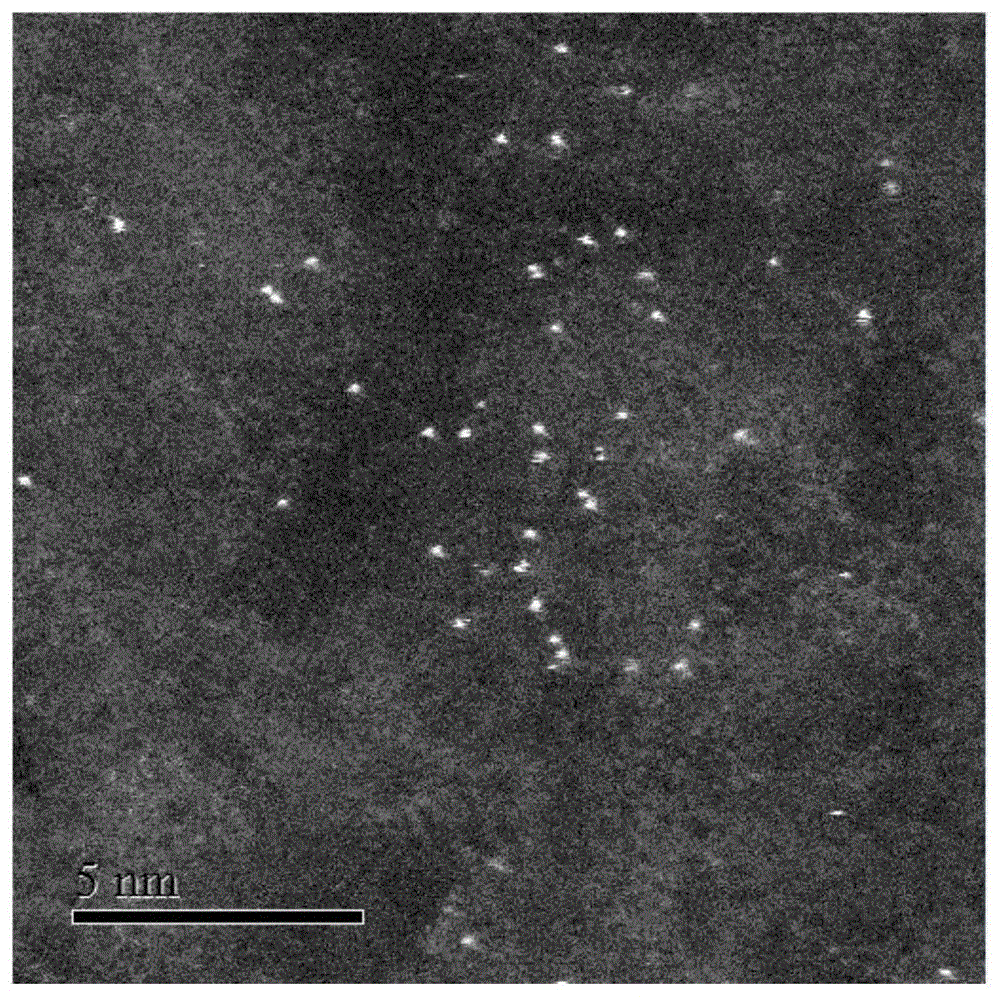
本发明属于合成氨催化剂制备
技术领域:
,具体涉及一种合成氨催化剂及其制备方法。
背景技术:
:合成氨工业是国民经济的重要部分,合成氨催化剂的性能是合成氨工业经济效益的重要影响因素。传统的合成氨采用的原料气为氢气和氮气,以熔铁催化剂为主催化剂,氧化铝、氧化钙等为助催化剂(例如cn1091997a、cn1293593a等),虽然铁基催化剂具有价格低廉、稳定性好等优点,但其操作压力(10~30mpa)和操作温度(450~550℃)都较高,而且催化活性低,能耗高。钴催化剂以钴元素为活性成分、碱土金属元素和碱金属元素为助剂(例如cncn105597760a、cn1293593a),虽然在高氨浓度条件下,可以作为铁催化剂的补充,但是催化活性比铁低。钌催化剂以贵金属钌为活性组分、以活性炭为载体、以钡,银等金属盐为助剂的氨合成催化剂能显著降低反应的温度和压力(例如cn102950026a、cn101579627a、cn1401426a等),因而具有显著的节能降耗效果,但是,钌的分散度较小,粒子大小不均匀,不利于降低单位质量载体钌的用量和提高催化剂的性价比,使得成本居高不下,阻碍了催化剂的工业化应用。因此,需要提供一种低成本、高活性、低能耗的合成氨催化剂。技术实现要素:本发明的目的在于提供一种合成氨催化剂及其制备方法,其制备方法操作简便,易于工业化,制得的合成氨催化剂,钌以单原子形式存在,钴、铁的氧化物之间具有协同作用,结合单原子钌的高催化活性,能在较低的钌负载量下,实现低温低压条件下高的催化活性,降低了合成氨过程中的能耗,节约成本,提高催化效率,具有广泛的应用推广价值。为了实现上述目的,本发明的技术方案如下:一种合成氨催化剂的制备方法,包括以下步骤:常温下,将钌盐、铁盐和钴盐溶于溶剂中,搅拌下滴加沉淀剂溶液,形成共沉淀,搅拌分散、静置、过滤、洗涤、干燥,在金属助剂溶液中浸渍,焙烧,含氢气体中活化,得到合成氨催化剂。优选地,钌盐为rucl3﹒3h2o,k2ruo4,ru3(co)12中的任意一种,铁盐和钴盐为硝酸盐,溶解钌盐、铁盐和钴盐的溶剂为水、甲醇、乙醇。优选地,沉淀剂为naoh、na2co3、koh、k2co3中的任意一种,溶解沉淀剂的溶剂为水、甲醇、乙醇。优选地,金属助剂为kno3、ba(no3)2、la(no3)2中的任意一种,溶解金属助剂的溶剂为水、甲醇、乙醇。优选地,钌盐的加入量相对于催化剂基准以金属量换算为0.04-0.25wt%,金属助剂的加入量相对于催化剂基准以金属氧化物量换算为3-10wt%,铁盐和钴盐按金属量换算摩尔比为1:2-2:1。优选地,共沉淀在稳定ph下进行,ph值保持在8-9之间。优选地,焙烧温度为300-500℃,焙烧时间为1-5h。优选地,干燥温度为20-100℃,干燥时间为2-24h。优选地,浸渍温度为20-100℃,浸渍时间为0.5-2h。