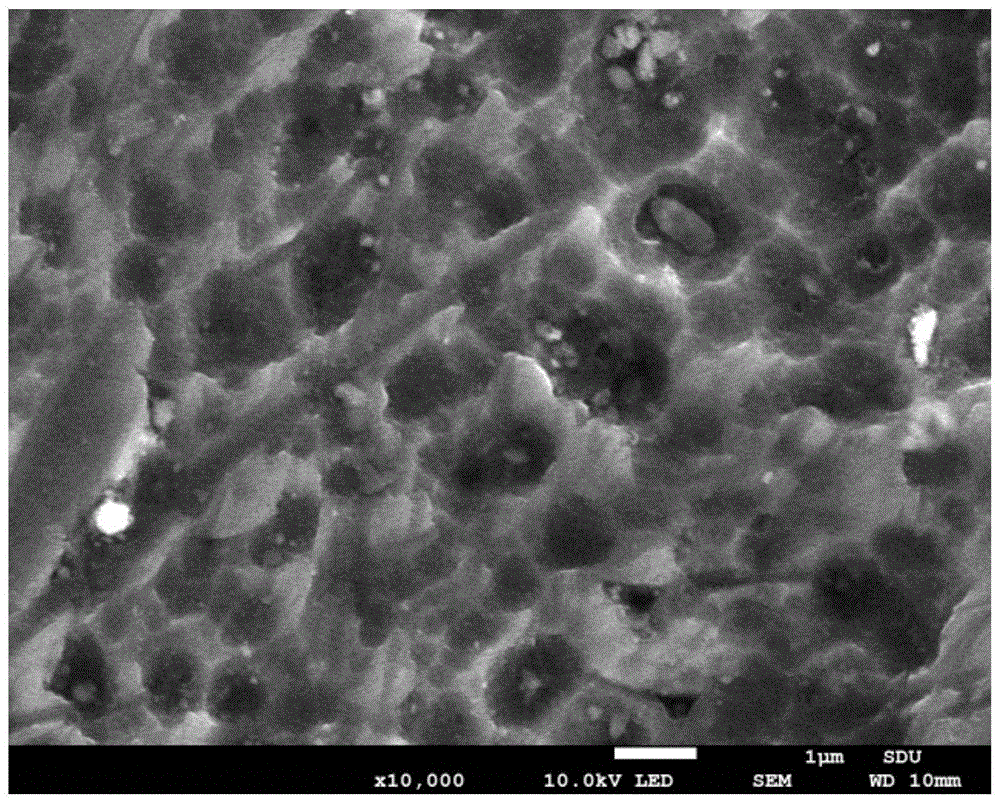
本发明属于材料表面涂层制造领域,具体涉及一种二硫化钼/氧化铝/石墨润滑减摩复合涂层及其制备方法。
背景技术:
:公开该
背景技术:
部分的信息仅仅旨在增加对本发明的总体背景的理解,而不必然被视为承认或以任何形式暗示该信息构成已经成为本领域一般技术人员所公知的现有技术。摩擦磨损在生产生活中消耗巨大的能量,据不完全统计,全球能源的三分之一到二分之一消耗于摩擦磨损,约80%的机器零件失效是由摩擦磨损引起的,因此,如何减小摩擦系数、减少磨损量对资源的节约起着至关重要的作用。随着航空工业、空间技术等不断发展,传统的润滑油和润滑脂已经无法满足苛刻的工作环境,因此,必须选用特殊的固体润滑剂来保证工件的正常工作。其中,二硫化钼作为应用最广泛的固体润滑材料之一,由于其特殊的层状六方晶系结构和层状结构的层间粘合弱的特点,使得二硫化钼在夹层之间非常容易滑动,从而具有了较低的摩擦系数和优异的固体润滑性能,因此,二硫化钼涂层已经广泛应用于航空、航天、建筑和汽车等工程领域。然而,单一的二硫化钼涂层也有着不可忽视的缺点,如硬度较低、导热性较差等,使其并不能完全满足复杂的工作环境,并且这些缺点成为制约二硫化钼涂层使用范围扩大的主要障碍。目前,氧化铝是一种高硬度的化合物,可显著提高涂料的耐高温性能,但γ-al2o3作为涂料填料时,涂覆性能很差,而纳米级的α-al2o3虽然可以有效地提升涂料的耐温性能,但由于成本较高,限制了其工业化应用。技术实现要素:为了克服上述问题,本发明提供了一种制备工艺简单、成本低廉、摩擦磨损性能良好的二硫化钼/氧化铝/石墨润滑减摩复合涂层,该复合涂层以二硫化钼和鳞片状胶体石墨为润滑剂,球形氧化铝为硬质颗粒,环氧树脂/聚酰胺树脂/聚四氟乙烯为胶黏剂,相较于未掺杂氧化铝的涂层,本发明的复合涂层的摩擦系数大约降低40%,显微硬度可达80.4hv0.2。为实现上述技术目的,本发明采用的技术方案如下:一种二硫化钼/氧化铝/石墨润滑减摩复合涂层,所述复合涂层由二硫化钼、鳞片状胶体石墨、球形氧化铝和胶黏剂组成。需要指出的是:本申请中若未作特别说明,则“复合涂层”是指:“二硫化钼/氧化铝/石墨润滑减摩复合涂层”。针对目前单一的二硫化钼涂层硬度较低、导热性较差的问题,本发明公开了一种二硫化钼/氧化铝/石墨润滑减摩复合涂层,利用球形氧化铝和鳞片状胶体石墨掺杂改性二硫化钼涂料,然后通过测试不同质量比对复合涂层的表面形貌、摩擦磨损性能的影响,确定最佳配比,最终找到一个最佳方案克服了二硫化钼导热性差、硬度低等缺点,同时,提高了复合涂层的综合性能。相较于其他涂层,本发明的复合涂层生产工艺简便、成本较低、产品摩擦磨损性能较好,非常适合工厂生产环境。研究发现:二硫化钼含量过多时,由于摩擦生热的作用,二硫化钼在温度较高时,氧化作用明显,使复合涂层摩擦系数变大,影响了润滑效果;鳞片状胶体石墨过多,复合涂层的耐磨性较差,容易脱落,起不到持久的减摩润滑效果。球形氧化铝的添加量过多,复合涂层的柔韧性和耐冲击性能会出现明显下滑。