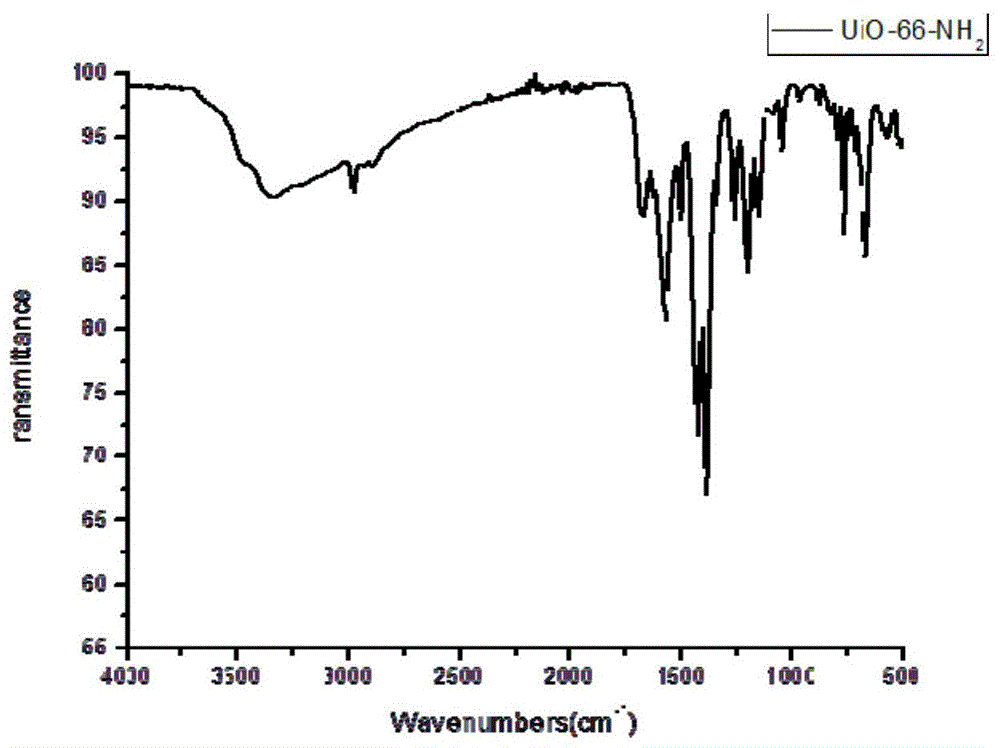
本发明涉及催化剂
技术领域:
,尤其涉及一种用于合成磺酸酯的催化剂cubr2@uio-66-nh2-cf3cooh及其制备方法与应用。
背景技术:
:本发明
背景技术:
中公开的信息仅仅旨在增加对本发明的总体背景的理解,而不必然被视为承认或以任何形式暗示该信息构成已经成为本领域一般技术人员所公知的现有技术。金属有机框架(mofs)是由有机配体和无机金属离子或者团簇通过配位键自组装形成的具有分子内孔隙的有机-无机杂化材料。mofs能控制孔的结构并且比表面积大,因此比其它的多孔材料有更广泛的应用前景,如吸附分离、催化、磁性材料和光学材料等。uio-66-nh2则是mofs中的一种,它是以zr4+为金属离子并且以2-氨基对苯二甲酸为配体合成得到的mof,它具有较好的热稳定性和化学稳定性。因此,uio-66-nh2作为晶态多孔材料在催化方面的应用存在很大的优势。磺酸酯是许多药物和其他生物活性化合物中常见的片段。例如,磺酸酯类药物可以预防或治疗不希望的血栓形成或作为一种新的细菌胸苷酸合成酶抑制剂。传统的磺酸酯合成方法是在碱存在下的磺酰氯的酯化反应,这需要制备有害的磺酰氯。科学家们也在不断地研究新的更“绿色”合成方法:溴化铜在三氟乙酸的辅助下均相催化磺酸酯类药物合成,相比较前边的合成方法有了很大的进步。尽管如此,但发明人发现目前的溴化铜催化剂在合成磺酸酯的过程中仍存在以下问题:(1)溴化铜作为金属盐催化后排放,造成环境的污染;(2)三氟乙酸作为辅助催化剂也不能回收,造成浪费;(3)催化剂体系不能循环使用,利用率降低。技术实现要素:针对上述存在的问题,本发明旨在提供一种催化剂cubr2@uio-66-nh2-cf3cooh及其制备方法与应用。经试验验证,本发明提出的催化剂cubr2@uio-66-nh2-cf3cooh利用率高,反应条件温和,绿色环保,能够有效降低催化成本,具有良好的应用价值。本发明第一目的:提供一种催化剂cubr2@uio-66-nh2-cf3cooh。本发明第二目的:提供一种催化剂cubr2@uio-66-nh2-cf3cooh的制备方法。本发明第三目的:提供所述催化剂cubr2@uio-66-nh2-cf3cooh的应用。为实现上述发明目的,本发明公开了下述技术方案:首先,本发明公开一种催化剂cubr2@uio-66-nh2-cf3cooh,其由cubr2、uio-66-nh2和cf3cooh组成,其中,所述cf3cooh配位在uio-66-nh2中的金属锆簇节点上,所述cubr2负载在uio-66-nh2上。作为进一步的技术方案,所述cubr2、uio-66-nh2、cf3cooh的比例为:1-2:1:6。作为进一步的技术方案,所述cubr2@uio-66-nh2-cf3cooh的粒径为:100-500nm。本发明催化剂cubr2@uio-66-nh2-cf3cooh的特点是:cubr2、uio-66-nh2和cf3cooh通过物理吸附和化学配位的方式有机地结合在一起,相对于单独地添加溴化铜及其辅助催化剂三氟乙酸,操作简单,并实现了均相催化到异相催化的转变,从而催化剂回收利用简单易行。其次,本发明公开一种催化剂cubr2@uio-66-nh2-cf3cooh的制备方法,包括如下步骤:(1)合成uio-66-nh2-cf3cooh:将uio-66-nh2置于cf3cooh的水溶液中进行浸泡处理,完成后对反应液进行分离,将得到的固体产物进行洗涤,干燥后即得uio-66-nh2-cf3cooh;(2)合成cubr2@uio-66-nh2-cf3cooh:将步骤(1)的uio-66-nh2-cf3cooh,置于溴化铜溶液中浸泡,完成后对反应液进行分离,将得到的固体产物进行洗涤,干燥后即得cubr2@uio-66-nh2-cf3cooh。