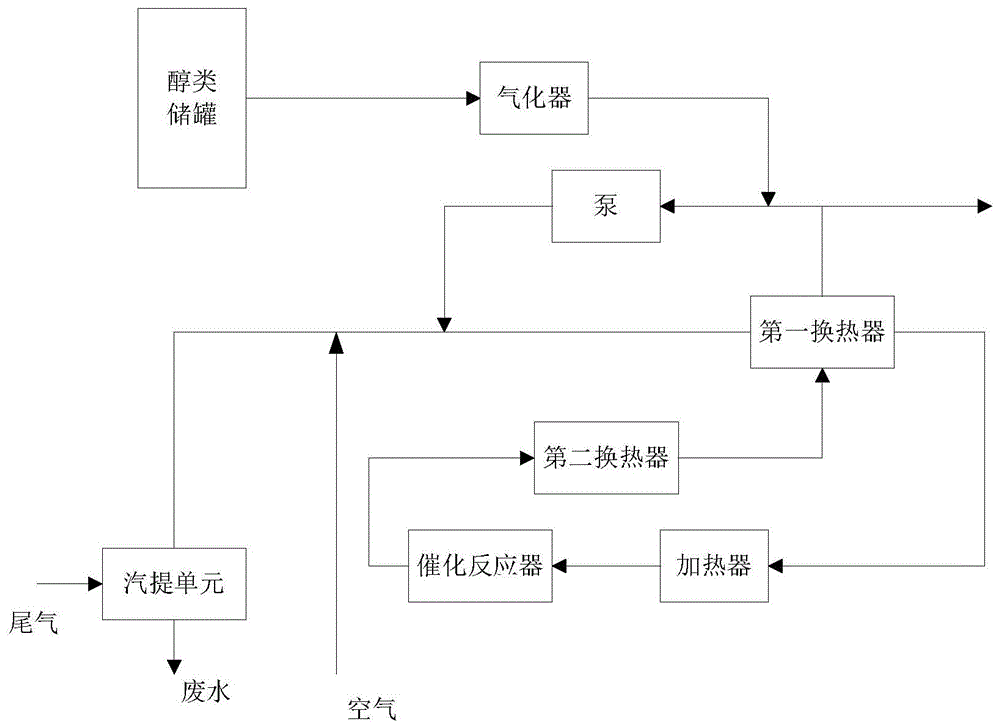
本实用新型涉及尾气处理,特别涉及丙烯酸生产中尾气的处理装置。
背景技术:
:丙烯酸及酯装置在生产过程中,从尾气吸收塔塔顶排放出来的丙烯酸尾气中含有丙烯、丙烷、甲醛、乙醛、丙烯酸、丙烯醛、乙酸和乙酸乙酯等挥发性有机物(VOCs)和一氧化碳等可燃组份,当前主要采用催化氧化技术对该股废气进行催化氧化处理,净化后的尾气经烟囱直接排放。随着丙烯酸及酯装置的技术进步、原料丙烯纯度的提高及新的环保排放标准对NMHC(非甲烷总烃)排放限值的提高,已有的丙烯酸催化氧化处理技术已不能满足新的环保排放标准的排放要求。为了排放达标,目前的改进方式为:1.提高丙烯酸及酯装置生产原料丙烯的纯度,如采用聚合级丙烯,减少丙烯酸尾气中的丙烷含量。该方式的主要不足在于:丙烯酸尾气中丙烷浓度的降低并不能弥补催化反应器反应温度降低(丙烷浓度降低后,丙烯酸尾气中的可燃物减少,导致尾气的绝热温升降低)所导致丙烯和丙烷转化率降低带来的影响,且聚合级丙烯的价格远高于普通的丙烯,本方法既不能解决实际问题又很不经济。2.通过更换更大面积的尾气换热器或开启加热器的方式提升催化反应器进口温度以提升反应器出口温度。该方式的主要不足在于:采用更换更大换热面积尾气换热器和开启加热器的方式,对提升反应器进口温度有限,不足以弥补由于丙烯酸及酯装置技术进步及原料丙烯纯度提高所导致的催化反应器出口温度的降低,且采用该方法或者需要对原系统进行大幅度的改造,或者会导致排气温度的提升导致系统运行能耗大幅度提高,经济性很差。3.增加催化氧化处理系统催化剂的使用量及缩短催化剂更换周期,来弥补由于反应温度降低导致的丙烯和丙烷转化率降低带来的影响。该方式的主要不足在于:丙烯酸催化氧化处理系统所采用的贵金属催化剂需要从国外进口,价格昂贵,大大增加了丙烯酸尾气催化氧化处理系统的使用成本;同时,更换下来的贵金属催化剂依然具有不错的催化活性,也造成了贵金属催化剂的浪费。技术实现要素:为了解决上述现有技术方案中的不足,本实用新型提供了一种处理效果好、排放达标、成本低、结构简单的丙烯酸生产中尾气的处理装置。本实用新型的目的是通过以下技术方案实现的:丙烯酸生产中尾气的处理装置,所述丙烯酸生产中尾气的处理装置包括:加热器,所述加热器用于加热所述尾气,并送催化反应器;催化反应器,所述催化反应器用于处理加热后的尾气;气化器,所述气化器具有进口和出口,所述进口适于连接丙烯酸生产中的醇类储罐,气化后的醇类传送到所述催化反应器。与现有技术相比,本实用新型具有的有益效果为:1.本方案通过向丙烯酸尾气中添加丙烯酸生产中的原料醇类,如甲醇、乙醇或丁醇,利用在当前催化反应器运行工况下贵金属催化剂对醇类的催化氧化的去除效率接近100%的特性,依靠添加的醇类在催化氧化时释放的热量,可以有效地提升催化反应器的出口温度,从而可以有效提升催化剂对丙烯酸尾气中丙烯和丙烷的去除效率,保证丙烯酸尾气经催化氧化处理系统处理后能达到新的环保排放标准的排放要求,实现达标排放;2.工艺简单,安全可靠,改造工作量小,可实现对现有丙烯酸尾气催化氧化处理系统的无扰动升级改造;3.本方案所需要添加的醇类乃是现有丙烯酸及酯生产装置的原料:甲醇、乙醇或丁醇,原料供应充足、方便和可靠;4.本方案可确保现有丙烯酸催化处理系统在不增加贵金属催化剂使用量及缩短贵金属催化剂更换周期的前提下,提高丙烯和丙烷的转化率,确保净化后的丙烯酸尾气能达到环保排放标准的要求,降低了成本;5.本方案向丙烯酸尾气中添加的醇类,在发生催化氧化反应后释放出来的热量可以通过现有丙烯酸尾气催化氧化处理系统的余热锅炉进行热量回收(如有),或者在排气烟囱前增加热回收装置(如热水换热器)进行热量回收,有效减少操作费用。附图说明参照附图,本实用新型的公开内容将变得更易理解。本领域技术人员容易理解的是:这些附图仅仅用于举例说明本实用新型的技术方案,而并非意在对本实用新型的保护范围构成限制。图中:图1是根据本实用新型实施例的丙烯酸生产中尾气的处理装置的结构简图。