因此,在一些实施例中,所述二硫化钼、鳞片状胶体石墨、球形氧化铝的质量比为6~8:1~3:1~3,有效地提高了复合涂层的综合性能,特别是摩擦磨损性能和硬度。研究发现:与普通的微米级氧化铝相比,球形氧化铝的比表面积大,易游离于涂层表面,容易脱落。为此,本发明采用鳞片状胶体石墨与其复配,利用鳞片状胶体石墨的粘稠性,有效地改善了二硫化钼/氧化铝/石墨润滑减摩复合涂层的附着力。因此,在一些实施例中,所述球形氧化铝的直径为1~10μm。在一些实施例中,所述球形氧化铝的直径为3~6μm。研究发现:石墨和二硫化钼由于其特殊的晶体结构,都具有相对宽的分子层间距,很容易在层间发生相对滑动,在金属表面形成膜层后,能够隔绝金属之间的磨损,而鳞片状胶体石墨与球形氧化铝复配后,利用鳞片状胶体石墨的粘稠性可以更好地促进球形石墨在润滑剂和胶黏剂中发生自转与滑动,提高复合涂层的摩擦磨损性能。因此,在一些实施例中,所述石墨为鳞片状胶体石墨,直径为1~10μm。在一些实施例中,所述鳞片状胶体石墨的粒径为1~3μm。在一些实施例中,所述胶黏剂为环氧树脂、聚酰胺树脂或者聚四氟乙烯,胶黏剂的作用除了包覆填料以外,还可提高复合涂层的耐磨性和导热性,及整体的润滑、防粘效果。在一些实施例中,所述复合涂层厚度为15~25μm。本发明还提供了一种二硫化钼/氧化铝/石墨润滑减摩复合涂层的制备方法,包括:对基片进行磷化处理,形成磷化膜;将球形氧化铝、鳞片状胶体石墨掺杂到二硫化钼润滑涂料,混合均匀,得复合涂料;将上述的形成有磷化膜的基片预热处理,然后采用空气喷涂法将复合涂料喷涂到预热好的基片表面,得到涂层;将上述得到的涂层在40~80℃下,干燥20~40min,然后在160~200℃固化,得到表面形貌良好的二硫化钼/氧化铝/石墨润滑减摩复合涂层。上述干燥过程的增加极大地保证了复合涂层具有良好的宏观表面形貌,若缺少干燥过程,直接将制备好的复合涂层置于160~200℃条件下固化,复合涂层中的有机溶剂会快速挥发,导致复合涂层的表面形貌较差,降低了其耐磨性和硬度。本发明还提供了任一上述的复合涂层在电子、食品、医药以及空间机械领域的应用。本发明的有益效果在于:(1)本发明所述的二硫化钼/氧化铝/石墨润滑减摩复合涂层,将三种物质复合,在保证润滑性的基础上,最大限度提高复合涂层的耐磨性。采用二硫化钼作为润滑剂,由于其特殊的层状六方晶系结构,以及层状结构层间粘合弱的特点,使其在夹层中非常容易滑动,具有低摩擦系数和优异的固体润滑性能。采用鳞片状胶体石墨作为润滑剂,鳞片状胶体石墨更容易分散于有机溶剂中,并且石墨导热性、润滑性较好,既能够进一步降低复合涂层的摩擦系数,又能改善二硫化钼导热性较差的缺点。采用球形氧化铝作为硬质颗粒,球形相较于不规则形状,在摩擦过程中可以大大降低摩擦系数,球形氧化铝在润滑剂和胶黏剂中发生自转与滑动,可以很好地提高复合涂层的摩擦磨损性能和硬度。(2)本发明所述材料制备方法中,采用磷化处理增加复合涂层与基片的结合面积,进而提高了复合涂层与基片的结合力。