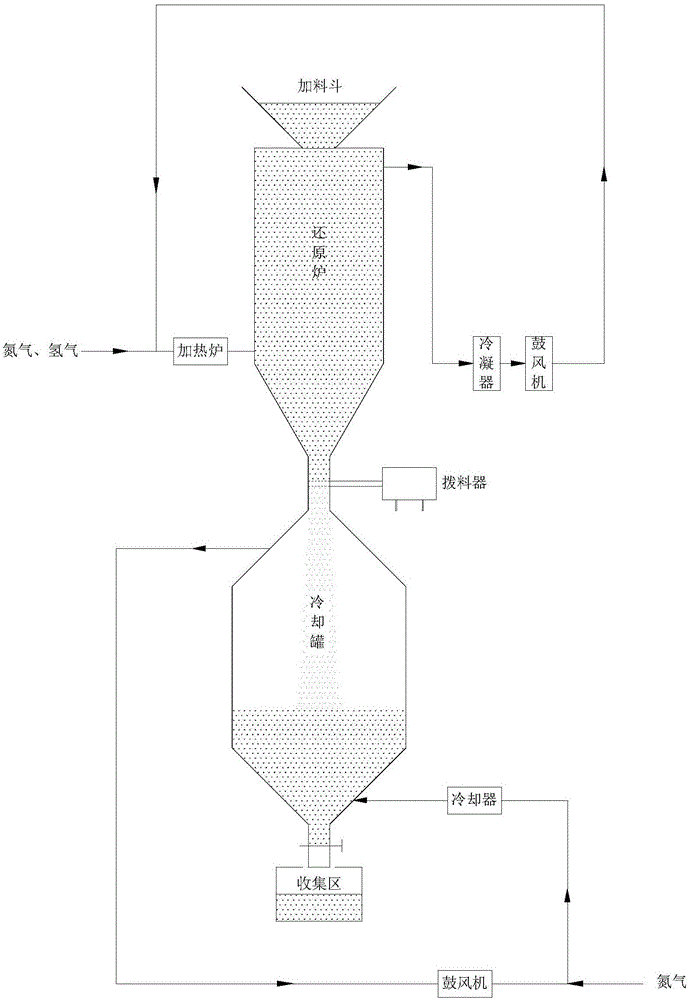
本发明属于催化剂领域,具体涉及一种催化剂还原工艺方法。
背景技术:
:金属催化剂广泛的应用于当今的石油化工等领域。例如石脑油重整pt催化剂,丙烷脱氢pt催化剂,汽车尾气pt-pd催化剂,油脂加氢ni催化剂。这类金属催化剂在制备过程中,催化剂经焙烧后,活性组分是氧化态的物种,催化剂还需经过还原将活性组分转化成金属单质态物种,这样催化剂才具备反应活性。国内外大型的催化剂厂均建有还原装置,而这些还原装置均采用的是常规的固定床还原工艺。采用固定床还原工艺还原催化剂时,还原炉需先装填催化剂,然后置换空气,再升温并进还原气还原,再降温,最后卸出催化剂,完成还原。常规的固定床式还原工艺为间歇式操作,存在还原周期长,步骤繁琐不连续,效率低下,批次与批次之间还原效果存在差异等问题。技术实现要素:本发明所要解决的技术问题是克服现有的固定床式还原工艺为间歇式操作而存在还原周期长、步骤繁琐不连续、效率低下、批次与批次之间还原效果存在差异等问题,提供一种可连续操作的催化剂还原工艺方法。发明人提出采用移动床式反应器还原催化剂,催化剂在还原炉中从上至下缓慢移动,还原气从下至上吹扫催化剂床层,通过调节拨料器的转速,来控制催化剂在还原炉中的停留时间以实现充分还原催化剂。催化剂经还原后再缓慢移动到冷却罐,用低温氮气降温,待降到室温后,从冷却罐中移出,完成还原。使用该方法还原催化剂,可有效的缩短催化剂还原后的降温时间,避免装卸催化剂的重复性工作,提高催化剂还原效率,实现了催化剂还原工艺的可连续性和高效性。具体的技术方案如下:本发明一种可连续操作的催化剂还原工艺方法,包括:1)还原工艺:待还原的催化剂在还原炉中自上而下缓慢移动,将预热至100~900℃的还原气从还原炉的下端以100~20000h-1的体积空速自下而上吹扫催化剂床层进行还原;通过调节催化剂的移动速度,控制催化剂在还原炉中的停留时间,达到能充分还原催化剂的目的;2)冷却工艺:将已还原的催化剂移出还原炉,流入到冷却罐,10~20℃的低温氮气从冷却罐的下端以100~1000h-1的体积空速自下而上吹扫催化剂床层快速冷却催化剂;3)还原好的催化剂冷却到室温后从冷却罐出口移出密封储存,同时在还原炉的上端补加待还原的催化剂,从而实现了催化剂还原的可连续性操作工艺;其中还原气为氢气和氮气的混合气,氢气占混合气的体积分数可任意调节。优选地,催化剂在还原炉中的停留时间为2~12h。优选地,冷却罐的压力为微正压。优选地,已还原的催化剂在冷却罐的冷却时间为1~5h。本发明的一种可连续操作的催化剂还原工艺方法,可用于各种催化剂的还原,优选用于贵金属催化剂和ni催化剂。试验结果发现,使用本发明的可连续操作的催化剂还原工艺方法,相较用常规方法,在相同的操作时间内,催化剂的还原量提高3倍,氮气的消耗量仅为传统工艺的80%,氢气的消耗量仅为传统工艺的60%,有效的提高了催化剂还原效率和降低了催化剂制造成本。此外,因催化剂在还原炉中的停留时间大大缩短,有效的保证了活性组分在催化剂上的高分散度,提高了催化剂的活性。附图说明图1是本发明一种可连续操作的催化剂还原工艺方法的一个具体实施方案的装置示意图。具体实施方式以下的实施例用于对本发明的技术原理、实施方法及效果进行具体说明,但本发明的方法及核心思想不受其限制。