本发明合成cubr2@uio-66-nh2-cf3cooh的原理如下:作为进一步的技术方案,步骤(1)中,所述uio-66-nh2可直接采用现有产品,或者采用的方法合成,本发明提供一种具体的合成方法,包括:称取zrcl4和ch3cooh溶于dmf溶液中,超声分散,待溶液澄清后,加入2-氨基对苯二甲酸,再超声分散,将溶液转移到密闭高压釜中进行反应,反应结束后,离心分离、洗涤、干燥,得到uio-66-nh2。作为进一步的技术方案,所述反应的温度为110-135℃,反应时间为22-26h,优选为24h。作为进一步的技术方案,所述zrcl4、ch3cooh和2-氨基对苯二甲酸的摩尔比为1:(14-17):1。作为进一步的技术方案,步骤(1)中,所述cf3cooh的水溶液的浓度为5-7mol/l。作为进一步的技术方案,步骤(2)中,所述溴化铜溶液浓度为3-6mg/ml。作为进一步的技术方案,步骤(2)中,所述溴化铜溶液为溴化铜的乙醇/甲醇/乙腈等溶液。作为进一步的技术方案,所述uio-66-nh2-cf3cooh与乙醇/甲醇/乙腈的质量体积比为(8-12)mg:8ml。作为进一步的技术方案,步骤(1)和(2)中,所述洗涤为用水或乙醇进行洗涤,必要时可以进行多次洗涤,以更好地去除固体产物中残留的反应液。作为进一步的技术方案,步骤(1)和(2)中,所述干燥处理的条件为:处理温度为60-90℃,处理时间为8-16小时;进一步优选为:处理温度为80℃,处理时间为12小时。最后,本发明公开所述cubr2@uio-66-nh2-cf3cooh在催化磺酸酯合成反应中的应用。作为进一步的技术方案,所述应用的具体方法为:将对硝基苯四氟硼酸重氮盐、dabso、甲醇、二氯甲烷和cubr2@uio-66-nh2-cf3cooh混合均匀后进行反应,即得对硝基苯磺酸甲酯。作为进一步的技术方案,所述反应温度为25-29℃,即采用本发明的cubr2@uio-66-nh2-cf3cooh作为磺酸酯合成的催化剂时,既不需要额外的辅助催化剂,而且反应温度温和,不需要加热再消耗额外的能源,也不用担心因高温反应带来的一系列危险,并且容易控制。作为进一步的技术方案,所述对硝基苯四氟硼酸重氮盐、dabso、甲醇和cubr2@uio-66-nh2-cf3cooh的摩尔比依次序为1:1:245:0.002。所述二氯甲烷是作为常规溶剂,可根据需要进行添加。本发明催化剂cubr2@uio-66-nh2-cf3cooh催化磺酸酯合成反应的原理如下:与现有技术相比,本发明取得了以下有益效果:(1)本发明提供的催化剂代替了一些过渡金属应用,减少了环境污染。(2)采用本发明的催化剂进行催化,不需要用过渡金属盐做催化剂,实现了异相催化,催化剂易于通过简单地过滤或离心分离回收,减少催化剂带来的污染,同时可以重复利用五次以上,并且催化剂回收容易,提高了催化剂的利用率,降低了成本。(3)本发明的反应温度温和,催化剂用量少,不需要额外的辅助催化剂。附图说明构成本发明的一部分的说明书附图用来提供对本发明的进一步理解,本发明的示意性实施例及其说明用于解释本发明,并不构成对本发明的不当限定。图1是本发明实施例1制备的uio-66-nh2的红外谱图。图2是本发明实施例2制备的uio-66-nh2-cf3cooh的红外谱图。图3是本发明实施例2制备的uio-66-nh2-cf3cooh的sem图。图4是本发明实施例3制备的cubr2@uio-66-nh2-cf3cooh的红外谱图。图5是本发明实施例3制备的cubr2@uio-66-nh2-cf3cooh的sem图。图6是本发明实施例3制备的cubr2@uio-66-nh2-cf3cooh在催化磺酸酯合成反应后的对应pxrd谱图。具体实施方式应该指出,以下详细说明都是例示性的,旨在对本发明提供进一步的说明。除非另有指明,本文使用的所有技术和科学术语具有与本发明所属