在复合涂层制备过程中增加了干燥过程,干燥温度为40~80℃,优选为40~60℃,干燥时间为20~40min,优选为20~30min,干燥过程的增加极大地保证了复合涂层具有良好的宏观表面形貌,若缺少干燥过程,直接将制备好的复合涂层置于160~200℃条件下固化,复合涂层中的有机溶剂会快速挥发,导致复合涂层的表面形貌较差。(3)本发明的操作方法简单、成本低、具有普适性,易于规模化生产。附图说明构成本发明的一部分的说明书附图用来提供对本发明的进一步理解,本发明的示意性实施例及其说明用于解释本发明,并不构成对本发明的不当限定。图1为实施例1的步骤(1)制得的磷化膜的扫描电镜图,由图1可以看出磷化膜为多孔状,孔的分布较为均匀。图2为实施例1的步骤(2)掺杂的氧化铝的扫描电镜图,由图2可以看出氧化铝为球形,直径多分布于4~6μm。图3为实施例1的步骤(4)制得的复合涂层的扫描电镜图,由图3可以看出复合涂层表面形貌良好。图4为实施例1的复合涂层的摩擦系数曲线图,a为普通微米级氧化铝掺杂摩擦系数曲线图,b为二硫化钼摩擦系数曲线图,c为球形氧化铝掺杂摩擦系数曲线图,由图4可以看出相较于普通氧化铝,球形氧化铝摩擦系数更低且更稳定,相较于未掺杂的涂层,复合涂层的摩擦系数大约降低40%。具体实施方式应该指出,以下详细说明都是例示性的,旨在对本发明提供进一步的说明。除非另有指明,本发明使用的所有技术和科学术语具有与本发明所属
技术领域:
的普通技术人员通常理解的相同含义。需要注意的是,这里所使用的术语仅是为了描述具体实施方式,而非意图限制根据本发明的示例性实施方式。如在这里所使用的,除非上下文另外明确指出,否则单数形式也意图包括复数形式,此外,还应当理解的是,当在本说明书中使用术语“包含”和/或“包括”时,其指明存在特征、步骤、操作、器件、组件和/或它们的组合。正如
背景技术:
所介绍的,针对目前单一的二硫化钼涂层存在硬度较低、导热性较差等缺点,使其并不能完全满足复杂的工作环境的问题。因此,本发明提出一种二硫化钼/氧化铝/石墨润滑减摩复合涂层的制备方法,首先进行基片表面预处理制备多孔磷化膜,经预热处理后,通过空气喷涂工艺制备复合涂层,最后通过干燥固化处理后得到表面形貌良好的二硫化钼/氧化铝/石墨润滑减摩复合涂层。本发明的创新点在于:掺杂氧化铝与石墨的选择。普通的微米级氧化铝也可以作为硬质颗粒进行复合涂层的掺杂,但发明人发现:普通的微米级氧化铝棱角明显,在摩擦磨损过程中,大大增加了复合涂层的摩擦系数,难以达到润滑的效果,而普通的石墨由于在有机溶剂中分散性不好,制备得到的复合涂层中石墨极易发生团聚现象,复合涂层成分不均匀,部分区域由于石墨的团聚导致硬度极低。发明人经过不断摸索,找到球形氧化铝和鳞片状胶体石墨作为掺杂物,球形氧化铝粒径为10μm以下,优选为3~6μm,相比于普通的微米级氧化铝,球形氧化铝在保证摩擦系数较低的同时,能够极大地增加复合涂层的耐磨性,鳞片状胶体石墨粒径为10μm以下,优选1~3μm,鳞片状胶体石墨可以很好地分散在有机溶剂中,保证了复合涂层成分的均匀性。本发明的难点在于掺杂二硫化钼、球形氧化铝与鳞片状胶体石墨的质量掺杂比。