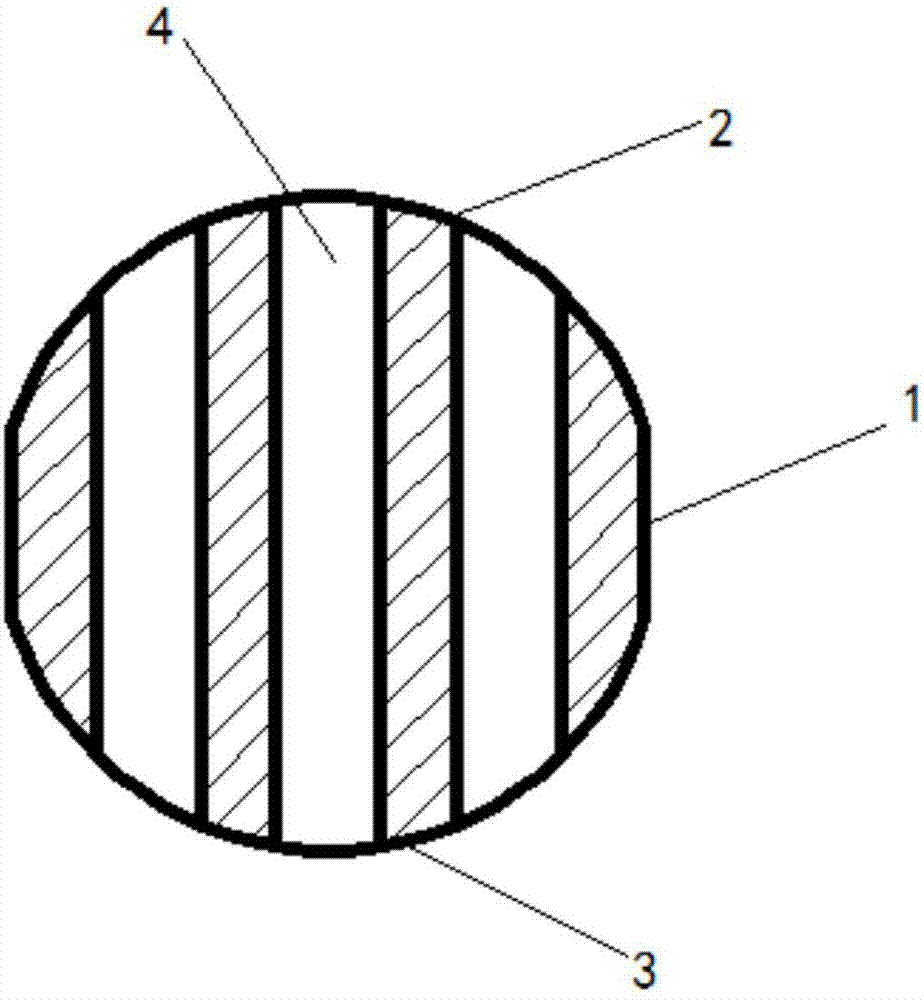
本发明属于直接还原铁催化剂
技术领域:
,具体为一种用于直接还原铁工艺的烃类重整催化剂、制备及应用。
背景技术:
:世界直接还原工艺根据使用还原剂的不同,可分为两大类:使用气体还原剂的气基直接还原法和使用固体还原剂的煤基直接还原法。气体还原剂法,是将矿石装入竖炉、流态床炉或罐式容器中,用还原气体(经过裂化的天然气,主要成分为h2或co)使氧化铁中的氧以h2o和co2形式除去,还原成金属铁。该法由于采用较纯的还原气体,因此产品较纯,可以获得高质量还原铁。目前气体还原剂法代表工艺为midrex竖炉法、hyl反应罐法和流态化法。midrex竖炉法是当前发展最快、应用最广的直接还原炼铁法。midrex法标准流程由还原气制备和还原竖炉两部分组成。还原气制备:将净化后含co与h2约70%的炉顶气加压送入混合室,与当量天然气混合送入换热器预热,后进入1100℃左右有烃类重整催化剂的反应管进行催化裂化反应,转化成co:24%~36%、h2:60%~70%、ch4:3%~6%和870℃的还原气。后从风口区吹入竖炉。还原竖炉:竖炉断面呈圆形,分为预热段、还原段和冷却段。选用块矿和球团矿原料,从炉顶加料管装入,被上升的热还原气干燥、预热、还原。随着温度升高,还原反应加速,炉料在800℃以上的还原段停留4~6小时。新海绵铁进入冷却段完成终还原和渗碳反应,同时被自下而上通入的冷却气冷却至<100℃。还原气通过净化后返回转化炉。midrex竖炉法中煤气转化炉和竖炉是最主要的构成部分,而煤气转化炉的核心是其内放置的烃类重整催化剂。现国外有德国南方、unicat等烃类重整催化剂,而国内现没有自主知识产权的用于该工艺的烃类重整催化剂。在midrex竖炉法中煤气转化炉是重要组成部分,与传统的天然气转化炉的操作条件有着很大差别:1、水碳比低,约为0.3;2、反应压力低,约为0.2mpa;3、反应炉管直径大,传统天然气转化炉管直径在100mm左右,而midrex工艺的煤气转化炉管直径在200mm左右;4、转化气出口温度高,传统天然气转化炉反应温度在800℃,而midrex工艺的煤气转化炉反应温度在1100℃。由于转化炉的操作条件存在较大差异,因此在选用催化剂时也存在较大差别,目前在midrex工艺中大部分使用的催化剂为平面多孔圆柱体结构,此种结构的催化剂强度较低,大约为1500n/颗,且装填后催化剂层的压力降较大,一般在0.05mpa左右。不能很好的满足生产需求。技术实现要素:本发明的目的在于提供一种强度高,活性稳定,抗积碳性能好,催化剂层压力降较低的用于直接还原铁工艺的烃类重整催化剂,具体地,本发明催化剂是一种应用于midrex竖炉法直接还原铁工艺中煤气转化炉的烃类重整催化剂。本发明目的通过以下技术方案来实现:一种用于直接还原铁工艺的烃类重整催化剂,以质量份数计,所述催化剂包括5~30份的活性组分,75~95份的载体,其中,所述活性组分为氧化镍,所述载体为al2o3;所述催化剂的外形结构包括圆柱状本体,所述圆柱状本体的两端面分别设置有向外凸起的弧形面ⅰ和向外凸起的弧形面ⅱ,催化剂上还开设有若干个贯穿于弧形面ⅰ、弧形面ⅱ以及圆柱状本体的竖直通孔。