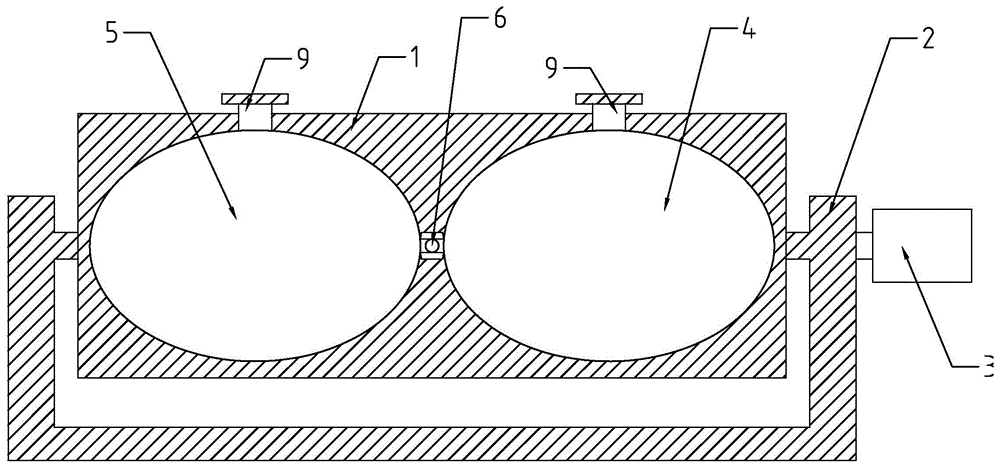
本发明涉及物料粉碎
技术领域:
,尤其是涉及一种双腔体两级球磨机及高效永磁铁氧体细粉碎方法。
背景技术:
:铁氧体细粉碎是铁氧体生产工艺中十分重要的一个环节,是将预烧得到的铁氧体经过粗粉碎后得到粗粉再经过进一步的细粉碎得到粒度更细的成型用料浆。预烧料是一种密度小,较松散的具有铁氧体晶体结构的物质,而通过细粉碎工艺将预烧料细化得到浆料,使其具有较好的粒度分布,良好的二次烧结化学反应活性,较好的毛坯成型性对最终得到性能良好的成品率高的磁体具有十分重要的作用。细粉碎后的料浆粒度分布是影响料浆成型性能的重要因素,粗细颗粒的比例要搭配合理,如果粗粒径颗粒过多,细粒径颗粒少,粒径分布曲线右移,成型后毛坯孔隙率大,烧结后磁体气孔多,晶体生长也不连续,大晶粒“吞并”小晶粒,磁体中大晶粒比例过多,磁体性能变差。如果细粒径颗粒过多,粗粒径颗粒过少,会导致成型时间加长,影响成型效率,成型毛坯内部细微裂纹增多,烧结后磁体开裂增加,影响成品率。因此较理想的粒径分布应呈现一个正态分布曲线,粗细颗粒分布合理,并且正态分布曲线“尖锐”些对铁氧体生产中越有利。现主流的铁氧体生产细粉碎方法主要有球磨和砂磨,铁氧体生产用球磨机为圆柱形结构,两端焊有两块金属圆板,形成一个密闭的圆柱体。内部装有球磨介质钢球、粉碎物料、弥散剂水,由电机带动球磨机筒体转动,筒体转动带动筒体内的钢球与物料一起运动,在离心力及球磨机筒体内壁摩擦力作用下,钢球提升到一定高度,然后在重力的作用下下落,物料在钢球的冲击下粉碎,通过球与球之间、球与筒体壁、球与物料之间的撞击摩擦达到将预烧料磨细的效果。砂磨机是在一立式圆筒内,用旋转圆盘或搅拌棒使圆筒内的钢球产生无规则的高速运动,对圆筒内物料起到研磨作用。目前大生产铁氧体细粉碎用球磨机较多,其内部装有数根用于加强钢球与物料相互碰撞作用的“筋”,形状一般为长方形或圆弧形,通过球磨机的匀速转动磨细物料,永磁铁氧体是磁铅石型晶体结构,晶体内的晶胞的各个离子主要是由离子键的作用相互键合的,键合力仅次于原子键,故永磁铁氧体宏观表现为硬而脆,因此要磨至亚微米级的粒度不仅球磨时间较长,特别是高性能的永磁铁氧体材料要求料浆粒径分布更窄,晶粒更细,这就需要经过两级球磨,要将一台球磨机中的料浆用高压气流将料浆转移至另外一台球磨机,不仅费时费力对不同批次料浆的稳定性也有较大影响,如专利cn102553683a中提到一种永磁铁氧体预烧料的粉碎工艺,利用两台球磨机分级研磨,其性能相比现有工艺有一定提高,但该工艺不仅设备复杂,工艺步骤繁琐,对操作水平要求较高对控制料浆的稳定性带来很大难度。技术实现要素:为解决上述问题,本发明提供了一种双腔体两级球磨机,其能在一台球磨机中实现两级球磨工艺,并且能够提高不同批次料浆的稳定性,增加球磨的均匀性,提高球磨效率,经其处理后料浆粒径分布相比现有技术球磨也更加窄;本发明还提供了一种通过上述双腔体两级球磨机实现的高效永磁铁氧体细粉碎方法。为实现上述目的,本发明采用的技术方案如下:一种双腔体两级球磨机,其包括筒体、支架与驱动机构,筒体内设有两个球磨腔,分别为一级球磨腔和二级球磨腔,一级球磨腔与二级球磨腔相邻设置,一级球磨腔与二级球磨腔之间通过阀门相连通。一级球磨腔和二级球磨腔上均设有进出料口。