找到球形氧化铝与鳞片状胶体石墨作为掺杂物后,质量掺杂比成为本发明的最大难点,二硫化钼作为目前最优的固体润滑剂,质量占比应该保证一定的比例,球形氧化铝掺杂过多则会导致复合涂层润滑性不好,鳞片状胶体石墨掺杂过多则会导致复合涂层变软,极易破坏。发明人经过不断实验测试,发现了三者最优的掺杂质量比范围,二硫化钼、球形氧化铝与鳞片状胶体石墨的掺杂质量比范围为6~8:1~3:1~3,优选范围为6:2:1~3,例如6:2:1、6:2:2或者6:2:3。具体地,本发明提供了一种二硫化钼/氧化铝/石墨润滑减摩复合涂层的制备方法,该方法包括以下步骤:步骤1:将基片通过打磨、除锈、除油处理,得到表面平整、无锈、无油的基体,然后将基片进行磷化处理,表面形成连续的、多孔的磷化膜。步骤2:将一定质量的氧化铝、鳞片状胶体石墨掺杂到zby801二硫化钼润滑涂料,并用磁力搅拌器搅拌,得到混合均匀的复合涂料。步骤3:将步骤1得到的基片预热处理,然后利用空气喷涂工艺,将步骤2配置好的涂料喷涂到预热好的基片表面,得到均匀的涂层。步骤4:将步骤3得到的复合涂层放入烘箱中干燥,然后转移到马弗炉中固化,得到表面形貌良好的二硫化钼/氧化铝/石墨润滑减摩复合涂层。进一步的,所述步骤1中打磨基片的金相砂纸依次为400目、500目、600目,每种金相砂纸打磨50次左右,每次更换砂纸基片转动90度。任选的,所述步骤1中除锈采用硝酸酒精溶液,体积分数为4%。任选的,所述步骤1中除油采用丙酮酒精溶液,体积分数为4%。任选的,所述步骤1中磷化液采用锌系磷化剂,将磷化剂与去离子水1:7(体积比)配比配置成磷化剂溶液,超声分散3min。任选的,所述步骤1中基片磷化在室温中进行,磷化时间为10~20min,固化温度为130~180℃,优选150~180℃,固化时间为15~30min。任选的,所述步骤2中氧化铝为球形氧化铝,直径为10μm以下,优选3~6μm,石墨为鳞片状胶体石墨,直径为10μm以下,优选1~3μm。任选的,所述步骤2中二硫化钼、球形氧化铝与鳞片状胶体石墨的质量比为6~8:1~3:1~3,优选为6:2:1~3。任选的,所述步骤2中搅拌温度为室温,搅拌时间为5~20min,优选15~20min。任选的,所述步骤3中基片预热的温度为50~100℃,优选50~80℃;预热时间为20~60min,优选40~60min。任选的,所述步骤3中空气喷涂工艺气压为0.7mpa。任选的,所述步骤3中喷枪距基片15~30cm,优选为15~20cm,倾斜角度40~80°,优选为40~60°,往复次数为2次。任选的,所述步骤4中干燥温度为40~80℃,优选为40~60℃,干燥时间为20~40min,优选为20~30min。任选的,所述步骤4中固化温度为160~200℃,优选为180~200℃,干燥时间为30~60min,优选为50~60min。实施例中未注明具体技术或条件者,按照本领域内的文献所描述的技术或条件或者按照产品说明书进行。所用试剂或仪器未注明生产厂商者,均为可以通过市购获得的常规产品。在下面的实施例中,如未明确说明,“%”均指重量百分比。