作为本发明所述一种用于直接还原铁工艺的烃类重整催化剂的一个具体实施例,所述活性组分氧化镍为10~20份,所述载体al2o3为80~85份。作为本发明所述一种用于直接还原铁工艺的烃类重整催化剂的一个具体实施例,所述弧形面ⅰ及弧形面ⅱ为互相对称的球形面或椭球形面。作为本发明所述一种用于直接还原铁工艺的烃类重整催化剂的一个具体实施例,所述催化剂包括圆柱状本体,所述圆柱状本体的两端面分别设置有互相对称且向外凸起的半球形面ⅰ和半球形面ⅱ,催化剂上还开设有5个贯穿于半球形面ⅰ、半球形面ⅱ以及圆柱状本体的竖直通孔。作为本发明所述一种用于直接还原铁工艺的烃类重整催化剂的一个具体实施例,所述圆柱状本体的底面直径为25-35mm,高度为7-11mm,所述半球形面ⅰ和半球形面ⅱ的直径为25-35mm,所述竖直通孔的直径为3-7mm。作为本发明所述一种用于直接还原铁工艺的烃类重整催化剂的一个具体实施例,所述催化剂包括圆柱状本体,所述圆柱状本体的两端面分别设置有互相对称且向外凸起的半椭球形面ⅰ和半椭球形面ⅱ,催化剂上还开设有5个贯穿于半椭球形面ⅰ、半椭球形面ⅱ以及圆柱状本体的竖直通孔。作为本发明所述一种用于直接还原铁工艺的烃类重整催化剂的一个具体实施例,所述圆柱状本体的底面直径为25-35mm,高度为7-11mm,所述半椭球形面ⅰ和半椭球形面ⅱ的短轴为16-24mm,长轴为25-35mm,所述竖直通孔的直径为3-7mm。本发明还提供所述一种用于直接还原铁工艺的烃类重整催化剂的制备方法,所述制备方法为将氧化铝经球磨,造粒,并压制成上述催化剂外形结构,经烘干、高温煅烧得到氧化铝载体,最后将成型的氧化铝载体放入镍溶液中浸渍即可得到用于直接还原铁工艺的烃类重整催化剂成品。作为本发明所述一种用于直接还原铁工艺的烃类重整催化剂的制备方法的一个具体实施例,所述氧化铝为粒度≤320目的超细氧化铝粉末;所述球磨需要加入占氧化铝质量0.5%~6%的润滑剂石墨;所述烘干时间为1小时~10天,烘干温度为50℃~750℃;所述煅烧温度为800℃~1600℃,煅烧时间为1h-10h。本发明还提供所述一种用于直接还原铁工艺的烃类重整催化剂的应用,所述催化剂应用于midrex竖炉法直接还原铁工艺的煤气转化炉中。与现有技术相比,本发明具有以下有益效果:本发明用于直接还原铁工艺的烃类重整催化剂主体为圆柱状本体,在圆柱状本体的两端面分别设置有向外凸起的弧形面ⅰ和向外凸起的弧形面ⅱ,催化剂上还开设有若干个贯穿于弧形面ⅰ、弧形面ⅱ以及圆柱状本体的竖直通孔。从催化剂结构上来说,本发明采用双弧形面圆柱状多孔结构,多孔可以增加气体的流动,提高烃类转化为一氧化碳和氢气的转化率。双弧形面结构可以有效增加催化剂成品的孔隙率,从而降低催化剂层的压力降,同时通过圆柱状本体将双弧形面连接,可以提供催化剂的整体强度,防止催化剂在过程中出现破碎,保证催化剂的完整性。