作为优选,球磨腔为椭球形球磨腔,一级球磨腔的两条极半径与赤道半径的比例为(1.4~3.2):(1.4~3.2):1,二级球磨腔的两条极半径与赤道半径的比例为(1.2~3):(1.2~3):1。本发明中的球磨机为圆柱形筒体内有两个椭圆形的腔体,采用椭圆形腔体可以很好的分散由钢球、预烧料、弥散剂向两端运动带来的冲击,使其均匀受力于整个筒体,增加球磨的均匀性,提高球磨效率,相邻的两个椭圆形腔体可以实现两级球磨,第一级球磨后的料浆用气压打至筒体的另外一个腔体内进行第二级球磨,由常规的两台球磨机实现两级磨工艺到本发明的一台球磨机即可实现,不仅节省一台球磨机设备,而且同一个筒体内料浆的传输更加方便快捷,操作工艺简单,有利于不同批次料浆的稳定性,粒径分布相比一级球磨也更加窄,对制备高性能永磁铁氧体材料十分关键。本发明不涉及球磨机驱动机构等部件的改动,除本发明所涉及以外的部件及处理方法均可采用现有技术解决。作为优选,一级球磨腔与二级球磨腔内壁上设有若干均匀分布的凸块,凸块的顶面设有圆弧形凹槽。作为优选,凸块顶面的圆弧形凹槽的圆心角为70°~190°。在球磨机转动一圈的过程中,如何能最大化将电机的动能转化为预烧料粉碎的表面能,预烧料磨越细表面能增加越大,所需要转化到预烧料上的功也越多。在球磨过程中,能量的损失主要有三大块,第一块是电能通过电机转化为机械能时产生损失,按照较高的电机效率93%左右计算,这部分能量损失在7%左右,这部分损失直接跟电机性能相关,提升空间有限;第二块是电机输出的机械能进过传动系统转化为球磨介质的机械能,这块的能量损失一般占总能耗的10~15%左右,主要取决于传动系统的效率高低,这部分提升的效果也有限;第三块是球磨介质的机械能转化为预烧料的表面能,据相关文献报道,真正作用于提高预烧料表面能的功只占输入功的0.3~1.3%左右,大部分功成为球磨损失功,这些球磨损失功主要表现为预烧料、球磨介质与磨球,磨球之间,磨球与衬板等的相互摩擦、撞击产生的热量,所以直观的观察到球磨后的料浆温度有时能高达七十多度。因此球磨机在转动过程中,提高球磨介质的机械能就有较大的空间。本发明中在球磨腔体内壁设置若干凸块能在球磨机转动一圈的过程中提高磨球的机械能,凸块能比传统球磨机更好的“兜”住磨球,提高其势能,待其转动到一定位置的时候转化为动能击打冲击预烧料,同时采用较大的磨球增加磨球的动能将较大粒径的预烧料磨至较小的粒径为后面二级进一步细磨打下基础。凸块顶面设有圆弧形凹槽,弧形面有利于进一步提升磨球的势能,一部分磨球聚集在弧形面上,球磨机转动的时候,在离心力与凸块表面弧形的摩擦力,作用下,磨球提升到较高的高度下,在重力的作用下形成许多个瀑布式泄落的效果,在这种模式下,磨球对物料的冲击更加强烈,磨球与预烧料相互摩擦,磨球、凸块、腔壁的之间的预烧料摩擦频率更高,有利于高效的磨细预烧料,增加其表面能。转速过低,对于大粒径的预烧料冲击力不够,影响最终的球磨效果,转速过高,钢球的离心力超过重力,钢球容易贴着筒壁,钢球对预烧料的冲击作用大大减少,起不到粉碎的效果。另外采用顺时针转动和逆时针交替转动的球磨方式能极大的避免球磨死角,提高不同批次球磨的稳定性和一致性,为后面成型及烧结工艺的工艺控制打下良好的基础。