以下使用的测试方法包括:使用由日本电子生产的jsm-7800f热场发射扫描电镜来表征样品的表面形貌。实验中采用的加速电压为5kv和25kv,放大倍数100~5000倍。使用由兰州中科凯华科技开发有限公司生产的ht-1000高温摩擦磨损试验机来表征复合涂层的摩擦磨损性能。实验中采用的摩擦副为球-盘摩擦副,摩擦副材料为sin3,直径为6mm,载荷为5n,摩擦直径8mm,转速为560rpm,摩擦时长选择10min。复合涂层制备方法:称取15gzby801二硫化钼润滑涂料置于烧杯中,将烧杯在磁力搅拌器上进行搅拌,称取1g球形氧化铝、1g鳞片状胶体石墨,将球形氧化铝、鳞片状胶体石墨加入到正在搅拌的二硫化钼涂料中,继续搅拌15min,直到烧杯中无明显团聚球状物质。将配置好的复合涂料加入到喷枪中,在0.7mpa气压下,进行空气喷涂。将制备好的涂层置于60℃条件下干燥30min,然后转移至180℃条件下固化60min,待降至室温后封装。以下实施例中采用的锌系磷化剂为gy-601锌系磷化剂,厂商为:广东高远金属处理材料科技有限公司。zby801二硫化钼润滑涂料为市售产品,购自在邦润滑材料(上海)有限公司。实施例1按照以下步骤制备二硫化钼/氧化铝/石墨润滑减摩复合涂层:(1)基片预处理取一块切好的19*19*8mmht250基片,将基片依次在400目、500目、600目的金相砂纸打磨,每种金相砂纸打磨50次左右,每次更换砂纸基片转动90度。量取48ml乙醇溶液于100ml烧杯中,向烧杯中加入2ml硝酸溶液,在室温下超声分散5min,得到溶液a;量取48ml乙醇溶液于100ml烧杯中,向烧杯中加入2ml丙酮溶液,在室温下超声分散5min,得到溶液b;取100ml去离子水于150ml烧杯中,向烧杯中加入10ml锌系磷化剂溶液,在室温下超声分散5min,得到溶液c。取适量无水乙醇于100ml烧杯中,将基片置于烧杯中,在室温下超声清洗2min,然后将基片置于溶液a中超声清洗30s,再次取适量无水乙醇于100ml烧杯中,在室温下将基片超声清洗2min,然后将基片置于溶液b中超声清洗90s,最后取适量无水乙醇于100ml烧杯中,在室温下将基片超声清洗2min,并用吹风机将基片吹干。将清洗完毕的基片置于溶液c中,磷化15min,然后将基片取出在去离子水中钝化90s,钝化后的基片置于150℃的烘箱中,烘干30min,得到附着有磷化膜的基片。(2)复合涂层的制备称取13.8gzby801二硫化钼润滑涂料于50ml烧杯中,将烧杯放在磁力搅拌器上进行搅拌;称取0.92g球形氧化铝,将称好的球形氧化铝粉末缓慢加入到盛有二硫化钼涂料的烧杯中,边搅拌边加入;然后称取0.92g鳞片状胶体石墨,将称好的鳞片状胶体石墨加入到二硫化钼、球形氧化铝复合涂料中,边搅拌边加入;继续搅拌15min,得复合涂料。将步骤(1)预处理好的基片在60℃条件下预热60min,同时将配置好的复合涂料加入到喷枪中,保持气压在0.7mpa,将预热好的基片水平放置,喷枪距基片15cm,倾斜角度45°,往复次数为2次。