本发明用于直接还原铁工艺的烃类重整催化剂在结构上的改进,常规的催化剂外形为平面带孔齿轮状,但存在着容易破碎,装填后转化炉的压差较大的缺点,本申请催化剂采用双弧形面圆柱状多孔结构,使催化剂在以纯氧化铝为载体的情况下,都能获得较高的强度,在装填后转化炉的压差降低。本申请催化剂成分不含有任何助剂,以纯氧化铝为载体,改变了常规催化剂需要加入助剂来提高催化剂的耐热性以及稳定性等各项性能,采用载体单一组分不仅降低了催化剂成本且使生产工艺更加简化,产品易于控制。将本发明催化剂应用于midrex竖炉法直接还原铁工艺的煤气转化炉中作为烃类重整催化剂,其催化剂强度≥2500n/颗,远高于其它同类型的烃类重整催化剂;转化炉压差≤0.02mpa,有效降低压力降。且在整个使用过程中,几乎没有破碎,当催化剂有效成分消耗完全,能从煤气转化炉中取出完整无破碎的催化剂,减少了对煤气转化炉设备的清洗频率,使生产更加高效,进一步降低成本。附图说明图1为示例1当弧形面ⅰ和弧形面ⅱ为半球形面时催化剂的立体结构图。图2为示例1当弧形面ⅰ和弧形面ⅱ为半球形面时催化剂的俯视图。图3为图2中a截面的剖视图。图4为示例2当弧形面ⅰ和弧形面ⅱ为半椭球形面时催化剂的立体结构图。图5为示例2当弧形面ⅰ和弧形面ⅱ为半椭球形面时催化剂的正视图。附图标记:1-圆柱状本体,2-半球形面ⅰ,3-半球形面ⅱ,4-竖直通孔,5-半椭球形面ⅰ,6-半椭球形面ⅱ。具体实施方式为了使本发明的目的、技术方案及优点更加清楚明白,以下结合附图及实施例,对本发明进行进一步详细说明。应当理解,此处所描述的具体实施例仅仅用以解释本发明,并不用于限定本发明。下面结合具体组成及结构对本发明一种用于直接还原铁工艺的烃类重整催化剂、制备及应用进行详细说明。一种用于直接还原铁工艺的烃类重整催化剂,以质量份数计,所述催化剂包括5~30份的活性组分,75~95份的载体,其中,所述活性组分为氧化镍,所述载体为al2o3;所述催化剂的外形结构包括圆柱状本体,所述圆柱状本体的两端面分别设置有向外凸起的弧形面ⅰ和向外凸起的弧形面ⅱ,催化剂上还开设有若干个贯穿于弧形面ⅰ、弧形面ⅱ以及圆柱状本体的竖直通孔。本发明对于用于直接还原铁工艺的烃类重整催化剂的改进主要体现在两个方面,一个是催化剂成分上的改进,一个是催化剂的外形结构上的改进。具体地,对于催化剂的成分,本发明催化剂包括5~30份的活性组分氧化镍,75~95份的载体al2o3。催化剂不含有任何助剂,以纯氧化铝为载体,改变了常规催化剂需要加入助剂来提高催化剂的耐热性、稳定性及强度等各项性能,本发明催化剂载体采用单一组分,不仅降低了催化剂成本且使生产工艺更加简化,产品更易于控制。从催化剂整体外形结构上来说,本发明采用双弧形面圆柱状多孔结构,多孔可以增加气体的流动,提高烃类转化为一氧化碳和氢气的转化率,从而更好地将竖炉中的氧化铁进行还原。双弧形面结构可以有效增加催化剂成品的孔隙率,从而降低催化剂层的压力降,同时通过圆柱状本体将双弧形面连接,可以提供催化剂的整体强度,防止催化剂在过程中出现破碎,保证催化剂的完整性。