作为优选,一级球磨腔中,凸块的宽度与球磨腔较长极半径的比例为1:20~70,凸块的高度与球磨腔较长的极半径的比例为1:18~50;二级球磨腔中,凸块的宽度为与球磨腔较长极半径的比例为1:40~80,凸块的高度与球磨腔较长的极半径的比例为1:30~50。作为优选,凸块为条状,其由球磨腔极轴的一段延伸至另一端。作为优选,一级球磨腔中设有7~14条凸块。二级球磨腔中设有8~13条凸块。作为优选,凸块为底面为正方形的凸块。作为优选,一级球磨腔中设有7~14块底面为正方形凸块。二级球磨腔中设有8~13块底面为正方形凸块。一种通过双腔体两级球磨机实现的高效永磁铁氧体细粉碎方法,包含以下步骤,a)将球磨原料加入到一级球磨腔中,并加入磨球与球磨介质;b)一级球磨:以20~35rpm的转速顺时针处理50~100分钟,然后以15~30rpm转速逆时针处理50~100分钟;c)循环重复步骤b)中处理5~10小时;d)将一级球磨处理后制得的料浆输送至二级球磨腔中;e)二级球磨:以20~35rpm的转速顺时针处理50~100分钟,然后以15~30rpm转速逆时针处理50~100分钟;f)循环重复步骤e)中处理5~10小时;g)将经上述步骤处理后获得的料浆输送至料塔。作为优选,球磨过程中球磨原料、磨球与球磨介质的比例为1:(4~7):(1.1~1.4)。作为优选,球磨介质为水。作为优选,步骤d)具体为,打开一级球磨腔与二级球磨腔之间的阀门,采用高压气体将经一级球磨处理后的料浆输送至二级球磨腔中。作为优选,步骤b)一级球磨采用的磨球为直径7~11mm的钢球;步骤e)二级球磨采用的磨球为直径3.5~8mm的钢球。二级球磨采用更细的钢球,是基于在第一级腔体内预烧料在磨至一定的粒度后,钢球之间及钢球与凸块、筒壁、水之间的相互摩擦的方式来进一步磨细预烧料是一种主要的粉碎方式,对提高表面能的贡献占比增大,因此对钢球直接冲击预烧料的需求降低。作为优选,在步骤e)进行二级球磨的同时,一级球磨腔中加入新球磨原料同时进行一级球磨处理。因此,本发明具有以下有益效果:与现有技术相比,本发明中的双腔体两级球磨机及高效永磁铁氧体细粉碎方法具有球磨效率高、工序简单、操作性强、稳定性高、磨出的料浆粒径分布窄,料浆成型效率高等优点;磨至相同的粒径,采用本发明中的双腔体两级球磨机及高效永磁铁氧体细粉碎方法可以缩短球磨时间3~6小时,相同工况下,磁性能提高50~100gs,料浆成型时间节约15~25%,综合成品率提高5~20%,内禀提高100~400oe。附图说明图1为本发明中双腔体两级球磨机的一种截面示意图;图2为本发明中双腔体两级球磨机一级球磨腔的一种截面示意图;图3为本发明中双腔体两级球磨机二级球磨腔的一种截面示意图;图4为本发明中双腔体两级球磨机球磨腔内壁凸块的一种截面示意图;图5为不同球磨粒径分布图。图中:筒体1,支架2,驱动机构3,一级球磨腔4,二级球磨腔5,阀门6,凸块7,圆弧形凹槽8,进出料口9。具体实施方式下面结合具体实施方式对本发明的技术方案作进一步的说明。显然,所描述的实施例仅是本发明的一部分实施例,而不是全部的实施例。基于本发明中的实施例,本领域普通技术人员在没有做出创造性劳动前提下所获得的所有其它实施例,都属于本发明保护的范围。在本发明中,若非特指,所有的设备和原料均可从市场上购得或是本行业常用的,下述实施例中的方法,如无特别说明,均为本领域常规方法。