涂层制备完成后,将基片置于烘箱中,温度为60℃,干燥30min,然后转移至马弗炉中固化,固化温度为180℃,固化时间为60min,待降至室温后,得到二硫化钼/氧化铝/石墨润滑减摩复合涂层。图1为步骤(1)制得的磷化膜的扫描电镜图,由图1可以看出磷化膜为多孔状,孔的分布较为均匀。图2为步骤(2)掺杂的氧化铝的扫描电镜图,由图2可以看出氧化铝为球形,直径多分布于4~6μm。图3为步骤(4)制得的复合涂层的扫描电镜图,由图3可以看出复合涂层表面形貌良好。图4为复合涂层的摩擦系数曲线图,a为普通微米级氧化铝掺杂摩擦系数曲线图,b为二硫化钼摩擦系数曲线图,c为球形氧化铝掺杂摩擦系数曲线图,由图4可以看出相较于未掺杂的涂层,复合涂层的摩擦系数大约降低40%,相较于普通氧化铝,球形氧化铝摩擦系数更低且更稳定。实施例2按照以下步骤制备二硫化钼/氧化铝/石墨润滑减摩复合涂层:(1)基片预处理取一块切好的19*19*8ht250基片,将基片依次在400目、500目、600目的金相砂纸打磨,每种金相砂纸打磨50次左右,每次更换砂纸基片转动90度。量取48ml乙醇溶液于100ml烧杯中,向烧杯中加入2ml硝酸溶液,在室温下超声分散5min,得到溶液a;量取48ml乙醇溶液于100ml烧杯中,向烧杯中加入2ml丙酮溶液,在室温下超声分散5min,得到溶液b;取100ml去离子水于150ml烧杯中,向烧杯中加入10ml锌系磷化剂溶液,在室温下超声分散5min,得到溶液c。取适量无水乙醇于100ml烧杯中,将基片置于烧杯中,在室温下超声清洗2min,然后将基片置于溶液a中超声清洗30s,再次取适量无水乙醇于100ml烧杯中,在室温下将基片超声清洗2min,然后将基片置于溶液b中超声清洗90s,最后取适量无水乙醇于100ml烧杯中,在室温下将基片超声清洗2min,并用吹风机将基片吹干。将清洗完毕的基片置于溶液c中,磷化15min,然后将基片取出在去离子水中钝化90s,钝化后的基片置于150℃的烘箱中,烘干30min,得到附着有磷化膜的基片。(2)复合涂层的制备称取12.9gzby801二硫化钼润滑涂料于50ml烧杯中,将烧杯放在磁力搅拌器上进行搅拌;称取0.86g球形氧化铝,将称好的球形氧化铝粉末缓慢加入到盛有二硫化钼涂料的烧杯中,边搅拌边加入;然后称取0.43g鳞片状胶体石墨,将称好的鳞片状胶体石墨加入到二硫化钼、球形氧化铝复合涂料中,边搅拌边加入;继续搅拌15min,得复合涂料。将步骤(1)预处理好的基片在60℃条件下预热60min,同时将配置好的复合涂料加入到喷枪中,保持气压在0.7mpa,将预热好的基片水平放置,喷枪距基片15cm,倾斜角度45°,往复次数为2次。涂层制备完成后,将基片置于烘箱中,温度为60℃,干燥30min,然后转移至马弗炉中固化,固化温度为180℃,固化时间为60min,待降至室温后,得到二硫化钼/氧化铝/石墨润滑减摩复合涂层。实施例3按照以下步骤制备二硫化钼/氧化铝/石墨润滑减摩复合涂层:(1)基片预处理取一块切好的19*19*8ht250基片,将基片依次在400目、500目、600目的金相砂纸打磨,每种金相砂纸打磨50次左右,每次更换砂纸基片转动90度。