进一步,所述活性组分氧化镍为10~20份,所述载体al2o3为80~85份。进一步,所述弧形面ⅰ及弧形面ⅱ为互相对称的球形面或椭球形面。更进一步,所述弧形面ⅰ及弧形面ⅱ为互相对称的半球形面或半椭球形面。相比于弧形面,球形面或椭球形面具有更加规则的结构,能进一步增加孔隙率,从而进一步降低催化剂床层的压力降。同时球形面或椭球形面与圆柱状本体形成的结构更加稳定,进一步提高催化剂强度。而互为对称的半球形面或半椭球形面能进一步提高催化剂结构的稳定性,使催化剂强度及床层的压力降达到更佳。进一步,催化剂包括圆柱状本体,所述圆柱状本体的两端面分别设置有互相对称且向外凸起的半球形面ⅰ和半球形面ⅱ,催化剂上还开设有5个贯穿于半球形面ⅰ、半球形面ⅱ以及圆柱状本体的竖直通孔。其中,5个竖直通孔采用均匀分布的方式,其中一个分布在催化剂中心,另外四个均匀分布在以其为中心的圆周上。当催化剂采用上述结构时,所述圆柱状本体的底面直径为25-35mm,优选为30mm;高度为7-11mm,优选为9mm;所述半球形面ⅰ和半球形面ⅱ的直径为25-35mm,优选为31mm;所述竖直通孔的直径为3-7mm,优选为5mm。进一步,所述催化剂包括圆柱状本体,所述圆柱状本体的两端面分别设置有互相对称且向外凸起的半椭球形面ⅰ和半椭球形面ⅱ,催化剂上还开设有5个贯穿于半椭球形面ⅰ、半椭球形面ⅱ以及圆柱状本体的竖直通孔。其中,5个竖直通孔采用均匀分布的方式,其中一个分布在催化剂中心,另外四个均匀分布在以其为中心的圆周上。当催化剂采用上述结构时,所述圆柱状本体的底面直径为25-35mm,优选为30mm;高度为7-11mm,优选为9mm;所述半椭球形面ⅰ和半椭球形面ⅱ的短轴为16-24mm,优选为20mm,长轴为25-35mm,优选为31mm;所述竖直通孔的直径为3-7mm,优选为5mm。一种用于直接还原铁工艺的烃类重整催化剂的制备方法,所述制备方法为将氧化铝经球磨,造粒,并压制成上述催化剂外形结构,经烘干、高温煅烧得到氧化铝载体,最后将成型的氧化铝载体放入镍溶液中浸渍即可得到用于直接还原铁工艺的烃类重整催化剂成品。其中,镍溶液为硝酸镍溶液,温度加热到140-160℃,溶液比重:1.3-1.5g/ml。催化剂的组分发生改变,常规催化剂要添加多种助剂来提高催化剂的强度、活性、耐热性、稳定性等;本发明催化剂只采用氧化铝为载体,不添加任何助剂,同样使催化剂达到较好的强度、活性、耐热性、稳定性等。采用单一组分使催化剂生产工艺更加简化,更有利于生产控制,并降低了原材料成本。催化剂外观的改变,常规催化剂的外形为平面多孔齿轮状,本发明催化剂外形为双弧形面圆柱状多孔结构,通过外形的改变有助于提高催化剂的强度并有效的降低了转化炉的压力降,节约了生产成本。进一步,所述氧化铝为粒度≤320目的超细氧化铝粉末;所述球磨需要加入占氧化铝质量0.5%~6%的润滑剂石墨。这样设置可以使催化剂在成型填充时能增加有效进料量,更有利于催化剂成型。