具体实施方式图1和以下说明描述了本实用新型的可选实施方式以教导本领域技术人员如何实施和再现本实用新型。为了教导本实用新型技术方案,已简化或省略了一些常规方面。本领域技术人员应该理解源自这些实施方式的变型或替换将在本实用新型的范围内。本领域技术人员应该理解下述特征能够以各种方式组合以形成本实用新型的多个变型。由此,本实用新型并不局限于下述可选实施方式,而仅由权利要求和它们的等同物限定。实施例1:图1示意性地给出了本实用新型实施例的丙烯酸生产中尾气的处理装置的结构简图,如图1所示,所述处理装置包括:加热器,所述加热器用于加热所述尾气,并送催化反应器;催化反应器,所述催化反应器用于处理加热后的尾气,尾气在所述催化反应器内催化氧化为二氧化碳和水;气化器,所述气化器具有进口和出口,所述进口适于连接丙烯酸生产中的醇类储罐,如甲醇、乙醇或丁醇,气化后的醇类经过所述加热器后传送到所述催化反应器;汽提单元,丙烯酸生产中的尾气送所述汽提单元,之后和空气混合,混合气送第一换热器;第一换热器,经过第一换热器换热后的尾气送所述加热器;排出所述催化反应器的净化气体送所述第一换热器,换热后的净化气体的部分排往下游,部分通过泵输送;泵,所述泵用于把经过第一换热器后的净化气体的部分传送到第一换热器和汽提单元之间的管道内,与混合气一起到所述第一换热器;气化后的醇类传送到第一换热器和泵之间的管道内;第二换热器,所述第二换热器设置在所述催化反应器和第一换热器之间的管道上。上述丙烯酸生产中尾气的处理装置的工作过程为:丙烯酸生产中尾气经过汽提后和空气混合,混合气和气化后的醇类一起送第一换热器加热,之后送加热器;气化后的醇类和所述混合气经过加热后送催化反应器,所述醇类是丙烯酸生产的原料,如甲醇、乙醇或丁醇;醇类在所述催化反应器被催化氧化,产生的热量提高了所述催化反应器的温度;所述尾气在所述催化反应器被催化氧化为二氧化碳和水;排出所述催化反应器的净化气体依次经过第二换热器和第一换热器降温,排出第一换热器的净化气体的部分排往下游,部分和气化后的醇类混合,被泵送至第一换热器和汽提单元之间的管道内,和所述混合气混合。实施例2:根据本实用新型实施例1的丙烯酸生产中尾气的处理装置在某丙烯氧化法生产丙烯酸企业中的应用例。在该应用例中,该丙烯酸生产企业的吸收塔塔顶排放的丙烯酸尾气流量为15780Nm3/h,压力为14kPaG,温度为30℃,尾气中的气体组份具体如下:序号成分丙烯酸废气kg/h质量(%)1氮气17737.885.6722一氧化碳121.30.5813氧气1250.76.2174二氧化碳390.41.8695丙烯132.60.6356丙烷16.5750.0797甲醛4.90.0238乙醛0.4410.0029丙烯醛8.380.04010丙酮4.10.02011水981.4474.69912醋酸10.30.04913丙烯酸8.8200.04214空气205.4090.07215甲苯15.1410.072将企业原有乙醇储罐的乙醇经输送泵输送至气化器,在气化器内将乙醇气化,并经流量控制稳定在50kg/h,再经气体分布器与第一换热器和泵之间的管道内的净化气体混合,进入催化反应器内发生反应。乙醇的加入使得催化反应器出口温度提高了70℃,并稳定维持在550℃以上,净化后的尾气中NMHC(非甲烷总烃)维持在30~70mg/m3,完全满足当前环保排放标准的要求。消耗的乙醇所产生的热量,经过第二换热器得到了回收,相比其它措施,运行能耗大幅度降低,产生了较好的经济效益。作为对比,采用现有技术中的处理方式,催化反应器的出口温度维持在480~520℃之间,净化后尾气中的NMHC(非甲烷总烃)维持在60~400mg/m3,达不到当前该企业所在地环保排放标准小于80mg/m3的要求。上述实施例仅是示例性地给出了第一换热器和催化反应器之间设置第二换热器,汽化后的醇类送泵和第一换热器之间的管道内,当然还可以在第一换热器和第二换热器之间设置第三换热器,汽化后的醇类直接送加热器。当前第1页1 2 3