下述实施例与对比例中采用的球磨原料均为相同标号的铁氧体预烧料并二次添加caco31.0wt%,sio20.3wt%,la2o31.0wt%,co3o40.5wt%,其中球磨原料的中值粒径d50为4.5微米。实施例1一种双腔体两级球磨机,其包括筒体1、支架2与驱动机构3,筒体内设有两个椭球形球磨腔,分别为一级球磨腔4和二级球磨腔5,一级球磨腔与二级球磨腔相邻设置,一级球磨腔与二级球磨腔之间通过阀门6相连通;一级球磨腔的两条极半径与赤道半径的比例为1.4:1.4:1,二级球磨腔的两条极半径与赤道半径的比例为1.2:1.2:1;一级球磨腔与二级球磨腔内壁上设有若干均匀分布的凸块7,凸块的顶面设有圆弧形凹槽8;一级球磨腔中,凸块的宽度与球磨腔较长极半径的比例为1:20,凸块的高度与球磨腔较长的极半径的比例为1:18,凸块顶面的圆弧形凹槽的圆心角为70°;二级球磨腔中,凸块的宽度为与球磨腔较长极半径的比例为1:40,凸块的高度与球磨腔较长的极半径的比例为1:30,凸块顶面的圆弧形凹槽的圆心角为70°;凸块为底面为正方形的凸块,一级球磨腔中设有7块底面为正方形凸块,二级球磨腔中设有8块底面为正方形凸块。一种通过双腔体两级球磨机实现的高效永磁铁氧体细粉碎方法,包含以下步骤,a)将球磨原料加入到一级球磨腔中,并加入磨球与水,球磨原料、磨球与水的比例为1:4:1.1;磨球采用直径为7mm的钢球;b)一级球磨:以20rpm的转速顺时针处理50分钟,然后以15rpm转速逆时针处理50分钟;c)循环重复步骤b)中处理5小时;d)打开一级球磨腔与二级球磨腔之间的阀门,采用高压气体将经一级球磨处理后的料浆输送至二级球磨腔中,并使球磨原料、磨球与水的比例为1:4:1.1,磨球采用直径为3.5mm的钢球;e)二级球磨:以20rpm的转速顺时针处理50分钟,然后以15rpm转速逆时针处理50分钟;f)循环重复步骤e)中处理5小时;g)将经上述步骤处理后获得的料浆输送至料塔。此外,在步骤e)进行二级球磨的同时,一级球磨腔中加入新球磨原料同时进行一级球磨处理。实施例2一种双腔体两级球磨机,其包括筒体1、支架2与驱动机构3,筒体内设有两个椭球形球磨腔,分别为一级球磨腔4和二级球磨腔5,一级球磨腔与二级球磨腔相邻设置,一级球磨腔与二级球磨腔之间通过阀门6相连通;一级球磨腔的两条极半径与赤道半径的比例为3.2:1.4:1,二级球磨腔的两条极半径与赤道半径的比例为3:3:1;一级球磨腔与二级球磨腔内壁上设有若干均匀分布的凸块7,凸块的顶面设有圆弧形凹槽8;一级球磨腔中,凸块的宽度与球磨腔较长极半径的比例为1:70,凸块的高度与球磨腔较长的极半径的比例为1:50,凸块顶面的圆弧形凹槽的圆心角为190°;二级球磨腔中,凸块的宽度为与球磨腔较长极半径的比例为1:80,凸块的高度与球磨腔较长的极半径的比例为1:50,凸块顶面的圆弧形凹槽的圆心角为190°;凸块为条状,其由球磨腔极轴的一段延伸至另一端,一级球磨腔中设有14条凸块,二级球磨腔中设有13条凸块。