进一步,所述烘干时间为20小时~48小时,烘干温度为50℃~750℃;所述煅烧温度为800℃~1600℃,煅烧时间为1h-10h。长时间的烘干使催化剂不含有游离水,在高温煅烧时,使催化剂收缩一致不出现裂纹。一种用于直接还原铁工艺的烃类重整催化剂的应用,所述催化剂应用于midrex竖炉法直接还原铁工艺的煤气转化炉中。具体地,将本发明催化剂应用与midrex竖炉法直接还原铁工艺的煤气转化炉中作为烃类重整催化剂,将烃类转化为一氧化碳和氢气,从而通入竖炉中作为还原氧化铁的气体。将本发明催化剂应用于midrex竖炉法直接还原铁工艺的煤气转化炉中作为烃类重整催化剂,其催化剂强度≥2500n/颗,远高于其它同类型的烃类重整催化剂;转化炉压差≤0.02mpa,有效降低压力降。且在整个使用过程中,几乎没有破碎,当催化剂有效成分消耗完全,能从煤气转化炉中取出完整无破碎的催化剂,减少了对煤气转化炉设备的清洗频率,使生产更加高效,进一步降低成本。应当说明,本发明用于直接还原铁工艺的烃类重整催化剂的外形结构可以通过压制成型获得,整个催化剂内部为实心结构,只要是能制备出本发明催化剂结构外形即可,这个对于本领域技术人员来说是很容易实现的。具体地,成型步骤包括进料-填充-压制-出料,进料的物料是具有一定颗粒度的物料,填充时采用多次填充的方式保证填充均匀,压制时通过液压传感器设定主压力成型,成型模具采用与催化剂外形相符的形状,出料时通过出料推板缓慢将成型后的颗粒推出成型区。这些对于本领域技术人员是很容易实现的,只要能制备本申请催化剂外形结构即可。下面结合具体示例对本发明一种用于直接还原铁工艺的烃类重整催化剂、制备及应用进行进一步说明。示例1本示例用于直接还原铁工艺的烃类重整催化剂的具体制备过程如下:1、球磨:秤取10kg粒度为300目的氧化铝粉末,并加入占氧化铝质量4%的石墨,投料进入球磨机,进行混料6h,混匀后取出。2、压制成型:将球磨后的粉料压制成外形结构为双半球面圆柱状载体结构,具体外形结构如图1、图2和图3所示:本示例烃类重整催化剂的外形结构包括圆柱状本体1,所述圆柱状本体1的两端面分别设置有互相对称且向外凸起的半球形面ⅰ2和半球形面ⅱ3,催化剂上还开设有5个贯穿于半球形面ⅰ2、半球形面ⅱ3以及圆柱状本体1的竖直通孔4。其中,5个竖直通孔4采用均匀分布的方式,其中一个分布在催化剂中心,另外四个均匀分布在以其为中心的圆周上。上述结构中,所述圆柱状本体1的底面直径为31mm,高度为9mm;所述半球形面ⅰ2和半球形面ⅱ3的直径为30mm,所述竖直通孔4的直径为为5mm。3、成型后处理:将成型后的载体在温度200℃,烘干10h;然后再在1500℃恒温煅烧8h。4、浸渍处理:浸渍处理:将上述煅烧后的氧化率载体在镍溶液中浸渍2h,分解后得到催化剂a成品。成品组成:氧化镍:14份,氧化铝:86份。示例2本示例用于直接还原铁工艺的烃类重整催化剂的具体制备过程如下:1、球磨:秤取10kg粒度为250目是氧化铝粉末,并加入占氧化铝质量4%的石墨,投料进入球磨机,进行混料8h,混匀后取出。