技术领域:
的普通技术人员通常理解的相同含义。需要注意的是,这里所使用的术语仅是为了描述具体实施方式,而非意图限制根据本发明的示例性实施方式。如,在这里所使用的,除非上下文另外明确指出,否则单数形式也意图包括复数形式,此外,还应当理解的是,当在本说明书中使用术语“包含”和/或“包括”时,其指明存在特征、步骤、操作、器件、组件和/或它们的组合。正如前文所述,目前的溴化铜催化剂在合成磺酸酯的过程中仍存溴化铜作为金属盐催化后排放,造成环境的污染;三氟乙酸作为辅助催化剂也不能回收,造成浪费;催化剂体系不能循环使用,利用率降低等一系列问题。因此,本发明提出种用于合成磺酸酯的催化剂cubr2@uio-66-nh2-cf3cooh及其制备方法;现结合附图和具体实施方式对本发明进一步进行说明。实施例1uio-66-nh2的制备,包括如下步骤:(1)将zrcl4(139mg,0.6mmol)和ch3cooh(538μl,9.4mmol)溶于15mldmf溶液中,超声分散30min,待溶液澄清后,加入2-氨基对苯二甲酸(108mg,0.6mmol),再超声分散10min;(2)将步骤(1)中超声分散后得到的溶液转移到高压釜中,在120℃加热24小时,完成后对反应液进行分离,将得到的固体产物用乙醇洗涤三次,然后在80℃干燥12h,得到uio-66-nh295.0mg,产率89.7%。实施例2uio-66-nh2-cf3cooh的合成,包括如下步骤:取实施例1制备的uio-66-nh220.0mg,置于10ml浓度为6mol/l的cf3cooh水溶液中搅拌12小时后,完成后对反应液进行分离,将得到的固体产物用乙醇洗涤三次,然后在80℃干燥12h,得到uio-66-nh2-cf3cooh。实施例3催化剂cubr2@uio-66-nh2-cf3cooh的制备,包括如下步骤:取10mg实施例2制备的uio-66-nh2-cf3cooh,加入含有溴化铜的8ml乙醇溶液(浓度为5mg/ml),搅拌成均匀的浊液,浸泡12小时,离心分离即得cubr2@uio-66-nh2-cf3cooh。实施例4一种催化剂cubr2@uio-66-nh2-cf3cooh的制备方法,包括如下步骤:1、uio-66-nh2的制备,包括如下步骤:(1)将zrcl4(1mmol)和ch3cooh(14mmol)溶于15mldmf溶液中,超声分散30min,待溶液澄清后,加入2-氨基对苯二甲酸(1mmol),再超声分散10min;(2)将步骤(1)中超声分散后得到的溶液转移到高压釜中,在110℃加热26小时,完成后对反应液进行分离,将得到的固体产物用乙醇洗涤三次,然后在80℃干燥12h,得到uio-66-nh2。2、uio-66-nh2-cf3cooh的合成,包括如下步骤:取实施例1制备的uio-66-nh220.0mg,置于10ml浓度为5mol/l的cf3cooh水溶液中搅拌12小时后,完成后对反应液进行分离,将得到的固体产物用乙醇洗涤三次,然后在60℃干燥16h,得到uio-66-nh2-cf3cooh。3、催化剂cubr2@uio-66-nh2-cf3cooh的制备,包括如下步骤:取8mg实施例2制备的uio-66-nh2-cf3cooh加入含有溴化铜的8ml乙醇溶液(浓度为6mg/ml),搅拌成均匀的浊液,浸泡12小时,离心分离即得cubr2@uio-66-nh2-cf3cooh。