一种通过双腔体两级球磨机实现的高效永磁铁氧体细粉碎方法,包含以下步骤,a)将球磨原料加入到一级球磨腔中,并加入磨球与水,球磨原料、磨球与水的比例为1:7:1.4;磨球采用直径为11mm的钢球;b)一级球磨:以35rpm的转速顺时针处理100分钟,然后以30rpm转速逆时针处理100分钟;c)循环重复步骤b)中处理10小时;d)打开一级球磨腔与二级球磨腔之间的阀门,采用高压气体将经一级球磨处理后的料浆输送至二级球磨腔中,并使球磨原料、磨球与水的比例为1:7:1.4,磨球采用直径为8mm的钢球;e)二级球磨:以35rpm的转速顺时针处理100分钟,然后以30rpm转速逆时针处理100分钟;f)循环重复步骤e)中处理10小时;g)将经上述步骤处理后获得的料浆输送至料塔。此外,在步骤e)进行二级球磨的同时,一级球磨腔中加入新球磨原料同时进行一级球磨处理。实施例3一种双腔体两级球磨机,其包括筒体1、支架2与驱动机构3,筒体内设有两个椭球形球磨腔,分别为一级球磨腔4和二级球磨腔5,一级球磨腔与二级球磨腔相邻设置,一级球磨腔与二级球磨腔之间通过阀门6相连通;一级球磨腔的两条极半径与赤道半径的比例为2.3:2.3:1,二级球磨腔的两条极半径与赤道半径的比例为2.1:2.1:1;一级球磨腔与二级球磨腔内壁上设有若干均匀分布的凸块7,凸块的顶面设有圆弧形凹槽8;一级球磨腔中,凸块的宽度与球磨腔较长极半径的比例为1:40,凸块的高度与球磨腔较长的极半径的比例为1:30,凸块顶面的圆弧形凹槽的圆心角为85°;二级球磨腔中,凸块的宽度为与球磨腔较长极半径的比例为1:60,凸块的高度与球磨腔较长的极半径的比例为1:40,凸块顶面的圆弧形凹槽的圆心角为100°;凸块为条状,其由球磨腔极轴的一段延伸至另一端,一级球磨腔中设有12条凸块,二级球磨腔中设有8条凸块。一种通过双腔体两级球磨机实现的高效永磁铁氧体细粉碎方法,包含以下步骤,a)将球磨原料加入到一级球磨腔中,并加入磨球与水,球磨原料、磨球与水的比例为1:5:1.2;磨球采用直径为10mm的钢球;b)一级球磨:以30rpm的转速顺时针处理20分钟,然后以20rpm转速逆时针处理60分钟;c)循环重复步骤b)中处理8小时;d)打开一级球磨腔与二级球磨腔之间的阀门,采用高压气体将经一级球磨处理后的料浆输送至二级球磨腔中,并使球磨原料、磨球与水的比例为1:5:1.2,磨球采用直径为4mm的钢球;e)二级球磨:以30rpm的转速顺时针处理20分钟,然后以20rpm转速逆时针处理60分钟;f)循环重复步骤e)中处理8小时;g)将经上述步骤处理后获得的料浆输送至料塔。此外,在步骤e)进行二级球磨的同时,一级球磨腔中加入新球磨原料同时进行一级球磨处理。实施例4实施例4中除了永磁铁氧体球磨细粉碎时步骤c)和f)循环处理时间为9小时以外,其他如采用的设备、处理步骤、参数设置均与实施例3相同。实施例5实施例5中除了永磁铁氧体球磨细粉碎时步骤c)和f)循环处理时间为10小时以外,其他如采用的设备、处理步骤、参数设置均与实施例3相同。实施例6实施例6中除了,一级球磨腔中凸块顶面的圆弧形凹槽的圆心角为90°,二级球磨腔中凸块顶面的圆弧形凹槽的圆心角为120°,在一级球磨处理时采用重量比1:1的直径10mm和8mm钢球作为磨球,在二级球磨处理时采用重量比1:1的直径6mm和4mm钢球作为磨球外,其他如采用的设备、处理步骤、参数设置均与实施例3相同。