量取48ml乙醇溶液于100ml烧杯中,向烧杯中加入2ml硝酸溶液,在室温下超声分散5min,得到溶液a;量取48ml乙醇溶液于100ml烧杯中,向烧杯中加入2ml丙酮溶液,在室温下超声分散5min,得到溶液b;取100ml去离子水于150ml烧杯中,向烧杯中加入10ml锌系磷化剂溶液,在室温下超声分散5min,得到溶液c。取适量无水乙醇于100ml烧杯中,将基片置于烧杯中,在室温下超声清洗2min,然后将基片置于溶液a中超声清洗30s,再次取适量无水乙醇于100ml烧杯中,在室温下将基片超声清洗2min,然后将基片置于溶液b中超声清洗90s,最后取适量无水乙醇于100ml烧杯中,在室温下将基片超声清洗2min,并用吹风机将基片吹干。将清洗完毕的基片置于溶液c中,磷化15min,然后将基片取出在去离子水中钝化90s,钝化后的基片置于150℃的烘箱中,烘干30min,得到附着有磷化膜的基片。(2)复合涂层的制备称取13.2gzby801二硫化钼润滑涂料于50ml烧杯中,将烧杯放在磁力搅拌器上进行搅拌;称取0.88g球形氧化铝,将称好的球形氧化铝粉末缓慢加入到盛有二硫化钼涂料的烧杯中,边搅拌边加入;然后称取1.3g鳞片状胶体石墨,将称好的鳞片状胶体石墨加入到二硫化钼、球形氧化铝复合涂料中,边搅拌边加入;继续搅拌15min,得复合涂料。将步骤(1)预处理好的基片在60℃条件下预热60min,同时将配置好的复合涂料加入到喷枪中,保持气压在0.7mpa,将预热好的基片水平放置,喷枪距基片15cm,倾斜角度45°,往复次数为2次。涂层制备完成后,将基片置于烘箱中,温度为60℃,干燥30min,然后转移至马弗炉中固化,固化温度为180℃,固化时间为60min,待降至室温后,得到二硫化钼/氧化铝/石墨润滑减摩复合涂层。对比例1涂层的制备方法与实施例1完全相同,不同之处在于,采用普通微米级氧化铝替代球形氧化铝。表1为附着力等级测试标准为:色漆和清漆寂寞的划痕实验gbt9286-1998;涂层结合力iso等级均为最优等级。显微硬度采用200g,加载15s测得数据,可以看出球形氧化铝的加入大大提升了复合涂层的硬度。表1实施例附着力iso等级(级)显微硬度(hv0.2)实施例1075.6实施例2080.4实施例3050.6二硫化钼030.3最后应该说明的是,以上所述仅为本发明的优选实施例而已,并不用于限制本发明,尽管参照前述实施例对本发明进行了详细的说明,对于本领域的技术人员来说,其依然可以对前述实施例所记载的技术方案进行修改,或者对其中部分进行等同替换。凡在本发明的精神和原则之内,所作的任何修改、等同替换、改进等,均应包含在本发明的保护范围之内。上述虽然结合附图对本发明的具体实施方式进行了描述,但并非对本发明保护范围的限制,所属领域技术人员应该明白,在本发明的技术方案的基础上,本领域技术人员不需要付出创造性劳动即可做出的各种修改或变形仍在本发明的保护范围以内。当前第1页12