优选的,活化温度为100-200℃,活化时间为0.5-2h。与现有技术相比,本发明的合成氨催化剂,在较低的钌负载量下,能在100℃-300℃和0.1-10mpa具有很强的催化效果,降低了合成氨过程中的能耗,节约成本,提高催化效率,具有广泛的应用推广价值。附图说明图1为本发明催化剂的透射电镜图。具体实施方式下面结合实施例对本发明的具体实施方式做进一步的描述,并不因此将本发明限制在所述的实施例范围之中。实施例1将0.001grucl3﹒3h2o、1.51gfe(no3)3和1.82gco(no3)2﹒6h2o溶解在100ml去离子水中,在搅拌下滴加1mol/l的naoh溶液35ml中,形成共沉淀,调节ph值为8,继续搅拌2h,静置2h,过滤,去离子水洗涤,20℃下干燥24h,再在0.02mol/l30ml的kno3溶液中浸渍2h,300℃下焙烧5h,100℃10%氢气还原2h,得到合成氨催化剂。实施例2将0.006gk2ruo4、2.20gfe(no3)3和0.66gco(no3)2﹒6h2o溶解在100ml去离子水中,在搅拌下滴加1mol/l的koh溶液35ml中,形成共沉淀,调节ph值为9,继续搅拌5h,静置2h,过滤,去离子水洗涤,100℃下干燥2h,再在0.02mol/l30ml的ba(no3)2溶液中浸渍0.5h,500℃下焙烧1h,200℃纯氢气还原0.5h,得到合成氨催化剂。实施例3将0.002gru3(co)12、1.95gfe(no3)3和1.18gco(no3)2﹒6h2o溶解在100ml去离子水中,在搅拌下滴加1mol/l的k2co3溶液20ml中,形成共沉淀,调节ph值为9,继续搅拌2h,静置2h,过滤,去离子水洗涤,50℃下干燥12h,再在0.02mol/l30ml的la(no3)3﹒6h2o溶液中浸渍2h,450℃下焙烧3h,200℃纯氢气还原1h,得到合成氨催化剂。实施例4将0.003grucl3﹒3h2o、1.95gfe(no3)3和1.18gco(no3)2﹒6h2o溶解在100ml去离子水中,在搅拌下滴加1mol/l的na2co3溶液20ml中,形成共沉淀,调节ph值为9,继续搅拌2h,静置2h,过滤,去离子水洗涤,50℃下干燥12h,再在0.1mol/l10ml的kno3溶液中浸渍2h,450℃下焙烧3h,200℃纯氢气还原1h,得到合成氨催化剂。实施例5将0.003gk2ruo4、1.95gfe(no3)3和1.18gco(no3)2﹒6h2o溶解在100ml去离子水中,在搅拌下滴加1mol/l的koh溶液30ml中,形成共沉淀,调节ph值为9,继续搅拌5h,静置2h,过滤,去离子水洗涤,50℃下干燥2h,再在0.01mol/l30ml的ba(no3)2溶液中浸渍2h,450℃下焙烧1h,200℃纯氢气还原1h,得到合成氨催化剂。