实施例7实施例7中除了,二级球磨腔中凸块顶面的圆弧形凹槽的圆心角为120°,在二级球磨处理时采用重量比1:1的直径6mm和4mm钢球作为磨球外,其他如采用的设备、处理步骤、参数设置均与实施例3相同。实施例8实施例8中除了,二级球磨腔中凸块顶面的圆弧形凹槽的圆心角为120°,在二级球磨处理时采用重量比1:1的直径6mm和4mm钢球作为磨球外,其他如采用的设备、处理步骤、参数设置均与实施例5相同。对比例1采用本发明改进前的球磨机,以28转/分的转速匀速球磨,球磨19h,球磨原料、磨球与水的比例为1:5:1.2;磨球采用直径为10mm的钢球。对比例2采用本发明改进前的球磨机,以28转/分的转速匀速球磨,球磨21h,球磨原料、磨球与水的比例为1:5:1.2;磨球采用直径为10mm的钢球。对比例3采用本发明改进前的球磨机,以28转/分的转速匀速球磨,球磨19h,球磨原料、磨球与水的比例为1:5:1.2;采用重量比1:1的直径10mm和8mm钢球作为磨球。对比例4采用本发明改进前的球磨机,以28转/分的转速匀速球磨,球磨22h,球磨原料、磨球与水的比例为1:5:1.2;采用重量比1:1的直径10mm和8mm钢球作为磨球。对比例5采用本发明的球磨机,只用一级球磨腔以28转/分的转速匀速球磨,球磨22h,其余工艺按照实施例3进行控制。由上述实施例与对比例球磨后获得的浆料,取00g的料浆烘干后用激光粒度仪测试粒度分布曲线,其余料浆抽至料塔沉淀,料浆控制含水量在35%-40%后,用250t湿压磁瓦成型压机压制,所有实施例比较例的成型工艺、烧结工艺曲线、成型设备、烧结设备、均保持一致,烧结后的磁瓦由磁性材料测试设备23℃的恒温条件下测试磁性能,测试数据见表1。表1编号球磨时间(h)料浆d50(µm)毛坯成型时间(s)综合成品率%br(gs)hcb(oe)hcj(oe)bh(max)mgoe实施例1120.948094.04210364139004.31实施例2130.888593.04225365539504.35实施例3140.828992.04239368940104.39实施例4150.809590.24252371040794.46实施例5160.7910288.04260374041004.47实施例6160.769692.04280379942304.51比较例1160.839187.04230367539704.34比较例2190.7810883.04240360040604.36实施例7160.759695.04475407047904.99实施例8170.749994.04510410048805.01比较例3160.839088.04410386446234.82比较例4190.7810784.04445390047054.87比较例5190.7710190.04479399747864.99并针对实施例8和对比例2、5绘制其获得的粒径分布图,粒径分布图如图5所示。从图5粒径分布图和表1性能对比看,改进后的球磨机,采用相同批次的预烧料,球磨至相同粒径,具有更窄的粒径分布,球磨时间平均缩短3~5小时,成型时间缩短10%,成品率提高10%,剩磁提高1%~3%,内禀矫顽力提高3%~5%。应当理解的是,对于本领域普通技术人员来说,可以根据上述说明加以改进或变换,而所有这些改进和变换都应属于本发明所附权利要求的保护范围。当前第1页12