速度保持稳定、排料口调节液压缸调节量可检测功能。智能化程度高,安全可靠,操作简单,间隙调整准确,可用于在线调整排料口间隙,提高生产效率。以上所述仅为本实用新型较佳可行的实施例而已,并非因此局限本实用新型的权利范围,凡运用本实用新型说明书及附图内容所作的等效结构变化,均包含于本实用新型的权利范围之内。当前第1页1 2 3