对比例1(1)将0.1mol/l10ml的kno3溶液浸渍到5g活性炭中;(2)将0.003grucl3﹒3h2o、1.95gfe(no3)3和1.18gco(no3)2﹒6h2o溶解在100ml去离子水中,然后浸渍到步骤(1)的活性炭中,50℃下干燥12h,450℃下焙烧3h,200℃纯氢气还原1h,得到合成氨催化剂。对比例2(1)将0.1mol/l10ml的kno3溶液浸渍到5g活性炭中;(2)将2.45grucl3﹒3h2o溶解在100ml去离子水中,然后浸渍到步骤(1)的活性炭中,50℃下干燥12h,450℃下焙烧3h,200℃纯氢气还原1h,得到合成氨催化剂。对比例3(1)将0.1mol/l10ml的kno3溶液浸渍到5g活性炭中;(2)将3.67gco(no3)2﹒6h2o溶解在100ml去离子水中,然后浸渍到步骤(1)的活性炭中,50℃下干燥12h,450℃下焙烧3h,200℃纯氢气还原1h,得到合成氨催化剂。对比例4(1)将0.1mol/l10ml的kno3溶液浸渍到5g活性炭中;(2)将2.87gfe(no3)3溶解在100ml去离子水中,然后浸渍到步骤(1)的活性炭中,50℃下干燥12h,450℃下焙烧3h,200℃纯氢气还原1h,得到合成氨催化剂。对比例5将0.0003grucl3﹒3h2o、0.90gfe(no3)3和2.72gco(no3)2﹒6h2o溶解在100ml去离子水中,在搅拌下滴加1mol/l的na2co3溶液20ml中,形成共沉淀,调节ph值为10,继续搅拌2h,静置2h,过滤,去离子水洗涤,50℃下干燥12h,450℃下焙烧3h,200℃纯氢气还原1h,得到合成氨催化剂。对比例6将0.008grucl3﹒3h2o、2.61gfe(no3)3和0.52gco(no3)2﹒6h2o溶解在100ml去离子水中,在搅拌下滴加1mol/l的na2co3溶液20ml中,形成共沉淀,调节ph值为11,继续搅拌2h,静置2h,过滤,去离子水洗涤,50℃下干燥12h,450℃下焙烧3h,200℃纯氢气还原1h,得到合成氨催化剂。将实施例1-5和对比例1-6所得催化剂作为催化剂,使氢气和氮气在催化剂上反应而合成氨。本实施例制备的催化剂在压力2mpa、温度300℃、氢氮比为3:1、空速为24000ml/g﹒h,反应测试前先在200℃通反应气(流速为30ml/min)预处理1h,再升温升压进行活性测试。结果见表1。表1:催化剂的氨合成反应速率氨合成反应速率(mmol/g·h)实施例12实施例222.8实施例319.3实施例418.6实施例520.2对比例115.2对比例213.8对比例311.7对比例49.6对比例517.2对比例614.8从表1可以看出,在相同条件下,本发明所得催化剂的氨合成速率比传统铁基氨合成催化剂、钴基氨合成催化剂高。上述实施例对本发明的技术方案进行了详细说明。显然,本发明并不局限于所描述的实施例。基于本发明中的实施例,熟悉本
技术领域:
的人员还可据此做出多种变化,但任何与本发明等同或相类似的变化都属于本发明保护的范围。当前第1页12