2、压制成型:将球磨后的粉料压制成外形结构为双半椭球面圆柱状载体结构,具体外形结构如图4和图5所示:本示例烃类重整催化剂的外形结构包括圆柱状本体1,所述圆柱状本体1的两端面分别设置有互相对称且向外凸起的半椭球形面ⅰ5和半椭球形面ⅱ6,催化剂上还开设有5个贯穿于半椭球形面ⅰ5、半椭球形面ⅱ6以及圆柱状本体1的竖直通孔4。其中,5个竖直通孔4采用均匀分布的方式,其中一个分布在催化剂中心,另外四个均匀分布在以其为中心的圆周上。所述圆柱状本体1的底面直径为31mm,高度为9mm;所述半椭球形面ⅰ5和半椭球形面ⅱ6的短轴为20mm,长轴为30mm,所述竖直通孔4的直径为5mm。3、成型后处理:将成型后的载体在温度300℃,烘干10h;然后再在1500℃恒温煅烧10h。4、浸渍处理:将上述煅烧后的氧化率载体在镍溶液中浸渍2h,分解后得到催化剂a成品。成品组成:氧化镍:16份,氧化铝:84份。对比例1本对比例为示例1的对比例,在示例1的基础上,改变催化剂的外形结构,将催化剂的外形结构压制成现有的常规平面带孔齿轮状,并采用示例1相同的组成成分和制备方法。对比例2本对比例为示例1的对比例,在示例1的基础上,在催化剂的制备过程中加入镁粉,制备的催化剂成品中包括氧化镍、氧化铝还有助剂氧化镁,其余与示例1一致,研究镁粉的加入对催化剂的影响。对比例3本对比例为示例1的对比例,在示例1的基础上,改变催化剂的外形结构,将催化剂的外形结构压制成对称的双弧形面,并采用示例1相同的组成成分和制备方法。催化剂性能测试结果上述示例1至2及对比例1至3制备得到催化剂的性能结果如下表1所示:表1示例1至2及对比例1至3制备得到催化剂的性能结果催化剂强度(n/颗)转化炉压差(mpa)残余ch4%使用后催化剂完整性示例127060.01515.21完整无破碎示例226900.01815.05完整无破碎对比例117800.04516.02破碎严重对比例226800.01915.98完整无破碎对比例325200.02015.85几乎无破碎从上表1对示例和对比例制备得到的催化剂的性能结果可以看出,本申请催化剂采用双弧形面圆柱状结构,相比于现有的常规平面带孔齿轮状,可以显著提高催化剂的强度及转化炉压差,使催化剂的强度从现有的1780n/颗提高到2520n/颗以上,特别是当采用半球形面或半椭球形面时强度提高更强;转化炉压差从现有的0.045mpa降低到0.020mpa以下,有效降低压力降,从而节约了能源成本,大约能降低10%的能源消耗。将本申请催化剂应用氧化铁还原进行烃类重整,残余ch4的含量并没有特别大的变化,说明采用本申请催化剂外形及不加入助剂的情况下能达到现有催化剂的催化活性。且在整个使用过程中,几乎没有破碎,能从煤气转化炉中取出完整无破碎的催化剂,减少了对煤气转化炉设备的清洗频率,使生产更加高效,进一步降低成本。以上所述仅为本发明的较佳实施例而已,并不用以限制本发明,凡在本发明的精神和原则之内所作的任何修改、等同替换和改进等,均应包含在本发明的保护范围之内。当前第1页12