本发明的一种可连续操作的催化剂还原工艺方法,可用于各种催化剂的还原,例如贵金属催化剂和ni催化剂,具体地举例为用于丙烷脱氢pt/al2o3催化剂的还原,该种催化剂用于丙烷脱氢制丙烯的反应。实施例1将本发明的还原工艺应用于丙烷脱氢pt催化剂的还原过程。还原气为氢气和氮气的混合气,还原气中氢气的体积分数为20%,还原气的空速为2000h-1,还原温度为500℃。本发明的还原工艺所用氢气和氮气的耗气量,以及装置操作100h后的催化剂的还原量见表1。本发明的还原工艺的具体还原操作方法如下:还原炉的装填量为2m3,将还原炉装满催化剂,电加热炉升温,升温速率为20℃/h,同时向还原炉中通入还原气。电加热炉的温度升至500℃后,开启拨料器,使还原炉中的催化剂缓慢的移动到冷却罐中。同时从还原炉的上端入口处向还原炉补充催化剂,保障还原炉中的催化剂的量始终是2m3。拨料器的拨料速度控制在刚好能使还原炉上端的催化剂移动到还原炉下端的时间是10h。还原好的催化剂移动到冷却罐中,通入20℃的氮气吹扫催化剂,氮气的空速为可调节,要保障催化剂的温度降至室温为5h,当催化剂的温度降至室温后,将催化剂从冷却罐中卸出。计量装置连续运转100h后还原的催化剂的体积。用本发明的还原工艺还原的催化剂记为a,经过还原的催化剂a用于丙烷脱氢反应,反应条件如下:反应温度600℃,压力为常压,h2/丙烷(mol比)=0.6,丙烷的空速1000h-1。连续反应50h催化剂丙烷脱氢平均转化率和平均选择性数据见表2所示。对比例1传统的还原工艺所用氢气和氮气的耗气量,以及装置操作100h后的催化剂的还原量见表1。传统的还原工艺的具体还原操作方法如下:还原炉的装填量为2m3,将还原炉装满催化剂,电加热炉升温,升温速率为20℃/h,同时向还原炉中通入还原气,还原气为氢气和氮气的混合气,还原气中氢气的体积分数为20%,还原气的空速为2000h-1。电加热炉的温度升至500℃后,维持在500℃下10h。然后电加热炉停止加热,向还原炉中通入温度为常温的n2吹扫,n2的空速为1000h-1,n2吹扫20h催化剂的温度降至常温,将催化剂从还原炉中卸出,密封保存,完成一个批次的还原。重复上述的操作,进行下个批次的还原。计量装置连续运转100h后还原的催化剂的体积。用传统的还原工艺还原的催化剂记为b,经过还原的催化剂b用于丙烷脱氢反应,反应条件与催化剂a的评价条件一样。连续反应50h催化剂丙烷脱氢平均转化率和平均选择性数据见表2所示。表1本发明的还原工艺与传统还原工艺的耗气量及还原量对比表耗气量及还原量本发明的还原工艺传统的还原工艺氢气用量(m3)57909245氮气用量(m3)2900035000操作100h后的催化剂还原量(m3)155表2本发明的还原工艺与传统还原工艺还原的催化剂的丙烷脱氢反应数据对比表催化剂丙烷转化率(%)丙烯选择性(%)a33.692.5b31.490.1从表1的数据可以看出,在相同的还原操作时间下,本发明的方法还原的催化剂量是传统方法还原的催化剂量的3倍,氢气耗气量是传统方法耗气量的63%,氮气耗气量是传统方法耗气量的83%。从表2的数据可以看出,本发明的方法还原的催化剂的丙烷转化率和丙烯选择性均要高于传统方法还原的催化剂。所以,本发明的还原工艺极大的提高了催化剂还原的效率,降低了氢气和氮气的消耗,并且显著提高了催化剂的反应性能。当前第1页12