实施例5一种催化剂cubr2@uio-66-nh2-cf3cooh的制备方法,包括如下步骤:1、uio-66-nh2的制备,包括如下步骤:(1)将zrcl4(1mmol)和ch3cooh(17mmol)溶于15mldmf溶液中,超声分散30min,待溶液澄清后,加入2-氨基对苯二甲酸(1mmol),再超声分散10min;(2)将步骤(1)中超声分散后得到的溶液转移到高压釜中,在135℃加热22小时,完成后对反应液进行分离,将得到的固体产物用乙醇洗涤三次,然后在80℃干燥12h,得到uio-66-nh2。2、uio-66-nh2-cf3cooh的合成,包括如下步骤:取实施例1制备的uio-66-nh220.0mg,置于10ml浓度为7mol/l的cf3cooh水溶液中搅拌12小时后,完成后对反应液进行分离,将得到的固体产物用乙醇洗涤三次,然后在90℃干燥8h,得到uio-66-nh2-cf3cooh。3、催化剂cubr2@uio-66-nh2-cf3cooh的制备,包括如下步骤:取12mg实施例2制备的uio-66-nh2-cf3cooh加入含有溴化铜的8ml乙醇溶液(浓度为3mg/ml),搅拌成均匀的浊液,浸泡12小时,离心分离即得cubr2@uio-66-nh2-cf3cooh。性能表征和测试:(1)对实施例1制备的uio-66-nh2进行表征,ir如图1所示。从图中可以看出:uio-66-nh2上金属锆簇配位羧酸的峰位值1550cm-1和3450cm-1附近。(2)通过ir和sem对实施例2制备的uio-66-nh2-cf3cooh进行表征,结果分别见图2、3。从图中可以看出:uio-66-nh2-cf3cooh上金属锆簇配位三氟羧酸的峰位值1600cm-1和3500cm-1附近;uio-66-nh2-cf3cooh颗粒为不规则球状,粒径为100-500nm。(3)通过ir、sem表征实施例3制备的cubr2@uio-66-nh2-cf3cooh,结果分别见图4、5。从图中可以看出:cubr2@uio-66-nh2-cf3cooh红外特征峰改变不大,cubr2@uio-66-nh2-cf3cooh颗粒发生改变,变为不规则块状,粒径为100-500nm。实施例6磺酸酯的合成反应,包括如下步骤:室温条件(25-29℃之间)下,在10ml圆底烧瓶中加入对硝基苯四氟硼酸重氮盐(0.0236g,0.1mmol)、dabso(0.0240g,0.1mmol)和实施例3制备的催化剂cubr2@uio-66-nh2-cf3cooh(0.040g),并取甲醇(10ml)和二氯甲烷(2ml)加入至烧瓶中,在室温下混合反应48小时,得到黄色浑浊液,将其过滤,留下的滤液进行旋蒸,抽真空去溶剂之后得催化产物。回收催化剂(按质量计算回收率98%),直接投入下一循环反应,按照上述条件,催化剂使用5个循环,通过gc测试计算产率,催化效果如表1所示。回收的催化剂通过pxrd表征,cubr2@uio-66-nh2-cf3cooh仍保持原来的框架(如图6所示)。表1cubr2@uio-66-nh2-cf3cooh催化二氧化硫插入反应制备磺酸酯5个循环的产率反应次数反应时间/h转化率/%a产率/%a选择性/%a148>99.0>99.0100248>99.0>99.0100348>99.0>99.0100448>99.0>99.0100548>99.0>99.0100注:表1中a表示产率通过核磁测定。以上所述仅为本发明的优选实施例,并不用于限制本发明,对于本领域的技术人员来说,本发明可以有各种更改和变化。凡在本发明的精神和原则之内,所作的任何修改、等同替换、改进等,均应包含在本发明的保护范围之内。当前第1页12